Ledbury & Brockhampton STWs (2021)
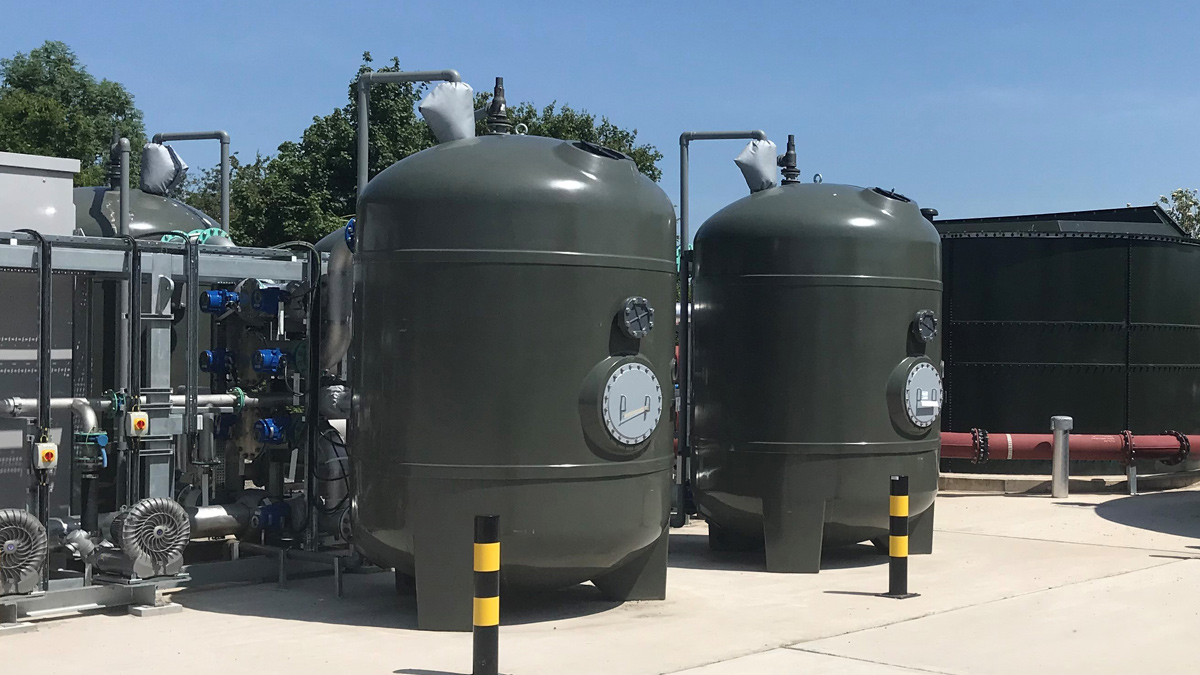
Brockhampton STW tertiary treatment plant - Courtesy of Costain
Both Ledbury and Brockhampton are medium sized works (c15,000 PE) serving the catchments of Ledbury and Cheltenham respectively. Each site was subject to a first-time phosphorus permit with Brockhampton receiving higher flow to full treatment and a tighter BOD permit, and Ledbury having significant growth projected in the catchment. Both sites both required new tertiary solids removal (TSR) package plants with two-point dosing of ferric sulphate. Costain delivered these projects for Severn Trent under their AMP6 delivery vehicle CiM6; a collaboration between Costain PLC and Stantec UK. Having the lowest whole life cost, Bluewater Bio Ltd’s Filterclear® mixed media pressure filter was selected for both schemes, with Colloide Engineering Ltd supplying the Severn Trent approved standard ferric sulphate dosing rigs.
Ledbury STW
Ledbury receives significant trade waste (up to a third of load) from a brewery and cheese manufacturer in the catchment. The site consists of an inlet works with grit removal, two crude oxidation ditches configured in alternating enhanced biological phosphorus removal (EBPR) mode with up front anaerobic tank, SAS thickening and two FSTs. The broader scope of the new works at Ledbury STW includes:
- Refurbishment of an existing dosing rig to meet Severn Trent’s design manual standard and dose ferric sulphate using feed forward control:
- At the oxidation ditch outlet (pre-FST).
- Before the tertiary solids removal plant.
- A new Bluewater Bio Ltd Filterclear® mixed media pressure TSR filter treating FST effluent.
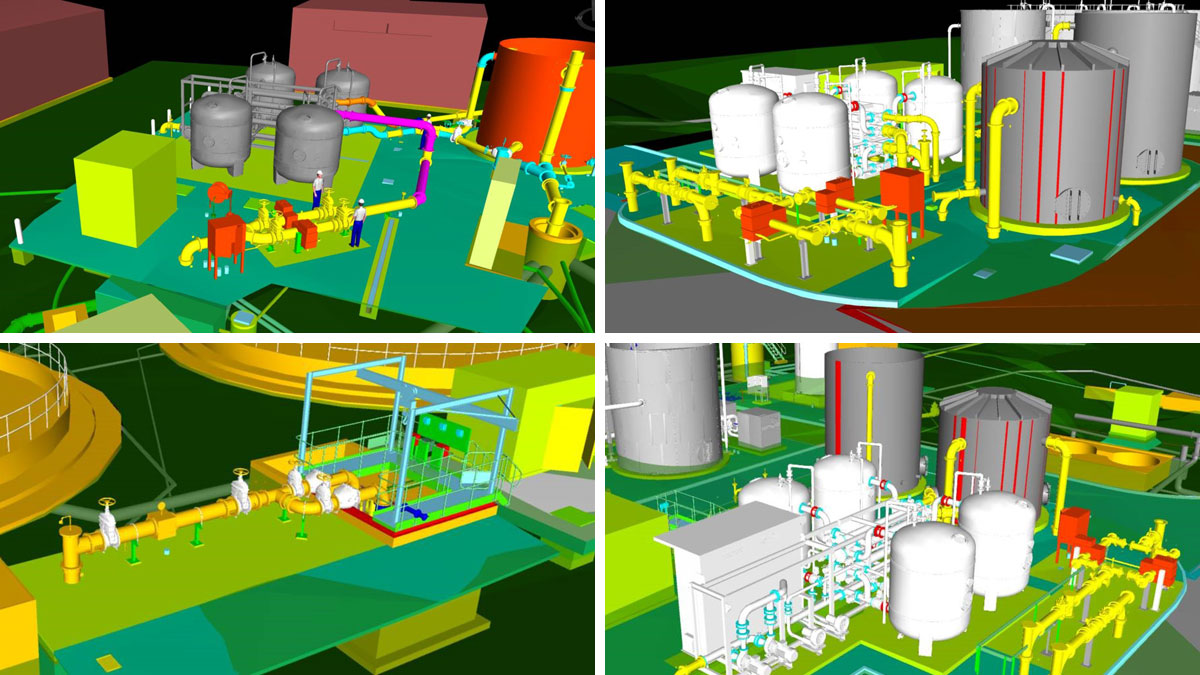
Model overviews of tertiary solids removal plant at Ledbury STW – Courtesy of Costain
Brockhampton STW
Brockhampton is a traditional ASP works subject to some distinct trade loads (15,000 PE), as well as being the primary treatment plant for flows from Cheltenham Racecourse and having the challenge of dealing with sewage flows from up to 80,000 visitors during the week of the Cheltenham Gold Cup.
The works has inlet screw pumps to screens and storm separation, Dortmund primary settlement tanks (PST), activated sludge plant (ASP), surplus activated sludge (SAS) thickening and final settlement tanks (FST). The broader scope of the new works required at Brockhampton includes:
- Modifications to the inlet works to facilitate higher flows, with innovative re-purposing of existing structures to increase storm capacity.
- Revised aeration within the existing ASP including raising of the liquid level (by 700mm) to deal with increased flows and increasing the anoxic retention time.
- Ferric sulphate dosing both to the inlet of the ASP (using a diurnal dose) and to the upstream of the new tertiary solids removal filter (TSR) using feed forward control based upon pre-TSR ortho-phosphate.
- A new Bluewater Bio Ltd Filterclear® mixed media pressure TSR filter treating FST effluent.
- Minor capital maintenance items involving return activated sludge (RAS) pumps and trade waste control and monitoring.
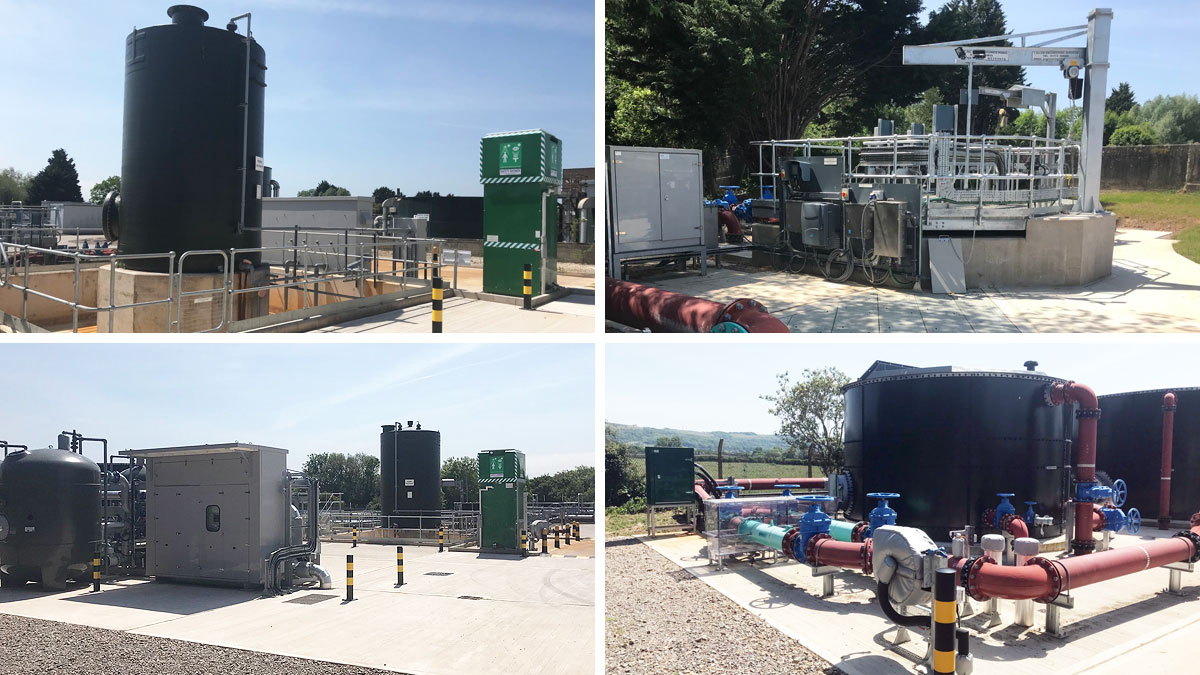
Brockhampton STW tertiary solids removal plant – Courtesy of Costain
Challenges
Programme challenges lead to a very tight situation on both projects where an impending permit required a very prompt response from the newly installed plant. All parties were very satisfied to see an immediate response from the TSR and TSR dosing.
At Brockhampton, in the months running up to the regulatory date the total phosphorus figure was averaging 0.6 mg/l total phosphorus and with some final tweaks to the dose rate, by the end of March 2020 the plant was achieving the 0.25 mg/l total phosphorus permit. By September 2020, during a twenty-eight-day suite of intensive sampling, output achieved an average of just 0.1 mg/l of total phosphorus from spot samples. This performance is well within permit and has been consistently achieved ever since.
By using feed forward control for the secondary ferric dose, chemical consumption has been minimised. The iron permit levels of 4 mg/l (at 95 percentile) and an 8 mg/l upper tier are safe with average iron in the final effluent sitting at only 0.4 mg/l
Similarly at Ledbury, although a long way from its growth design horizon, the new equipment has responded quickly to the challenge. Before the new tertiary solids removal and tertiary dosing plant were brought online, total phosphorus in the final effluent averaged 4 mg/l.
By the end of March 2020 and the implementation of the 0.3 mg/l total P permit, the site was achieving an average of 0.2 mg/l. Total iron in the effluent was also well within the 4 mg/l (at 95 percentile) and 8 mg/l (upper tier) permit, consistently averaging 0.2 mg/l.
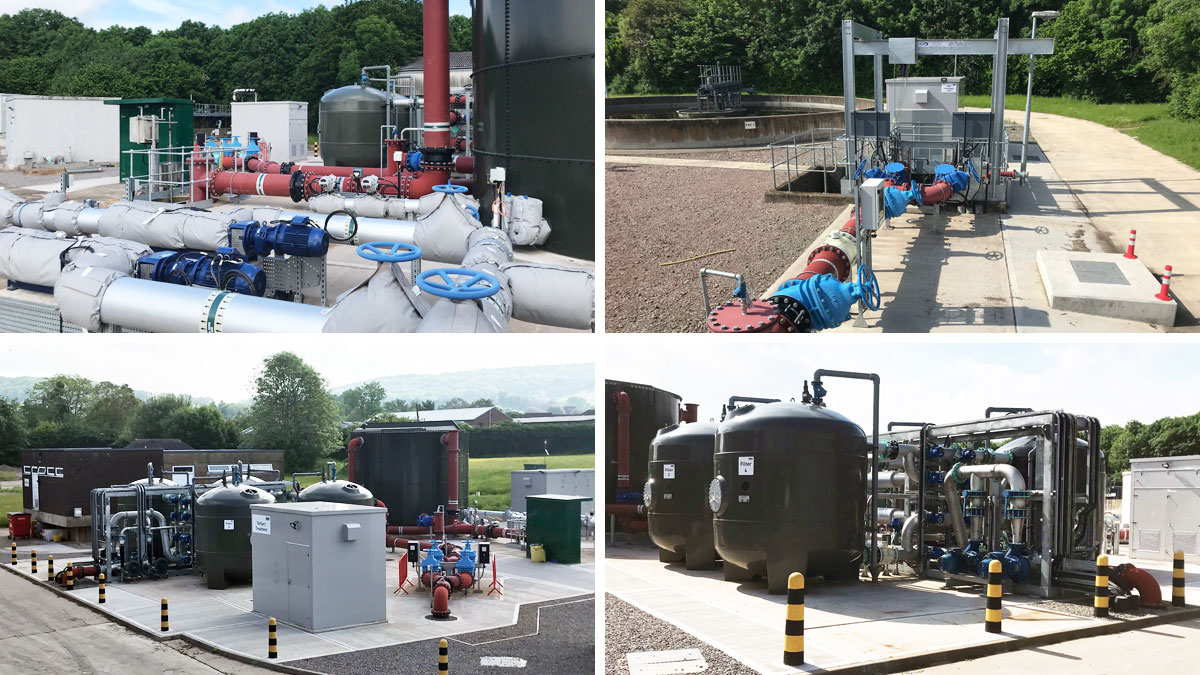
Ledbury STW tertiary solids removal plant – Courtesy of Costain
Ledbury & Brockhampton STWs: Supply chain – key participants
- Main contractor: Costain Group PLC
- Consultant designer: Stantec UK
- Geotechnical investigation: Geotechnics Ltd
- Chemical dosing package plant: Colloide Engineering
- Filterclear® mixed media filter: Bluewater Bio Ltd
- Pipework & mechanical installation: De Havilland Engineering Group
- Systems integration & electrical control panels: CEMA Ltd
- Backwash water tanks: Stortec Engineering Ltd
Project success
The success of a project can be measured in many ways, with the ultimate measure being end user satisfaction. From the outset, Costain carried this belief throughout the duration of the project. Though Severn Trent’s Operations teams are now trained and primed for action, the project team are delighted that very little intervention has been needed.
Teething issues aside, the requirement for planned maintenance is minimal and effluent quality has remained consistently high throughout the after-care period. The Filterclear® system is proving a robust technology and the common/template arrangement of Colloide’s dosing rig makes for a simple resolution if minor issues arise.
High expectations were set at the start of AMP6 for Severn Trent, and Costain has worked hard to maintain standards and drive these high expectations through to completion. In terms of delivering high quality final effluent and achieving sound uptake of the new equipment by Severn Trent’s operations teams, both projects have exceeded expectations.