Mayflower WTW (2016)
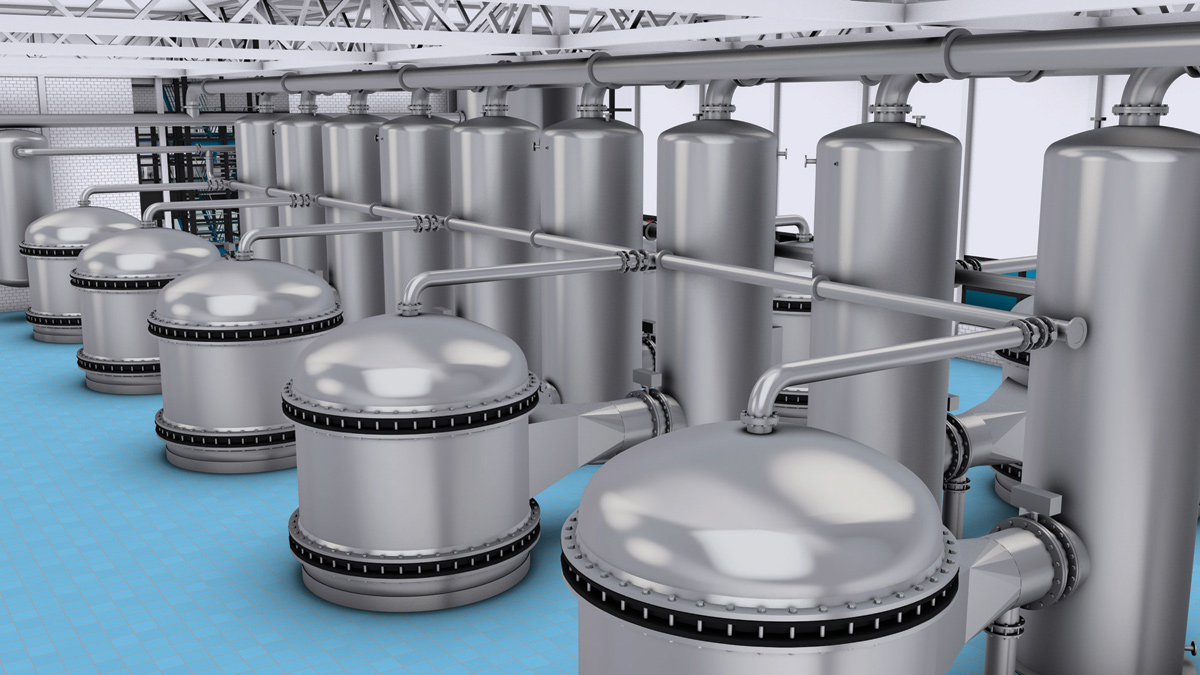
Ceramic membrane microfiltration units (CeraMac) - Courtesy of PWN Technologies
South West Water (SWW) has started construction on a new £60m state-of-the-art water treatment works in Devon, the company’s flagship project in its 2015-2020 business plan. Mayflower WTW will use cutting-edge treatment processes, designed and developed by leading Dutch water technology company PWNT and will serve around 250,000 customers in Plymouth and the surrounding area. It is being built at Roborough Down, just outside the city, and will replace Plymouth’s outdated Crownhill WTW. The construction phase is scheduled to finish by the end of March 2018. Mayflower WTW will become operational in September 2018, with Crownhill WTW retiring from service a few months later. The new works will be capable of producing up to 90ML of drinking water every day, with an average of 55ML a day. It will serve more than 6,000 businesses, including Her Majesty’s Naval Base Devonport and Derriford Hospital.
Project background and drivers
Crownhill WTW was built in the 1950s, long before automation, modern water quality standards and operational best practice. Since then, the city of Plymouth has grown significantly and what was a rural works has been absorbed into a very busy city. The site is extremely constrained, which makes operation and access difficult as well as posing risks to site security, with limited room to expand or adapt the current treatment processes.
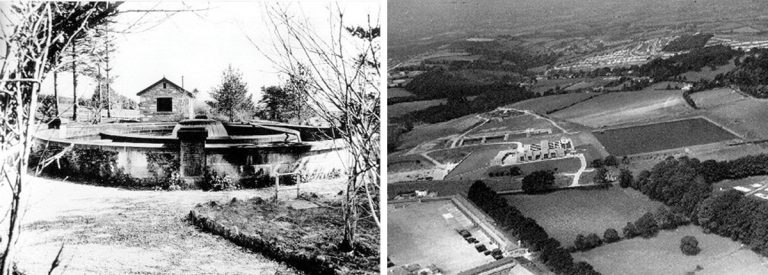
(left) Roxborough WTW – pre-1920s and (right) Crownhill WTW (1960s) – Courtesy of South West Water
Replacing Crownhill WTW has been a long-term part of South West Water’s strategic plans for developing the water supply network. There were three options:
- Refurbish the existing works.
- Build a new works with traditional treatment.
- Build a new works with innovative treatment.
A business case was established for a new build with an innovative water treatment process,which will be the first time this technology has been used in the UK. The investment case was submitted in South West Water’s Business Plan for the 2014 Price Review as an exceptional item. Ofwat accepted the case without challenge and commended the innovative approach to the project.
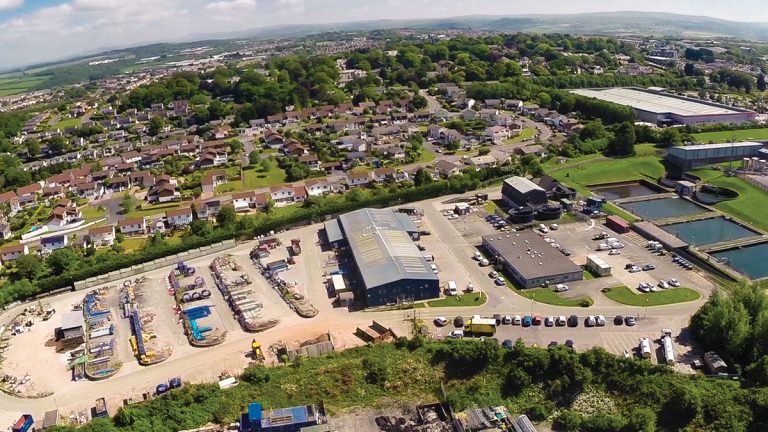
Crownhill WTW (2016) – Courtesy of South West Water
Project partners
The project will be undertaken by South West Water Delivery Alliance H5O, which has worked with SWW as part of the since 2009.
- Global design and consultancy firm Arcadis is the main design contractor, in partnership with consulting engineers Pell Frischmann. Together they are responsible for all the design work outside of the key treatment process.
- Infrastructure group Balfour Beatty is the main construction contractor, in partnership with Interserve, with responsibility for the construction of all infrastructure, buildings and pipelines for the new water treatment works.
- PWNT is responsible for the design, installation and commissioning of the main water treatment process.
Pilot plant
From June 2013 until June 2015, a prototype facility using suspended ion exchange (SIX®), inline coagulation (ILCA®) and ceramic membrane microfiltration (CeraMac®) was tested at Crownhill WTW using water from Burrator Reservoir, the River Tavy and River Tamar.
The pilot plant confirmed that the new technology can successfully treat South West Water’s raw water sources to produce exceptionally high quality drinking water while minimising the impact on the environment.
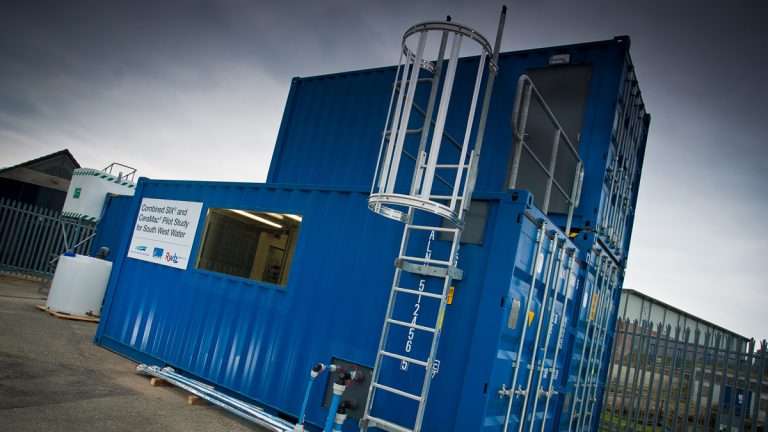
Pilot plant at Crownhill WTW – Courtesy of South West Water
New technology
The new process, which will mark a significant step away from chemical and energy intensive traditional technology, is around five times faster and more robust than traditional treatment processes.
- After screening, ion exchange resin is added to the water and mixed with air as the water and resin flows through a number of tanks. SIX® can use a variety of resins in suspension to remove natural organic material. During this time (about 15-30 minutes), natural organic matter and nutrients such as nitrates transfer from the water to the resin.
- After contacting time the resin is separated, regenerated with a salty solution and recycled back around the process.
- The water is then coagulated and filtered by CeraMac®, with around 900 ceramic membranes encased inside 10 (No.) vessels. These ceramic membranes filter the water through tiny pores that are less than 1/10,000th of a millimetre. Filtering to this level removes almost all particles including bacteria and other harmful organisms including cryptosporidium.
- Next the water passes through deep beds of activated carbon where any more natural and man-made dissolved organic matter is removed. Each tiny grain of carbon contains a huge surface area on which organic molecules get trapped.
- The water is given a final disinfection with ultraviolet light. Prior to being stored on site and making the journey to customers the naturally low pH and hardness of the water is adjusted with lime and carbon dioxide, and a small residual dose of chlorine is added.
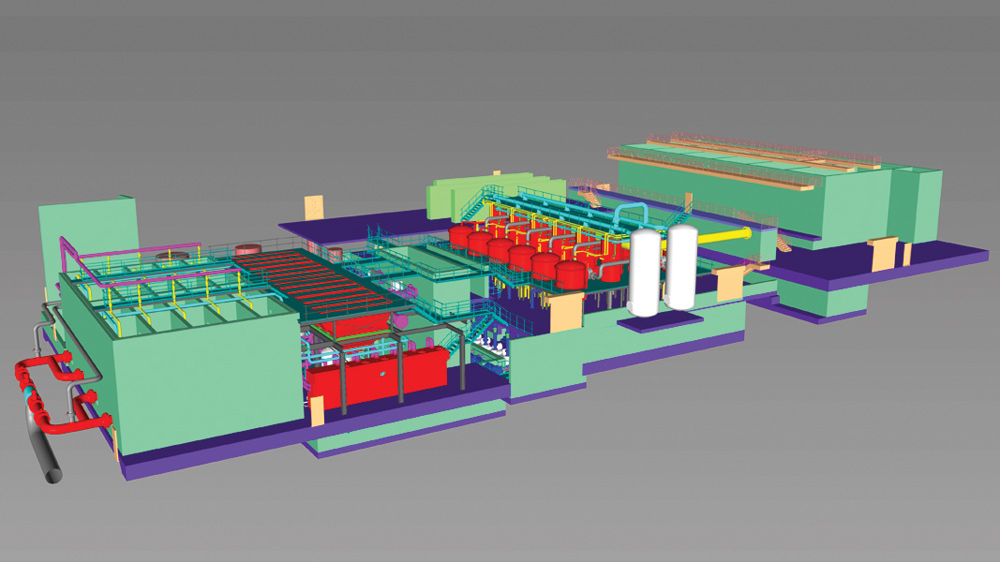
Current 3D Model – Courtesy of South West Water
Comparison with conventional treatment technology
The new process is very efficient and has a smaller footprint than conventional treatment technology. The ion exchange technology only consumes salt and the resin used can be recycled many times for several years. This reduces the amount of waste produced.
The coagulation is essentially the same as in conventional treatment but because of the ion exchange and membrane much less coagulant is required and the overall time of these processes reduces from hours to minutes. This means the process is very compact and therefore reduces the amount of construction materials required.
The membrane itself is very special and leads to an exceptionally high water quality. Because the pores are fixed within the ceramic material they are absolute, so no matter what the quality of the raw water, the filtered water is always safe.
Ceramic membranes have outstanding features compared to polymeric membranes:
- An unlimited life (meaning no replacement costs).
- No fibres that can break.
- The ability to backwash at very high pressures (improved cleaning).
- Stable water throughput over its lifetime.
The process can treat a wider range of raw water quality from almost any source. This is important because we are starting to see the early impacts of climate change on raw water quality, which is deteriorating all over northern Europe.
Location, location, location
The construction site at Roborough Down, on the edge of Dartmoor National Park, has a history of water treatment dating back 118 years. The south-west corner of the current site was bought by the then Plymouth Corporation in 1898 and an early water treatment works was located on the site before Crownhill was built. This piece of land was inherited by the South West Water Authority in 1974 and then South West Water in 1989. SWW purchased two further parcels of land in 1991 for the site’s current raw water tank, which feeds Crownhill and Littlehempston WTWs, and a proposed treatment works to supplement Crownhill WTW, which was never built.
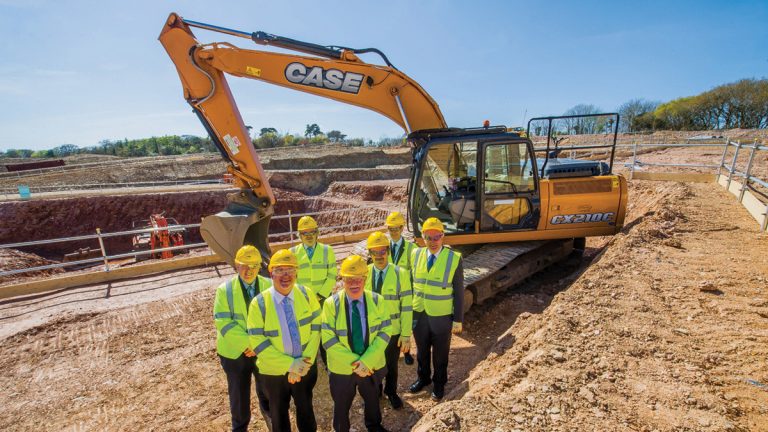
Local authority representatives on site May 2016 – Courtesy of South West Water
Since Crownhill was built in the early 1950s, the city of Plymouth has grown and much of the new development has been on the higher ground to the north and east of the treatment works. Consequently water now has to be pumped from Crownhill up to Belliver Service Reservoir to supply 14,500 properties (40,000 population). The new site will enable water to gravitate to a wider area, which reduces costs and lowers the carbon footprint.
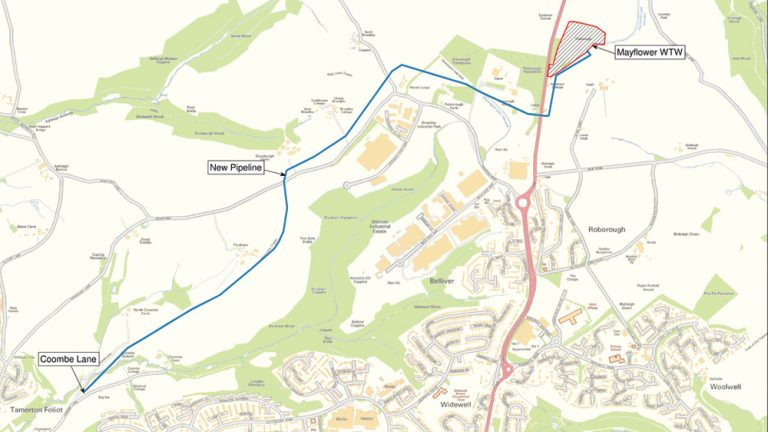
Pipeline route – Courtesy of South West Water
Ancillary works
The £60m project is complex and includes a range of infrastructure and non-infrastructure asset groups including raw water mains, intake pump stations and the water distribution system. As part of the project, a new 7km treated water main will be laid, following the route of the existing raw water main, from the new treatment works to Crownhill, where it will connect into the distribution network.
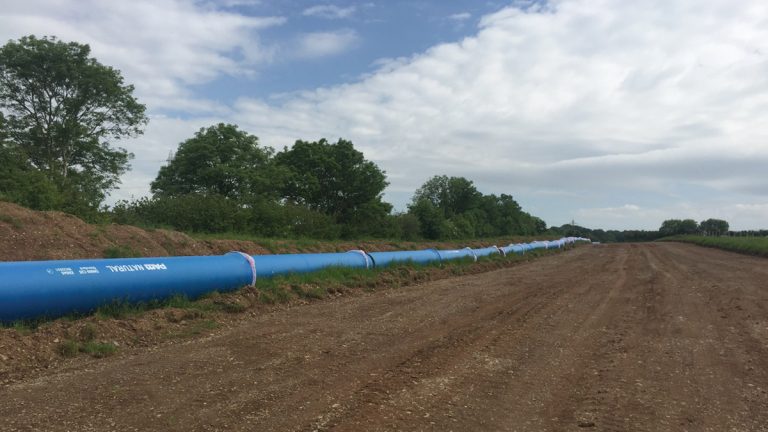
Pipes ready to be laid – Courtesy of South West Water
Main construction materials
Over the course of the project the following materials will be used:
- 20,000 tonnes of aggregates.
- 4,500m³ of concrete.
- 410 tonnes of steel reinforcement.
- 7km of off-site pipeline.
- 2km of on-site pipe work.
- 3km of cable ducts.
- 80,000 tonnes of earth.
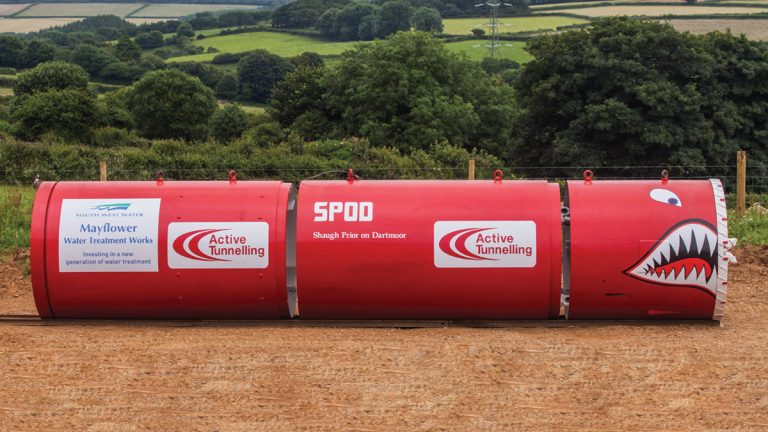
‘SPOD’ – the tunnelling machine which will burrow underneath the A386 – Courtesy of South West Water
Conclusion
The construction phase is scheduled to finish in March 2018. The works will become operational in September producing up to 90ML of drinking water every day.
“We’re delighted, after many years of planning and preparation, to have started work on this very exciting and globally significant project. Our aim is to continue to provide good, safe drinking water that has the trust of our customers, while minimising the cost of water treatment and our impact on the environment.
“This long-term investment will meet the needs of Plymouth’s growing population and provide a secure, high-quality drinking water supply for the wider Plymouth area for generations to come.”
Senior Project Manager, Mike Court.