Ogston WTW (2018)
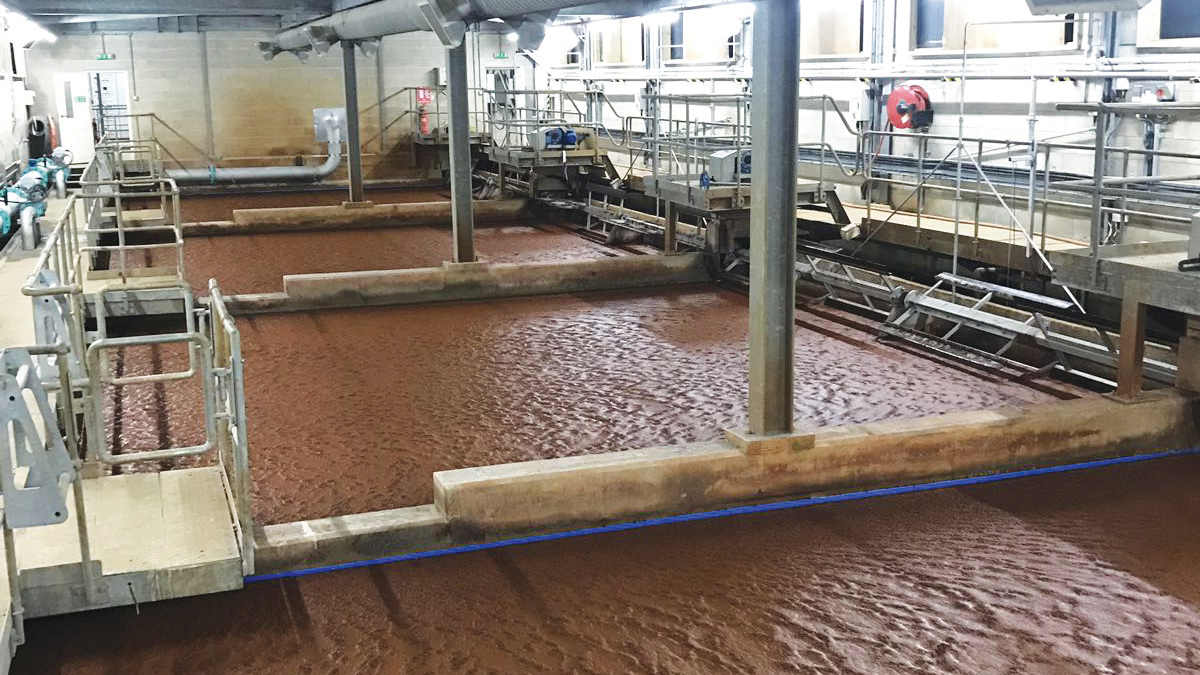
New DAF cell beach scrapers, including new sludge trough spray bars Courtesy of Stantec Treatment
Ogston Water Treatment Works (WTW) is located at Stretton, Higham in Derbyshire and it provides treated water to Higham, Ambergate and Whiteborough Reservoirs. The maximum works output is 76 mega litres per day (MLD) with an output for the New works DAF (dissolved air flotation) plant of 50 MLD. As part of the AMP6 coagulation and clarification (C&C) batch awarded to Stantec Treatment (now MWH Treatment) under the CIM6 joint venture framework, the New Works is undergoing capital maintenance improvements to the C&C systems, in order to reduce risks to Severn Trent Water’s (STW) Drinking Water Safety Plans.
The existing process overview of the New Works
Ogston WTW raw water is abstracted from the River Amber and stored in Ogston Reservoir. The works can also receive raw water from the River Derwent via the Ambergate Pumping Station, which can pump water to the works or the reservoir. On the New Works, the inlet raw water is dosed with coagulant prior to splitting to 4 (No.) DAF clarifiers, comprising two-stage flocculation and DAF flotation cells. The DAF cells are in a single stream with dedicated duty/standby recirculation pumps and duty/standby saturators.
The duty/standby compressors provide air to the DAF stream, clarified water then distributes to 8 (No.) rapid gravity filters (RGFs) and filtered water from the RGFs gravitates to the low lift pumping station. It is then pumped to 8 (No.) granular activated carbon (GAC) absorbers. The treated water gravitates to the contact tanks from the respective works and balance tanks prior to pumping into supply.
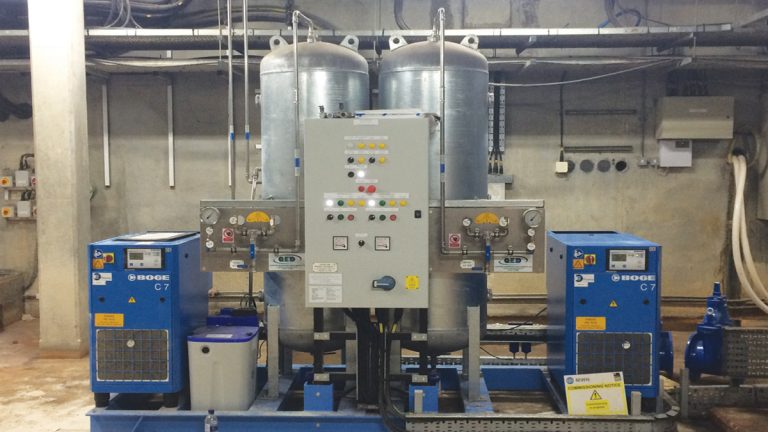
The new DAF saturator compressors and air receiver vessels – Courtesy of MWH Treatment
Overview of C&C including DAF technology
Coagulation involves the addition of a chemical coagulants for the purpose of conditioning the suspended, colloidal and dissolved matter, for subsequent processing by flocculation that will allow for the removal of particulate and dissolved matter from the water. Coagulants such as aluminium sulphate, ferric chloride, and ferric sulphate hydrolyse rapidly when mixed with the water to be treated. As these chemicals hydrolyse they form insoluble precipitates that destabilise particles by adsorbing to the surface of the particles and neutralising the charge and/or forming bridges between them.
At the New Works, the chemical coagulant employed is ferric sulphate, however, the system is also designed to accept aluminium sulphate. Organic polyelectrolytes are also used for particle destabilisation but a polymer dosing system is not required on the New Works and no new upgrades were required to the existing flocculation system either.
Downstream of the flocculation processes, the water goes through the clarification process; at Ogston New Works this is a DAF process. This involves the separation of flocculated particles from the water using fine air bubbles, which are dissolved in saturated water with compressed air, rather than more traditional methods such as gravity separation. The fine air bubbles are introduced at the bottom of each basin via a pipework manifold complete with distribution nozzles. As the bubbles rise to the surface they become attached to the flocculated particles and other matter. The air is first dissolved in water further upstream through a set of compressors, air receivers, recirculation pumps and saturator vessels filled with packing (pall rings). Once the saturated water enters the basin and comes in contact with the process water to be treated, the combination of particulate matter, flocculant particles and bubbles are sufficiently buoyant and thus rise to the surface of the basin. A scraper system removes the solid matter from the surface of the basin by mechanical means or through entrainment into a sludge trough. The process water is subsequently filtered further downstream.
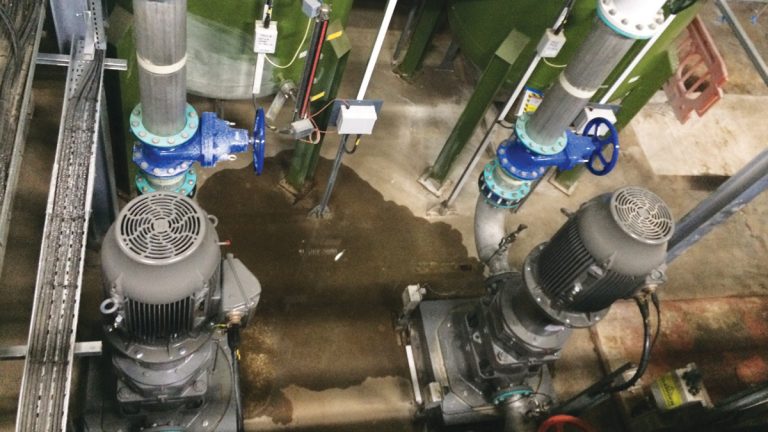
The new DAF recirculation pumps and discharge pipework – Courtesy of MWH Treatment
Scope of works
The capital maintenance improvements to the coagulation and clarification systems at the Ogston New Works includes:
- The installation of a new coagulant dosing day tanks system which will ensure the future operational reliability and process resilience of coagulant dosing to the works.
- The implementation of a new coagulant transfer pipework system, linking the existing coagulant bulk storage tank to the new coagulant day tanks rig.
- Upgrades to the existing saturator system on the dissolved air flotation (DAF) plant.
- The DAF plant control upgrades will allow a standardised approach across similar operational sites and together with the mechanical and electrical (M&E) upgrades, allows for plant optimisation in terms of operational energy savings.
- Upgrades to the existing scraper system on the DAF cells.
The installation of a new coagulation dosing rig
The new coagulant dosing rig was manufactured off site and transported complete to the site, with the two day storage tanks, chemical dosing pumps, valves and instruments housed in a kiosk and crane lifted into place on site. Other rig infrastructure included the construction of access steelwork, an emergency shower and all the associated civil work to enable this, was completed once the rig was in situ.
A batch design approach was employed which enabled design efficiencies to be realised across several schemes in the coagulation and clarification batch of projects. This also ensures that a similar control approach was adopted across the other coagulant dosing rigs on each of the schemes.
The new coagulant day tanks are fed from bulk storage tanks which run through underground ducting within dual contained pipework across the site. Additional pipework, transfer pumps, associated valves and catch pots were also designed and are being constructed on this scheme to transfer the chemical from the bulk storage tanks to the day tanks and from the day tanks to the point of application dosing point, into an existing static mixer housed in an underground chamber local to the day tanks.
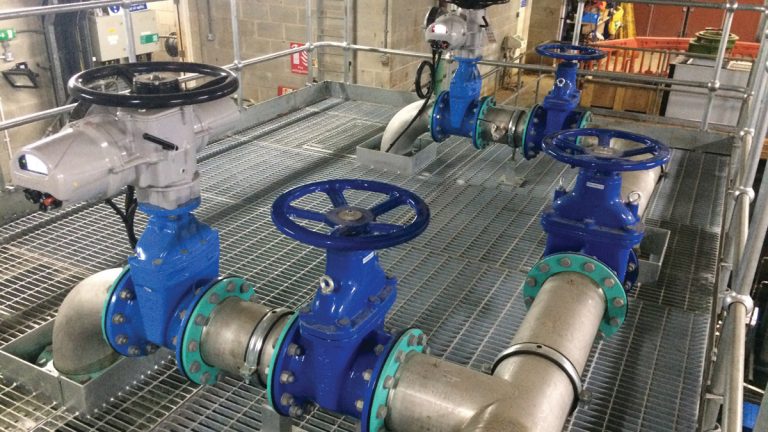
The new DAF saturator pipework and valve assemblies and platform about the existing saturator vessels – Courtesy of MWH Treatment
Upgrades to the existing saturator system on the DAF plant
A new DAF software algorithm was implemented that controls the system to achieve a set quantity of dissolved air per m3 plant flow. The old software controlled the system on a saturator pressure set point. The new control algorithm is designed to control the plant based on a set dissolved air precipitation set point by modulating the recirculation pump flow-rate based on measured inputs of saturator pressure, works flow-rate and raw water temperature.
The old control was providing the DAF cells with a dissolved air precipitation value of 19g/m3 versus the recommended value of 10g/m3. Therefore an unnecessary amount of energy was expended by running the plant on the old control system. Projected energy savings are realised though a reduced recirculation pump flow-rate. The new system will therefore provide significant projected energy savings estimated at 118,000kWh per year (or £14K a year as calculated in the Gate 3/pre-construction revenue effect of capital (REOC) assessment). Furthermore, the new control algorithm adopts a standardised approach that is being rolled out on other coagulation and clarification DAF schemes across the batch in the STW region, including Bamford and Draycote, allowing for easier comparison between operational sites.
DAF upgrade construction challenges and enabling works
Significant construction challenges were overcome in order to implement the new DAF header and recirculation pipework and control system. As this was an upgrade to an existing site, this included a transitional approach with two out of the four cells running on the old software and pipework system with the remaining two on the new system and the duty/standby recirculation pumps, compressors, air receivers and saturator systems temporarily running as dedicated duty systems to each set of two DAF cells.
Temporary pipework spool pieces were constructed to physically enable the split of the system in to two dedicated duty systems. Close liaison with STW site operators was required to ensure that the lack of any standby capacity and the necessary restriction to the works capacity, was adequately assessed with regard to impacts on the network during the construction phase.
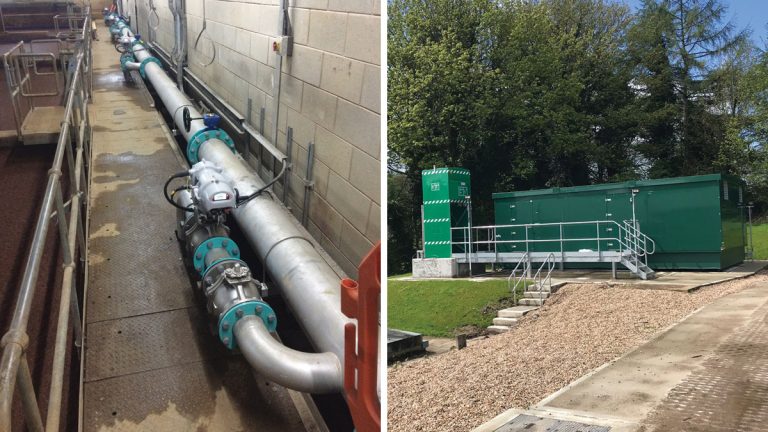
(left) New DAF header and DAF cell droppers including valves and (right) New coagulation dosing rig day tanks, access steelwork and emergency shower – Courtesy of Stantec Treatment
Upgrades to the existing scraper system on the DAF cells
The scheme includes the replacement of the existing chain and flight type DAF scrapers system with a new beach scraper system. A temporary beach scraper was constructed and underwent a trial in Cell 2 of the DAF plant in May 2017, ahead of a permanent upgrade. The combined turbidity level within the cells for the duration of the trial remained below the 2 NTU criteria. Any spikes within the cell during the trial were attributed to issues with ‘black water’ relating to poor levels of air saturation within the water entering the cell, as at this point in the project the DAF system itself had not undergone any upgrades. The old chain and flight system suffered from reliability issues with regular breakages to the chain, requiring frequent occurrences of the DAF cells being taken out of service to replace these chains.
The new twin blade beach-type scraper system contains less moving parts, thus improving the potential for service reliability. The new beach scraper mechanism also improves the process reliability of the plant allowing a higher degree of separation of the solids from the supernatant, with improved levels of turbidity in the individual and combined cell clarified water outlets. A new sparge pipe spray bar was also constructed to ensure that the sludge collection channel/trough was kept free from build-up.
Conclusion
The DAF upgrades and new coagulant (ferric) dosing system will provide both added resilience and long term operational savings for STW. Notable improvements include the added performance reliability of the scraper system associated with the new twin blade beach type scrapers. In addition there will be projected savings estimated at up to 118,000kWh per year associated with controlling the dissolved air precipitation set point to 10g/m3.