Ravenhill Avenue, Belfast, Flood Alleviation Project (2024)
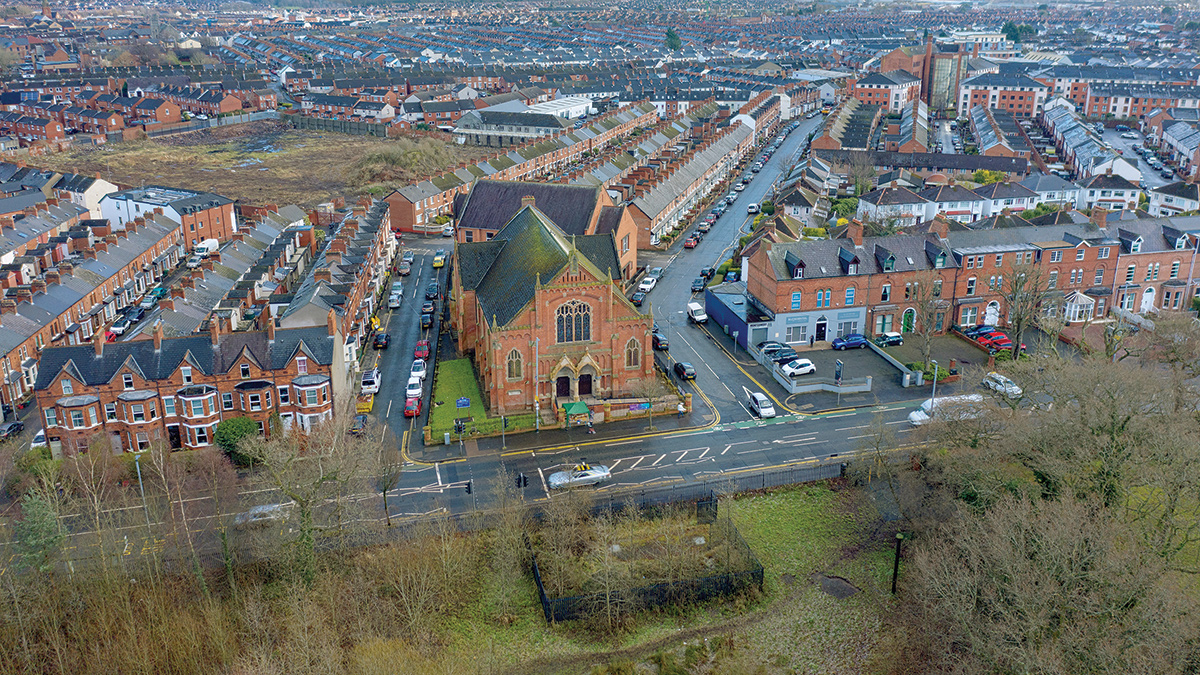
View of Ravenhill Avenue & Ravenhill Road from Edge of Ormeau Park - Courtesy of GEDA Construction
Ravenhill Avenue is located in south Belfast, close to the city centre. It is a densely populated residential area which has seen recent development of historically industrial sites. In recent years, customers have experienced flooding of their properties during heavy rainfall when the combined sewers fill with stormwater. From concept, it was expected that this project would present many challenges. Existing infrastructure dates back to early 20th century, and with the area being so densely populated, construction would have major customer impact. Project success would be measured against time, cost and quality, so it was important to have the right delivery partners, procured through the most effective form of contract.
Background
As part of Belfast’s strategic ‘Living with Water Programme’, NI Water has invested £7m on the Ravenhill Avenue Flood Alleviation Project to upgrade the existing infrastructure in order to:
- PROTECT against Flooding: Removing 11 properties from the DG5 (internal flooding) Register.
- ENHANCE the Environment: Storm separation of 9 hectares of impermeable ground and return to River Lagan.
- GROW the Economy: Providing first time services (storm sewers) for 572 properties.
NI Water used existing framework partners to develop and deliver the solution:
- AtkinsRéalis was appointed through an NEC3 PSC Option E contract to provide modelling support.
- AECOM was appointed through an NEC3 PSC Option A contract to develop a reference design, and professional services including project management, cost management and site supervision. AECOM acted as NEC Project Manager.
- GEDA Construction was appointed as the Contractor through an NEC4 ECC Option C contract.
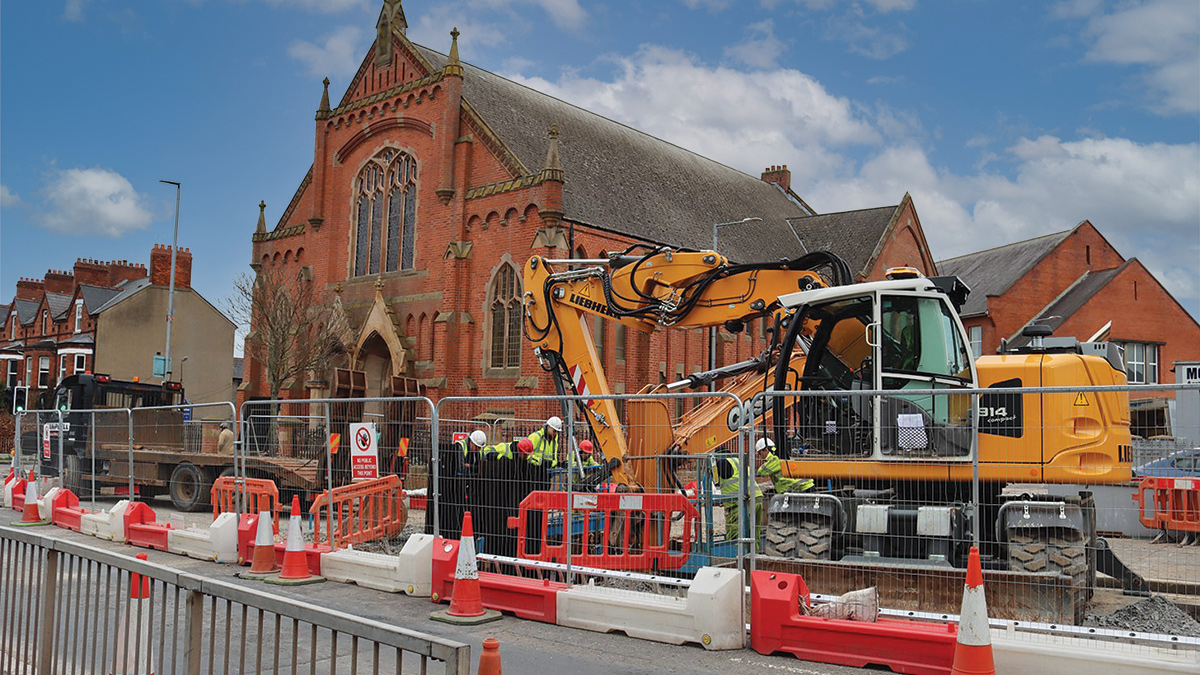
Laying storm sewer on Ravenhill Road – Courtesy of GEDA Construction
Choosing an Option C Contract
An NEC Option C contract is a cost reimbursable contract with a target price and pain/gain share mechanism. This means that if the costs of the project exceed the Target Cost the excess, or ‘pain’, is allocated between the Client and the Contractor, and if the project comes in under Target Cost then the ‘gain’ is allocated.
The philosophy behind this type of contract is to actively encourage all parties to work together to manage the costs of the works.
As the Client, NI Water wanted to achieve best value. This type of contract incentivised the Contractor to develop value engineering solutions that would generate cost savings to benefit both parties. Payment was through an open-book accounting approach; meaning the Client had full transparency of costs. This also provided good data for the Client’s cost database.
It was recognised that the challenges and complexities of the project should be addressed and risk mitigated through a spirit of collaboration. In an NEC Option C contract, the Client and Contractor share the financial risk, which incentivises collaboration. Through Early Contractor Involvement the project team adopted an open and collaborative relationship.
Then through successful collaboration, risk was effectively managed. On a project of this scale changes are inevitable, but this approach encouraged shared problem solving and fostered a non-adversarial approach.
Managing an Option C Contract
When an NEC Option C Contract is suggested, people often worry about mounds of paperwork. AECOM were appointed as Project Manager for the NEC ECC Option C Contract which included providing cost management services. As with any NEC contract there were monthly valuation assessments and change control to be managed through compensation events. Importantly, with an Option C Contract, interim audits were completed at regular intervals during the project to keep on top of the paperwork and also help verify contractor forecasts.
The Contractor was open and accommodating with the auditing process, understanding the importance of regular checks and the cost elements that make up the Schedule of Cost Components plus what would be a Disallowed Cost or included in the Fee. It was important for the Contractor and the project manager to remember that it was not a ‘Cost-Plus’ type form of contract and that project controls were imperative to ensure a commercially acceptable outcome.
While regular checks of invoices and payments would be expected in an NEC4 ECC Option C contract, the Contractor effectively managed and utilised the Cl.50.9 mechanism to gather records for part of the works at these regular intervals, invite the Project Manager to inspect them, and demonstrate that they have been correctly assessed. Such notification puts a time limit on the Project Manager to review and make a decision on these records, ensuring that assessments are accurate throughout the project, rather than a time-consuming substantial audit at the end.
While a Contractor would normally carry out regular internal updates to their forecasts on other forms of contracts, it was encouraging to see under NEC4 ECC Option C that the Contractor makes this information readily available to the Project Manager and to the Client to aide their various monthly reports and understanding of how the project is progressing. While forecasts can understandably change, the Contractor was required under the Contract to explain any changes made from the previous forecast had been submitted. Inevitably this stimulated further collaboration between the Project Manager and the Contractor to discuss and mitigate risks where possible through the early warning and value engineering processes if appropriate.
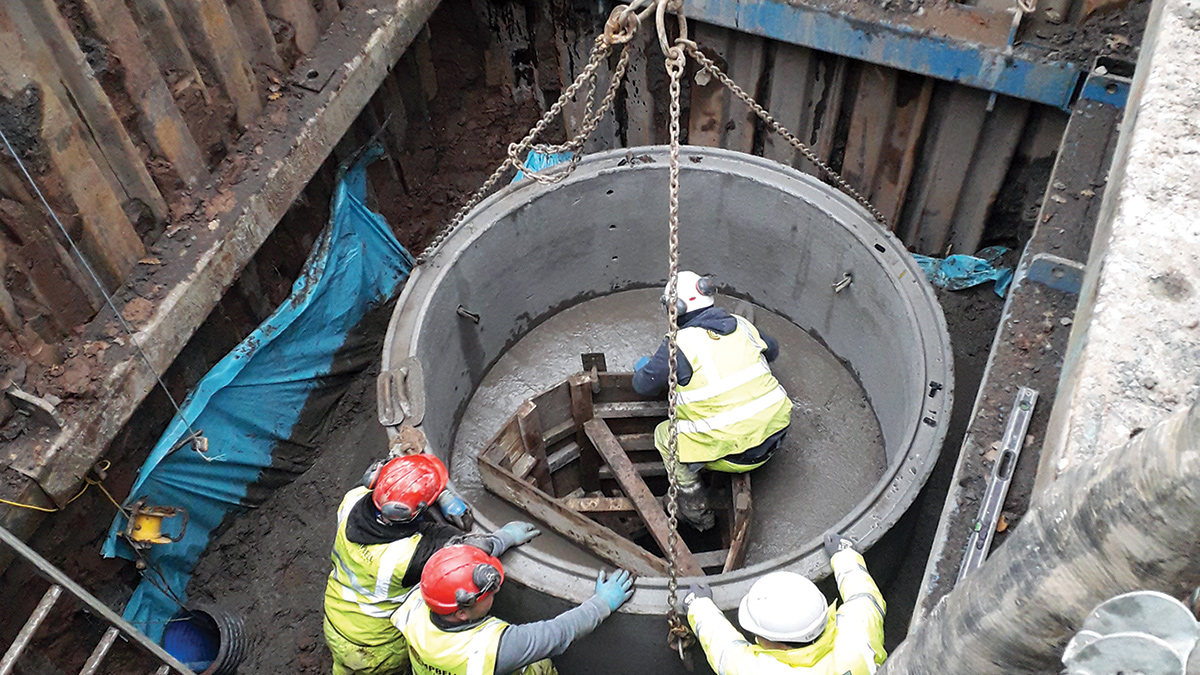
Manhole construction – Courtesy of NI Water
Risk mitigation on an Option C Contract
As already noted, Option C contracts share the risk and reward between Client and Contractor with everyone focused on balancing cost, time and scope. Typically once a contract has been awarded the Client will not move on scope, as they see scope and quality being interlinked. On Ravenhill both the Contractor and Client understood that value engineering, requiring a change to scope, could benefit both parties.
Value engineering was only possible due to the buy-in from NI Water’s Operation & Maintenance team. Non-man entry manholes to the 1800mm combined sewer were proposed by the Contractor to save on time and cost, whilst also reducing health & safety risks during construction. It was also agreed with NI Water that non-man entry would act as a deterrent for anyone attempting to access the manhole without the required equipment.
Another example of value engineering originated when a clash was predicted between the new storm sewer and an existing alleyway sewer. Again the Contractor and designer worked with NI Water’s operations to develop a solution which not only resolved the clash by sleeving the combined sewer within a ductile iron pipe but also reduced the number of new manholes that were required. Thus again a change of scope saved on time and cost.
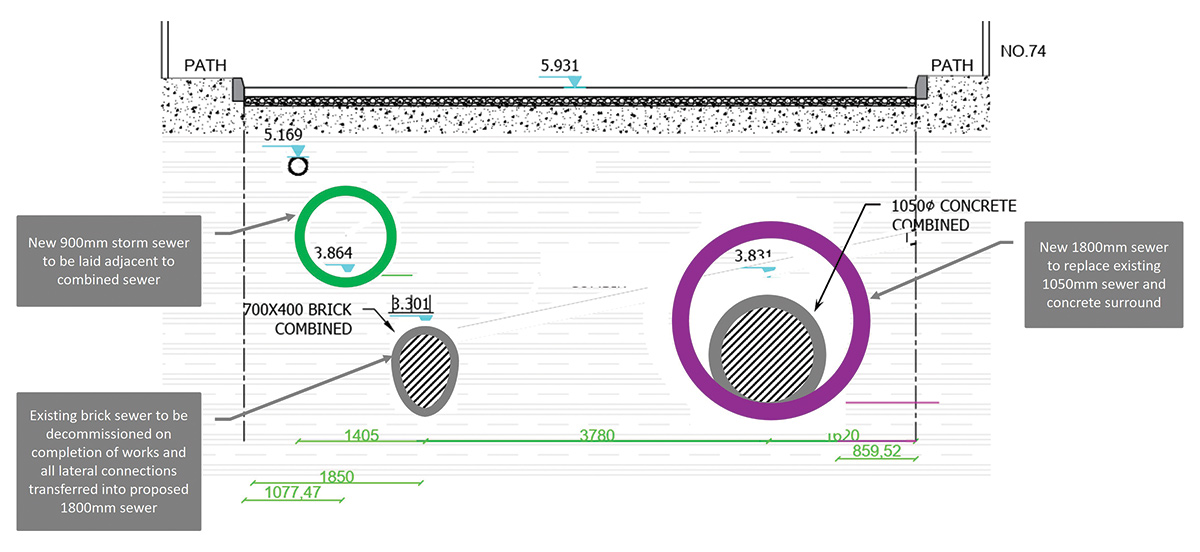
Reference design cross section sketch – Courtesy of AECOM
Construction
The initial tunnelling stage of the project was detailed in a previous article published by WaterProjectsOnline in 2022. After the tunnel was completed, the next phase was to replace the brick egg sewer which was identified to be in very poor condition, and the 1050mm combined sewer, which included a concrete surround associated with timber heading construction. These two sewers were to be replaced by an 1800mm combined sewer which would create space to lay the 900mm storm sewer required to achieve the proposed storm separation. There were many challenges with this proposal including laying a 1800mm combined sewer up to 6m deep in a narrow residential street. Also, and most notably, major flow control was needed which effectively meant building a mini temporary pumping station.
In order to minimise the risks associated with the proposed works, an early warning workshop was held between all parties. A list of alternative solutions were proposed, relevant assessment criteria selected and then each option was evaluated. From the workshop an alternative more sustainable solution was proposed which retained the existing 1050mm concrete sewer, negating the need for flow control and instead involved laying a new 1050mm concrete sewer at a shallower depth above the existing to provide the required capacity. It is estimated that the revised design saved the project £850k and at least six months on the construction programme. Again all relevant stakeholders including NI Water operations were included in the value engineering process.
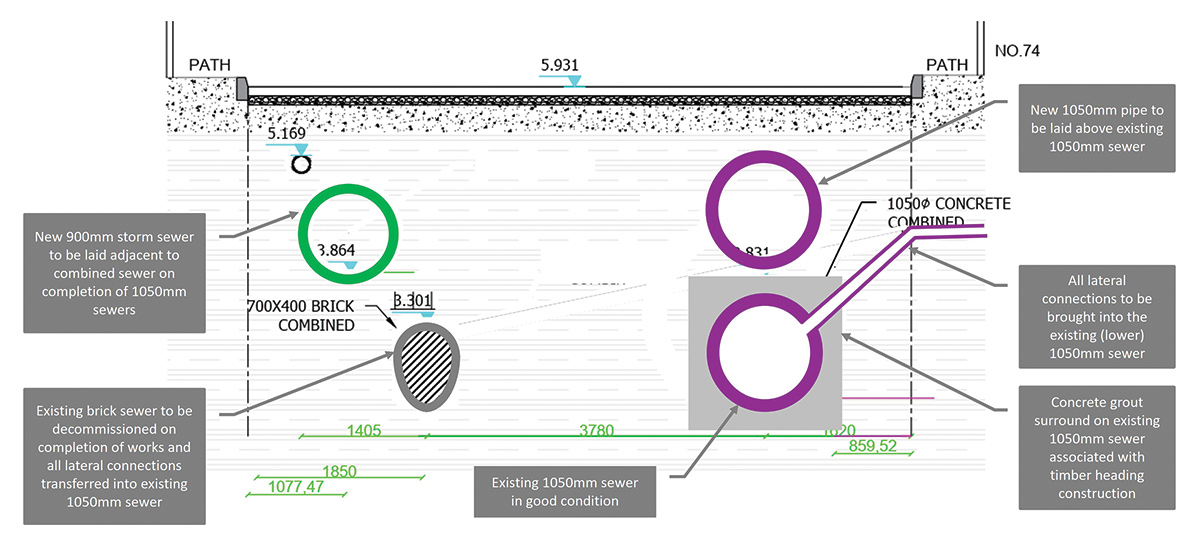
Revised design cross section sketch – Courtesy of AECOM
Ravenhill Avenue Flood Alleviation Project: Supply chain
- Main contractor: GEDA Construction
- Project & cost management: AECOM
- Civil design: McAdam
- Modelling support: AtkinsRéalis
- Geotechnical designer: Cassidy Geotechnical (Belfast)
- Civil engineering: Campbell Contracts
- Tunnelling: Active Tunnelling Ltd
- Tunnel design: BSP Consulting
- Temporary works: Groundforce
- Temporary works designer: Byrne Looby
- Precast concrete: Tracey Concrete
- Pipeline supplier: APP Fusion Group
- Metalwork: LA Steel Fabrication
- Traffic management: Graham
- Reinstatement: Breedon
- Landscaping: Annett Landscaping
- Tree surgery: JC Tree Surgery
- Fencing: Kane Fencing
- Construction materials: McNaughton & Blair
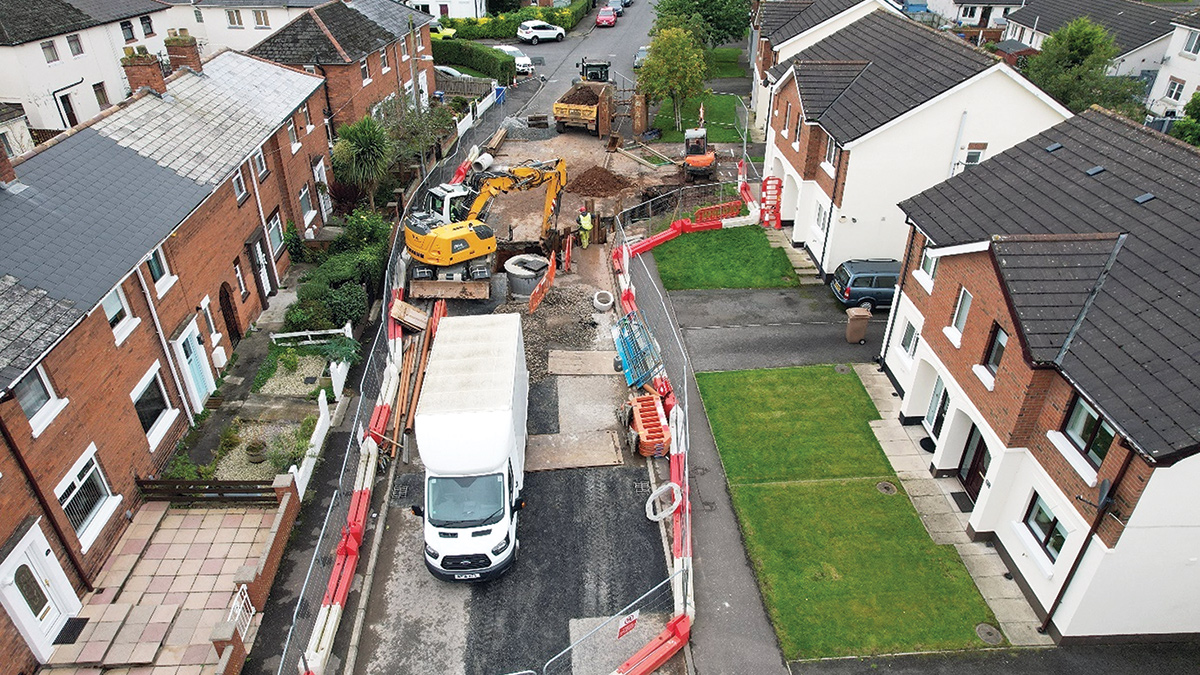
Storm separation at Millar Street – Courtesy of GEDA Construction
Delivering an Option C Contract
So what was an Option C Contract like to deliver from a contractor’s point of view? GEDA Construction, the Contractor had successfully delivered many NEC Option A and B contracts and other bespoke contracts but had limited experience of NEC Option C.
There were many learnings regarding the particulars of delivering an NEC Option C Contract including:
- Collaboration across the client and contractor team is essential for the project to work. There is full visibility of costs whether it be valuations, compensation events or value engineering proposals.
- Usually with an Option A the Contractor will draw down against a sum of money for various tasks completed on site. Instead in this form of contract, the Contractor had to get all costs from their accounting department, present these costs in the correct template for an Option C Contract and carry out a projection for the next four weeks work in each valuation. AECOM would then assess, query and certify each valuation.
- The Contractor also had to present back up for the various costs in each valuation for regular audits. In the case of Ravenhill, five interim audits were undertaken at regular intervals throughout the project. Everything was checked by AECOM, from subcontractor costs, to materials, to people and plant rates.
- Overall, the Contractor noted the use of an Option C Contract was the correct contract type to deliver this project. Compensation events were agreed in a reasonable time frame. Also, the risk is shared between the Client and Contractor creating more of a team environment. There is always the incentive of achieving gain not pain to keep everyone’s mind focused.
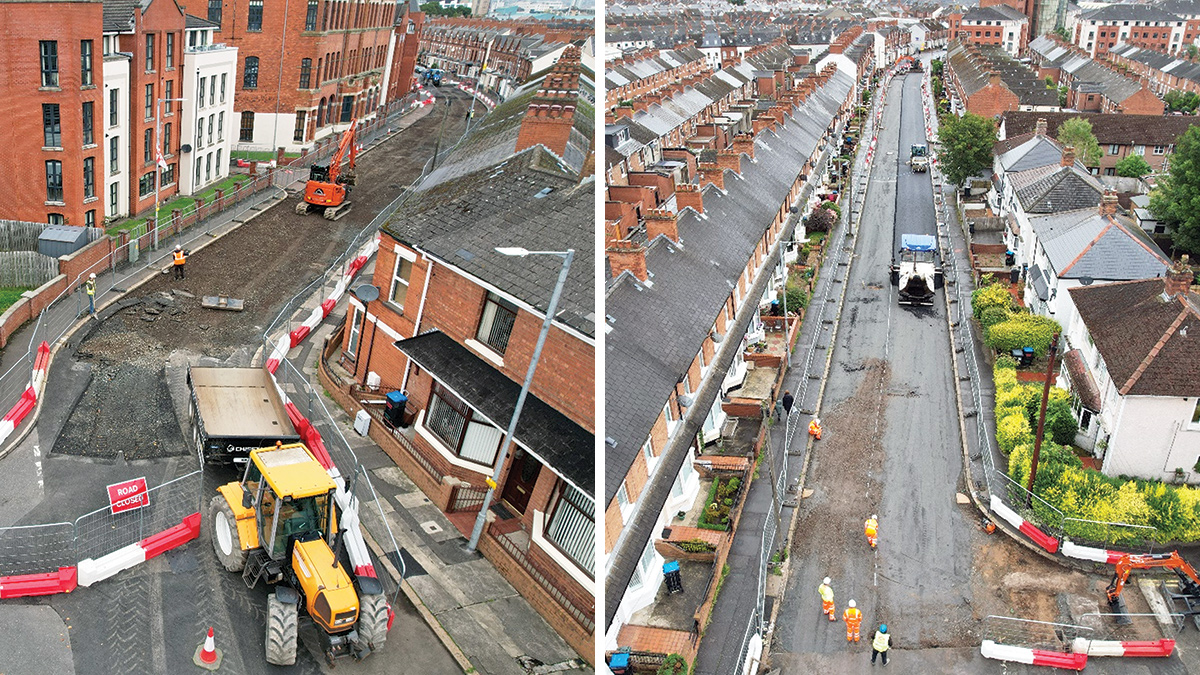
(left) Preparing for reinstatement at Bakers Court and (right) Permanent reinstatement on Ravenhill Avenue – Courtesy of GEDA Construction
Conclusion
Through good project management, successful utilisation of the NEC4 Option C Contract and collaborative working, the project team delivered a solution that met the project drivers.
- PROTECT against Flooding: Removing 11 properties from the DG5 (internal flooding) Register.
- ENHANCE the Environment: Storm separation of nine hectares of impermeable ground and return to River Lagan.
- GROW the Economy: Providing first time services (storm sewers) for 572 properties.
However, this approach delivered other benefits that set a platform upon which to build a collaborative relationship to deliver future projects:
- Health & Safety: More than 700 days accident-free.
- Stakeholder engagement: Considerate Constructors Scheme: ‘Excellent’.
- Social value/legacy: Successfully achieved through education and community involvement.
- United Nations Sustainable Development Goals: The project contributed to at least 6 goals:
- Quality education.
- Clean water & sanitation.
- Decent work and economic growth.
- Industry, innovation & infrastructure
- Sustainable cities & communities.
- Climate action.
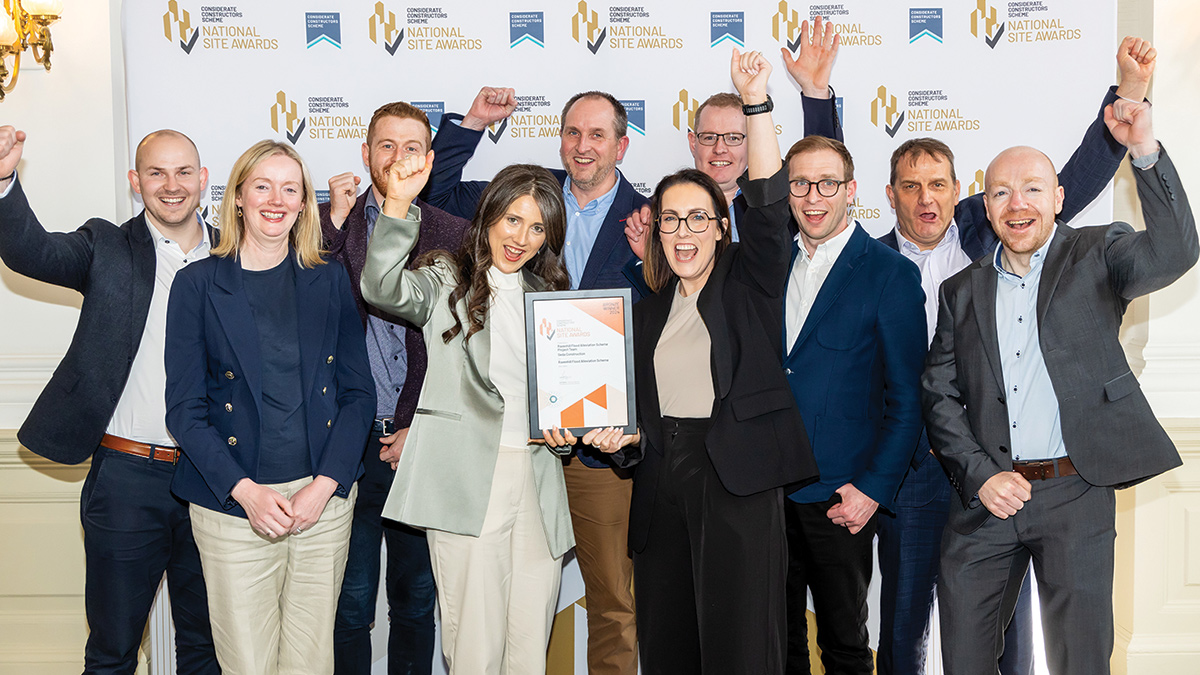
Project team receiving the CSS National Award (May 2024) - Courtesy of NI Water