Ringsend WwTP: Phosphorus Fixation (2023)
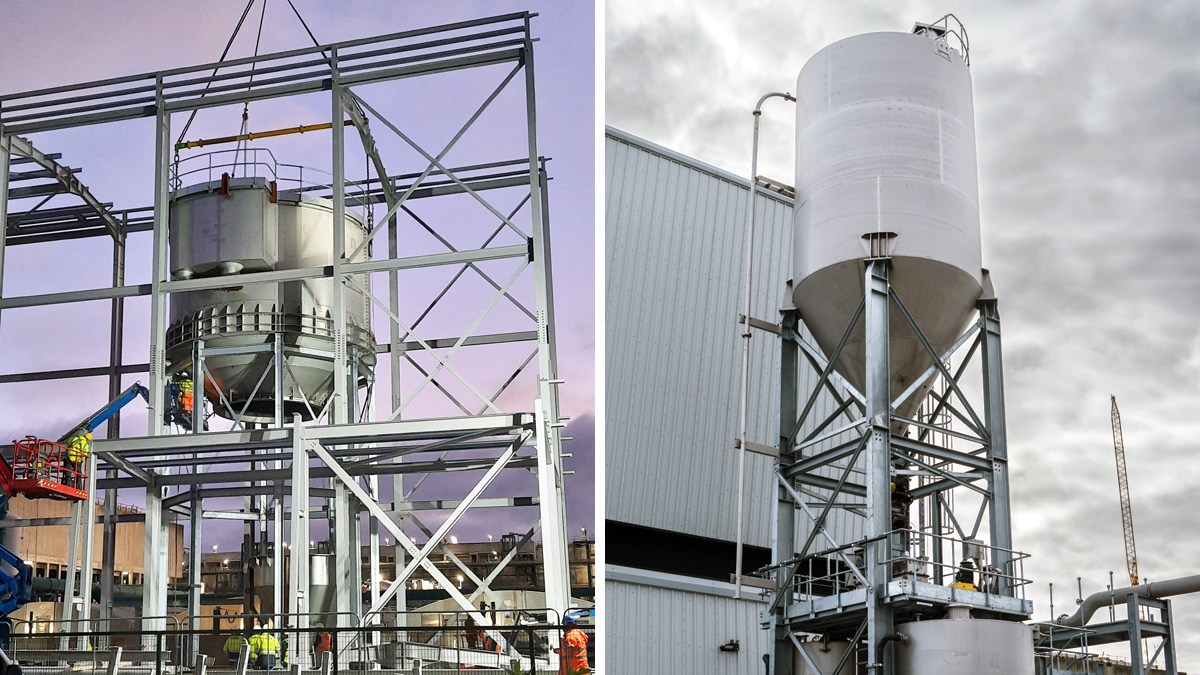
(left) Phosphorous reactor being lifted into place and (right) complete magnesium oxide storage silo - Courtesy of Murphy Ireland
Ringsend WwTP is the largest wastewater treatment plant in the Republic of Ireland that currently treats most of the wastewater arising in the Greater Dublin area; a 1.98 million population equivalent (PE) which accounts for 37% of Ireland’s 5.124 million population. Wastewater from Ringsend WwTP is discharged into the Lower Liffey Estuary, which has been designated a nutrient sensitive area under the EU directives, which requires Uisce Éireann to reduce nutrient loads of phosphorus and nitrogen from Ringsend before discharging into the estuary, which in turn feeds Dublin Bay.
Nutrient load reduction
The objective of the overall Ringsend WwTP Upgrade Project is to achieve compliance with the relevant legislation, which requires a reduction in the level of nutrients in the final treated effluent. The introduction of Nereda® and EBPR is being carried out in phased upgrades to reduce the phosphorus concentration in the treated wastewater, but to reduce the recirculation of phosphorus at the WwTP, a new treatment stream for phosphorous recovery has been installed; which is the focus of this paper.
The capacity of the upgraded plant will be ~2.4 million PE, where 1 PE is taken as 60g BOD per day. The Ringsend Phosphorus Fixation Plant is the first in Ireland to recover phosphorus from liquors generated from the dewatering of sludges arising at a wastewater treatment plant, and is the largest in Europe by reactor volume.
Murphy Ireland was responsible for the detailed design and construction of the phosphorus recovery (P-recovery) facility which features an Ostara Pearl® 10K reactor using Ostara’s WASSTRIP® technology.
This technology solves nutrient management challenges by recovering phosphorus and nitrogen (as ammonia) from municipal water streams as a magnesium ammonium phosphate (struvite) precipitate. This transforms these nutrients into a sustainable fertiliser product called Crystal Green, which is sold globally to the turf, ornamental, and agricultural markets, and is non-water soluble and thus helps to alleviate nutrient runoff from fertiliser application in addition to helping with the wastewater discharge.
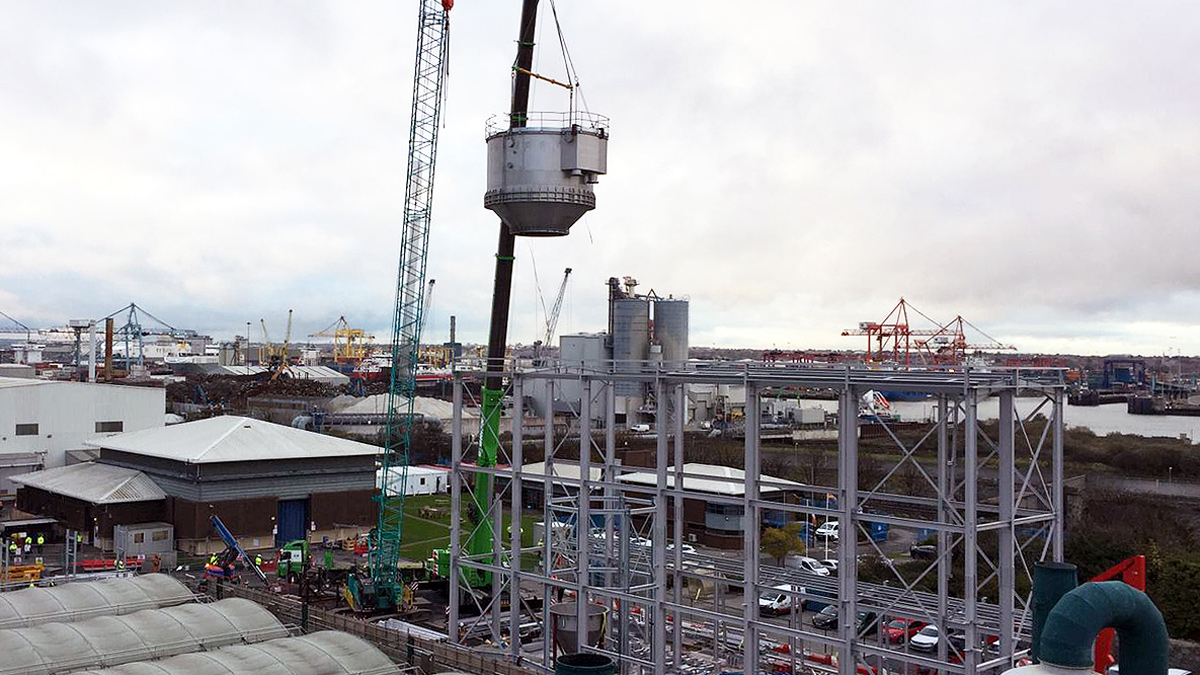
Reactor vessel lift into partially completed structural frame – Courtesy of Murphy Ireland
Ringsend WwTP – Phosphorus Fixation Project: Supply chain – key participants
Murphy Ireland undertook the roles of designer, Project Supervisor Design Process (PSDP), and Project Supervisor Construction Phase (PSCS) – equivalent to principal designer and principal contractor under CDM (2015) Regulations – for the design, construction, and operational phases of the contract.
- Main contractor: Murphy Ireland
- Civil designers: Atkins
- Nutrient recovery technology: Ostara®
- Electrical subcontractor: LDC Electrics Ltd
- MCCs: Pronto Automation Systems Ltd
- Valves: Spartan Controls Ltd
- Pumps: Grundfos Ireland
- Stainless steel tanks: Russell Metal Fabrication Ltd
- Butterfly valves: ESI Technology Group
- Gate & non-return valves: AVK UK Ltd
- Conductivity probes: Central Pump Supplies
- Pressure Transmitters: Modern Plant Ltd
- Flow meters: Endress+Hauser Ltd
- Variable speed drives: Cully Automation
- PE pipe & DI pipe: Fusion Pipeline Products
- Steel reinforcement: Midland Steel Supplies
Undertakings
The existing Ringsend WwTP is noted as providing for thermal hydrolysis, mesophilic anaerobic digestion and thermal drying of sewage sludges arising. Murphy designed and constructed the phosphorus fixation facility and following commissioning are operating the facility for a one-year period. The logistics of the site required infrastructure improvements within the treatment works to facilitate the plant and vehicle movements.
Murphy installed the new treatment streams into the existing plant without disruption to operation, with a hybrid approach of having areas of the site handed over to our possession and working under permit from the operator of the facility. The works included modifications into live treatment streams to attain connections.
These approaches are applicable to all live treatment works, regardless of technology application and is consistent with the working procedures employed on Murphy works delivery. Standard processes include HAZOP, HAZCON and ALM regular meetings between the team. The weekly meetings also included discussion on construction and plant activities to ensure everyone was aware of programme scope.
The new facility will be operated in collaboration with the main WwTP with influent sludge liquors (from pre-dryer and pre-THP) delivered to the facility at interface points with the existing works, which provide for the return of the treated liquors for onward (further) treatment at the existing works.
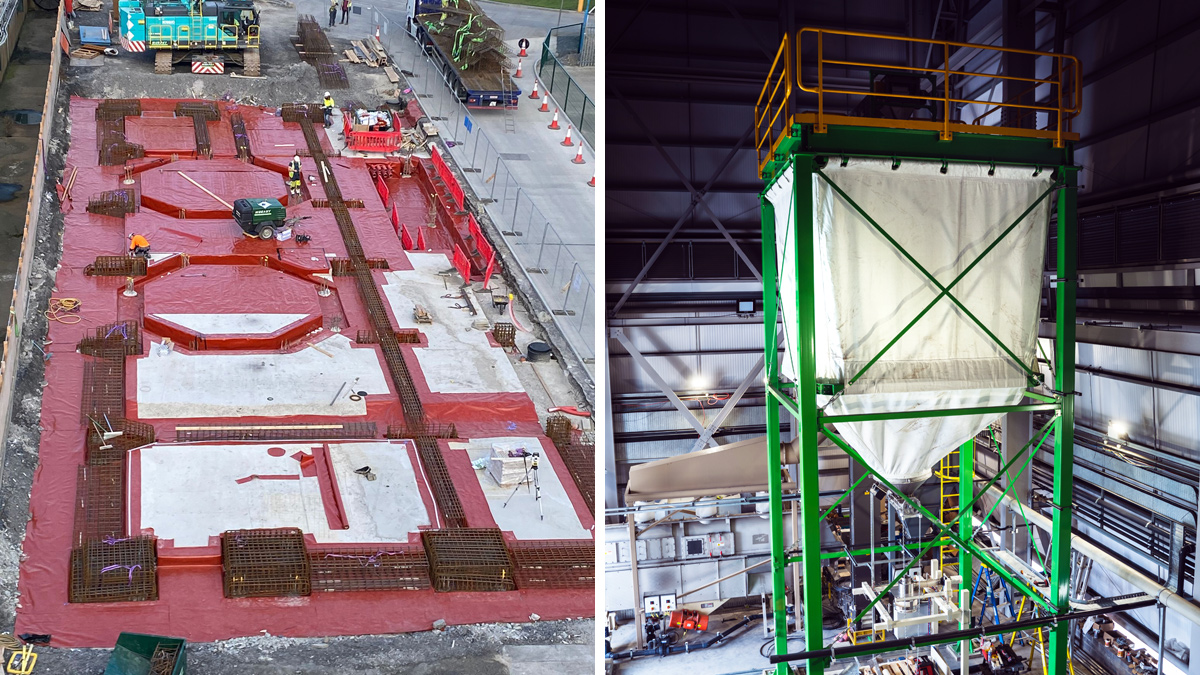
(left) Formation of plant building during radon barrier install and (right) storage silo for struvite product – Courtesy of Murphy Ireland
Scope of works
The scope of works was for the design, construction, installation, commissioning and operation of a bespoke P-fixation and recovery facility, as well as ancillary equipment, pipework, electrical installation and ICA systems. In addition, Murphy was responsible for:
- The design and construction of storage facilities for bulk chemicals (60 tonne magnesium oxide (MgO) storage) and for the recovered struvite product.
- Facilities for heating, cooling, air supply etc. The building was designed to passively ventilate, based on the analysis of the equipment being used and the level of thermal generation from processed reactions. Based on this, the cooling system was designed, to reduce instances of working from height and maintenance of the equipment and services.
- Within the building there was a welfare unit which was considered a habitable building under the Building Regulations, and it was designed considering all guidance presented, including Part L (energy efficiency) achieving a BER rating of B.
- The construction, re-alignment and upgrade of buildings, roads, and other civil engineering works for the above works and for ancillary facilities for the different items of units/equipment.
- Welfare facilities for operation and maintenance staff using the existing data infrastructure to be able to integrate the intelligence system from our project into the wider site network.
- Works outside of the main P-Fixation facility to intercept and deliver sludge liquors to the facility retrofitting pipework onto equipment in the wider treatment works (existing centrifuge and drainage pipework) to divert flow to the facility.
- Significant structural steelwork fabrication, which included a 30-tonne stainless steel reactor that is 19.8m above existing ground level.
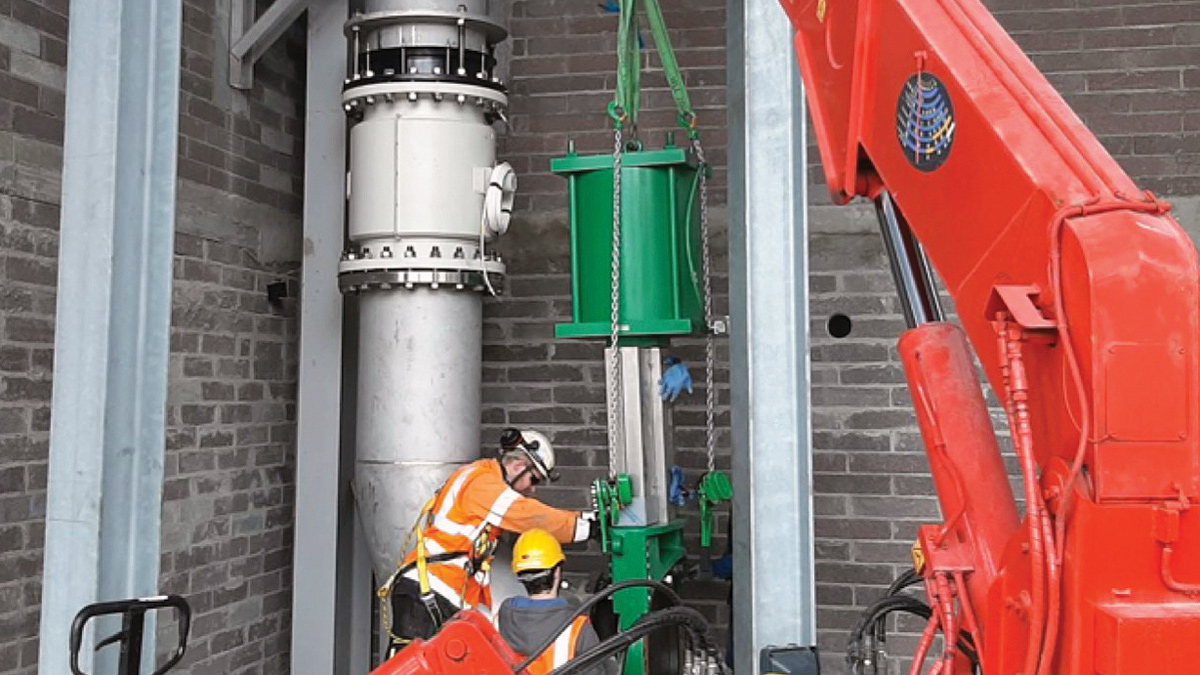
Installation of DN600 knife gate valve on recirculation line – Courtesy of Murphy Ireland
Pre-commissioning works
A pre-commissioning plan was created early for approval by Uisce Éireann, which then developed during the works. This included six-weeks of individual component testing with a further six-weeks of point-to-point testing, followed by a 28-day testing period to include 14 day autonomous test.
Prior to commissioning, Murphy undertook several months’ worth of laboratory testing to fully understand the product and to confirm expectations. Findings suggested that the water was too sediment-heavy, so the strainers were adjusted to accommodate the need.
Fabrication in Ireland
All fabrication manufacturing was carried out in Ireland, which significantly reduced the associated carbon emissions from the transportation of the steel. Wherever possible prefabricated steel was used, and Murphy engaged early with the supply chain for the rebar, Ostara® reactor, concrete tanks, stainless tanks, and pipework.
The Ringsend reactor weighed 30-tonnes when empty and arrived on site in five separate fabricated pieces. It was assembled outside the main process building and then craned in through the roof. This method of fabrication was the first of its kind for an Ostara® reactor.
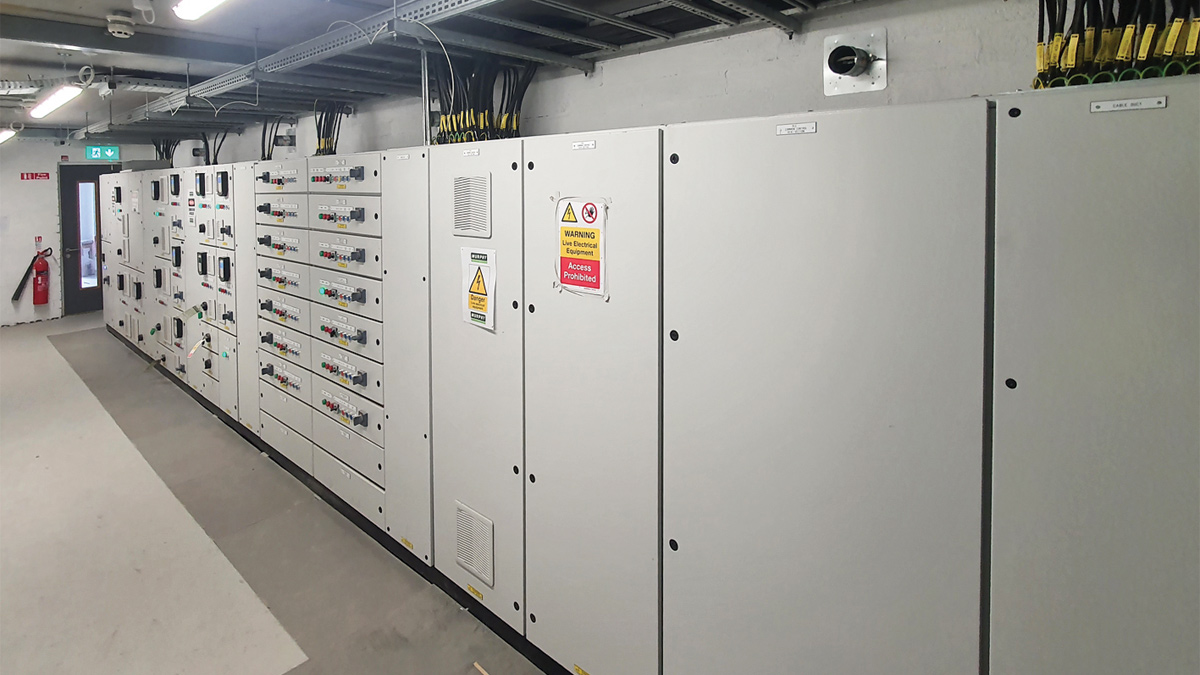
Completed MCC unit – Courtesy of Murphy Ireland
Environmental successes
Murphy engineered outstanding achievements in technical design and environmental sustainability, accomplishing low environmental impact of, and maintaining the ecological balance for Dublin Bay and the surrounding coastline.
A small area located between the principal wastewater treatment plant and the storm tanks to the north of the site was designated as a zone of archaeological interest. Monitoring was carried out through the construction stages to ensure the works did not disrupt or cause damage to anything in this protected zone. An invasive plant species specialist was also engaged to undertake a pre-construction survey. There were reports of Japanese knotweed being present on the treatment works, and if it was also encroaching into the working area then it would need to be removed – which is a lengthy and costly process – and then control measures would have been required.
Successful delivery
Collaborative working was a key facet of the approach and of success. The works were within the strict confines of the existing, and very busy, live wastewater works, therefore Murphy had to collaborate with a multitude of contractors who were working on site at the various phases of the project. Priority was given to the existing contractor on the live plant and Murphy worked with them to ensure that there was no disruption to the daily operations and undertook the phosphorus fixation works by putting in road crossings and by working during nights and weekends.
Traffic management was meticulously planned and managed, ensuring no interference to the existing plant operators.
Despite the challenges presented by Brexit and Covid-19, the project remained on programme. The programme was managed through hosting regular collaborative meetings with Uisce Éireann; including a meeting at month-end and midway through the month to determine progress, and set up the plan for the month. The team also maintained a three-week look-ahead and master information delivery plan (MIDP) outlining when sub-tasks and documentation could be completed. Primavera P6 project programme software was utilised, providing the team with clearly presented data.
The approach to Health & Safety on the project was positively received, with 21,837 hours worked with no reportable incidents.
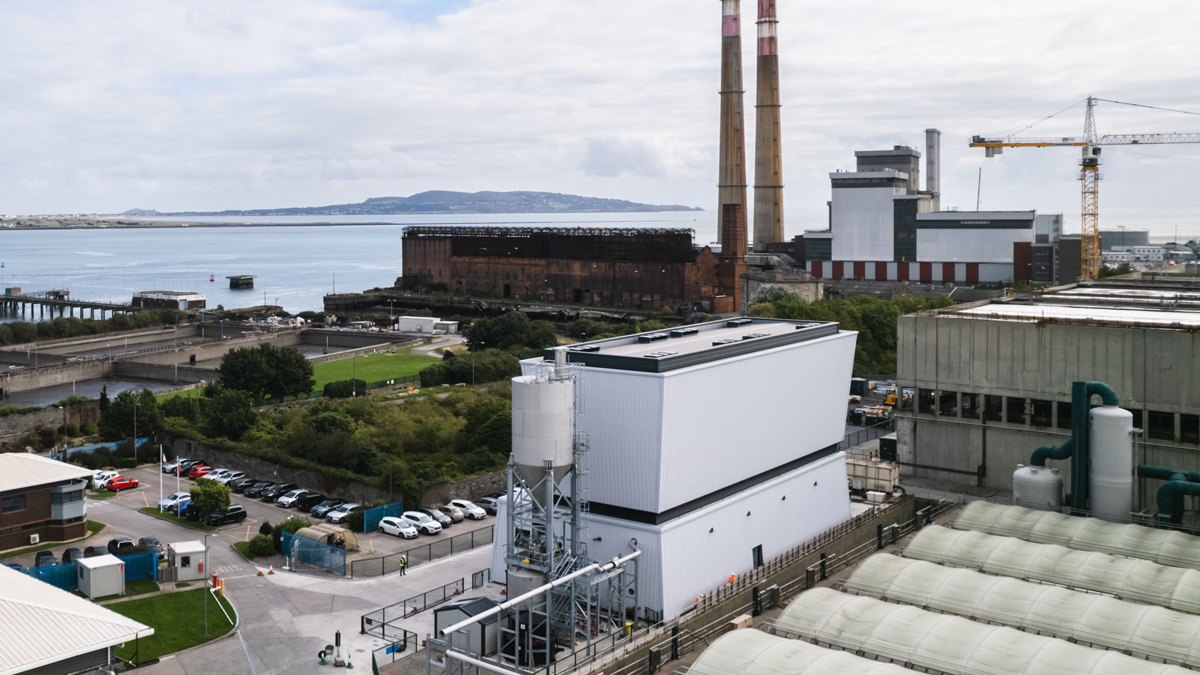
Completed building within the plant confines – Courtesy of Murphy Ireland
Sustainable manufacture
A circular economy method was used to remove nutrients from being discharged to the watercourse. The entire project was based on the sustainable manufacture of fertiliser and during the design stage, to maximise off-site prefabrication, BIM was used to undertake the modular fabrication process, mirroring the procedures outlined in ISO 204000.
Meeting Uisce Éireann’s customers’ needs
The Ringsend WwTP Phosphorus Fixation Project provides a major contribution to recreational amenity features of Dublin Bay.
The advanced treatment process now happening will ensure that the final effluent being discharged into Dublin Bay is the highest quality and complies with EU standards maintaining water quality in the surrounding area.
This project is the first of its kind in Ireland and is the largest in Europe by reactor volume. It involved the use of innovative technology to sustainably remove phosphorus from the wastewater being treated at Uisce Éireann’s largest wastewater treatment plant.
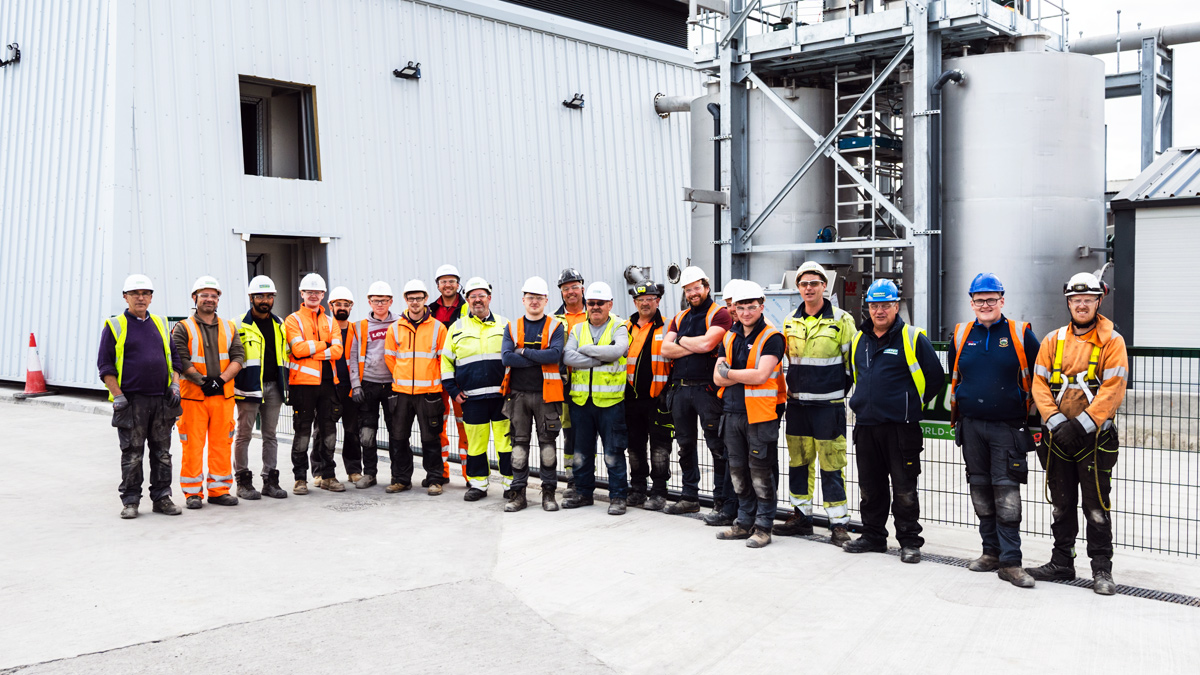
Murphy team during electrical commissioning – Courtesy of Murphy Ireland