Royton WwTW (2018)
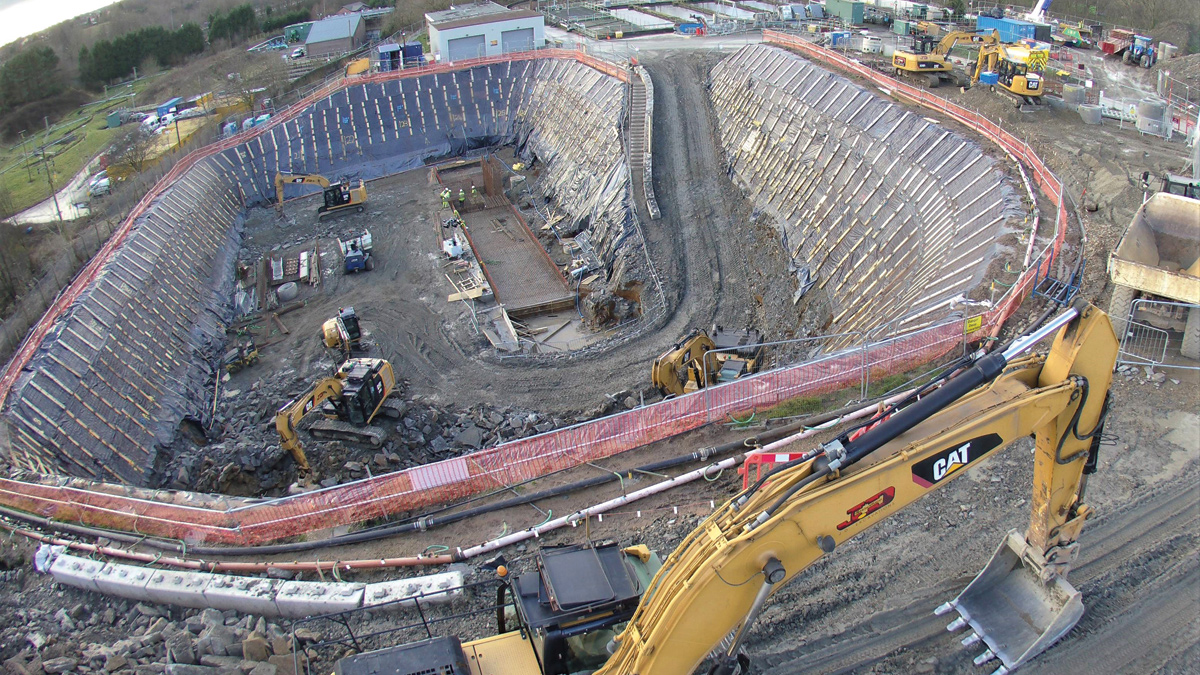
Excavation through rock close to formation level - Courtesy of Farrans Construction
Oldham and Royton WwTWs, operated by United Utilities, are located approximately 4km apart, close to Manchester. The WwTWs were aging facilities, and in need of an upgrade for the river water quality to meet European standards, and to serve an increasing population of over 185,000. United Utilities considered various options to improve the wastewater treatment in the area as part of a feasibility study. The study concluded that the Oldham site would be upgraded significantly to handle additional treatment capacity as a result of decommissioning some treatment facilities at Royton. New infrastructure was required at the Royton site including a new stormwater detention tank (storm tank). This would enable the effluent and storm water to be transferred to Oldham via a new 600mm diameter pipeline. The estimated cost of the Oldham Royton Integration Strategy (ORIS) was £80m.
Introduction
Black & Veatch was awarded the contract for the project and sub-contracted the civil works for the pipeline and for the Royton site to Farrans Construction Ltd. The storm tank formed a major part of the works and had dimensions measuring 47.7m by 21.8m in plan with a height of 10.5m. The ground level at the site ranged from 136.0m OD to 130.0m OD with the excavation level at 120.4m OD.
OGI Groundwater Specialists Ltd (OGI) was appointed to provide design and engineering services for the construction engineering (temporary works) to enable the construction of the storm tank. This article describes the simple but novel methodology OGI devised, to incorporate low cost building materials and negate specialist sub-contractors for the construction engineering.
Site conditions
The ground level across the site was inclined towards the south-east by around 6° towards a deeper bowl feature outside the site boundary. The existing wastewater treatment works remained live during the construction works and restricted the extent of the excavation. The existing combined sewer overflow (CSO), 5m box culvert and manholes had to be considered as part of the design in order to avoid clashes with reinforcement and to prevent settlement.
During construction, Victorian pipework and a demolished tank were discovered which were otherwise unknown. In addition to the existing structures, plant and machinery were considered, including mobile cranes, concrete pump trucks, dump trucks and excavators.
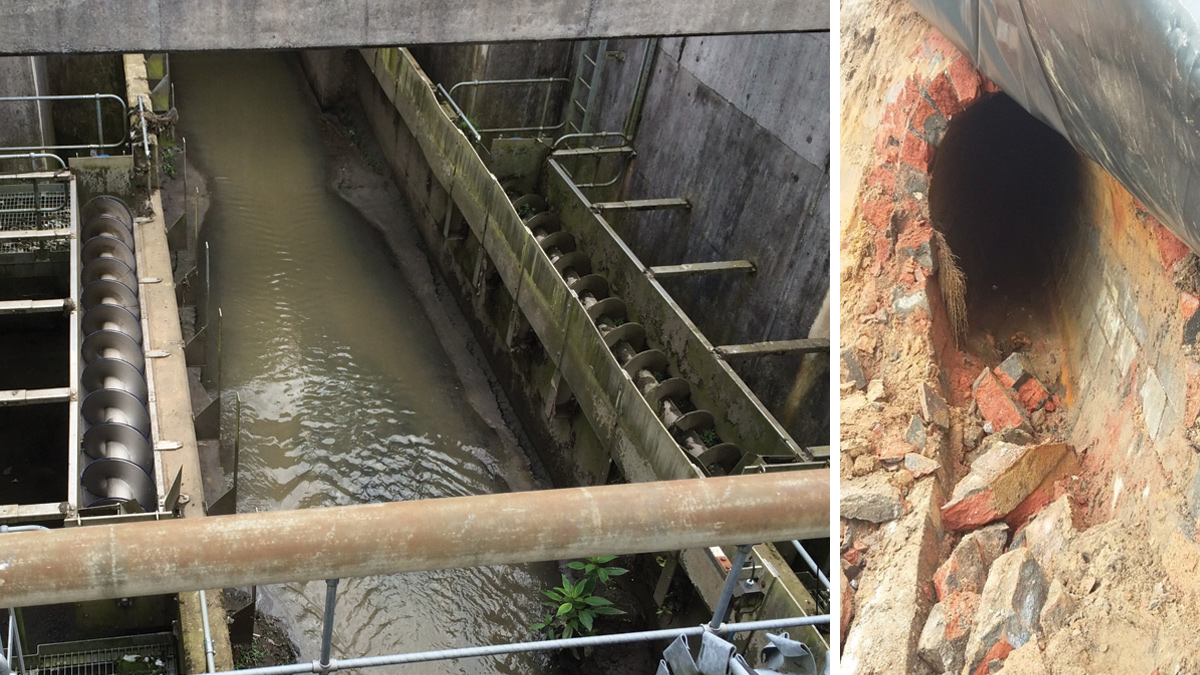
(left) Existing live infrastructure combined sewer overflow – Courtesy of OGI Groundwater Specialists Ltd and (right) Victorian buried pipe – Courtesy of Farrans Construction
Ground conditions
The ground conditions at this site generally comprised a 2m layer of Made Ground, underlain by a layer of glacial till approximately 4m to 6m thick, underlain by weathered and intact rock.
The made ground was characterised by gravelly clayey sand to soft sandy gravelly clay, generally poorly compacted and of low strength. Where the water table was encountered within the made ground, it was of very low strength and running sands were encountered.
The glacial till comprised interbedded layers of medium dense sand and firm clay. The borehole information available suggested the layering within the unit was non-uniform and therefore both drained and undrained parameters were selected for slope stability purposes.
Borehole descriptions suggested the intact rock was strong, but locally medium strong, closely fractured sandstone, siltstone or mudstone. The overlying weathered rock was very weak and crumbled under a firm blow from a geological hammer.
The water table was encountered at a depth of approximately 4m below ground level (bgl) and was observed to flow from bedding material and surrounding structures.
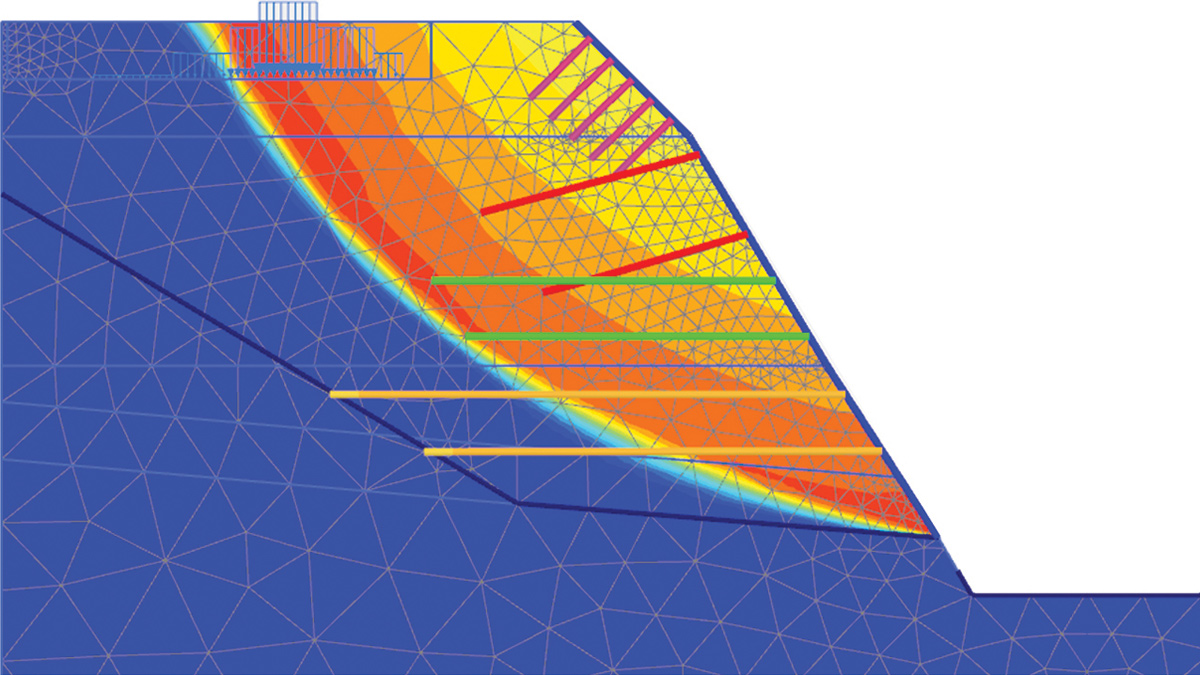
Displacement field from PLAXIS 2D modelling – Courtesy of OGI Groundwater Specialists Ltd
Design solution
Achieving the formation level for the storm tank required excavation to depths between 9m and 14m. Forming a retaining wall using contiguous, secant or sheet pile methods were considered unfavourable due to the high costs, high rock level and potential requirement for propping. The tender design method utilised a soil nailed and Shotcrete solution using specialist contractors which did not offer the flexibility to negotiate the existing live structures and was again considered poor value for these temporary works.
OGI offered its cost-effective Stable-Earth service to construct stable engineered slopes by incorporating three key techniques:
- Theoretical modelling to simulate the earth and groundwater behaviour in order to quantify the requirement for groundwater control and earth reinforcement.
- A physical groundwater control system to reduce pore water pressure. This has the effect of reducing the destabilising forces on the slope.
- A physical earth reinforcement system to provide additional strength to the soil mass. This increases the stabilising resistance of the slope.
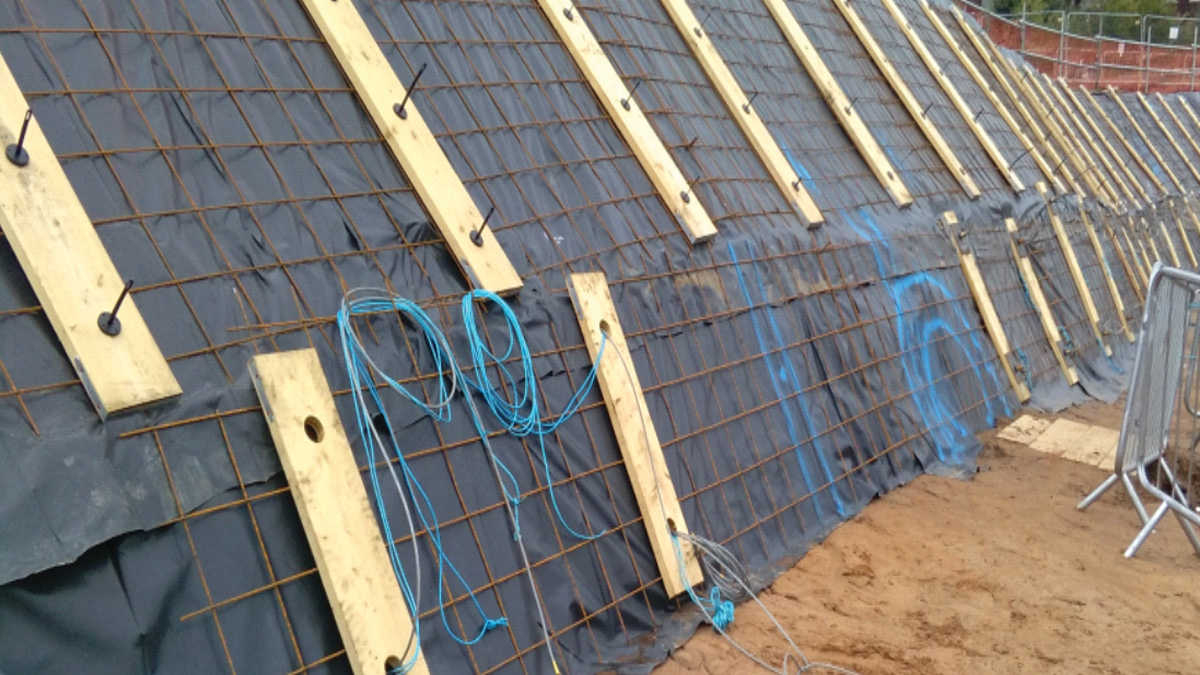
Phase 2B showing make-up of reinforcement system – Courtesy of OGI Groundwater Specialists Ltd
The proposed solution was an inherently flexible approach that enabled OGI’s design engineers to modify the earth reinforcement system as necessary for the ground conditions and site geometry encountered.
The materials selected for the slope stabilisation were chosen due to their availability and cost-effectiveness. The materials which composed the Stable-Earth service included:
- Platipus ground anchors of varying size and length to reinforce the batter.
- Polythene sheeting to prevent erosion due to rainfall.
- Timber walings and steel mesh to spread the anchor load and hold down the polythene sheeting.
- Nylon wick drains to enable passive drainage and pore pressure reduction from the ground.
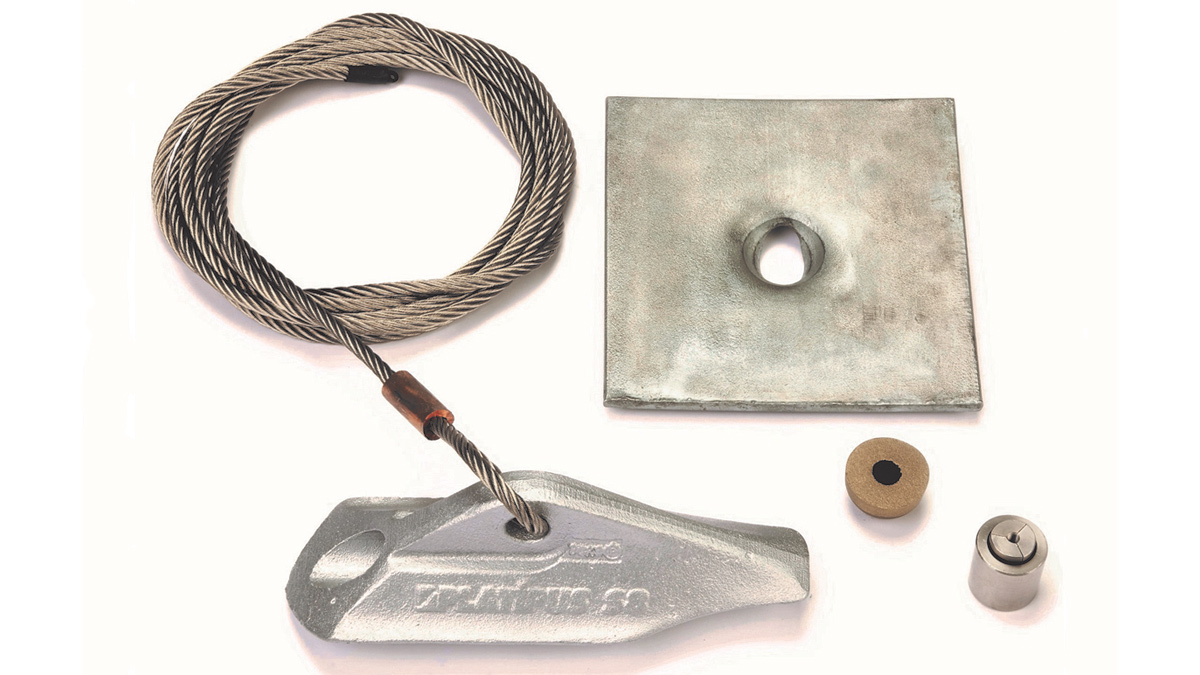
Platipus anchor – Courtesy of Platipus Anchors Ltd
Design
As part of the Stable-Earth system, the groundwater control system was specified to be installed by dewatering contractor, Alba De-Watering Services Ltd. The groundwater control system comprised a suction system to achieve a drawdown of up to 4m below initial water table (8m below ground level). Groundwater control wells were supplied by Boode UK together with a designed sand filter in order to extract clean silt free water from the ground. This was to meet the Environment Agency standards in case the groundwater was discharged directly to the local watercourse, and to prevent potential for ground loss. To mitigate the risk of pump failure, passive drainage was specified in the form of nylon wick drains installed with each individual ground anchor.
The flexibility of the Stable-Earth system enabled variable loads associated with cranes and concrete pumping plant at the perimeter of the excavation, and dumper trucks on the access ramp to be accounted for. To enable safe operation of the plant, working platforms were designed in accordance with BRE 470 (Working Platforms for Tracked Plant) for lifting mats and for the haul road.
In both cases Maccaferri needle punched geotextile and gravel fill were used to provide the required stability. Where working platforms were not required, exclusion zones were cordoned-off to prevent elevated loads within 4m of the batter tops.
To design the batters in accordance to Eurocode 7, PLAXIS 2D finite element software was utilised. This software enables complex geometry to be assessed and can account for the failure mechanism of the soil around the anchors, strength of the cable and pre-stressing of the anchor. A number of models were developed depending on the constraints around the perimeter of the tank and the anthropogenic hazards encountered.
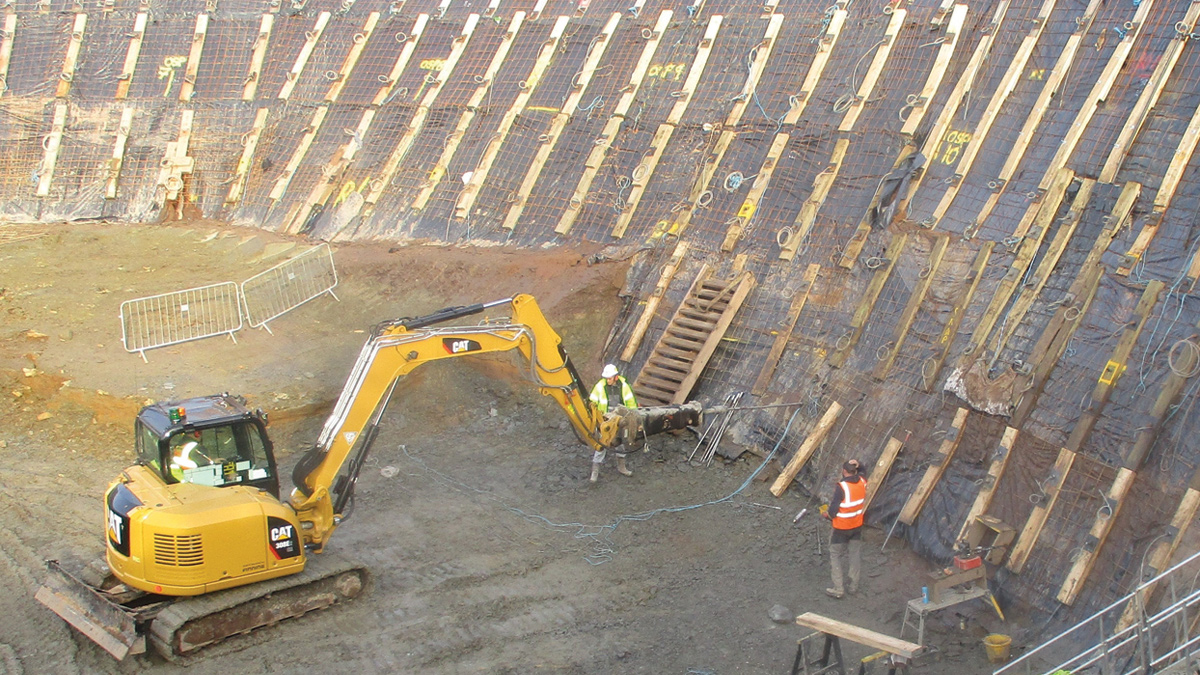
Installation of a Platipus Anchor – Courtesy of OGI Groundwater Specialists Ltd
For each phase, the design approach was typically characterised by:
- Conceptual Model 1 (CM1): Accounted for the site constraints in each particular area, slope geometry and expected geology to be encountered.
- Conceptual Model 2 (CM2): Attributed design parameters to the slope geology and included a reinforcement system and benefits of the groundwater control system.
- Mathematical Model: Presented the simulation of the CM2 model using PLAXIS 2D, including presentations of displacements (serviceability limit state) and utilisation (ultimate limit state).
- Construction Sequencing: Presented the sequencing and specifications for the Stable-Earth system. This enabled the decisions of the design team to be clearly conveyed to the construction workers. Details included the material descriptions, Phase levels, anchorage requirements and other pertinent information. These drawings reduced the requirement for the designer to attend site.
- Design Certificate: A 3-page document to detail (i) the purpose of the design (ii) sources of information, and (iii) the output documents.
To ensure the designs were implemented as intended, an Inspection, Testing and Maintenance Plan (ITM Plan) was issued to the contractor.
This included procedures for inspecting and reporting the anchor load capacity back to the designer, testing of the groundwater control system and settlement monitoring, amongst other activities.
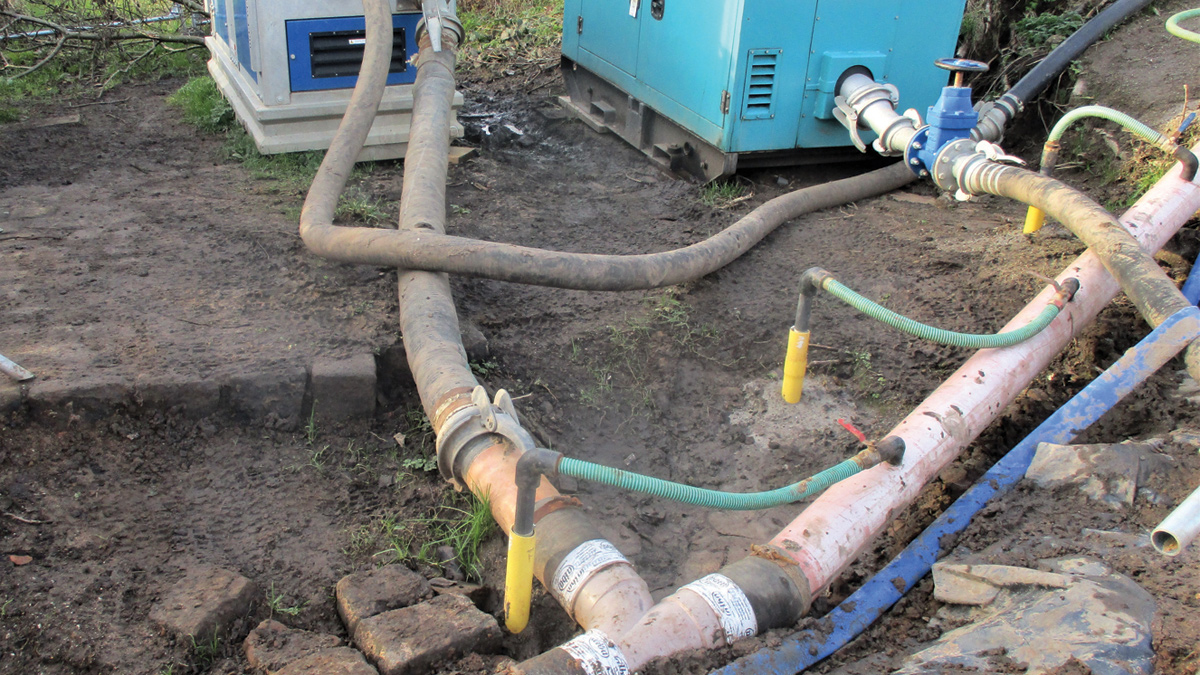
Groundwater control system showing suction wells and header pipe – Courtesy of OGI Groundwater Specialists Ltd
Installation
The groundwater control system was installed by Alba De-Watering using augering techniques. Wells were installed at a spacing of 1.5m around the perimeter of the excavation from existing ground level down to rockhead. This system reduced the pore water pressure within the slopes, increased the strength of the soils, and therefore reduced the anchor requirement and reduced the risk of running sand. The groundwater control system was installed and commissioned within around two weeks.
The earth reinforcement system was installed by Farrans Construction’s sub-contractor, JD Excavations. After two days training from both Platipus Anchors and OGI Groundwater Specialists, JD Excavations was able to install the system, including installing and tensioning of the anchors. A specialist contractor was not required to install the system thereby reducing the cost of the temporary works.
Challenges arose when existing structures had to be restrained from ground movement. OGI’s Stable-Earth service was particularly well suited to the bridging over of existing infrastructure. With careful and detailed design, live pipelines and a manhole were protected as part of the slope stabilisation works.
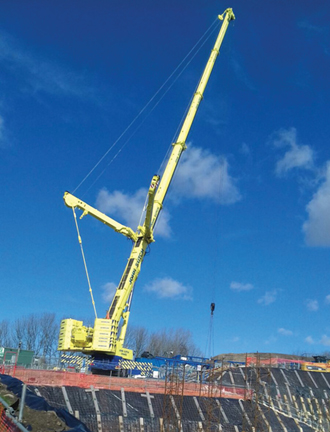
Operation of 350t crane at the top of the batter – Courtesy of Farrans Construction
During tensioning of the anchors, a maximum load was recorded and relayed to OGI. This enabled OGI to make adjustments to the design of the subsequent phases by identifying stronger or weaker areas of ground than expected. This feedback process enabled an efficient design to be employed and reassurance that expected ground conditions were being realised on site.
Royton WwTW – Storm Tank Slope Stabilisation Project
- Client: United Utilities
- Project delivery contractor: Black & Veatch
- Main contractor: Farrans Construction Ltd
- Designer: OGI Groundwater Specialists Ltd
- Sub-contractor: JD Excavations
- Dewatering contractor: Alba De-Watering Services Ltd
- Anchor supplier: Platipus Anchors Ltd
- Geotextile supplier: Maccaferri
Conclusion
The construction of the new storm tank at Royton WwTW required short-term temporary works to form the slopes. The Stable-Earth system provided a low-cost alternative to more traditional excavation methodologies, without sacrificing the safety of the works.
The cost savings were largely achieved by negating the appointment of a specialist contractor, and the use of low-cost materials such as ground anchors, scaffold boards and steel mesh.
The high quality in the delivery of the excavation designs included detailed construction sequencing drawings supported by geotechnical modelling in accordance with British Standards and Guidelines. Negligible monitored settlements demonstrated that the Stable-Earth system was robust and also flexible enough to bridge and secure existing infrastructure.
By offering a phased approach for the construction works, excavation commenced within two weeks of OGI’s contract award. Designs for further phases were provided ahead of the excavation works and incorporated anchor load results to optimise the designs.
The use of OGI’s Stable-Earth service for this large-scale infrastructure project has demonstrated the viability of using cost effective, durable materials to stabilise steep batters for temporary excavation works, particularly where a high water table is encountered.