Seedy Mill WTW (2023)
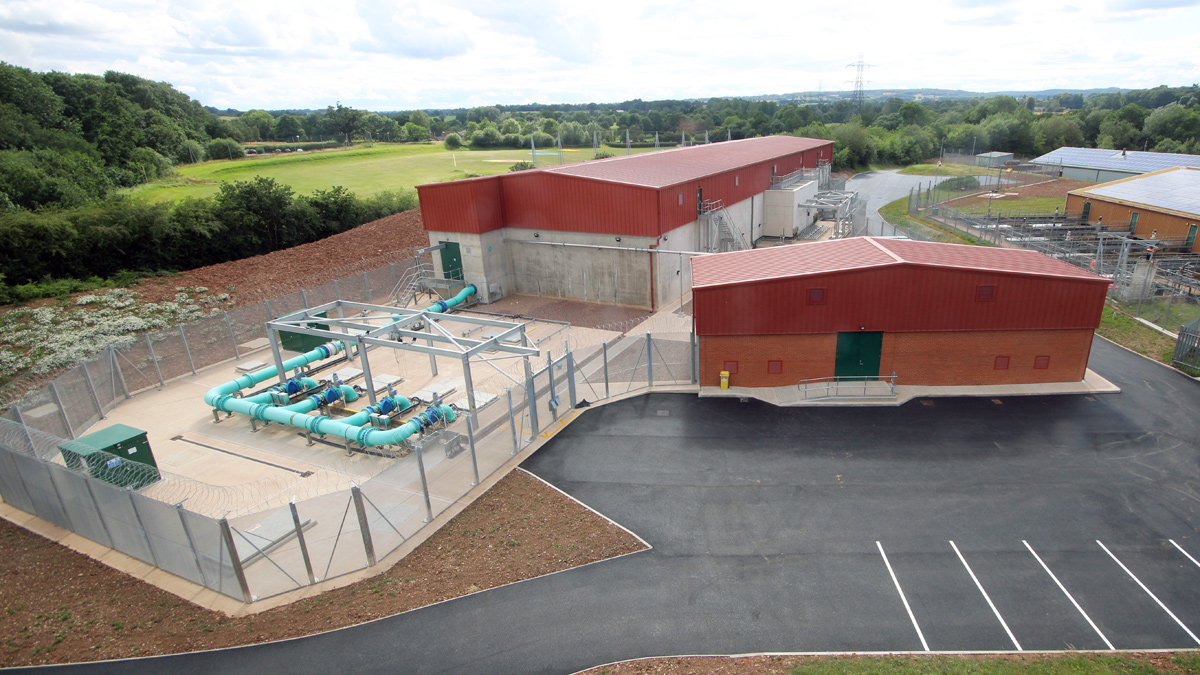
Rapid gravity filters, clean water backwash tank and MMC (by Lobster Pictures) - Courtesy of Galliford Try
Seedy Mill WTW treats surface water from the Blithfield Reservoir. The existing supply to the works is gravity-fed up to a maximum of 85 MLD. Additional yield could be provided by utilising three in-line booster pumps located at Nethertown. In addition, there are two individual borehole contributions at Seedy Mill and Trent Valley, which can be introduced at various stages throughout the treatment process. The Water Resources Management Plan confirms maximum flow is 110 MLD (with or without the borehole yields), although the treatment capacity is 115-120 MLD dependent upon raw water quality. Flows through the existing plant are highly variable with minimum flows as low as 20 MLD. This tends to occur during Blithfield Reservoir conservation periods. Daily demand increases from 20 MLD to 110 MLD can be achieved with an average of between 50 and 110 MLD in six hours.
Existing works
The existing treatment works includes clarifiers with poly-aluminum chloride coagulant, polyelectrolyte, and sulphuric acid dosing. There are two clarifier streams, one with four accelators and one train with four Dissolved Air Flotation (DAF) streams. Chlorine is added seasonally to the clarified water before it enters several banks of rapid gravity filters. Next, the water passes through chlorine contact tanks, before being subjected to ultraviolet light irradiation, and then pumping to distribution. Filter-to-waste flows are decanted to the head of the DAF and are limited to 5% of the DAF flows.
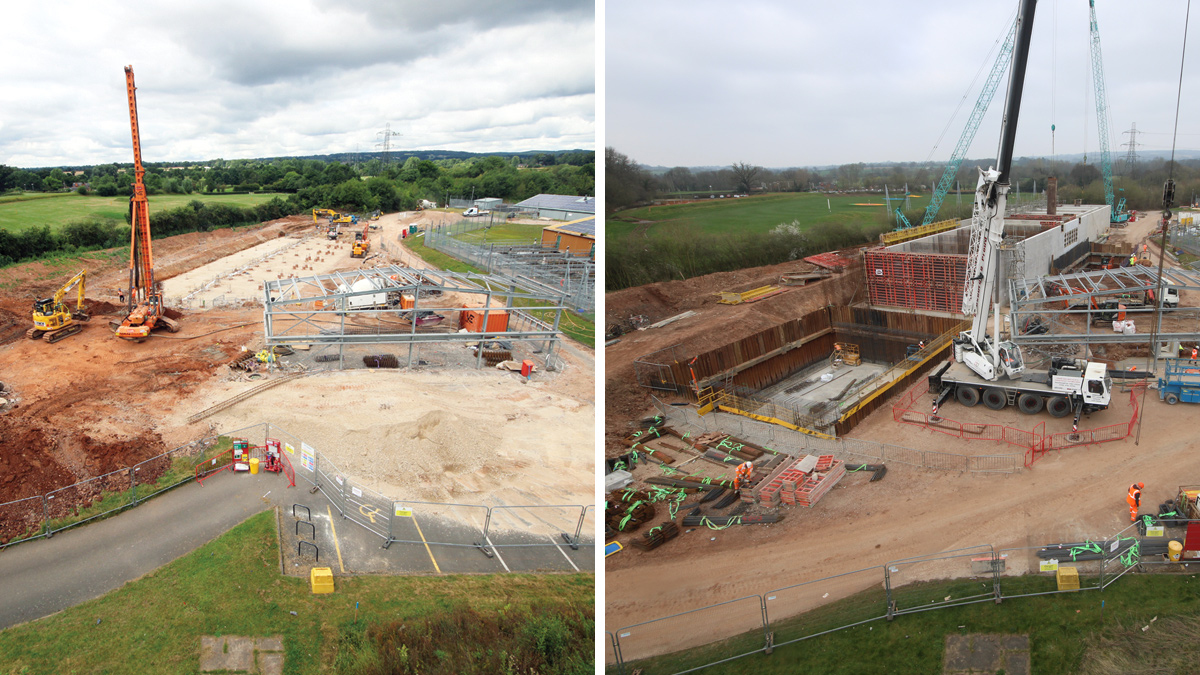
(left) Piling works for the RGF building and (right) construction progress March 2022 (photo by Lobster Pictures) – Courtesy of Galliford Try
Project driver
In 2019, following a Drinking Water Inspectorate (DWI) assessment of Seedy Mill WTW, South Staffs Water was required to review and revise and/or make operational the construction, installation and commissioning of an additional filtration stage or other agreed solution to reduce total trihalomethanes and other disinfection by-products.
Recommended solution
Two options for additional filtration were identified by South Staffs Water; Rapid Gravity Filters (RGF) and a ceramic solution. In May 2020, RGFs were chosen as the preferred option, with associated upgrades to the existing sludge treatment processes to deal with the additional expected dirty washwater.
This solution satisfies the criteria laid down within the DWI notice, ensures the plant will consistently deliver all the required water quality parameters, and improves the capacity, performance and resilience of the sludge treatment system.
Following Early Contractor Involvement (ECI) works, South Staffs Water issued Galliford Try with an NEC Option C contract for £21m for the detailed design and civil and MEICA construction of the new filtration stream and sludge treatment upgrades. These were required to be installed and commissioned before the Regulatory Date of 31 March 2023.
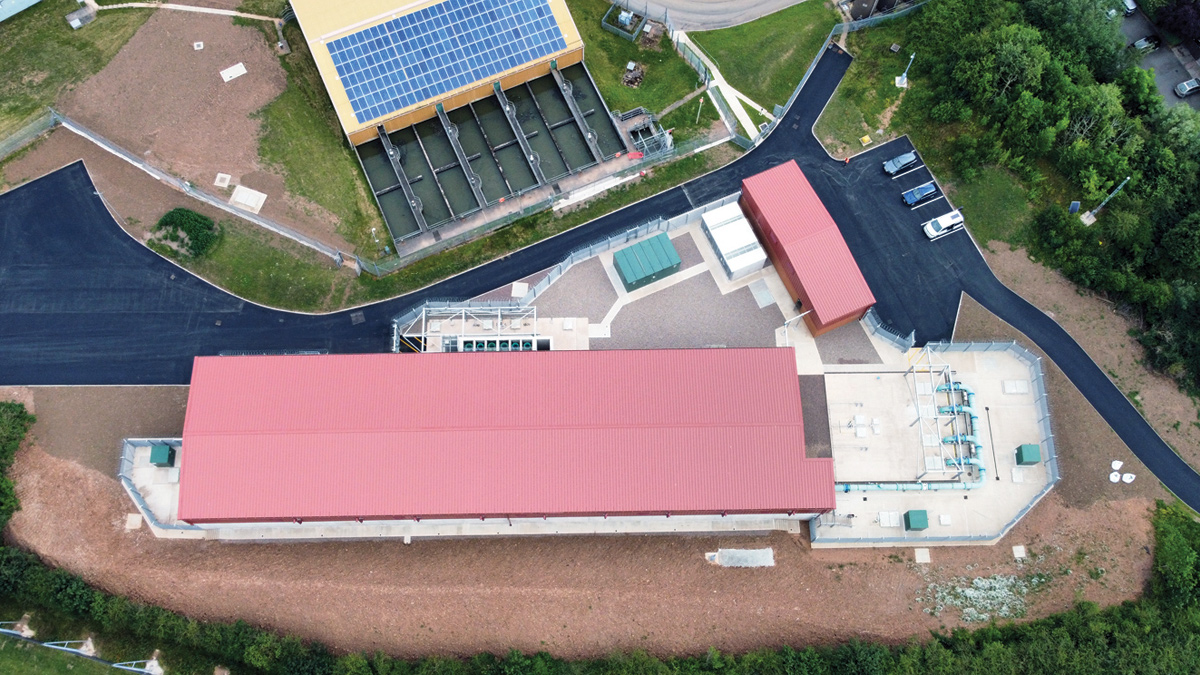
Clean water backwash tank, interstage pumping station and rapid gravity filter building – Courtesy of Galliford Try
RGF treatment stream – project scope
- Ten new RGF cells with treatment capacity of 120 MLD.
- Common pipe gallery.
- 1000m diameter inlet and outlet process pipework.
- Interventions to connect new RGF process stream.
- New clean backwash tank and pumps.
- New Intermediate Pumping Station (IPS).
- Re-purpose the existing structural frame of the disused bottling plant to reduce the use of new materials.
- New MCC and systems integration.
- Transformer compound.
- Portal frame and cladding over RGF and MCC/blower building.
- Security enhancement works, including perimeter fence.
Sludge works – project scope
- New sludge holding tank.
- Two new Alfa Laval (Aldec 105) centrifuges to replace existing – duty/standby phased changeover.
- Duty/standby poly make-up and dosing systems.
- Sludge conveyors.
- Building extension to house new centrifuges.
- New MCC.
- Modifications to existing Opus SCADA system.
- Removal of existing plate press/centrifuges and existing MCC.
- The sludge feed of 12m3/hr @5% changed to 15m3/hr @3%.
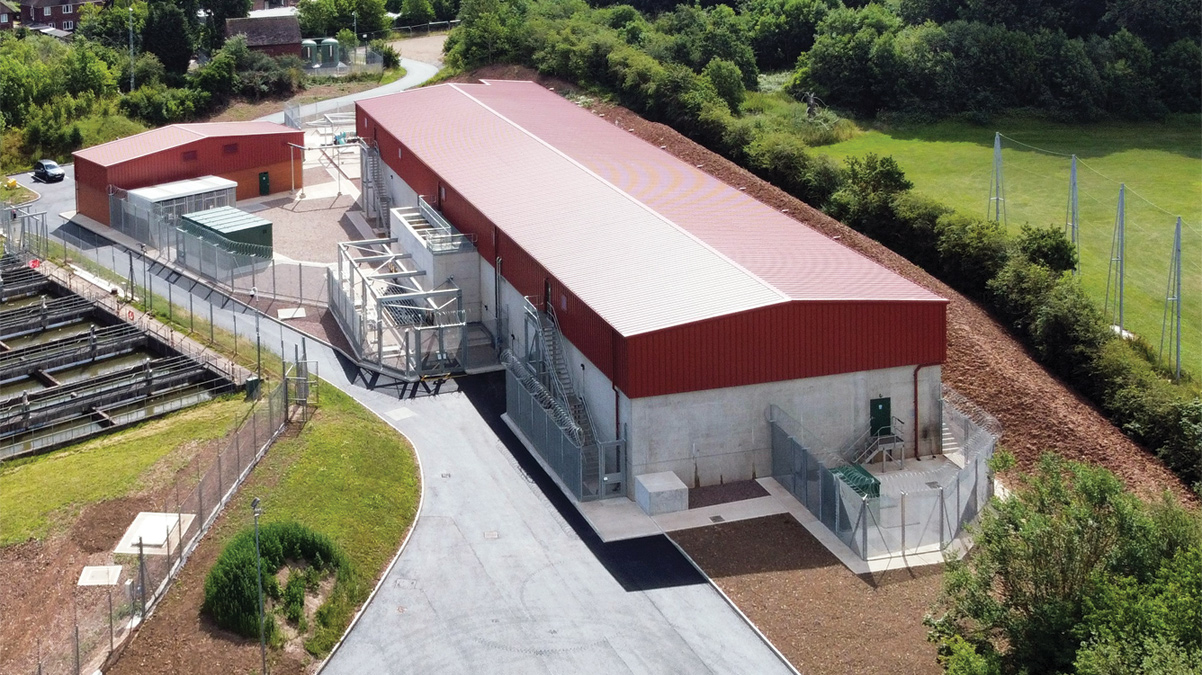
Interstage pumping station and rapid gravity filter building (from west) – Courtesy of Galliford Try
HV works – project scope
- Replace existing 11kV switchgear.
- Provide an additional 1500kVa transformer with a civil compound and HV cabling to new 11kV switchboard.
- Modification to the generator synchronisation system to accommodate new switchgear.
- New 3.3kV switchgear to feed the new RGF transformers and the existing Block 4 transformers.
- New secure enclosure for the 3.3kV switchgear with a plinth, trenches and ducting for cabling.
- HV cabling to and from switchgear.
Supply chain engagement
The team employed a clear strategy – to utilise Galliford Try’s in-house capabilities where possible, including design, steelwork, lifting equipment, sample pump backboards, instrumentation backboards, point of application boxes and asset intelligence (SEMD). The team also used the company’s in-house civil and mechanical labour force whenever possible.
The engagement and performance of the supply chain were fundamental to the project’s success. A number of key suppliers and subcontractors were engaged early and helped develop the design and constructability of key areas. Due to the confined space, the on-site reviews and pre-order minutes of meetings helped flush out access dates, laydown areas and points of interaction. Coupled with daily collaborative planning sessions, this approach helped to control the work areas on site and enabled better communication around supplier movements and working areas.
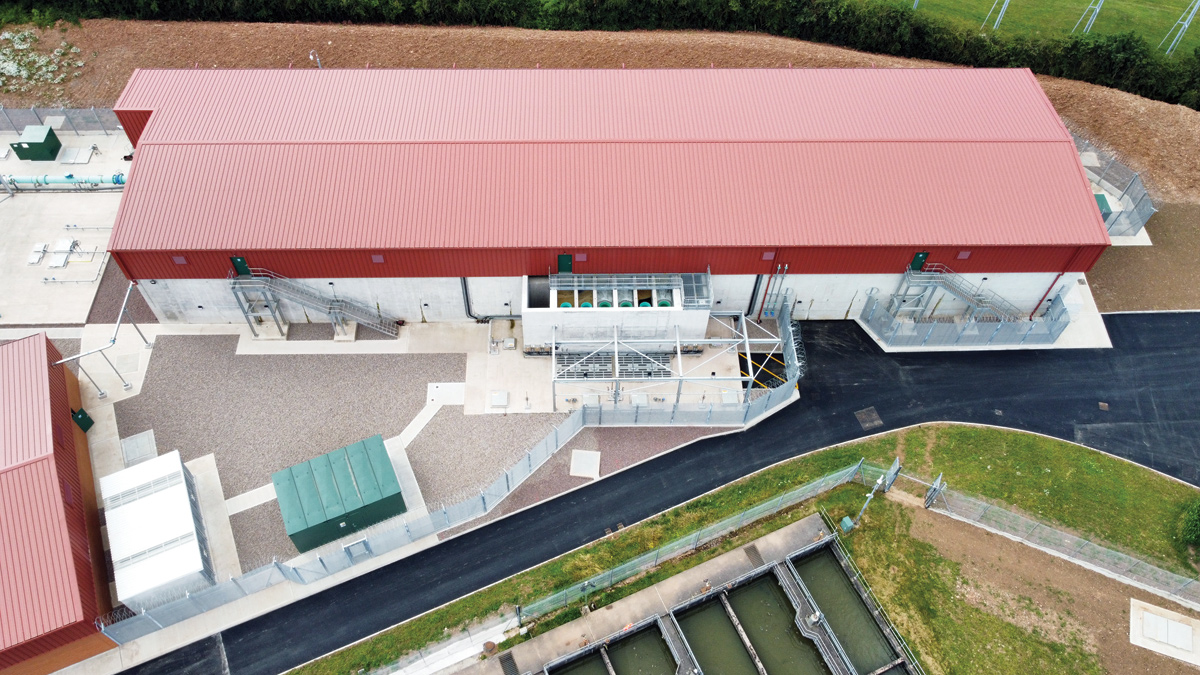
Interstage pumping station and RGF building from the north – Courtesy of Galliford Try
The Seedy Mill WTW project was faced with an extremely challenging regulatory target, by which point the new RGFs had to be in service. There were significant challenges with costs and programme, set against a backdrop of instability and unpredictability in supply chains and construction costs inflating at a much greater rate than CPI. However, Galliford Try and South Staffs Water’s proactive and collaborative approach to managing risk, delivered a project which was within the original target price, and the team met the regulatory date challenge with two weeks to spare.
Galliford Try’s construction management was key to the delivery of the Seedy Mill WTW project, and their collaboration with South Staffs Water allowed them to meet and surmount a significant number of challenges by careful planning, risk mitigation and challenging the programme whilst always maintaining focus of health, safety and wellbeing of personnel and the customer.
Seedy Mill WTW: Supply chain – key participants
- Client: South Staffs Water
- Principal designer/contractor: Galliford Try
- Civil design checks: Eastwood & Partners
- Hydraulic modelling: Hydrotec Consultants
- RC works: STAM Construction Ltd
- Underground pipework/earthworks: Draper Construction
- Piling: Van Elle
- Shoring/temporary works: National Trench Safety UK
- Fabricated steelwork: GT Fabrications
- Structural steel & cladding: Structural Steel Limited
- Mechanical installation (RGF): Frankyln Yates Engineering
- Mechanical installation (dewatering): Watermark
- Electrical installation: Elsym Installations Ltd
- SCADA & systems integration: HBX Ltd
- RGF Leopold flooring: Xylem Water Solutions
- Filter media installation: Western Carbons Ltd
- Centrifuges: Alfa Laval
- Conveyors: CTM Systems Ltd
- Polymer systems: SNF UK Ltd
- Dosing rigs & instrument backboards: GT Plymouth
- MCC & RIO panels: BGEN
- Carbon steel pipework: Freeflow Pipesystems Ltd
- Ductile iron pipework: Saint Gobain PAM UK
- IPS & CWBT pumps: Sulzer Pumps
- Air blowers: Aerzen Machines
- Penstocks: GT Ham Baker Engineering
- Pressure instruments: Trafag Sensors & Controls
- Level & flow instrumentation: Siemens
- Level instrumentation: Hawker Electronics
- Flow instrumentation: ABB
- Valves: Affco Flow Control
- Valves: Cotswold Valves
- Security works: GT Asset Intelligence
- Ventilation: Air Technology Systems Ltd
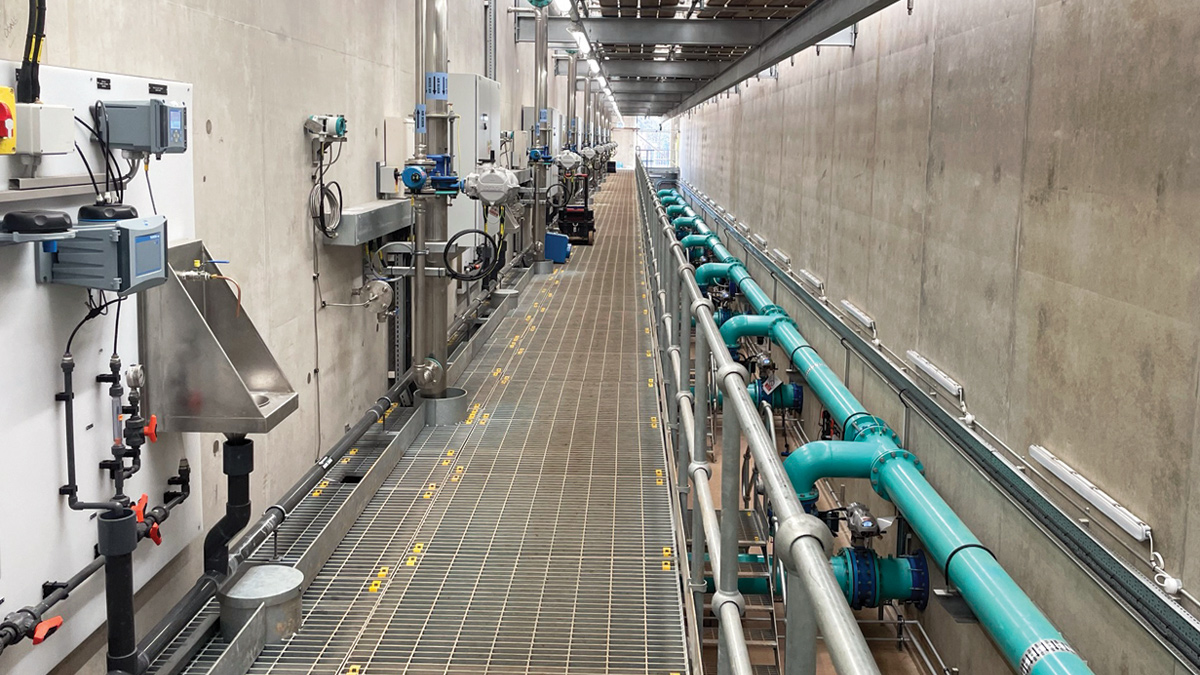
RGF pipe gallery – Courtesy of Galliford Try
Construction – Filtration stage
The Seedy Mill project requirement was to provide an additional stage of filtration on site, primarily to reduce the turbidity in the water. The build was an off-line solution built on the south side of the existing treatment works. The scope included:
Underground pipework
Connections into the 1000mm diameter pipework downstream of the DAF were made with suitable valving to allow flows to be diverted to the new intermediate pumping station. Draper Construction undertook a significant number of underground pipework connections to connect the RGF to the existing process and also to the wastewater systems on the project. This required careful planning with all stakeholders and submissions and agreement of ‘authorised outages’ to reduce the output of the site while the connections were made.
Intermediate Pumping Station (IPS)
The IPS consisted of two compartments, which could be isolated from each other via penstocks to allow for future maintenance. Each compartment contained three 45 kw centrifugal pumps from Sulzer, each capable of operating at 30 MLD.
Water is pumped directly up from the IPS into the bellmouth chamber, which contains baffling to regulate the flow into the RGF’s common inlet channel that allows the process water to enter the ten RGF cells via inlet actuated penstocks.
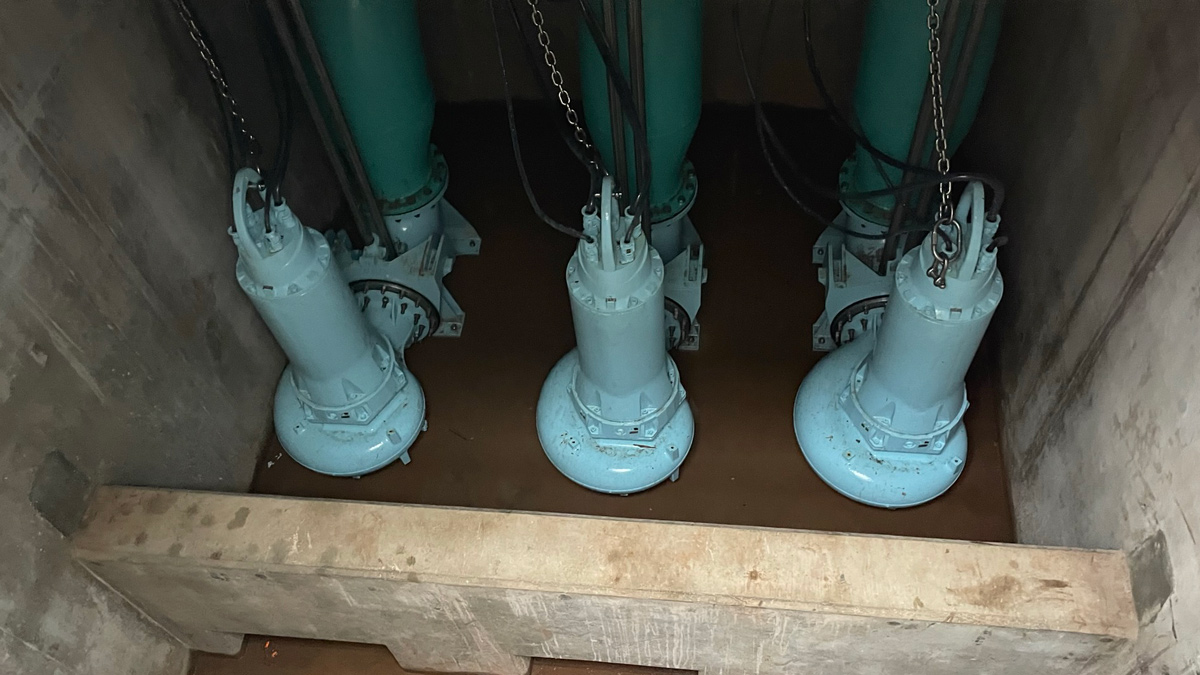
Interstage pumping station wet well – Courtesy of Galliford Try
Pipe gallery
On the south wall of the RGF cells is a 71m long pipe gallery, which contains the backwash pipework system, the process outlet pipework system and the rinse pipework, used after the cell had a backwash but prior to the cell going into service.
Rapid Gravity Filter cells
The RGFs are housed in a cladded structure 71m long x 18m wide. There are ten cells built upon continuous flight auger piles, designed to take 10-15 MLD. The RGFs are concrete tanks, cast in situ using a mix of blending cement with fly ash to slow down the cure time and reduce thermal cracking and shrinkage.
On the floor of each cell is a Xylem Water Solutions Leopold underdrain flooring system (rather than the traditional nozzle approach), which provides improved bubble coverage and reduced installation time. Above the Leopold flooring are layers of sand and anthracite media.
Each cell has its own primary (ultrasonic) and secondary (level electrode) level measurement equipment as well as local control panels, turbidity monitor backboard, sample tap and differential pressure monitors. Access steelwork on top of the RGF cells allows access for maintenance of the associated equipment.
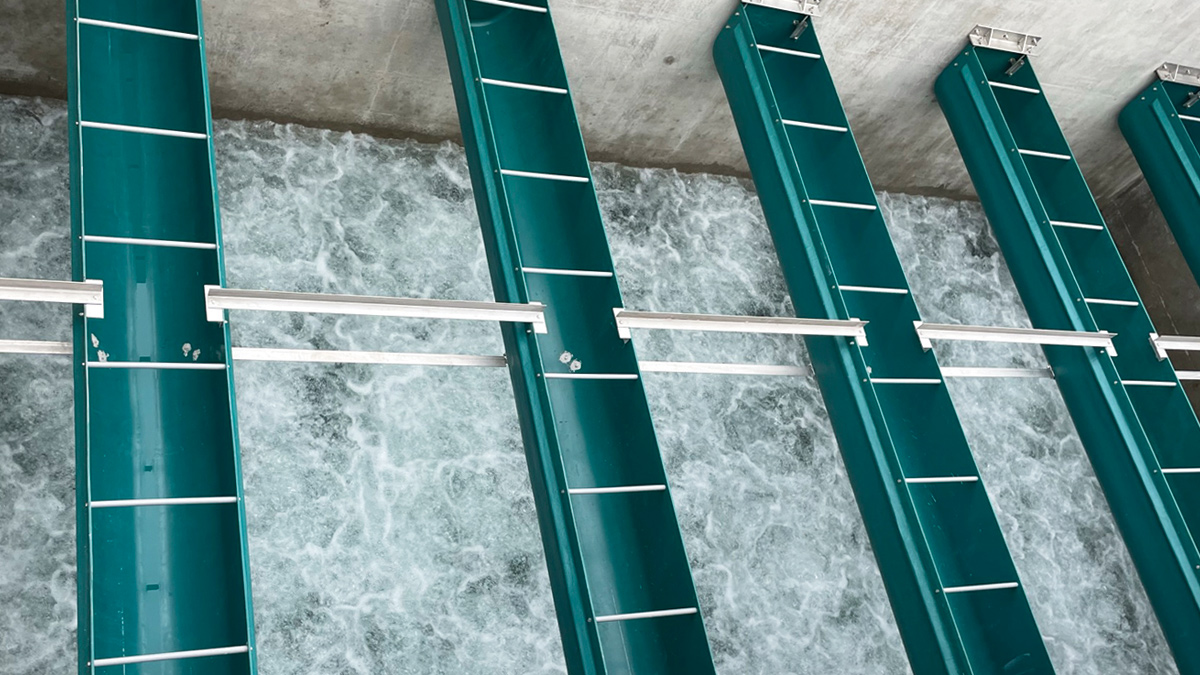
RGF air pattern test – Courtesy of Galliford Try
Clean Water Backwash Tank (CWBT)
The new CWBT was built in two compartments, fed by treated RGF process water. There are two 75kw pumps (duty/standby) per compartment, each capable of pumping up to 330 l/s, which flows back up through and cleans the filters. This is in conjunction with the blowers adding air into the system at various parts of the wash. The dirty backwash water is discharged in the existing waste systems.
Motor Control Centre (MCC) building
This building houses the new MCC contained in the IPS and CWBT drives and the main Programmable Logic Controller (PLC), which controls the operation of the IPS, RGF and CWBT systems. It also houses the two (duty/standby) air blowers that are utilised for backwashing of the filters.
Commissioning
The new IPS/RGF/CWBT arrangement was commissioned as far as practical offline. After successful dry testing, wet testing was conducted utilising process flow in but running all flow that had been through the RGF to waste until satisfactory water quality laboratory results and Site Acceptance Tests were achieved. Three cells at a time were turned into supply, in order to stagger the impact of bringing RGF cells online into the works. Each stage had a proving period, after which the core team would meet to review the results and then decide ‘Go’ or ‘No-Go’ for the next bank of cells.
Construction – Dewatering stage
The existing dewatering system comprised of an existing building with centrifuges and ancillary equipment that was beyond its asset life. The new dewatering system comprised of a new sludge holding tank with mixers, centrifuge feed pumps, polymer make-up, day tank and dosing system, centrifuges capable of 15m3 @ 3% dry solids, conveyors and an MCC to control the system.
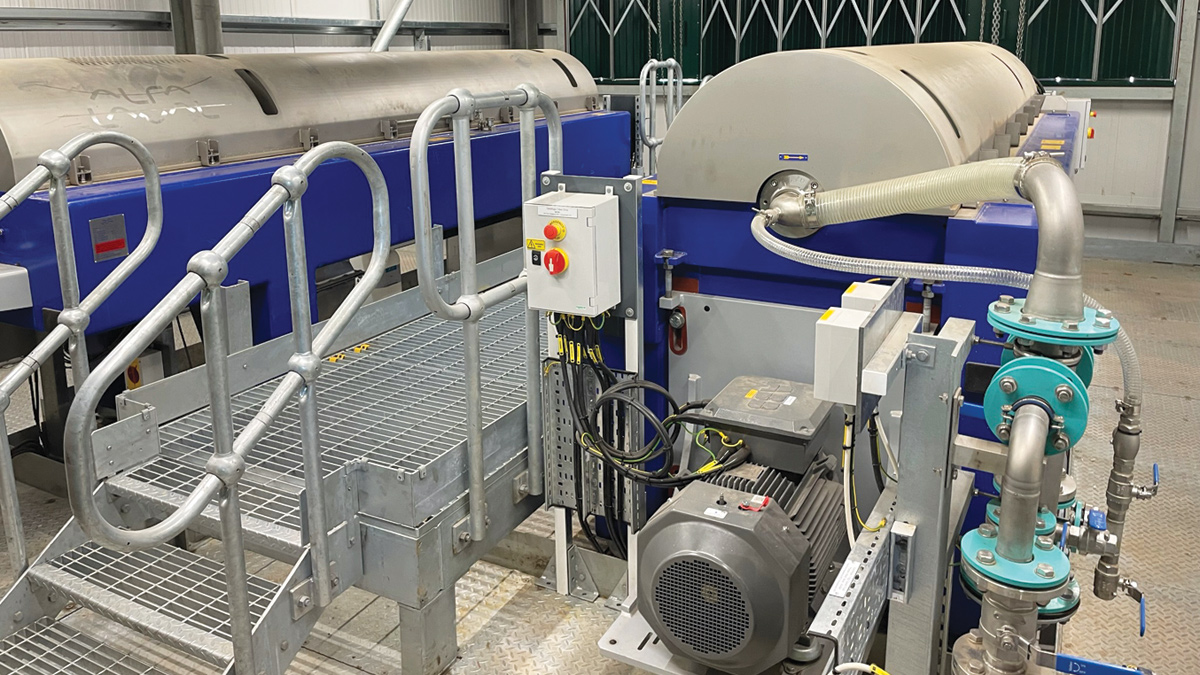
Alfa Laval centrifuges – Courtesy of Galliford Try
The new dewatering works had to be undertaken in the existing building around existing operational assets. A building extension was required to house the new Alfa Laval centrifuges and two screw conveyor systems from CTM Systems Ltd. However, the new polymer system and MCC were installed within the existing building, requiring careful planning to replace equipment in a phased manner with minimal disruption to the client’s process.
HV works
The HV works consisted of modifications to existing HV switchgear, new 3.3kV HV switchgear, the replacement of the 11kV mains incomer panel, new transformers and compounds, and associated cabling and transformers. GT utilised its HV SAP to work together with the South Staffs Water SAP on the isolations and phasing of the work to carry out these works with minimal disruption to the process. These works were also done in and around the new RGF, which required careful planning involving morning CP sessions with team coordination, exclusion zones and access areas.
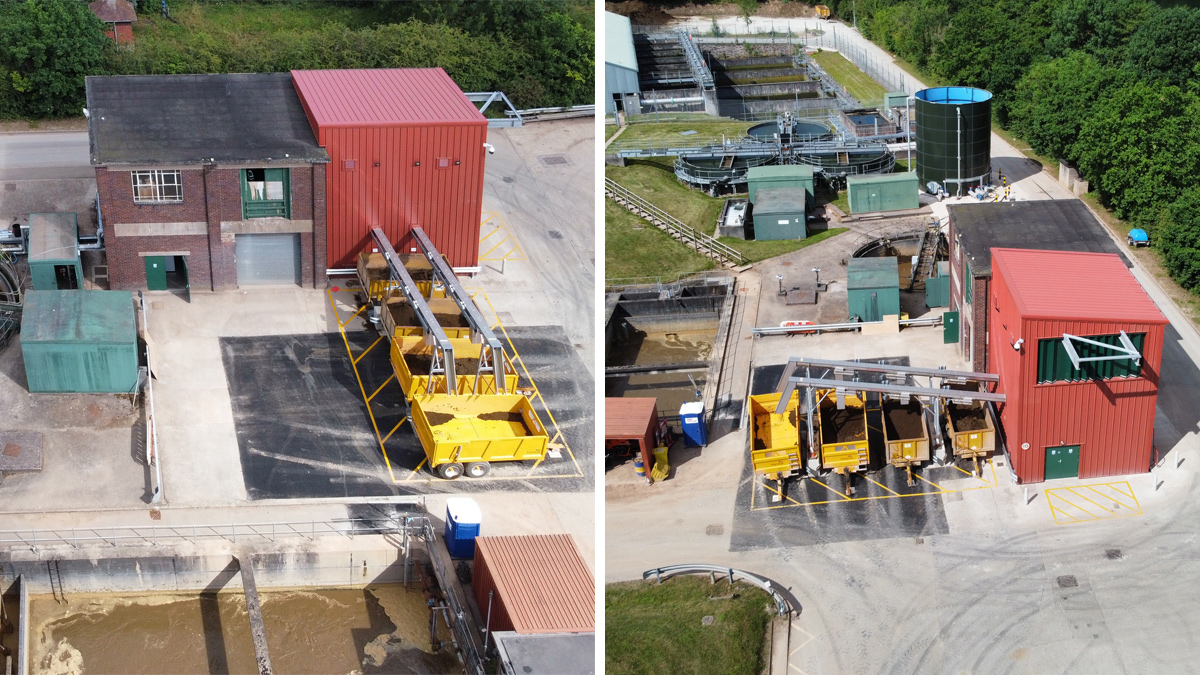
Dewatering area – Courtesy of Galliford Try
Time saving solutions
The Seedy Mill WTW project team achieved Plant In Use (PiU) more than nine days before the Regulatory Date of 31 March 2023. PiU is defined as all flow entering the site running through the new RGF filtration system, with capacity ranging from 60 MLD up to 120 MLD.
At one stage, the PiU was forecast as being more than 37 days behind schedule but the team turned this around by running a number of programme workshops. Galliford Try and South Staffs Water collaborated and challenged each other on different construction and commissioning methods, resulting in a significant improvement on the PiU date.
To have achieved PiU prior to the regulatory date is exceptional and is a credit to everyone involved. This achievement is a result of the high level of cooperation between the respective site operation teams, a collaboration which was essential for the delivery of the scheme.