Sheeplands WTW (2018)
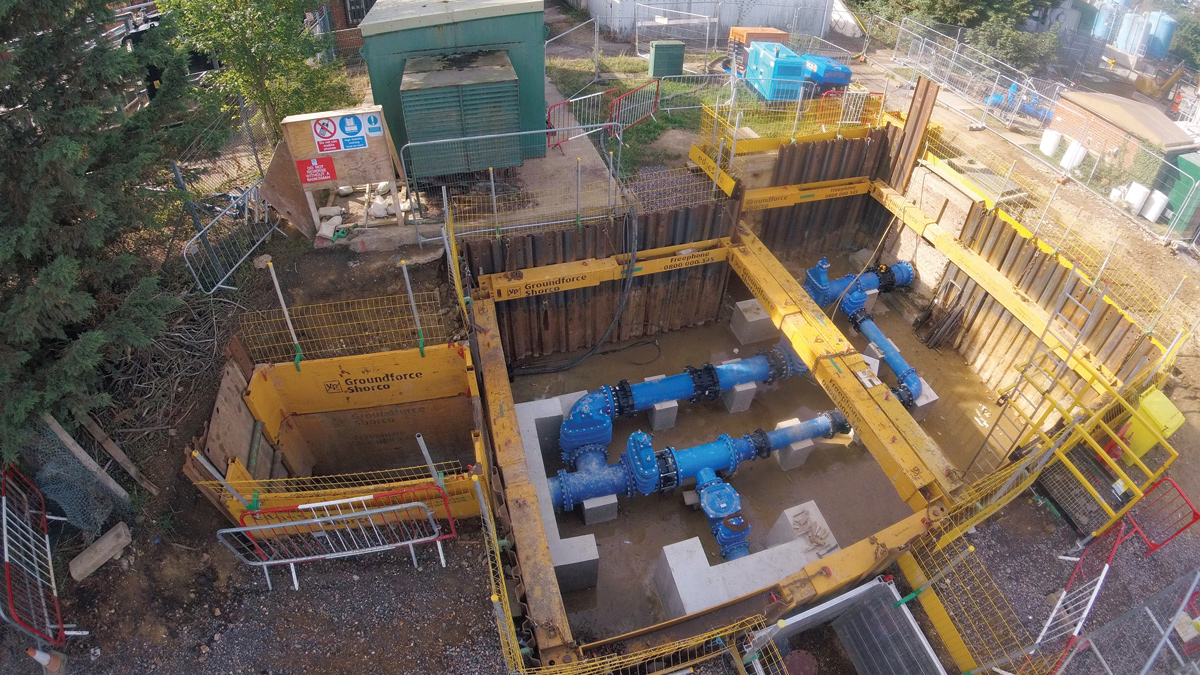
Borehole pipework modification - Courtesy of Barhale Ltd
Sheeplands WTW is a groundwater treatment plant supplying an average of 12Ml/d to the Bowsey Hill Service Reservoir and local district zones. The site comprises of three boreholes, a ‘blending’ raw water supply main received from Harpsden WTW, a nitrate removal plant, GAC vessels, sodium hypochlorite storage and dosing, sodium bisulphite storage and dosing, single contact tank and three treated water lift pumps. The abstraction boreholes have been in function since the 1940s, while the high lift pump house, disinfection system and contact tank were built in the 1960s and 1970s. The GAC plant to remove pesticides, the ‘blending’ raw water supply, and the ion exchange nitrate removal plant were built during the 1990s and 2000s. Improvements carried out during AMP5 included pipework cross-connections and control system upgrades.
Overview and challenges
Despite the AMP5 improvements, the WTW continued to come short of Thames Water (TW) standards on a number of grounds. Specifically the boreholes, when running to waste discharge to a local ditch contributed to local flooding during periods of high rainfall and river flow, thus requiring a new transfer main to allow the flushing of the three boreholes to the River Loddon. Moreover, the WTW’s reliance on a single contact tank with integrated aeration system made it impossible to remove the tank from service for either maintenance or periodic inspection without stopping the entire treatment process. Finally, the sodium hypochlorite chlorination and de-chlorination loop times at two sample points (SP2) exceeded TW’s 3-minute loop time standard.
As part of AMP6, TW has planned to fully address the remaining issues at the Sheeplands WTW. The following solutions have been identified to the problems highlighted above.
New run to waste pipe and discharge headwall structure
A new run to waste pipeline was constructed to enable the boreholes at WTW to be flushed to waste. The route passes underneath a railway and an existing draining ditch, in a groundwater protection zone.
Due to these constraints, microtunneling was chosen to construct 200m of tunnel under the railway line and a local ditch. Barhale, the tunnelling contractors, used a 600mm Iseki Unclemole micro tunnel boring machine (MTBM). The machine was launched from a 5m (ID) driving shaft (which was decommissioned after the civil works were completed), towards two 2.1m (ID) reception shafts, which will also be used for inspection and maintenance after completion of the works.
The water table was 1m below ground level during the shaft construction. The team addressed this challenge by employing the caisson method to build the shaft while it was flooded. A clamshell telescopic arm excavator was used for digging, while the caisson precast rings were pushed into the ground with the help of 3 (No.) jacking gallows. Once the formation level was reached divers were sent inside the shaft to install dowel bars, to pin the shaft into the ground.
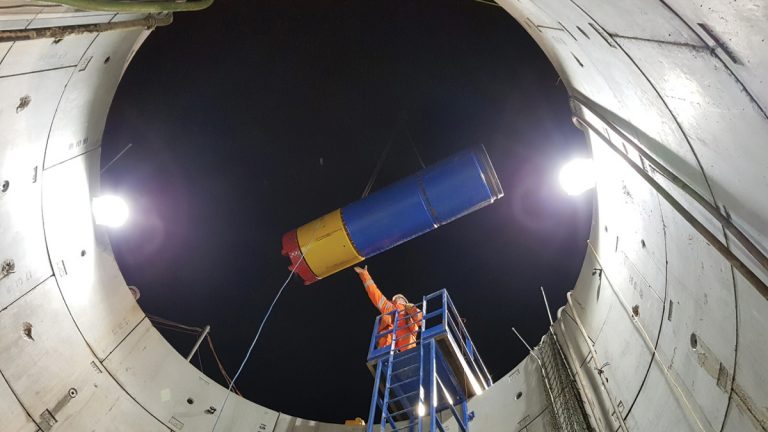
MTBM at Shaft ‘B’ – Courtesy of Barhale Ltd
The machine was remotely operated from a control room situated on the surface. A video camera integral to the Unclemole enabled the operator to assess the existence of possible water ingress and defects inside the machine close to the inside face of the TBM, as well as with laser targeting. Ground conditions were assessed at the separation plant, during the tunnelling process, and the amount of additives used (TK50 flocculants or chalk floc) was adjusted to suit the actual ground conditions at any time.
While the MTBM progressed under the railway at a depth of 6m, the track settlements were constantly monitored by a high precision electronic distance measurement that monitored targets on the tracks prior to tunnelling commencing. This helped to ensure that the settlements were not higher than the theoretical figures previously calculated by designers, which were also assessed and approved by Network Rail.
The desired tunnel alignment was determined after the reception shaft was sunk and its bottom surveyed in order to take into consideration a possible minor tilting of the shaft while it was being sunk. This is especially critical when reception shafts are of a small diameter; a minor alignment deviation could mean a significant angled entrance of the MTBM in the shaft and thus a compromised structural integrity of its rings due to a non-orthogonal tunnel eye broken in the shaft. To avoid this, the site engineers constantly monitored the plan and level of the tunnel alignment and thus ensured the TBM would arrive at the exact centre point of the reception shaft.
The water ingress at each breakout point inside the shafts created two additional risks. Firstly, the shafts and all the equipment involved in the operation could be flooded. Secondly, a void could occur behind the shaft walls as the water coming inside the shaft flushed the chalk particles in the adjacent ground. Ground stability could also be weakened as a result. To address these issues, Barhale’s team used TAM (tube-a-manchettes) grouting with GeoTek LV. This is a low viscosity, single shot polyurethane based on MDI in combination with polyether polyols and an amine based catalyst. The system only reacts when it comes into contact with water, forming a rigid polyurethane foam. GeoTek LV stabilised the soil and gave high strength in a short period of time, thus preventing further movement and improving the bearing capacity.
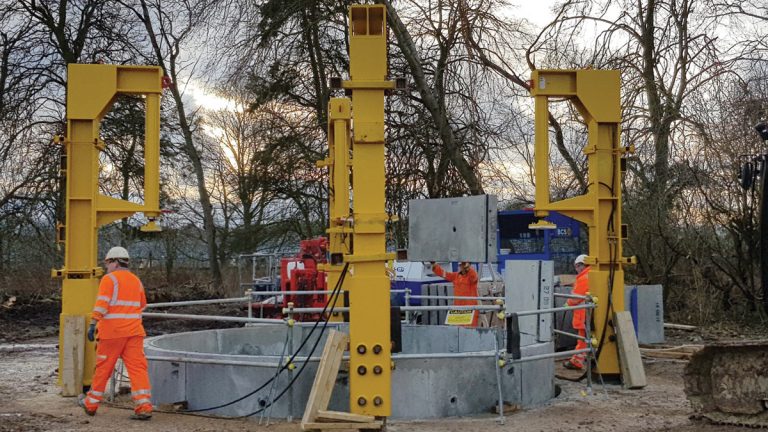
Shaft ‘B’ – Courtesy of Barhale Ltd
After the primary lining was completed and the MTBM demobilised, the straight alignment of the tunnel from drive to reception shaft was confirmed with laser. This helped to obtain the minimum clear sight-line diameter required for the ductile iron (DI) pipe installation. To avoid any possible clash of the DI pipeline with the casing pipe the engineers checked the minimum value of the theoretical bending radius for DN350 DI pipe against the measured alignment of the tunnel; the flanged joints were taken into consideration as full rigid (no angular deflection allowed). The pipe installation only started when it was confirmed that the maximum curvature was compatible with the clear sight line diameter observed in the tunnel.
DN300 PN16 rated double flanged ductile iron pipes were then inserted in the tunnel. This entailed a significant risk that the flanged connection would be damaged during the pipe insertion process. As a solution, the engineers liaised with FT Pipeline Systems and designed a custom made 12.83” x 17.91” (OD) flange to 23.03” ID casing spacer with fusion bonded epoxy rollers.
The spacer was also designed to have two additional legs at the top side to avoid flotation of the pipe while being grouted. Thrust blocks were also installed at the pipeline material transition connections to ensure stability and prevent joint pull-out on the DI sections; all the pipework sections were hydrostatically tested after being cast into each thrust block. In the open-cut sections, 315 OD SDR11 HDPE was used to minimise man-entry into the pipe trench.
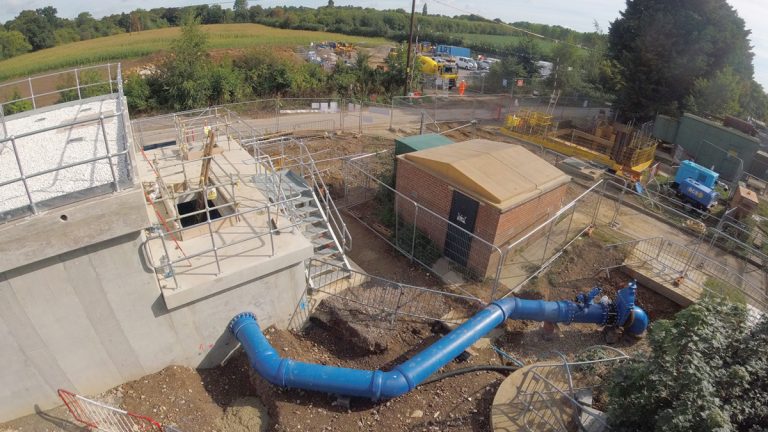
Contact tank and borehole pipework – Courtesy of Barhale Ltd
The work on the run-to-waste pipeline also involved pipework modification to the existing boreholes. This included diversion of existing services and temporary support for existing assets to maintain operation of the works during construction, and removal of existing underground borehole’s delivery pipework, based on TW’s shutdown regime.
The existing cast iron pipework was replaced with DN450 PN16 ductile iron. VJ special flange adaptors, dismantling joints and couplings were introduced to allow flexibility in the new pipe alignment. DN450 PN16 gate valves were strategically placed across the alignment to enable independent flushing of each borehole. Once the installation was completed, the pipe alignment was thrust-restrained by casting RC blocks at each weak point.
A precast concrete headwall, air break chamber (with air break system) and spillway were also constructed at the discharge point near the River London. This will avoid contamination of water into the run-to-waste pipeline during high flood events and local ground erosion resulting from flushing events.
Sheeplands WTW Project Team
- Client: Thames Water
- Principal designer: CABV JV
- Discipline designer: Atkins
- Principal contractor: CABV JV
- Contractor: Barhale Ltd
- Other consultant: Barhale Construction (Tunnelling)
- Bespoke steel manufacturing (pipe brackets & supports) and handrails & staircases for chlorination tank: BCS
- Waterproofing and reflective gravel layer on chlorination tank roof: Waterseal
- Chlorination tank structure: Precast concrete manufacture & installation & in situ concrete: Carlow Concrete
- Supply/installation of baffle curtains for chlorination tank: Waterlines
- Security access covers for the chlorination tank: EJ Group
- Design and supply of temporary ground shoring – Sheets, frames and walers: Groundforce
- Supply of welding equipment for HPPE pipe: MCA
Secondary contact tank and common aeration system
The construction of a new contact tank has been proposed as a solution to the issues raised by the existence of only one tank at the WTW previously. Due to space and time constraints, the tank was made of precast concrete sections, with a baffle curtain system that uses reinforced polypropylene curtains, 1.4404 grade stainless steel fixings and fittings and PVCu pipework to minimise the footprint of the tank. The new tank also has an overflow capable of discharging the maximum design flow of 12.96Ml/d to the existing emergency overflow discharge point.
Since the old tank has an integrated aeration system, a new, common aeration system has also been proposed. This will consist of a new pressurised air injection system on the common inlet pipework to the new contact tank. The new aeration in-line static mixer and new SP2 and aeration sample points will be housed in a new, partially buried, dry well chamber integral to the new precast contact tank structure. The dry well will also contain the inlet, outlet and bypass valves and the bypass pipework.
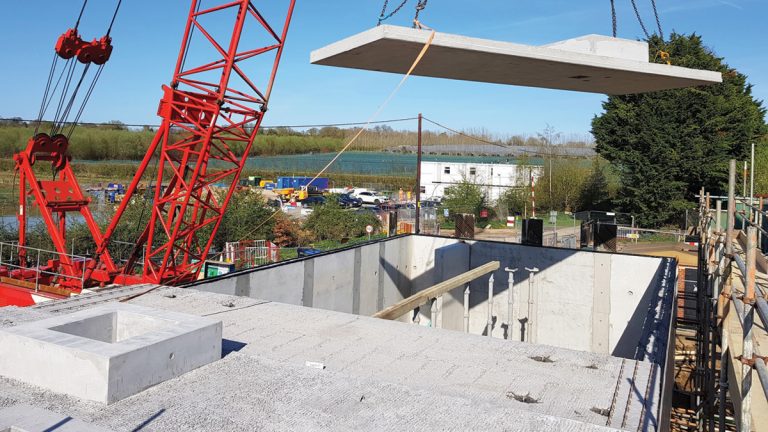
Contact tank during construction – Courtesy of Barhale Ltd
Loop time improvement
The key contributor to the excessive loop times associated with SP2 has been the length of pipework, and the corresponding volume between the sodium hypochlorite dosing point and the sample point. To address this, the SP2 sample point will be brought closer to the sodium hypochlorite dosing point.
The sample points will be located on the inlet pipework to the new contact tank, within the aeration dry well chamber. The sample points will comprise of two DN40 PN16 flanged connections for the installation of sample lances and sample pump suction pipework.
A single DN40 flanged connection will be installed downstream of the sample draw off points, to create a fast loop back to the system.
All sample pipework within the dry well aeration chamber and in the sample pump kiosk will be fabricated from 1.4401 grade stainless steel. The interconnecting cross-site sample pipework between the aeration dry well chamber and the sample pump kiosk, and between the sample room and the sample pump kiosk will be run in PE. This pipework will be installed through a series of new ducts and draw pits, through the shortest available route.
Conclusion
Barhale has recently finalised the civil works on the project. Despite challenging ground conditions, the team has delivered a new run-to-waste pipeline and chlorination tank that complies with or even exceeds the client’s expectations.
eight2O’s M&E contractors will now take over, to install the common aeration system and to undertake the other works that are required to improve the loop times. It is anticipated that the works will be finalised in March 2019.