Sluvad WTW (2024)
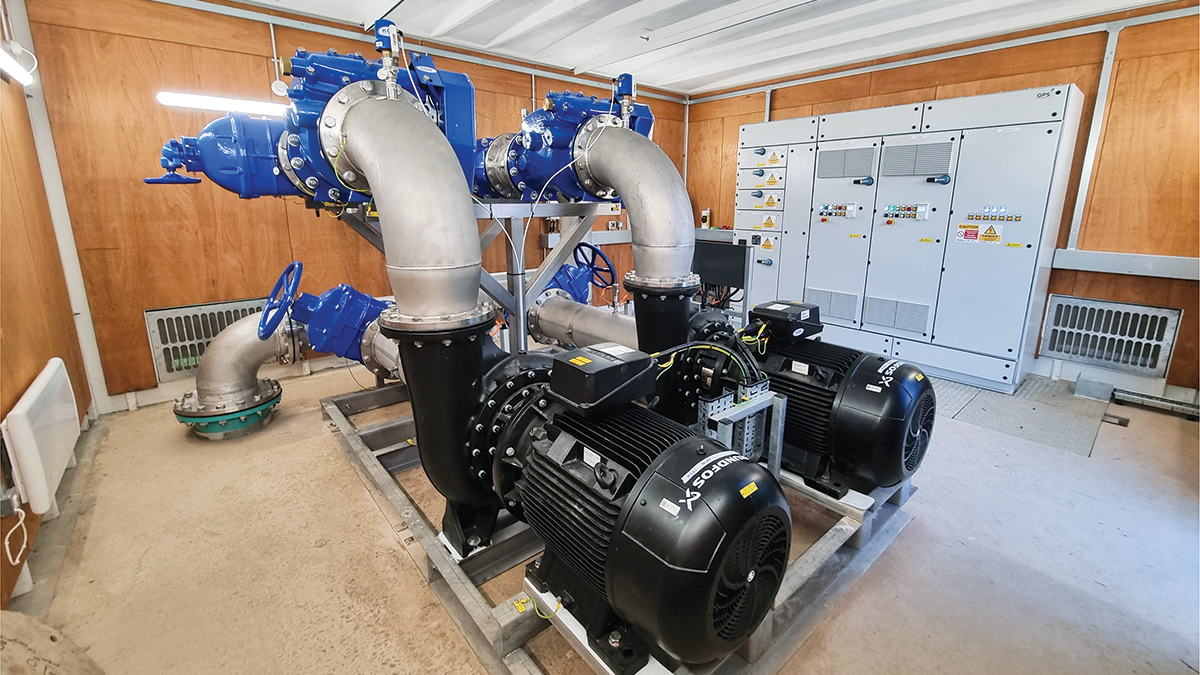
Constructed pump-skid with Grundfos pumps and bottom-entry MCC within the security-rated kiosk - Courtesy of Mott MacDonald Bentley
Sluvad Water Treatment Works produces an average of 120 Ml/day of clean water to supply the South Wales region and has a maximum production of 172 Ml/day. Located approximately two miles south-east of Pontypool, it overlooks Llandegfedd Reservoir from where the raw water is pumped into the treatment works via the Sôr Pumping Station. At Sluvad WTW, raw water is dosed with a ferric sulphate coagulant followed by polyelectrolyte flocculant before entering 28 inverted pyramid clarifiers where the flocculated particles are retained in a sludge blanket. The clarified water passes to 28 rapid gravity filters before chlorination and flowing to the three contact tanks on site and entering distribution.
Background
Dŵr Cymru Welsh Water’s (DCWW) PR19 business plan for AMP7 identified several schemes to minimise customer contacts including water discoloration and taste/odour against the customer Acceptability of Water measure. This is a historic challenge in Wales and is one that is understood to be driven by both raw water characteristics and the prevalence of unlined iron trunk mains.
There is seasonal variation in incoming flow to Sluvad WTW owing to changes in the Llandegfedd Reservoir during the late summer period, such as thermal stratification, that results in spikes of manganese. The increased load of manganese coincides with increased iron levels in the final water as the ferric sulphate coagulant dose is increased to maintain water quality. Mott MacDonald Bentley (MMB) was employed by DCWW to design and build a solution to reduce the levels of manganese and iron.
Improving coagulant mixing was identified as the solution to reduce particulate manganese and iron levels in the final water. Coagulant mixing results in more efficient dosing of ferric sulphate, reducing iron levels, and aids floc formation that is better able to capture raw water contaminants such as manganese while reducing turbidity. At the clarification stage, the inverted pyramid clarifiers would see a more robust sludge blanket formation through which incoming water has to pass, ensuring particles combine into heavier flocs.
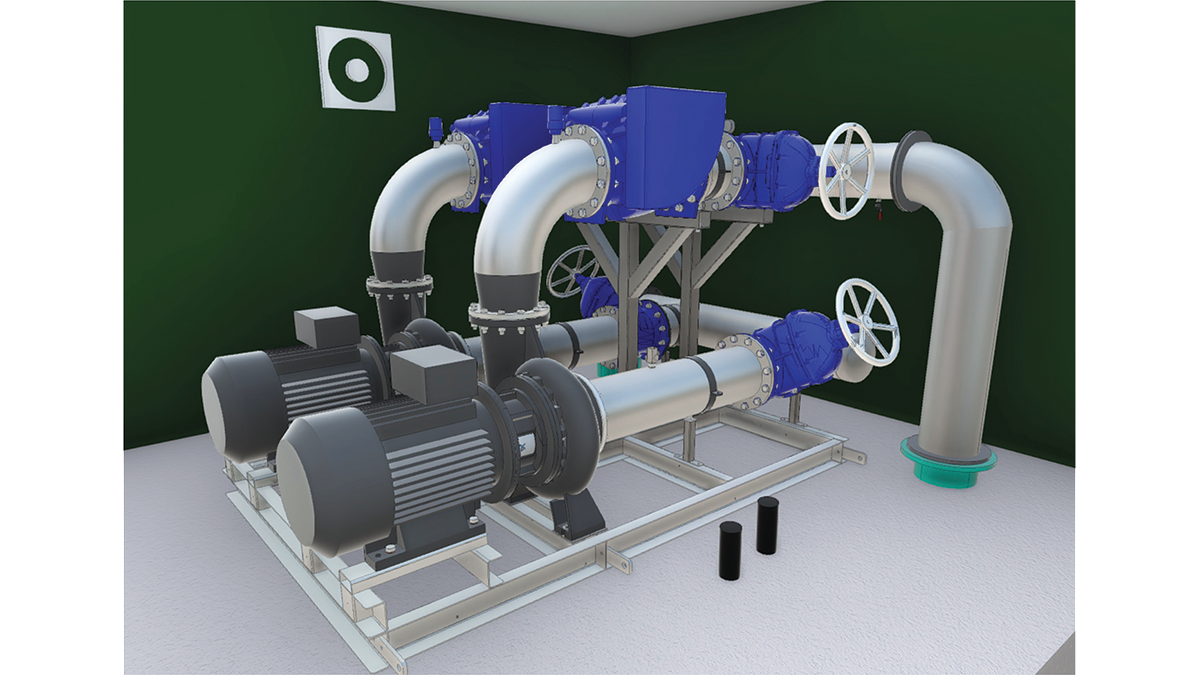
3D model of the pump-skid within the kiosk – Courtesy of Mott MacDonald Bentley
Constraints on coagulant mixing
At Sluvad WTW, ferric sulphate was dosed into the incoming main through pairs of injection lances and previously had no method of mixing coagulant due to technological and constructability constraints. For this scheme, traditional mixing methods were considered at optioneering, including static mixing and mechanical mixing. Mechanical mixing was discounted as the retention volume required would result in a very large chamber to which there was no available space to feasibly install on site.
Static mixing was discounted due to the critical 48” incoming main requiring equivalent sized under pressure connections and flow-stops that posed a severe risk to water supply during construction. Static mixing also results in increased headloss which in this case would have reduced the maximum capacity of the WTW through its effect on the fixed-speed pumps that feed the works.
With limited options to apply a meaningful method of mixing, it was decided that a jet mixing solution needed to be designed and built in its first UK application to coagulant mixing in clean water treatment.
Jet mixer basis of design
Jet mixing technology is not particularly novel and has been commonly applied to wastewater treatment in cases such as solids suspension, sludge storage, and storm tank mixing. There have also been some cases of applying coagulant jet mixing at wastewater treatment works, normally dosed into an open channel at the inlet works and a jet of water provides the mixing agitation to disperse the coagulant more effectively. In these instances, static channel mixing could have posed maintenance issues such as ragging or changes in treatment system hydraulics.
Existing mixing challenges at the treatment works
At Sluvad WTW, it was deduced that the coagulant mixing rate was too slow to ensure a uniform concentration of coagulant, as the mixing relied on the natural turbulence within the pipe.
This issue was compounded at lower works flows in which there was lower ambient turbulence within the pipe to provide the necessary mixing energy. In addition, the incoming flows split into two branches before it entered the clarifiers and an uneven coagulant concentration within the pipe cross section may have resulted in more coagulant entering one branch than the other. The objective was then set that a Coefficient of Variation (CoV) < 0.05 must be reached within the pipe before the flow was split.
Proposed jet mixing solution
Framatome Ltd was employed to carry out the technical investigation and analysis into the current and proposed mixing performance to form the basis of design for the jet mixing solution. The initial investigation confirmed there was poor mixing at all works flow rates. Framatome Ltd then completed an outline jet mixer design with CFD verification to meet the mixing objectives with an approximately 10-fold improvement on time to reach a CoV < 0.05 and, most importantly, before the flow split to the clarifiers.
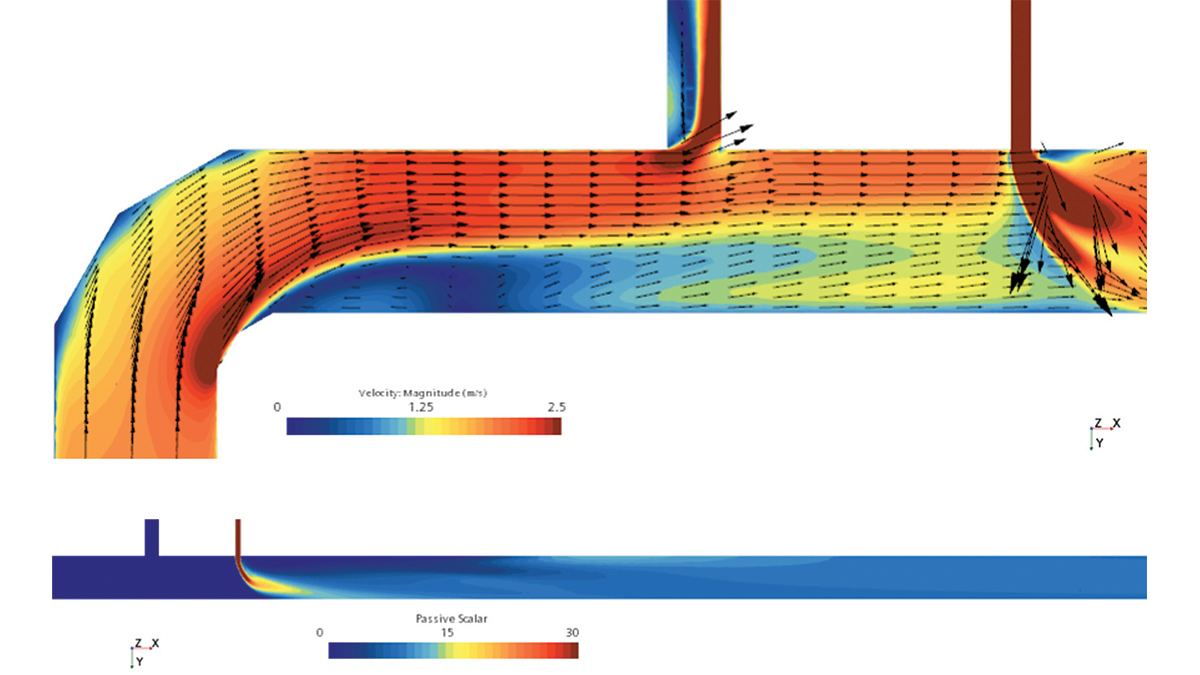
CFD verification of the jet mixer – Courtesy of Framatome Ltd
The outline solution
Detail of the proposed jet mixing solution are as follows:
- A suction line tee-off from the 48” inlet main receives a small portion of the works flow that is fed to duty/standby end-suction centrifugal pumps with a variable speed drive (VSD). The pumps are VSD driven to minimise energy consumption and reduce OPEX by adjusting the pump speed according to the treatment works flow.
- The pump discharge then returns the raw water through a small diameter static mixer which becomes the new point of application for coagulant dosing.
- After ‘pre-mixing’ the solution, the discharge pipe diameter is decreased to increase the jet flow velocity before entering back into the inlet main just downstream of the suction point.
- The high jet flow velocity ensures there is sufficient mixing energy to effectively mix the coagulant in the main within 10 to 12 seconds.
Scope of works
The main elements of work included:
- Installation of two welded underpressure tees to an existing 48” steel main.
- Precast concrete chamber and cover slab with security-rated access covers.
- DN350 static mixer.
- Duty/standby pump skid with VSD centrifugal pumps.
- Installation of approximately 210m of epoxy-coated steel and HPPE pipework between the underpressure tees and the pumps.
- Installation of a bottom-entry Form 4 MCC.
- Installation of a security-rated kiosk.
- Concrete road extension to the new kiosk.
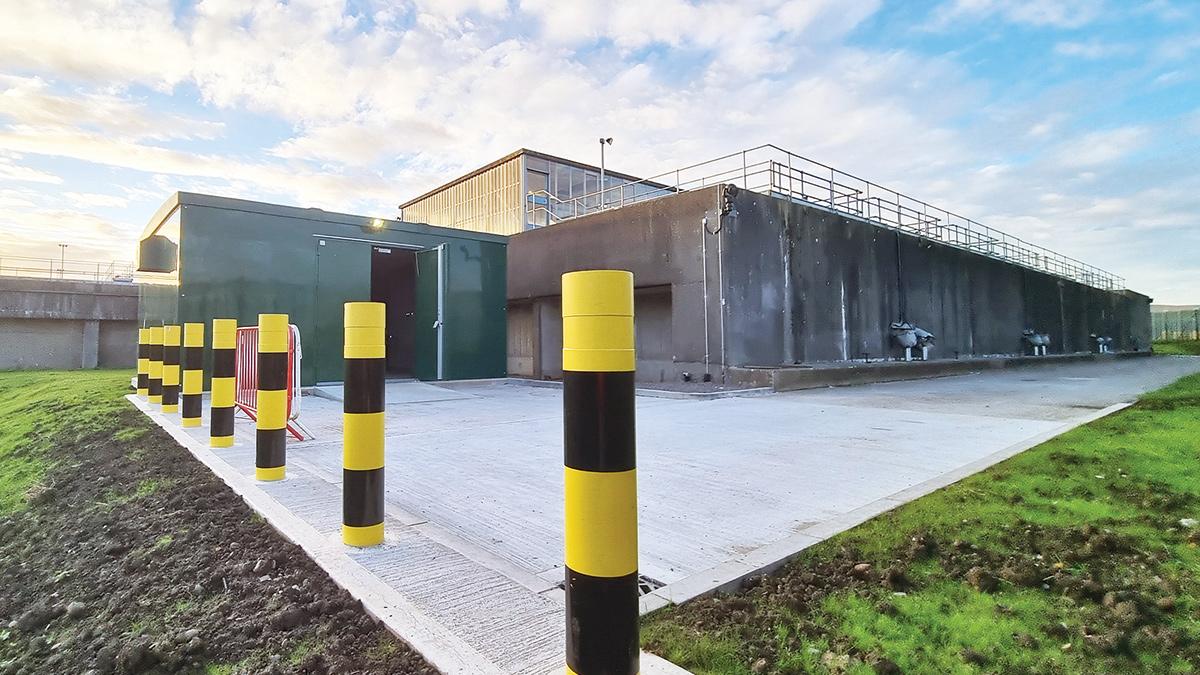
External view of the kiosk and road extension – Courtesy of Mott MacDonald Bentley
Sluvad WTW: Supply chain – key participants
- Client: Dŵr Cymru Welsh Water
- Principal contractor & designer: Mott MacDonald Bentley
- Technical investigations: Framatome Ltd
- Geotechnical: Mott MacDonald
- Ground investigations: Spencer Quantum
- Groundworks: Envolve Infrastructure
- Hydro-demolition: Sabre Jetting
- Underpressure tees: UTS Engineering Ltd
- Electrical installation: Celtic Process Control Ltd
- Mechanical installation: Tema Group
- Systems integration: Oasis Software Solutions
- MCC: GPS Group
- Steel pipework: George Green (Keighley) Ltd
- Steel pipework: Freeflow Pipesystems
- HPPE pipework: Radius Systems
- Kiosk: Morgan Marine
- Static mixer: Statiflo International
- Valves: AVK UK Ltd
- Pumps: Grundfos Pumps Ltd
- Pump skid: KGN Pillinger
- Precast concrete: FP McCann
- Access covers: Technocover Ltd
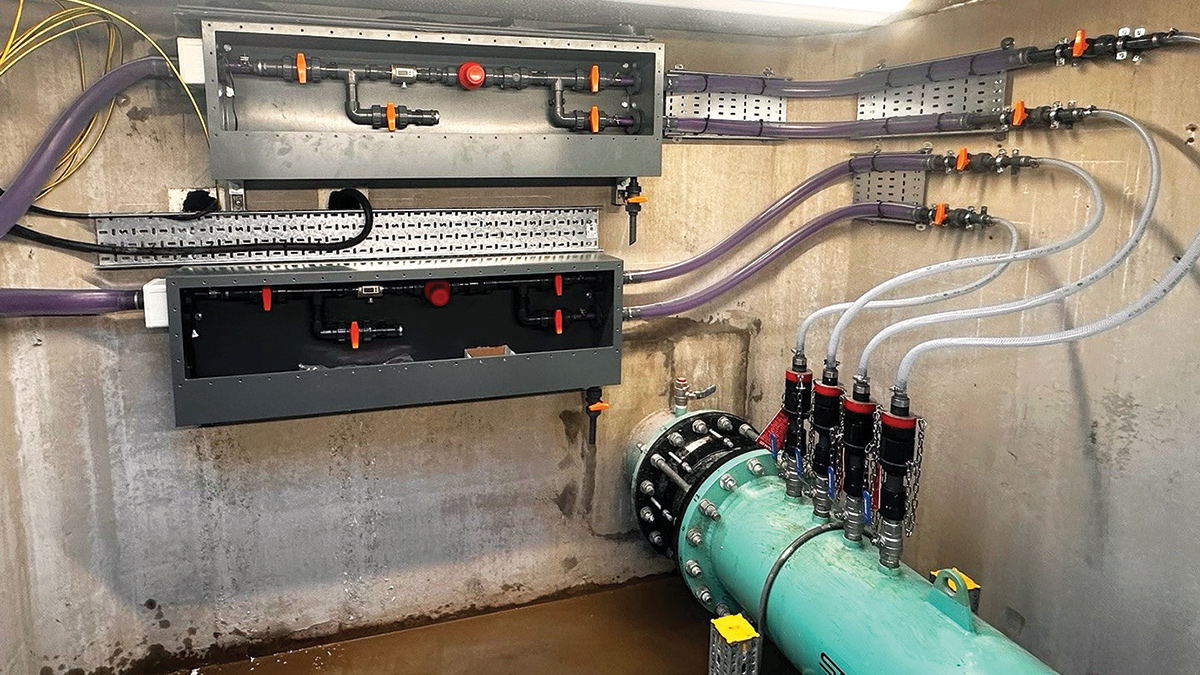
Ferric sulphate point of application in the underground precast concrete chamber – Courtesy of Mott MacDonald Bentley
Construction and challenges
After receiving the outline design from Framatome Ltd, MMB carried out the detailed design of a constructable and commissionable jet mixing solution.
The design involved a precast reinforced concrete chamber with a cover slab that serves as the ‘mixer chamber’ in which the static mixer and the coagulant point of application is located. The suction and discharge points were installed as two steel under-pressure tees that were welded onto the 48” steel main after being exposed from its concrete surround with hydro-demolition.
Site cabin power supply: It was recognised early on that the site cabins would require a large amount of fuel to power them and would produce significant noise pollution. It was therefore agreed for the site cabins to be connected to the WTW power supply to provide a significant reduction in fuel costs and mitigate environmental hazards during the construction programme.
Hydro-demolition: The construction area was situated adjacent to the Sluvad Training Academy on site at Sluvad WTW, so measures were taken to protect the building and reduce noise levels during hydro-demolition. Scaffolding with acoustic barriers were installed to encapsulate the working area.
Underpressure connections: Welded tees were installed as opposed to mechanical tee fittings to provide a more permanent fixture to the main and mitigate the risk of leakage. An added benefit of using welded tees was a reduced programme and safety risk in carrying out hydro-demolition.
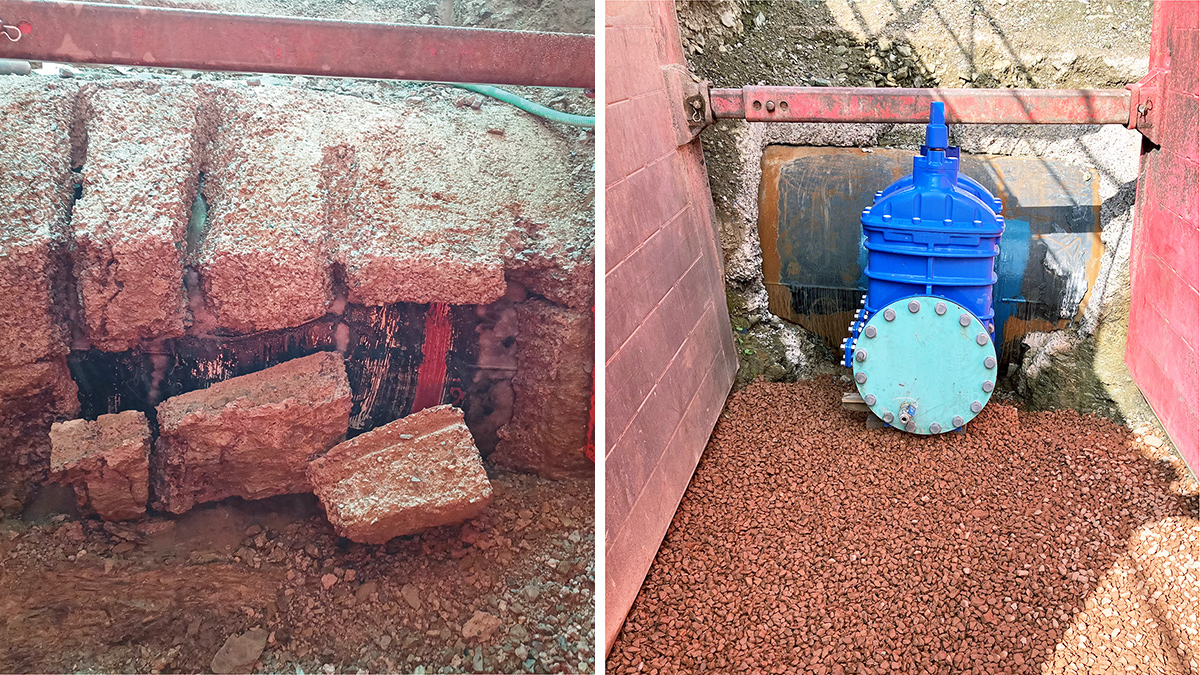
(left) Hydro-demolition carried out on the concrete surround of the existing 48” main and (right) DN400 underpressure connection with a welded tee on the existing main – Courtesy of Mott MacDonald Bentley
Site topography: Challenging topography of the site required custom steel pipes with complex geometry for some parts of the suction and discharge legs. The bulk of the remaining suction and discharge legs were constructed with SDR17 HPPE, that better followed the site topography, joined with electrofusion couplers. HPPE pupped stub flanges were installed where material transitions occurred between PN16 steel pipework and SDR17 (equivalent to PN10) HPPE pipework. An electromagnetic flow meter was also installed to provide verification of the pumped jet flows.
MCC and DfMA pump-skid within a kiosk: The duty/standby pump skid was manufactured and delivered as a DfMA product and installed within a 5.5m x 6.5m x 3.0m security-rated kiosk. The pump suction and discharge manifold pipework was manufactured using 316L stainless steel and supported by a galvanised mild steel skid structure.
A bottom-entry Form 4 MCC was also installed within the kiosk and situated atop a precast concrete service trench that provides ample room for access and maintenance below the MCC.
Testing & commissioning
Coagulation is a critical part in the water treatment process so it was essential that a comprehensive risk assessment was undertaken to ensure the works was able to continue to produce drinking water during the commissioning stage.
Recognising this importance and with the application of an innovative mixing method, a robust design and commissioning methodology was devised that mitigated the risk of loss of supply. The existing point of application arrangement remained in place, acting as a standby, and the existing pipework was modified to allow a valve arrangement and connection to the new point of application.
If any issues were encountered with the new mixing arrangement during commissioning or operation, ferric dosing can be quickly reverted to its original regime.
However, through rigorous planning, the jet mixer was successfully commissioned, and no mitigation measures were required. Following commissioning of the jet mixing system, water quality trends on the SCADA system showed an almost instant improvement in treatment performance at the works, and work is ongoing to realise further treatment process performance and optimisation.
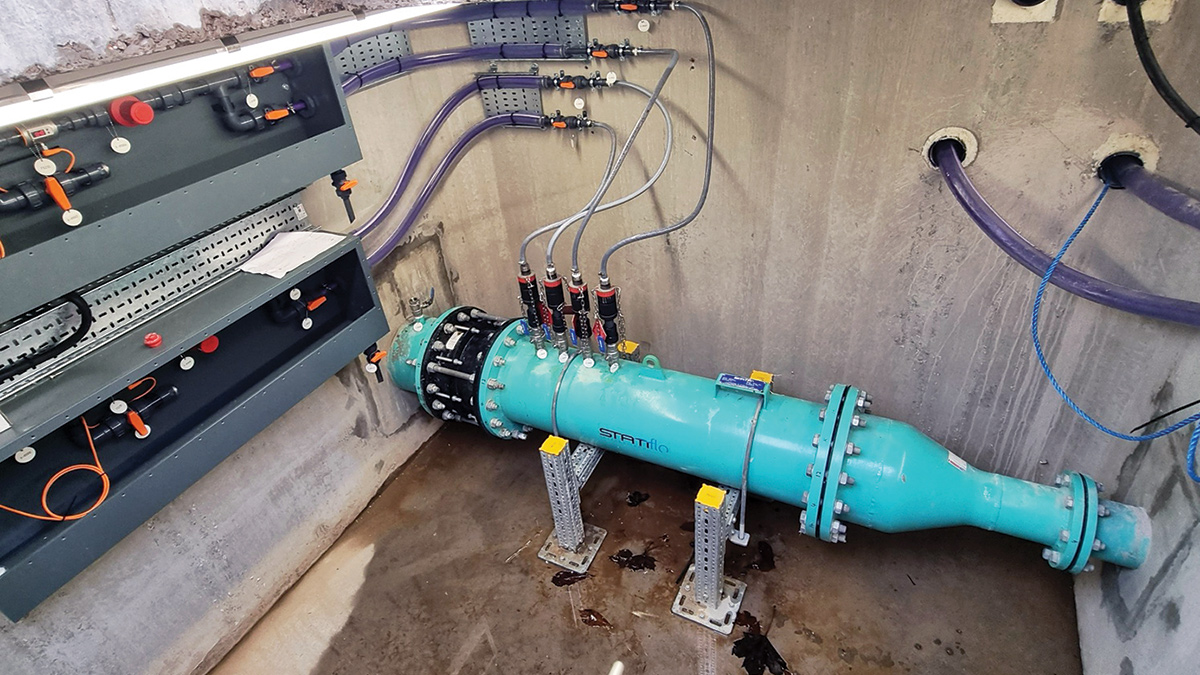
Static mixer and reduction in pipe diameter to increase the velocity of the jet flow before injection into the existing main – Courtesy of Mott MacDonald Bentley
Process benefits
- Clarifier turbidity levels improved.
- 46% mean reduction of clarified water turbidity.
- Clarifier iron levels improved.
- 48% mean reduction in clarified water iron levels.
- Filter headloss reduction.
- 20% to 40% reduction in filter headloss, allowing for filter run times to be extended and reduce wash water production.
- Reduced chlorine demand.
- Reduced post-clarifier hypochlorite dosing, indicating the Cl2 setpoint is being achieved more effectively with less chemical dosing. This suggests there is better organics capture through the clarification stage.
- Post-RGF filter disinfection turbidity decreased by over 50%.
- 35% reduction in ferric sulphate coagulant dosing rate.
Conclusion
Through excellent collaboration between Welsh Water and Mott MacDonald Bentley, this innovative solution to coagulant mixing was completed in November 2023, ahead of programme.
Jet mixing has been successfully implemented and demonstrated to deliver water treatment process benefits and provides an alternative to mixing solution where site constraints make traditional mixing options infeasible.
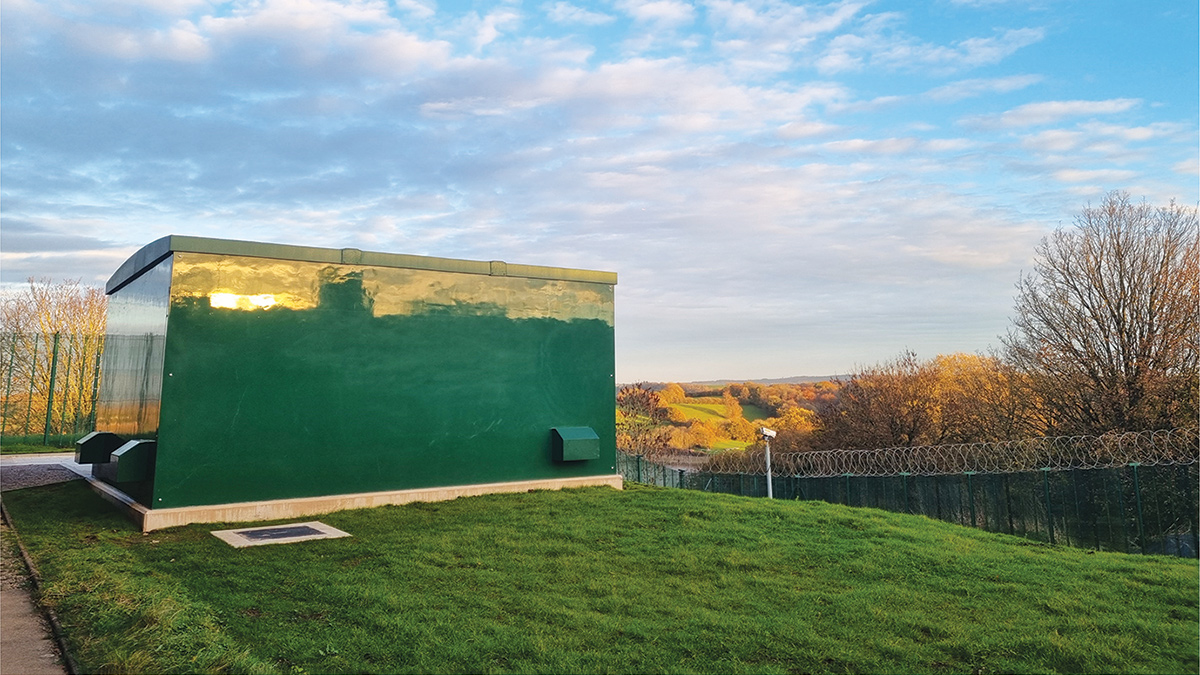
External view of the kiosk - Courtesy of Mott MacDonald Bentley