Southern Water WINEP (2023)
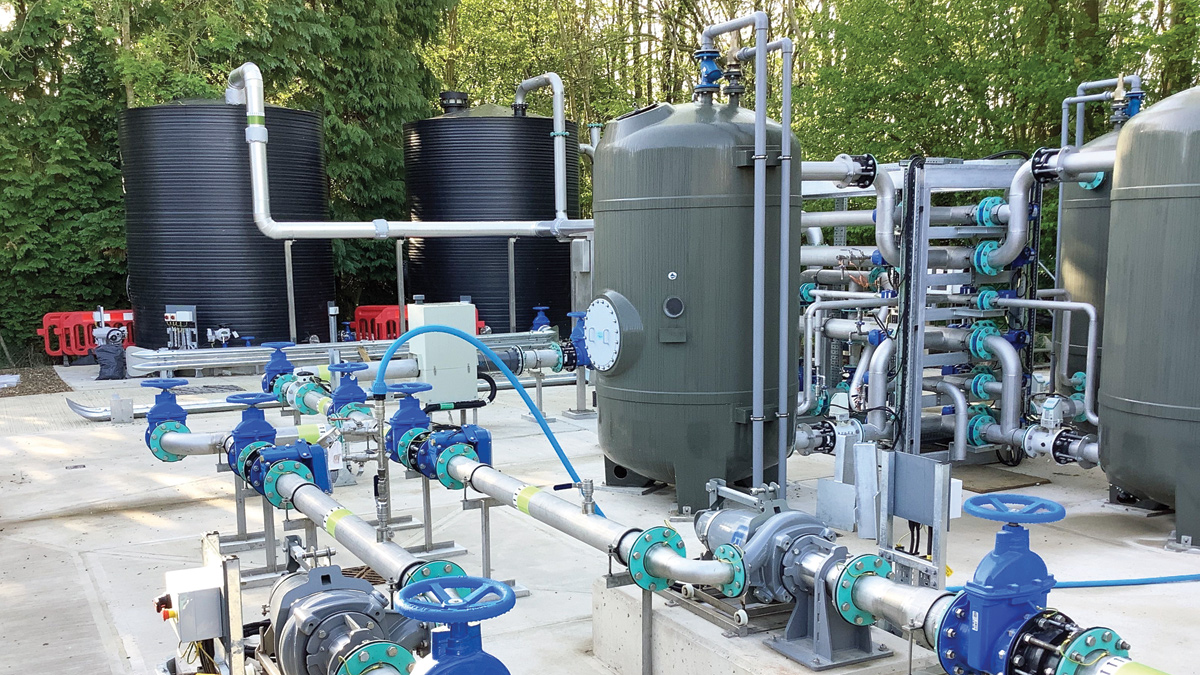
Tertiary treatment plant installation complete with clean and dirty backwash tanks under hydrostatic test - Courtesy of CMDP JV
To ensure compliance with tighter Environment Agency permits for phosphorus removal, the number of phosphorus reduction schemes have quadrupled since AMP5 and is seen by some as one of the biggest challenges ever to face the water industry. The Water Industry National Environment Programme (WINEP) is a programme of actions that water companies are required to undertake to improve the environment and to meet the environmental legislative requirements that apply to water companies in England. Southern Water are undertaking a five-year programme of work, with CMDP JV appointed as framework contractor in 2020 for the east region covering Kent, East and West Sussex and Surrey, along with emergent works in the West, with responsibility for delivering 37 WINEP projects during AMP7.
Design
In collaboration with the design team, a variety of solutions have been delivered, from a small bespoke 1m3 ferric dosing solution at Cherry Gardens WwTW, to larger scale projects such as a 40m3 caustic dosing system along with a 7-lane deep bed sand filter at Scaynes Hill Treatment Works.
Process engineering specialists from CMDP JV (a joint venture between Costain and MWH Treatment) collaborated with Southern Water to review the scope of each site, identifying opportunities for no-build and low-build solutions by optimising existing assets to meet permits. This was achieved by commissioning extended load and flow surveys to pinpoint issues and identify the level of intervention required.
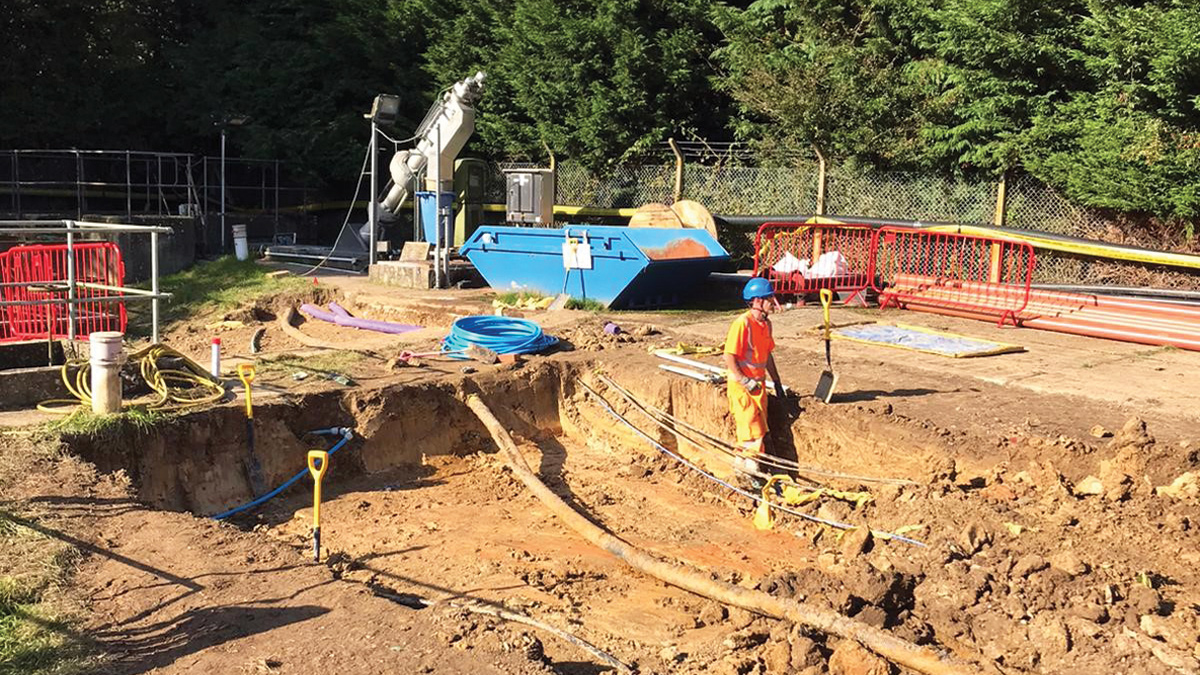
Excavation for sub-slab level ducting and drainage pipework to the chemical dosing kiosks – Courtesy of CMDP JV
This approach identified full no-build solutions at four sites, allowing £8m to be invested in other sites which presented greater risk. CMDP JV also invested in trials at three sites, which helped to establish that the existing tertiary treatment facilities were capable of satisfying the requirement of the new permits, thus providing millions of pounds of savings to Southern Water.
At the start of AMP7, it was decided to undertake the design work in a shared integrated space with Southern Water, CMDP JV, subcontractors and supply chain working closely together to ensure a well thought out, robust design was in place before starting on site. The main objective of this approach was to ensure the on-site delivery and commissioning of the projects runs smoothly and is ‘right first time’.
The team engages with Southern Water in weekly workshops to review design; challenging specifications and value engineering solutions by walking through the design virtually to gain buy-in to the solution and first-time approval at Risk and Value (R&V) meetings. The team approach ensures design consistency and use of standard solutions through a core design team of civils, mechanical, electrical and process designers.
Southern Water WINEP: Supply chain – key participants
- Client: Southern Water
- Delivery partner: CMDP JV
- Civils installation: Coleman Construction & Utilities Ltd
- Electrical installation: Econotech Ltd
- Mechanical installation: Pipe Systems Ltd
- MEICA: Bridges Electrical Engineers Ltd
- MCC/switchgear: MCS Control Systems Ltd
- Tertiary treatment plant: Bluewater Bio Ltd
- Lamella plant: ATAC Solutions Ltd
- Phosphorus & iron monitoring/kiosks: Servitech International
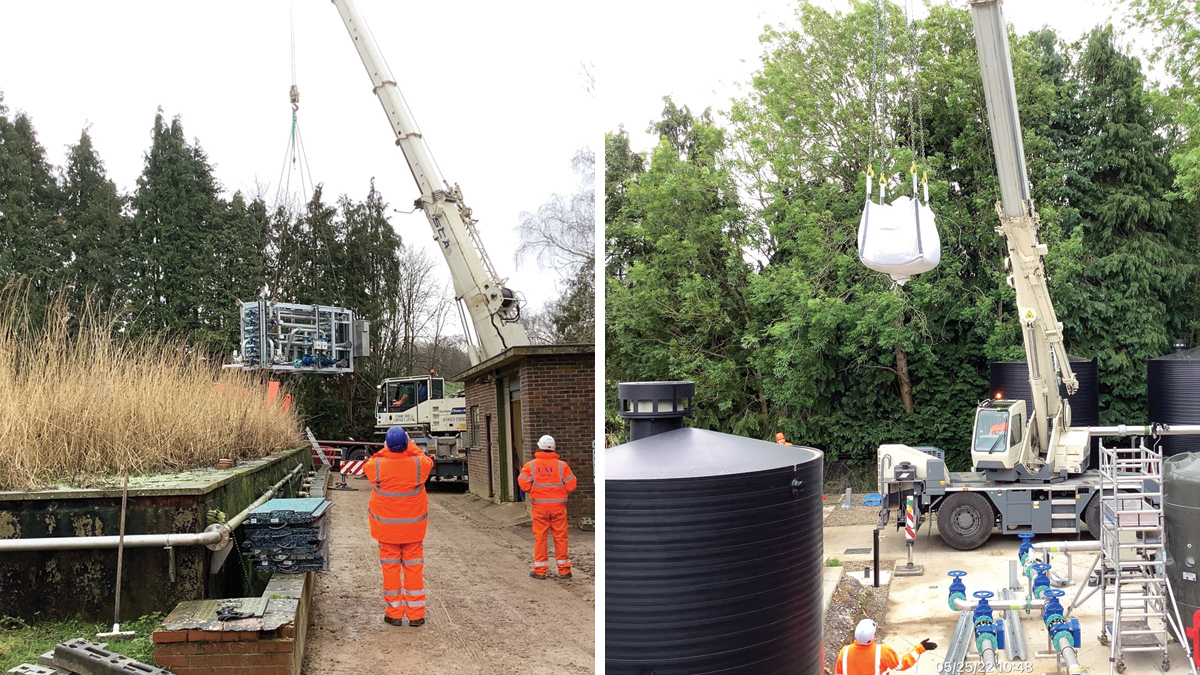
(left) Lifting of tertiary treatment plant, control panel and pipework manifold and (right) loading of media into TTP pressure vessels – Courtesy of CMDP JV
Smart construction solutions
The team has formed strategic relationships with the supply chain partners to retain learning and efficiencies across the WINEP sites. This is helping to support the client in a ‘left shift’ approach, bringing production thinking and constructability expertise into the design phase to enable safe, efficient construction.
Supply chain partners attend constructability reviews with construction delivery leads and the design team to ensure right first-time installation. The use of visual tools such as BIM 360 and Synchro 4D optimise the sequence, resolve interfaces, and develop logistics plans.
One example of this approach bringing programme, budget and environmental benefits, is the review of logistics and collaboration with the client ecologist at Wingham (Dambridge) WwTW. This identified opportunity to reuse spoil in redundant storm tanks to create a new habitat. This saved over 100 lorry journeys, £50,000 in cost and 3.62t CO2e.
Safety focus
Despite working across multiple active projects and tackling a range of challenges including deep excavations, complex deliveries and lifts plus a variety of temporary works, safety has remained the highest priority of all times. This led to the team achieving zero loss of time injuries across the programme during 2022, after 1,986 days worked across the programme.
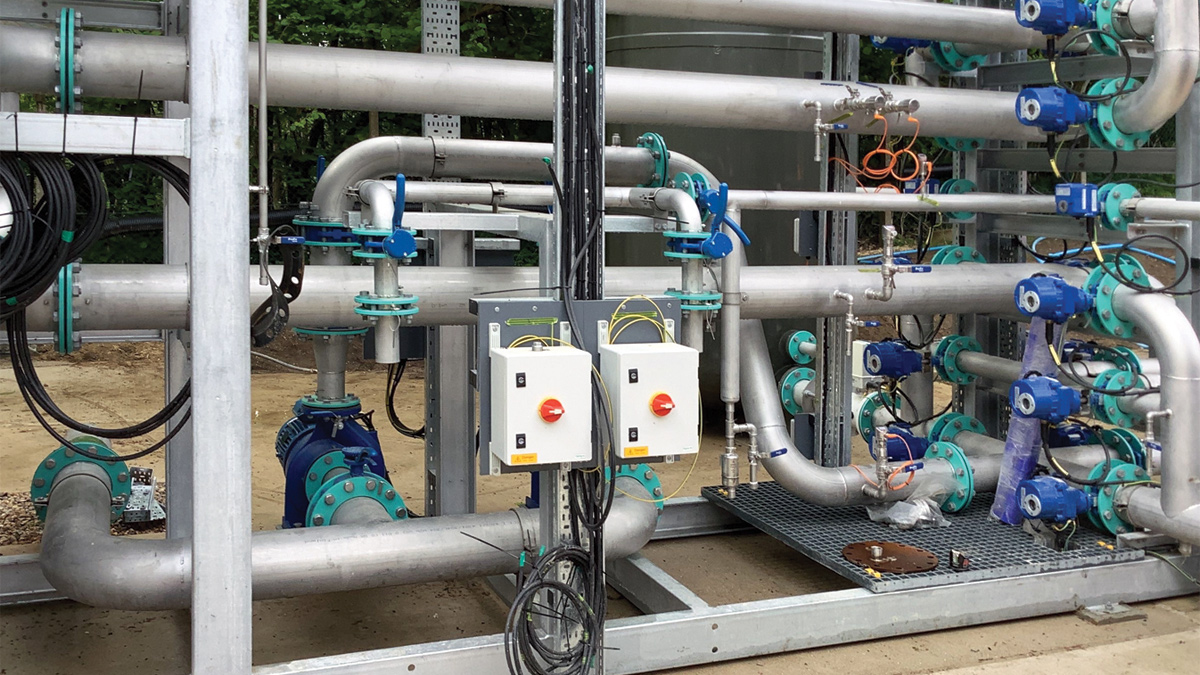
Close-up of pre-fabricated off-site manifold block – Courtesy of CMDP JV
Ticehurst WwTW
One example of where the team has successfully implemented a phosphorus reduction scheme is at Ticehurst WwTW, East Sussex, where the scope of work included:
Chemical dosing
Two dosing plants were incorporated into the treatment plant: ferric and alkalinity. The ferric dosing reduces phosphorus levels, while the alkalinity dosing balances the pH levels, which can be affected by the ferric dosing.
As the ferric dosing acts as a coagulant, increasing the volume of sludge produced, a tertiary treatment plant was installed to filter the final effluent with increased solids, removing phosphorus from the wastewater.
To ensure safety during chemical deliveries, an interceptor chamber was constructed. This will retain any chemicals spilled during the delivery process (eg. in the event of a tanker failure or hose split). Retaining the chemicals within the intercept chamber mitigates the risk of contamination to either the normal site drainage system, which feeds back to the inlet of the works, or the surrounding environment.
Monitoring system
To maintain compliance with regulations, a phosphorus and final effluent monitoring kiosk from Servitech International Ltd was installed. This monitoring system ensures that the effluent leaving the treatment plant meets the required standards. A pH monitor was added to verify the pH levels of the final effluent, guaranteeing its suitability for release.
MCC
A new MCC (motor control centre) was installed; serving as the central control hub and powering the site. Additionally, a new S2000 telemetry outstation was installed. This enables communication between new and existing plant, and Southern Water’s main control centre, enabling monitoring of any alarms on the site.
Potable water supply
To meet the requirements set by Southern Water, a potable water supply was essential for the treatment plant.
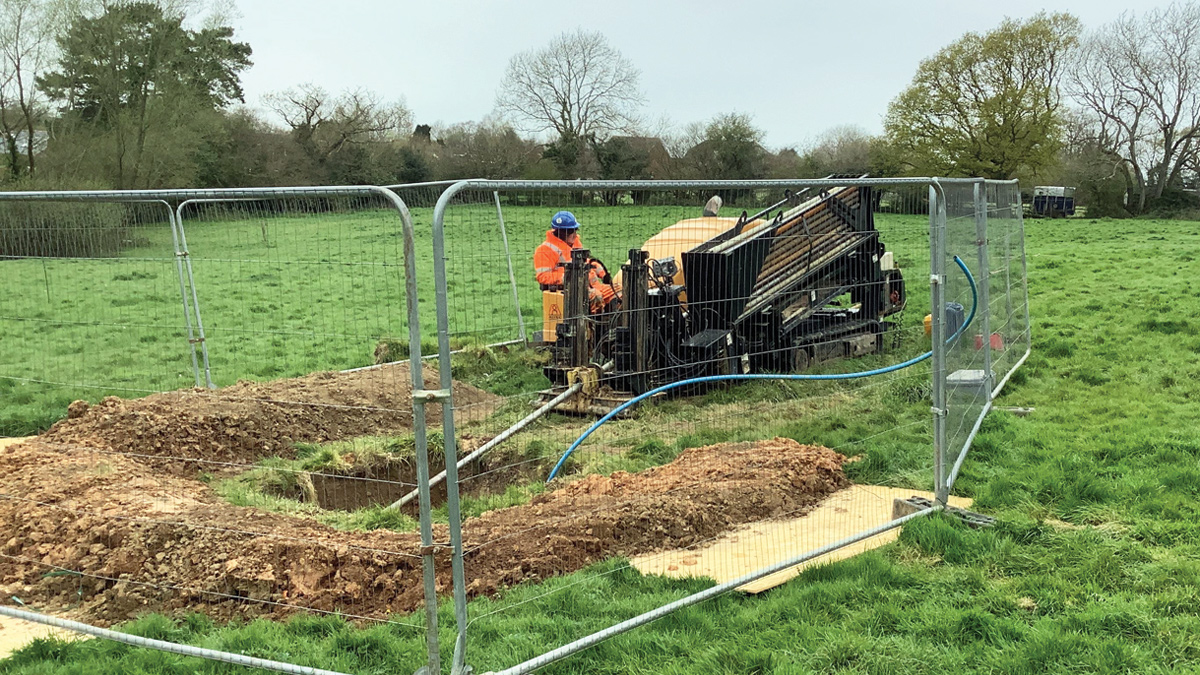
Directional drilling rig completing second drive – Courtesy of CMDP JV
While an existing final effluent water supply was available for plant maintenance activities, the installation of safety showers and eye-baths required access to clean, drinkable water. The nearest connection was 350m away off the site to the west. This required a pipeline to cross private fields and the neighbouring Dale Hill Golf Club.
To reduce the impact on local stakeholders, a directional drilling technique was deployed. This involved deploying a small drill head, which can drive up to 100m underground. This only required a small number of pits to be dug, rather than digging a trench across the whole length of the pipe.
Site access
An additional challenge arose due to the treatment plant’s sole access road, which crosses the golf course. To ensure the safety of drivers traveling along this access road for work or deliveries, close cooperation with golf course management was necessary.
Timetable/progress
CMDP JV commenced site mobilisation in August 2021. Civils works began in October, followed by early M&E installation works which enabled early start of ferric dosing and phosphate and ferric monitoring.
The construction completion milestone was achieved in August 2022, with takeover and final completion due by the end of 2023, following a period of process optimisation. The project was completed with zero safety, health and environmental accidents or incidents.
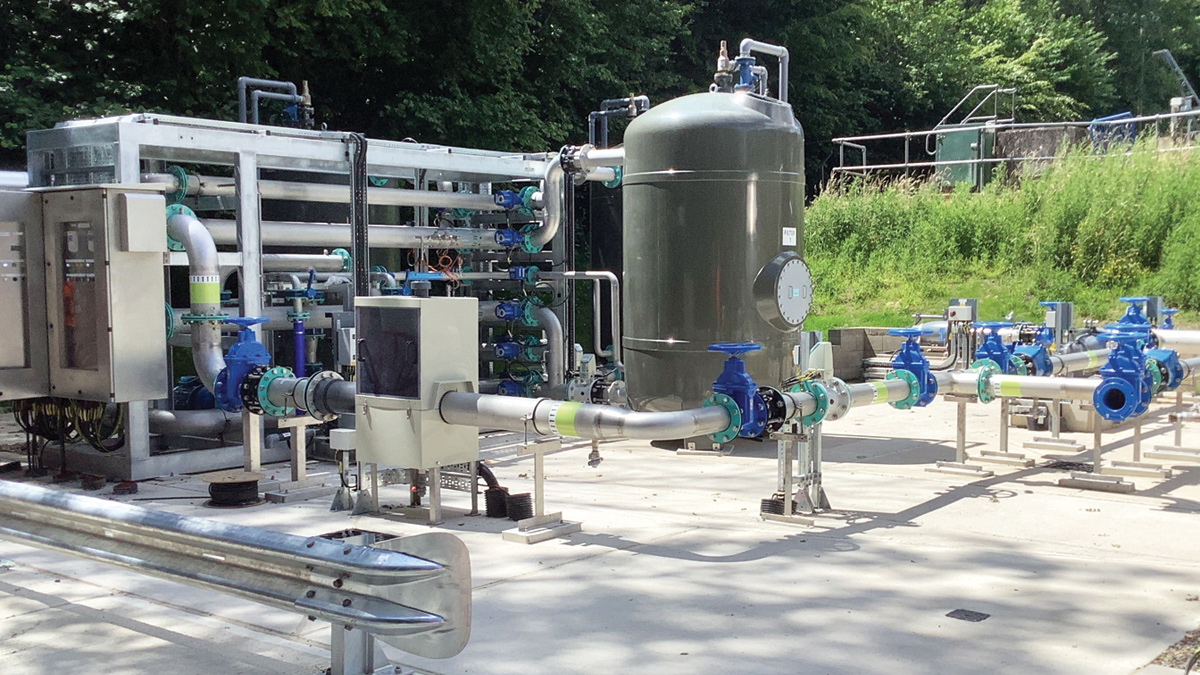
Completed installation of tertiary treatment plant – Courtesy of CMDP JV
Looking forward
CMDP JV will continue to support Southern Water’s WINEP projects, with 18 schemes planned over the next two years to complete Southern Water’s AMP 7 portfolio.
This includes Lingfield WwTW in Surrey, which will include new tertiary treatment, biological trickling filter, installation of a new pumping station, two pumping station upgrades and a new caustic dosing system. At Tunbridge Wells South, work will include a new 22.5m diameter final settlement tank, new caustic dosing and refurbishment of the ferric dosing facilities.
CMDP JV is playing a key role in Southern Water’s response to the challenges posed by WINEP, and will continue to implement learnings from previous works as the programme progresses.