Stithians WTW (2023)
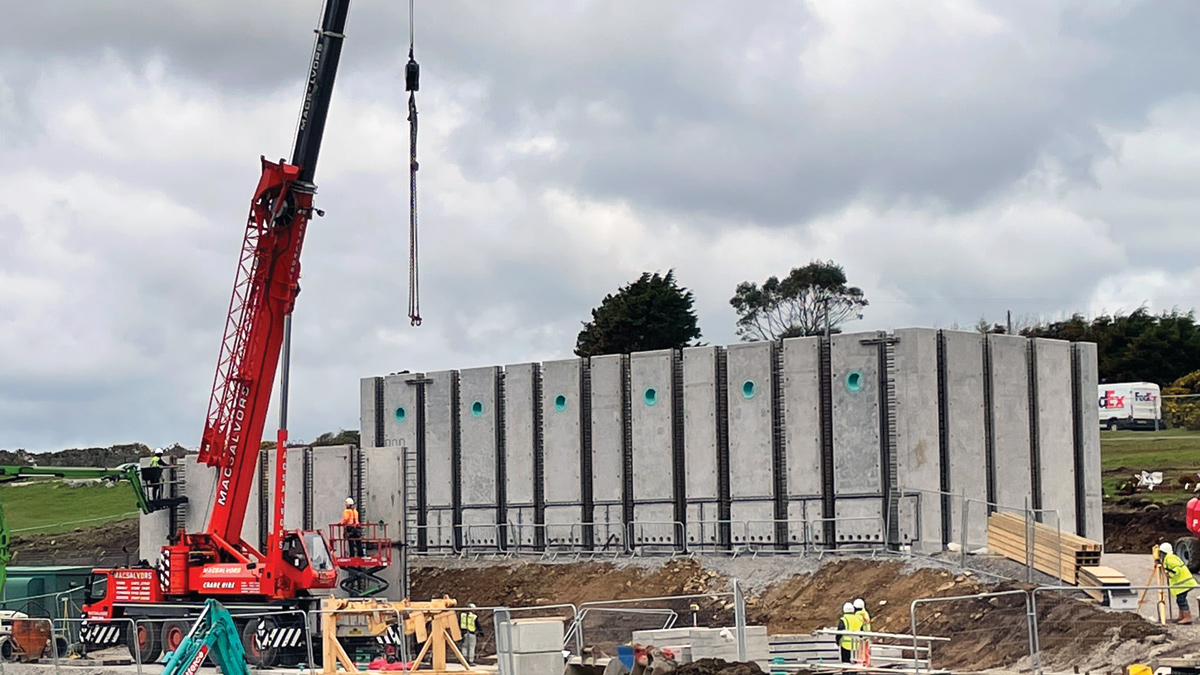
Stithians GAC precast wall installation - Courtesy of Galliford Try
Stithians is a village in Cornwall that lies in the middle of the triangle bounded by Redruth, Helston, and Falmouth. Stithians Reservoir (the largest inland lake in west Cornwall) is the raw water source that supplies a maximum of 27.7 ML/day to Stithians WTW, which in turn supplies a population equivalent of 276,741 in west and south Cornwall. The reservoir, formed in 1965, has an area of 1.08 km2 and a gross capacity of 5,415 ML. Stithians dam is recognised as the windiest inland water in the south-west due to the featureless surroundings and its geographic elevation.
Project summary
Galliford Try was contracted by South West Water to design and build a new Granular Activated Carbon (GAC) water treatment plant to target a 25% reduction in THMs (a group of volatile and potentially toxic chemicals formed during water treatment with disinfectants, such as chlorine), manganese removal, and improvements to taste and odour. The scheme was designed to maximise off-site build opportunities as this reduces error and waste and aligns with Galliford Try’s net zero carbon strategy, eliminating possible dangerous in situ site construction issues, thereby improving safety during construction.
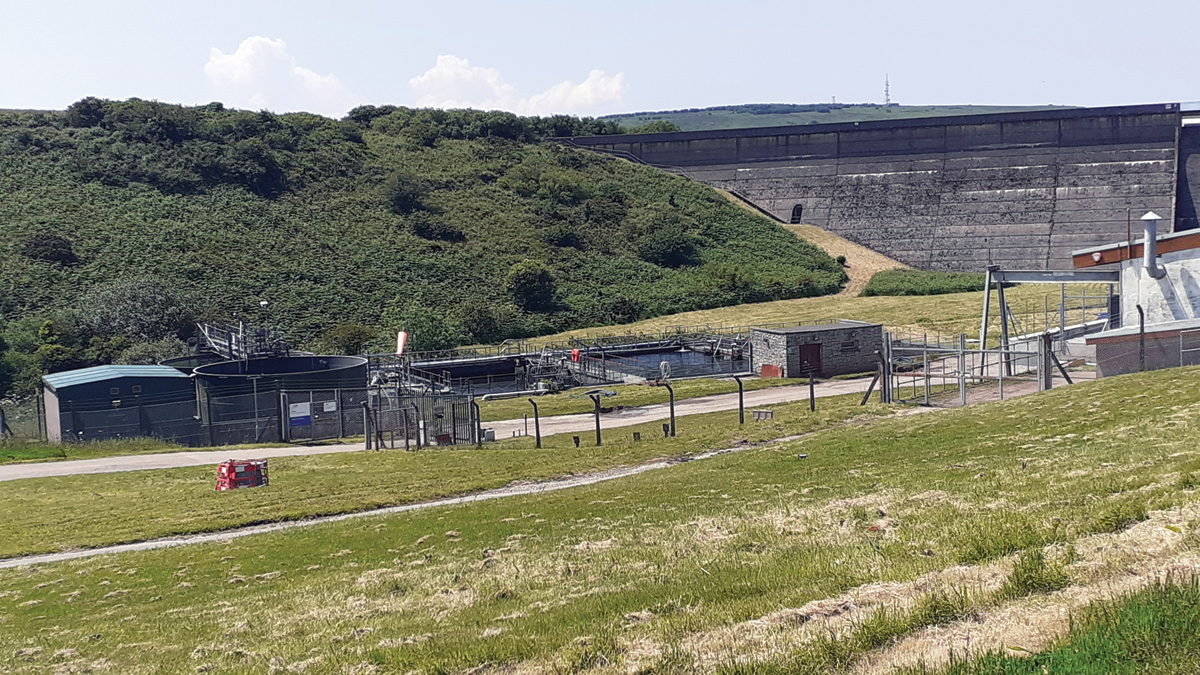
Stithians WTW and Stithians Reservoir dam prior to the commencement of the works – Courtesy of Galliford Try
Design
The new plant will be fed from the existing rapid gravity filters and pumped up to the new GAC contactors via the new interstage pumps and pipework. The design has utilised the site’s topography by siting the GAC contactors at the top of the hill, so the clean and waste flows can gravitate back down the hill, through the downstream processes (UV, contact tank, sludge plant) and then be transferred into the network via the existing pumps and main network pipelines. Galliford Try ensured that the design utilised the steep incline through the site. Over time, these subtle efficiencies will have a positive impact on the sites long term net operational costs.
Project scope
- New interstage pumping station from the existing primary filters.
- Chlorine dosing system for manganese oxidation and lime dosing for pH correction with an in-line static mixer.
- GAC plant downstream of existing rapid gravity filters.
- Clean backwash pumps.
- Regeneration waste tank.
- UV plant downstream of new GAC plant.
- Chlorine contact tank.
- New sludge thickener to provide additional treatment capacity for site produced sludges.
- Modifications to existing contact tank and existing high lift pumps pipework.
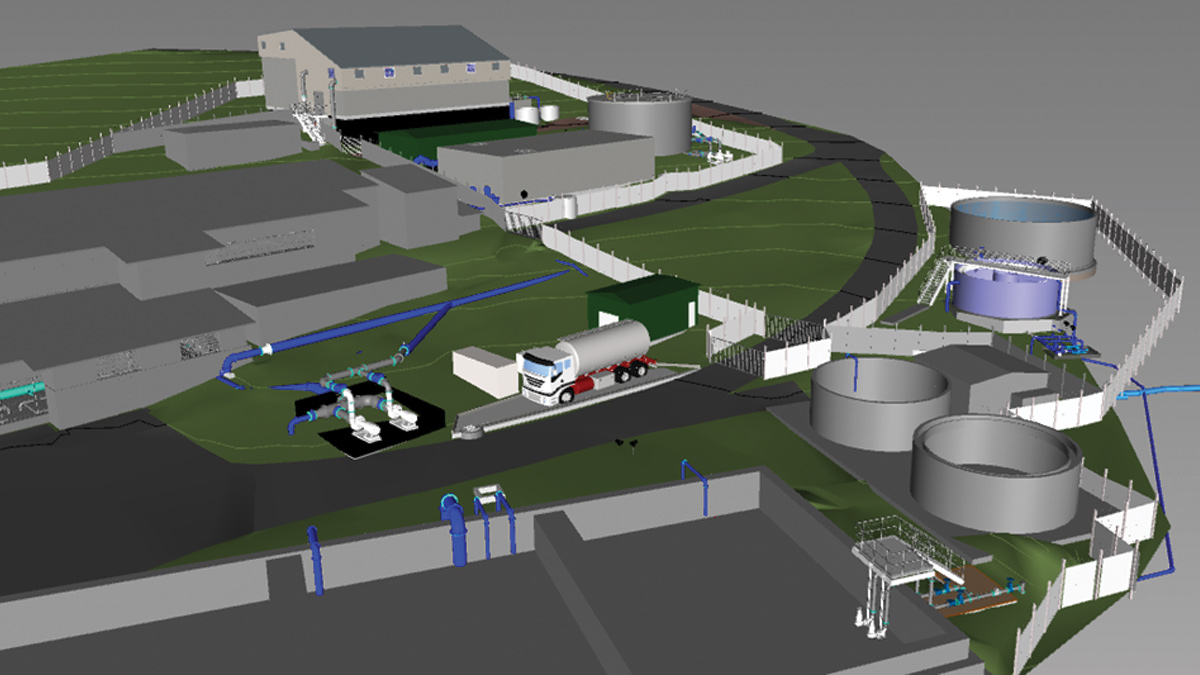
Model extract showing the existing works on the left, the new process plant on the right, and the GAC at the top of the slope – Courtesy of Galliford Try
Preparation, planning and early engagement
FLI Precast was engaged very early in the design stage and their programme was built into the main Galliford Try programme and weekly collaborative planning meetings were held with the site team as work progressed. FLI Precast and sub-contractor Freeflow Pipesystems were used to enable cast in wall couplers to be procured and sent to Ireland to allow early production of wall units to ensure a prompt start on site once the contract was signed for design to commence. The design also had to allow for three access roads which cross the construction area, all of which had to be always kept open for operations in order that they were able to receive delivery of process critical chemicals, on a regular basis.
Construction
Construction commenced in January 2022 with the GAC foundations being prepared for the delivery of the precast wall panels initially for the GAC and then the chlorine contact tank sitting lower down the slope. The GAC building is a critical element of the programme as the internal fit out is complicated and time consuming, comprising pipework, valves, dosing and sampling boards and electrical panels.
Off-site build was chosen as the fastest way of erecting the building to contain all the pipework, control cabinets, valves and sampling panels which are contained within being installed quickly.
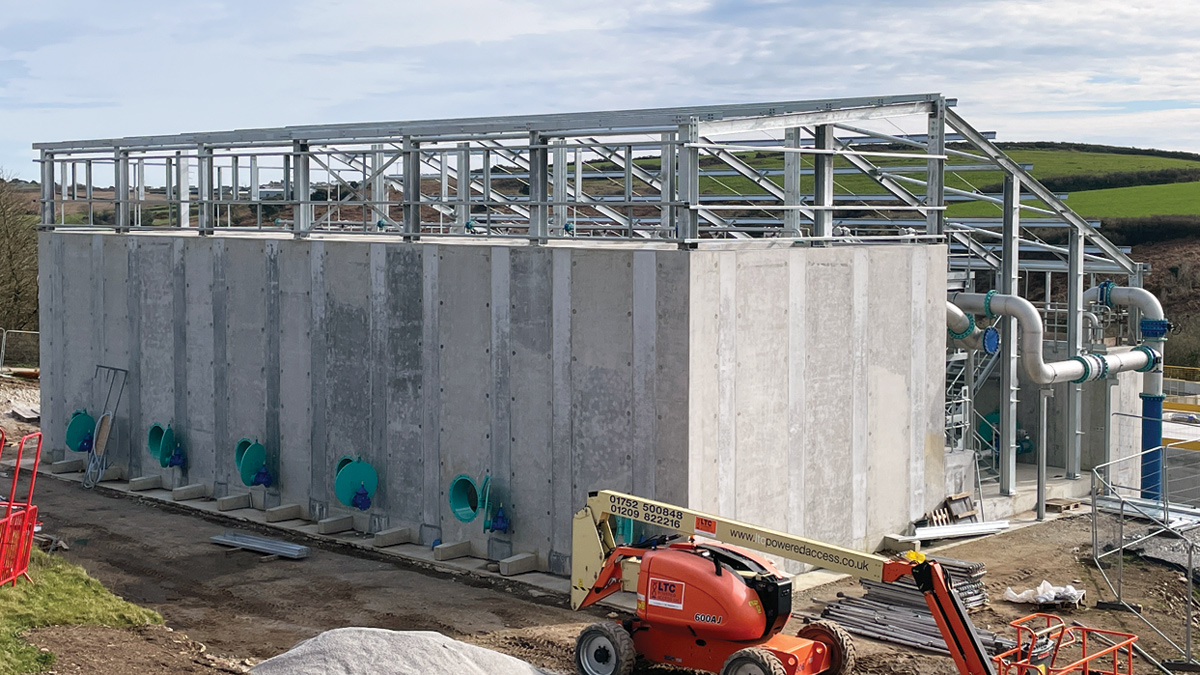
Stithians GAC steel frame prior to cladding – Courtesy Galliford Try
Off-site build was also the chosen methodology for the chlorine contact tank, the clean backwash storage tank and the rinse/regen tank, all of which were precast concrete panel system installations. The new sludge thickener tank was designed as glass coated steel, again off-site built with fast installation time.
Precast concrete storage tanks were the next structures to be completed, at the same time as the underground pipework. All the structural elements have been linked together with process pipework and an extensive underground cabling network links them electrically back to the main South West Water control room.
Stithians WTW: Supply chain – key participants
- Client: South West Water
- Main contractor: Galliford Try
- Civil engineering & process design: Arcadis
- Precast design & installation (GAC & chlorine contact tank): FLI Precast Solutions Ltd
- Wall couplers: Freeflow Pipesystems Ltd
- Precast design & installation (regen & clean backwash tanks): A-Consult Ltd
- UV disinfection: Wedeco Ltd
- Flow control valves/actuators: AFFCO Flow Control UK Ltd
- MCCs & LVDB: Galliford Try
- Electrical installation: Drew & Co Ltd
- GAC pipework & support steel: Alpha Plus Ltd
- GAC control valve actuators: Rotork Controls
- GAC steel frame & cladding: Hewaswater Engineering Ltd
- Standby generator: DTGen
- Sludge thickener: DD Engineering Ltd
- GAC launders & Leopold flooring: Xylem Water Solutions UK Ltd
- Media: Western Carbons Ltd
- Miscellaneous metalwork: Minear Engineering Ltd
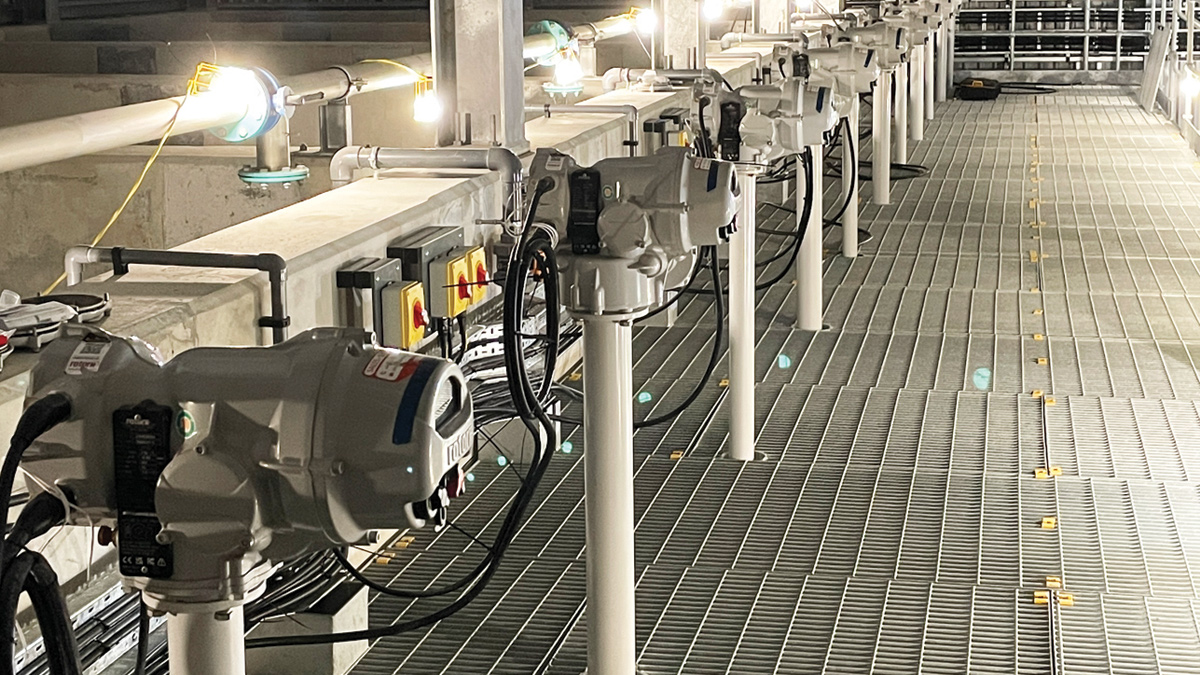
Inside the GAC gallery: Upper level control valves and valve actuators from Rotork Controls – Courtesy of Galliford Try
Savings
300T of site-won material was re-purposed to construct gabion basket retaining walls, saving material being sent to landfill, and approximately 40 additional vehicle movements to and from site which equates to a saving of 51 tonnes of carbon and approximately £75k of capital cost.
Local resources and materials were also utilised. Subcontract packages requiring a large site presence were all local and where local suppliers were not available, Galliford Try used off-site build solutions extensively to reduce carbon and minimise risk.
Safety & environment
A very experienced team of site operatives was key to service strike avoidance. Good early GPR (ground penetrating radar) scanning and existing client information was utilised by the designers.
Project specific surveys incorporating Matterport scanning of existing buildings, boreholes, trial pits and topographic surveys, were also undertaken prior to the start of scheme. This allowed for the BIM model to be built containing location information for all the existing services to prevent clashes and provide the site team a comprehensive picture to help prevent service strikes, by allowing trial holes to be accurately and safely excavated.
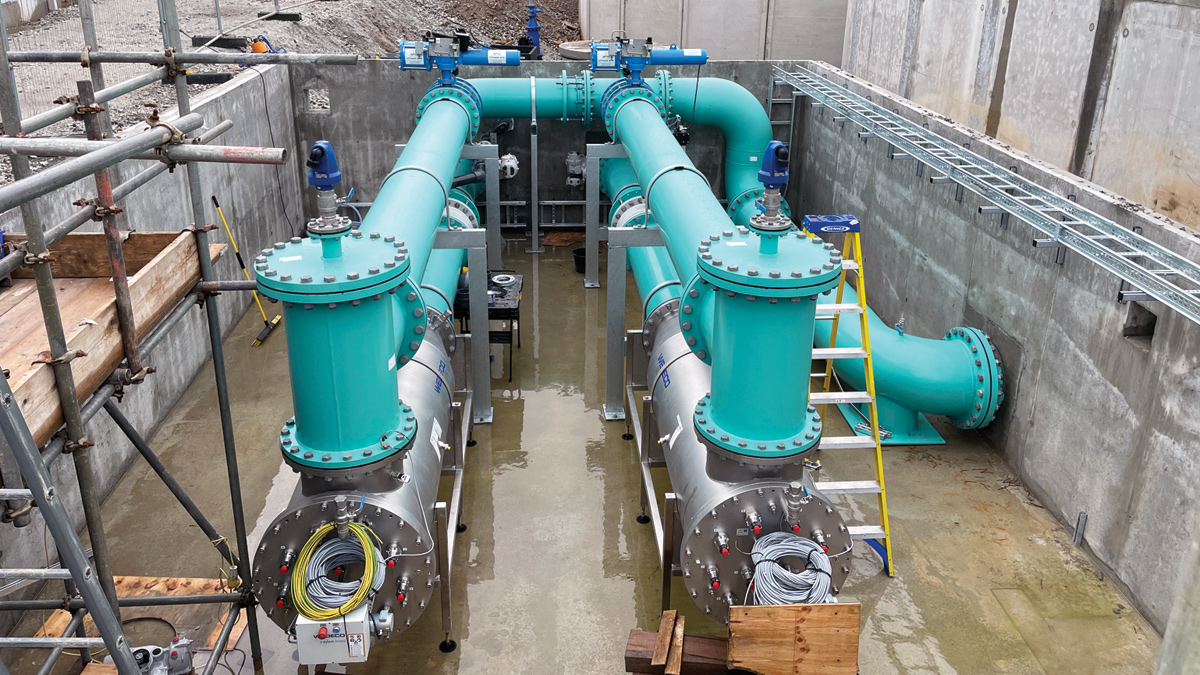
UV building process pipework and support concrete for GRP kiosk – Courtesy of Galliford Try
Communication
Regular letter drops were undertaken to local residents to keep them informed of busy delivery times and works progress. Client operations were involved in all monthly progress and programme meetings, alongside weekly updates of on-site activities.
Status
At the time of writing (July 2023) all the main civils structures have been constructed, GAC building, chlorine contact tank, UV building, chlorine contact tank, regen and clean backwash tanks, sludge thickener, and various concrete slabs for a standby generator, interstage pumps, sludge pumps and control kiosks.
Cabling works are now underway along with final pipework connections, and commissioning works will take place in the coming months for completion in December 2023.
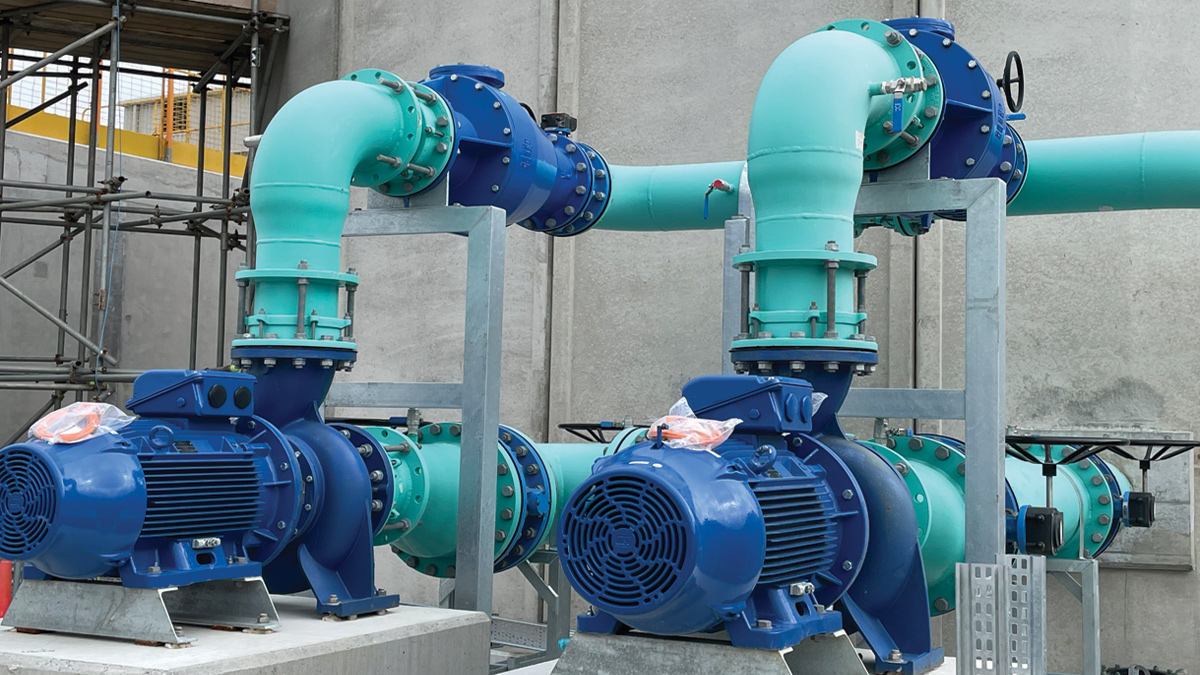
Clean backwash tank pump station - Courtesy of Galliford Try