Stoke Bardolph – Energy Crop AD Plant (2018)
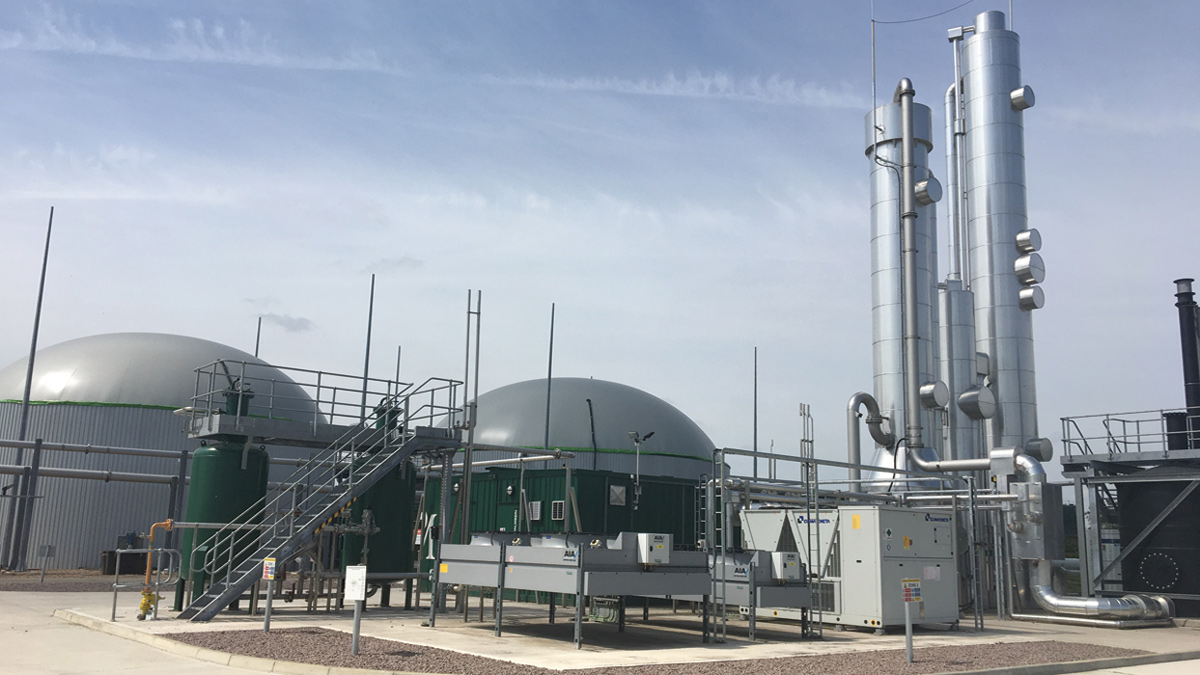
The completed biomethane upgrade plant - Courtesy of Severn Trent Green Power Ltd
In August 2010, Severn Trent commissioned its energy crop anaerobic digestion plant at Stoke Bardolph, Nottingham. It was built to help power the nearby sewage treatment works using crops grown on contaminated farmland which is not suitable for food production. The energy crop plant was sized to convert 37,000 tonnes of maize silage each year into a methane rich biogas to fuel 2 (No.) 1MWe combined heat and power plants (CHP). The CHP units would in turn generate 15GWh of electricity each year, as well supplying the heat demand for the AD process. In 2012 a third 1MWe CHP was added and, with the assistance of consultant Schmack Biogas, the plant was expanded to process 54,000 tonnes per annum.
Project driver
The addition of a third CHP in 2012 increased the electricity generation on the site to 23GWh per annum but any further expansion was limited by the organic loading rate on the digesters and network restrictions limiting the amount of embedded generation capacity.
To comply with the recommended maintenance schedule, the plant was completely drained down for inspection and refurbishment in 2017. However, taking the plant out of service for a prolonged period would result in a significant impact on production and loss of income through reduced feed in tariffs and electricity sales.
To mitigate this in 2016, a business case was developed which sought to combine the planned refurbishment with additional investment which would increase the size of the plant, adding in a third digestion stream to increase plant output and to upgrade a proportion of the biogas produced suitable for grid export. The new expanded plant would be capable of processing 89,000 tonnes of crop silage and would produce 44GWh per annum (electrical equivalent). By increasing the size of plant to incorporate three process streams meant that downtime during refurbishment could be minimised through careful sequencing of the work.
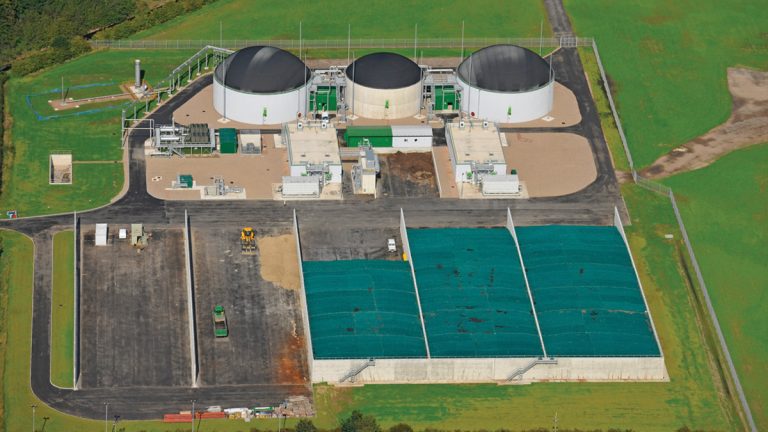
Aerial view of plant commissioned in 2010 – Courtesy of Severn Trent Green Power Ltd
Scope of works
In June 2016, a £6m design and build contract was let to North Midland Construction (now Galliford Try), the scope of works comprising:
- Construction of 5 (No.) additional reinforced concrete silage clamps measuring 75m x 25m x 5m.
- Construction of a new third process stream comprise a new 100T wet feed system and a new 4,000m3 heated digester complete with double membrane gas roof.
- Complete refurbishment of the 2 (No.) existing process streams comprising new 100T wet feed systems, refurbished primary and secondary digesters.
- Refurbishment and conversion of a 2,700m3 storage tank into a heated a digester.
- Upsizing and reconfiguration of all biogas pipelines to incorporate a new gas feed pipeline to the biogas upgrade plant and to a new upsized emergency flare.
The AD plant expansion timeline
To minimise downtime and to maintain the maximum amount of living digestate in the process at any one time, a phased approach was adopted. Phase 1 would be to establish the new third AD process stream first which included for a new 4,000m3 heated digester and new 100T wet feed system. After dry commissioning, 4,000m3 of digestate at 40°C was transferred from AD Stream 2 to assist with the wet commission of AD stream 3.
On upon successful commissioning of AD stream 3, AD stream 2 was fully emptied and taken out of service for refurbishment. During this process 1200m3 of surplus digestate was recycled to farmland By maintaining the live biology of the digestate throughout, biogas production was maintained and losses due to plant refurbishment were minimised.
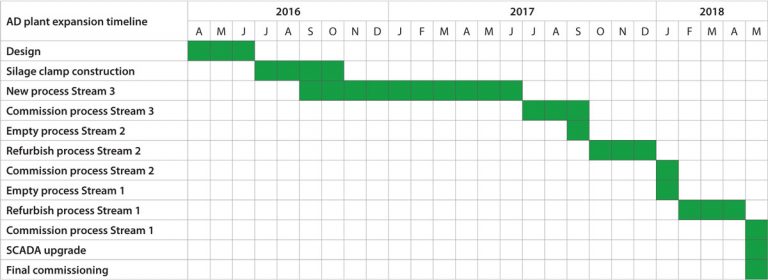
The AD plant expansion timeline
AD process stream 2
The refurbishment of AD stream 2 comprised:
- Emptying, cleaning and inspection of the primary digesters.
- Replacement of mixer bearings and refurbishment of gearboxes and agitators.
- Installation of new double membrane roof and desulphurisation membrane.
- Installation of a new 100T wet feed system which combines dry feed silage with digestate recycled back from the secondary digesters.
- Replacement instrumentation and controls.
When AD Process stream 2 had been dry commissioned, it was brought back into service using digestate from AD stream 1.
The refurbishment of AD Stream 1 was completed in a similar manner to AD stream 2. Upon inspection, the concrete structures were found to be in a good state of repair and whilst the need for some localised concrete repairs were expected, none were actually required. Refilling of AD stream 1 was achieved through a combination of increased feeding from the new upsized feed system but this was supplemented by importing 1500m3 of digestate from other third parties nearby. This was done to reduce overall plant commissioning time and to get the plant operating at full output as soon as possible.
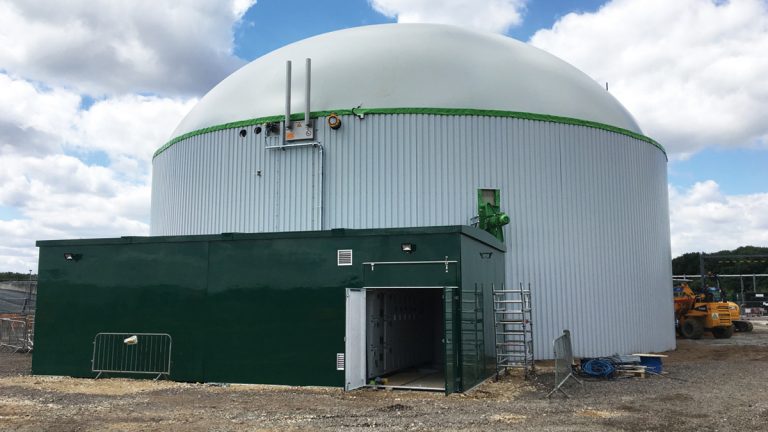
New 4000m3 digester – Courtesy of Severn Trent Green Power Ltd
Ahead of schedule
Through collaborative planning of all construction and decommissioning/recommissioning activities, the project was completed five months ahead of schedule and within budget. In addition, whilst a reduction in output was initially expected due to the refurbishment works, the plant actually achieved an output of 26GWh in 2017/18; 3GWh higher than in the previous year.
Gas to grid
In parallel with the AD plant Expansion, a separate £5m D&B contract was awarded to North Midland Construction for the provision of a new plant to upgrade biogas to biomethane and inject it in to the gas grid.
This AD plant previously utilised the biogas in its 3MW capacity combined heat and power (CHP) plant to be self-sufficient in electricity and heat required for the energy crop and sewage treatment process. Surplus electricity can be readily exported to the grid to offset our use on other sites, but It is not as easy to find a local cost effective use for surplus heat. For four months of the year the majority of the heat generated can be used efficiently in the energy crop and sewage treatment process but in the warmer months typically 1.5MW of heat was vented to atmosphere.
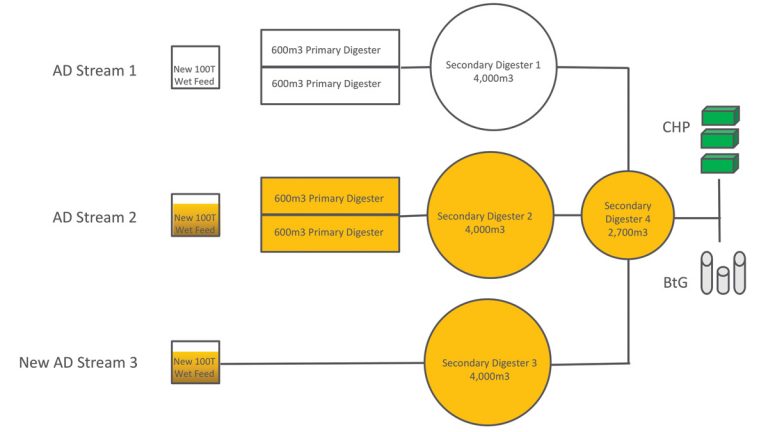
Phase 2: Commission Stream 3 , refurbish Stream 2 – Courtesy of Severn Trent Green Power Ltd
Upgrading biogas to biomethane
To maximise the efficient use of the available biogas renewable energy resource, a new plant was built to upgrade the biogas to biomethane for injection in the gas grid. The new ‘green gas‘ process makes more efficient use of the biogas that is generated, so it can be used safely as a substitute to natural gas in local homes.
The mix of CHP and biomethane plant allows Severn Trent to meet the site energy demands and export any surplus in an efficient and environmentally responsible manner.
The biogas is made suitable for use in homes with a simple process which involves some complex engineering techniques. The biogas composition received from the AD plant is 55% methane, 45% carbon dioxide (CO2) with traces of hydrogen sulphide (H2S). The energy in the biogas is contained in the methane so all the other components need to be removed.
Water wash process
The CO2 and H2S are removed from the biogas to upgrade it to biomethane by a physical absorption water wash process known as scrubbing. A Malmberg water wash upgrade plant was selected. The pressure, temperature and contact times are optimised so that the CO2 and H2S are absorbed in to re-circulated process water and the methane is not.
Through this process over 98% of the methane is recovered. The remaining biomethane is then dried before passing through a granular activated carbon filter to the next stage of the process.
The CO2 and H2S are then de-absorbed from the process water and filtered through granular activated carbon to remove any odour before being vented. The process water is continuously recycled with a typical usage rate of 1m3/day.
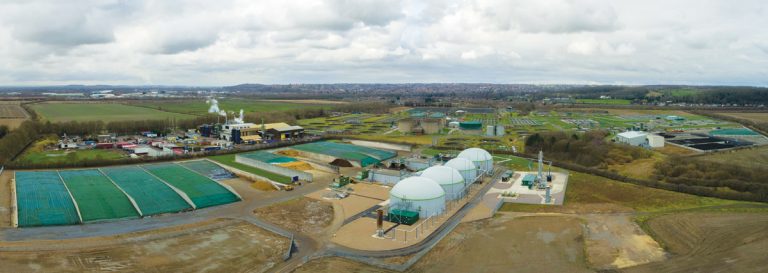
Completed AD plant – Courtesy of Severn Trent Green Power Ltd
Grid entry unit
Finally before any gas can flow to the grid the quality and volume of biomethane is measured in a grid entry unit to ensure that the gas meets the gas network entry requirements. Thyson Technology was selected to provide this equipment.
Because all the poisonous H2S is removed from the biogas it is odourless. A non-toxic odorant is then injected in to the gas to make it smell exactly like the grid gas. If required the energy value of the biomethane is matched to the gas grid by the addition of propane.
Summary
Stoke Bardolph Energy Crop AD Plant expansion and biomethane export: Key facts and figures:
- The biomethane plant is designed to process 1,100NM3hr of biogas in to 600SM3hr of biomethane.
- The capital cost was £5m.
- The project was commissioned in 2016 to a tight programme to accredit to the RHI.