Wark on Tyne STW (2024)
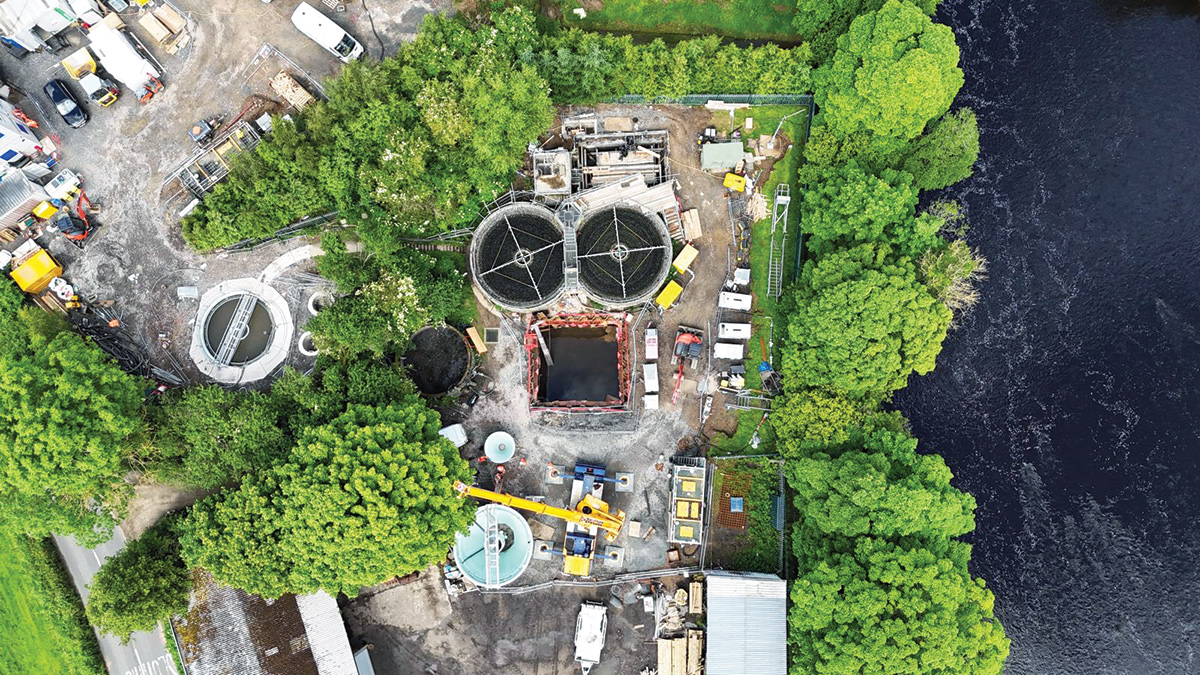
Wark on Tyne STW under construction - Courtesy of Mott MacDonald Bentley
Under the Urban Wastewater Treatment Regulations for improvement, Wark on Tyne STW in Northumberland was included within Northumbrian Water’s WINEP (Water Industry National Environment Programme) during Asset Management Plan 7. The works required an upgrade in line with the U_IMP5 Flow driver, which introduced a change to the consented full flow to treatment (FFT). As well as this, there were other WINEP obligations including U_MON3 and U_INV2, all of which are to be implemented from 31/03/2023. Fundamentally the objective of the U_IMP5 driver is to: (i) ensure no overflow into storm tank on dry days and (ii) enable storm tanks to be returned as soon as reasonably practicable after rainfall.
Identifying the proposed FFT
The WINEP Enabling Project undertook a review of the U_IMP5 methodology, identifying the proposed FFT to ensure compliance with the above objectives. As part of the permit revision for FFT, the respective values for P, G, IMAX, and E were used to bring the permitted DWF into alignment too. A capacity assessment of major process units was undertaken under the enabling project, to identify the investment required to ensure compliance with the driver due to the increased FFT and the change to DWF.
The final contract scope was to replace the PST and HST, as well as modify the storm tanks and inlet works.
Existing works
Wark on Tyne STW consisted of a narrow inlet channel with storm overflow, which fed an inlet pumping station with two fixed speed pumps, installed as duty/standby. The pumping station pumped flows to two pyramidal primary tanks with distribution and collection chambers. The storm overflow was connected to the two storm tanks with combined volume of 34.6m3.
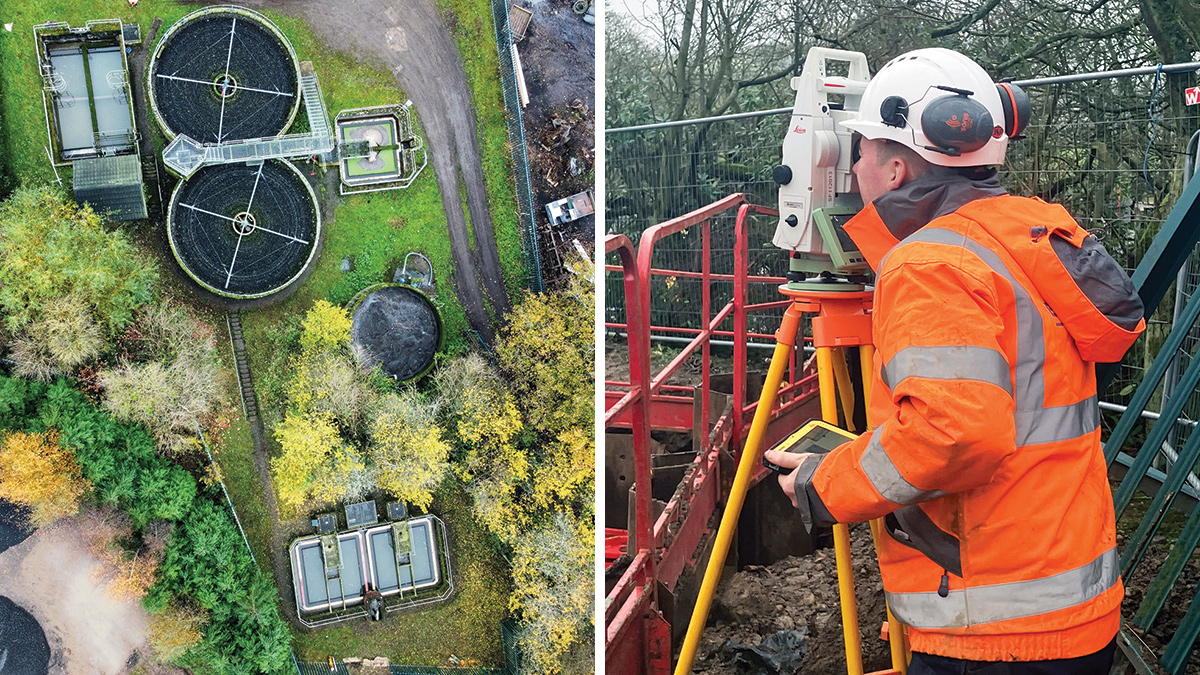
(left) The existing Wark on Tyne STW pre-construction and (right) digital surveying – Courtesy of Mott MacDonald Bentley
From the primary tanks, two biological filters were gravity fed, which in turn fed two pyramidal humus settlement tanks with humus sludge returns to the inlet pumping station. Primary sludge was stored within a dedicated sludge storage tank prior to tankering off site. There was an existing MCERTS UMON 3 storm tank spill flow meter at the inlet pumping station building with a local display and an FE flow meter on the outlet to the watercourse, again with local display. The required contracted scope of works to meet the drivers included:
- Installation of an actuated penstock to the inlet works for FFT control.
- Installation of a Siris Flume, UMON4 flow meter, and an actuated penstock valve to the blind tank for the site returns.
- The upgrade of the two pumps within the inlet pumping station including new local isolation.
- Modifications to the storm tanks and pumping station to allow the correct amount of DWF storage on site.
- Modifications/relocation of various sensors.
- Replacing both the primary settlement tanks and humus settlement tanks with GRP conical types to treat the new FFT.
- The upgrade of the biofilter arms to meet new FFT requirements.
New consent figures
The new consent figures are shown in the table below:
Parameter | Existing consent | Revised consent |
Discharge rate FFT(Vs) | 2.7 | 7.6 |
Dry Weather Flow (m3/d) | 146 | 146 |
BOD (mg/l) | 40 | 40 |
TSS (mg/l) | 70 | 70 |
NH4N (mg/l) | 30 | 30 |
Digital delivery
Wark was selected as a project to drive digital delivery. Due to Wark being a less complex scheme in comparison to others within the programme, it was perfect for the first implementation of intelligent piping and instrumentation diagrams (P&IDs), design acceptance and build from model. The funding for the digitalisation project was embedded within the original design budget with the reduction in drawing production outweighing the development costs to implement the new process.
Traditional delivery can be cumbersome; old information such as-built drawings can be difficult to find, necessitating additional survey work. Residual risks are not readily identified, and previous lessons learnt are lost. Furthermore, engagement from the supply chain and construction staff can also be limited as they focus on one aspect of site at a time. Additionally, site support from design teams can prove time consuming, particularly where significant rework through design stages and completion documentation is necessary.
The objective of using digital delivery on Wark was to bring together best practice from across the water sector and other industries to streamline delivery in design and on site. The project aimed to reduce programme and costs whilst increasing engagement and safety from construction, the supply chain, and operations staff.
Finally, from a client perspective, leaving a legacy with the handover of a digital shadow to streamline operations, maintenance, and future projects on site.
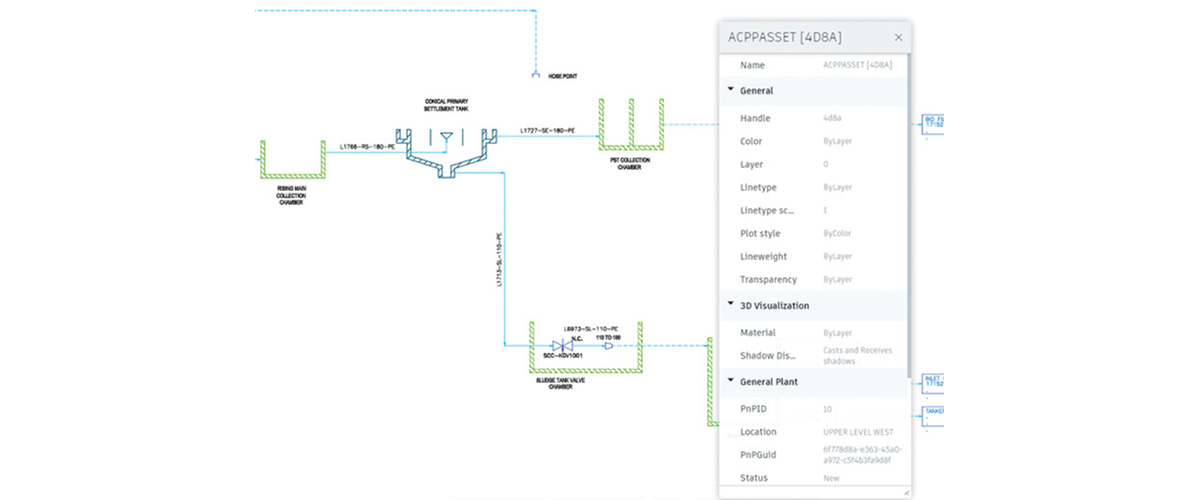
iPID screenshot – Courtesy of MMB
At the outset, a digital delivery plan was developed to identify which technologies and software were to be implemented. These included:
- Digital surveys including photogrammetry, LiDAR (light detection and ranging) and GPR (ground penetrating radar) were used to enable the build of an initial digital model of the brown field site.
- P&iDs were implemented to embed key metadata and asset tagging.
- Supply chain imported their assets directly into the digital model.
- Design acceptance was given from the client, using only the model rather than drawings.
- Access, lifting and maintenance (ALM) assessments were carried out using virtual reality.
- Synchro software for 4D digital rehearsal was used to simulate the build programme.
- The site team then built from the model rather than drawings. Operatives trained on the Leica Icon instrumentation can import sections of the model directly into their setting out equipment.
New processes to implement these major changes were agreed to identify the input and boundaries of the key stakeholders. The team researched across industries, drawing upon experience within oil and gas to develop internal quality assurance gateways to give confidence to the client and to implement their feedback.
Bringing all these digital delivery aspects together meant completely changing standard design practices with which the team and the client were familiar.
The use of Intelligent P&IDs is not yet established practice within much of the water industry, meaning that the procedures and workflow for this were still being developed during implementation. Senior mechanical, electrical and process engineers, external to this project, were engaged throughout to govern this, using their extensive experience.
BETA testing the intelligent P&IDs resulted in schedules being produced automatically, resulting in one source of the truth. This resulted in reduced errors, automated cross checking, and a greatly reduced programme. The same intelligence was also incorporated in the PFDs, again reducing design programme and error.
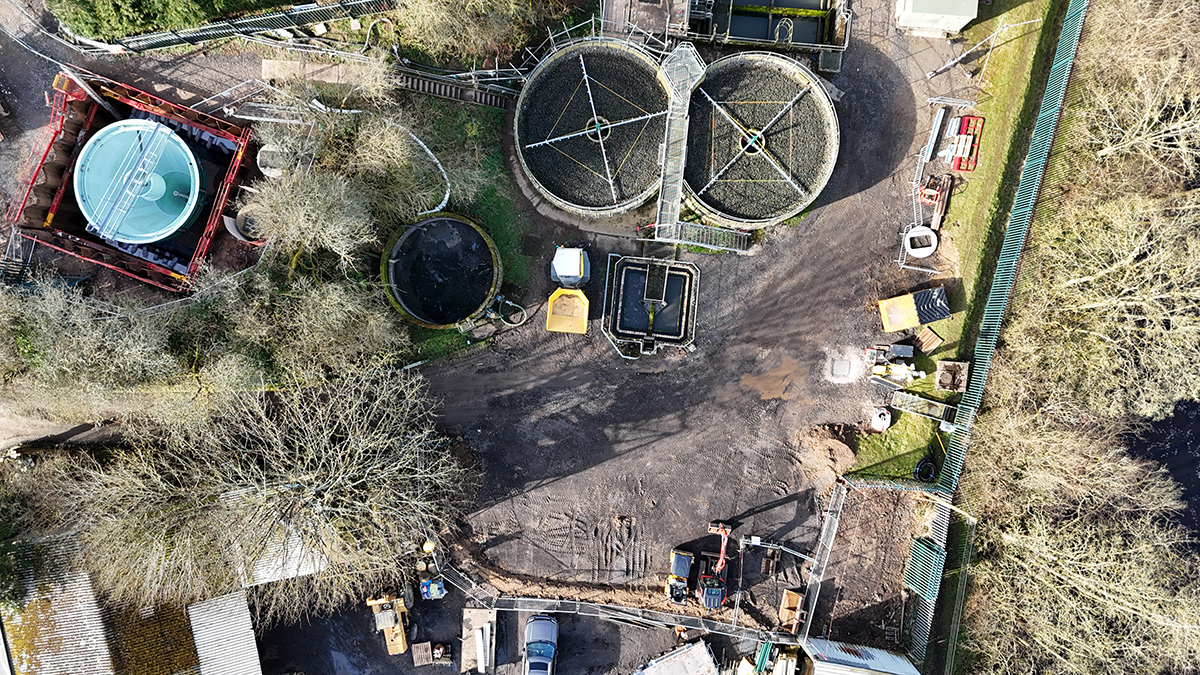
Wark on Tyne STW during construction – Courtesy of Mott MacDonald Bentley
All suppliers on Wark were engaged early, with 3D models requested to make the model build as seamless as possible. Discussions with the suppliers revealed that many of them design in 3D by default, and issue drawings following the model build. Therefore, requesting model data reduced their own workload and resulted in a quicker design turnaround. The digital shadow built to enable the ease of design acceptance and handover for the client, also allows the client to progress to their end goal of forming a digital twin of their network. The intelligence embedded in the model allowed the checkers and approvers to access the periphery information (calculations, enquires, etc) more readily, resulting in greater coordination checks and technical reviews with wider scopes.
Constructing from model enabled a greater level of detail around hazards captured within the model. Giving immediate health and safety benefits in the form of warning triangles, visible on the Icon whilst setting out in that location on site. Buildability reviews were also regularly held with the site team, to review the model, and ensure the design could be built as safely as possible. Items such as steepness of ground around the construction area, are not always noticeable in 2D form, when the team has not yet got site presence. Another immediate safety benefit was realised from the 4D Rehearsal. By sequencing the build within the model, the site team were able to recognise a hazard relating to the proximity of existing chambers and responded by resequencing the works to reduce the number of plant movements in a congested area.
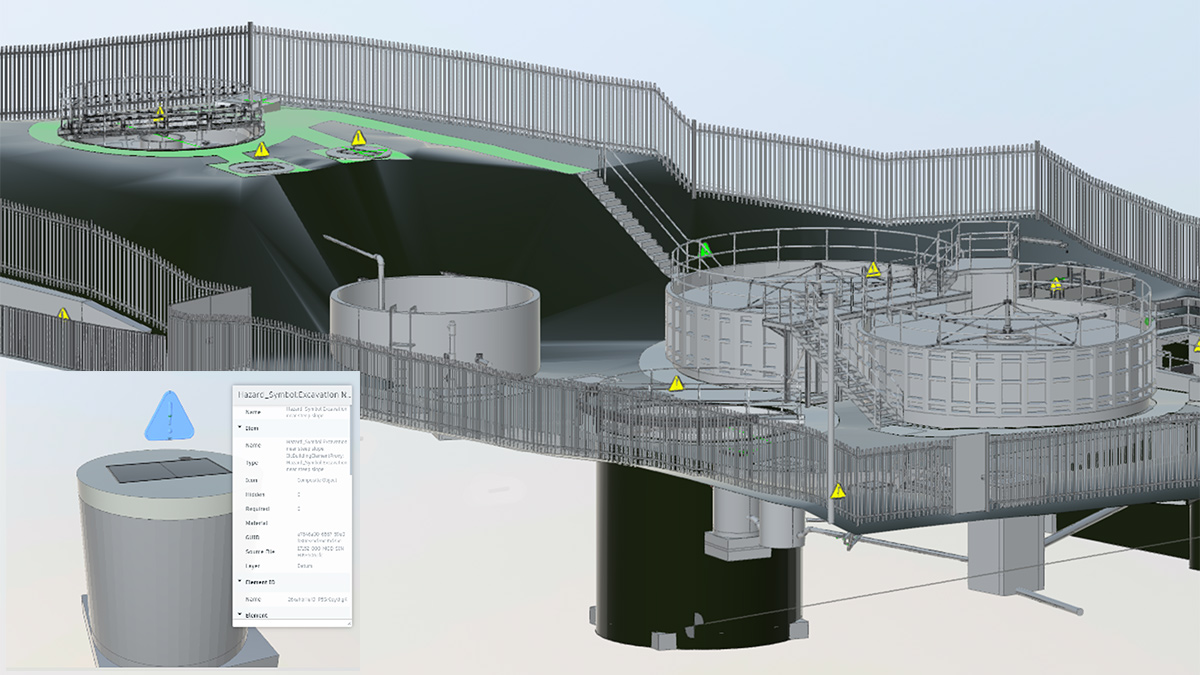
Model hazard layer screenshot – Courtesy of MMB
Wark on Tyne: Supply chain – key participants
- Principal designer & contractor: Mott MacDonald Bentley
- ECC project management team: Turner & Townsend
- Plant 3D P&ID software: Autodesk
- Leica iCON & Total Station hire & training: ESS
- Temporary settlement: United Rentals
- Electrical installation: Aceda Ltd
- Systems integration: Peak Technology Solutions
- MCC modifications: Labtec (Services) Ltd
- Conical PST & HST tanks: WCS Environmental Engineering
- Inlet flume & certification: SIRIS Environmental
- Pumps: Xylem Water Solutions
- Storm screens: Eliquo Hydrok Ltd
- Biofilter arms: IQ Engineers Ltd
- Shoring/temporary works: MGF Ltd
- Over-pumping: Selwood
- Metalwork : ADL Fabrications
- Site welfare: Wernick Group
Conclusion
This collaboration was conducted with both the client’s project team and engineering department to bring about lasting change; utilising their long-standing relationships to help drive this innovation across all projects in the future. The savings gained from digital efficiency and reduced drawing production is currently 4% of design budget but forecast to increase with the reduction in as-built production. It is anticipated that these efficiencies could increase on future projects once the new processes are embedded as business as usual.
The new design processes are being rolled out in the other teams working with Northumbrian Water, including their other framework partners to share the processes and learnings. The ongoing roll out to all MMB teams will enable similar benefits for all clients.