Northumbrian Water Wastewater Minor Works Programme (2017)
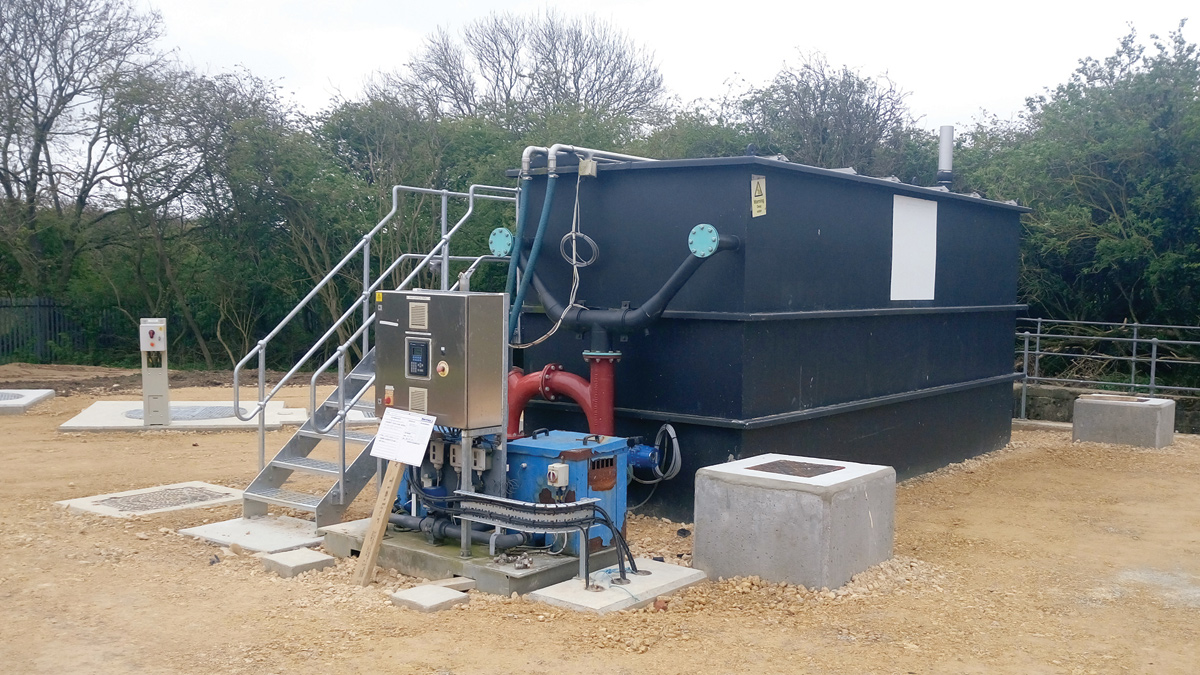
STW HSAF made permanent - Courtesy of MMB
Mott MacDonald Bentley (MMB) has been delivering the Wastewater Minor Works sub-programme for the Northumbrian Water Group (NWG) since 2006 with the number of schemes delivered annually increasing year-on-year. The team must deliver schemes for less than £150,000, and are targeted at maintaining wastewater compliance. The projects are batched where practicable, and estimated efficiencies in excess of £1,000,000 have been achieved by the team across the programme to date, with the focus being on delivering ‘outcome-based’ solutions to acute wastewater problems. The programme utilises an agile, fast moving, collaborative ‘can do’ approach with the objective of delivering solutions to operational problems.
Sub-programme schemes
The sub-programme schemes are categorised as ‘Planned’ or ‘Emerging High Risk’. Approximately 25% of the sub-programme workload is ‘emerging’ schemes, the remaining 75% is ‘planned’ schemes. ‘Emerging’ schemes are generally the result of treatment process triggers or the treatment works being required to operate in conditions outside the original design. Solutions often comprise of the installation of temporary treatment plants, or modifications to the existing process.
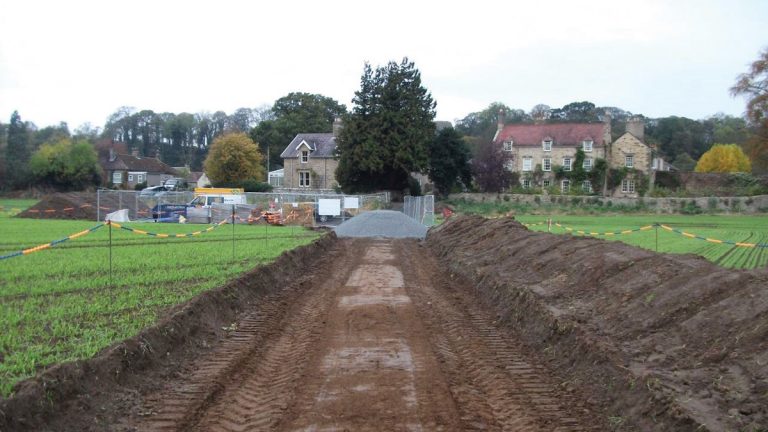
View of Warden STW under construction – Courtesy of MMB
Planned schemes
Solutions for wastewater compliance risks are very diverse and this is reflected in the scale and variety of the ‘planned’ schemes. The content of the ‘planned’ programme is developed using a survey process undertaken by both MMB and Interserve. Survey site visits with NWG Operations are undertaken to review the problems, identify potential solutions, understand buildability and develop budget costs before being peer reviewed jointly by NWG Operations and Asset Delivery. The process ensures that the work scope is fixed when the contract is awarded, ensuring lean design and reducing contract costs. The true collaborative approach is shown here when Interserve use surveys carried out by MMB to deliver projects, and vice versa. This forms the template for future working as it demonstrates collaboration through high levels of trust, consistency and cooperation between the design teams, construction teams and client project team.
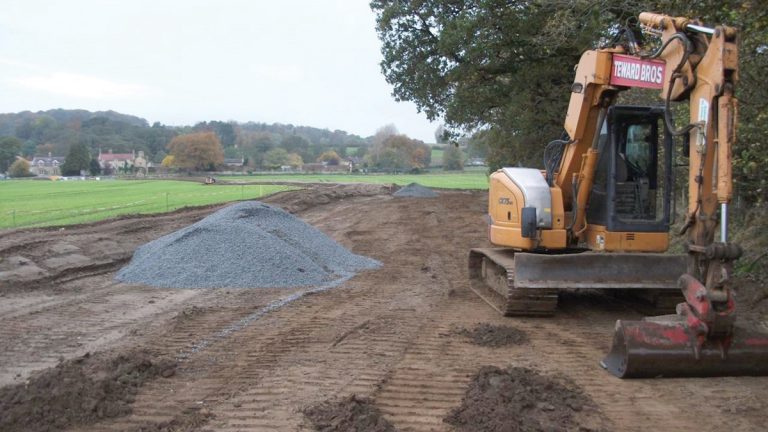
Ecologically sensitive location of the works – Courtesy of MMB
The drive for capital efficiency, as well as following a sustainable approach, has encouraged the reuse of existing assets including those stripped out of other sites, or free issue equipment to ensure that NWG gain the best value from their equipment during its lifetime. For example assets were reused at Sherburn STW where continued compliance was maintained through phased installation of multiple temporary treatment units, and the reconfiguration at Brasside STW allowed old and new equipment to run in parallel, removing significant temporary works risk and costs.
Emerging schemes
The ‘Emerging Schemes’ programme requires the MMB and NWG joint team to work together to react quickly to newly-identified issues. A protocol was developed for such circumstances, allowing teams on emerging projects to be quickly assembled. In turn, works can be delivered rapidly, but in a safe and controlled manner within the required timescales to respond to consent-related changes. These were reduced from around 10 days to 3-4 days.
The designs are delivered by a small team with civil, mechanical/electrical and process specialists, ensuring that everyone can work to their individual strengths. The nature of the works is such that previous designs can often be re-used and developed, whilst building in ‘lessons learned’ in an efficient and cost effective way. In the event of compliance triggers, MMB, NWG and the supply chain work together to react quickly to maintain compliance. The involvement of suppliers negates any abortive works and drives efficiencies and best value through a true ‘One Team’ approach. The developed protocol ensures adherence to MMB’s Operational Safety Standards and NWG operational procedures as well as ensuring the projects are delivered right first time.
Case Study: Warden STW – Outfall Relocation
Warden Outfall presented a number of ecological challenges to the project team. A significant amount of pre-start work was undertaken to ensure adequate protection measures were addressed in design, and implemented during construction to ensure minimal environmental impact. Examples of the environmental mitigation challenges overcome by the team include:
- Water voles
- Himalayan balsam
- Freshwater pearl mussels
- Freshwater fish spawning grounds
- Natural England consents
- Environment Agency consents
MMB operate in line with their ISO 14001 environmental management certification in order to protect and enhance the environment in the delivery of our services. The ecological sensitivities associated with this site demanded that the strictest management controls were adopted on site. The challenges that the team faced on site included:
- Himalayan balsam: Evident on the river bank and required monitoring during all works on the bank. Foliage was stripped from the bank and retained close by to avoid any cross-contamination. The same procedure was implemented for the reinstatement of topsoil once the headwall was completed. Plant and machinery was cleaned before tracking on the field after working on the bank, and operatives’ footwear was also cleaned on exiting the bank.
- Freshwater pearl mussels, water voles and newts: A survey was carried out prior to the commencement of works, with any freshwater pearl mussels found moved by specialists prior to starting work.
- River Tyne pollution protection: The design adopted a precast solution to avoid wet concrete near the watercourse. The precast solution meant that off-site manufacture reduced embodied carbon, providing a more sustainable approach as well as reducing the ecological impacts on site through the construction methods. Flood defence consents were agreed with the Environment Agency, and straw bales placed to prevent silt run off into the river. A sandbag cofferdam was also utlised in the river adjacent to the works, with water pumped out and passed through a fine silt filter before being allowed to discharge back into the river. Strict limitations and controls were placed on plant refuelling arrangements.
- Natural England: Following consultations and with consents in place, any clean water clams found were to be moved / relocated ahead of the works.
- Local Environment: Access to Warden STW was through the sensitive hamlet of Low Warden via a private ‘no through road’ gravel access track of 200-300m in length. There was no other means of access.
Residents were concerned that our plant would leave the road damaged following the works, especially as they had upgraded the track at great expense to themselves the year before. With this in mind, our team worked tirelessly to ensure the access track did not get damaged by:
- Containing any debris and mud which could otherwise have spread onto the road.
- Only taking plant in once and not changing it.
- Arranging deliveries at certain times so as not to inconvenience the residents.
- Not parking on their road or blocking access.
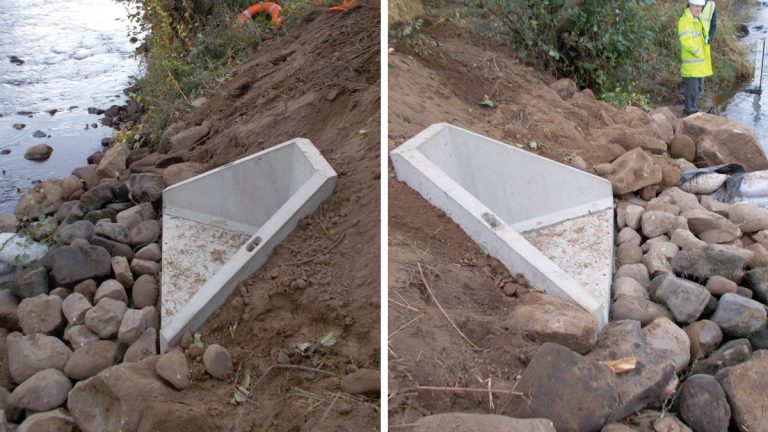
View of the new outfall – Courtesy of MMB
While the project was not the largest or most expensive we have or will deliver, it did present a number of logistical and environmental challenges. Diligent third party engagement was critical on this small but highly important scheme. Local residents were justified in their concerns prior to the project commencing because of the potential for disruption. The project team eased these concerns through careful stakeholder engagement and working as a sympathetic and conscientious unit. The team understood the potential environmental challenges and impacts presented by the scheme and overcame them by collaborating in order to arrive at robust mitigation strategies. The team promised the residents that disruption and noise would be minimised, and delivered what was promised. The strap line of the project was ‘we did exactly what we said we were going to do’.
The scheme was completed to programme and budget whilst enhancing NWG’s reputation within the local area. This was externally validated by a letter of praise from a local resident, making reference to how the ecological challenges have been addressed by the project team. This approach can only serve to enhance NWG’s reputation in their protection of the environment.
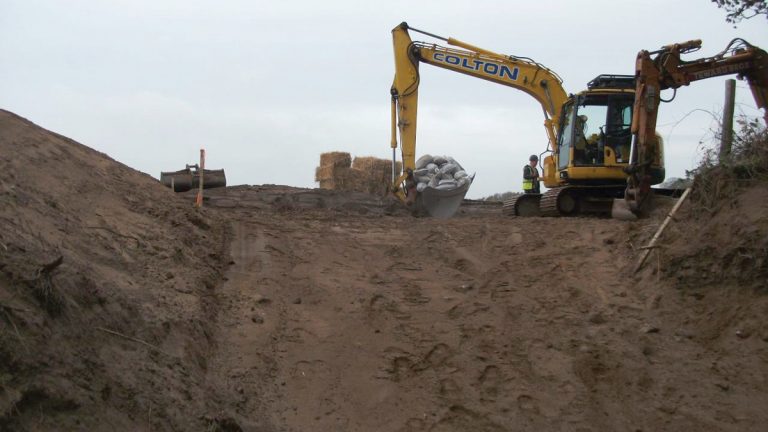
View of construction works – Courtesy of MMB
Collaborative teamwork
Key to the success of the Wastewater Minor Works Sub-Programme has been the collaborative team planning approach adopted by all stakeholders. This has been driven by constant learning carried forward by the consistent team deployed on the work. By working together in a ‘one-team’ approach NWG, MMB and Interserve are ensuring continued wastewater compliance using innovative solutions and flexible procurement methods, built on the foundations of effective project delivery. Collaborative working is at the heart of the wastewater Minor Works Sub-Programme, with team members working in a co-located environment. The maturity of this relationship has allowed open challenge to arrive at outcomes best suited to the needs of NWG. Collaborative ‘Peer Reviews’ with NWG Operations and Asset Delivery are undertaken following survey of candidate assets as described in the ‘planned projects’ section.
Excellent working relationships have been developed within the wider NWG community. This has helped to provide rapid and agile responses to acute issues, protecting NWG assets and reputation, and the environment. We have challenged existing ways of working to arrive at the most effective delivery mechanism and have utilised ‘lean’ planning techniques such as ‘Plan to Protect’ and the ‘3 Levels of Planning’ to deliver efficiencies, whilst providing a rapid response to serious compliance and flow issues.
The collaborative core team process has resulted in the wider community and other stakeholders being brought into the process at an earlier stage. This ensured a full understanding of the risks involved, better time management and reduction of waste through the life-cycle of the project. The variety and nature of the work takes us into the wider community, many times into small villages were there is a high likelihood of noise and disruption for NWG customers. Whenever possible, MMB and NWG work to deliver a lasting legacy for the local residents with a view to enhancing NWG’s reputation among its customers.