West Huntspill WRC Bathing Waters Improvements (2021)
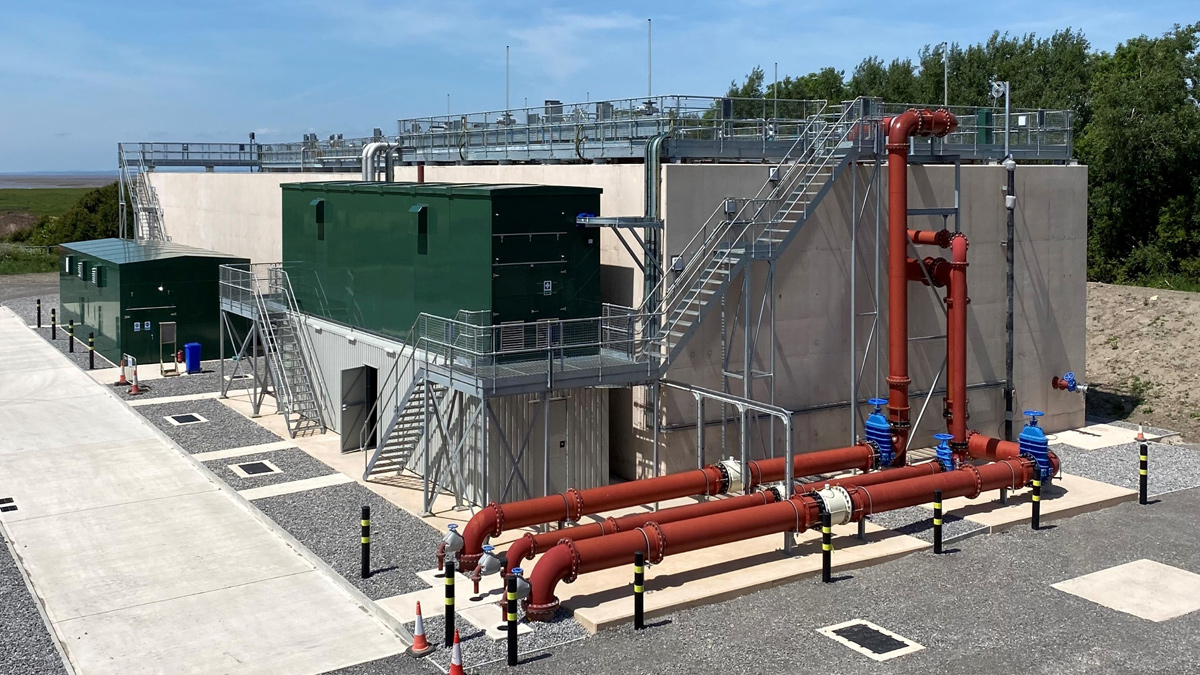
ASP structure with MCC and blower kiosks - Courtesy of Trant Engineering Limited
West Huntspill Water Recycling Centre (WRC) is a Wessex Water facility situated south of Highbridge in West Somerset. This environmentally sensitive site is within a National Nature Reserve and adjacent to a Site of Special Scientific Interest and a Special Protection Area (Bridgewater Bay and the Severn Estuary). The facility serves a catchment of 62,000 population equivalent and discharges its final effluent into the mouth of the River Parrett, which then flows into the Bristol Channel just south of Burnham Jetty North. The tighter standards for bathing water introduced in 2015 and the substantial development of the catchment in recent years called for the provision of additional treatment capacity and the improvement of the final effluent quality.
Proposed solution
The proposed solution was to supplement the existing treatment process with a new 3600m3 activated sludge plant (ASP) with two integral anoxic selector zones, a new distribution chamber and two new aeration lanes. To feed the ASP, a newly constructed ASP pumping station takes the flow from the existing primary settlement tanks (PST) and feeds into the new ASP selector zone. The effluent travels through the two-lane anoxic zones, enters the distribution chamber and is split between the new and existing ASP aeration lanes in a ratio of one third/two thirds in favour of the new treatment plant.
Low-pressure air supplied by three blowers and a fine bubble diffuser array ensures an optimal biomass oxygen uptake. The oxygen level is monitored by four dissolved oxygen (DO) probes in each lane.
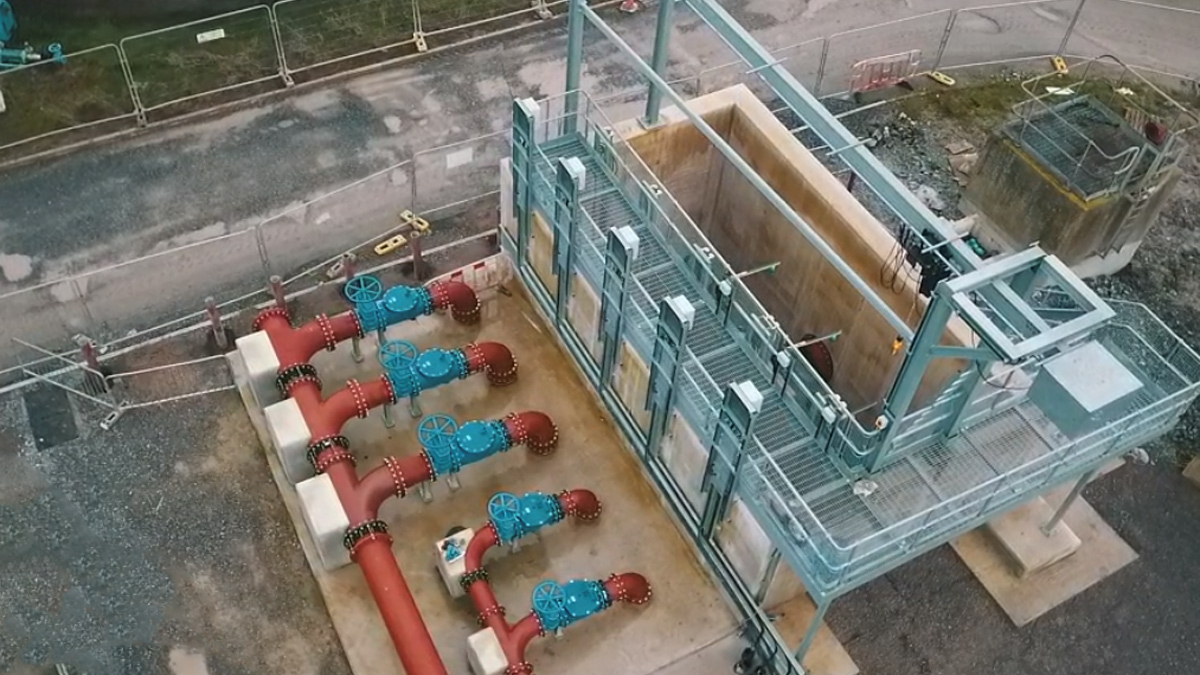
ASP pumping station with non-return valves from MGA Controls Ltd – Courtesy of Courtesy of Trant Engineering
A new return activated sludge (RAS)/surplus activated sludge (SAS) pumping station returns activated sludge from the existing final settlement tanks (FST) into the new ASP initial selector zone, while the sludge surplus is pumped by the new SAS pumps to the picket fence thickeners (PFT).
Such improved biological treatment will enhance the UV treatment efficacy to achieve up-to 4.4 log reduction in enteroviruses and a 5.4 log reduction in faecal coliforms.
A collaborative approach
Water industry specialists Lewis Civil Engineering (LCE) – now (Dec 2022) Envolve Infrastructure – and Trant Engineering (TEL) were respectively appointed Civil and M&E Delivery Partners by Wessex Water’s Engineering and Sustainable Development Team (ESD) for this project. Alongside WW ESD, SWECO (design partners), and Wessex Water’s own Automation & Commissioning Team, the scheme was successfully developed from the optioneering stage through detailed design to construction.
Over the course of the project all partners have worked very closely to deliver the West Huntspill Bathing Water Improvement scheme, a £12m capital investment from Wessex Water.
West Huntspill WRC Bathing Improvements: Supply chain – key participants
- Civil engineering contractor: Lewis Civil Engineering (now envolve infrastructure)
- M&E contractor: Trant Engineering
- Detailed design: SWECO
- Shaft contractors: Active Tunnelling
- Piling contractors: Roger Bullivant
- Piling contractors: Van Elle
- Temporary works: MGF Ltd
- MCC, MDP & LVD panels: Bridges Electrical Engineers Ltd
- Fine bubble diffuser system: Xylem Water Solutions
- HV & transformer: High Voltage Design & Build Ltd
- UV system: Trojan Technologies
- Under-pressure connections: UTS Engineering
- PFT & sludge tank: Stortec Engineering Ltd
- Mechanical pipework: ELG Civil & Mechanical Ltd
- Lagging & trace heating: PG Insulation
- Actuated penstocks: FW Marsh Electrical & Mech Ltd
- Actuated penstocks: Glenfield Invicta
- Flow controls: AUMA Actuators Ltd
- Non-return valves: MGA Controls Ltd
- Steelwork: Westbury Park Engineering Ltd
- GRP kiosks: GRPro Ltd
- Scum box install: Jacopa Ltd
- Blowers: Atlas Copco
- Transfer pumps: Xylem Water Solutions
- Ductile pipework: European Pipelines
- Valves: AVK UK Ltd
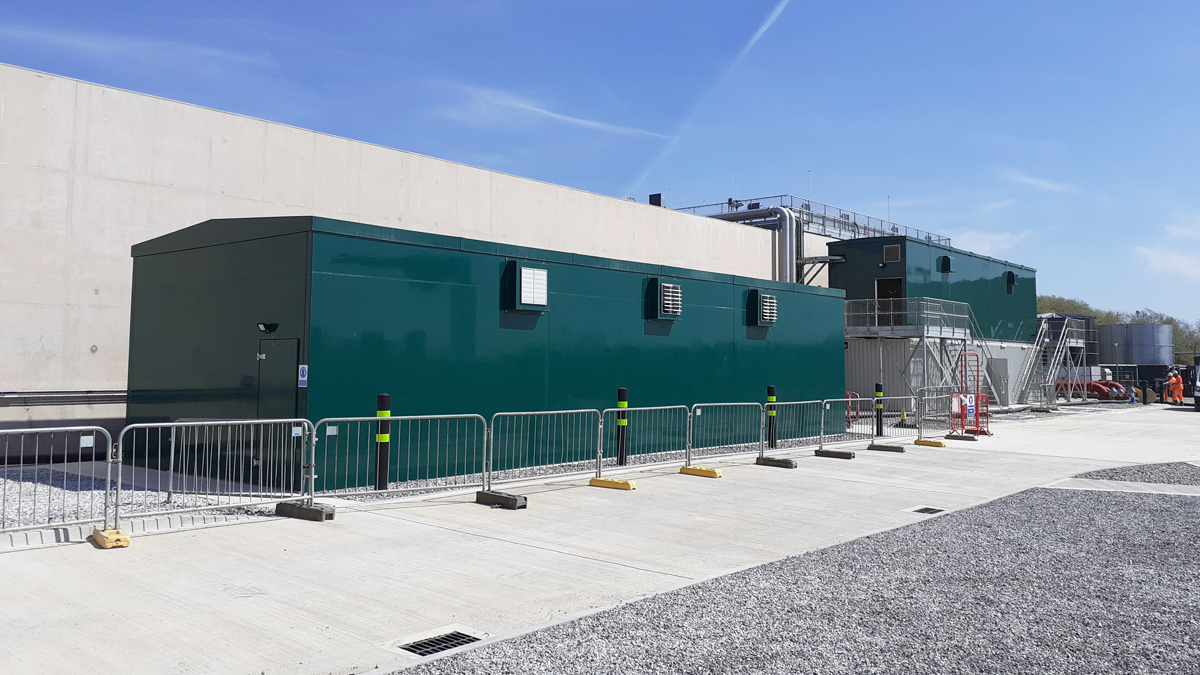
ASP blowers and MCC – Courtesy of Lewis Civil Engineering
Design
Through early contractor involvement (ECI) during the design phase, LCE and TEL were able to use their specialist sector knowledge to guide the project team through key constructability decisions. Assessments were made with regards to safety, quality, time and cost which aligns with all partners underlying business ethos.
For LCE, two crucial decisions were construction methodology for the ASP lanes, and installation technique of the RAS/SAS pumping station shaft. In situ concrete and precast concrete (PCC) options were considered for the ASP, and a detailed comparison report was undertaken for both methods. The concluding findings were that both methods had comparable standards for health, safety and quality, but that the increased cost of the PCC option could not justify a small programme saving, especially considering the potential for the additional design interfaces to cause delay. The optimal option was to construct the ASP as an in situ RC structure. The RAS/SAS chamber was determined as a top-down caisson shaft, primarily due to the poor ground conditions.
It was crucial for Trant Engineering to efficiently accommodate the new electrical arrangement. A new main primary distribution (MDP) switchboard was installed, acting as a centralized hub for all circuitry elements both on the new installation and all remaining existing plant.
The new MDP replaced the two existing MDP’s on site and together with the installation of the new 1200Kva transformer, required a complicated electrical changeover sequence. Multiple site and plant shutdowns were needed to move existing supplies to the plant from the existing distribution panels to the new MDP.
The works involved extensive planning and coordination with multiple partners including Wessex Water Operations Personnel, Western Power Distribution, Wessex Water’s Commissioning and Automation Teams and specialist subcontractors for the HV installation, cable jointing and generator changeover controls.
Over a period of seven weeks the works were completed successfully and safely as per the planned timetable, despite the added challenges with Covid-19 compliance.
The selection of a single supplier, the pump expert Xylem Water Solutions, for all pumping equipment was another strategic choice made to ensure straightforward operation and maintenance for the client.
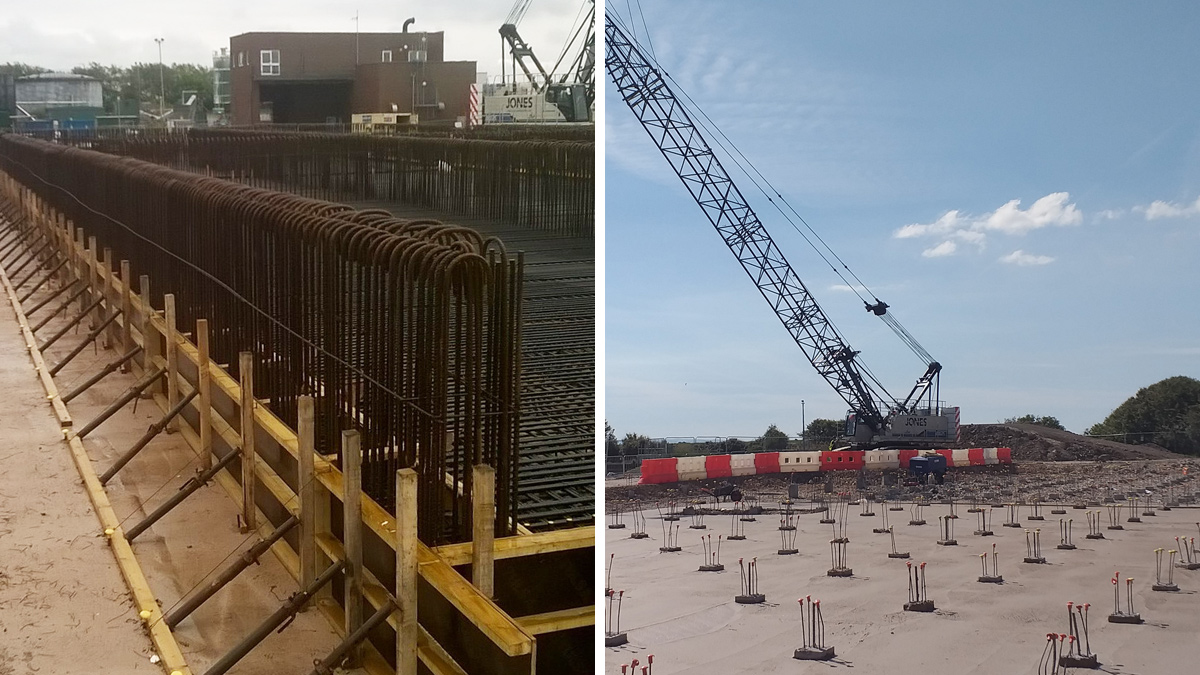
(left) ASP base slab reinforcement and (right) ASP piling – Courtesy of Lewis Civil Engineering
Challenges and mitigation
The work environment: Ground conditions along the Severn Estuary are inherently poor, consisting of approximately 20m of tidal deposits lying above the mudstone bedrock. Structural stability has been ensured by piling all elements down to the underlying bedrock. Additionally, the coastal location provided some challenging weather conditions for both contractors, with high winds hindering the use of cranes required for civil construction and the installation of the M&E assets.
To ensure the provision of the most effective outcomes, despite the congested environment, Trant Engineering and Lewis Civil Engineering, in collaboration with the key supply chain partners, developed an interdisciplinary approach ensuring strict time and resource management within all phases of the project.
The collaborative workforce was also delivering a second sizeable project at the West Huntspill WRC, alongside the Bathing Water Scheme – The Sludge Treatment Strategic Maintenance Scheme.
The existing ‘live’ process: Throughout the project, the existing works had to remain on-line with little opportunity for shutdowns. Two key under-pressure connections were made by UTS Engineering, specialists in innovative pipeline technologies. Connections were made below process flow levels, against a head of water. A gate valve was fixed to the existing concrete chamber wall. A diamond tipped corer was then inserted through the open valve and a clean cut was made through the thickness of the chamber wall.
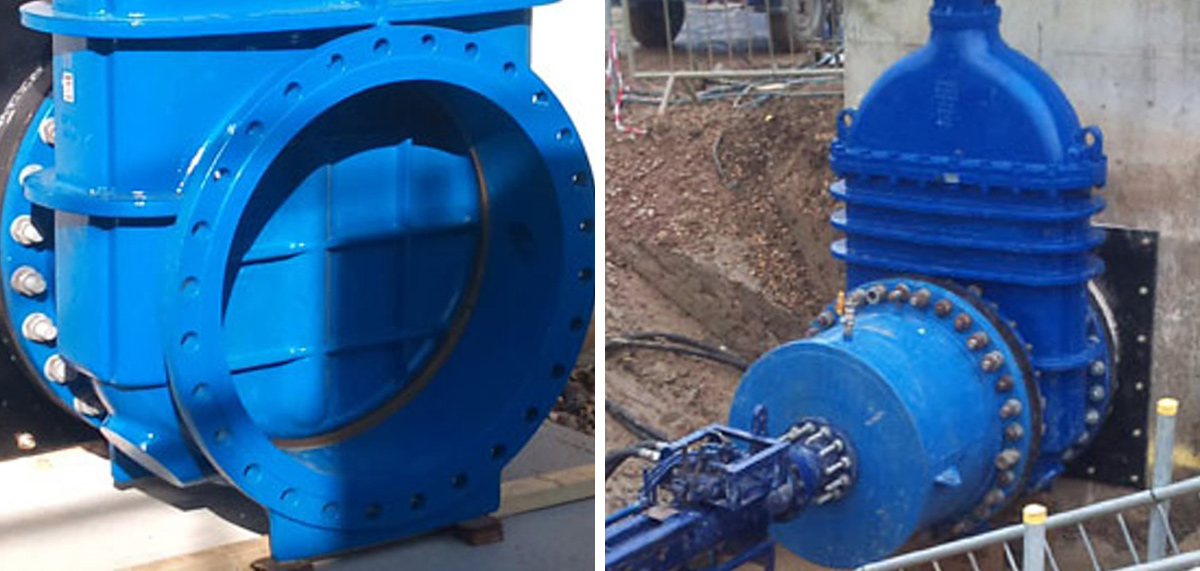
UTS hot tapping valve – Courtesy of Lewis Civil Engineering
The corer was retracted with the concrete core inside until it passed the gate which is then shut ensuring no leaks. The first connection was located upstream of the existing pre-mixing chamber and the second downstream of the existing ASP chamber.
The ‘hot tappings’ allowed the existing process to remain uninterrupted during commissioning and also provides additional control points for the treatment process.
Work within a flood plain: With the location of the works directly adjacent to the Severn Estuary, there remains an inherent risk of flooding of the West Huntspill works. A key requirement of the design was for both the new ASP motor control centre (MCC) and the main primary distribution (MDP) to be elevated on steelwork platforms set between 2.8m and 3.0m above the main site ground level.
This necessitated detailed coordination of the design for the structural steelwork, GRP kiosks and MCC manufacturer taking into account the wind loading in such an exposed location and the interconnection of each of the components.
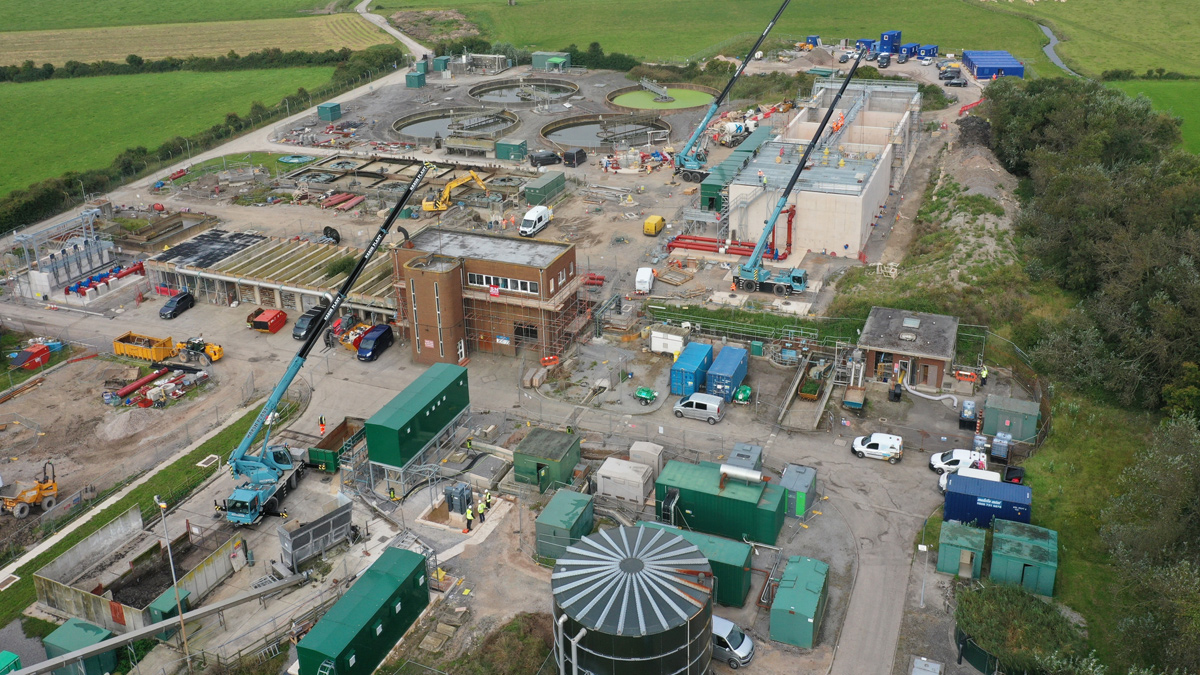
West Huntspill ASP and transformer installation activities – Courtesy of Trant Engineering
Covid-19: However successful and ahead of the programme, the delivery of the scheme was severely challenged by the global pandemic. Factory closures around the world, delivery of key material and package suppliers were delayed or even cancelled. LCE and TEL showing adaptability and reactivity reached out the other suppliers to ensure the continuity of the work.
Arrangements were made on site, with the implementation of new work practices ensuring the health and safety of all employees and site personnel.
Construction
Works commenced on site in February 2019 when Lewis Civil Engineering Ltd (LCE) were appointed principal contractor. As works progressed, LCE activities on site decreased and Trant Engineering activities increased, making it appropriate to transfer the principal contractor appointment from LCE to TEL in August 2020.
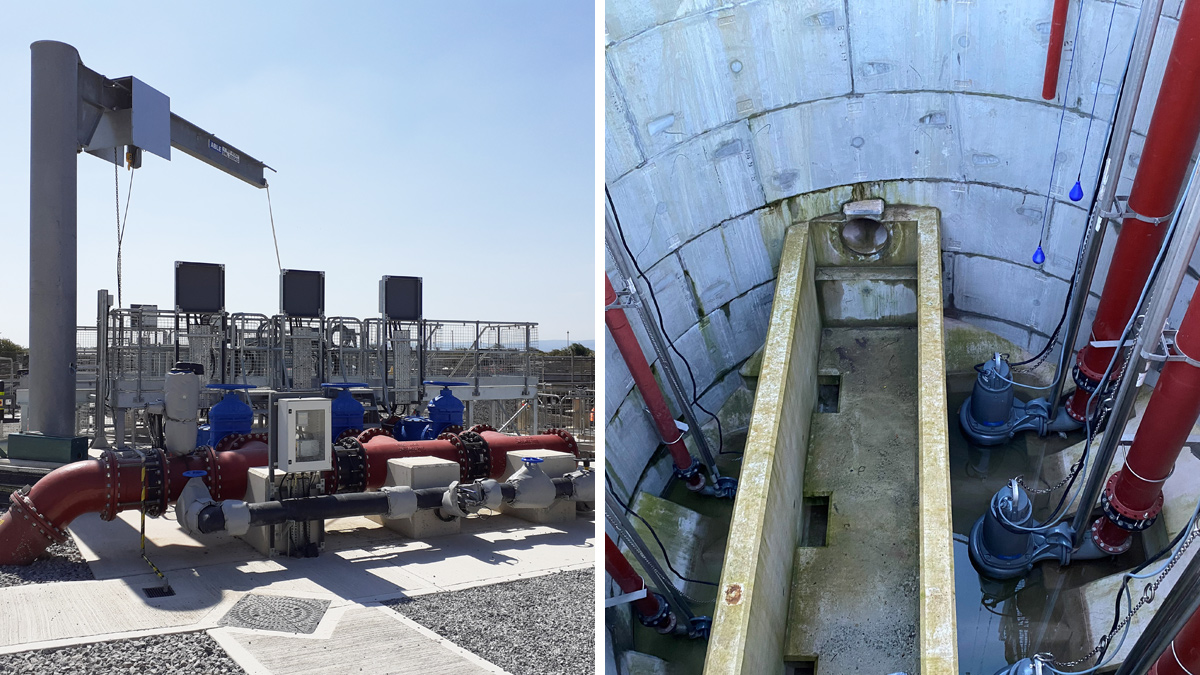
RAS/SAS pumping station – Courtesy of Lewis Civil Engineering
RAS/SAS pumping station shaft: The RAS/SAS pumping station was constructed as a top-down caisson shaft. Caisson shafts are the preferred method of shaft construction in poor ground conditions such as those found at West Huntspill. Precast concrete sections are bolted together at ground level before the material within the shaft is removed, allowing the structure to sink under its own weight. The initial ring has a cutting edge and the direction of the shaft can be ‘steered’ using hydraulic jacks attached to the collar.
A 2.0m wide, 1.2m deep piled reinforced concrete collar was constructed before specialist contractor Active Tunnelling sunk a 9m deep, 6m ID shaft. Piles were then driven from the bottom of the shaft, before the base slab and internal channels were constructed.
Activated sludge process lanes: The new reinforced concrete ASP structure is 59.9m long, 15.9m wide and over 7.5m high, founded on 260 (No.) PCC piles.
Unexpected sand lenses were encountered at approximately 17m below ground level, stopping the piles from being driven to their design founding level. Piling contractor, Roger Bullivant, were very proactive with redesigning the piles as ground conditions changed across the footprint of the ASP.
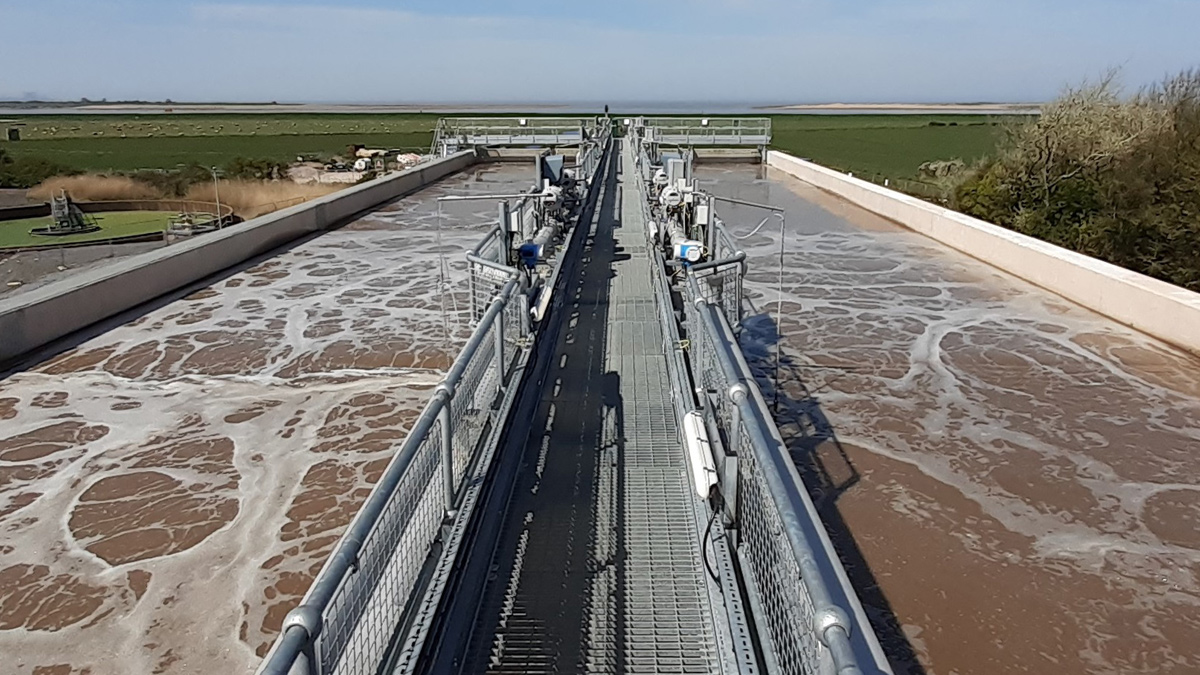
ASP lanes in service – Courtesy of Lewis Civil Engineering
During the civil construction of the main RC structure, ‘doorways’ were left in the walls of the ASP allowing access between cells without having to go over the top of the walls. These significantly improved confined space and Health & Safety implications during construction and were only in-filled prior to water test.
After completion of the civil structures, TEL completed the installation of the mechanical and electrical equipment. All assets installed ensure the most efficient and reliable operation of the new process.
The aeration blower package plant consists of three Atlas Copco blowers contained in the new blower kiosk. The airflow regulated by the optimizer supplies air based on the demand required by the ASP. The aeration lanes control and monitoring are achieved using mass air flow meters and DO probes connected to a central controller. This monitors the dissolved oxygen levels in the ASP and sends the signal via profibus back to the PLC.
The communications panels are connected to the profibus networks via optical link modules and the main fibre ring on-site serves as the main communication route for the Inter PLC and SCADA servers.
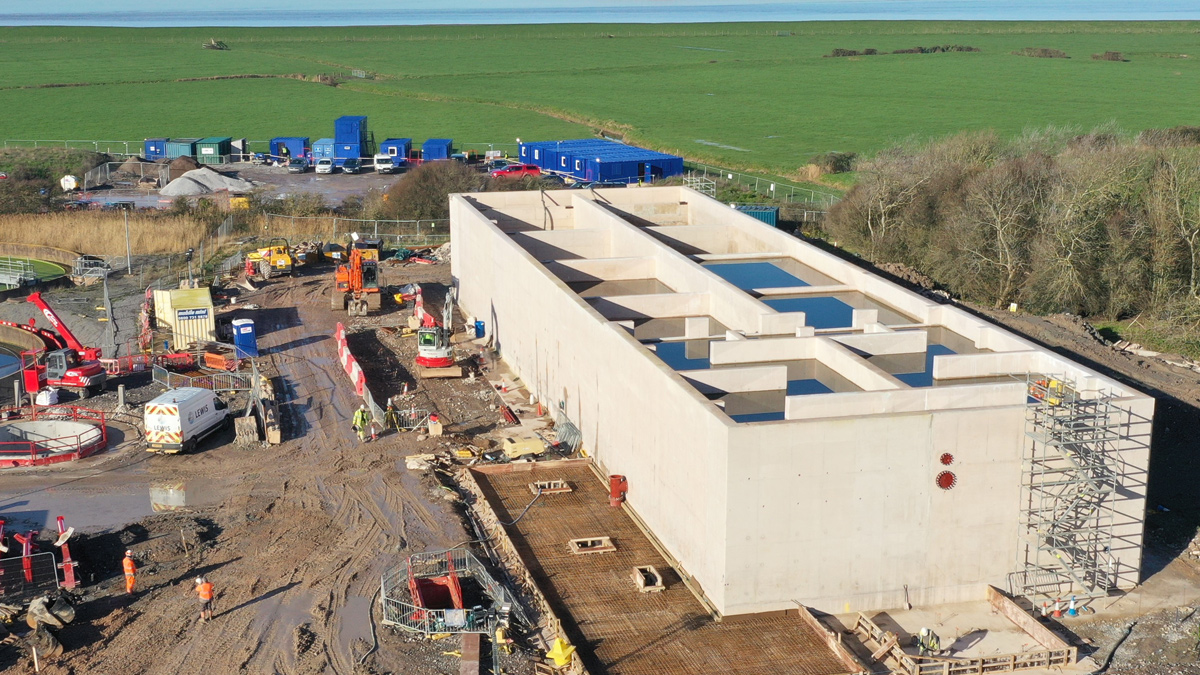
ASP water test – Courtesy of Lewis Civil Engineering
Summary
Excellent project management by Wessex Water’s ESD Team, combined with successful collaborative working between all framework partners has ensured the West Huntspill WRC scheme achieved all required outputs ahead of the regulatory date set out by the Environment Agency (EA), as part of their Water Industry National Environmental Programme (WINEP).
At the time of writing (August 2021) the West Huntspill WRC scheme is nearing completion despite the challenge of delivering the Project throughout the Covid-19 pandemic. This complex but ultimately successful project ensures that future development growth can continue in the Huntspill/Highbridge area with a significant improvement to the treatment process and quality of final effluent.
The scheme has been delivered to the highest quality and H&S standards and is testimony an aligned project delivery team.
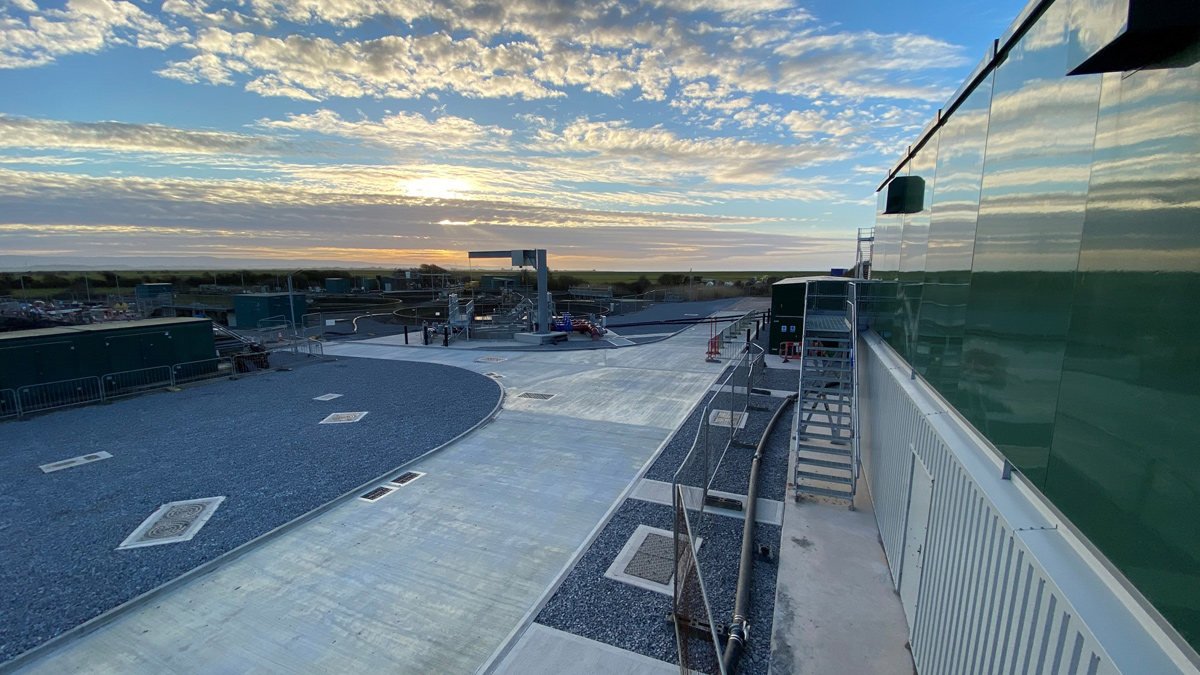
View towards RAS-SAS pumping station with complete road construction – Courtesy of Lewis Civil Engineering