Wooler WTW (2023)

Precast contact tank during construction and wastewater settlement tank temporary works - Courtesy of MMB
Wooler Water Treatment Works (WTW) is fed by four boreholes and supplies up to 160m3/hour of potable water to Wooler and surrounding areas, including several tourist and semi-residential holiday parks serving over 5,000 people. Seasonal fluctuation in demand can increase turbidity and increase iron and manganese concentrations in the borehole water, particularly when flows are high, interrupted or varied. The existing treatment facility was reaching the end of its asset life and did not have the treatment stages to remove the turbidity, causing flows to run to waste. Frequent power outages and varied seasonal populations led to regular manual operator intervention and a growing reliance on tankering from other sites to ensure the supply zone remained primed.
Background/drivers
In 2016, Northumbrian Water (NWG) awarded Mott MacDonald Bentley (MMB) an Investigate and Define contract to review potential solutions to improve treatment at Murton and Wooler WTWs. Following this, in April 2018, NWG issued MMB a NEC3 ECC Option C Design and Construction (D&C) contract to deliver the design, construction, testing and commissioning of the new treatment facilities. Design for Wooler commenced in June 2018, with construction works commencing in May 2020. The main build was completed in April 2021 and water brought into supply following testing and commissioning.
The previous treatment site was set to run to waste until turbidity in the borehole water was suitable to be treated further. NWG experienced turbidity spikes on pump start-up and flowrate changes, exacerbated by frequent power outages. This resulted in time consuming, costly operator intervention, and wastage of borehole water to the environment. Disruptions in supply needed quick operator intervention to ensure no impact to the customer, often necessitating tankering to maintain supply. The rural setting of the WTW meant during winter, operators faced increased risk in accessing the site.
The new WTW incorporates four large pressure filter vessels which are effective in removing turbidity, iron and manganese at higher levels. The reduction in run to waste occurrences provides a more sustainable use of water abstracted from the aquifer whilst improving water supply security to the Wooler area. Within the investigation phase MMB and NWG decided to relocate the works to a more urban setting to reduce the risk on operators and minimise risk of weather events affecting power supply and communications to the site, both of which are critical to maintaining supply to the local community. This is especially critical at Wooler, as the area benefits from a transient tourist population which puts additional strain on the water supply system.
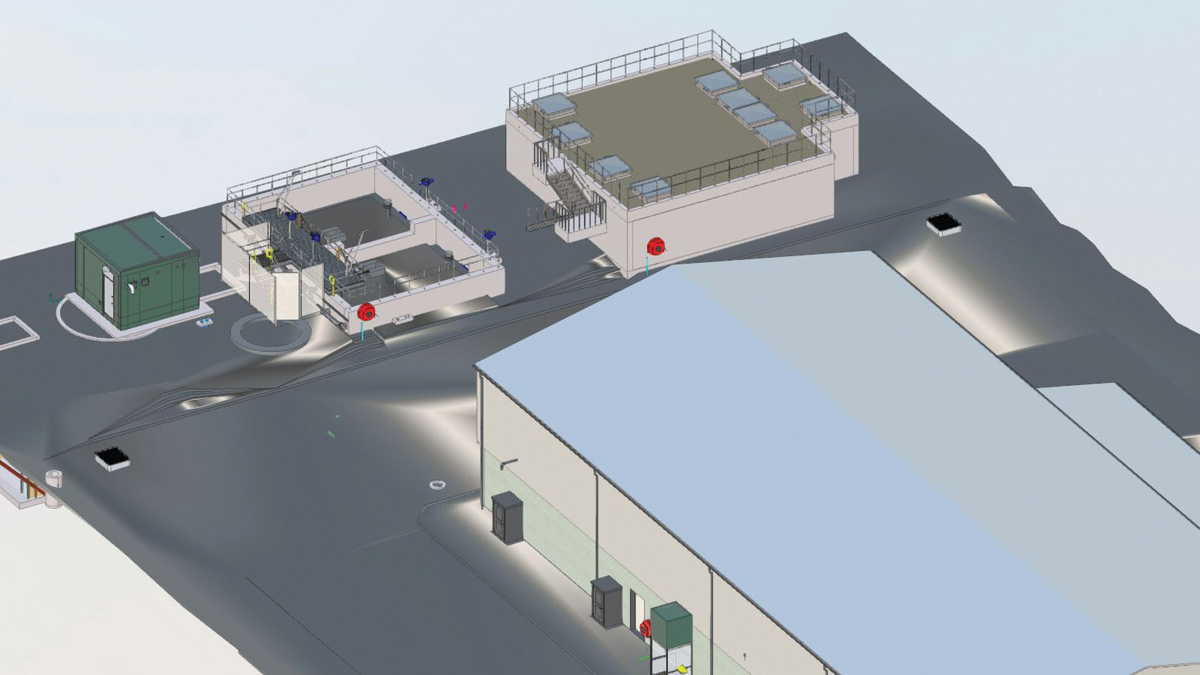
Clockwise from top left – Dechlorination plant, wastewater tanks, chlorine contact tank and treatment building – Courtesy of MMB
Design development
The design phase commenced during the latter phases of construction works at the nearby sister site, enabling the design team to capture positive and negative lessons from the construction and client operations team.
Over 100 lessons were collated and assigned owners to incorporate into the Wooler design. The results were evident in the programming and sequencing of the project, which halved the workforce on site when compared to Murton. Several design efficiencies were identified that further reduced the construction duration, including, designing out thrust block requirement, simplification of a complex dechlorination system and pre-washing filter media prior to delivery to reduce commissioning and significantly reducing commissioning water wastage.
The MMB project team successfully challenged client asset standards which would have required an additional filter, and as such specified filtration by four sand pressure filters. The filters consist of an anthracite cap, sand, and manganese dioxide (MnO2) media. The sand and anthracite layers capture larger solids particles during periods of poorer water quality whilst the MnO2 acts as a catalytic media and further promotes manganese and iron deposition onto the filter media.
By removing iron and manganese over a single stage, the project team designed out a secondary treatment stage, saving on TOTEX, carbon and minimising site footprint. The filtration method selected also provides a higher level of robustness, reliability and low operational costs compared with other technologies.
The notional solution proposed maintaining use of the borehole pumps to generate sufficient pressure to drive flow through the new treatment plant to the existing service reservoir served by the site.
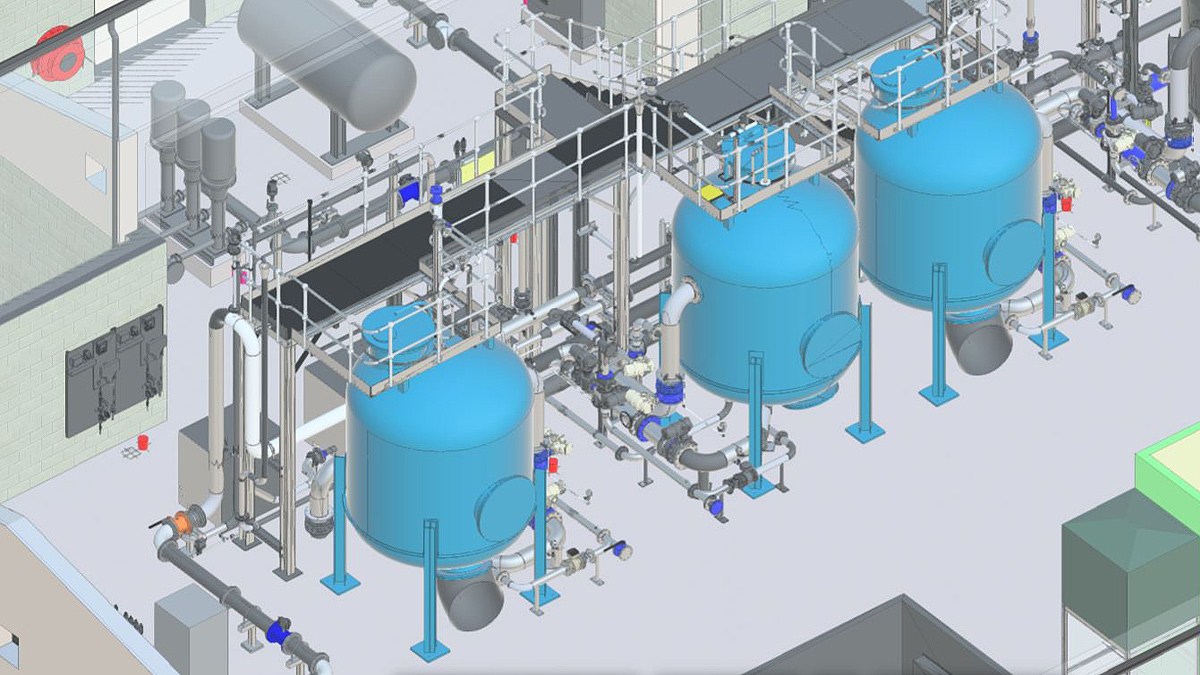
Multiple supply chain interfaces were modelled to proactively reduce snagging – Courtesy of MMB
The additional pressure required would require replacement of the borehole pumps and over 4km of mains in serviceable condition. Instead, the pressure head was broken within the site, reducing operation and maintenance risks, and improving site control and resilience through installation of high efficiency booster pumps to supply the network. Pumping of waste flows was minimised through agreeing discharges into the local sewer and surface water network, with dechlorination included for treatment of non-compliant flows. Pumping of drainage flows was also avoided through minimising site access roads, maximising green space and incorporation of SuDS trench and lagoon within the site footprint.
Digital delivery was preferred from the onset, and the site location was GPR and laser scanned to produce an accurate 3D model of the current land and subterranean utility infrastructure. This model was developed further with key suppliers and multidisciplinary designers to progress to a full site-wide model of the civil, electrical, mechanical and process elements.
The pressure filter, chemical dosing and metalwork suppliers uploaded models of their discrete works packages into the selected Common Data Environment (CDE) BIM360. The packages were incorporated into the overall site model, produced in Revit. This enabled the MMB design team to accurately model surrounding road structures, interconnecting pipework, services and road infrastructure in both Revit and Civil 3D. The 3D model is earmarked for use as a digital twin, to improve asset management and aid with efficiency of the everyday site operation.
The site was designed such that all key instrumentation is above ground, but transfer pipework between treatment stages is below ground, giving full access to all valves and dosing points. Through development of the 3D model, operators were able to fully review the site in advance of a spade being struck, leading to changes to further mitigate operational and site hazards. Rethinking of the operating pressures has reduced operator risk within the building and the new process utilises more resilient process units than previously, incorporating a sophisticated control philosophy which minimises unintended shutdowns and enables restart at the push of a button, rather than a complex series of manual valve operations.
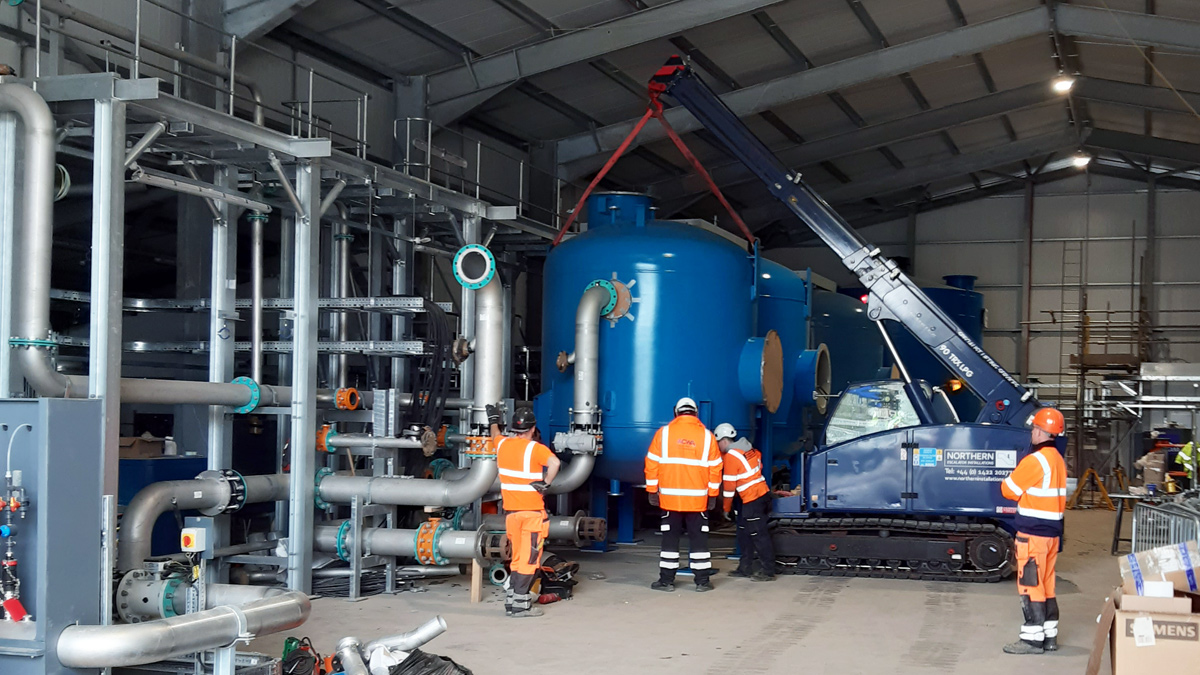
Treatment process units being installed after off-site manufacture and testing – Courtesy of MMB
Off-site manufacture opportunities were identified to minimise personnel operating on a relatively small site. Chemical dosing facilities were manufactured and tested within kiosks and delivered to site as plug-and-play elements of the process, improving quality control through factory testing and commissioning. Vertical pressure filter units, associated pipework, and metalwork access gantry were all pre-assembled and tested prior to final offload and assembly on site. This approach was taken for the complex manifold pipework weaving between and connecting the site process plant.
The 3D model was utilised by stainless steel pipework fabricators to design and detail the pipework for accurate off-site manufacture, eradicating cutting on site. Building on lessons learned from Murton, the contact tank design was changed from in-situ build to a semi pre-cast assembly, reducing the on-site build programme of the structure and reducing the trades and temporary works required.
Covid19 hampered the ability to carry out informal meetings, though the digital delivery of the project meant that communication was not impacted during the critical latter stages of the design. The 3D model was utilised to facilitate key coordination meetings including ALM and HAZOP reviews, helping both MMB and NWG communicate proposals to non-technical colleagues. Enabling NWG to utilise the same model during design aided with design acceptances and operational reviews of proposed site processes.
Fire and hazard reviews were carried out utilising third person perspective within the model. The integrated use of BIM360 brought more of the supply chain into the collaborative solution development allowing all stakeholders to visualise the final product in a way not possible with traditional 2D drawings. This allowed for greater clash detection prior to construction enabling designs to be tweaked at low cost in the office, reducing standing time on site. Key interfaces between each mechanical supplier were digitally inspected in advance of installation, reducing the likelihood of common avoidable defects in major treatment projects.
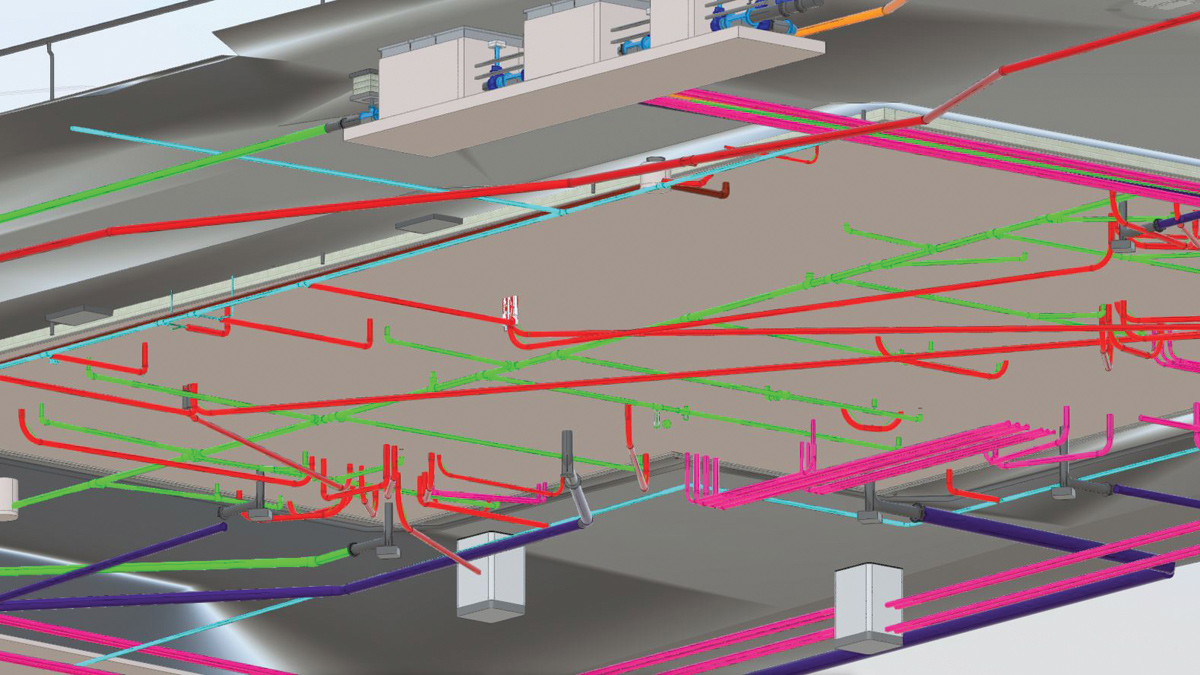
Complex subterranean service network required careful clash detection – Courtesy of MMB
Wooler WTW: Supply chain – key participants
- Design & build: MMB
- Hydraulic modelling: Mott MacDonald
- Ground investigation: Dunelm Geotechnical & Environmental
- Sheet piling: Van Elle
- Precast concrete: FLI Precast Solutions
- Blockwork: Gallaway Construction
- Structural steelwork design & build: Glendale Engineering (Milfield) Ltd
- Metalwork: JHT Fabrications Ltd
- Electrical/cabling: Dongard Mechanical & Electrical Ltd
- Scaffolding: Ingleford Scaffolding Ltd
- Shoring/temporary works: MGF Ltd
- Pressure vessels: ACWA Services
- Surge vessels: Quantum Engineering Developments Ltd
- Chemical dosing design & supply: Sheers Ltd
- Pumps: Grundfos
- Static mixers: Statiflo Intenational
- Major valves: AVK UK Ltd
- Steel pipework fabrication: JBF Group
- MCC: CEMA Ltd
- Systems integration: IDEC Technical Services
- Generator: WB Power Services Ltd
- Security systems: 2020 Vision Systems Ltd
- Roller shutter doors: Ascot Doors Ltd
- Security doors: Bradbury Group
Construction
Working within a D&C environment, constructability is considered at every stage. The Wooler construction team were identified early in the project, with regular reviews held to discuss the design, its buildability and associated temporary works requirements. These reviews, along with similar client meetings, were held to invite challenge and give the whole project team an opportunity to influence the design; reducing and controlling risk when total mitigation was not possible.
Excavators with in-built GPS and intelligent machine control utilised the digital terrain model to excavate within 6mm accuracy, reducing over dig but also bringing wider programme and health and safety benefits. The programme was sequenced using the 3D model, with the order of build determined by service and structure depth. All below ground structures and pipework were set out utilising the model which, alongside excavation accuracy, ensured pipes were laid accurately with no clashes or diversions incurred despite the complex subterranean service network required.
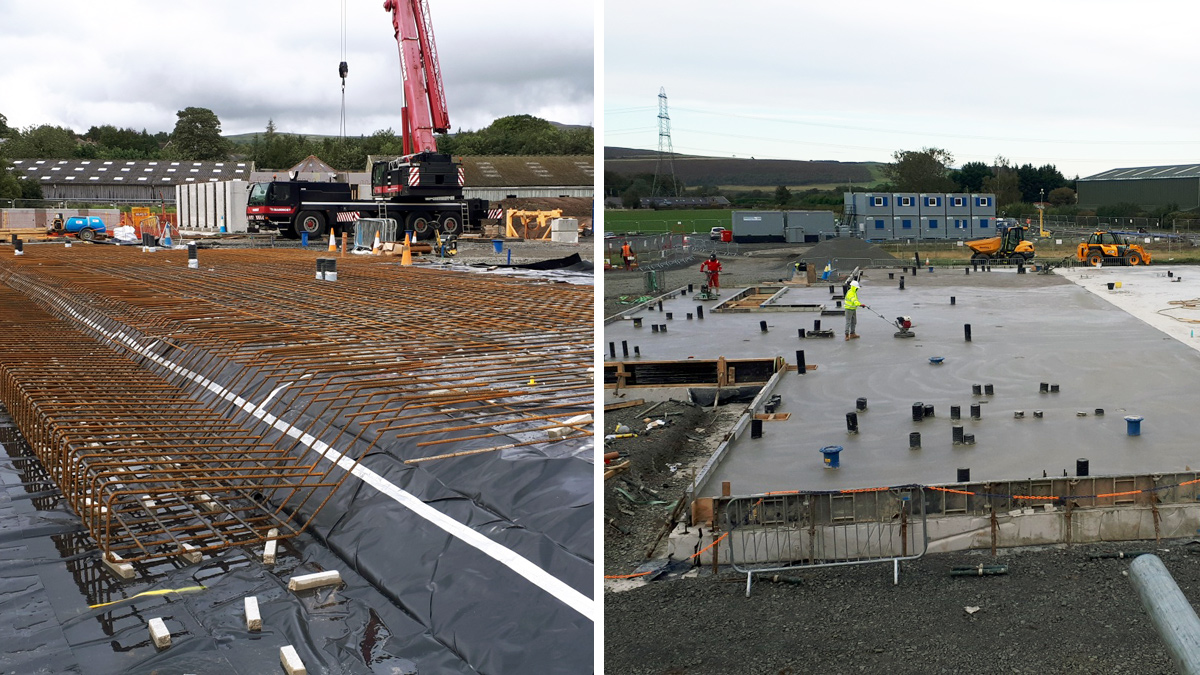
(left) Precise installation of below ground infrastructure and slab penetrations prior to main slab pour and (right) treatment building slab cast prior to superstructure installation – Courtesy of MMB
The accuracy minimised soil disposal resulting from over dig and designing out thrust blocks through modifications to the pipework specification further reduced excavation. Under licensed exemptions, 1000t of excavated soils were diverted to local agricultural projects and 1000t of compound stone was re-purposed for an off-site access road. Similarly, 1000t of clay arisings from a nearby project were utilised within the Wooler site.
Utilising CLIP (Collaborative Lean Improvement Programming) planning and careful sequencing halved the number of people working on site, compared to the sister project at Murton WTW, minimising the number of long journeys associated with rural working. Local suppliers and local staff were embedded within the delivery team, further reducing the embodied carbon impact. Accurate modelling of the proposal in advance of construction minimised material wastage in cut to suit elements of pipework, steelwork, and reinforcement.
MMB utilised the local supply chain as much as possible. Major successes were brought about through engaging with a heavy steel fabricator based within a quarter of a mile of the site and an electrical installation contractor based in Northumberland, rather than usual supply chain partners. Utilising more local suppliers meant that the level of service and quality provided was high, with benefits of carbon reductions and reduced transport of major steel elements along busy rural single carriageways. Through inviting NWG, stakeholders and supply chain to CLIP planning sessions, MMB identified programme savings for all parties through sequencing of site tasks and identifying mutually beneficial opportunities, such as sharing plant to reduce vehicles on site. For example, bringing electrical and major steel subcontractors together identified opportunities for cable containment hangers to be installed within the fabrication works at no additional cost, reducing work at height risk and task time for cable installation teams.
Construction sequencing, temporary works and site aesthetic were all modified to minimise impact on the local community. Installation of the permanent access point to the site was prioritised in the programme to minimise traffic management on Berwick Road, a main artery for the village. Moving treatment processes inside the main building negated the requirement for additional security fencing and the building itself was designed to resemble agricultural buildings in the area. The permanent site footprint was minimised as much as possible but in doing so, a larger temporary compound area was necessary. The project team worked with local landowners to identify the best location for the temporary works to reduce this impact, and temporary laydown areas were returned for use as soon as sequencing allowed.
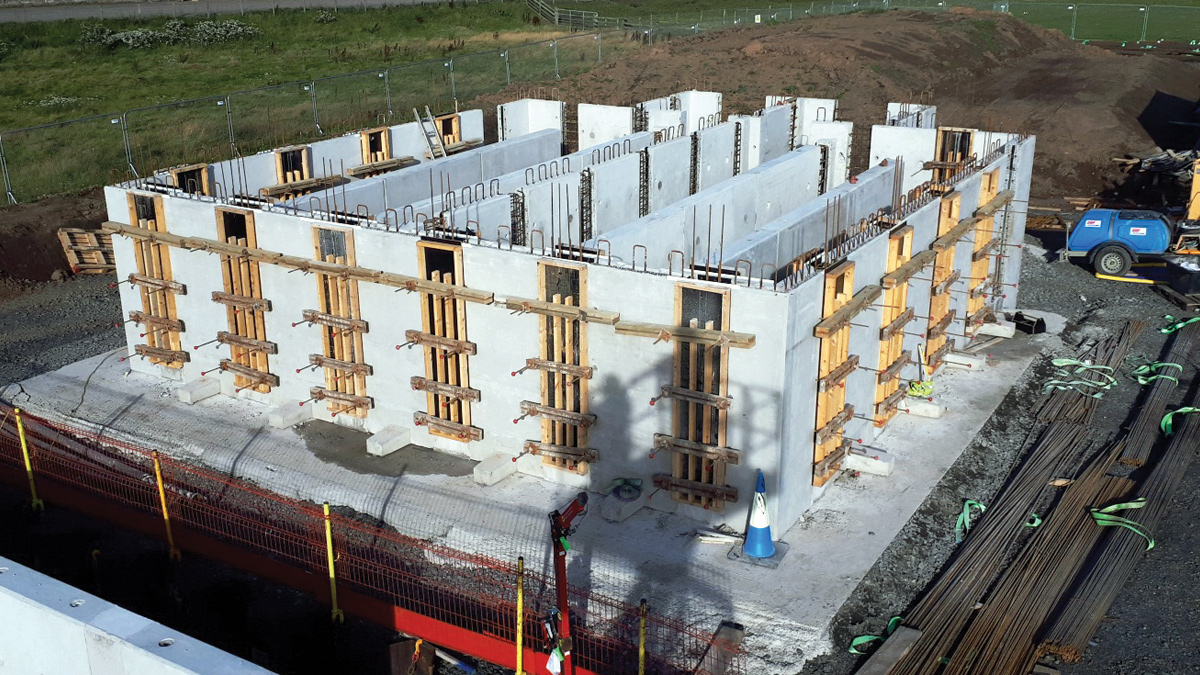
Precast contact tank during construction – Courtesy of MMB
Health & Safety
MMB’s positive safety culture was evidenced throughout construction, where in over 75,000 hours worked, over 5,500 proactive health and safety and environmental incidents were reported, resulting in no lost-time or reportable injuries. An added complication to this project has been the Covid19 pandemic, during which the site remained operational and avoided closure.
The project was sequenced to minimise the number of people working on the site at any time and method statements were developed to ensure as much work as possible could be completed whilst maintaining strict social distancing.
Conclusion
Wooler WTW was built as part of a two-project batch. The two sites were built sequentially, which enabled MMB to derive multiple lessons from the Murton project and deliver a new greenfield treatment works within the client’s budget and with minimal impact to the local community. MMB’s long-term collaborative relationship with NWG, combined with the use of trusted local suppliers, off-site build techniques and regular planning sessions enabled multiple sequencing and material efficiencies to be realised, further driving down the carbon impact of the project. Through digital delivery, a significant number of supplier interfaces were carefully managed, avoiding the delays and defects commonly associated with multidisciplinary projects.
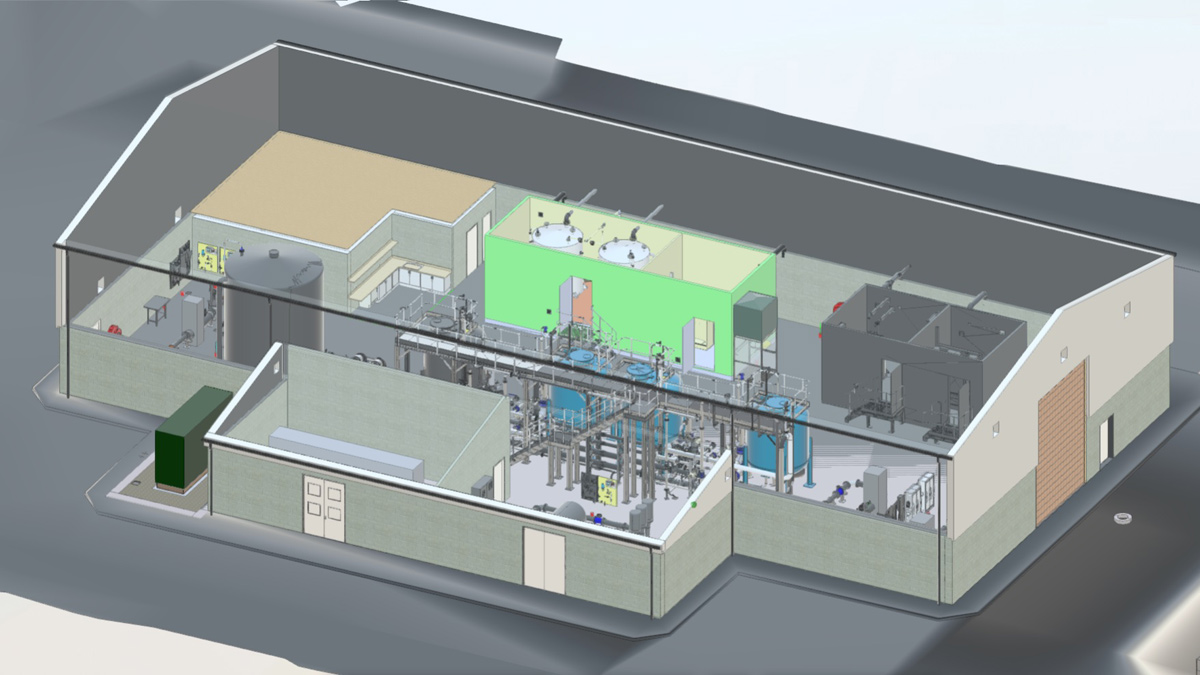
Model of multiple treatment processes within the main building - Courtesy of MMB