Woolston WwT Scheme – Part 5 (2020)
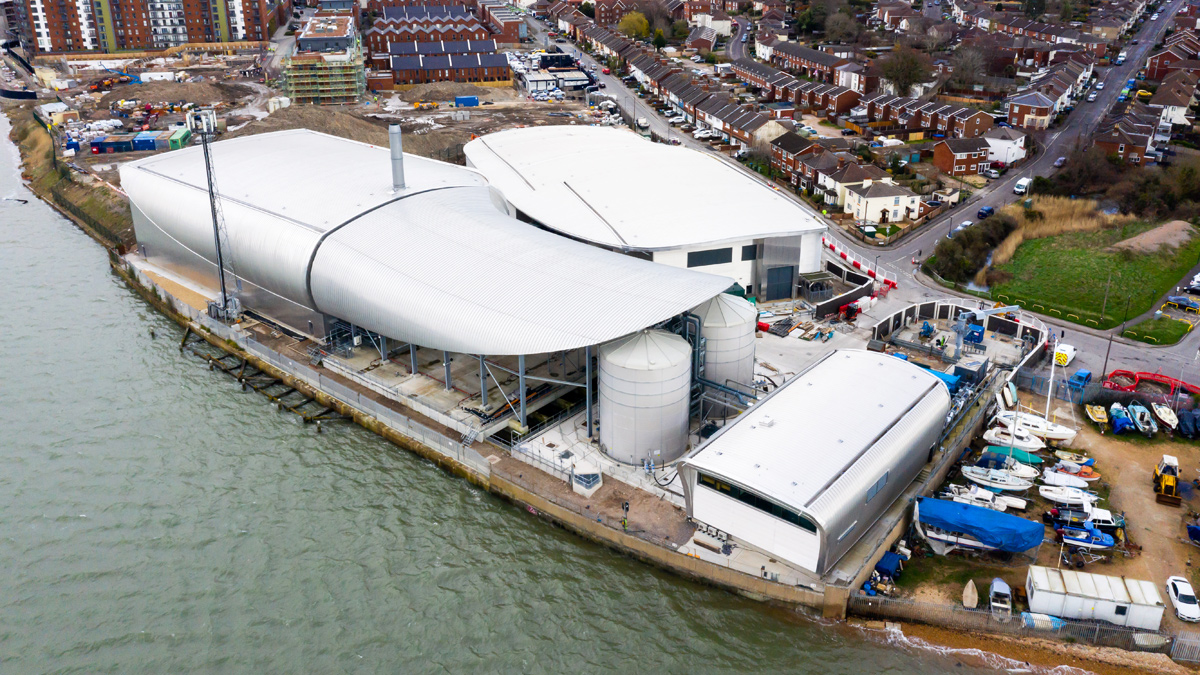
The redevelopment of Woolston WwTW is just a few weeks from completion - Courtesy of Southern Water
In October 2020, the finishing touches were undertaken at Woolston Wastewater Treatment Works, completing Southern Water’s £100m scheme to transform its works in Southampton, Hampshire. From the waterside, the new age space-like silver cladding that dominates the site is a much different picture from how the site has looked over the last few years when the site resembled a giant and complex jigsaw puzzle. The temporary wastewater treatment works, which served more than 60,000 people, was installed in 2015 since when the new works has steadily been erected. 4Delivery, a joint venture between Veolia Water Technologies, Costain and Stantec UK, undertook the design and construction of the project on behalf of Southern Water. The new site will fully treat flows up to 36.9 MLD, in compliance with the new discharge permit requirements.
Components of the site
The existing wastewater treatment includes:
- Inlet works comprising:
- Coarse and fine screens and screenings processing.
- Fat, oil, grease and grit, (FOGG) removal and processing.
- High rate primary sedimentation lamella process.
- Membrane bioreactor (MBR) plant comprising:
- Modified Ludzack Ettinger (MLE) activated sludge plant (ASP) for the biological removal of nitrogen.
- Membrane filtration tank, utilising microfiltration hollow fiber membranes.
- Existing ASP converted into a storm tank.
- Odour control comprising of chemical scrubbing and carbon units.
The sludge recycling includes:
- Sludge storage and blending.
- Indigenous sludge dewatering and processing.
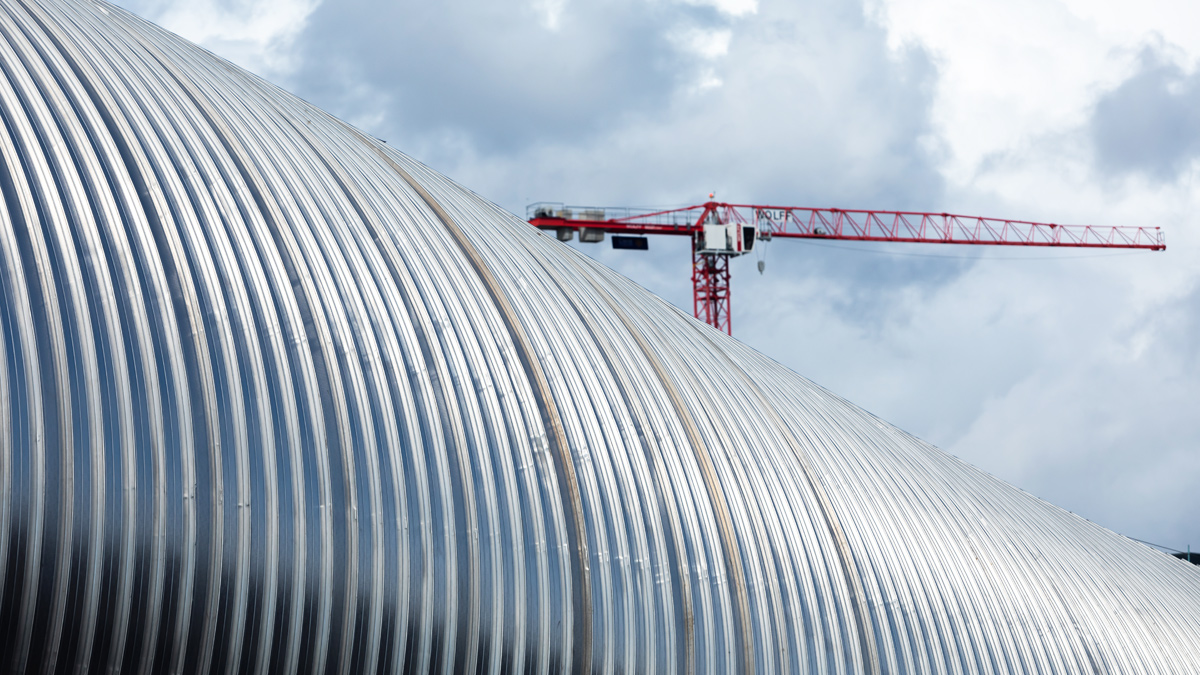
Finishing touches, including cladding, are taking place at the site – Courtesy of Southern Water
Final commissioning works
All the permanent process units have been in operation since May 2019, providing an effluent quality that exceeds the requirements with percentage removal in excess of 98% and 95% for the biological oxygen demand (BOD) and chemical oxygen demand (COD) respectively. The new processes allowed the final decommissioning of the old and temporary facilities in September 2019.
Optimisation and testing
To satisfy all expectations, 30 different tests were defined beforehand (in 2014). The required testing takes up to 28 days to complete and for some, at least three meetings with the contractor every week were needed to go through all the alarms raised by the plant, mainly for information. For example, a pump starting or finishing its normal cycle would send a message, but what the site team was looking out for was a potential alert of malfunction. More than 800 alarms have been revised in meetings this year.
Membrane bioreactor
The new membrane bioreactor (MBR) at Woolston WwTW, is capable of treating flow to full treatment of up to 427 l/s, significantly more that the 250 l/s which the old works could treat. Supplied by Koch Membranes, this MBR is considered to be in the range of ultrafiltration. Whilst not required by the Woolston consent, the installed membranes also meet the Environment Agency (EA) treatment-disinfection standard.
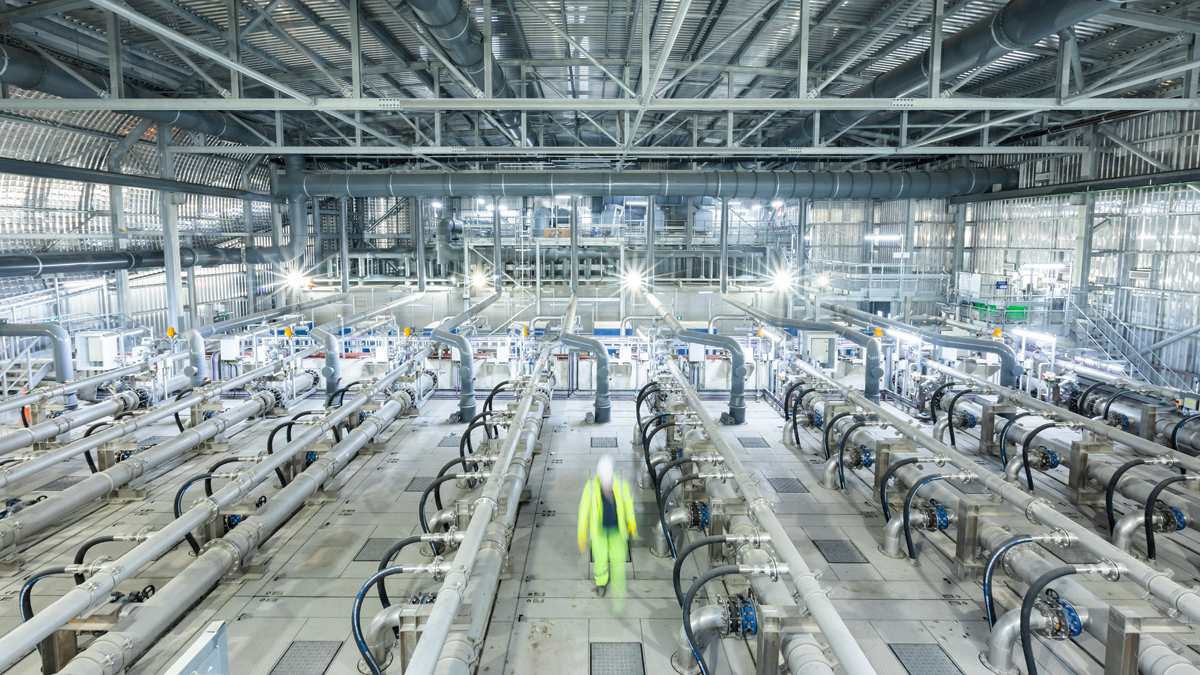
The impressive membrane bioreactor treats 427 l/s – Courtesy of Southern Water
The installed MBR consists of 8 lanes, with each lane comprising 5 (No.) modules, which totals a combined MBR surface area of 62,640m2. Unfiltered flows weir from the MBR tanks to a return activated sludge (RAS) pumping station and are returned upstream of the aeration tanks. The MBR operates on a 4:1 flow ratio, whereby 80% of the flow is passed to the RAS pumping station for recirculation and 20% is filtered through the membranes. Including for works generated flows, the RAS pumping is rated for returns of up to 2000 l/s, performed by 3 (No.) 1000 l/s duty/assist/standby RAS pumps. A second recirculation loop is provided by a dedicated recirculation pump for each aeration tank to return flows to the anoxic zone to achieve the process/denitrification requirements.
Filtered flows, known as permeate are drawn through the Pulsion LE-44 Koch membranes by in-dependent permeate pumps. Suction pressures across the membranes are dependent on the conditions but range from 0.05 bar up to their rated limit of 0.6 bar (~6 m water head).
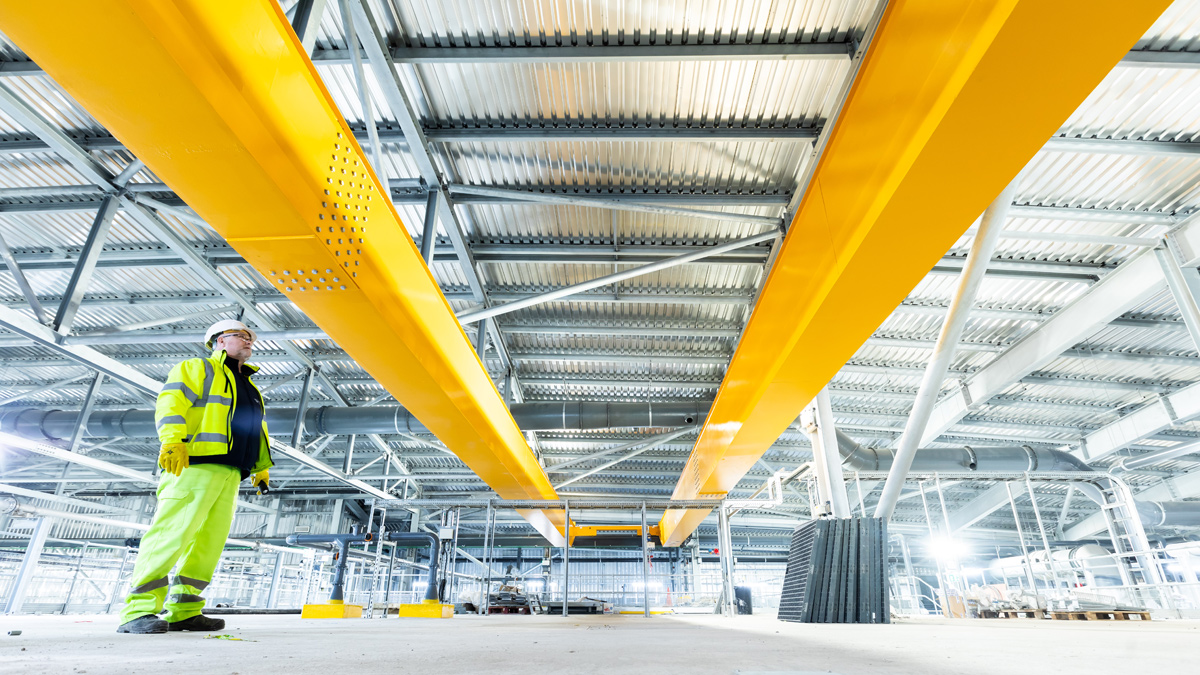
The cranes servicing the buildings are up to 33.8m long – Courtesy of Southern Water
Feedback from the community
One of the drivers of this scheme was to reduce the number of odour complaints received be neighbours and open dialogues between the site was set up from the start and included the community and local stakeholders such as councillors and group representatives. Overall, Southern Water has seen a drop in odour complaints despite the unfinished status of some key elements containing the odours, such as the cladding of the buildings, but this will be monitored following the full completion of the treatment works.
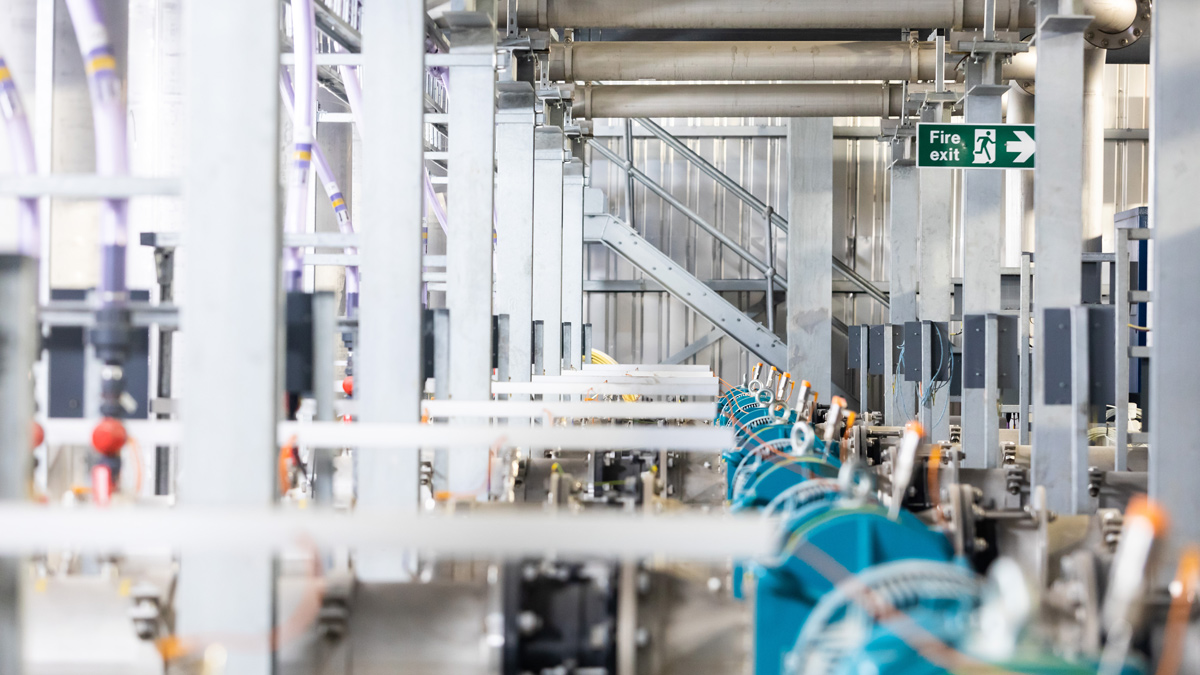
Southern Water operates the plant since March 2020 when the optimisation and testing was completed – Courtesy of Southern Water
Landscaping, paving and cladding
Landscaping was quite simple and in line with what would be expected at a regular wastewater plant. The number of trees and plants in the final design was limited in the early stages of the project by the aviation authorities as the site sits below the flight path to Southampton Airport and an excessive density of trees and plant could attract birds compromising the safety of the aircraft. However, a number of trees and plants were allowed to reproduce the old configuration that provided visual screening between the neighbours and, at that time, open tanks.
The cladding had to be adapted to the complex shapes of the buildings which required special attention in some areas of the buildings with double curvature and corners of the roofs. Some of the cladding design assumptions had to be revisited once installation started on site, but at the time of writing (September 2020) the cladding is well advanced and due to complete in October; a milestone that will represent the end to the construction activity for the project.
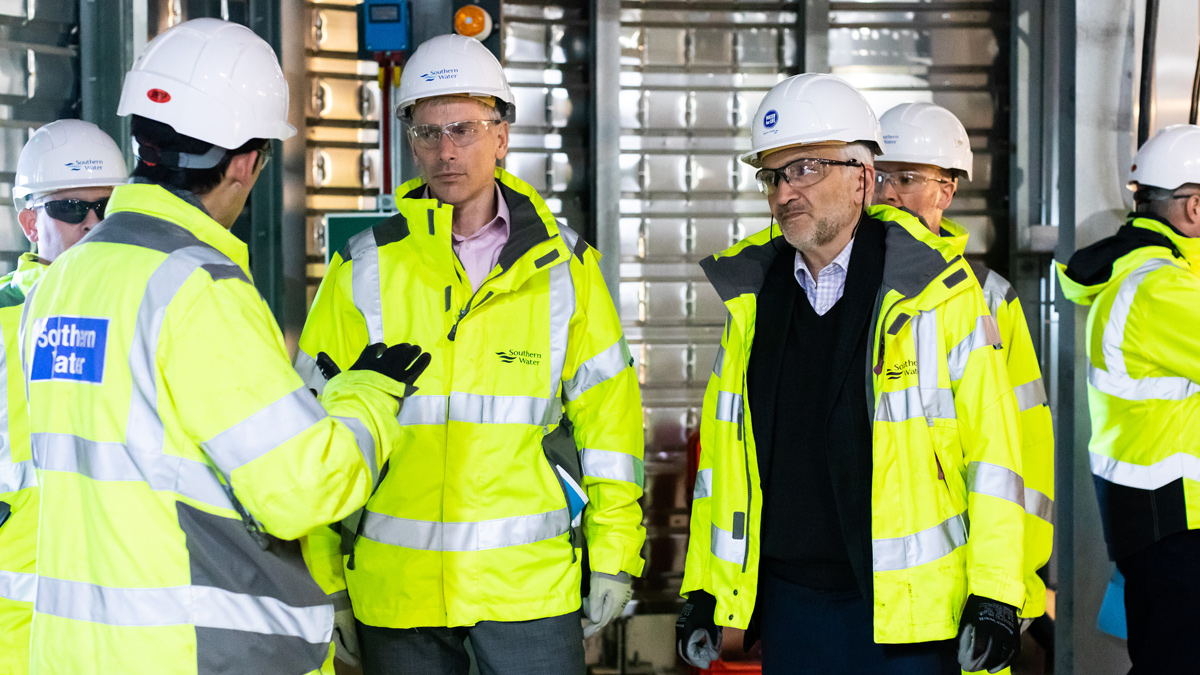
The collaborative ways of working were key in the success of the project with client and contractors based on site – Courtesy of Southern Water
Completion
Delays during the project and the impact of Covid-19 pushed the project completion time back to the end of October with a planned virtual launch with media and stakeholders.