Hawkhurst South WwTW (2021)
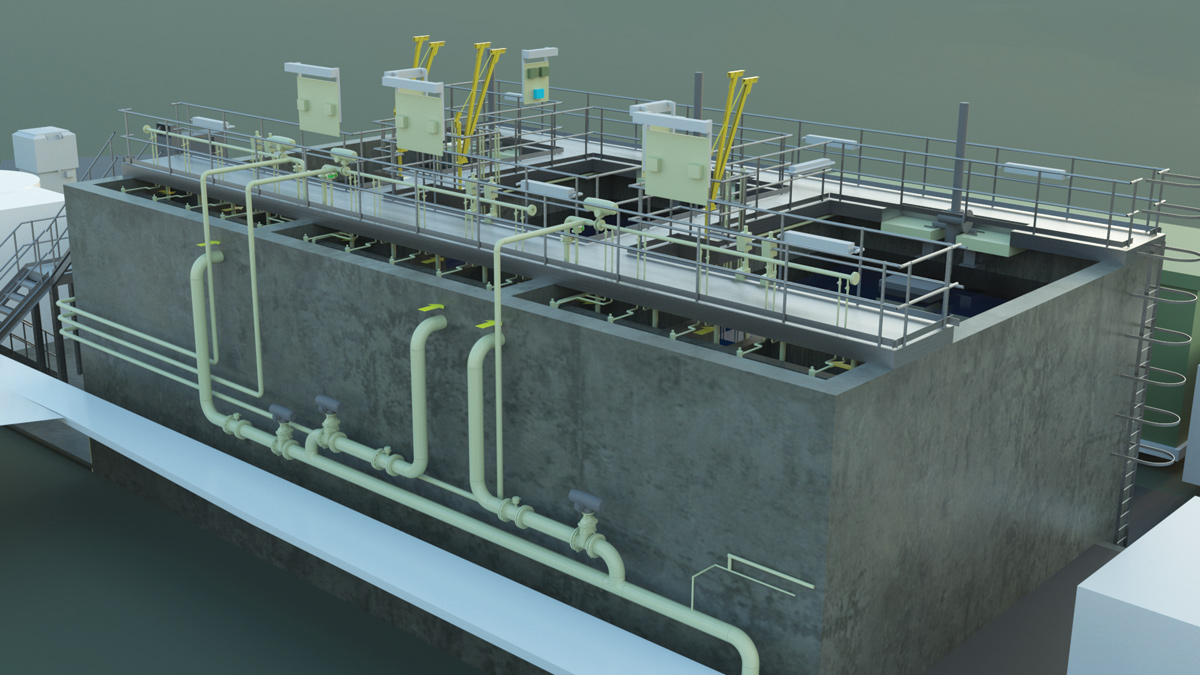
Figure 1: Hawkhurst South WwTW te-cyc™ tanks render - Courtesy of Te-Tech Process Solutions
The NEP Quality drivers for the Southern Water’s Hawkhurst South WTW are to meet the new iron and total phosphorus discharge permit limits by 31/12/2021, a tightened ammonia permit by 31/03/2025, and to maintain compliance with all aspects of the current discharge permit at lowest whole life cost. In addition, the population equivalent is set to rise from 1976 currently to 2285 by 2030. To meet the new consents and flow requirements, Trant Engineering Ltd proposed the use of an advanced cyclic activated sludge technology, te-cyc™, to be implemented to replace the existing aged biological trickling filters and humus tanks which are to be decommissioned and partly re-used, respectively. The te-cyc™ plant has been sized to treat a dry weather flow of 398m3/d and to meet the following consent values: BOD ≤ 20mg/l, NH4-N ≤ 3mg/l, Total-P ≤ 0.3mg/l (annual average), Total-Iron ≤ 4mg/l.
te-cyc™ system
The te-cyc™ process delivered by Te-Tech Process Solutions is a globally proven technology and was selected due to several key benefits over a conventional SBR design. These include:
- Smaller tank volume and footprint due to higher allowable MLSS concentration from improved settling characteristics.
- Bespoke design of anaerobic selector leads to formation of larger macroflocs which have an improved settling velocity and give a lower SVI, typically <100ml/g.
- The larger size of macrofloc also allows for simultaneous nitrification and denitrification which means that anoxic tanks with mechanical mixers are not required.
- Design of the anaerobic selector also promotes the growth of polyphosphate accumulation organisms (PAOs) within the macrofloc which provide an enhanced level of biological phosphorus removal and hence less ferric is required.
The fact that several drivers are satisfied simultaneously with the te-cyc™ process combined with the benefits listed above means that the process provides a lower whole life cost when compared to a conventional upgrade solution. The whole life cost savings are attributed to the reduced infrastructure required; a smaller footprint required which meant that additional land did not need to be purchased; and reduced chemical costs due to lack of alkalinity dosing required and enhanced biological phosphorus removal.
The te-cyc™ tank structure is made up of several individual basins. Always with two or more batch basins, the process allows for a continuous flow through the system as the basins are installed in parallel with their sequences out of phase with each other. This means that a buffer tank with expensive mechanical mixing is no longer required, therefore reducing overall site footprint and energy costs.
The process is broken down into three distinct stages that operate on a cycle: fill/aerate, settlement, and decant.
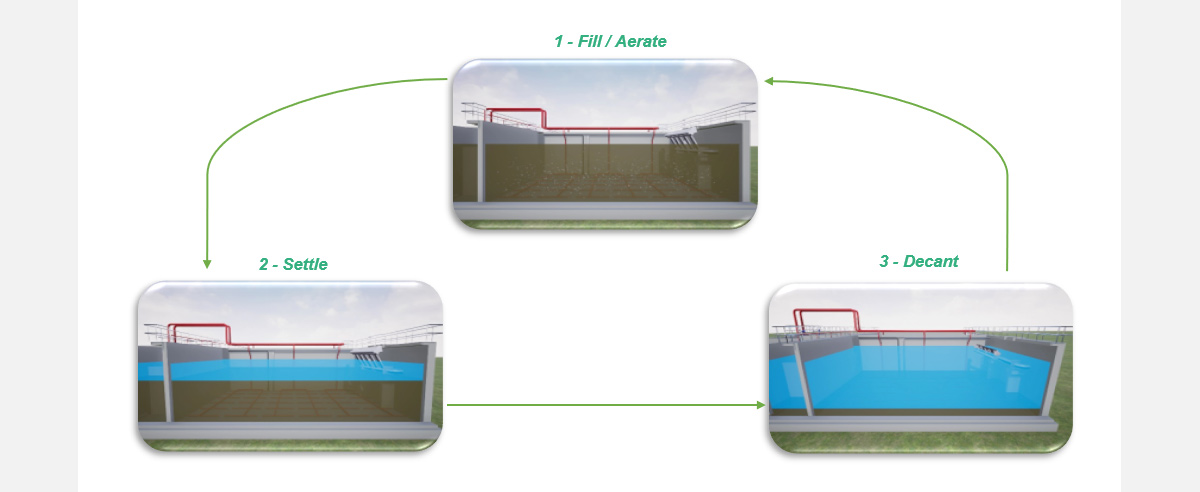
Figure 2: te-cyc™ process cycle – Courtesy of Te-Tech Process Solutions
Fill/aerate
During the fill/aerate stage, water enters a single te-cyc™ basin aerated zone via the anaerobic selector. Throughout this fill stage, the aeration zone is continually aerated at a rate controlled by the OUR (oxygen uptake rate) control system, and a portion of the sludge is constantly recycled to the inlet of the selector. Employing the OUR control system prevents over-aeration of the reactor basin allowing for additional energy savings. The design of this selector and recycle rate combined with the OUR control system allows for the formation of special macroflocs in which simultaneous nitrification/denitrification, BOD removal and biological phosphorus removal occurs. To meet the stringent phosphorus consent, ferric chloride is dosed during this phase into the inlet of the te-cyc™ to precipitate the phosphorus that is then removed with the waste sludge. Enabling biological phosphorus removal in the te-cyc™ process means that less ferric chloride is required, therefore reducing the operating expenditure.
Settlement
During the settlement phase, the inlet to the particular basin is closed, the internal recycle is stopped, and the sludge formed in the previous stage aggregates as a blanket and settles to the base of the reactor tank leaving a top layer of clear treated effluent. In typical wastewater applications, the settled sludge layer has a mean solids concentration of around 10 g/l.
Decant
In the decant phase, the mechanically driven decanter moves from the top water level to the bottom water level to remove approximately one third of the reactor volume which will be clear treated effluent. The decant arm also features a scum guard which prevents floating solids from discharging into the decanter. At the end of the decant phase, the decant arm is returned to its parked position which is above top water level. Towards the end of the decant phase, a portion of the settled surplus sludge is discharged.

Figure 3: te-cyc™ process cycle times – Courtesy of Te-Tech Process Solutions
Site constraints and project enabling works
Hawkhurst South WTW has a small site footprint which is constrained by surrounding ancient woodland and redundant infrastructure. The elevations also differ dramatically throughout the site which leads to extremely uneven ground levels. Due to the varying ground levels the te-cyc™ structure will be partially buried 1.75m into the ground on one side and 4.2m on the opposite side.
Before undertaking the detailed design, Ferroscan surveys were carried out at site on the existing concrete chambers and tanks surrounding the te-cyc™ to find out the current construction and condition of the structures. The survey results came back showing that the existing structures had been constructed without the use of reinforcement, only extensions to wall heights showed reinforcement. This meant that the sheet piling for temporary works would need to be vibration free to eliminate any risk of cracking to these existing structures. They would also need to be made a permanent part of the construction, remaining in place on completion of the te-cyc™ structure to ensure that no damage occurred to existing structures during sheet removal.
Modifications to the site would have to take place within the existing site perimeter, and construction and commissioning activities would have to fit around the continued operation of the existing site processes.
To create the space required for the new te-cyc™ plant and ancillary equipment, modifications will be made to the existing, redundant plant at Hawkhurst South WTW. This will comprise of the decommissioning and removal of an auto desludging pumping station as well as a glass coated steel sludge holding tank. This work will take place upfront of the main construction phase.
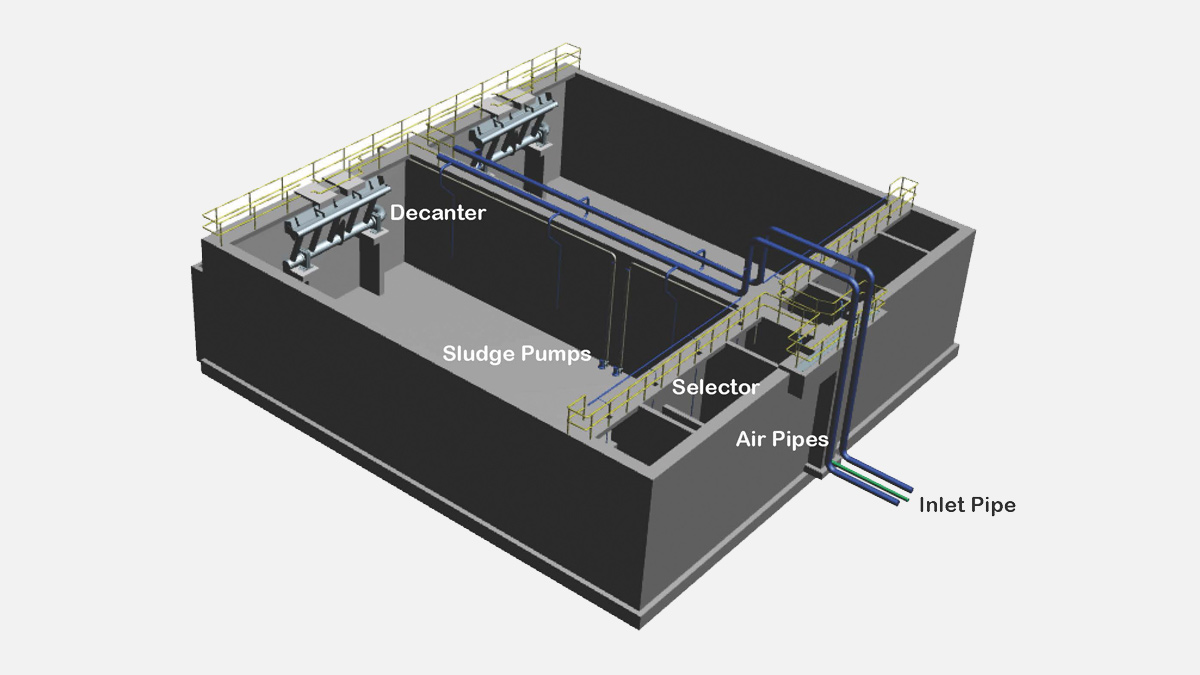
Figure 4: Typical te-cyc™ arrangement – Courtesy of Te-Tech Process Solutions
Project delivery partners
Te-Tech Process Solutions were sub-contracted for the design, build and installation of the new treatment MCC at Hawkhurst South WTW. The scope of work included for the design, manufacture, and testing of a new MCC including mains & generator incomer and feeder cubicles, DOL & VSD starter cubicles and ICA cubicle.
Te-Tech Process Solutions have a close link with the Trant Engineering Ltd and as such have access to the MEICA design resource pool. Early engagement ensured that the te-cyc™ process and panel designs were well on the way to completion prior to the MEICA detailed design being finalised thus guaranteeing a reduction in delivery. Without early engagement, this would not have been possible and would have increased the overall project programme.
The close working relationships forged between Trant Engineering Ltd and Te-Tech Process Solutions ensures that, during early engagement, all possible scenarios are explored, and designs verified, by people with extensive experience in all areas of MEICA project management and design. This ensures a ‘right first time’ product which can be built to the tightest of deadlines, is stringently tested, and is of the highest quality.
Hawkhurst STW: Supply chain – key participants
- Client: Southern Water
- Principal contractor: Trant Engineering Ltd
- Process partner: Te-Tech Process Solutions
- Process partner: SFC Umwelttechnik
- MCC design/manufacturer: Te-Tech Process Solutions
- Temporary works: MGF Ltd
- Chemical dosing: Lintott Controls
- Sludge pumping: Xylem Water Solutions
- Washwater/final effluent distribution: KGN Pillinger
- Air blowers: Aerzen Machines
- Tertiary filter: Eliquo Hydrok Ltd
- System integration: Te-Tech Process Solutions
- System integration: SFC Umwelttechnik
- Valve supply: Glenfield Invicta
- Flow controls: AUMA Actuators Ltd
- Kiosk access stairs & platform: Step on Safety Ltd
Delivery timescales
The detailed design and construction phases of the Hawkhurst South WTW Project are now well underway with the regulatory compliance date of the 31/12/2021 to meet the new iron and total phosphorus discharge limits due to be achieved.
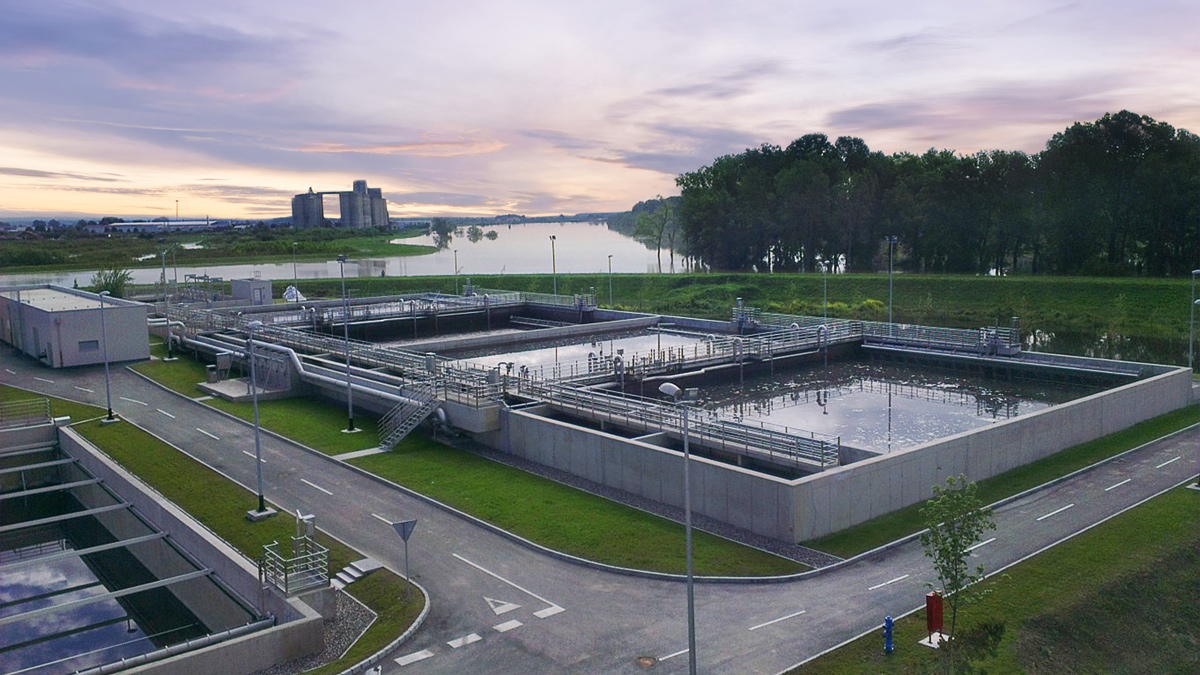
Figure 5: A te-cyc™ plant in Croatia (PE: 80,000) – Courtesy of Te-Tech Process Solutions
Conclusion
Through quality communication and a collaborative approach, the Southern Water, Trant Engineering Ltd and Te-Tech Process Solutions project team have produced a bespoke, compact, and efficient design to deliver the required iron and total phosphorus discharge permit limits and tightened ammonia permit limits whilst maintaining compliance with all aspects of the current discharge permits at lowest whole life cost. This approach has been maintained throughout the detailed design and construction and will ensure a good working relationship in any future projects.