Affinity Water Metaldehyde Removal Project (2020)
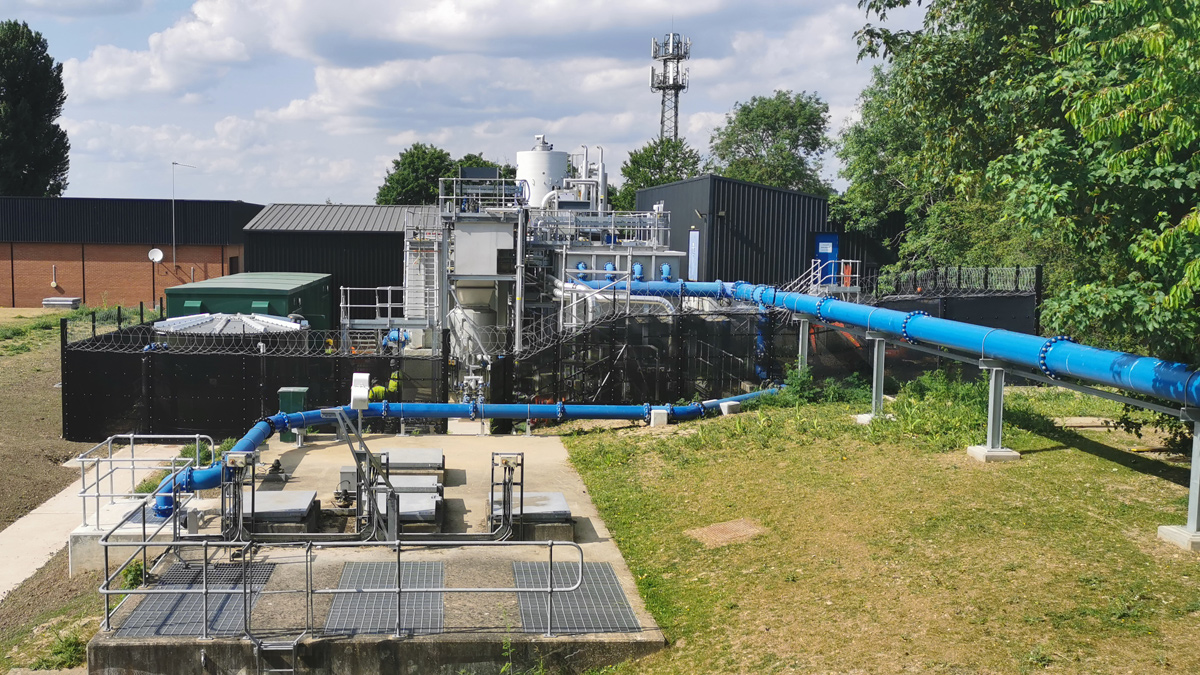
Affinity Water's metaldehyde removal plant - Courtesy of Trant Engineering
Affinity Water own and operate a crucial and long-standing water treatment works which is situated to support the north London water supply infrastructure. Any shortfall in the production of treated water leads directly to the need for importing water from a neighbouring water company. Four groundwater sources are combined and treated at site, all of which are susceptible to both historic and diffuse pollution such as pesticides, bromate, nitrate and turbidity. Currently, one of the pesticides of significant concern to a number of water companies is metaldehyde as it is not readily removed by conventional pesticide removal processes. Metaldehyde is an organic compound widely used in the agriculture industry against slugs and snails.
Background/process selection
Affinity Water’s catchment management activities have helped to flatten the curve of the metaldehyde concentrations present in the raw water sources being abstracted that are affected by the karstic geology in the area. However, due to historic ground contamination, the levels of metaldehyde present in the raw water from one of the sources is still above the European Drinking Water Directive specified maximum amount (0.1µg/l).
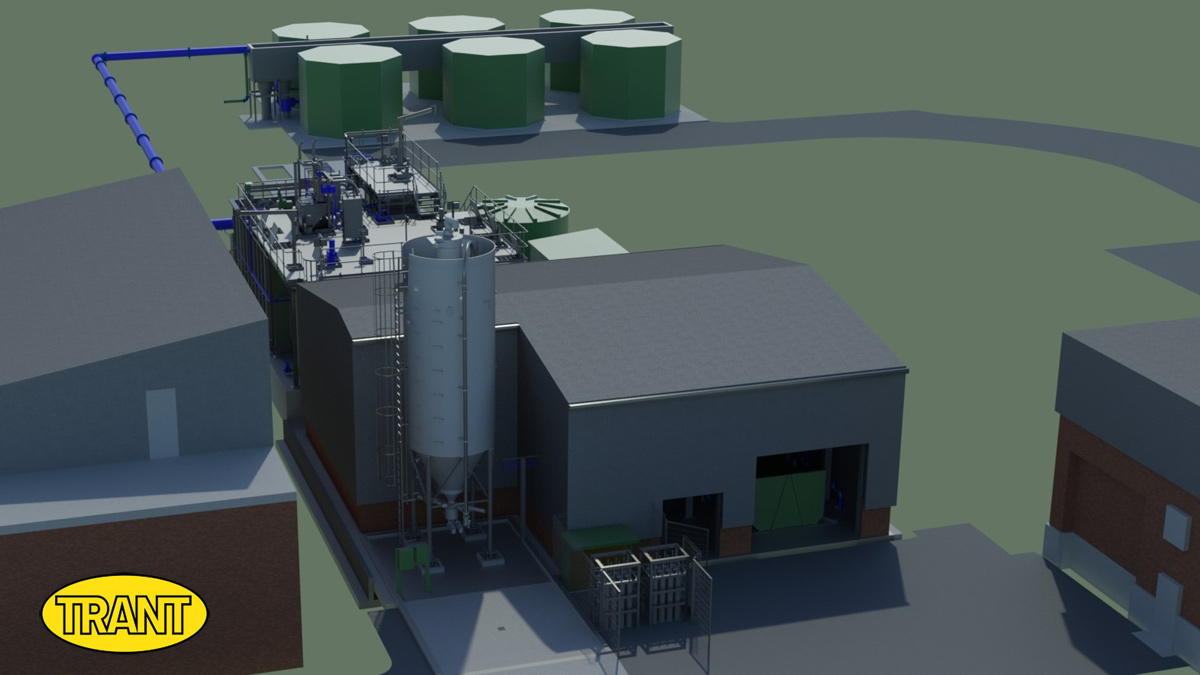
3D render of the metaldehyde removal plant – Courtesy of Trant Engineering
Affinity Water has an undertaking with the Drinking Water Inspectorate to construct and commission a new treatment process for metaldehyde removal. Affinity Water requires the treatment solution to deliver the required metaldehyde and turbidity levels, without adversely affecting the existing treatment process and final water quality. Affinity Water initially contracted Trant Engineering to review several options to increase resilience and reduce the need for importing treated water.
After a period of optioneering a solution was identified where a single groundwater source would be treated using Veolia Water Technologies UK’s Actiflo® Carb process and then blended with the remaining sources, thus reducing the residual metaldehyde content safely below the prescribed concentration. Affinity Water appointed Trant Engineering as principal designer and contractor to undertake the design, construction and commissioning of the option identified. Veolia Water Technologies UK were engaged and appointed as the process delivery partners for the Metaldehyde Removal Project.
Actiflo® Carb & powder activated carbon
Technologies using powdered activated carbon (PAC) are increasingly used in the treatment of drinking water for the removal of natural organic matter, pesticides, micro pollutants and substances that cause tastes and odours. Veolia Water Technologies have developed a process, called Actiflo Carb which combines its ballasted floc clarifier Actiflo and a powdered activated carbon reactor providing micro pollutant removal capabilities.
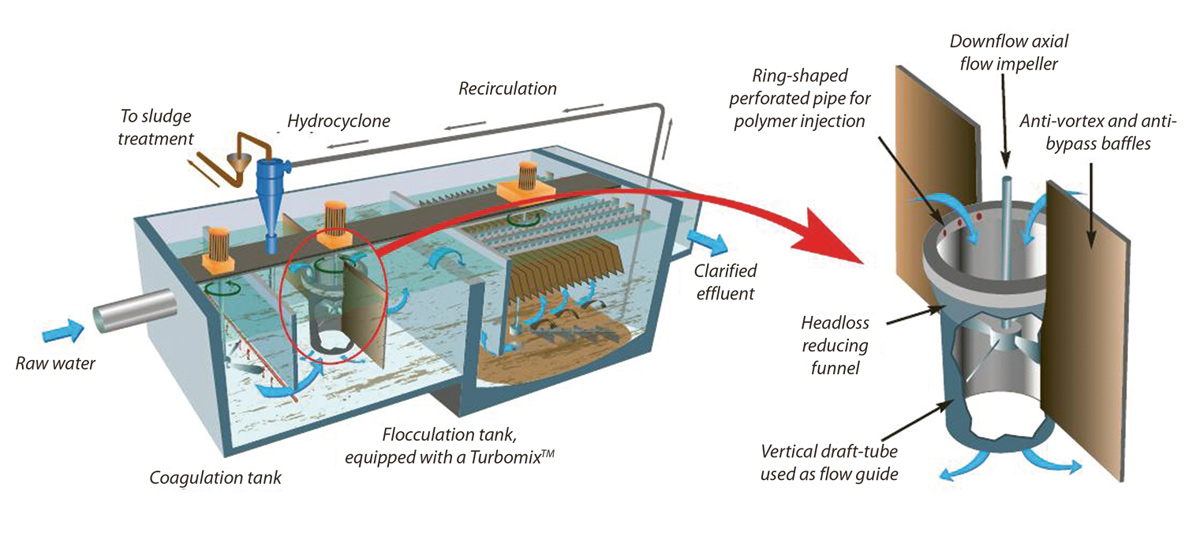
Example of the Actiflo® process flow diagram – Courtesy of Veolia Water Technologies
The porous structure of PAC develops a large hydrophobic specific surface area around 1000 m2/g PAC and the micro pollutants removal mechanism is dependent on the concentration gradient between water and the PAC pores. The adsorption capacity varies for each molecule. The heavier the molecular weight, less polar and less water soluble the molecule is, the better the removal efficiency by PAC adsorption. The removal of pesticides is directly dependant on the initial concentration of the compounds, the PAC dose and the type of PAC used in the process; the greater the PAC dose, the greater the elimination of pesticides. A ratio between octanol solubility and water solubility, called Ko/w is used to measure the expected removal rate, the higher this ratio is, the greater the expected removal rate.
Combining a PAC reactor with the Actiflo Carb process can treat a wide variety of raw water types, including water known to cause problems with classical settling techniques. This includes water that contains molecules related to the presence of plankton-based micro-algae, water that contains endocrine disruptors, coloured water and water with low total suspended solids. The main advantage of the Actiflo Carb is its dynamic ability to adapt to sudden variations in raw water flow, organic quality and load variations. It also has a quick start up time of around 20-25 minutes. For waters which vary in nature and concentration, laboratory experiments are carried out to determine the type of PAC to use and the dose of fresh PAC that needs to be added for optimal removal.
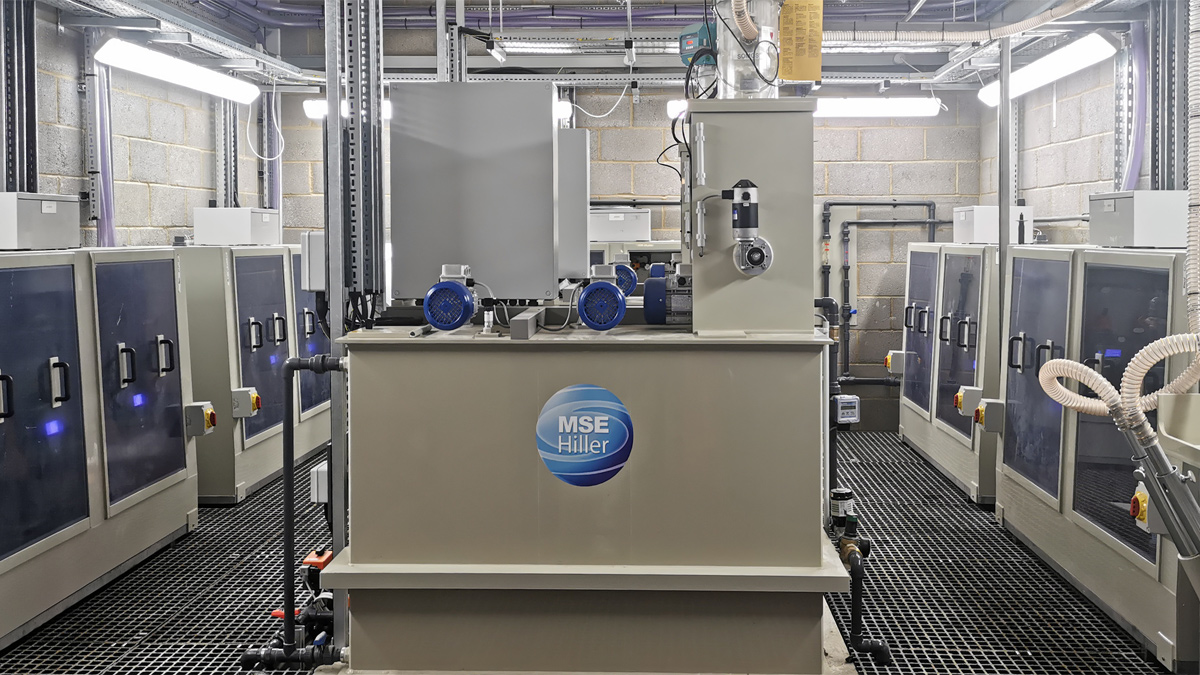
Chemical dosing room from MSE Hillier – Courtesy of Trant Engineering
Optimisation of plant shutdowns
During construction, it was critical that site outages were kept to a minimum to limit the potential risk of down time of the water supply to the public. This was achieved by optimising plant shutdowns at strategic times which coincided with specific construction works taking place. One example was the construction and connection of an offsite raw water pipeline which delivered flow to the Actiflo Carb process.
Trant Engineering designed the pipeline diversion early in the programme, providing details of the proposed connection location and methodology to enable Affinity Water to make the necessary arrangements for a shutdown of the source borehole pumps. Trant Engineering’s site team were then engaged to construct much of the pipework diversion offline. By working collaboratively, a date was identified to inhibit the source borehole pumps and simultaneously organise the isolation of the pipeline and the construction of the final connection to the new diversion pipe. In total the borehole pumps were inhibited for less than 6-hours meaning that the reduced site output did not adversely affect the infrastructure being supported.
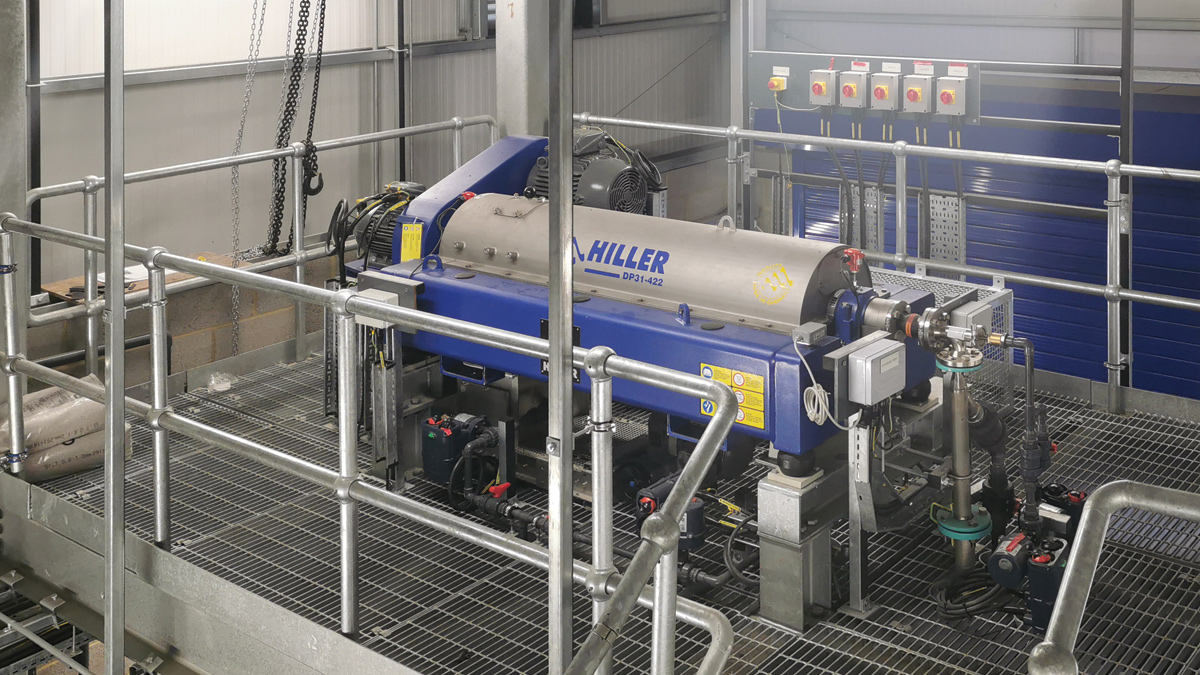
Dewatering centrifuge from MSE Hiller – Courtesy of Trant Engineering
Plant commissioning
Trant Engineering Ltd have access to specialist resources who would be present on site to manage and progress the dry and wet commissioning phases of the metaldehyde removal plant. The newly installed treatment facility was fed and commissioned using raw water from the source which has been identified for treatment. During wet commissioning, a bespoke site cabin was set up to facilitate the testing of raw water and treated clarified water. Samples were taken several times per day to analyse flow rate, total aluminium, soluble aluminium, turbidity, pesticides and metaldehyde. This enabled the Trant Engineering commissioning team to adjust system parameters and identify an optimum process setup thus achieving the best results from the metaldehyde removal plant.
Trant Engineering and Affinity Water made use of an existing online metaldehyde monitor during commissioning which took clarified water samples from the outlet of the metaldehyde removal plant. The sampling frequency of the online metaldehyde monitor can be as high as one sample every 36 minutes compared to over 24 hours for normal laboratory analysis of a single sample. This equipment provides robust and reliable metaldehyde data allowing the commissioning and operational teams to use near real time feedback on plant commissioning and performance.
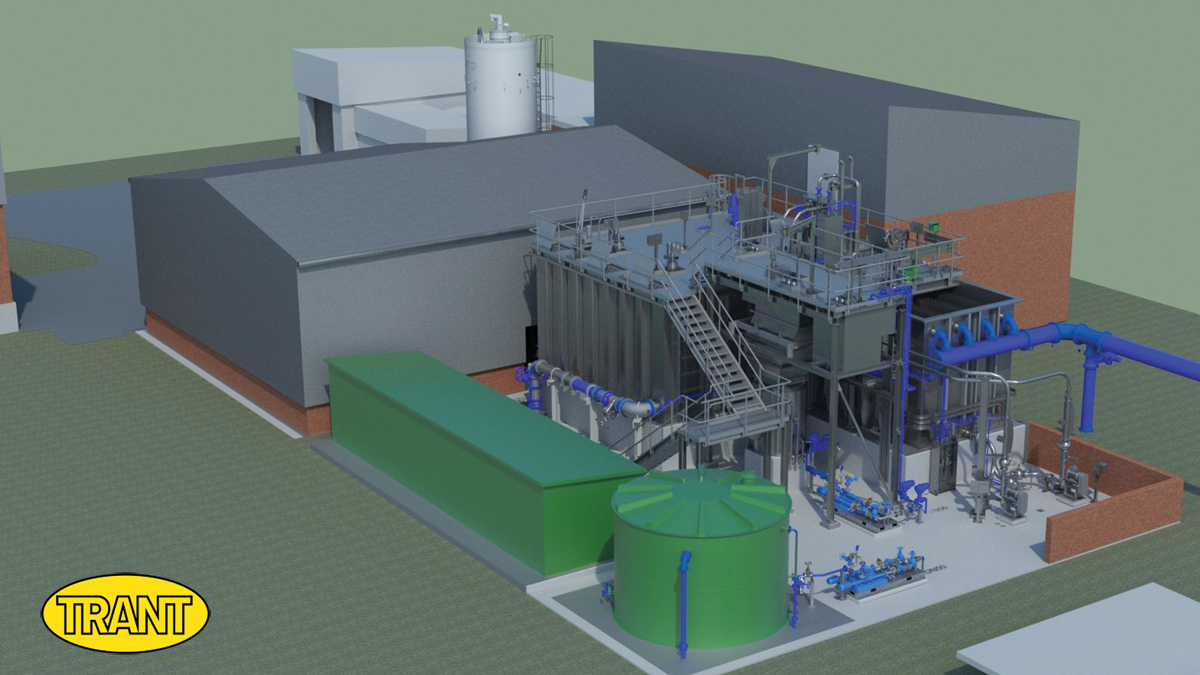
3D render of the metaldehyde removal plant – Courtesy of Trant Engineering
Project delivery partners
Trant Automation Control & Technology (ACT) were contracted for the design, build and installation of the metaldehyde treatment and wastewater MCC for Affinity Water. The scope of work included for the design, manufacturing and testing of a new MCC including mains & generator incomer cubicles, feeder cubicles, DOL and VSD starter cubicles and ICA cubicle.
ACT form part of the Trant Engineering Group and as such have access to the MEICA design resource pool. Early engagement ensured that the panel designs were well on the way to completion prior to the MEICA detailed design being finalised thus guaranteeing a reduction in possible delays. Without early engagement, this would not have been possible and would have increased the overall project programme length. Once manufacturing had been completed, ACT utilised water sector specific ISO approved test procedures to ensure that the factory acceptance tests undertaken conformed to a consistently high standard.
In addition to ACT, the Trant Group also contracted Trant Offsite Manufacturing & Assembly (OMA), who offer a specialist service with a primary focus on identifying, designing and manufacturing innovative offsite solutions within a highly controlled workshop environment.
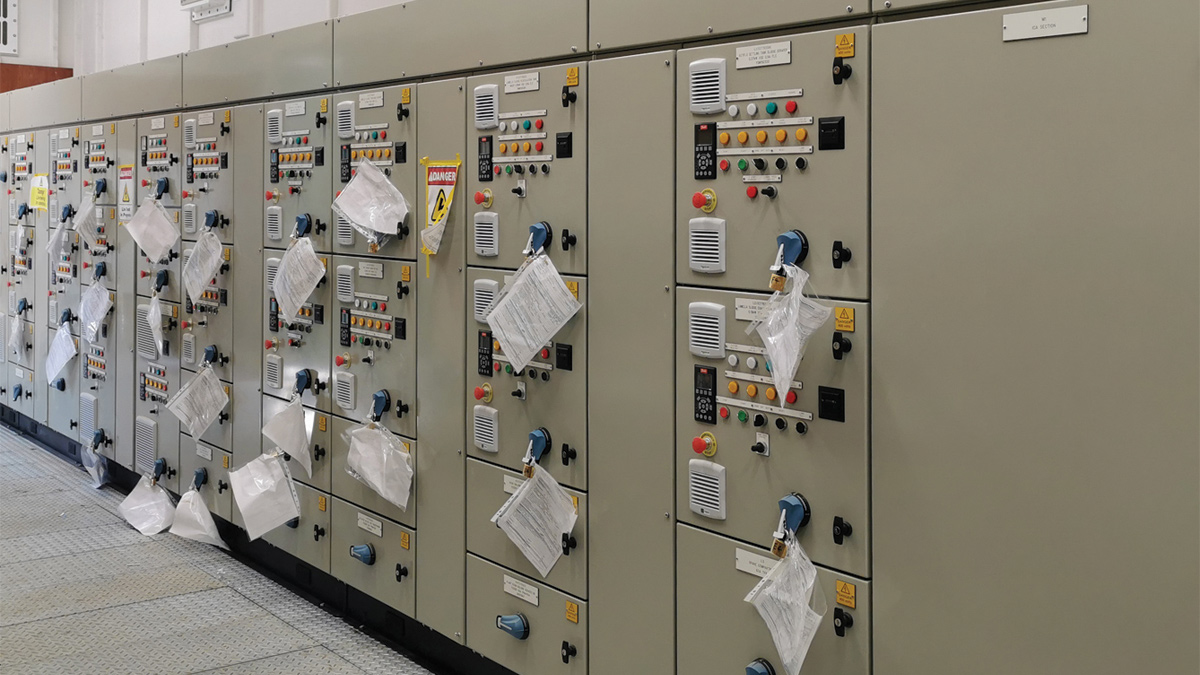
New metaldehyde removal plant MCC by Trant ACT – Courtesy of Trant Engineering
OMA utilise the latest 3D design software to develop detailed design drawings into fabrication drawings. They also utilise a large fabrication workshop which includes separate ferrous and non-ferrous welding areas and fabricators who are trained in a variety of high-quality welding techniques and to use the very latest technology and equipment.
With access to the knowledge and skill set that OMA offer, Trant Engineering has been able to incorporate DfMA and offsite manufacturing into the design which has reduced programme length and CAPEX whilst also increasing safety on site during installation.
The close working relationships, both personal and professional, forged within the Trant Group, ensured that during early engagement all possible scenarios were explored and designs verified by people with extensive experience in all areas of MEICA project management and design. This ensured a ‘right first time’ product which can be built to the tightest of deadlines, that is stringently tested, and is of the highest quality.
Affinity Water Metaldehyde Removal Project: Supply chain – key participants
- Principal contractor: Trant Engineering Ltd
- Process delivery partner: Veolia Water Technologies UK
- Civil design partner: Godsell Arnold Partnership Ltd
- Offsite manufacturing: Trant Engineering Ltd – OMA
- MCC panel design/build: Trant Engineering Ltd – ACT
- Dewatering & chemical dosing equipment: MSE Hiller
- Sludge pumping equipment: Mono Pumps
- Mechanical installation: TerraFlow
- Electrical installation: Vears M&E
- System integration: Riverside Automation
- Technical documentation: 3rd Light Media
- Valve supply: R2M Limited
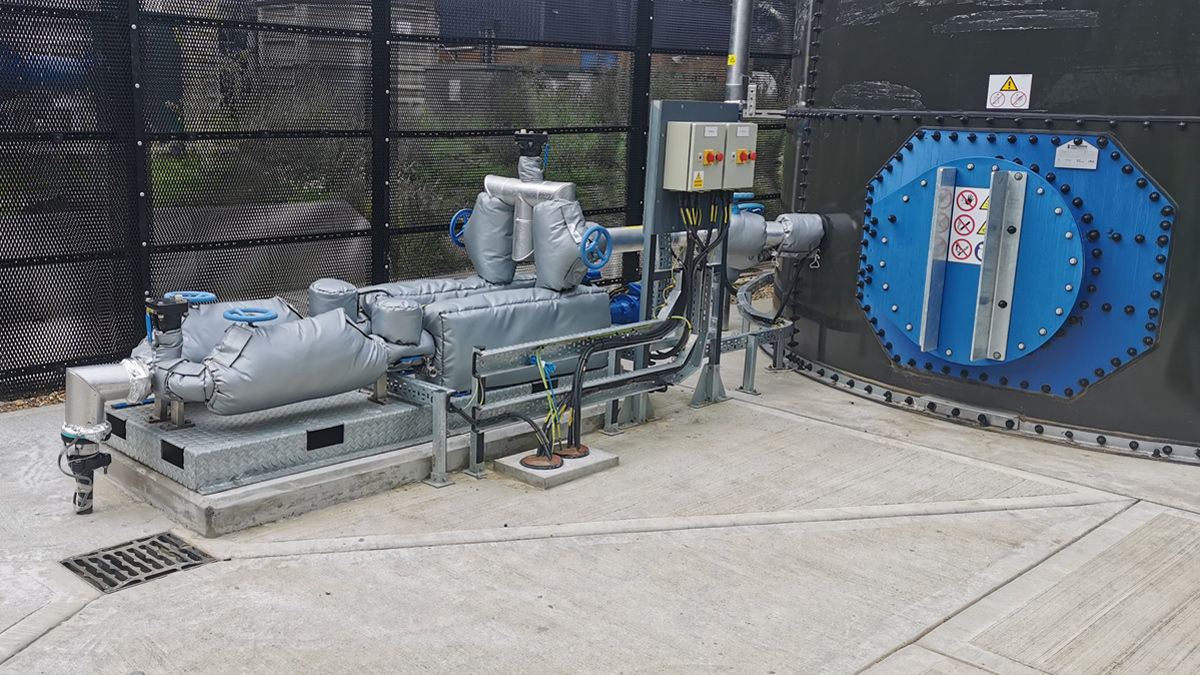
New sludge transfer pumps by Trant OMA & Mono Pumps – Courtesy of Trant Engineering
Delivery timescales
At the time of writing (June 2020) the detailed design and construction phases of the Affinity Water Metaldehyde Removal Project have now been completed and the commissioning is well underway. The project hand over is due to take place in the final quarter of 2020.
Conclusion
Through quality communication and a collaborative approach, the Affinity Water, Trant Engineering and Veolia Water Technologies UK project team have produced a bespoke, compact and efficient design to deliver the required metaldehyde and turbidity levels, without adversely affecting the existing treatment process and final water quality. This approach has been maintained throughout the detailed design and construction and will ensure a good working relationship in any future projects.