North Tawton STW (2016)
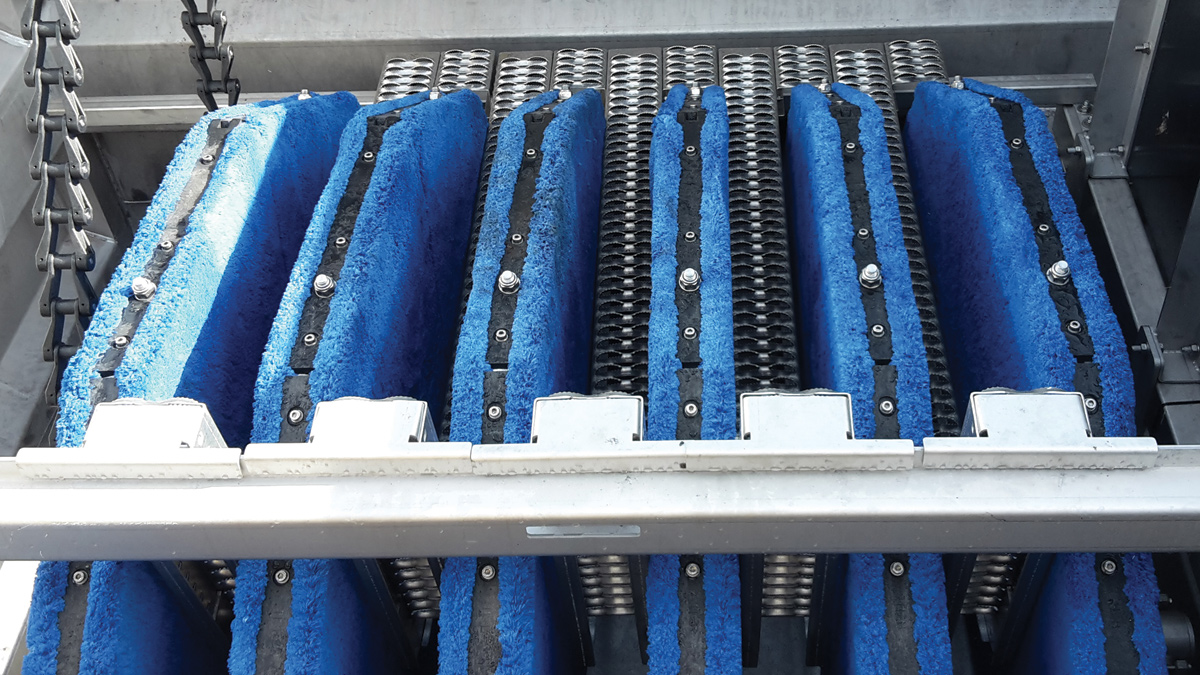
Mecana filter discs - Courtesy of SWW Delivery Alliance H5O
South West Water (SWW) is currently participating in a National Programme of Trials to investigate the feasibility of using new technologies to achieve very low phosphorus (P) levels in final effluent discharged from sewage treatment works. The trials, which are funded under the Phase 4 NEP, are organised by UK Water Industry Research (UKWIR) to a protocol agreed with the Environment Agency and involve all ten water and sewerage companies. As part of this programme, SWW was asked to install and evaluate the performance of a tertiary treatment process known as an Mecana filter from Eliquo Hydrok Ltd. This formed part of a project to design, construct, commission and optimise the sewage treatment process at North Tawton STW) targeting a total phosphorus level of <0.1 mg/L in the final effluent discharged to the River Taw. Following commissioning of the upgraded works, a 12 month sampling and monitoring period ending in March 2017 will provide data to evaluate the effectiveness of the Hydrok-Mecana filter technology in achieving the very low phosphorus target.
The project
North Tawton STW is located approximately 10km north east of Okehampton in mid-Devon. It receives pumped and gravity from the village of North Tawton, which has an existing population equivalent (PE) of 2196. The STW has a consented flow to treatment of 12l/s. The existing treatment process consists of a StormGuard screen (for storm and gross storm flows) discharging to a storm tank and an inlet screen (for flow to treatment) that feeds into twin primary settlement tanks.
There are 4 (No.) biological filters and 2 (No.) humus tanks which feed through an HSAF unit before the final effluent outfall.
At present there is no P permit for North Tawton STW and the P concentrations on the final effluent range between 2mg/l and 10mg/l. However given that the site will be subject to a P permit in future, the works provided under this project needed to meet both the requirements of the trial and ensure the site is ready to meet the requirements of the future P permit. In addition, the project aimed to improve the poorly performing inlet works screening and PSTs which presented a risk to the performance of the new P removal plant. The following upgrade was identified to fulfil this criteria:
- Replacement of the existing inlet screen with a new 6mm mechanically raked band screen.
- Construction of a new primary settlement tank (6.3m diameter) to reduce solids carry over into the process.
- Chemical dosing for phosphorus removal – new alkalinity and coagulant storage with dosing kiosks.
- Modifications to an existing grease trap to house a mechanical mixer to provide sufficient turbulence for chemical dosing upstream of the primary tank.
- As a result of the increased sludge production due to chemical dosing, a new 38m3 sludge tank was required.
- Modification to an existing humus tank distribution chamber to include a mechanical mixer for the second stage chemical dosing.
- A new Hyrok-Mecana filter for tertiary phosphorus removal.
- Instrumentation to monitor solids, phosphorus and aluminium.
Design and construction
South West Water’s Delivery Alliance H5O was responsible for the delivery of this project with a team consisting of SWW as the client, Interserve Construction as principal contractor and AECOM as lead designer.
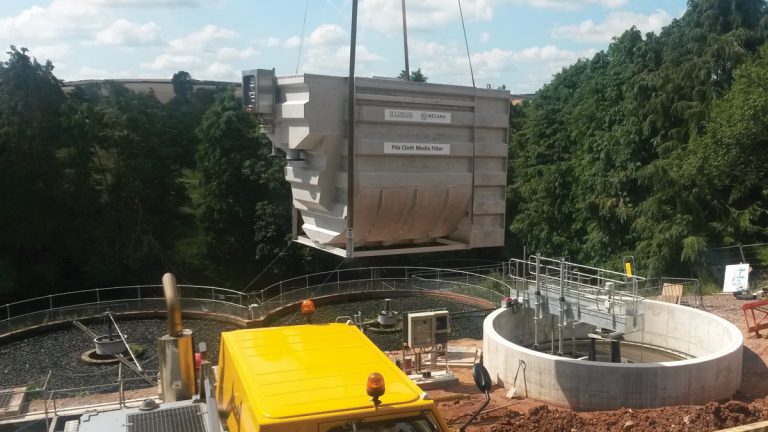
Lifting the Hydrok-Mecana filter over the site – Courtesy of SWW Delivery Alliance H5O
The H5O team was charged with delivering the design, construction and commissioning of the project within a challenging 12 month programme governed by the trial start date of December 2015.
The team was therefore keen to identify opportunities to expedite the design and construction phase; this included ensuring the production of design deliverables dovetailed with the critical path items on the construction programme, and employing innovative design and construction solutions.
Opportunities to reduce costs by means of reuse of existing assets were explored. The site layout posed a number of challenges due to its steep topography and restricted working space.
At the inlet works, the existing inlet screen was replaced with a Haigh band screen and associated modifications to the flow control weirs. The existing StormGuard storm screen was found to be in good order and was retained. Downstream from the inlet works, the existing grease trap chamber was re-configured for use as the primary coagulant dosing chamber with a paddle mixer.
The existing reinforced concrete Dortmund primary settlement tanks were unable to treat the effluent to a sufficient quality to suit the new tertiary process. There was limited space on site available to construct replacements but a solution was found for a 6.3m diameter RC tank located adjacent to the site access road on a sloping area of disused ground.
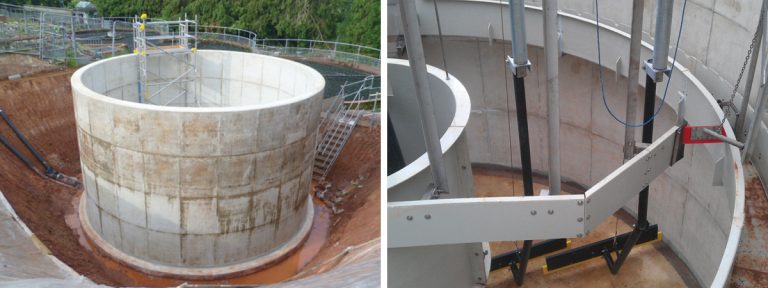
(left) Cast in situ primary settlement tank prior to backfilling and (right) Primary settlement tank scraper arrangement – Courtesy of SWW Delivery Alliance H5O
Careful landscaping design ensured safe access around the entire perimeter of the tank for maintenance whilst minimising the requirement for temporary works. Arisings from the excavation were used to backfill the old primary tanks before they were capped off with a concrete deck. This area was then used to site the alkalinity dosing kiosk thereby maximising the use of available site space. A difference in ground level between this area and the site access road resulted in a simple, yet innovative design for a delivery chute to safely convey bagged chemical deliveries.
Downstream from the primary settlement tank (PST), an alkalinity injection point was installed upstream of a new flow distribution chamber. This chamber was constructed using a GRP fabrication to minimise the temporary flow management needed to maintain the treatment process. Flows downstream pass through existing trickling filters and then collect in a distribution chamber where secondary coagulant doing is added upstream of the humus tanks.
The new Hydrok-Mecana filter was constructed on a reinforced concrete slab downstream of the existing HSAF. Flows from the HSAF were piped to the filter via a new pipe where tertiary poly aluminium chloride dosing is injected upstream of a static mixer and flow-paced via a flowmeter downstream.
As a consequence of the new chemical dosing, the increased sludge production required additional sludge storage. This was provided by means of a new GRP holding tank located on a disused sludge drying bed.
Time critical construction
The requirements for SWW to optimise the completed setup in good time for the national trial commencing 1/1/2016, required careful construction planning, risk mitigation and prompt decision making. Due to the lack of space and the sequential nature of the work many elements of the construction were critical.
A large proportion of the compound area was used to temporarily store the material from the PST excavation, which could only be reused once the new PST was online and the old PSTs ready for backfilling. Following on, only after the old PSTs had been backfilled could the base and alkalinity unit be installed and commissioned.
The team opted for a cast in situ system formwork PST which provided a robust reinforced concrete tank with excellent design life and installation time of just 2 weeks. Due to the small size of the PST (6.3m) the scrapers required careful design to ensure that they could be articulated around the launder channel and diffuser drum when raised. Meticulous supplier coordination was essential to facilitate the seamless transition between suppliers, adherence to programme and problem free install. Due to the critical nature of the PST operation it was brought on line with a temporary starter panel and an innovative clip on timer circuit to manage weekend de-sludging.
Downstream from the PST a new 4-way filter distribution chamber was required. For speed, efficient use of space and tolerances a GRP 1m x 1m x 0.6m was fabricated off site, with integral bell mouth, flanged connections, adjustable weirs and hinged covers all pre installed. Again careful pre-planning, design, and supplier coordination ensured a expedient right first time result.
The programme critical Hydrok-Mecana filter was also selected with a prefabricated stainless steel tank; this was simply placed on a slab and backfilled with sand minimising the on-site construction period and tolerance risks.
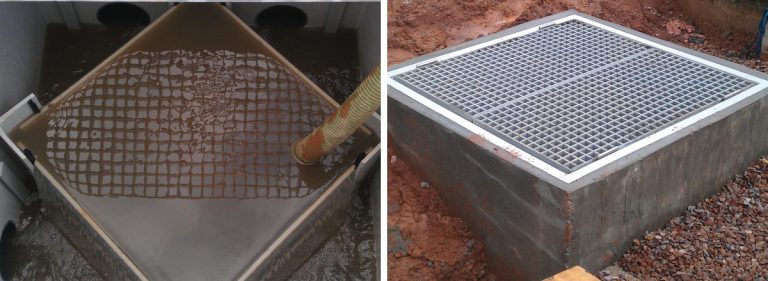
(Left) Flow splitter chamber internal and (right) Prefabricated GRP flow splitter chamber with concrete surround – Courtesy of SWW Delivery Alliance H5O
The confined nature of the site prevented turning any vehicles larger than a car; therefore the deliveries of all plant and materials warranted extremely careful planning and scheduling for both the construction activities and the integration with the general day to day STW operations, such as tankering and maintenance.
Due to the normally quiet nature of the village and the restricted site access the team also had to manage the vehicles beyond the site boundaries to ensure that the neighbours and general public were not adversely affected by vehicle movements. This was managed through tailored delivery restrictions and scheduling written into orders providing the required site control.
The construction team achieved a 100% score on Achilles audit and although not directly in the eyes of the public the team was able to achieve a Considerate Constructors score of 39.
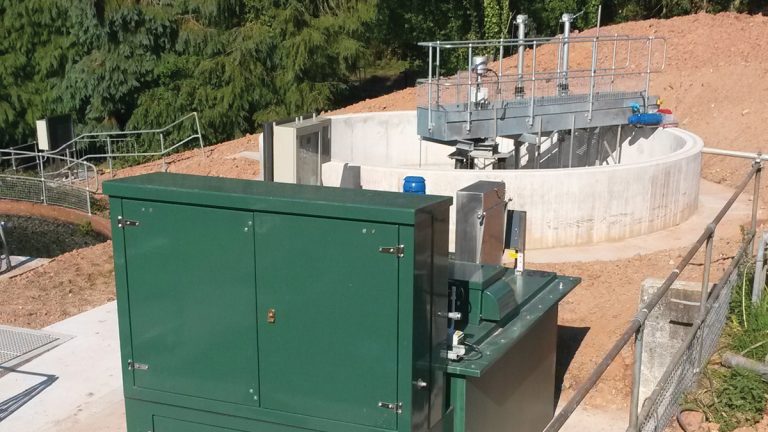
Alkalinity dosing unit on site of old PST – Courtesy of SWW Delivery Alliance H5O
Conclusion
The improvement works at North Tawton were complete and operational in time for the December 2015 deadline. Initial results from testing the final effluent show the new plant to be operating as anticipated.
SWW and their H5O delivery team would like to thank all the project stakeholders involved with this scheme. Collaboration between client, contractor, designer and the wider supply chain has been a key factor in delivering a successful project that both meet the scoped requirements and a challenging delivery programme.