Barston STW (2019)
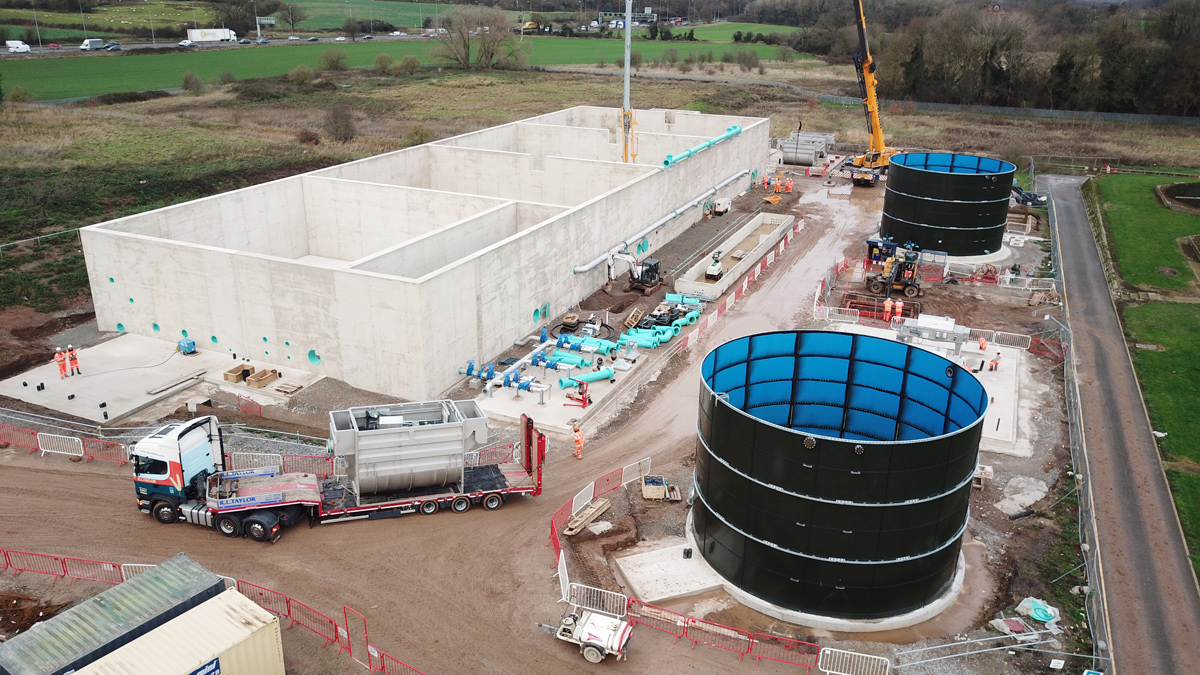
Aerial view of main process area - Courtesy of Costain
Barston Sewage Treatment Works (STW) is one of Severn Trent’s medium sized treatment works. The site is located to the east of Birmingham in the West Midlands. The STW treats foul water for the catchment serving Solihull, Shirley, Knowle and other outlying conurbations. It currently serves a population of 39,741 which will increase to 76,036. Increased flows are to be directed to Barston STW that would have otherwise gone to Coleshill STW. This releases treatment capacity at Coleshill for a significant development near the Birmingham Airport. The works discharges to the SSSI of the River Blythe, with Whitacre Water Treatment Works (WTW) abstracting not far downstream. CiM6, a design and construct partnership between Costain and Stantec UK Limited is undertaking the design, construction and commissioning of the new works as part of the STWL AMP6 South Non-infrastructure Design and Construct framework.
The existing works
Sewage treatment has been undertaken at Barston since at least the 1950s. The works has undergone expansion and upgrades since then. The current works includes, inlet screw pumping station lifting to an inlet works comprising 1D screens, detritor grit removal and flow control/storm separation, followed by 3 (No.) primary settlement tanks (PSTs), 16 (No.) percolating filters, 4 (No.) humus tanks, nSAF, sand filters and iron and lime dosing. Storm retention and grass plots are also provided.
Drivers for the project
The current consent of 10 (BOD), 25 (SS), 3 (NH4), 1 (P), 4 (Fe) will be tightened to 10 (BOD), 25 (SS), 1 (NH4), 0.2 (P), 2.5 (Fe) in 2020 as a result of Water Framework Directive, Quality and CRoW Act drivers.
Additionally, the works flow to full treatment (FFT) will be increasing from 262 l/s to 395 l/s. As a result of the tightening consent and the increased flow rate, a new facility is required. CiM6 is replacing all the existing site processes except for the storm tanks and storm grass plots.
The new treatment processes will comprise a crude Nereda® process (granular activated sludge) followed by Mecana (cloth filter technology). The new works will also include a new inlet pumping station, new 6mm 2D screens, grit removal which will pre-treat the crude effluent ahead of the Nereda® process.
On completion of this project, Severn Trent will be able to claim four Outcome Delivery Incentives (ODI) points by March 2020.
This will be one of the first three Severn Trent sites to receive secondary treatment using Nereda® technology by the ASP Batch, a collaboration between CiM6, MMB, nmcn PLC and Severn Trent.
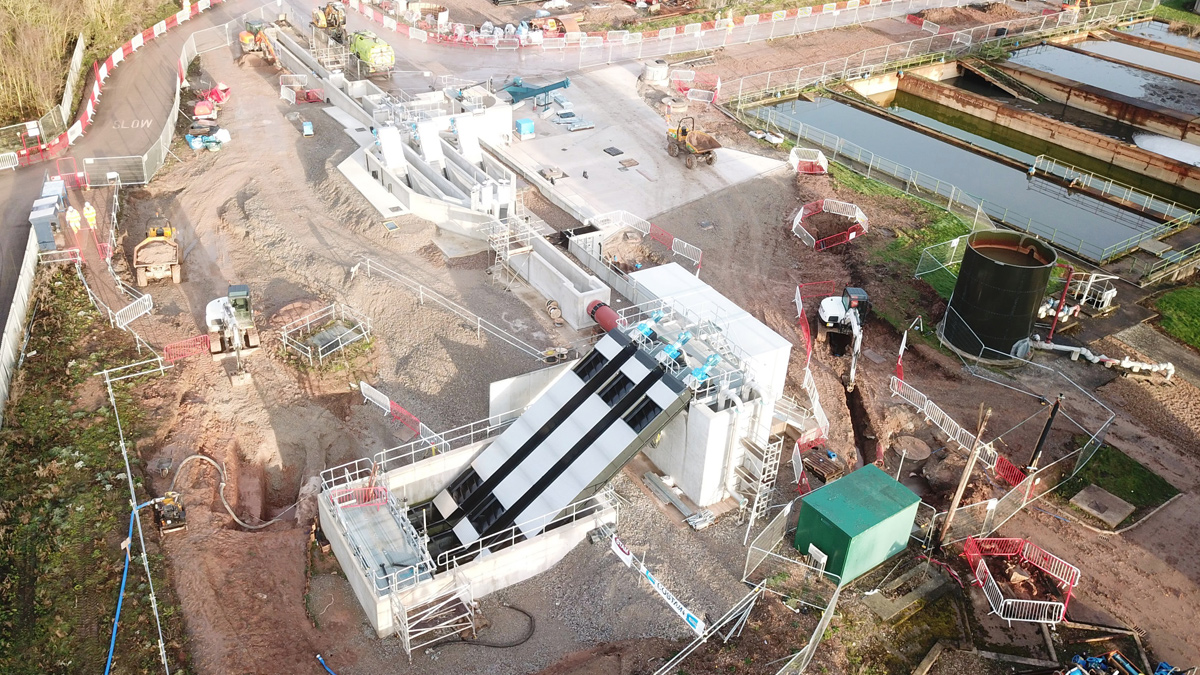
Aerial view of new screw pump station and inlet works under construction – Courtesy of Costain
Design
Detailed design for the project has been completed by CiM6’s design partner, Stantec UK Limited. Detailed design included process, civil, mechanical, electrical and geotechnical design. Additional process design has been provided by Royal HaskoningDHV (RHDHV) who provide the Nereda® technology and Eliquo Hydrok Ltd who provide the Mecana process.
A comprehensive 3D model utilising Bentley CAD software has been used throughout to generate the construction drawings but also to facilitate collaborative design development. Sub-supplier models have also been successfully integrated into the overall model further enhancing the design development process. Occulus Rift Virtual Reality utilising the 3D model has been used to facilitate Access Lifting and Maintenance reviews with the STWL operational staff.
Additionally, drone surveys, Spherevision 360° video system and point cloud surveys have been utilised to enable more efficient and safe design.
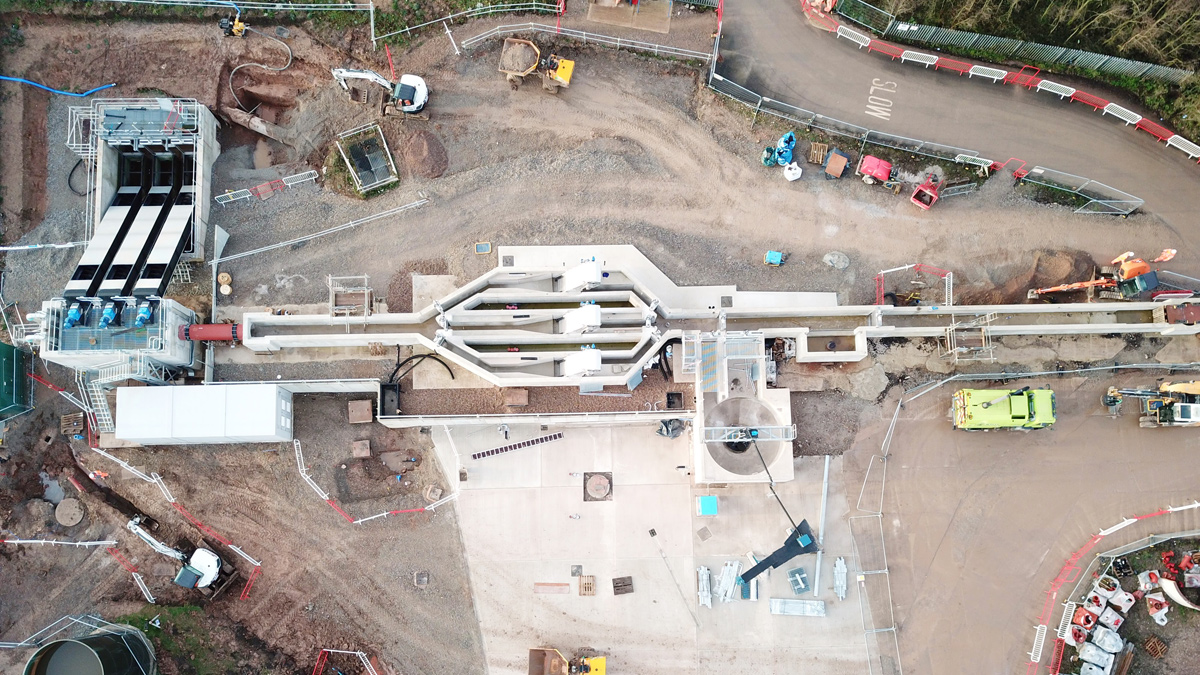
Aerial view of new inlet works under construction – Courtesy of Costain
New works
Most of the new works has been constructed off line, with only minor interfaces for connections to the incoming sewers and outfall. The new processes are compact, which enabled the new works to be constructed in an area a fraction of the existing works which has assisted in dealing with the constraints of the existing processes and poor ground conditions.
Inlet works: The maximum flow received by the works will be increased from 432 l/s to 600 l/s. A replacement screw pump station has been constructed complete with 3 (No.) 1200mm diameter compact style variable speed screw pumps. This lifts flow to a new elevated cast in situ inlet works. The inlet works is constructed upon a new embankment.
An effective inlet works, as with most sewage treatment works, is essential for optimal Nereda® technology operation. The inlet works has been designed to meet the Nereda® technology requirements and comprises 3 (No.) 1.3m wide 2D 6mm screens without an unscreened bypass. The screens operate as duty/assist/standby complete with 2 (No.) screenings handling units, the screens are followed by a single vortex grit plant with grit classifier, 3PG storm separation and MCERTS flow measurement flume.
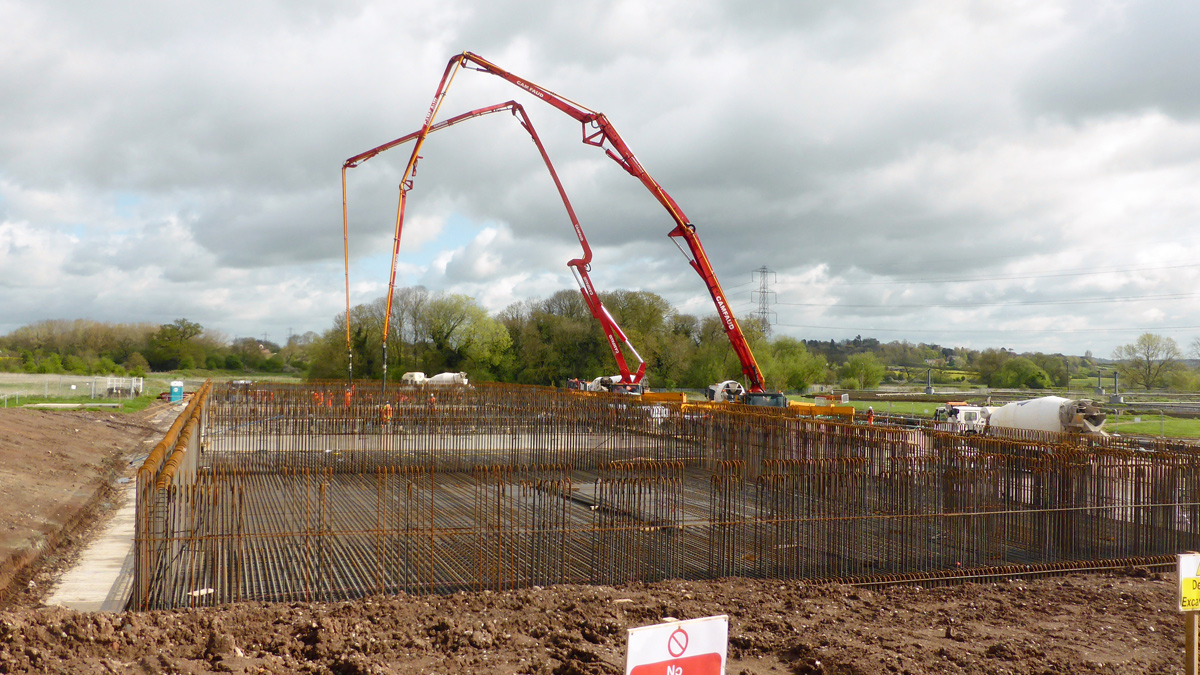
Nereda® reactor base pour – Courtesy of Stantec UK Limited
A purpose designed drop shaft exits the inlet works to mitigate against potential air gulping in the downstream pipeline triggered by variable water levels on the downstream Nereda® inlet buffer tank.
Due to space restrictions on site, the new inlet works is separated from the main treatment area. A gravity Weholite® pipeline runs for approximately 180m from the inlet works to the Nereda® influent buffer tank. Sampling of the incoming sewage determined at an early stage that removal of fats, oil and grease (FOG) was not required, with values below 90 mg/l being a requirement of the Nereda® process.
Secondary treatment process: The Nereda® granular activated treatment process is being utilised for the secondary treatment. Nereda® is a wastewater treatment technology invented by Delft University of Technology in the Netherlands and developed in conjunction with the Dutch Foundation for Applied Water Research (STOWA), the Dutch Water Authorities and Royal HaskoningDHV. The process purifies water using the unique features of aerobic granular biomass.
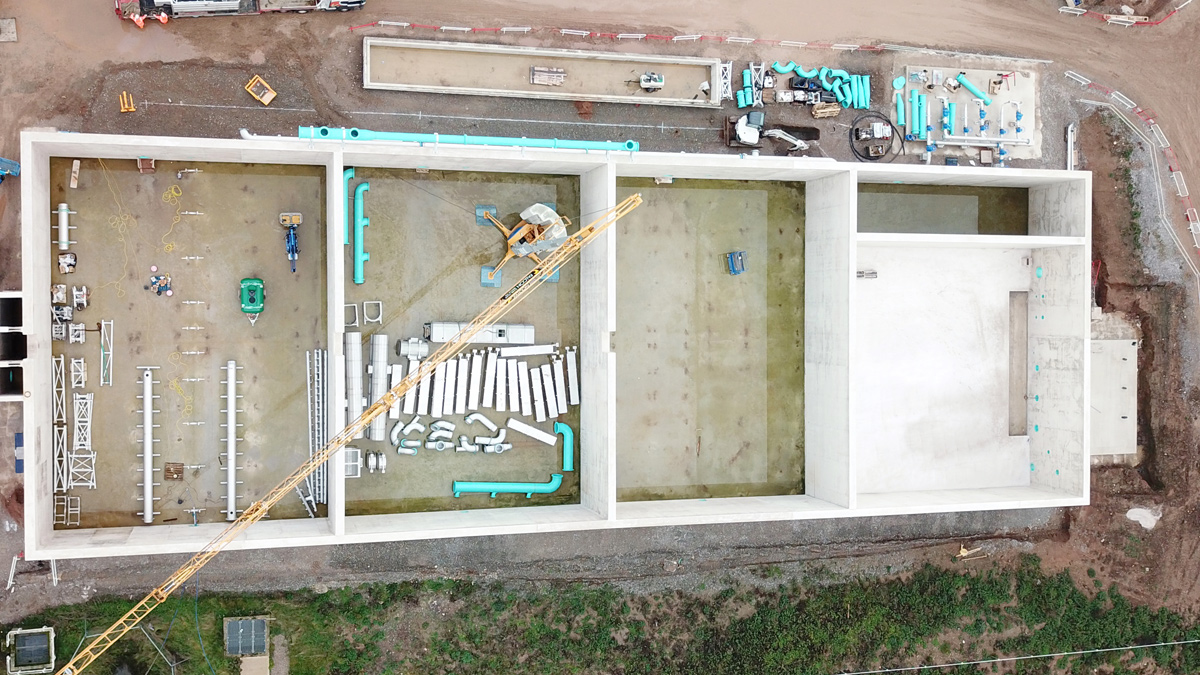
Aerial view of Nereda® reactor – Courtesy of Costain
It is a batch process, but unlike conventional sequencing batch reactors, does not require a separate time consuming decant phase due to the excellent settlement characteristics of the granular biomass.
The Nereda® plant at Barston comprises a 7.4m deep x 76.7m long x 26.2m wide cast in situ concrete tank. This contains a 19.7m x 19.8m influent buffer pumping station, 3 (No.) 25m x 18m reactors complete with stainless steel central outlet channel and a 19.7m x 4.5m sludge buffer pumping station.
A cost benefit analysis between prefabricated concrete, post tensioned or cast in situ indicated that a cast in situ solution was the most cost efficient. The reinforced concrete base and walls are all 600mm thick. Early collaboration with the concrete supplier, enabled testing of their limestone aggregate for its coefficient of thermal expansion. This resulted in a more efficient reinforcement design saving approximately 10% over conventional aggregate.
Additionally, to mitigate hazards associated with collapsing of tall reinforcement cages, a kingpost system was utilised to which the reinforcement was attached resulting in significantly less temporary works intervention. The tank was constructed by STAM Construction Ltd with most notably, an 870m3 base pour being undertaken in one continuous pour. The tank is now being fitted out with the required internal and external pipework and equipment by Suprafilt.
Due to process requirements, control valves on the Nereda® process are to close in no longer than one minute. The process pipeline sizes dictated the use of fast acting pneumatic actuated valves over electrically actuated valves. It was therefore decided to make all valves on the Nereda® process pneumatic actuated. Surge analysis was also undertaken on the feed and sludge pipework, the concrete tank and pipework and supports design have taken this into account.
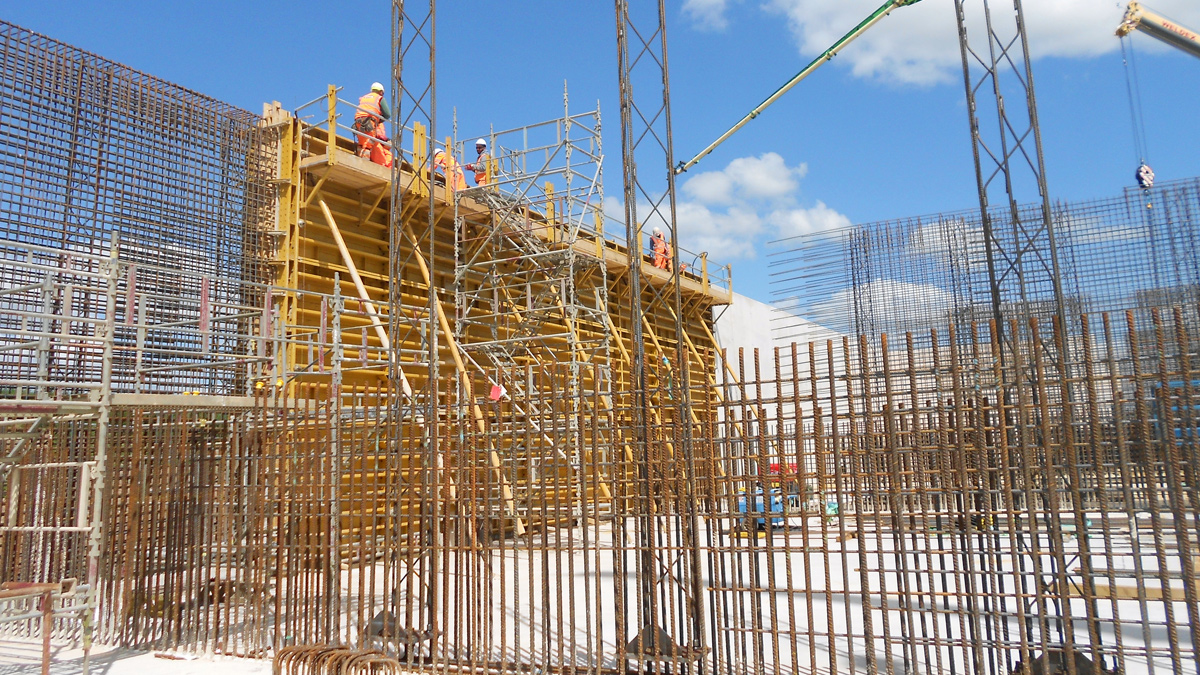
King posts used for Nereda® reactor construction – Courtesy of Stantec UK Limited
Tertiary solids removal: Due to the tight P and Iron consent, an iron dosed tertiary solids removal plant has also been included. This is being provided in the form of a two-stage Mecana cloth filtration system designed and provided by Eliquo Hydrok Ltd. The system comprises duty/standby static mixers for the Iron dosing, 2 (No.) flocculation tanks, 2 (No.) SF18-90 first stage followed by 3 (No.) SF12-60 second stage Mecana cloth filters.
The units come pre-fabricated and are assembled on a concrete support slab followed by pipework installation, after which an overhead travelling gantry will be installed to facilitate future cleaning and maintenance activities. In the event of individual unit maintenance activities or failure, a proportion of flow will be bypassed around the TSR. The flows will be automatically regulated by a distribution chamber comprising variable width side opening penstocks included within the Nereda® process tank construction.
The chemical dosing to the static mixers, controlled by either flow pacing or feed forward control on P monitors, is being provided by Colloide. This comprises a template design 30m3 concrete bunded storage tank and 3 (No.) pump dosing cabinet.
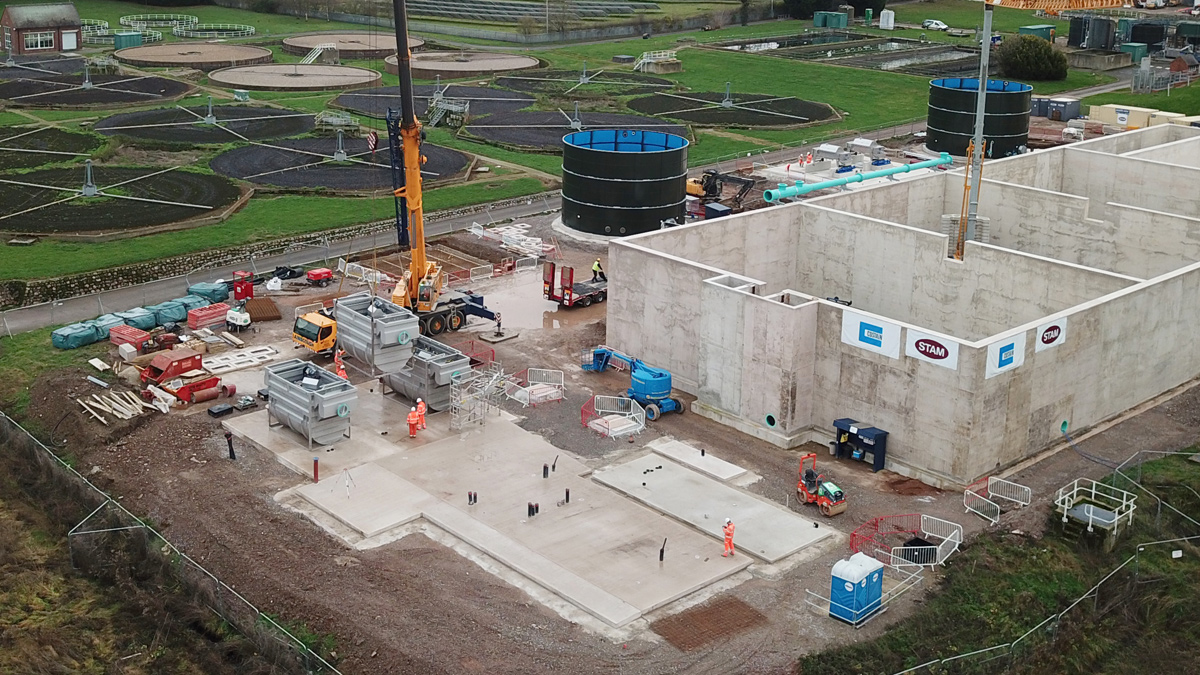
Aerial view of main treatment area showing second stage Mecana units being installed – Courtesy of Costain
Sludge management: The Barston STW site currently includes sludge digestion. STWL’s sludge strategy has included the construction of a thermal hydrolysis plant at the nearby Minworth STW which included for the closure of the digestion facility at Barston in cognisance of the capital works planned.
The only sludge generated as part of the new process requiring treatment for transport off site is that of the Nereda® surplus sludge. A thickening process has been included to enable tanker removal comprising a pre-thickening balancing tank, 2 (No.) BT100 Alfa Laval gravity belt thickeners (GBTs) and thickened storage tank. The GBTs will be enclosed in a GRP building complete with overhead travelling gantry.
Both epoxy coated steel storage tanks are 548m3 in volume, the tanks and bases were designed and installed by Balmoral Tanks. The pre-thickening tank includes air mixing providing the dual purpose of ensuring the contents are fully mixed but also aerated to stop P release in the event of anaerobic conditions.
A prefabricated polymer dosing plant has also been provided, designed, constructed and installed by Northern Pump Suppliers (NPS Engineering Group).
Miscellaneous items of note: The Nereda® process is a batch process. In times of low flow to the works there could be periods of time in which no flow is discharged from the treatment process. There was the potential to starve the washwater system for periods of up to 80 minutes. Based on the likely works washwater demand, a storage tank some 6m in diameter and 6m deep would be required to service this washwater requirement. However, this requirement was eliminated by careful design of the new outfall pipe, in effect turning the outfall pipe into the storage tank.
Return flows to the Nereda® process comprise TSR sludges and GBT filtrate. These required balancing. This has been achieved by careful design of the Liquor return pump station, finding an optimal compromise between sump volume and pump flow rate that is satisfactory to the Nereda® process.
Barston STW: Key participants
- Design & delivery contractor: CiM6
- Overall project design: Stantec UK (CiM6)
- Civil construction: Costain (CiM6)
- Design of Nereda process: Royal Haskoning DHV
- FRC Construction: STAM Construction Ltd
- Nereda internals/externals: Suprafilt
- Chemical dosing equipment: Colloide
- Polymer dosing equipment: Northen Pump Suppliers
- Safety showers & eyebaths: Aqua Safety Showers International Ltd
- MCC panel: CEMA
- MCC panel: Boultings Group
- Electrical installation: Lloyd Morris Electrical Ltd
- Mechanical installation: Servomac
- Mechanical installation: Balmoral Tanks
- Mecana disk filters: Eliquo Hydrok Ltd
- Gravity belt thickeners: Alfa Laval Ltd
- Pumps: Grundfos Pumps Ltd
- Storage tanks: Balmoral Tanks Ltd
- Inlet screens/screenings handling: M and N Electrical and Mechanical Services
- Inlet works grit removal: Jacopa Ltd
- Inlet works screw pumps: Spaans Babcock Ltd
- Penstocks: Industrial Penstocks Ltd
- Sampling Instrumentation: Hach Lange
- Metalwork: Hilton Industrial Services (Midlands) Ltd
Commissioning
Given the constraints of the existing sites process and the increase in flowrate, the commissioning is due to begin in September 2019 in four phases.
- Phase one, at current works flow, will involve commissioning and putting into service the new screw pump station and Inlet works. All the flows will then be diverted into the existing inlet works.
- Phase two, at current flows, the Nereda® process will be commissioned. All flows will be over-pumped from the washwater sump to the existing PSTs.
- Phase three, at current flows, the TSR system will be commissioned without Iron dosing. Only once the new processes are treating to the current works consent will phase four begin.
- Phase four, the flow will be diverted from the new plant to the outfall with the existing plant being abandoned. The Iron dosing system will be commissioned and the flow to the process stream gradually increased up to the future FFT.
For phase 4 to happen, a change in the way flows are distributed within the Solihull and Shirley catchment will also be required.
Currently, flows from the Solihull and Shirley catchment are split equally between Barston STW and Coleshill STW using a flow splitter gate. In future, up to 360 l/s will go directly to Barston STW, after which the flow will be capped and excess flows will then either pass to Coleshill STW or an upstream combined sewer overflow (CSO). The flow splitter gate in the catchment will be replaced by a simple weir.
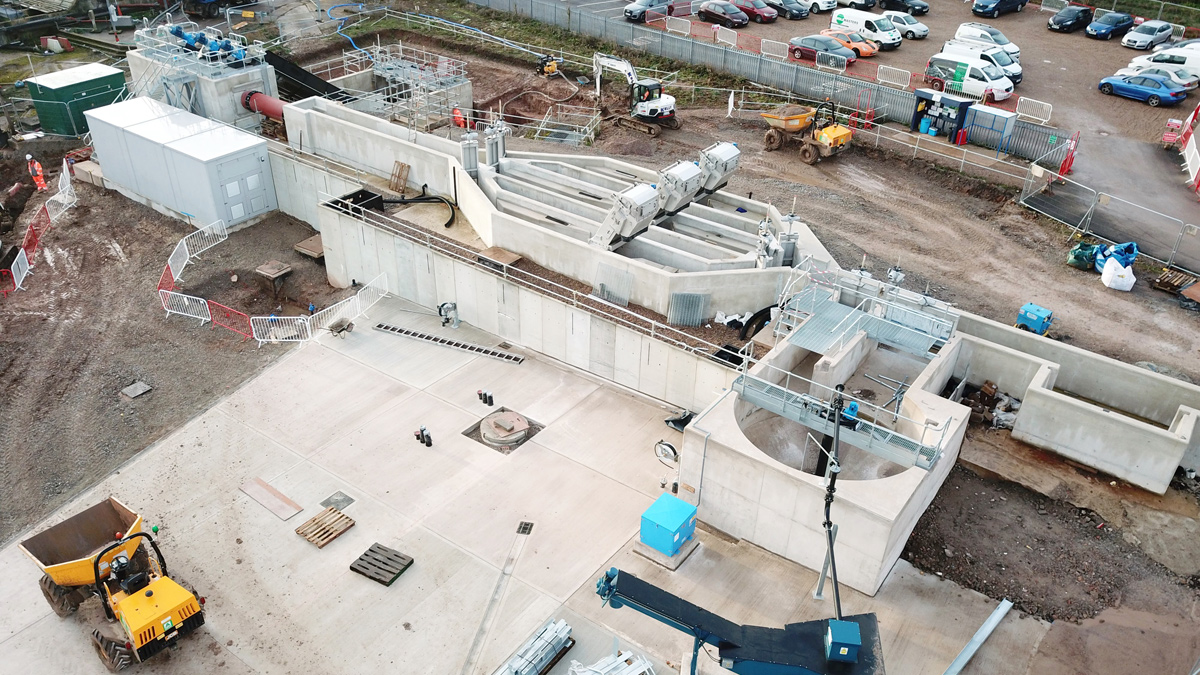
Aerial view of grit removal plant – Courtesy of Costain
Conclusion
At the time of writing the paper (May 2019), construction is well advanced with finishing of the metalwork, above ground pipework and electrical installation to follow in the following months. With completion and handover of the new works scheduled for February 2020, the new treatment facility being capable of treating STWL’s tightest STW consent.