Poolend & Highgate pH Correction & Plumbosolvency (2017)
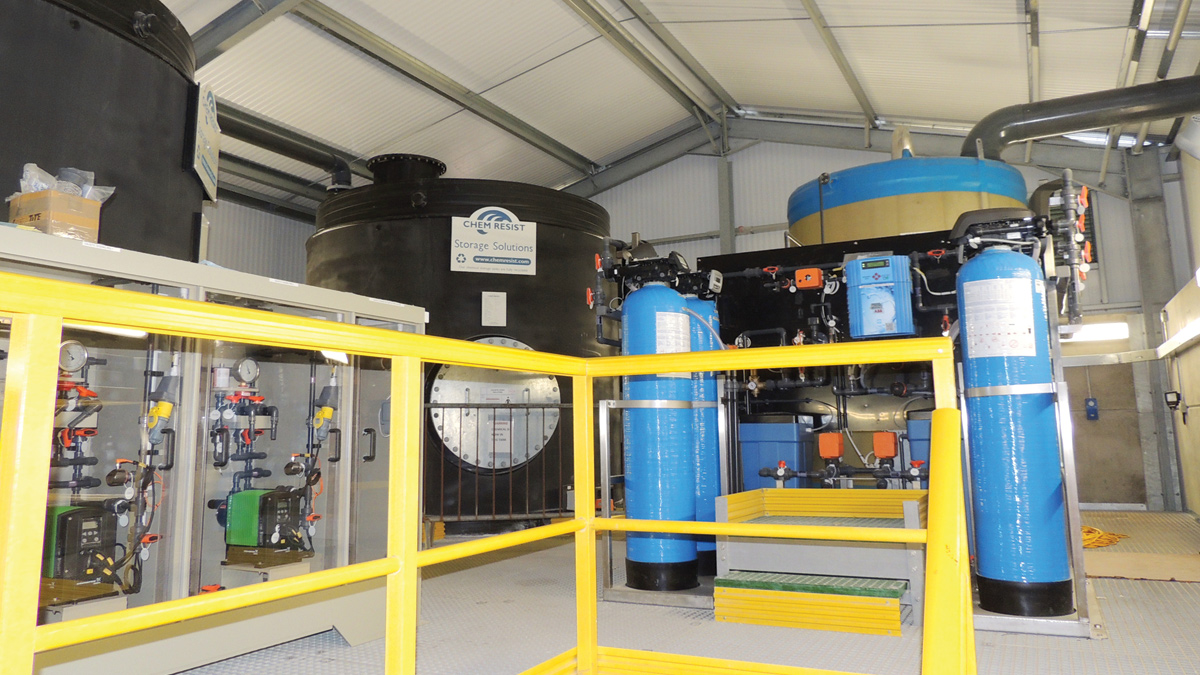
New dosing installations - Courtesy of MMB
The £2.25m Poolend and Highate pH Correction and Plumbosolvency Scheme required the design and construction of a 20Ml/d treatment plant. Poolend BPS is located near Leek in Staffordshire. Water from Poolend and Highgate is blended with water from other sources and supplies thousands of properties across Staffordshire. The successful completion of the scheme by design and build contractor Mott MacDonald Bentley (MMB) on behalf of Severn Trent Water (STW), ensured Poolend remains a robust water treatment site and leaves a lasting legacy of high quality water to service the needs of people in Staffordshire.
The challenge
The drinking water safety plans for Poolend and Highgate identified a deteriorating trend for pH and lead, and an elevated risk of bacteriological issues, making the project a high priority for STW. In light of this, in the summer of 2014, the Drinking Water Inspectorate (DWI) and STW brought forward completion of the project from June 2018 to June 2016. This reduced the anticipated duration of the programme by 50% and gave 18 months to deliver the project.
To add to the challenging programme, Poolend is located in the ‘green belt’ and also designated as a Special Landscape Area, meaning it required early environmental consultations and planning permission to extend the water treatment site area and to construct the new process.
The solution
In order to achieve a successful outcome an innovative delivery model was deployed by STW. MMB was involved from the offset to value engineer the project and avoid a circular or protracted design phase. A collaborative team, empowered to make decisions was brought together to ensure fast paced delivery. Three main efficiency levers were applied namely:
- Collaborative planning.
- Lean processes.
- Off-site manufacturing.
The proposed solution was to rationalise the sites at Poolend and Highgate into one, by provision of common:
- Sodium hydroxide dosing.
- Sodium hypochlorite dosing.
- Water softener plant for carrier water system.
- Orthophosphoric acid dosing.
- Utilisation of existing UV disinfection at Poolend.
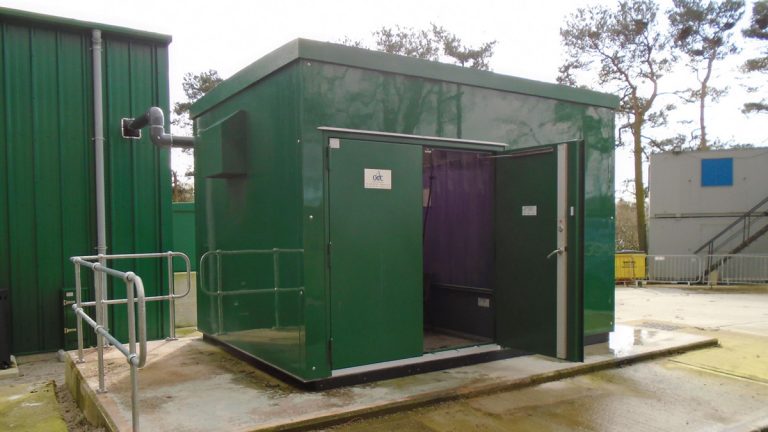
New PO4 dosing kiosk – Courtesy of MMB
The works at Poolend involved significant network reconfiguration, converting Highgate WTW into a raw water supply which is pumped to Poolend site for pH correction, disinfection, plumbosolvency and UV treatment.
Through careful design and rigorous challenge, the team was able to reuse the existing main between Poolend and Highgate to allow flow going back into area, previously supplied by Highgate. Carbon footprint calculations indicated a 40% saving on embodied carbon, £300,000 on a 1.8km 180mm pipe, and four months on the programme by reusing the main and by avoiding the installation of the new main. The delivery team performed a pressure monitoring on the existing main to ensure that customers continue to receive ample pressure in all demand scenarios.
Combination of Poolend and Highgate to a common treatment
Highgate is located approximately 1.3km to the north of Poolend. In order to provide a common treatment for both Highgate and Poolend borehole sources, the existing main from Highgate to Ladderedge had to be diverted into the Poolend treatment system, effectively rendering it a raw water source. Part of the treated water is returned to the booster station at Highgate, which feeds Heaton distribution service reservoir (DSR).
The Highate flow was connected into Poolend upstream of the existing UV plant, which had been installed at Poolend as part of a separate project. Although the UV plant was sized for the combined flow, the pipework between where the flows merge, and the UV inlet and also the outlet pipework had to be upsized to accommodate the combined flow.
The new treatment processes provided by MMB (see process diagram below) includes caustic dosing for pH correction, sodium hypochlorite dosing for marginal chlorination, and phosphoric acid dosing for plumbosolvency control. All chemicals are injected into a new static mixer installed dowsntream of the UV plant, meaning that the old UV plant, chlorine dosing plant and phosphoric dosing plant at Highgate are no longer required.
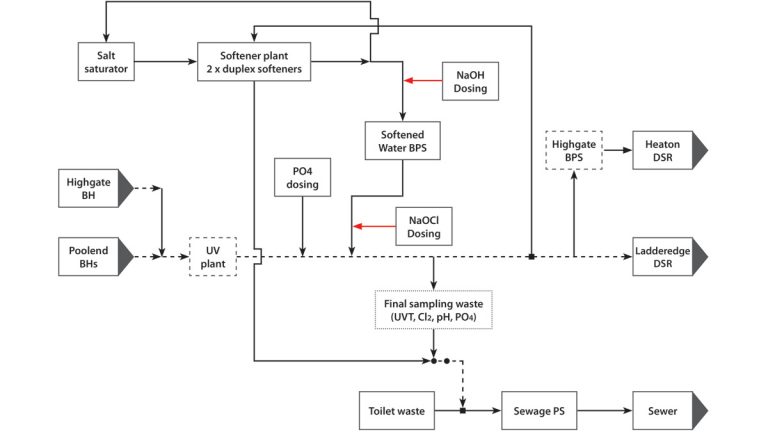
Poolend – Highgate process flow diagram – Courtesy of MMB
Chemical dosing
All new chemical dosing systems were designed for the combined flow from Poolend and Highgate.
The method selected for pH correction was dosing of sodium hydroxide at 50% concentration. The dosing control is flow proportional with trim to a target pH. The new sodium hydroxide plant includes two bulk storage tanks designed for 25 tonne chemical delivery, dosing cabinet and control panel.
The new sodium hypochlorite plant also contains two fully bunded bulk storage tanks, dosing cabinet and new control panel delivered to site as a pre-assembled package plant. The dosing control is flow proportional with residual trim.
A new orthophosphoric acid dosing plant was installed at Poolend to deliver a stable dose in the range 0.5-1.5 mg-P•L-1. The plant includes a bulk storage tank in a bund, dosing cabinet and control panel and it was delivered as a pre-assembled package plant in a security rated kiosk.
Carrier water
Carrier water is required for sodium hydroxide and sodium hypochlorite dosing. The carrier water needs to be softened to eliminate any risk of scaling in the dosing lines and injection lances. A salt saturator and duty/standby duplex softeners based on ion exchange were installed at Poolend.
The softened water pressure was boosted by new carrier water pumps before dosing back into the process main. As the carrier water is required for both sodium hydroxide and sodium hypochlorite dosing, the same system was used for the both chemicals. Following detailed chemical modelling, an additional saving was made by using common dosing lines and common withdrawable dosing lances.
Waste
The softening system produces a waste stream therefore a new wet well and sewage pumping station were installed on site to remove this waste, and a new 1.2km foul rising main was laid and was connected in to a local sewer. This main is now taking the softener, sampling waste together with domestic foul sewage.
Process building
New sodium hydroxide dosing, sodium hypochlorite rig, softener carrier water system and the new control panels were installed in a new security-rated steel framed building at Poolend. Construction of a new building involved expanding beyond the existing developed site boundaries (although still on STW owned land). This ground was previously falling away steeply from the developed site so major earthworks were undertaken to provide a level platform for the new building, tanker delivery area, tanker access road and turning area. Earth retaining structures were constructed where there was insufficient space to batter back the slope to a safe angle within the site boundaries.
The new phophoric dosing system was installed in a secure GRP kiosk in the location of the previous kiosk.
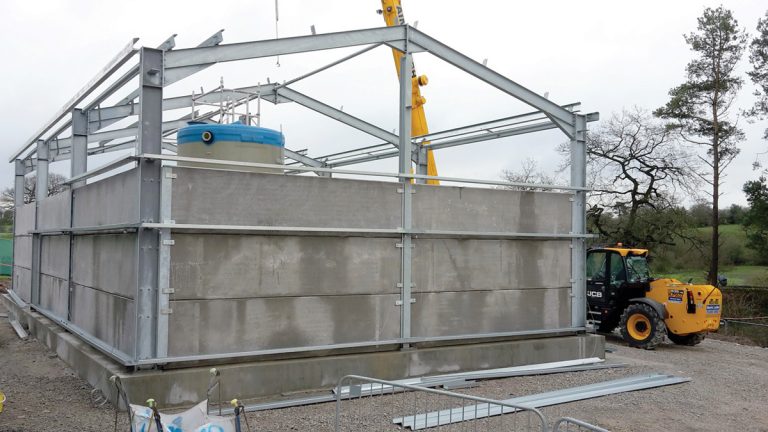
New steel clad building during construction – Courtesy of MMB
Delivery area
New fill point cabinets for sodium hypochlorite, sodium hydroxide and phosphoric acid were installed in a new common chemical delivery area, which includes two 3-way valves with interlock system and two interceptor tanks for separate chemicals, as well as new safety shower with head tank and eye bath.
The outcome
The Poolend Delivery team (MMB, Asset Creation, Operations and NCAM) excelled in delivering the DWI obligation on time, through hard work, strong collaboration and great commitment, embracing a strong ‘One Severn Trent’ ethos.
Using collaborative planning from feasibility to commissioning, the team delivered the programme of works in half the time of similar sized schemes in AMP5, taking just 14 months from design to completion. Work started in October 2015 with a clear milestone of completing earthworks (4,500 tonnes of soil shifted) and the raft slab by Christmas.
The steel-clad treatment building was started in January and ready for fit out in six weeks. This left just four and a half months to install and commission the disinfection, sodium hydroxide and softener plants and to reconfigure the network and the existing UV plant. Factory-build assembly significantly reduced the amount of time spent on installation of the dosing plants. In parallel the waste main using directional drilling was built in three weeks. The interconnecting pipework required six separate network interventions which were planned and executed flawlessly.
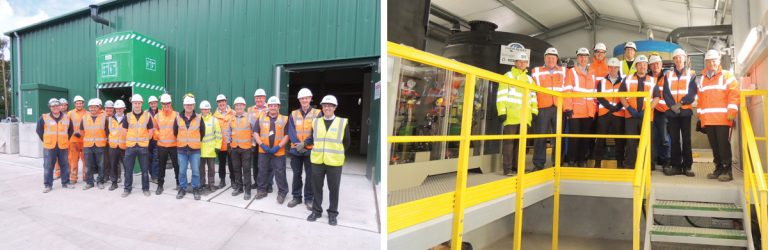
The collaborative delivery team – Courtesy of MMB
From start to finish, the Poolend delivery team has shown massive commitment to the collective goal of achieving the DWI obligation, which was met with time to spare.
The excellent health and safety culture of the site delivery team saw the completion of construction without lost time incidents or serious near misses. The team has reported 970 positive interventions per 100,000 worked hours, which demonstrates their great engagement and a lead measure of performance.
This successfully delivered project ensures that customers in Staffordshire will continue to be provided with a high quality supply of water.