Uttoxeter STW (2019)
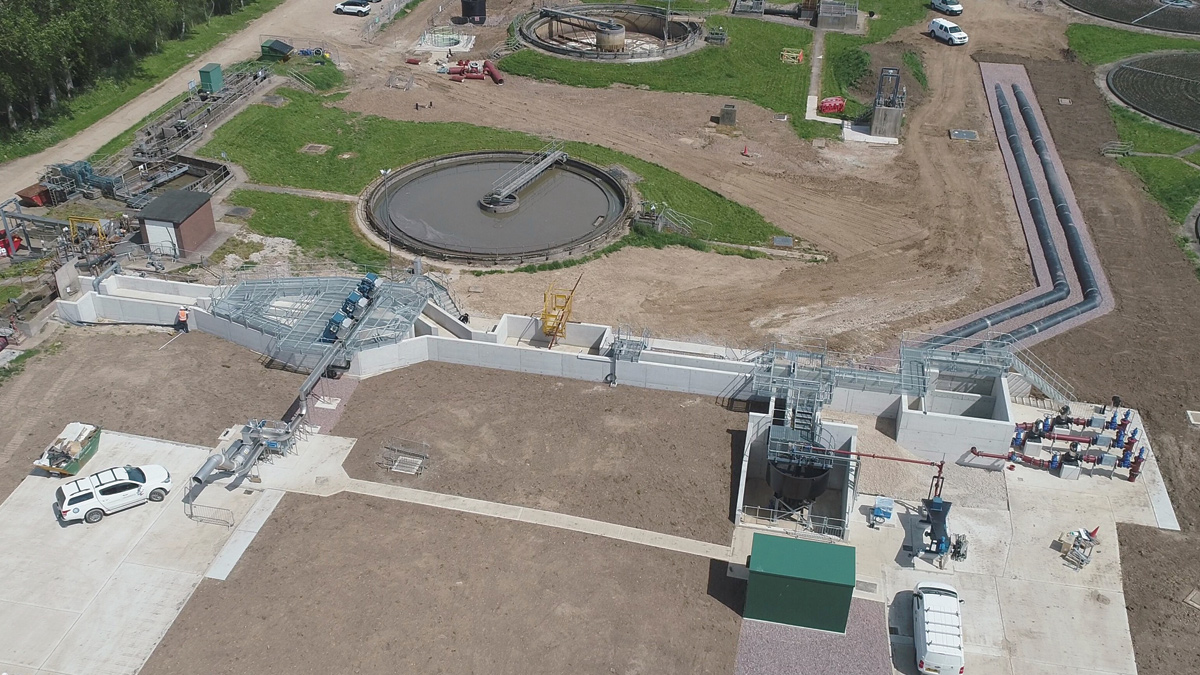
New inlet works under construction - Courtesy of Hollywood Civil Engineering Ltd
Situated in Staffordshire, close to the Derbyshire border, Uttoxeter STW serves a mainly domestic population from the town itself. Following catchment modelling, it was determined that there will be significant growth in the population, reaching 24,498 population equivalent in 2035. This increased population would mean that the existing inlet works would not have sufficient capacity as the population expanded. There has been a sewage treatment works in this location since the 1960s with the fully pumped inflow receiving conventional treatment of through preliminary processes, primary settlement, secondary filtration, secondary settlement and tertiary filtration. Severn Trent promoted the major process enhancement project as part of the AMP6 programme and appointed MWH Treatment (MWHT) to undertake the solution, detailed design, and construction of the new assets.
Key project deliverables
The key enhancement is the installation of a new preliminary treatment stream which includes 3 (No.) 6mm 2D screens and grit removal with a capacity to accept up to 711 l/s, the ability to control a flow to full treatment (FFT) of 213 l/s and to pass flows of 498 l/s from the inlet to the storm tanks.
Other capital maintenance work included the removal of inter-stage screens, improved distribution to the 3 (No.) primary tanks, refurbishment of the primary de-sludge pumps, improved filter recirculation system wetting rate, tertiary solids removal maintenance and renewal of a number of control panels across the site.
Project initiation and design
It is essential that supply chain information is available early in the design development process and the positive step to involve all the stakeholders at the earliest point in delivery was taken. This early engagement gave the additional opportunity to augment and mould the design and delivery strategy incorporating their innovative ideas. During collaborative planning sessions, every new asset was evaluated for off-site build and modularisation, wherever it was cost effective, thus avoiding conventional construction mind-sets.
The team adopted a Visual Project Initiation approach, undertaking both a full digital survey of the site and utilised a drone to take aerial images. This data, augmented with supplier’s information, was used to produce a federated model in Autodesk BIM360 Glue.
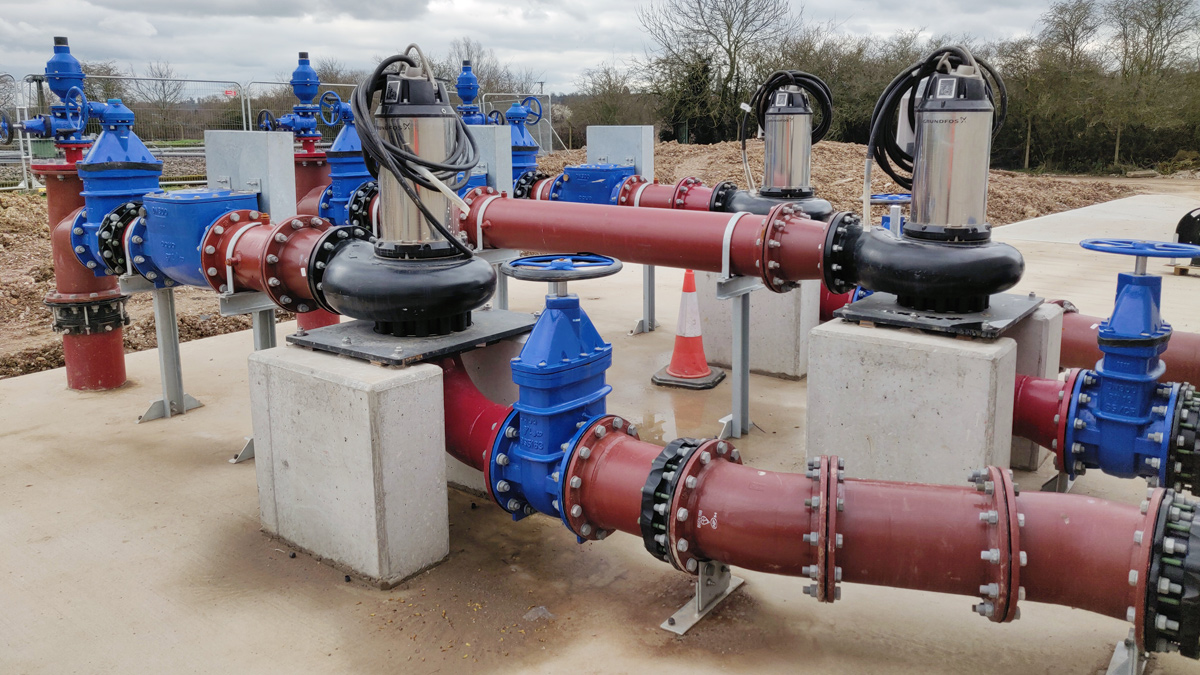
FFT pumping station during construction – Courtesy of MWH Treatment
The existing pumped inlet system had insufficient available head to accommodate the 2D screening at the required flow and allow gravity distribution to primary treatment. MWHT designers worked closely with the Severn Trent Process Design Engineering (PDE) team to develop an option to screen all flows and, with insufficient head for the gravity flow to primary treatment, provide FFT pumping. This was a lower TOTEX solution than pumping all flows and the storm solution avoided both storm screening and additional storm pumping.
The low lift pumping station at the elevated inlet presented an opportunity to place these pumps above ground. This removed the need for working at height and enabled easy access for future operation and maintenance of the pumps.
Uttoxeter STW: Supply chain – key participants
- Client: Severn Trent
- Main design & build contractor: MWH Treatment
- Civils subcontractor: Hollywood Civil Engineering
- Mechanical installation: Watermark
- Electrical installation: Southern and Redfern
- Screening plant: Longwood Engineering
- Grit removal plant: Jacopa
- Storm pipework, DfMA chamber: SDS Limited
- MCC: Total Automation & Power
- Structural steelwork: Galliford Try
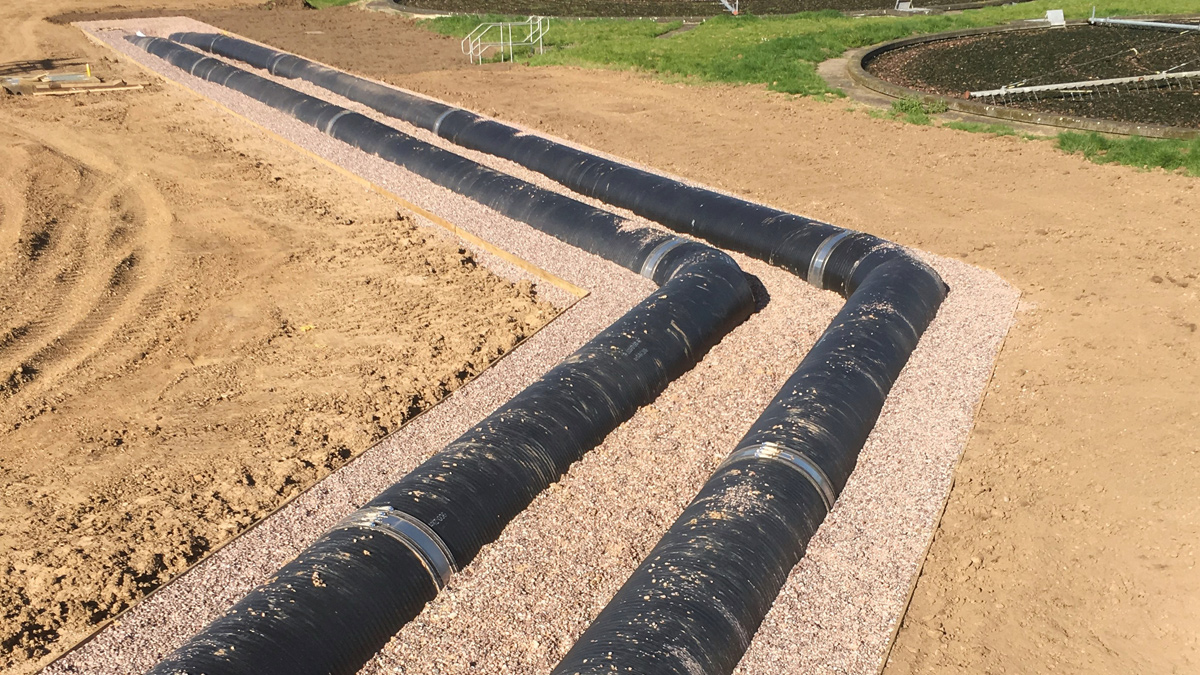
Twin 900 mm diameter storm pipework – Courtesy of MWH Treatment
Storm transfer
New storm flow transfer to storm tanks was achieved via partially buried twin 900mm pipes. The pipe route crossed many known services and the shallower excavation reduced the risks associated and the potential clashes with, or damage to, existing pipes and services and was time and cost efficient.
DfMA
Although the possibility of off-site manufacture was extensively explored at Uttoxeter, the only beneficial application identified was the creation of the primary distribution chamber made of Weholite® from SDS Limited.
The preformed chamber is a safer solution as excavations are open for shorter times and reduces the number of lifting operations necessary over traditional in situ base and precast section construction.
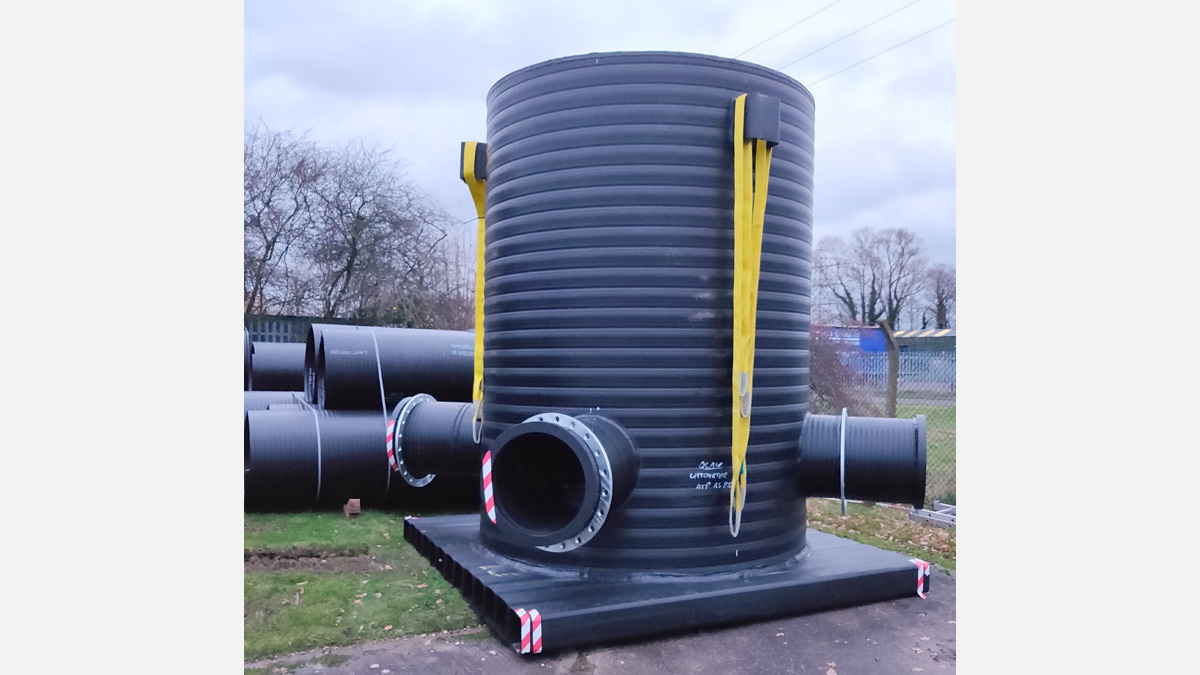
DfMA distribution chamber – Courtesy of MWH Treatment
Digital induction
It was essential that every worker on site receives a comprehensive induction to the site, project activities, systems, behaviours required and that their competency to undertake an activity was verified. The team have used an electronic induction system which splits induction into pre and post entry phases.
Prior to arrival, workers and visitors access a portal and are presented with specific information about the access to the site and generic issues such as business systems and approaches to health, safety, wellbeing, environment and quality. Data is collected from the visitor on skills and competencies and stored in a GDPR compliant repository.
The digital information collected at the initiation of the project was reused in the induction, to enable understanding of preferred access routes and have a good understanding of the restrictions before setting off for site.
The split induction allows the site management team to focus on the key site-specific dynamic issues, improving risk understanding and engagement, enabling people to start work more promptly and avoiding the data protection issues that storing completed inductions on-site presents.
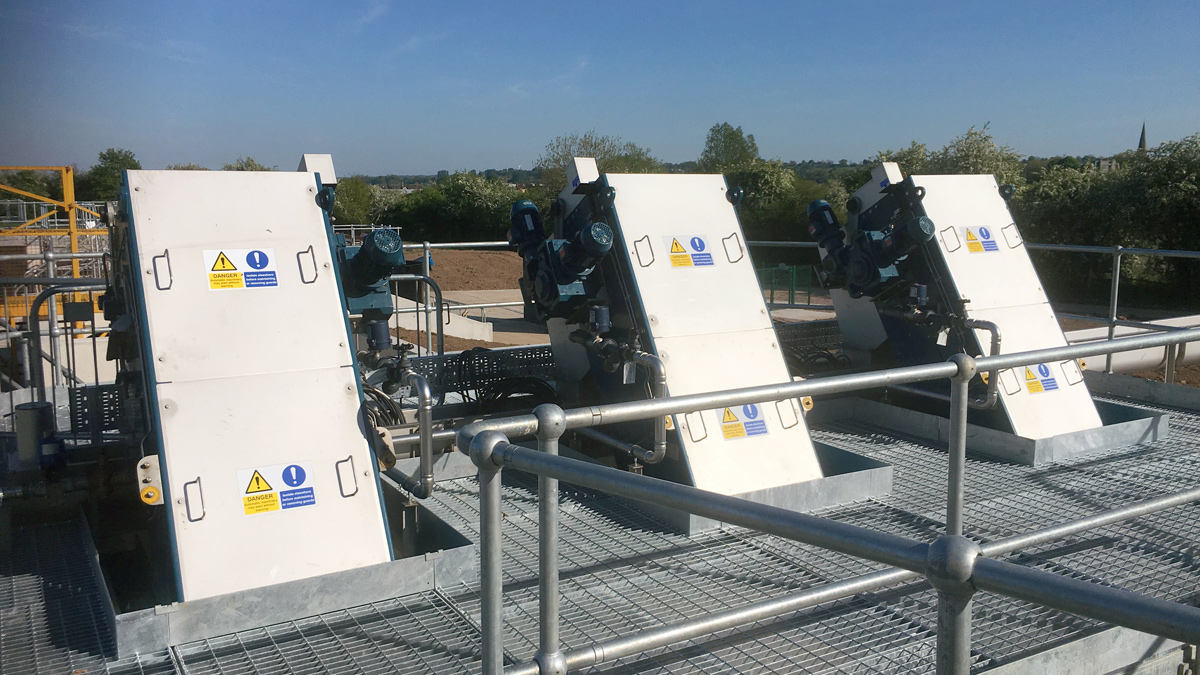
Inlet screen installation – Courtesy of MWH Treatment
Conclusion/summary
From project initiation, with the client and contractor developing the lowest TOTEX solution, to adoption and development of the digital delivery model with the supply chain, it is the collaborative ethos throughout the team that has enabled the successful delivery of this project.