Bluewater Bio
FilterClear® (2024)
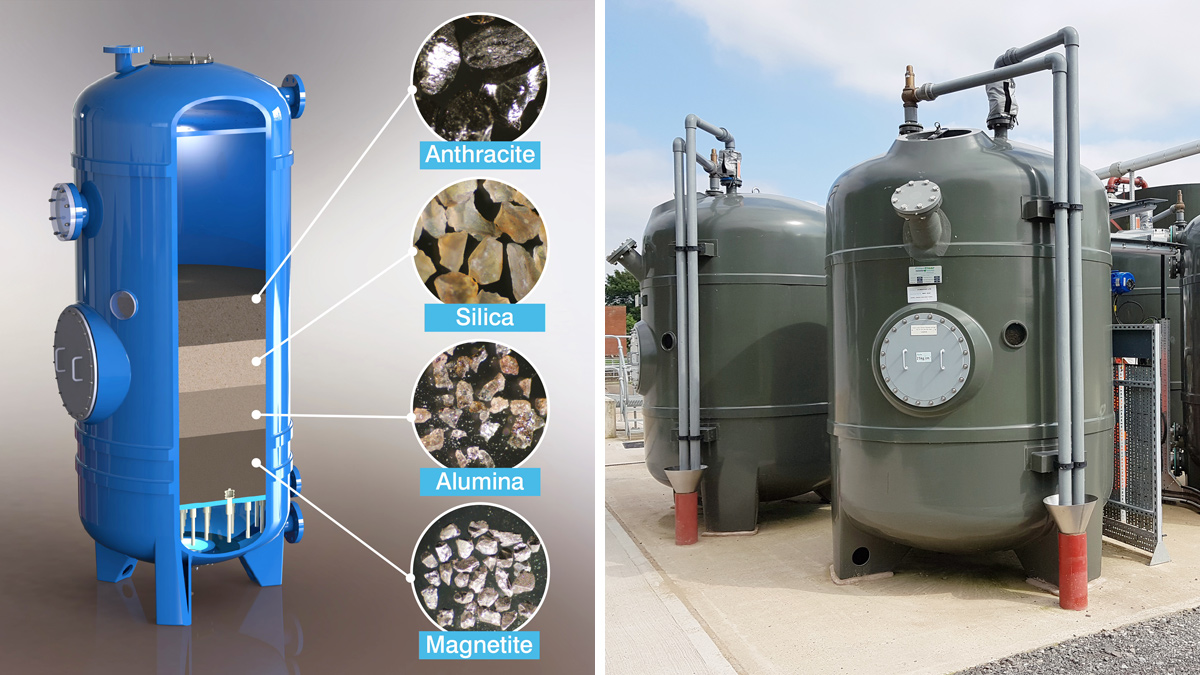
FilterClear: Four-media depth filtration (anthracite, silica, alumina and magnetite) - Courtesy of Bluewater Bio
During AMP7 over 800 sites were required to meet tighter phosphorus permits under the National P Removal Programme. The majority of these sites adopted the solution of using tertiary solids removal (TSR) plant with ferric or aluminium dosing to meet the permit requirements. There are 6 major TSR plant suppliers in the UK, three of which use the same technology, each with its unique feature, competing in the P removal market. This has driven the TSR technologies to evolve and improve, addressing the needs to enhance reliability and to minimise the use of chemicals whilst meeting increasingly stringent standards.
FilterClear for phosphorus removal
FilterClear is a true depth filtration technology, with 900 mm of filtration bed depth. The influent is pumped to the top of the filter and flows through four layers of media: anthracite, silica, alumina and magnetite, which have decreasing particle size and increasing density. This configuration provides an equivalent of 4-stage filtration in a single vessel, allowing the filter to operate at a much higher filtration rate (up to 35m3/h) and achieve a better effluent quality than conventional sand filters; coupled with its much smaller footprint. FilterClear is a powerful tool in a designer’s armoury.
The key benefit of depth filtration is to enable the solids to be removed progressively through the entire depth of the 4-layer filter bed, extending the run-time and reducing backwash frequencies. The backwash can be controlled by timer or pressure. After backwash, the media will settle back to the original layers thanks to the carefully selected density and particle sizes of the four media types.
FilterClear has an average operating pressure of 0.4 bar, offering a low energy demand and a low operational carbon footprint.
Experience across the many FilterClear plants installed to date has highlighted the low cost of ownership, particularly with respect to operation and maintenance. The plants are fully automated and typically require just one annual service (less on sites with activated sludge upstream). There is no routine requirement for replacement parts or filtration cloths and the FilterClear plants require only a top-up of anthracite every few years.
Furthermore, all media layers are naturally-occurring minerals, thereby not introducing any microplastics or fibres into the treated effluent or dirty backwash water.
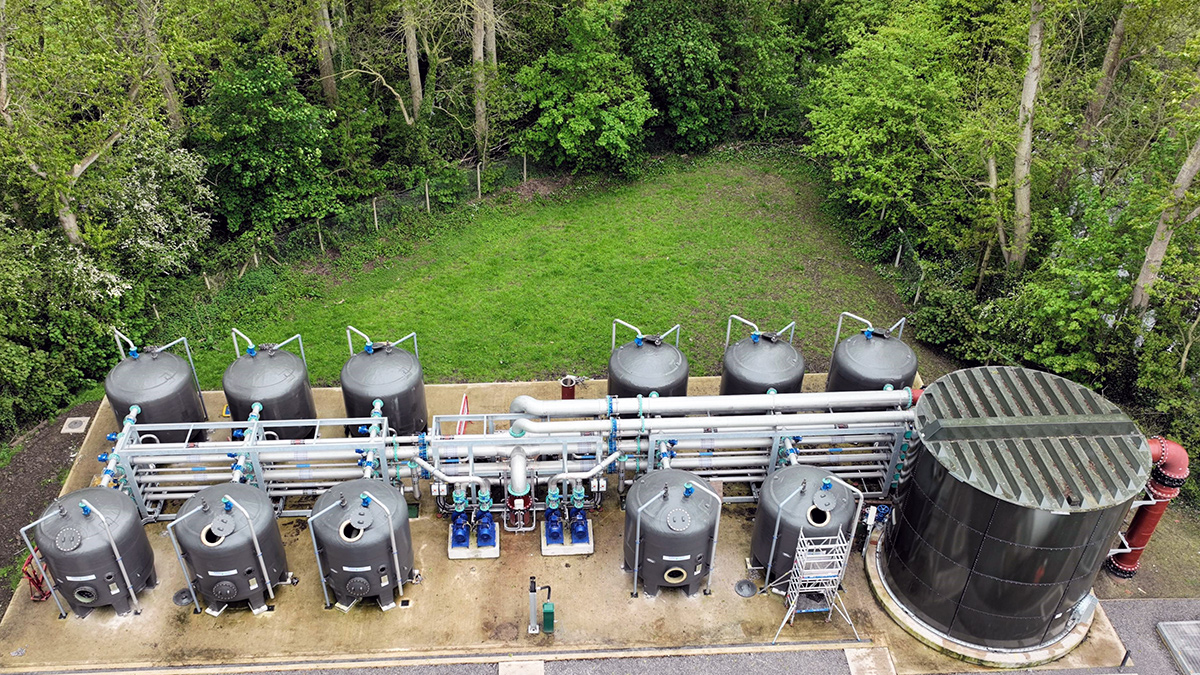
FilterClear plant at Yeovil WRC – Courtesy of Bluewater Bio
For chemical P removal, good coagulation and flocculation are critical. Many TSR technologies need purpose-built coagulation and flocculation tanks with mechanical mixing, and some will also require polymer dosing.
By comparison, FilterClear only requires coagulant dosing for P removal; no polymer or ballast material is required. This is because large flocs are not essential for depth filtration. Chemical dosing can be added directly upstream of the FilterClear plant via an inline static mixer, and flocculation will occur in the headspace inside the filter vessel, above the media bed, removing the need for mechanical mixing or a flocculation tank, thereby simplifying the asset and reducing associated costs.
The absence of a separate flocculation tank further minimises the FilterClear footprint, makes the solution simpler to build and operate and eliminates the associated operational and maintenance tasks. It also eliminates the need for an overflow from the flocculation tank which, having been dosed with coagulant, represents a compliance risk.
Design for manufacture and assembly (DfMA)
Increasingly, clients and their tier one partners are looking to minimise site construction activities and durations. FilterClear plants are designed to allow off-site assembly and testing, then delivery to site as a package plant. Where possible, the complete filter gallery, including backwash pumps, blowers, actuated valves, instruments and controls are skid-mounted and transported fully assembled. Site activities are then limited to coupling the filter vessels, adding the media and commissioning. This DfMA approach ensures both quality and safety are well controlled and ultimately delivers a better solution in a shorter time at a lower overall cost.
Health and safety is an integral part of the design process, ensuring that all equipment is safe to install, operate and maintain. Filtration and backwash of the FilterClear plant is fully automated, with minimum operational input. The filters are enclosed, with no moving parts or serviceable components within the vessels and need minimal operator intervention. Due to the enclosed, fully automated design, risk of operator exposure to wastewater or chemicals is minimised. Furthermore, all machinery is at ground level for easy access.
Proven performance
Most TSR plant suppliers prefer to offer an effluent total suspended solids (TSS) guarantee as a surrogate to a TP guarantee. However, water companies have realised that, at low concentrations, there is a very poor correlation between the TSS and TP concentrations thereby introducing compliance risk.
As the developer and owner of the technology, Bluewater Bio Ltd has a deep understanding of both the process and phosphorus removal, and accordingly are able to provide a TP guarantee. This offers the client and their contractor the simplest and clearest assurance of meeting the final effluent permit as well as being contractually most straightforward. FilterClear performance has been tested and proven at over 50 sites across most UK water companies, all reliably achieving the respective permit requirements for both TP and iron. Knowing that more stringent TP permits will be imposed in AMP8, Wessex Water carried out long-term trials to push the performance limits at several sites with impressive results.
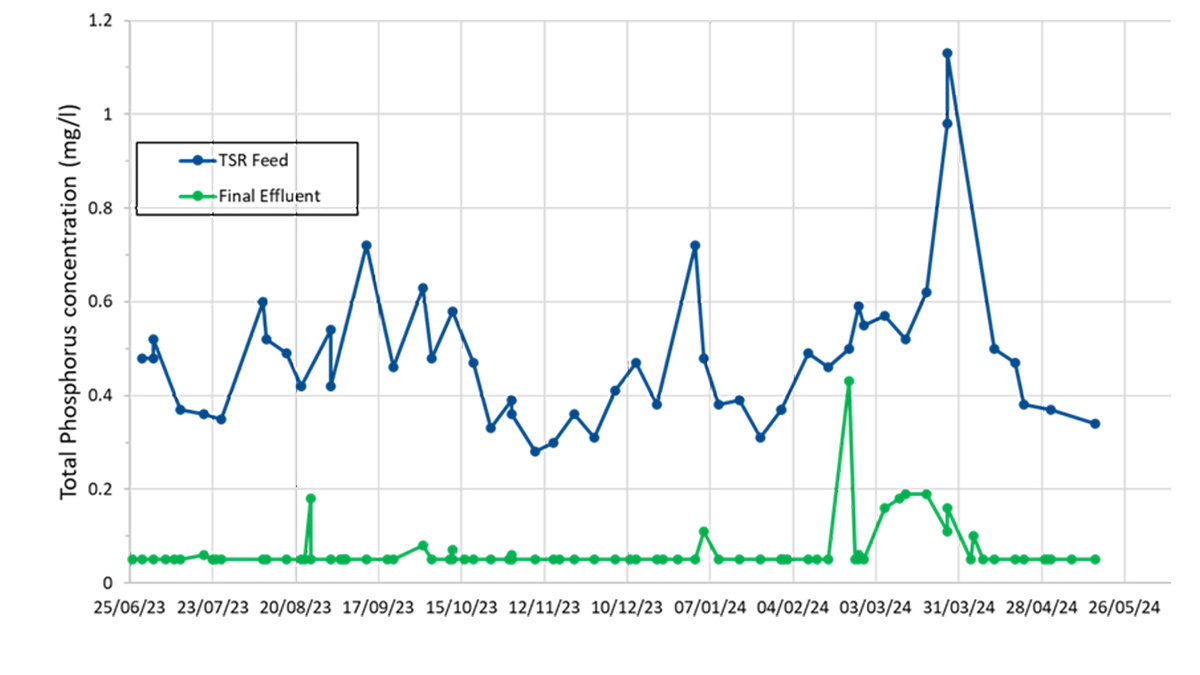
‘Site A’ performance graph: Blue line shows the Total P concentration of the TSR feed and the green line shows the Total P concentration of the final effluent after FilterClear treatment – Courtesy of Bluewater Bio
‘Site A’ is a typical small trickling filter site. In AMP7, a FilterClear plant was installed to meet a new 0.5 mg/l TP permit. The trial demonstrated that the plant achieved an average TP below 0.07 mg/l, with a 95%ile iron concentration of 0.27 mg/l. This performance has been achieved with an overall ferric dose of just 15 mg/l (including 1st point and 2nd point dosing) with simple flow-proportional dosing control, and despite some unrelated control issues during the trial. The long-term trials have demonstrated that FilterClear plants can reliably achieve a TP permit of 0.1 mg/l, making the solution future-proof. This offers the client a means of reducing WLC whilst adding future certainty.
FilterClear: Key advantages
Proprietary stratified FilterClear media of up to four layers, specially developed and applied over 10 years for exceptional performance.
- High loading rate (25-50 m3/m2/h, i.e. 2-5x flow rate of competing technologies).
- High solids retention (low pressure drop and long backwash interval).
- High quality filtrate in a single step (SDI <3 : NTU <0.1 : BOD concentration <6mg/l).
- Low CAPEX (2-5x less media, fewer vessels).
- Low OPEX (no chemical use, low electricity consumption).
- Low backwash volume (<6% of filtrate, small backwash tanks, better yield, less waste).
- Small footprint (2-5x smaller filter area, smaller plant).
- Low O&M (simple, reliable, easy to maintain).
- Modular systems up to 1200m3/h per vessel.
Case study: Wessex Water: Yeovil Pen Mill WRC
During AMP7, Wessex Water installed 14 FilterClear plants across its region for phosphorus removal, ranging from small sites less than 4,000 population to large sites over 75,000 population. Yeovil Pen Mill Wastewater Recycling Centre (WRC) is the largest site among these.
Yeovil WRC in Somerset is a large treatment works owned by Wessex Water, serving a population equivalent (PE) over 75,000 (including trade discharge). The existing treatment processes comprised:
- Primary settlement tanks.
- High-rate plastic media filters.
- Intermediate humus tanks.
- Trickling filters (slag media).
- Humus tanks.
To meet tightened consent requirements, a major upgrade was required during AMP7; comprising tertiary MBBR plant and a tertiary solids removal (TSR) plant.
The TSR plant with chemical dosing is required to achieve the total phosphorus (TP) consent of 0.5 mg/l. On a whole life cost basis, taking into account process reliability, delivery programme, power demands, chemical consumption and maintenance requirements, FilterClear from Bluewater Bio Ltd was identified as the preferred solution, and the contract was awarded in May 2022.
The key elements of the FilterClear plant at Yeovil WRC are:
- Number of filters (800mm diameter): 11
- Number of backwash pumps: 2 duty/2 standby
- Number of backwash blowers: 2 duty/2 standby
- Number of clean backwash tanks: 1
- Number of dirty backwash tanks: 1
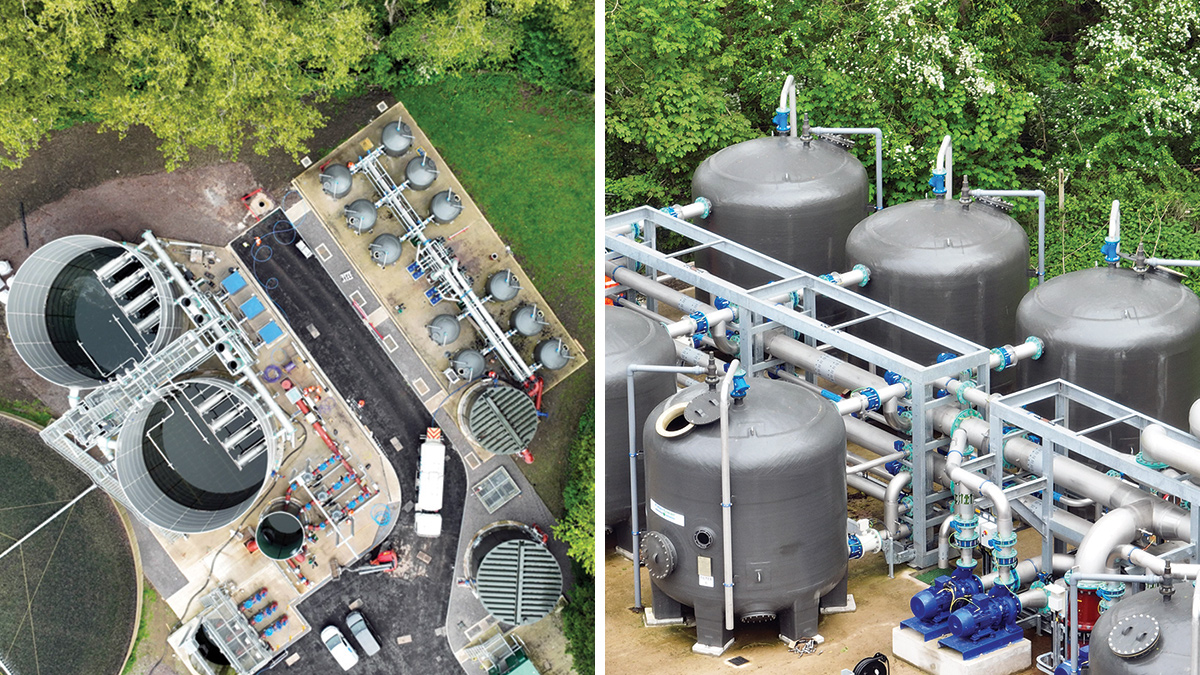
(left) FilterClear plant at Yeovil Pen Mill WRC next to a trickling filter and tertiary MBBR plant at Yeovil WRC and (right) Skid design at Yeovil Pen Mill WRC for easy access and maintenance – Courtesy of Bluewater Bio
The FilterClear plant design has taken into account the following:
- Treat the peak flow during filter backwashing.
- Ensure the solids holding capacity is adequate under the worst-case scenario.
- Manage the interfaces with tertiary pumping/ferric dosing.
- Minimise the whole life cost and footprint.
- Enable safe and easy access, lifting and maintenance (ALM).
Thanks to the high filtration rate, the FilterClear plant has a smaller footprint in comparison to conventional filters. The compact nature of the FilterClear plant makes it ideal for the very congested site at Yeovil. At the time of writing (July 2024), the FilterClear plant has been installed and is currently being commissioned.
Throughout the project, the design teams worked closely with Wessex Water on the ALM assessment to ensure that the plant is operator-friendly. Particular attention was paid to eliminating hazards during operation and maintenance.
Highest accolade – rising to the challenge in AMP8
Innovation plays a critical role in the water industry’s ability to adapt to climate change, population growth and new and emerging pollutants. Bluewater Bio Ltd continue to develop and enhance technologies so that they excel in performance, value, reliability and sustainability.
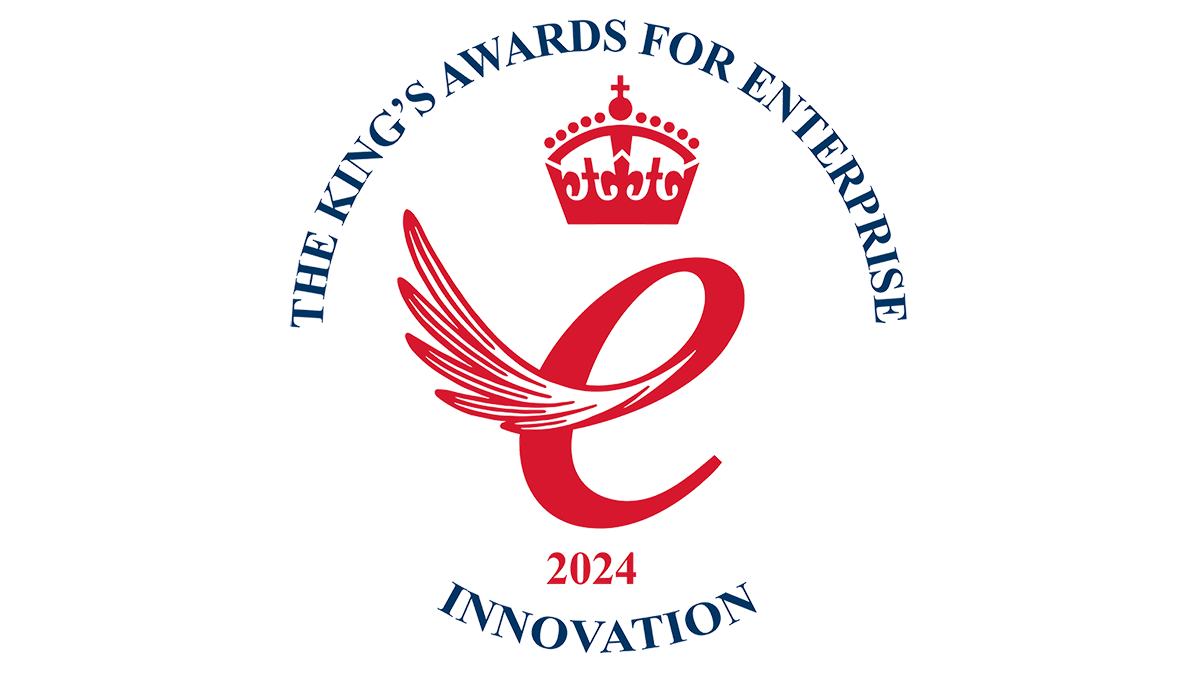
FilterClear technology received a King’s Award for Enterprise (Innovation category) in 2024
In 2024 Bluewater Bio Ltd received a King’s Award for Enterprise in the Innovation category for its FilterClear technology. The award was granted on a recommendation by the Prime Minister and approved by His Majesty The King and is the most prestigious award for a UK business. This award is further recognition that FilterClear has become the preferred choice for clients.
With AMP8 on the way, over 900 sites will be on the national P removal programme and FilterClear will play a major part in delivering a successful outcome.
Winchester House, 259-269 Old Marylebone Road, London NW1 5RA
| 020 7908 9500 | bluewaterbio.com |
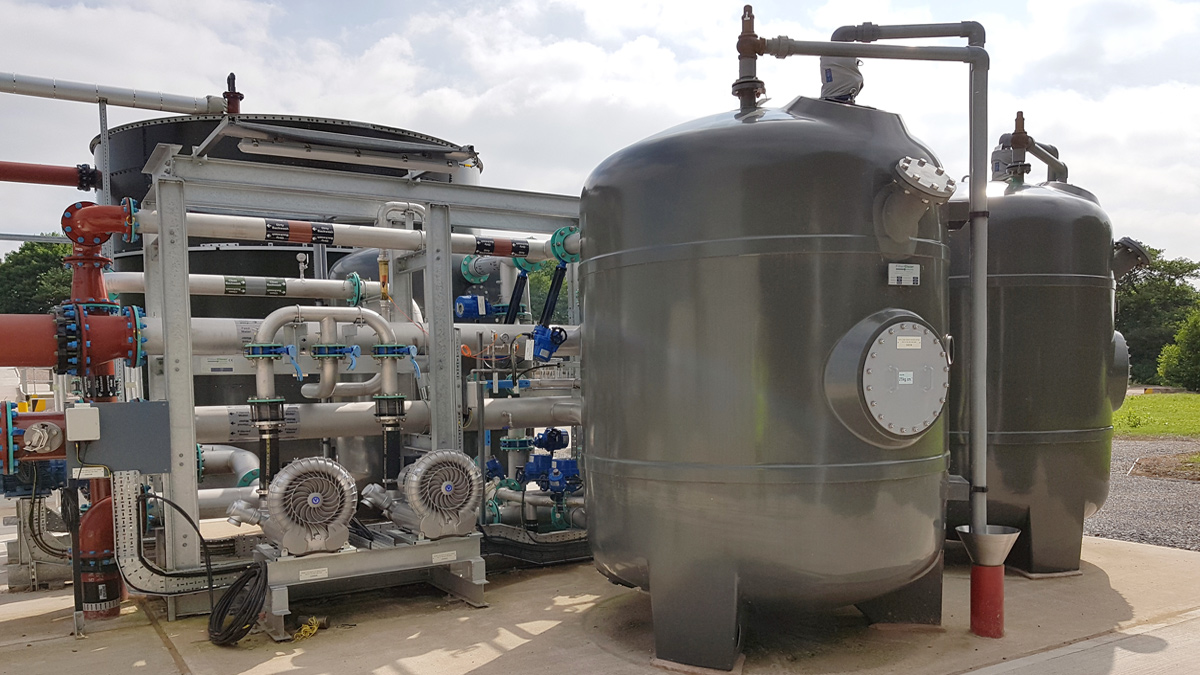
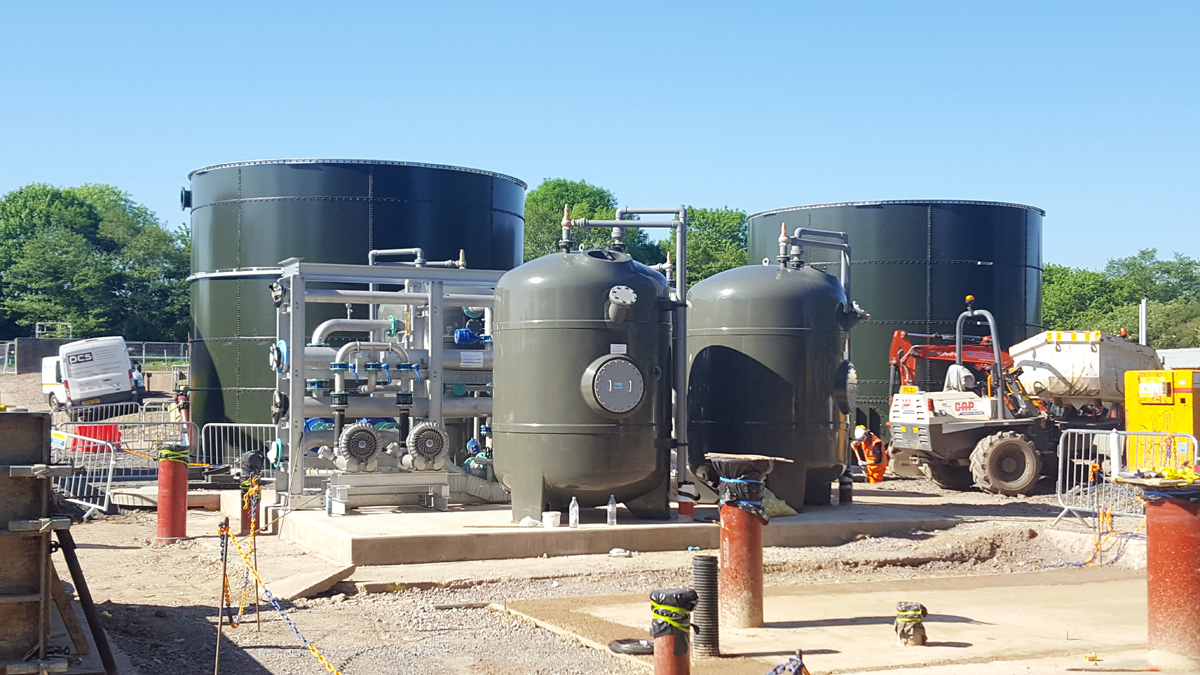
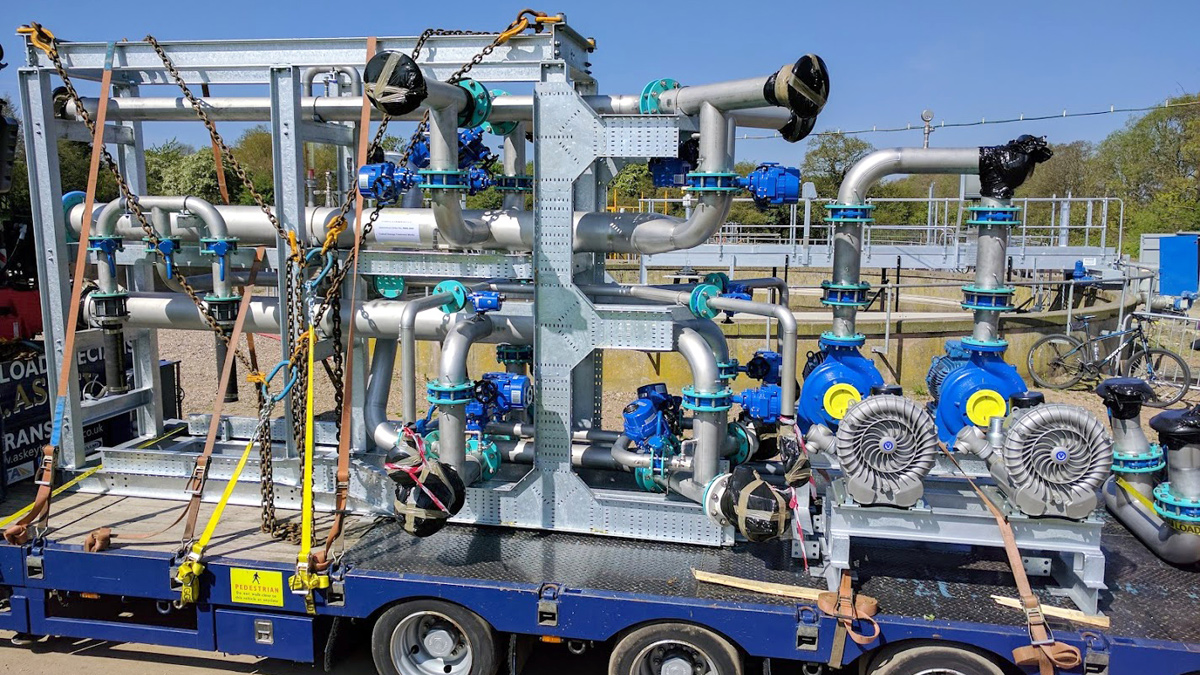
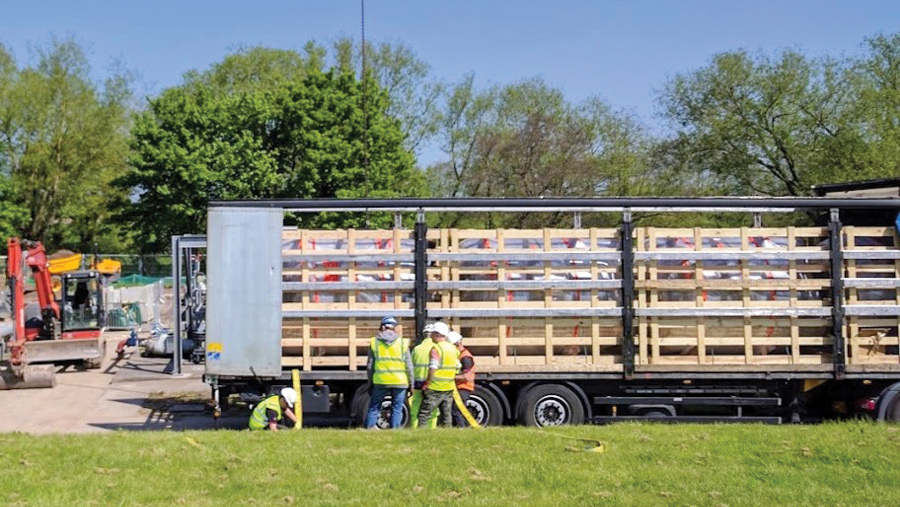
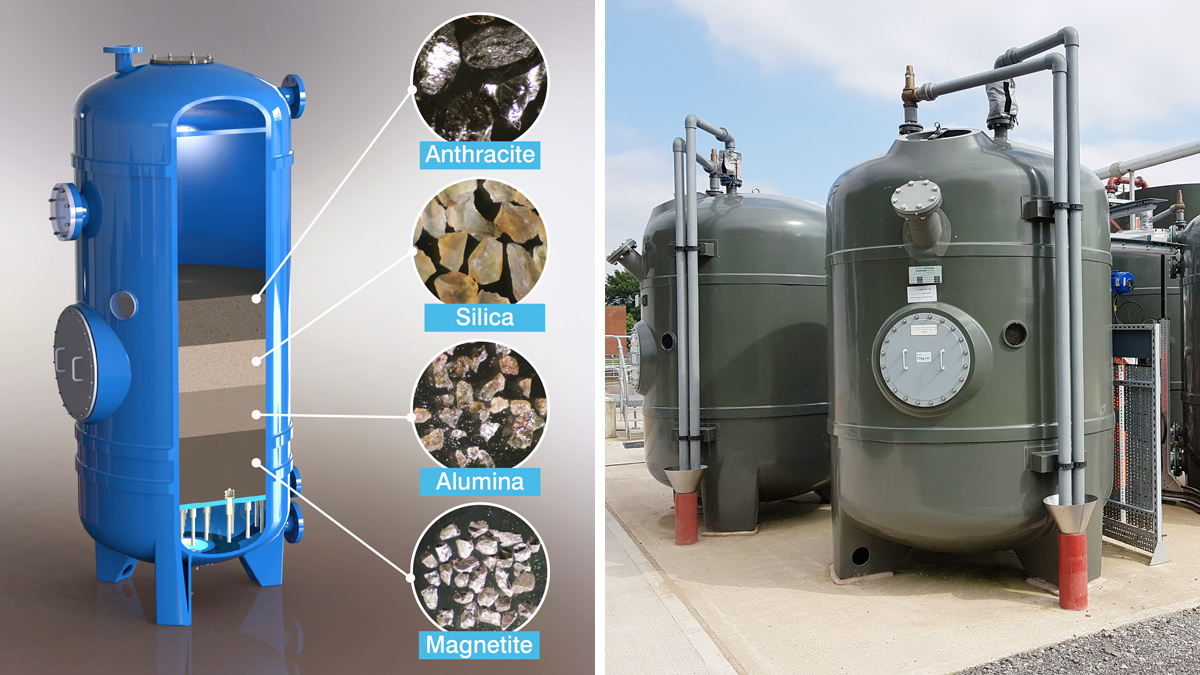
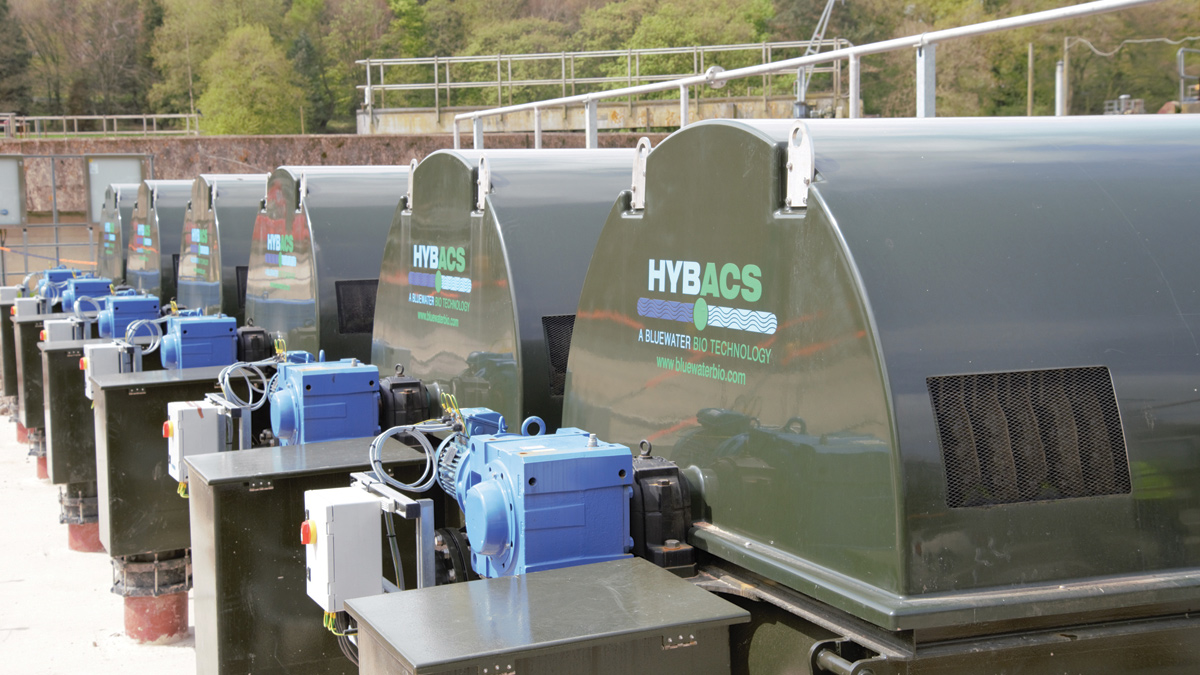
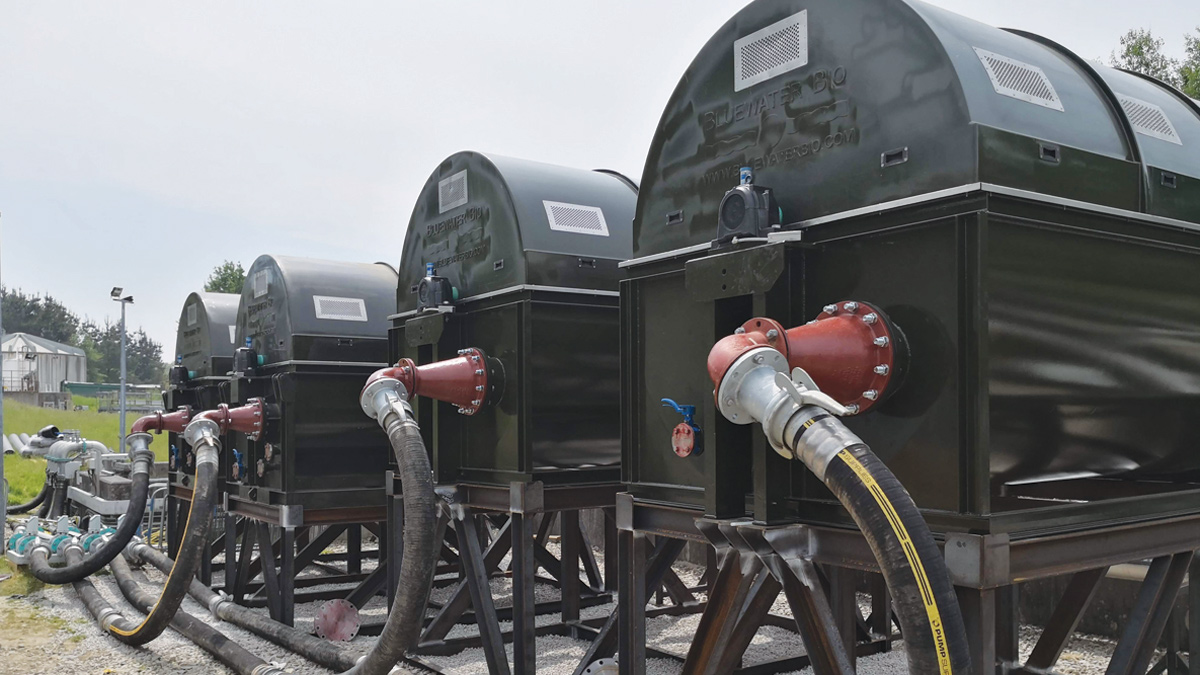
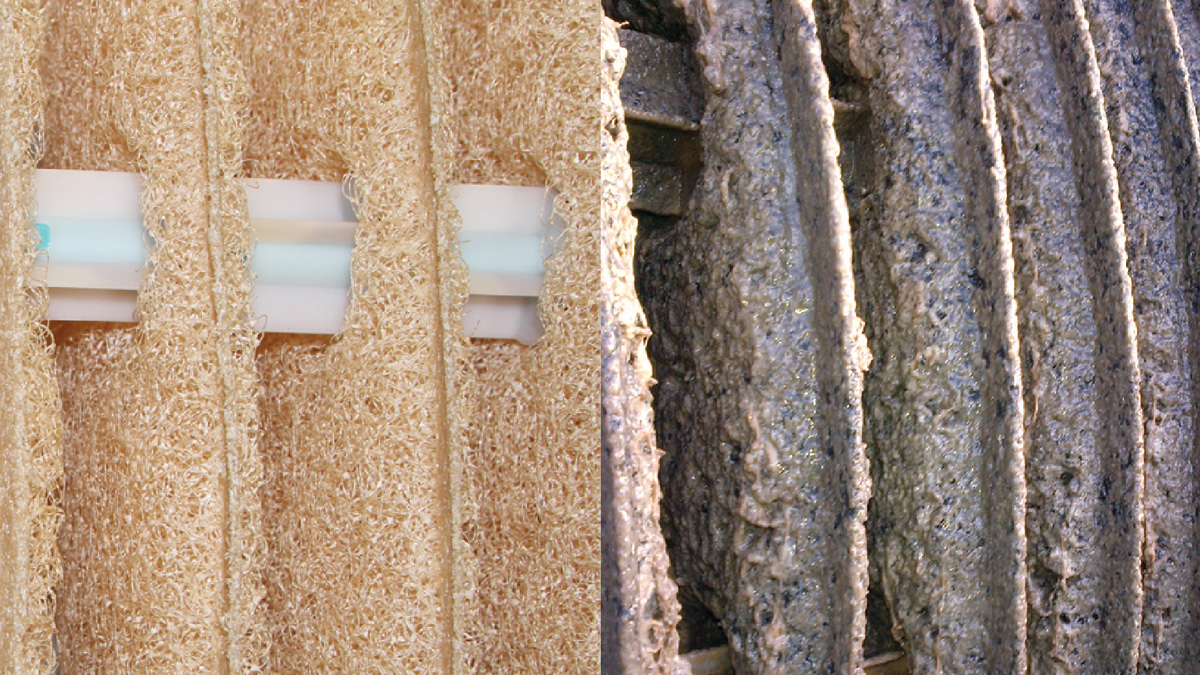
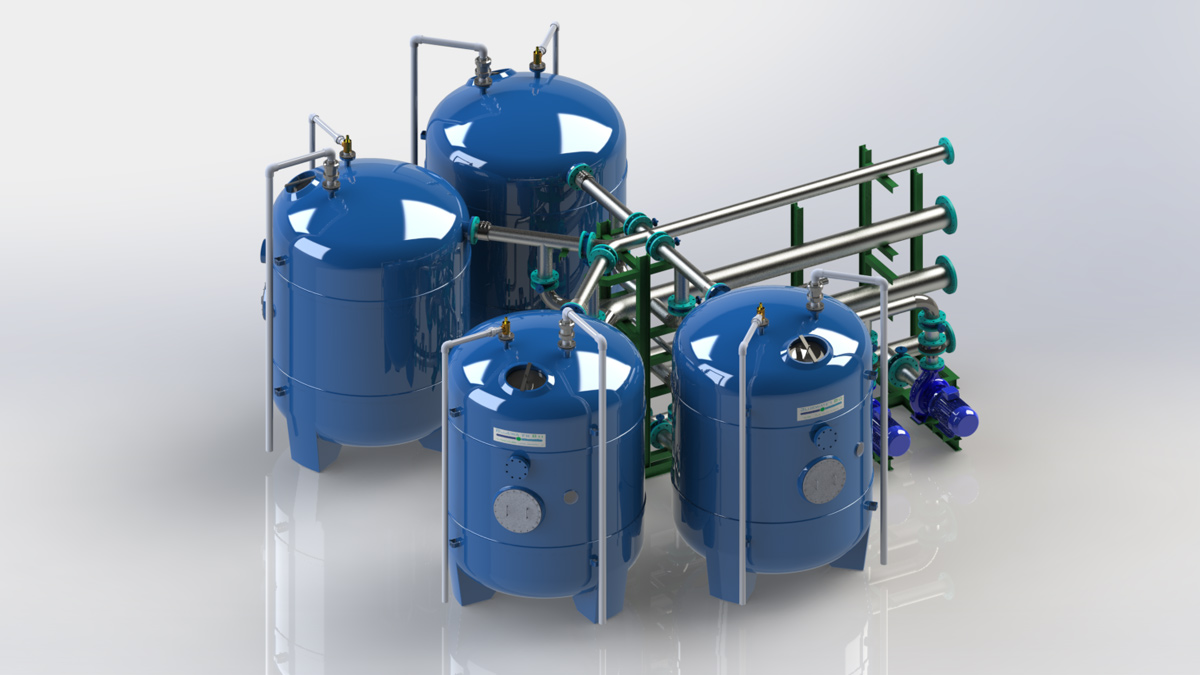
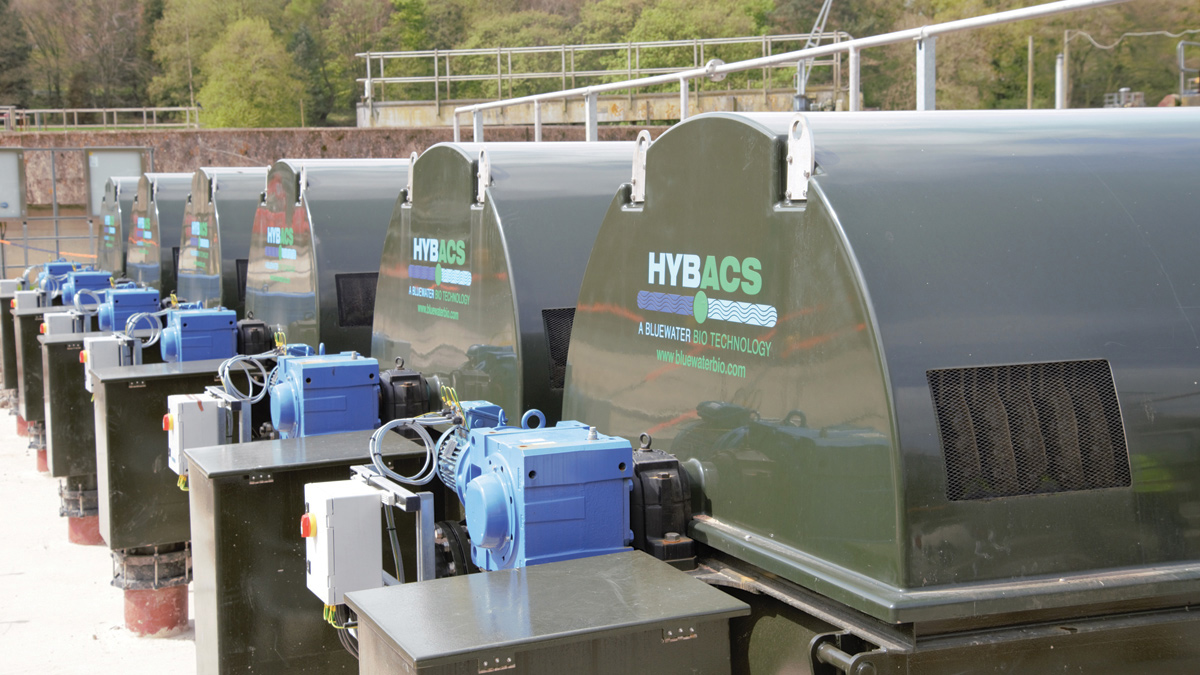
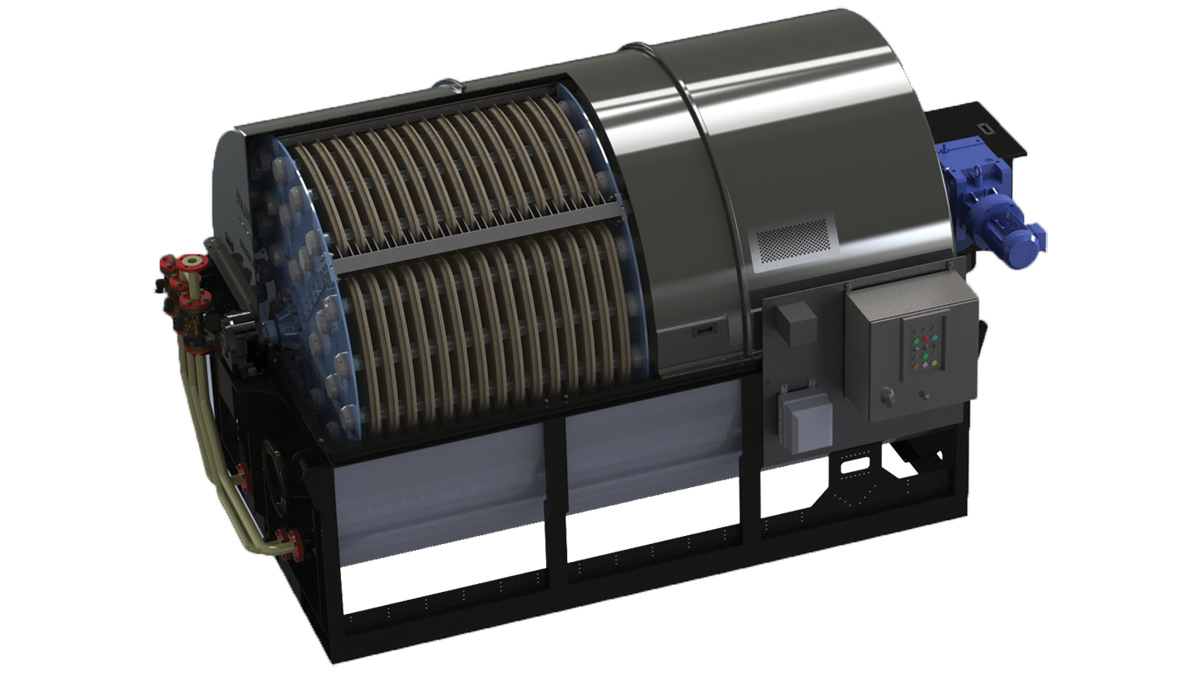
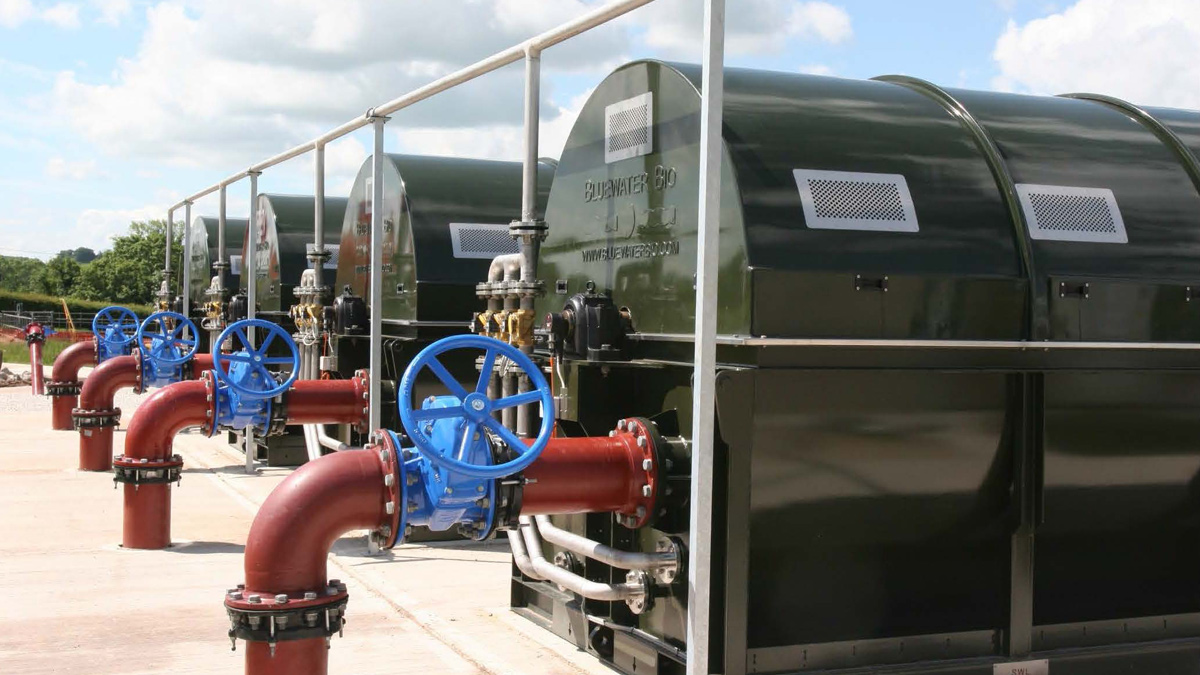
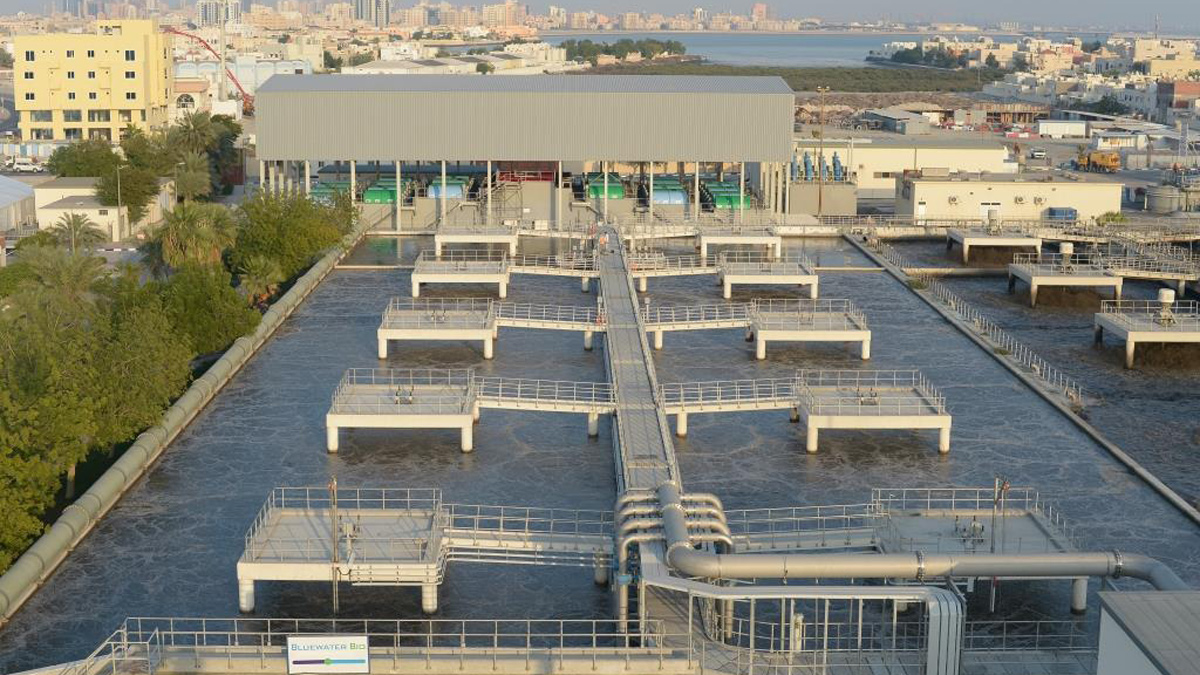