Newthorpe STW (2023)
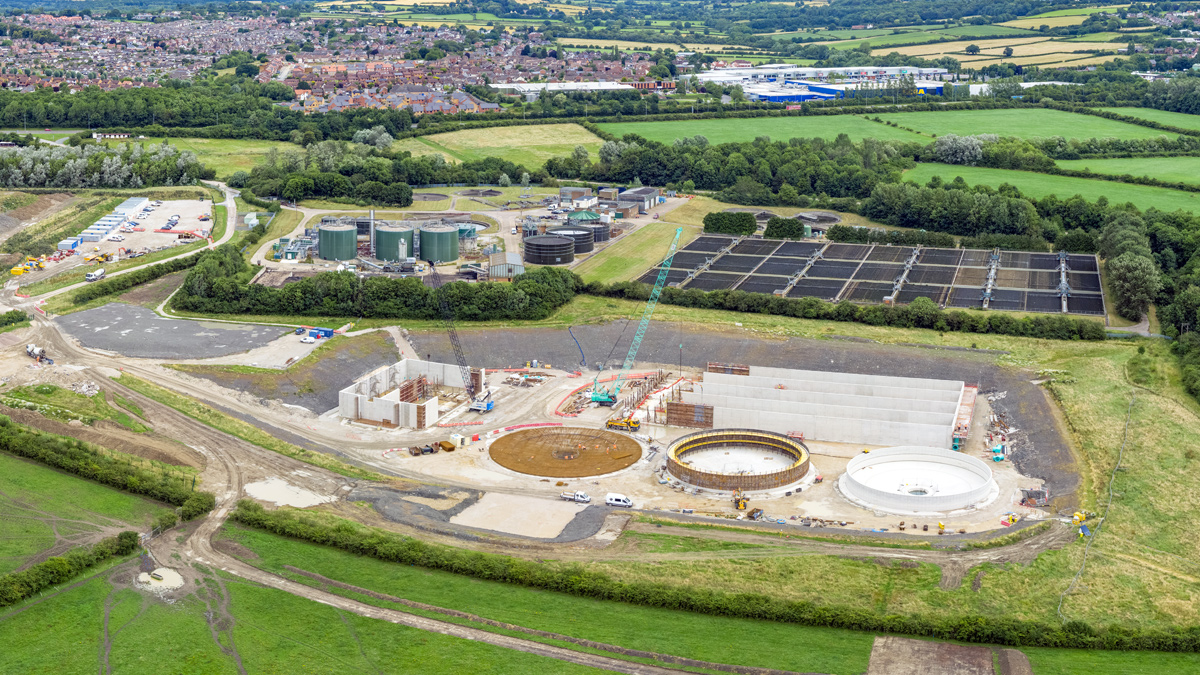
Newthorpe STW site overview July 2023 - Courtesy of Mott MacDonald Bentley
North-west of Nottingham and separated by the River Erewash, two of Severn Trent’s sewage treatment works are situated within 2.5km of each other; part of the legacy of the times of the public statutory undertakers. Heanor Milnhay STW in Derbyshire has a dual-stream process, with part of the flows going through trickle filters and the rest being treated in a conventional activated sludge plant. It treats up to 258 l/s from a population equivalent of 41,000 from the Heanor catchment. Newthorpe STW in Nottinghamshire, which also serves a PE of approximately 41,000, is a filter treatment process with a maximum capacity of 324 l/s.
Project objectives
The objectives of the project are to improve the quality of the effluent at Heanor Milnhay STW and Newthorpe STW to meet the Water Framework Directive (WFD) requirements set out in the National Environmental Programme (NEP).
This is to be achieved through the transfer of flow to full treatment (FtFT) from Heanor Milnhay STW to Newthorpe STW for combined treatment. As part of the NEP commitments to meet the obligations of the WFD in AMP7, a new phosphorus (P) permit of 0.2 mg/l will be introduced on 22 December 2024. The target price of the project is £35.8m.
Project summary
Heanor Milnhay: Heanor Milnhay will be decommissioned once construction at Newthorpe is complete, with the site only retaining its storm tanks. The storm capacity will be increased from 2,000m3 to 7,000m3 by the transformation of its two primary settlement tanks into new storm tanks and the construction of an extra blind tank.
A combined sewage overflow chamber will split the storm flows from the flows to be treated at Newthorpe, which will be pumped through a dual rising main to the new works.
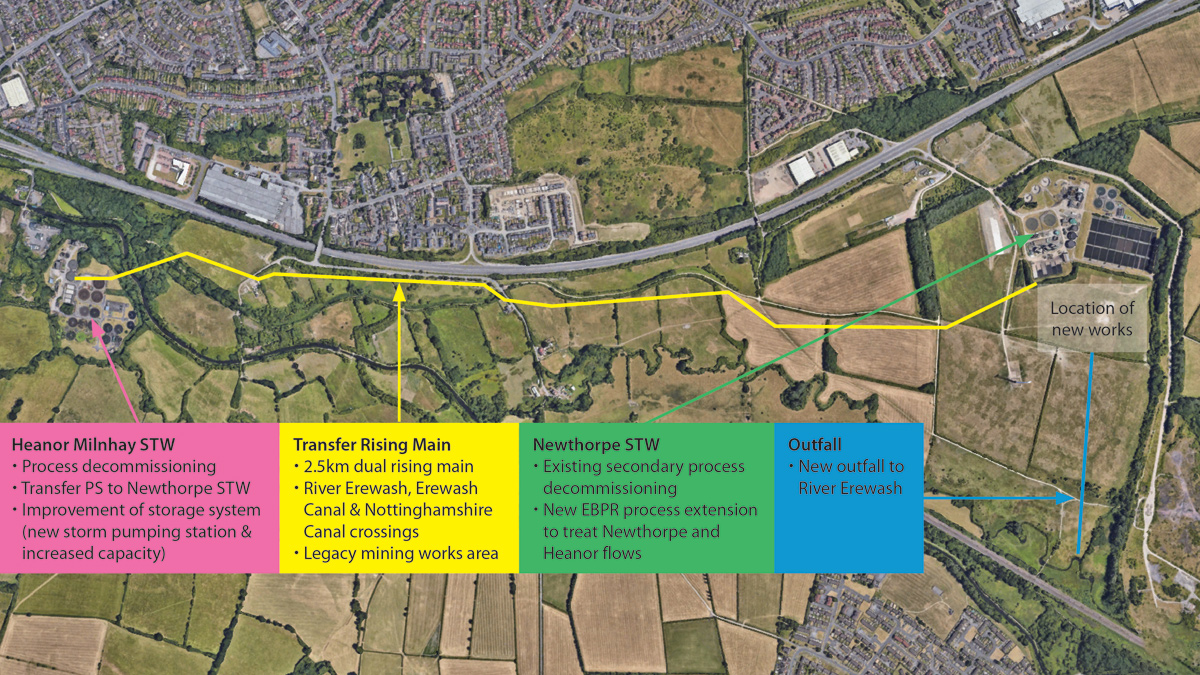
Google Maps image showing general scheme overview – Courtesy of Mott MacDonald Bentley
Newthorpe: At Newthorpe, the secondary and tertiary treatment will be decommissioned. Only the preliminary treatment (screening and grit removal) and the primary settlement tanks will be retained as part of the new process stream.
The extension, which will be built on the field adjacent to the existing works, will use an Enhanced Bio-Phosphorus Removal (EBPR) process, in a modified University of Cape Town (UCT) configuration. This process aims to reduce chemical consumption using polyphosphate-accumulating organisms (PAO) to eliminate phosphorus.
Newthorpe STW extension
Newthorpe STW will see a complete transformation. The new process will be capable of treating double the flow in a similar footprint to the existing works. The extension will consist of:
- New inlet works to treat the flows transferred from Heanor Milnhay STW: While the Newthorpe flows will still be treated at the existing inlet works on site, Heanor Milnhay flows, which will arrive at the site crude, will go through a 2D 6mm escalator fine screen provided by Longwood Engineering and a Crossflow grit detritor provided by Tuke & Bell, before entering the new treatment.
- Combination chamber with a high flow overflow: The new chamber will combine the flows coming from Newthorpe, which have been settled in the existing primary settlement tanks, with the flows coming from Heanor Milnhay. Heanor Milnhay flows will not be settled before entering the secondary treatment to provide the EBPR with the right level of load. However, the process is protected from highly diluted load flows with a high-flow overflow, that will allow flows above 66% of FtFT to bypass the anaerobic and anoxic section and go directly to the aerobic treatment.
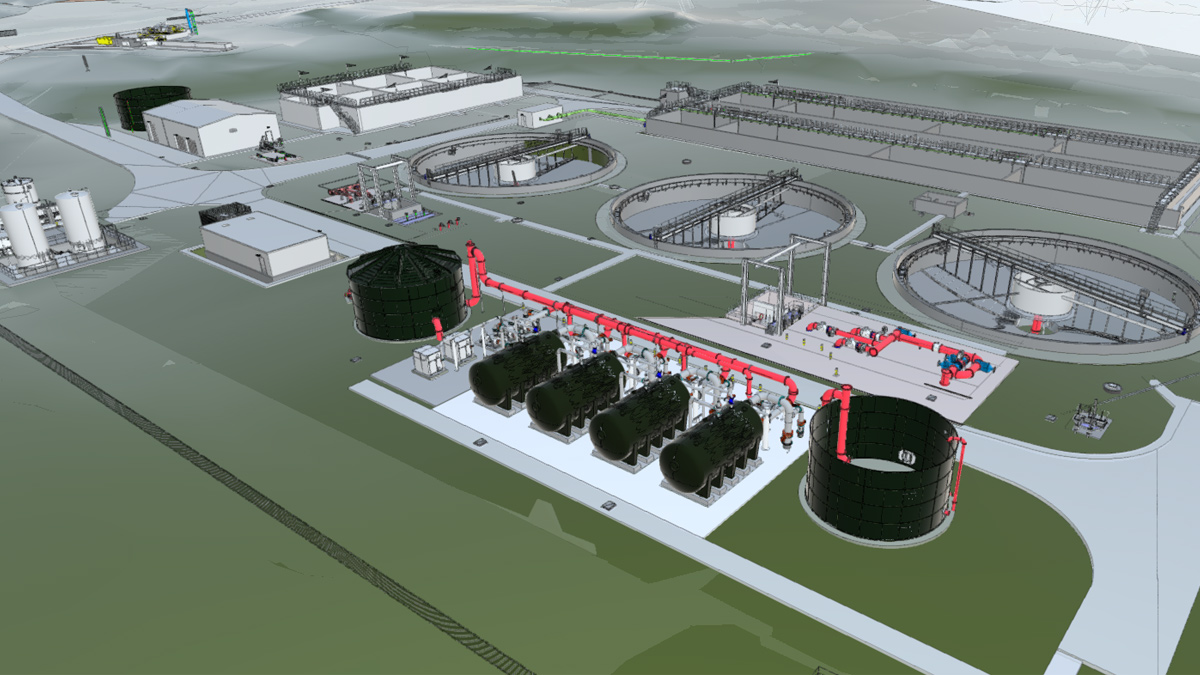
Newthorpe STW extension Revit model – Courtesy of MMB
- An anaerobic and anoxic tank, with a capacity of 2,438m3 per section (4,876m3 in total): To provide the right level of tank in series and mixing in the system, each tank consists of three equal pockets with submersible mixing. The recirculated active sludge (RAS) and the liquors from the thickening of the surplus active sludge (SAS) will join the process in an intermediate chamber located between the anaerobic and the anoxic sections. The tank is a 40m long, 25m wide and 6.5m high structure.
- A 4-lane activated sludge plant (ASP) holding a total process volume of 20,000m3 (5,000m3 per lane): This is the biggest structure on site; 90m x 42m and a height of 6.5m. Each line has a swing zone that turns 3,000m3 of volume from aerobic to anoxic in summer. Sulzer are providing the blowers and Xylem Water Solutions provides the aeration grid and pipework for the tank.
- Final settlement tanks: 3 (No.) 33m diameter final settlement tanks designed and built by Tank Consult Ltd, with full scraper bridges designed by EPS Water.
- Mixed media filtration: Consisting of four horizontal vessels supplied by Bluewater Bio Ltd, this is the largest plant of this kind for the treatment of wastewater installed in the UK.
- Sludge thickening: Comprising Alfa Laval gravity belt thickeners aided by polymer dosing by Richard Alan Engineering.
- Chemical dosing: Alkalinity dosing to limit ammonia from Lintott Control Systems and ferric dosing to trim P to meet the new tightened permit of 0.2mg/l from Colloide.
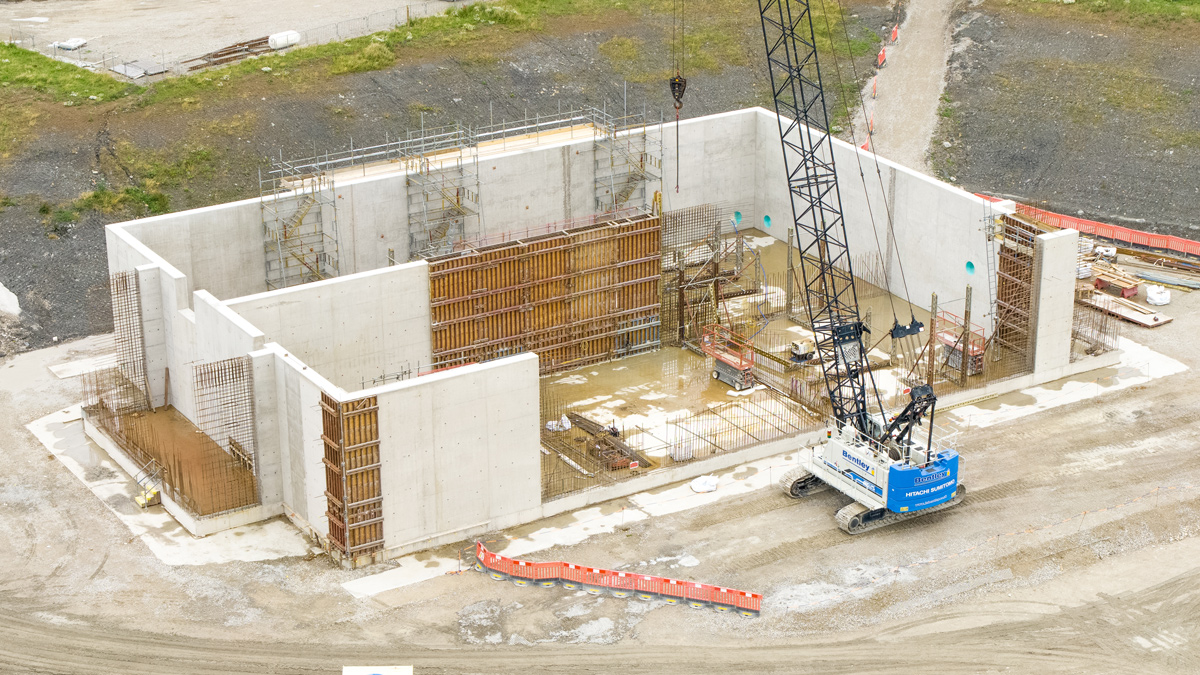
Anaerobic & anoxic tank construction progress – (July 2023) – Courtesy of Mott MacDonald Bentley
Newthorpe STW: Supply chain – key participants
- Client: Severn Trent
- Principal designer & contractor: Mott MacDonald Bentley
- FRC: Bell Formwork Services Ltd
- Design/build of FRC final settlement tanks: Tank Consult Ltd
- Rising main HDD: Johnston Trenchless Solutions (JTS)
- Tertiary solids removal: Bluewater Bio Ltd
- Gravity belt thickeners: Alfa Laval
- Inlet screens: Longwood Engineering Company Ltd
- Grit removal plant: Tuke & Bell
- Scraper bridges: EPS Water
- Glass-coated steel tanks: Goodwin Tanks
- Aeration diffusers for ASP: Xylem Water Solutions
- MCCs: CEMA Ltd
- Kiosks: Morgan Marine
- Coated pipework & wall starters: George Green (Keighley) Ltd
- Polymer dosing: Richard Alan Engineering
- Alkalinity dosing: Lintott Control Systems
- Ferric dosing: Colloide
- Mixers, blowers & submersible pumps: Sulzer Pumps Wastewater Ltd
- Progressive cavity pumps: NOV
- Booster pumps: Grundfos
- Valves: AVK UK Ltd
- Lifting equipment: T Allen Engineering Services Ltd
- Steelwork: Galliford Try Fabrications
- Fencing: Town & Country Fencing (Midlands) Ltd
Carbon reduction
One of the main aims for the Newthorpe delivery team has been minimising the carbon footprint of the project, using the PAS2080 carbon hierarchy.
- Build nothing: The original scope of works included new inlet works to treat Newthorpe STW flows. However, after a structural inspection of the existing inlet works, and given that the design flows were not increased, it was proposed to reuse the existing structure, with some minor modifications, just replacing the mechanical equipment. The estimated carbon saving was circa 250 tonnes of CO2.
- Build less: A joint effort of the Mott MacDonald Bentley process and structural team lead to a big carbon saving in the ASP structure. The process team identified the opportunity of reducing one lane from the outline design, with no detriment to the process.
At the same time, the structural team developed a solution with variable wall and slab thickness to optimise the concrete. In total, it was estimated that the embodied carbon of the structure was reduced by 400 tonnes.
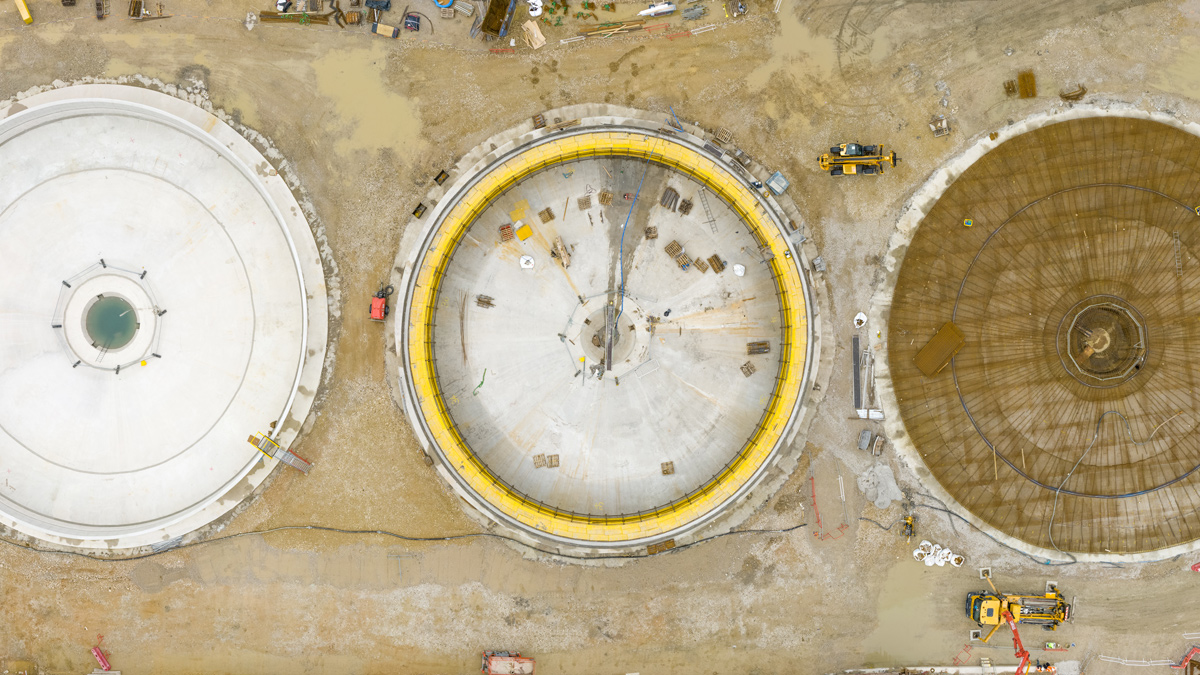
Final settlement tanks construction progress July 2023 – Courtesy of Mott MacDonald Bentley
Build smart: Due to the depth of the final settlement tanks into the ground, flotation was the limiting factor in the design. In the preliminary calculations, the estimated slab thickness required for the tank to float in a maintenance scenario was above 1000mm. The project team, therefore, challenged themselves to try to achieve a more sustainable solution. The outcome was to install an active drainage system that, in case of maintenance, would lower the groundwater level to 2m below the final ground level. That reduced the slab thickness to 400mm, without having a major impact on the operation of the plant, as this drainage system will only be required during maintenance scenarios where the tank needs to be emptied.
Build efficiently: To carry out the earthworks for the new site, the site team has used GPS-intelligent plant that, utilising a 3D model of the ground, reduced the plant-operator interface on site, improving H&S as well as efficiency. The excavated ground has been re-used to screen the site and provide biodiversity net gain, instead of having to transport it off-site.
Progress to date
Construction started in the summer of 2022 and at the time of writing, July 2023, is progressing well:
- The ASP slab is complete and the ASP walls are 70% complete and there is similar progress on the anaerobic/anoxic tank. Both structures will be ready to start hydrostatic testing and installation of M&E equipment by early Autumn.
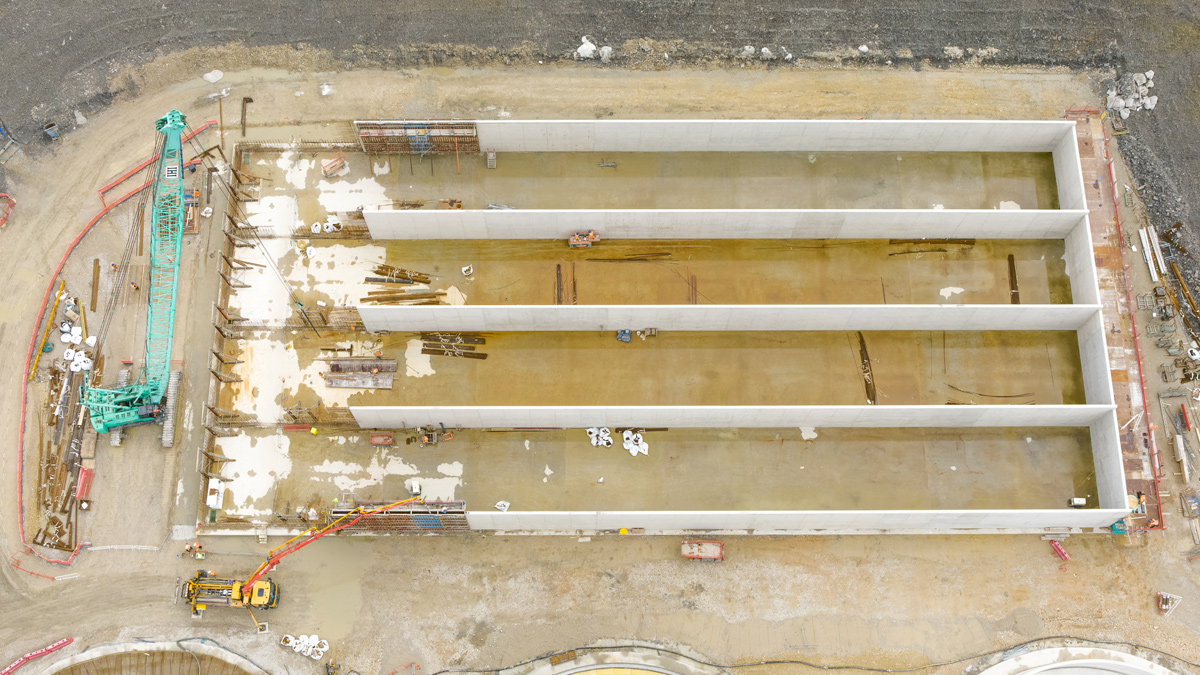
ASP Tank construction (July 2023) – Courtesy of Mott MacDonald Bentley
- FST1 is now completed and undergoing hydraulic test and FST2 and FST3 are under construction.
- Construction of the inlet works for the Heanor Milnhay flows and the MCC basement are due to start shortly.
- The first section of the rising main connecting Heanor Milnhay and Newthorpe are underway with a planned completion by the end of 2023. The rising main design has been challenging due to the number of features and a large number of external stakeholders requiring complex management by MMB. While half of the rising main will be installed by open trench methodologies, almost 1.2km will be built using directional drill, in two separate sections. The first section will cross the River Erewash, the Erewash Canal, and the disused Nottinghamshire Canal. The second section will follow the alignment of Newmanleys Road and will avoid any need for road closures or traffic management in the area. Particularly challenging is the section closer to the works, which has old mine works recorded, and therefore needs special measures to minimise the risk of encountering unknown mining features.
- In Heanor Milnhay STW, the redundant assets in the area where the new assets will be built have been demolished, however, the construction on site is subject to the completion of the first directional drill shot and has not yet progressed.
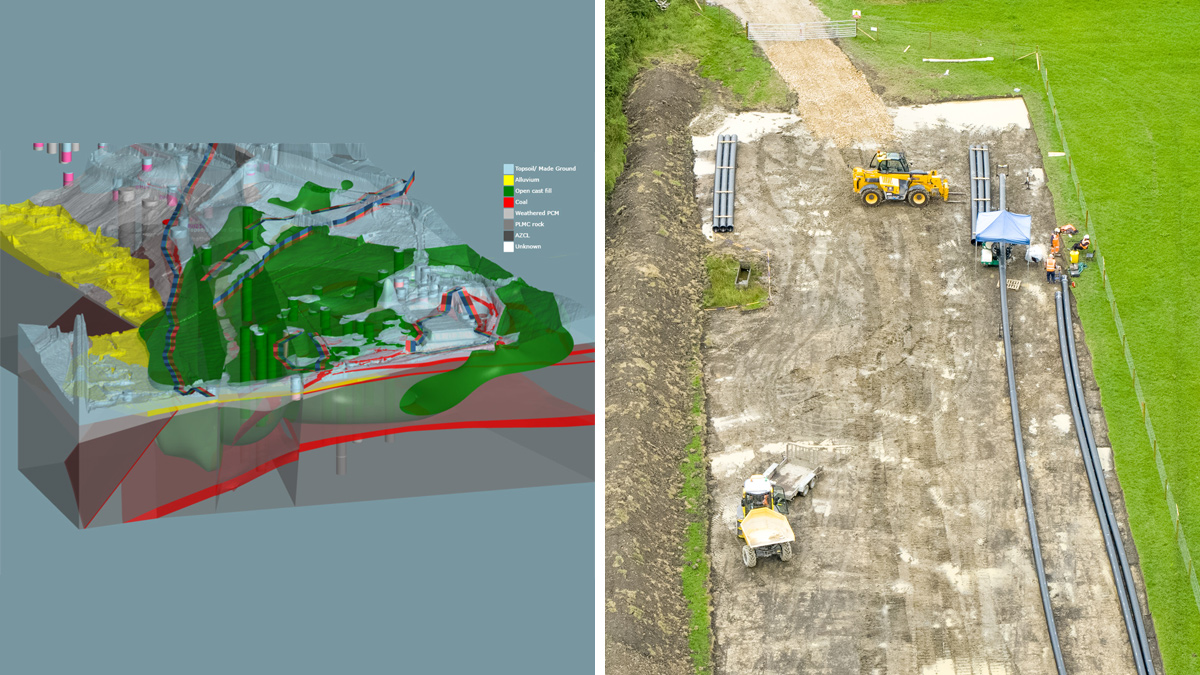
(left) Ground modelling to explore coal seams and (right) detail of rising main welding area – Courtesy of Mott MacDonald Bentley
Summary
Newthorpe and Heanor Milnhay STWs are being merged together in one of Severn Trent’s major AMP7 projects, with Mott MacDonald Bentley as principal designer and contractor. The expansion of Newthorpe STW will make it one of the largest enhanced bio-phosphorus treatment sites in the region, covering a population equivalent of 100,000; achieving a tightened permit of 0.2 mg/l while minimising the use of chemicals to remove phosphorus. The construction of the project is ongoing with the biggest structures set to be completed in Autumn 2023.
The expected completion date of the project, including the biological maturation of the EBPR is December 2024.
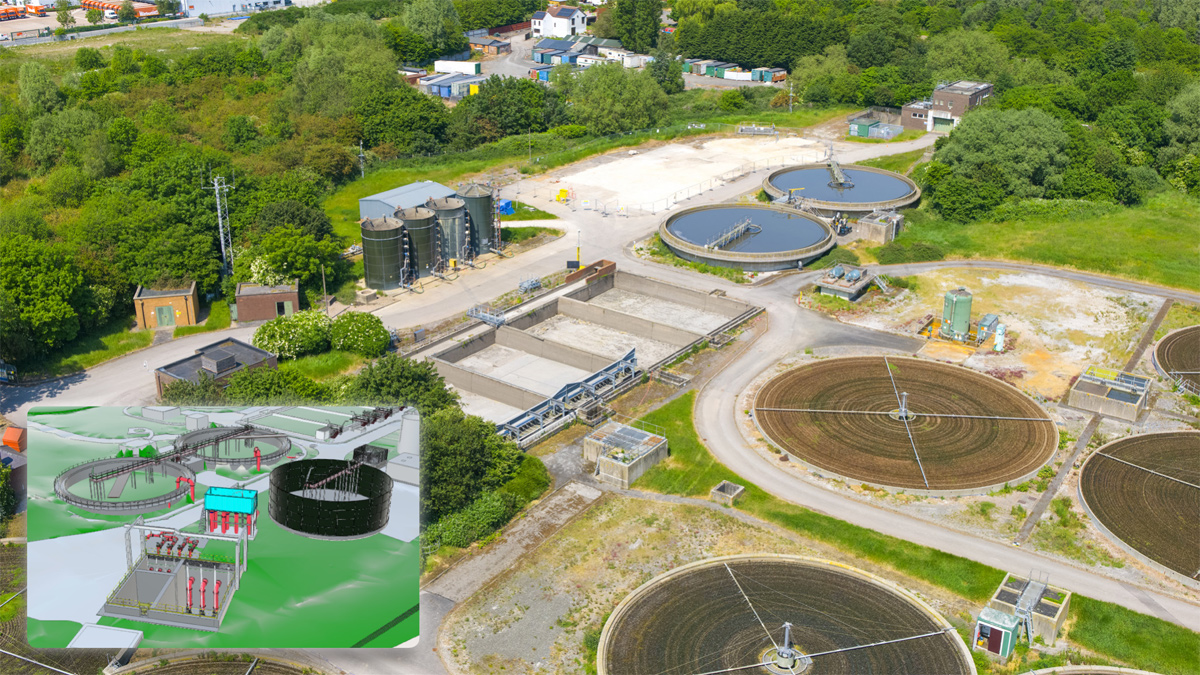
Heanor Milnhay STW: (main image) demolition completed July 2023 and (inset) Revit model - Courtesy of MMB