Nereda
Nereda (2016)
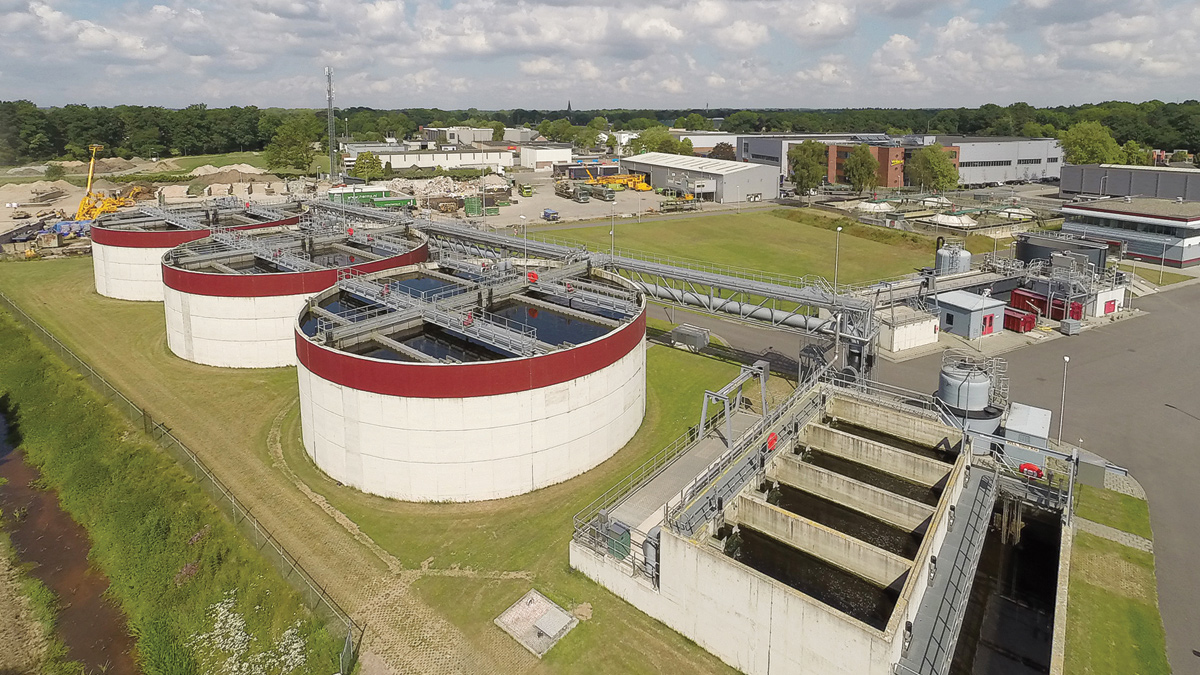
Nereda® Epe WwTP, the first Dutch municipal full-scale Nereda plant, operational since 2011 - Courtesy of Royal HaskoningDHV
UK water companies currently face many challenges, including the drive for improved phosphorus removal from a number of directives, in particular the Urban Wastewater Treatment Directive. There is also a growing requirement for increased nutrient removal, requiring low levels of ammonia, total nitrogen, BOD and suspended solids. In addition, there is the ongoing challenge to drive improved sustainability in wastewater treatment and lowest long-term cost of service to customers. All these challenges need to be met, but in many cases without increasing the footprint of the works, so there is often the challenge of fitting improvements onto existing wastewater treatment sites. The full-scale development of Nereda® is setting new standards in sustainable wastewater treatment with more than 30 plants now in operation or construction around the world. The UK Water sector is now investing in the technology, supported by Royal HaskoningDHV, and taking advantage of its compact design, high quality effluent standards and significantly lower energy costs.
How Nereda® can help meet these challenges
Nereda® is considered to be the first aerobic granular sludge technology which has been successfully applied at full scale, with more than 30 plants now in operation or under construction worldwide. Nereda® provides the advantages of high levels of nutrient removal particularly biological phosphorus removal, and it is cost effective, with lower energy usage when compared to activated sludge plants (20-50% lower power requirement). Recent examples have shown this technology can provide a compact, small footprint solution, typically requiring a land area of 25% of that needed for an equivalent conventional activated sludge (four times smaller).
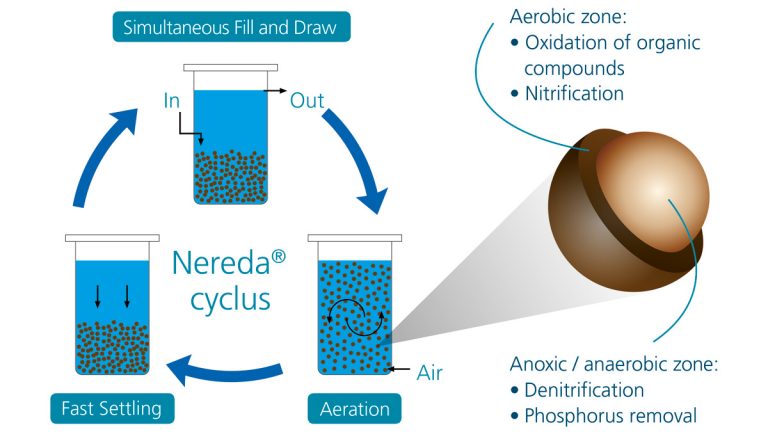
Nereda® Process Cycle – Courtesy of Royal HaskoningDHV
A typical Nereda® plant for UK requirements includes a feed buffer tank and 3 (No.) Nereda® reactors. Each reactor operates a cyclical process with three stages. The first stage involves simultaneously feeding and displacing treated water from the top of the reactor.
The second stage is aeration and the final stage is settling. All these stages occur in each reactor, with the reactors being fed in sequence. Aerobic granular sludge is naturally selected by wasting slow settling biomass during each cycle. Granular sludge with fast settling characteristics allows operation at a high biomass concentration of 8-15g/l compared to conventional activated sludge that would normally operate at 3-4g/l.
The aerobic granular sludge allows for aerobic conditions on the outer edge of the granule, whilst the inner core provides anoxic and anaerobic conditions. Also, the operating conditions favour the formation of poly-phosphate acuminating organisms (PAO). Granular activated sludge provides the advantages of simultaneous nitrification-denitrification and enhanced biological phosphorus removal, whereby phosphate uptake occurs during aeration and phosphate rich sludge is subsequently removed from the system.
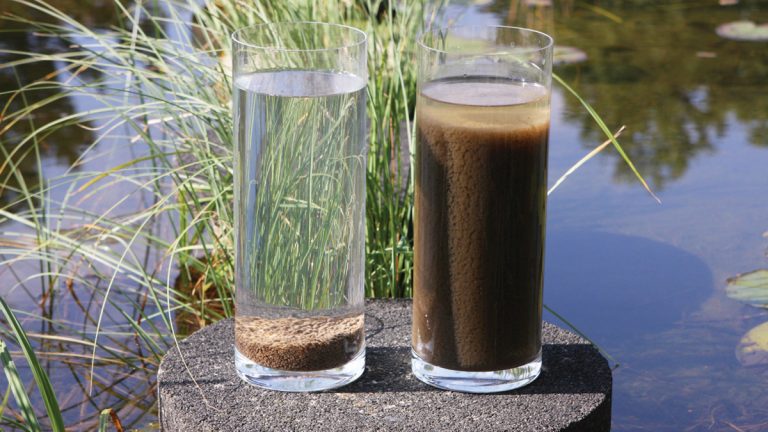
Settling Properties of the aerobic granular biomass (left) compared to activated sludge (right) – Courtesy of Royal HaskoningDHV
Aerobic granular sludge can therefore achieve high levels of biological nutrient removal in a single tank compared to activated sludge systems where at least three distinct zones, multiple recycle streams and final settlement tanks are required.
The enhanced sludge settleability of aerobic granular sludge is evident from a comparison of typical full scale SVI (sludge volume index) values – for aerobic granular sludge the SVI5 (five minutes) tends towards the SVI30 (30 minutes), with typical values at operational Nereda® plants around 30-60mℓ/g (Giesen et al, 2013), whereas for activated sludge the SVI30 is typically in the range of 110-160mℓ/g and the SVI5 is not measured because activated sludge exhibits minimal settling within five minutes (Tchnobanoglous et al, 2004).
The recently completed Nereda® project at Ryki in Poland is a good example of what can be achieved in UK conditions.
Ryki WwTP – Poland
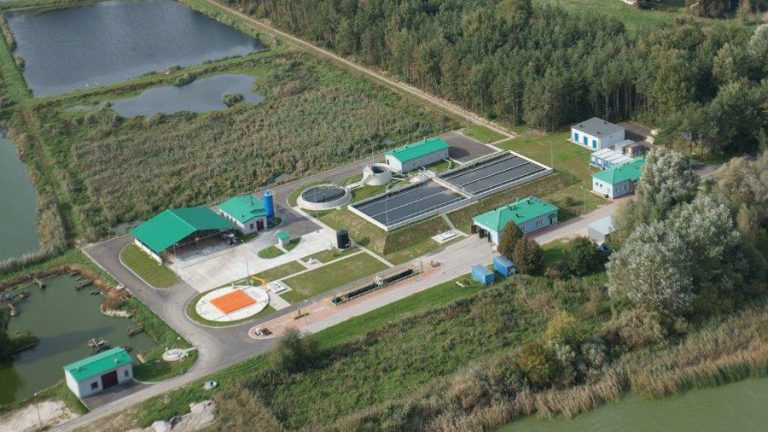
Nereda® Ryki WWTP in Poland proving a fast start-up also in winter conditions – Courtesy of Royal HaskoningDHV
In the city of Ryki (Lublin Province, Poland) a new Nereda® wastewater treatment plant entered operation in February 2015. This is the first Nereda® installation located in the eastern part of Central Europe and also the first Nereda® plant that has to contend with low process temperatures during the winter period. The Ryki Nereda® plant is designed to treat 5,320m3/d (dry weather), corresponding to 38,600 PE.
In addition to the challenging winter temperatures, the plant has to treat a range of different incoming sewage (domestic, septic tanks and industrial effluent) and has to handle extended periods of peak industrial load.
The combined pre-treated sewage flows to an influent buffer tank (500m3) from where 2 (No.) Nereda® reactors (2,500m3 each) are separately fed by 3 (No.) submersible pumps (one buffer plus two reactors configuration).
The treated wastewater is discharged to surface water via an existing pond. Table 1 shows the design loads for the plant, Figure 1 the wastewater temperatures experienced at the plant and Table 2 shows the effluent quality compared to the consent requirements.
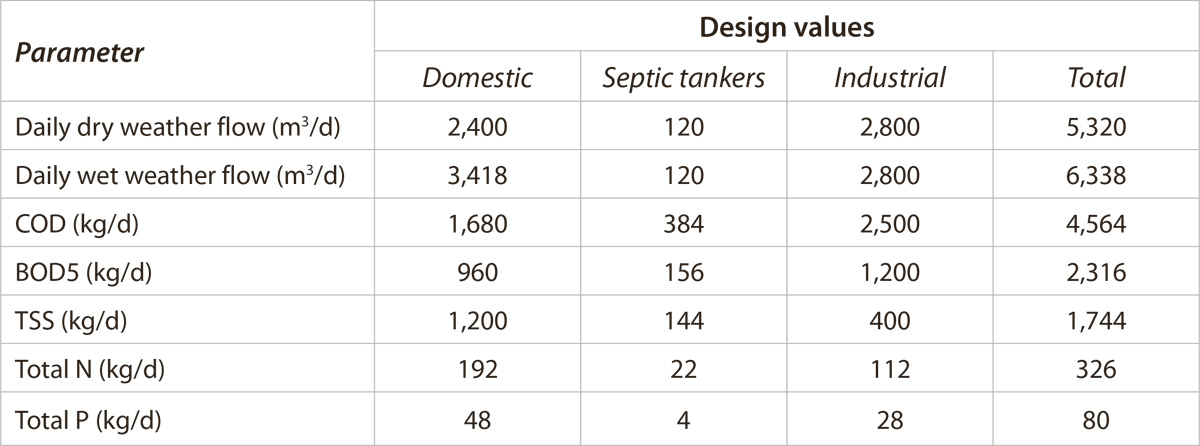
Table 1: Design loads for the Ryki Nereda® plant
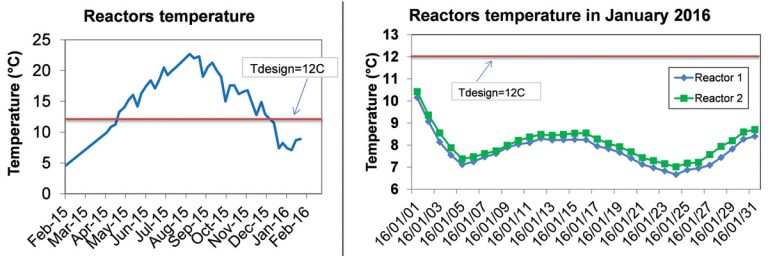
Figure 1: Temperatures at the Ryki WwTP
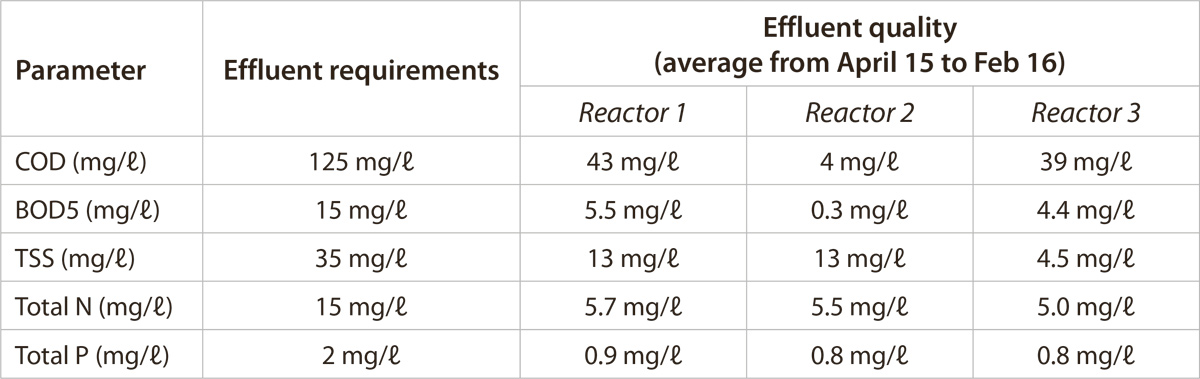
Table 2: Effluent quality at the Ryki Nereda® plant
The Nereda® installation at Ryki has been operational for more than two years and continues to achieve effluent compliance, despite the low winter temperatures and highly variable seasonal loading.
Adoption of Nereda® in the UK
Interest in Nereda® from UK water companies was initially pioneered by both Scottish Water and United Utilities. In 2013 each company initially invested in pilot plants to test the claims made by Royal HaskoningDHV following visits to full-scale plants in The Netherlands. Scottish Water demonstrated the benefits of the technology for uprating its wastewater treatment works at both Daldowie and Dalmarnock. Similarly, United Utilities used its pilot plant to investigate wastewater treatment at several works including Davyhulme and Crewe.
In 2015, Thames Water decided to install a new granular activated sludge plant at Highworth WwTW, serving a population of approximately 10,000 customers as part of its investment into the National Chemical Investigation Programme to demonstrate how effectively Nereda® technology can provide improved and more sustainable wastewater treatment with higher levels of nutrient removal. This plant has been developed by Costain Atkins JV, part of eight2O, Thames Water’s investment alliance for AMP6.
Highworth is nearing completion and will be commissioned later this year. In the meantime, Scottish Water has selected the technology for improved wastewater treatment at Inverurie and is actively developing solutions at other sites. In addition, United Utilities selected Nereda® for improved wastewater treatment at Kendal WwTW in Cumbria as well as at Morecambe WwTW in Lancashire.
There are ongoing pilot investigations by both United Utilities and Anglian Water as part of the Environment Agency’s Low P demonstration programme. Other water companies are particularly interested in developing projects utilising this new technology, including Severn Trent Water and Dŵr Cymru Welsh Water.
Developments in Ireland
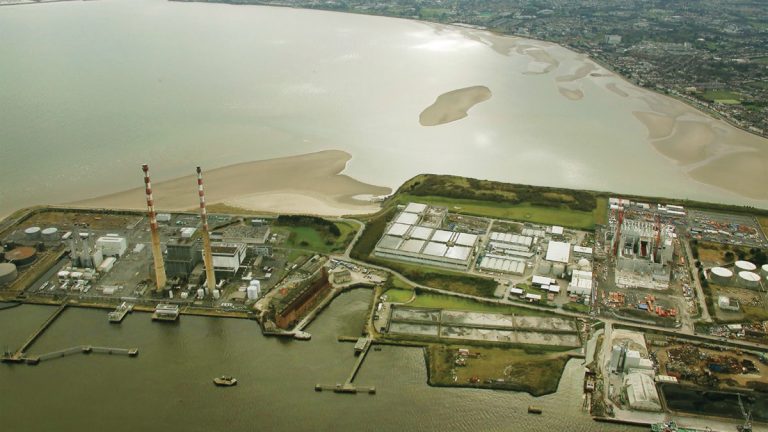
Nereda® Dublin Ringsend WwTP: significantly more biological treatment capacity by retrofit existing SBR – Courtesy Barrow Coakley Photography
The Clonakilty, Carrigtwohill and Cork projects are full-scale examples of Nereda that have been delivered by Royal HaskoningDHV’s licensee, EPS. The first plant installed by EPS was in Clonakilty, which has now been operational for over a year. EPS also developed its approach further and has now completed a second installation at Carrigtohill. This works has been a significant step forward in developing a compact technology solution within a single, small footprint concrete structure, where the benefits of factory manufacture and pre-assembly were first demonstrated. This approach has been further developed by EPS for its latest project at Cork Lower Harbour. This plant has been designed to serve a population of approximately 90,000 people and will be commissioned later this year.
The largest Nereda installation to date is being developed for Irish Water at Ringsend, Dublin. This project will help increase the capacity of the Ringsend wastewater treatment works to allow wastewater from a population of 2.4 million customers to be effectively and efficiently treated to a tightened effluent consent.
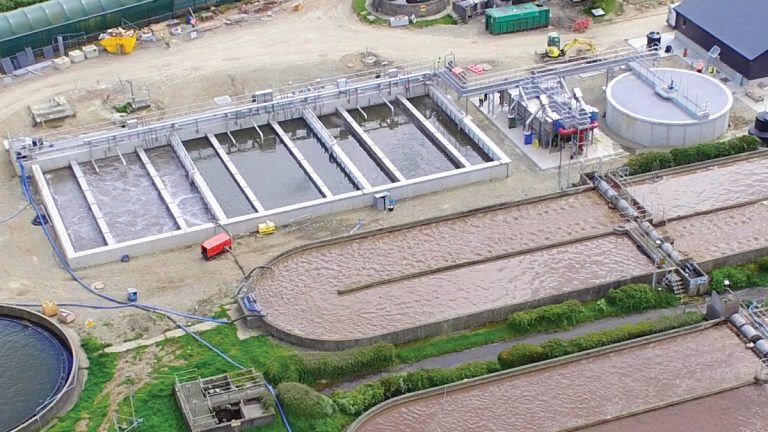
Nereda® Clonakilty WwTP, Ireland’s first WWTP using Nereda technology – Courtesy of Mark Cliffe, Aerial Photography
The learning and expertise from these Irish projects, and others around the world, is being actively used in the delivery of early schemes in the UK, de-risking solutions and driving efficiency for the benefit of UK water companies.
Further developments – Alginate recovery
Research at TU Delft uncovered the ability to extract alginate-like exopolysaccharides (ALE) from aerobic granular sludge (Lin et al, 2010). Alginate is currently produced from seaweed at relatively high costs and is used in a variety of industries as a thickener or gel and as a basis for coatings. Aerobic granular sludge has been found to contain between 15 to 25% of ALE.
Extracted ALE could potentially be used in the chemical sector, textile and paper industries (van der Roest et al, 2015). The recovery of ALE from Nereda® excess sludge (aerobic granular sludge) is a potential reuse opportunity, whereby a waste stream could be converted into a product with a high resale value. Combining alginate extraction with the existing excess sludge treatment processes at wastewater treatment plants could also improve sludge treatment efficiency because alginate extraction reduces sludge volumes and the remaining sludge has a higher digestibility and improved dewatering characteristics.
The National Alginate Research Programme (NAOP) has been set up in The Netherlands to further research and develop this promising sustainable reuse concept. The NAOP is a public-private sector collaborative research initiative with the goal of developing sustainable and commercially viable ALE-extraction from Nereda®excess sludge (van der Roest et al, 2015). The NAOP is similar to the public-private collaborative partnership that successfully developed Nereda®. Currently a pilot study is being carried out and demonstration projects will be operational in 2017.
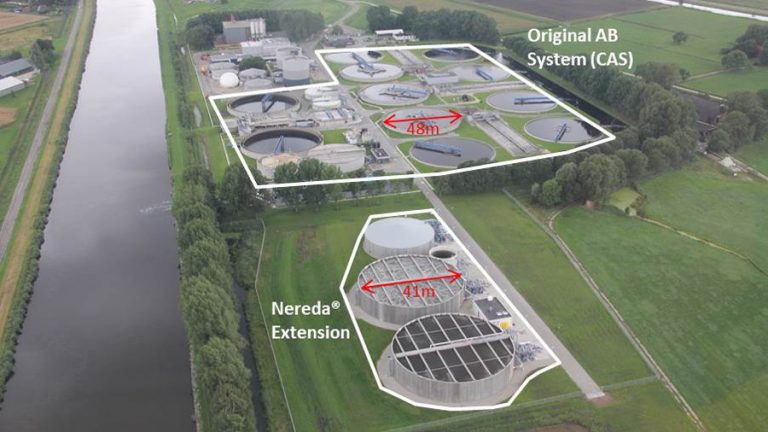
Nereda® Garmerwolde WwTP (Netherlands). 50% energy savings compared to parallel A/B. The 2 (No.) Nereda® tanks treat approx. 50% of the sewage. The existing AB-system in the back the other 50% – Courtesy of Water Authority Noorderzijlvest
Where it all started
In the early 1990s, lab-scale research at the Delft University of Technology (TU Delft), showed that aerobic granular sludge could be formed under a variety of conditions and that granular sludge could be used to achieve stable biological COD, phosphorus and nitrogen removal (de Kreuk et al, 2007). A collaborative public-private partnership was set up involving TU Delft, Royal HaskoningDHV, several Dutch District Water Authorities and STOWA (the Dutch Foundation for Applied Water Research). This partnership led to the development of the Nereda® wastewater treatment system, which is a full scale application of aerobic granular sludge technology.

(left) Nereda® reactor at Wemmershoek WwTP in South Africa discharging effluent and (right) Nereda® Kingaroy WwTP in Australia under construction. Opening end 2016 – Courtesy of Aquatec Maxcon
Conclusion
Full scale Nereda® plants have demonstrated reliable biological phosphorus removal consistently to levels of less than 1mg/l, down to less than 0.2mg/l. Similarly treated water ammonia concentrations are of less than 1mg/l have been demonstrated together with total nitrogen levels of less than 5mg/l.
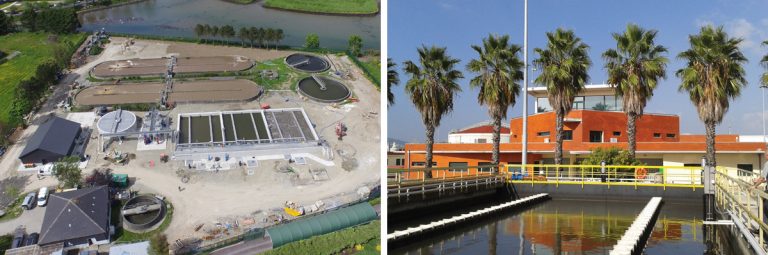
(left) Nereda® Deodoro WWTP in Rio de Janeiro, Brazil, officially opened in May 2016 – Courtesy of Américo Vermelho and (right) Nereda® Frielas, Lisbon, Portugal. Although using only 9% of the total biological volume of the plant, the Nereda® technology will treat 25% of the total flow and produces effluent with a better quality. Nereda® Deodoro WWTP in Rio de Janeiro, Brazil, officially opened in May 2016 – Courtesy of Américo Vermelho
Low levels of SS and BOD can be achieved (less than 10mg/l) with the benefit of additional tertiary treatment. A wide range of applications have been developed using Nereda; these range from new standalone plants, uprating existing SBRs, replacing old filter works and hybrid applications, where a small Nereda® plant is installed alongside an existing activated sludge plant.
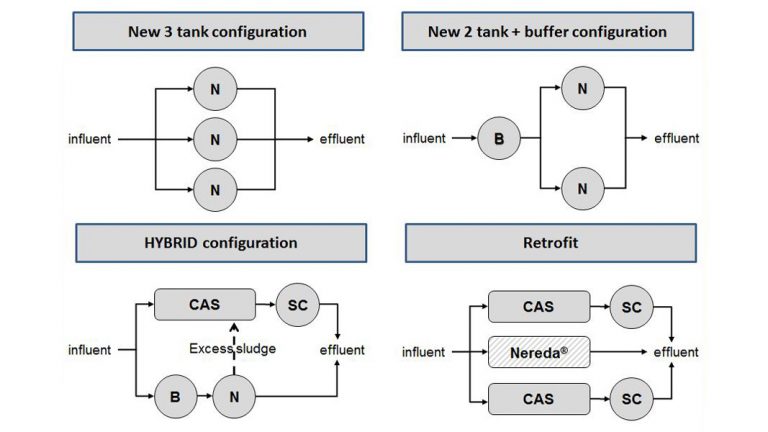
Nereda® configurations/approaches – Courtesy of Courtesy of Royal HaskoningDHV
Nereda® has proven to be a very compact design, allowing the installation of a new treatment plant, often within the boundaries of the existing works. Full scale Nereda® plants, such as those at Garmerwolde and Frielas have demonstrated power savings of 20-50% when compared to the existing adjacent conventional treatment plants. When combined with similar or lower capital cost for Nereda®, this represents significantly lower whole-life costs, without the high dependency on chemical dosing for phosphorus removal. Furthermore, if Nereda® is installed on a site with advanced digestion, this power saving opens the opportunity for power self-sufficient wastewater treatment.
Nereda® is now acquiring a growing reputation for setting new standards in efficient, compact and sustainable wastewater treatment.
This paper was prepared by Barry Oliver, Sales Director, and Andrew Thompson, Technical Manager, both with Royal HaskoningDHV.
For more information: Royal HaskoningDHV | +44 (0)121 709 6521 |www.nereda.net
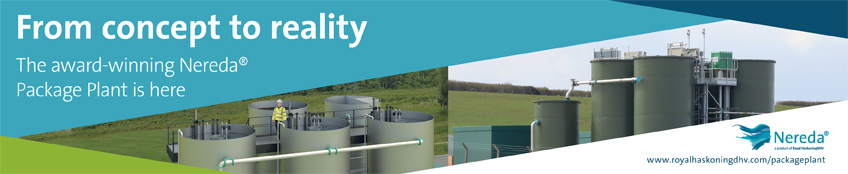
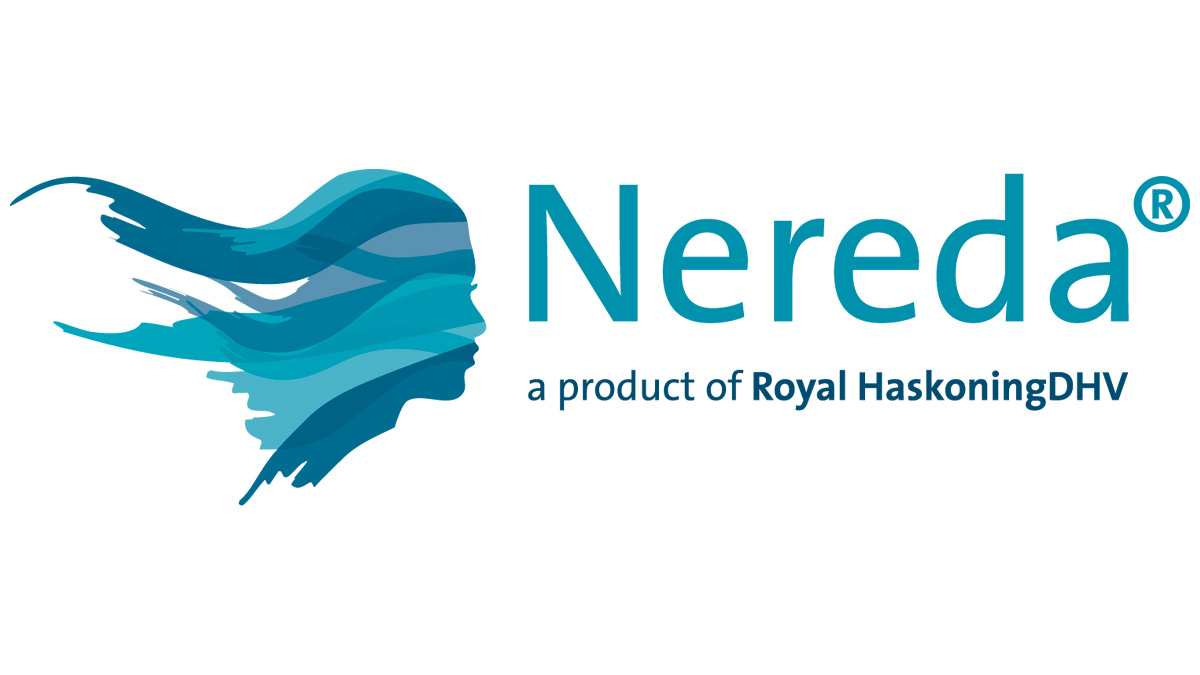
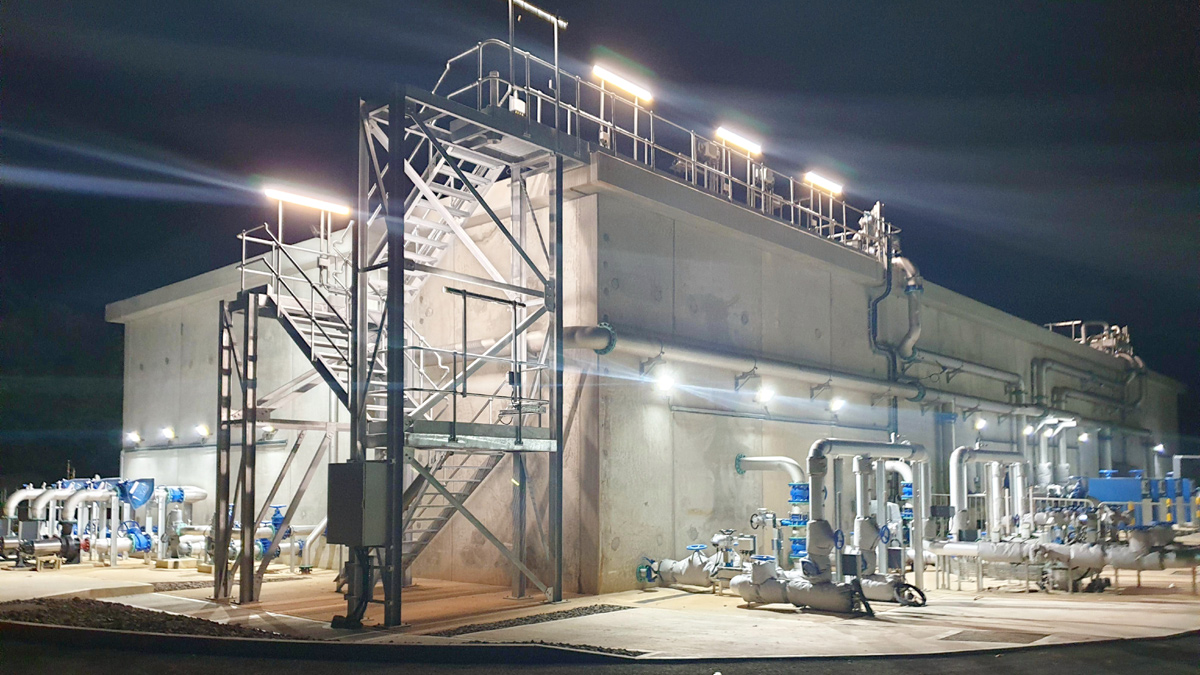
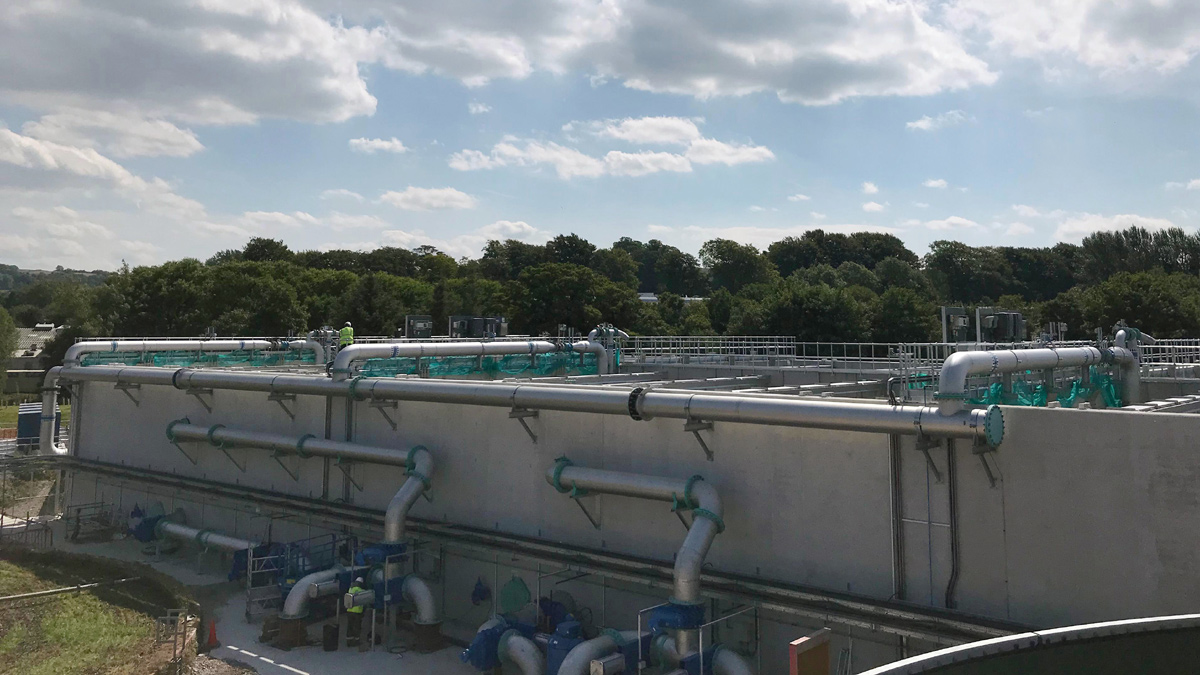
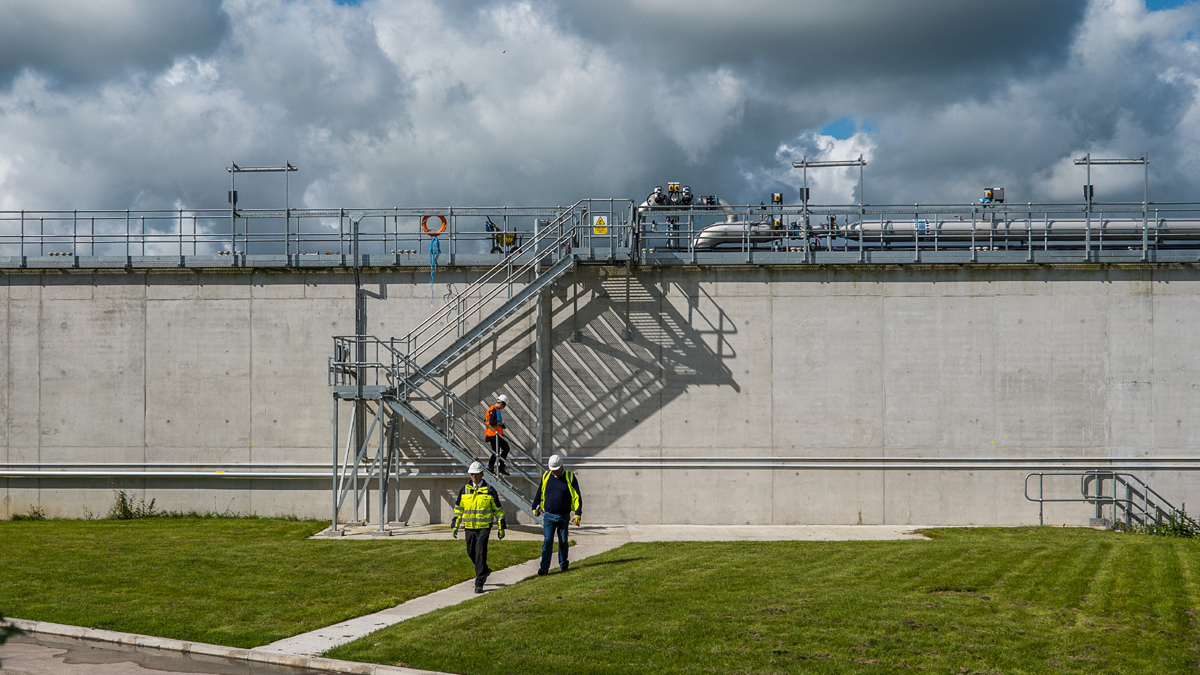
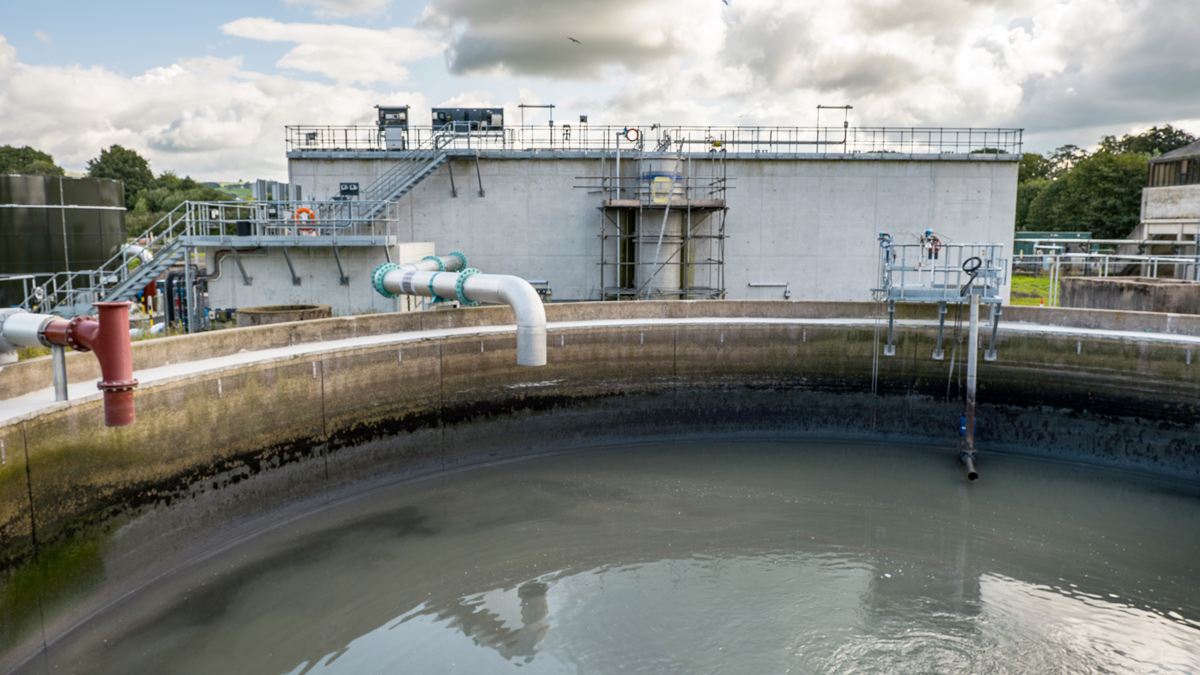
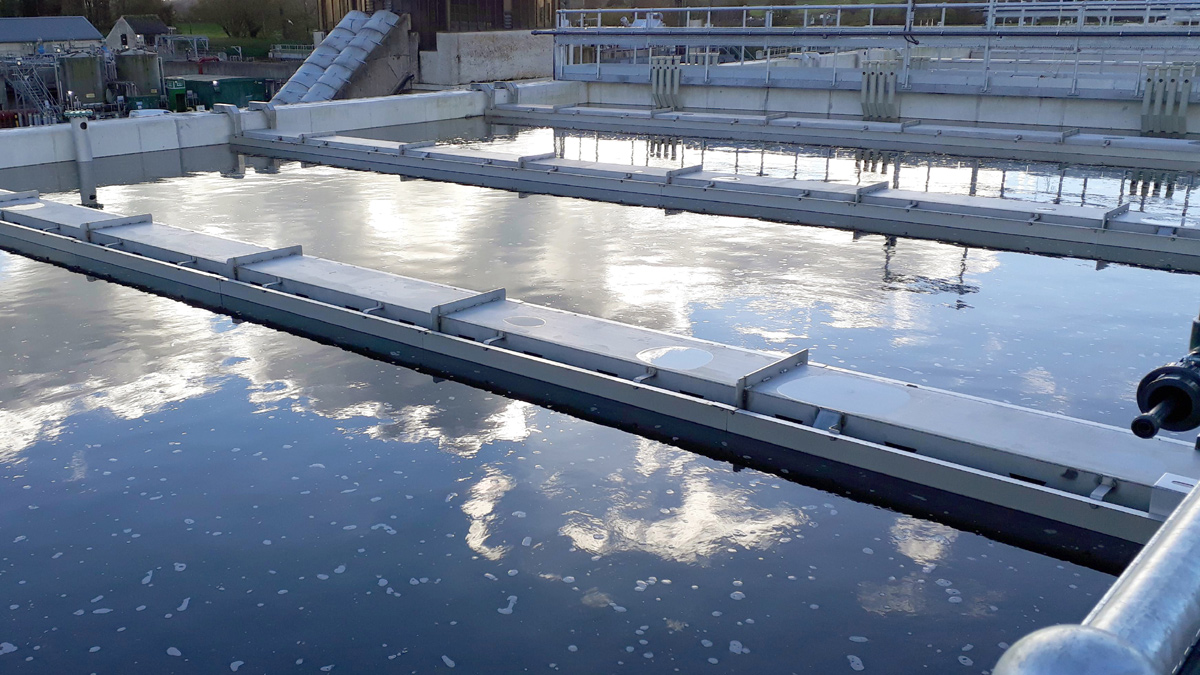
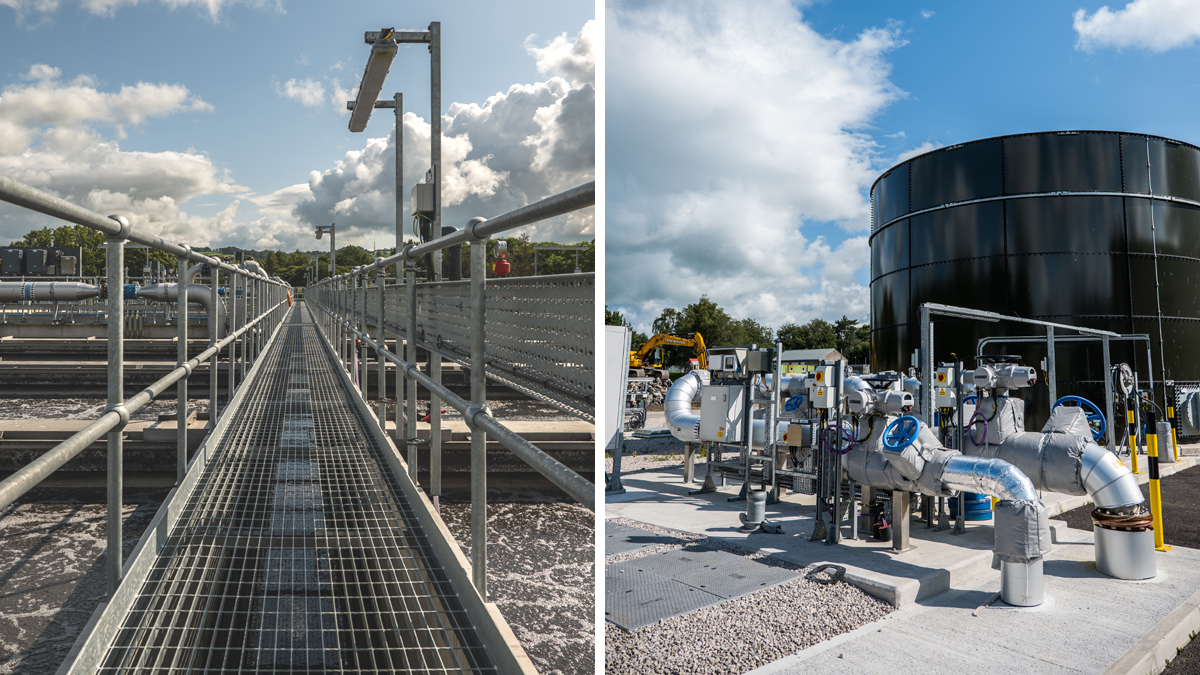
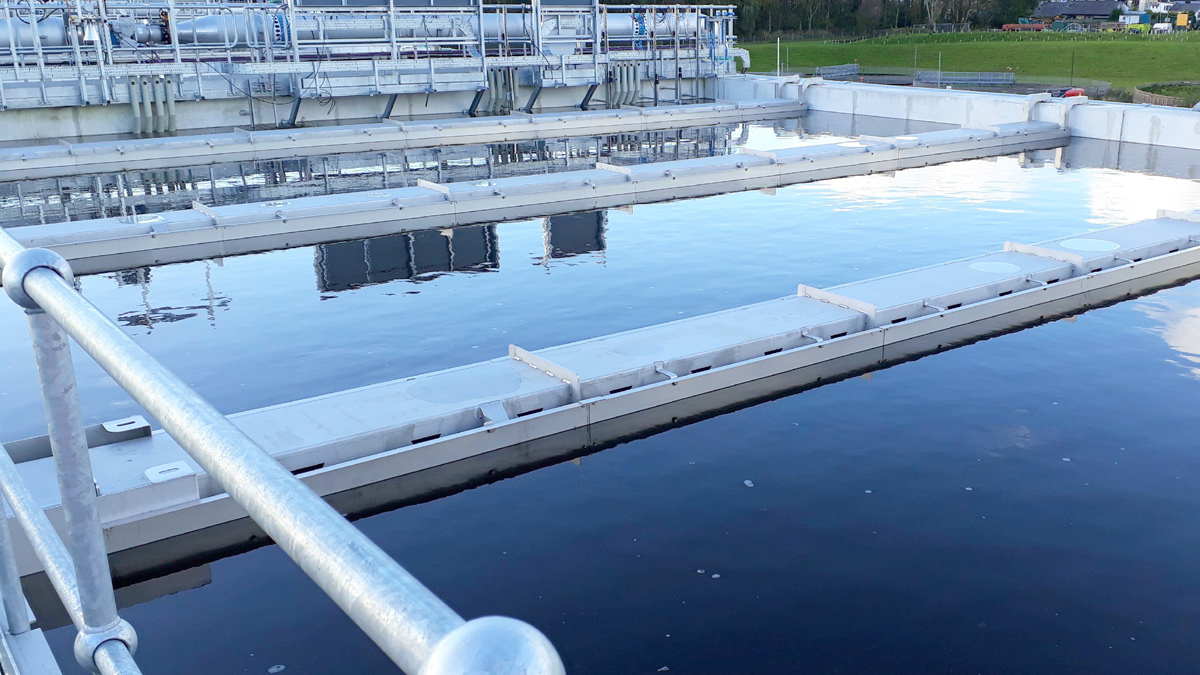
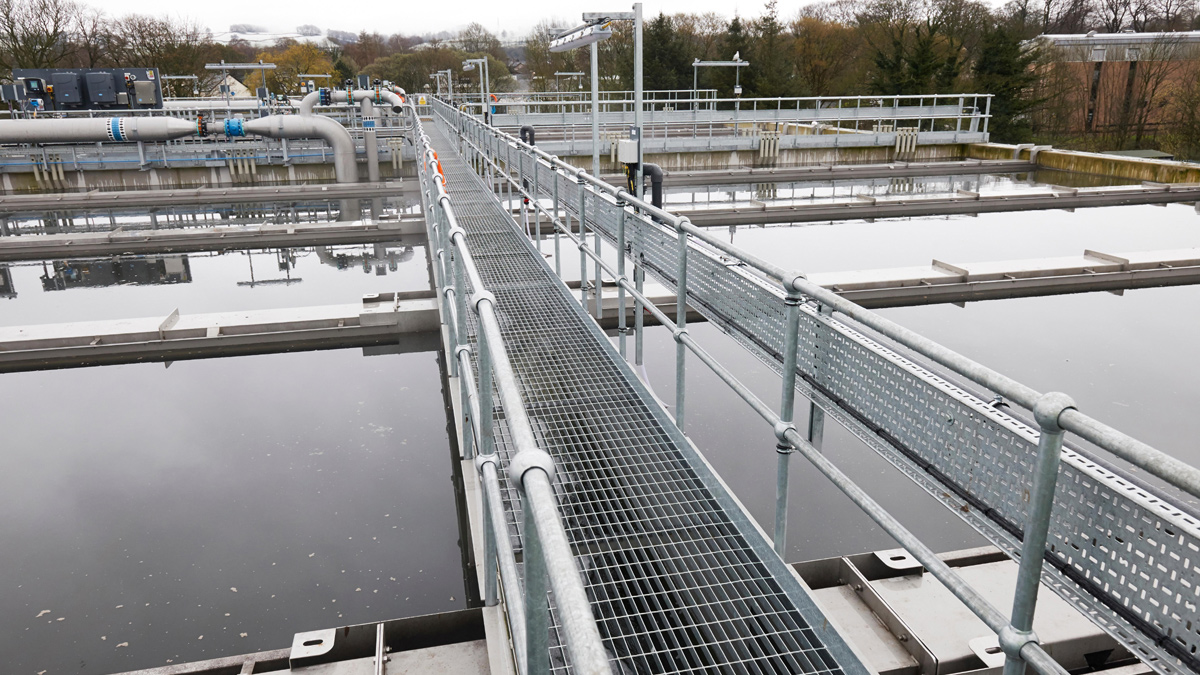
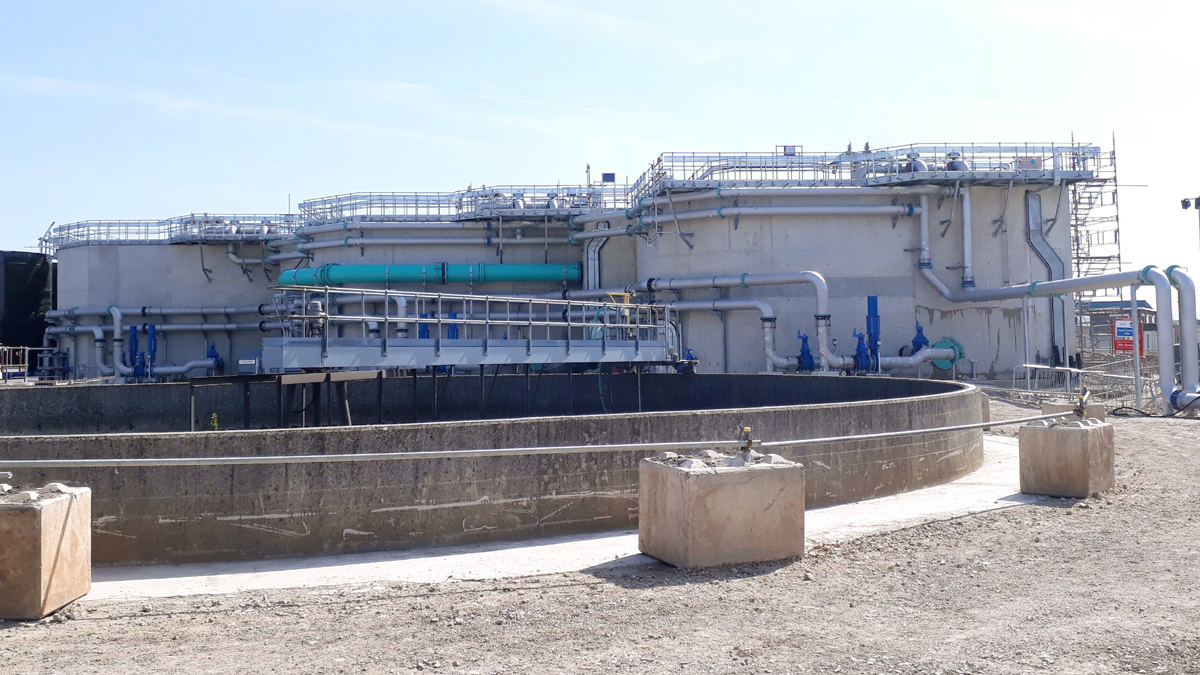
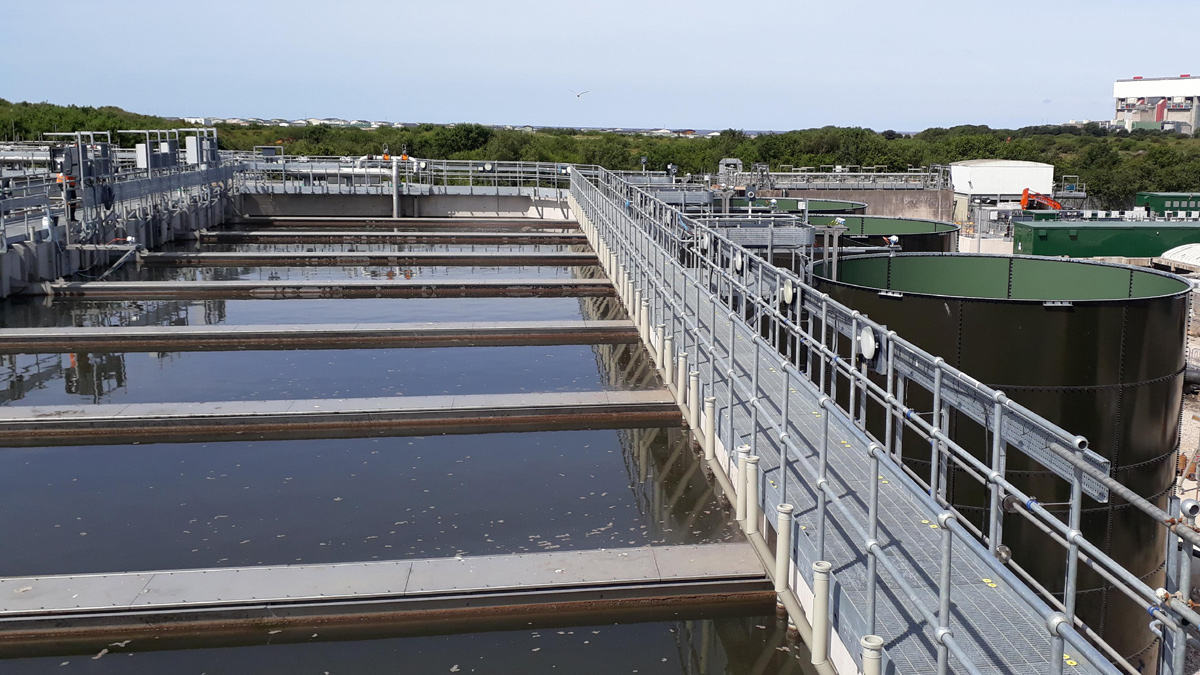
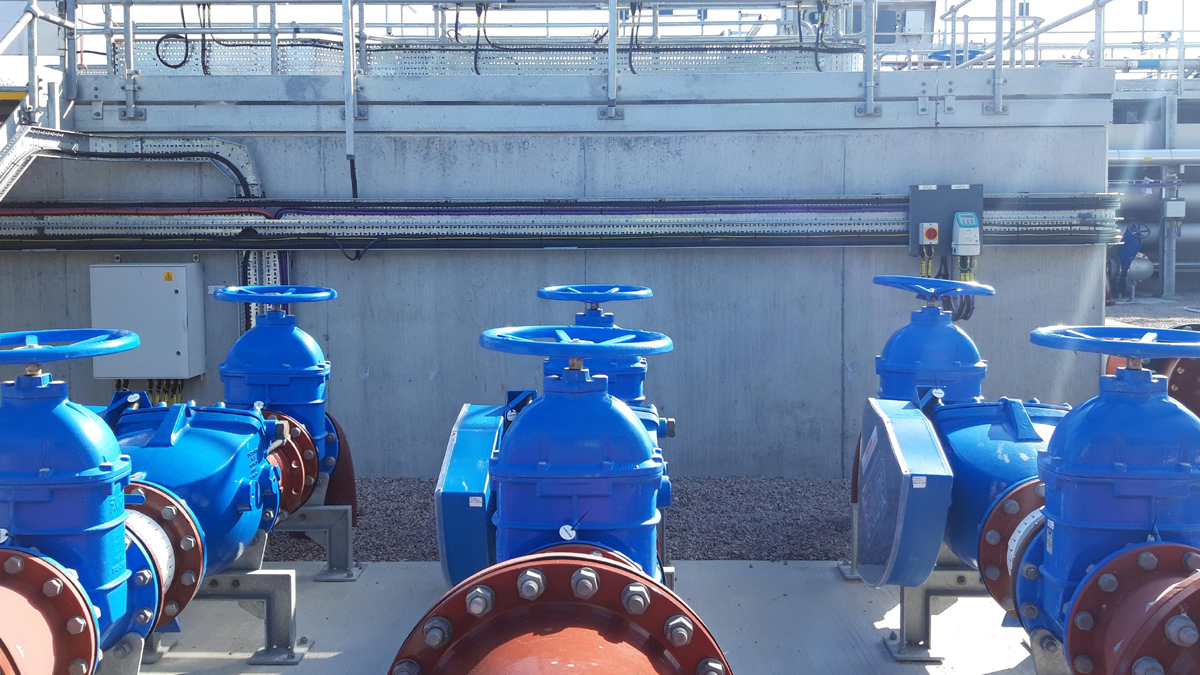
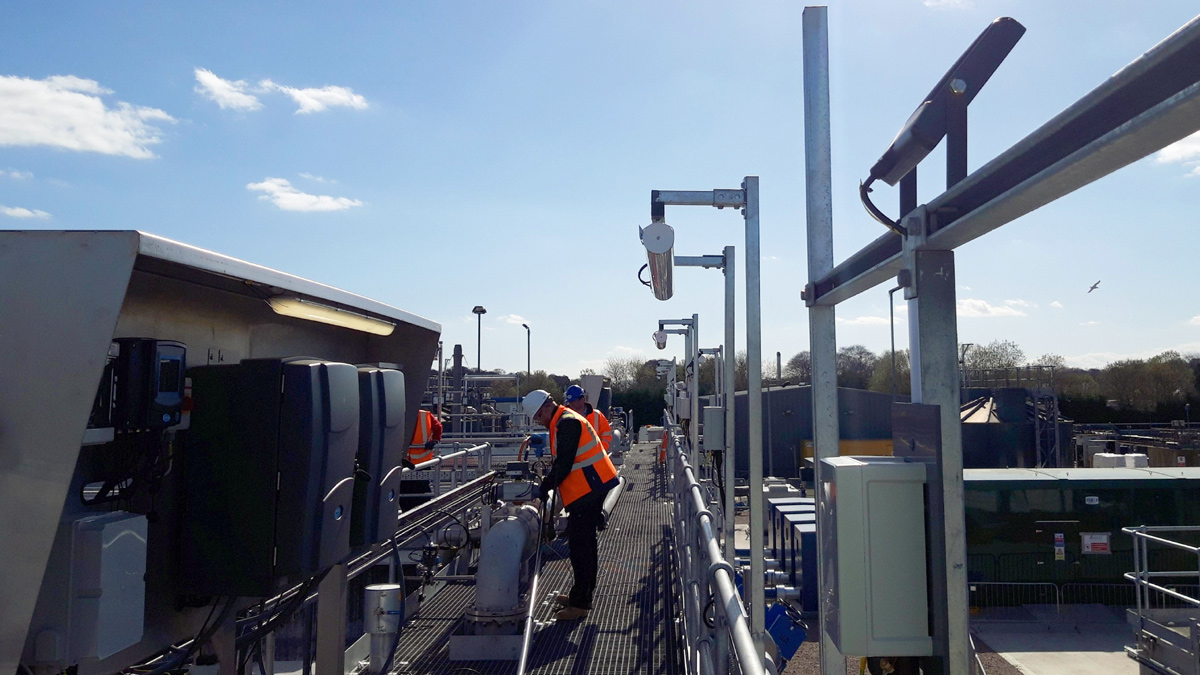
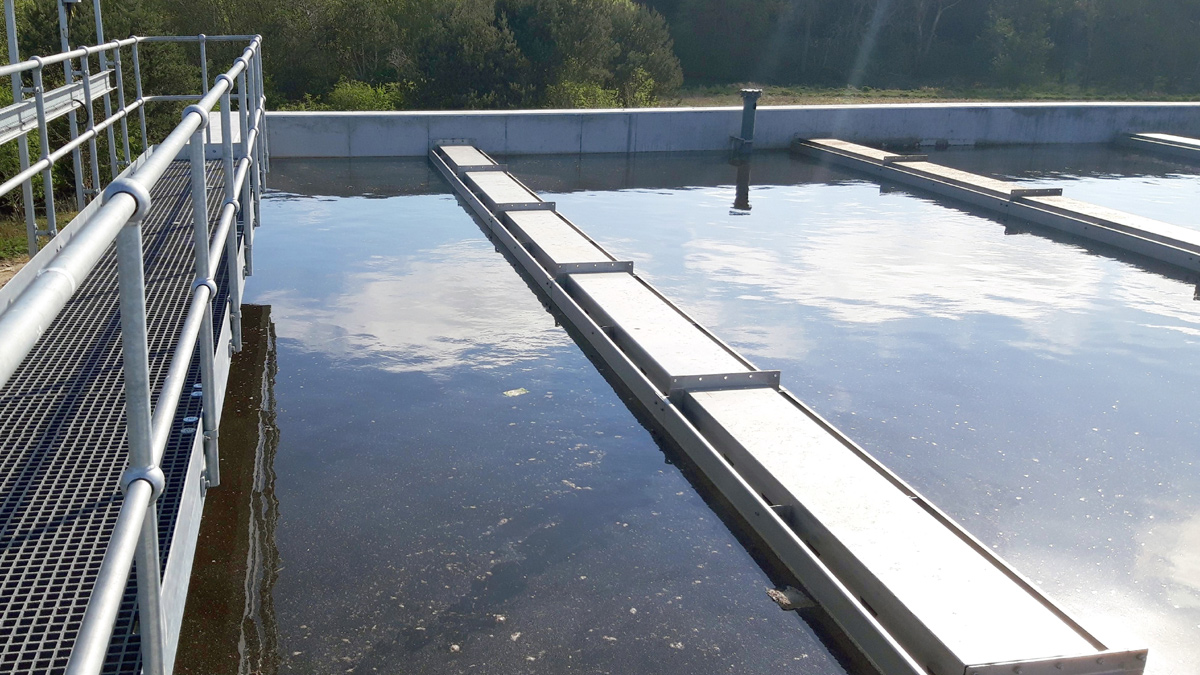
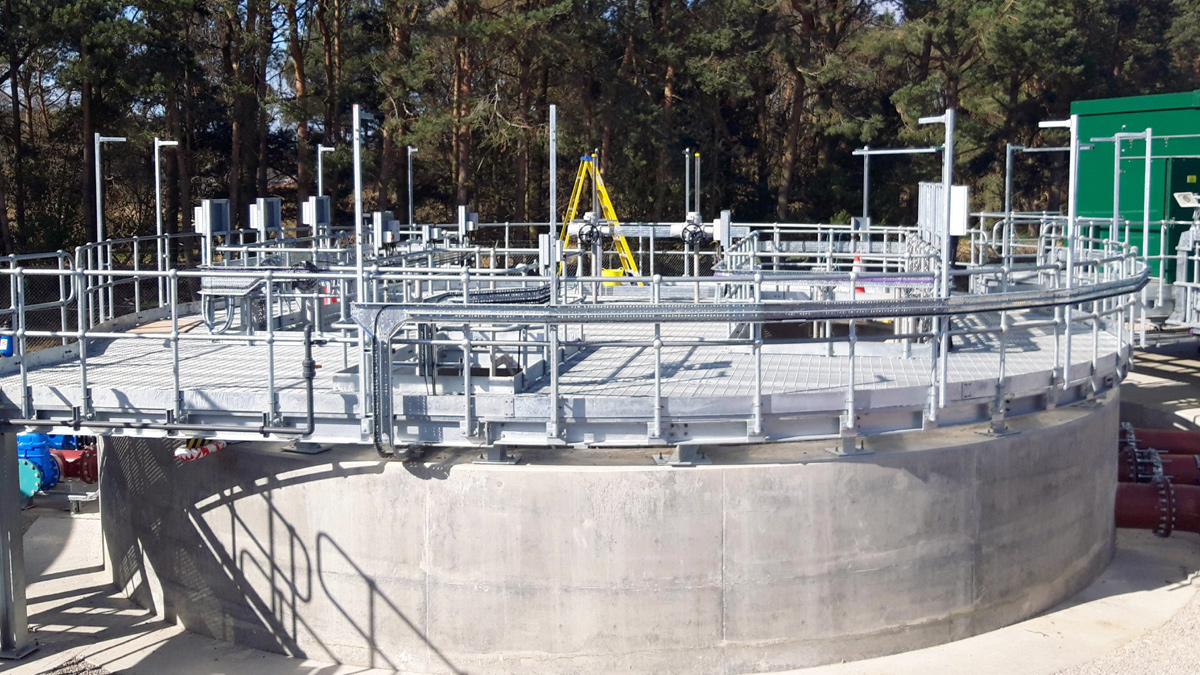
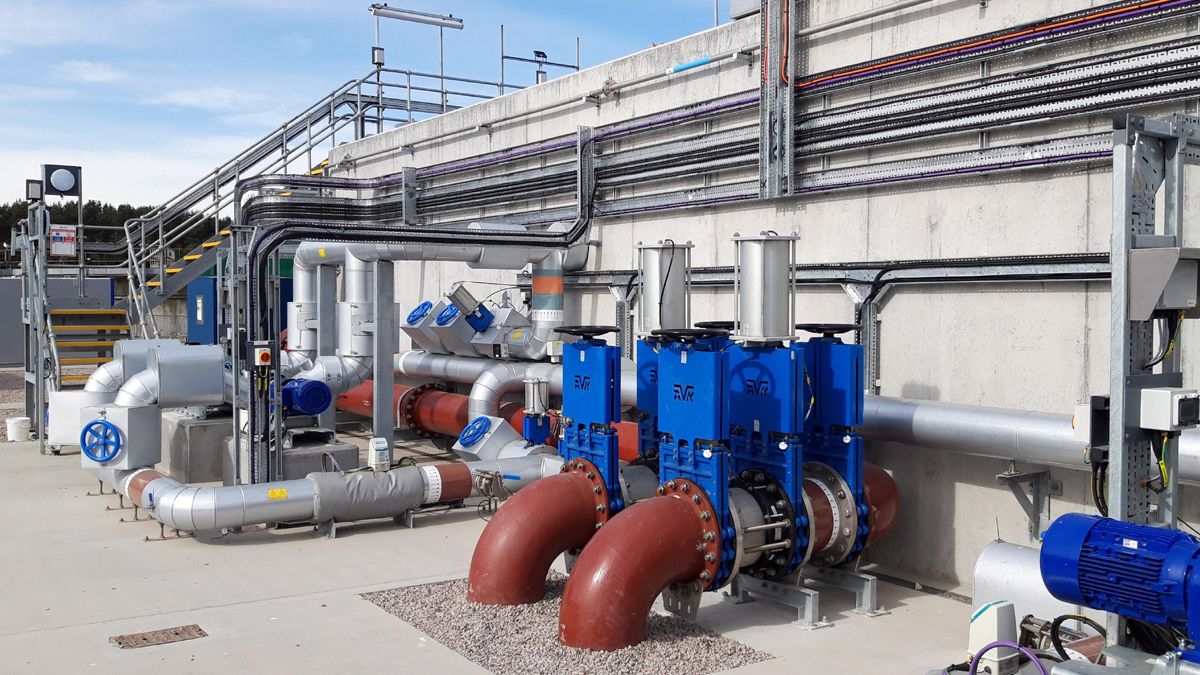
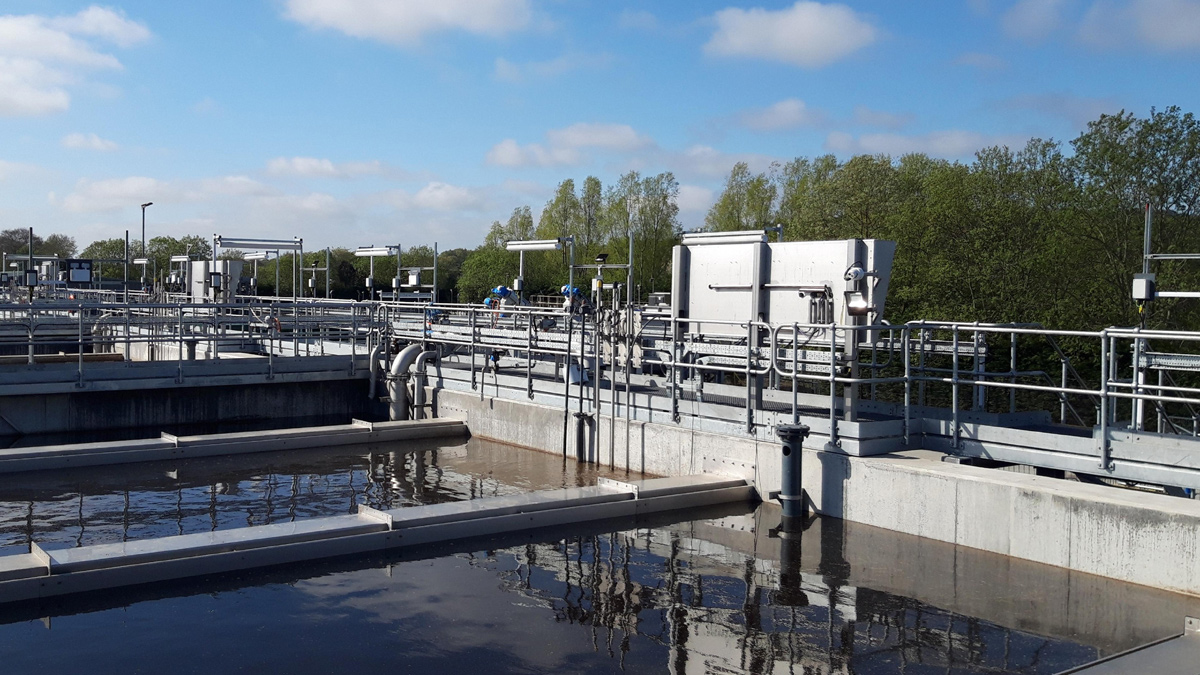
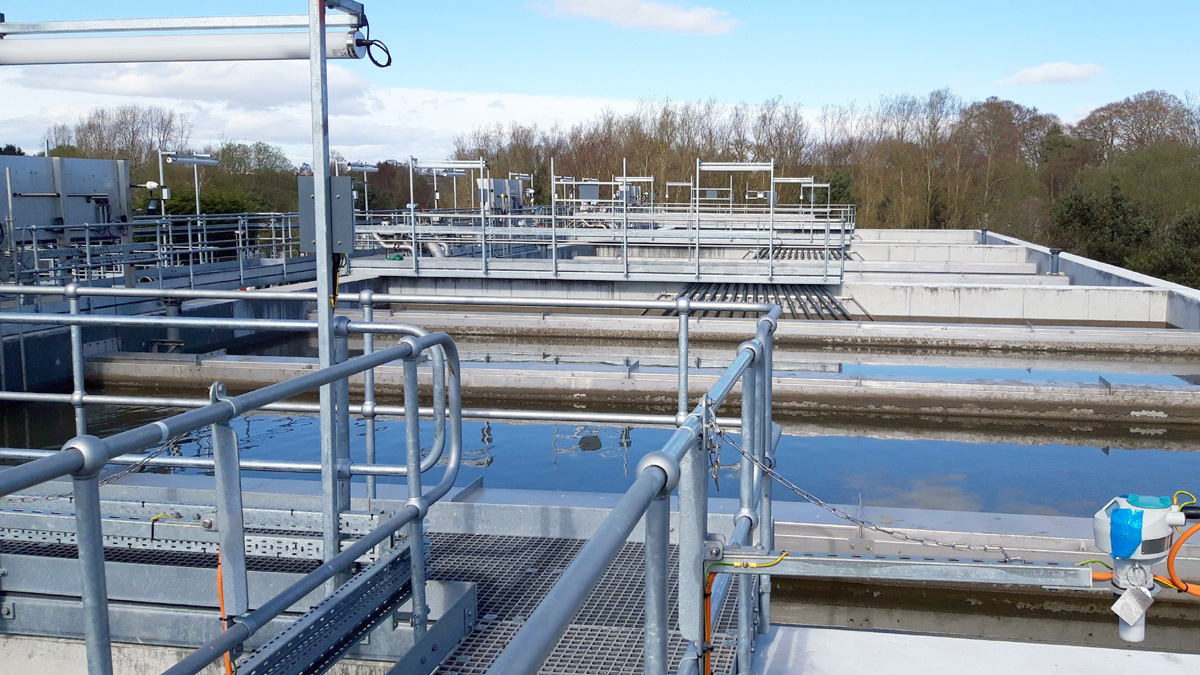
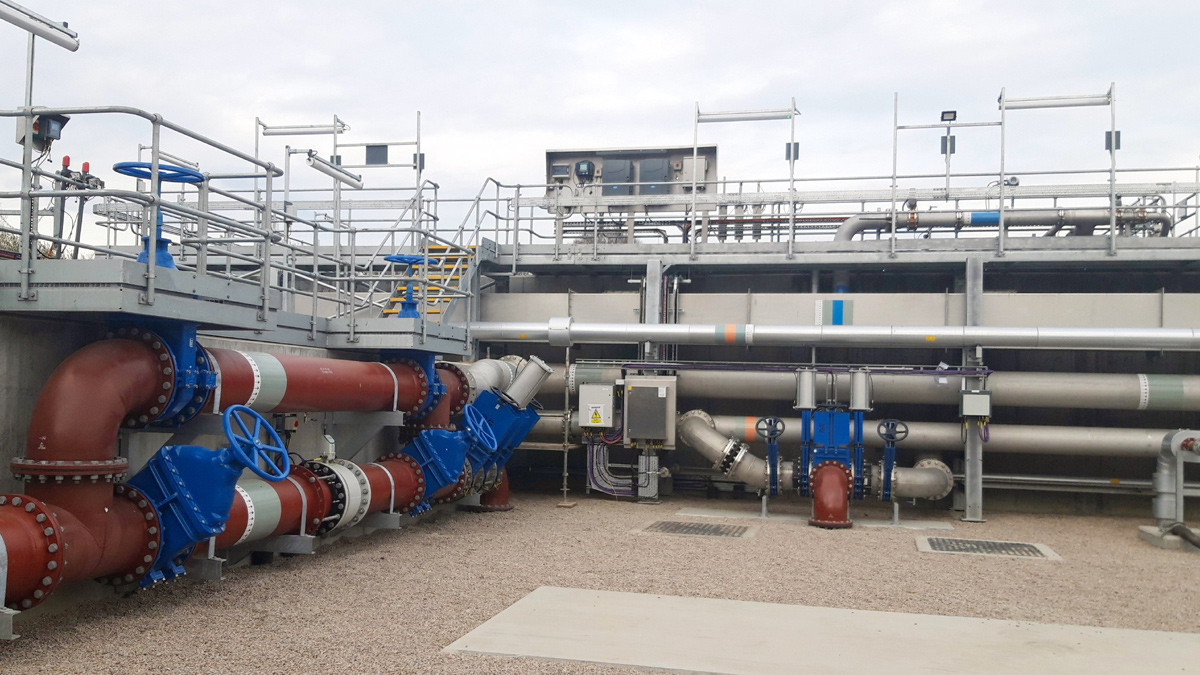
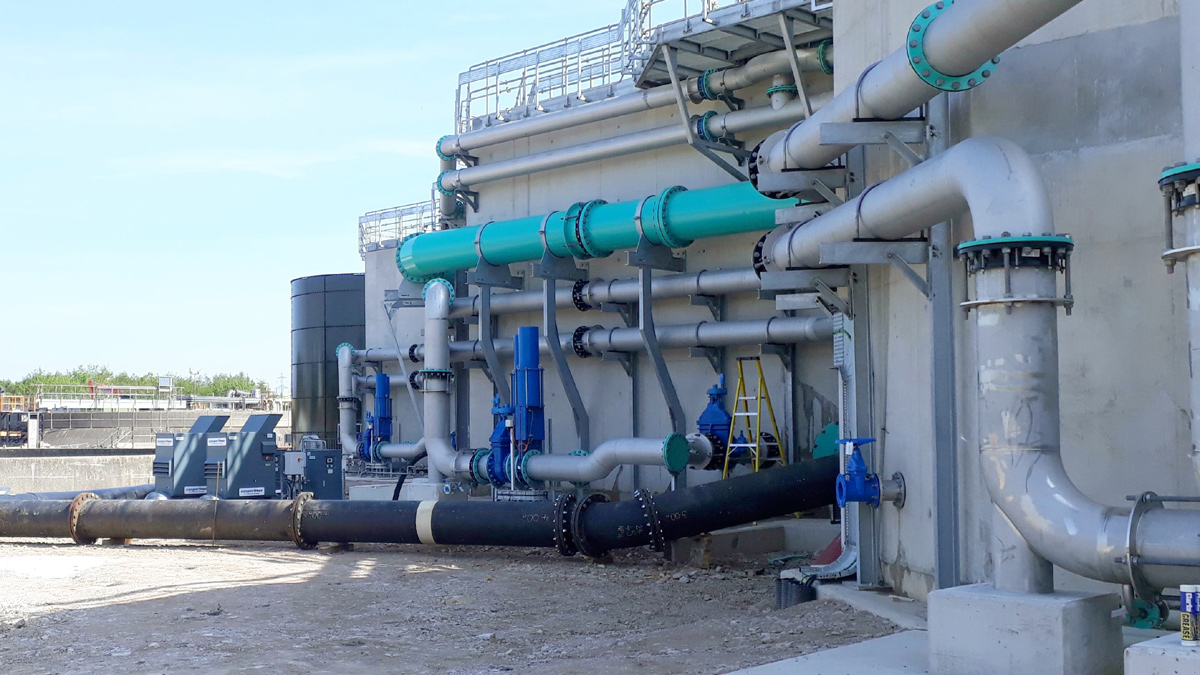
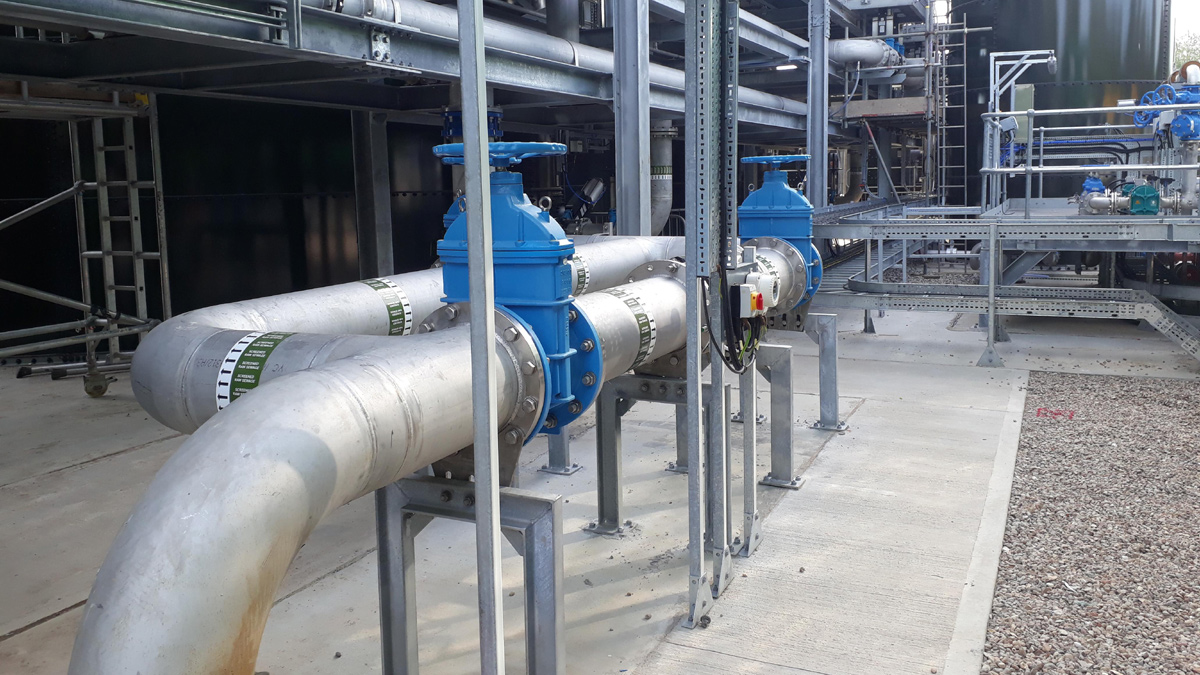

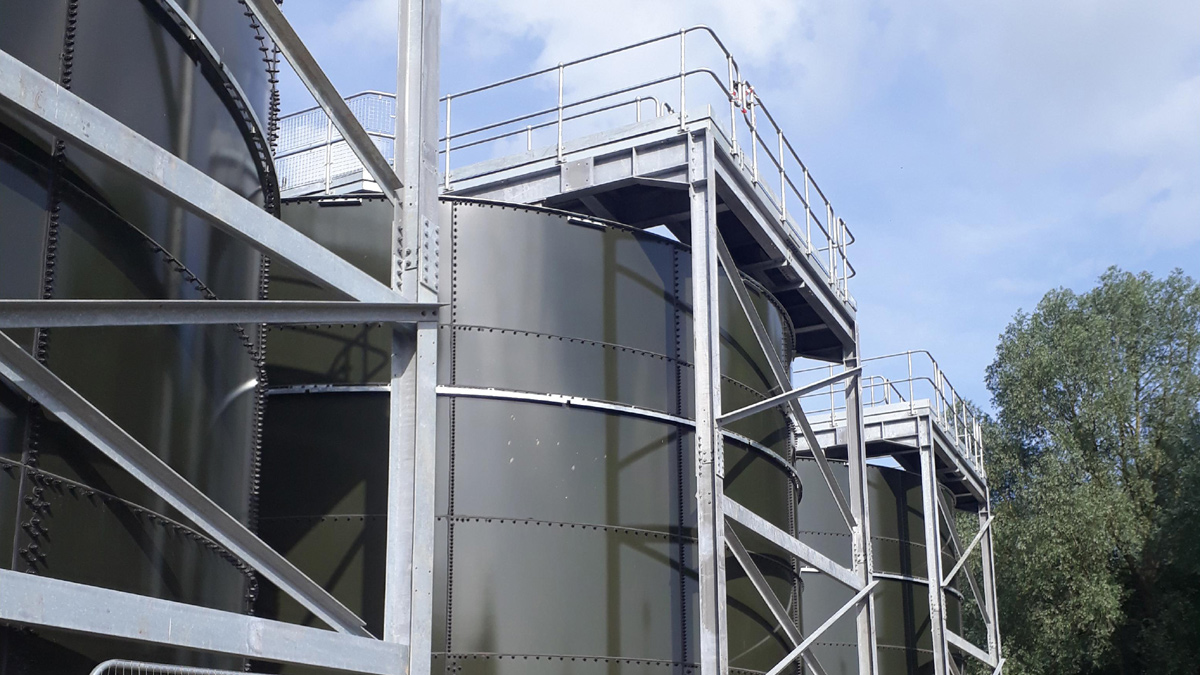
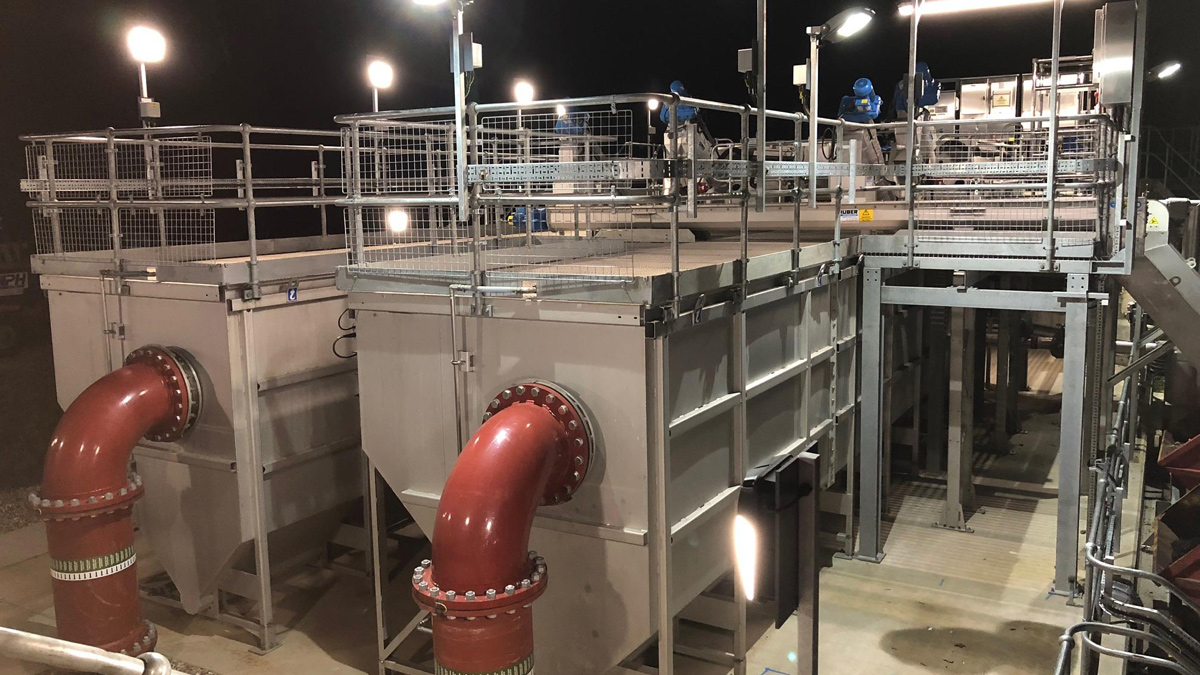
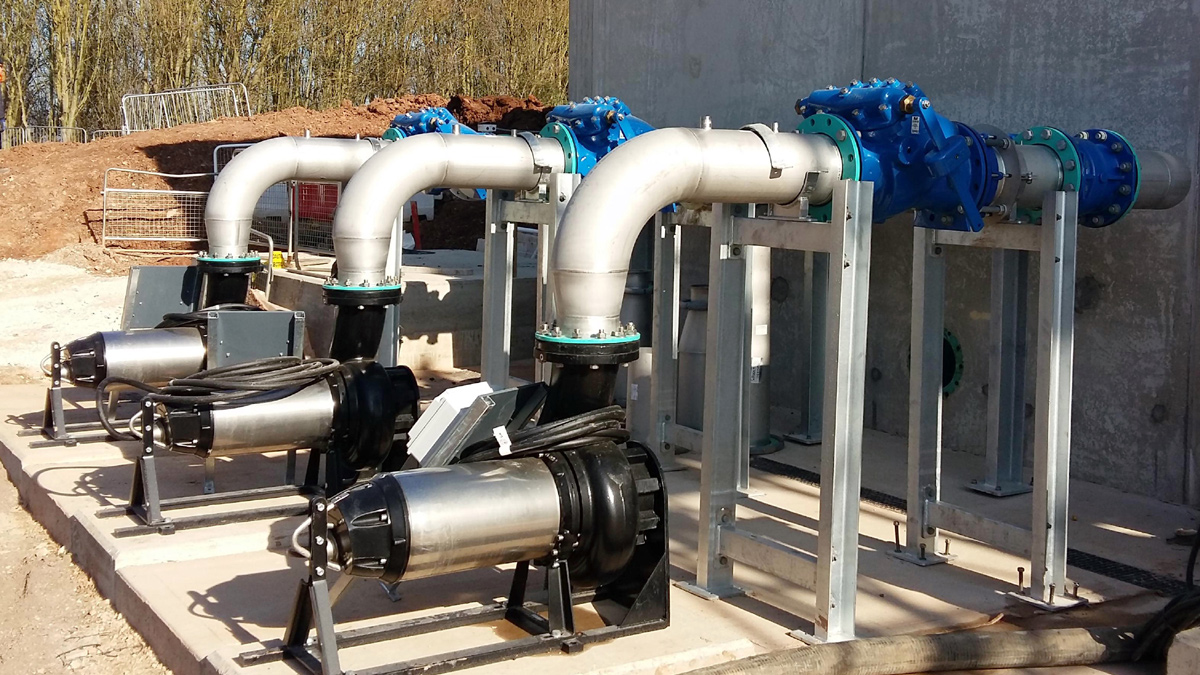
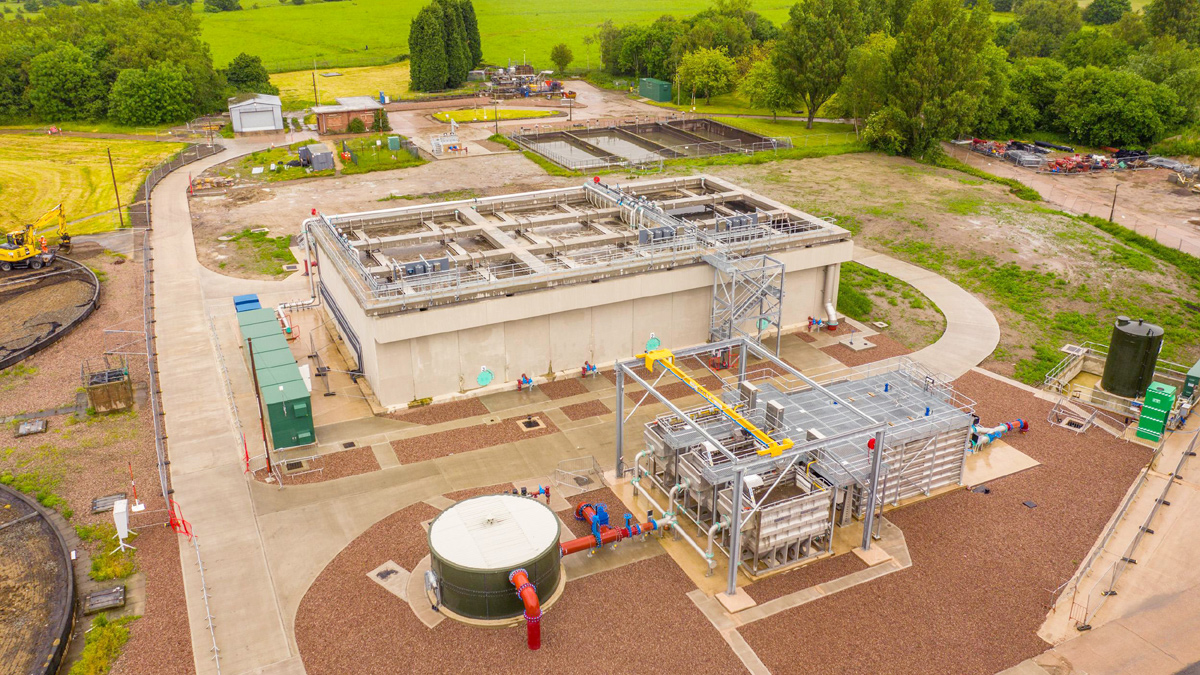
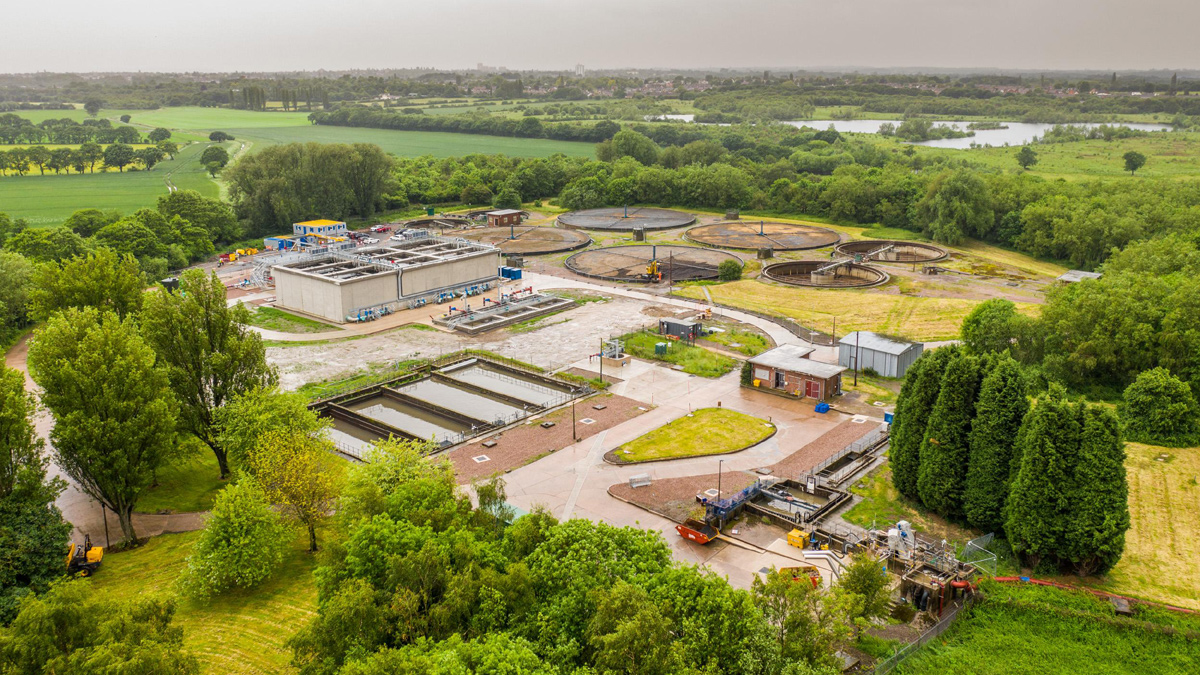
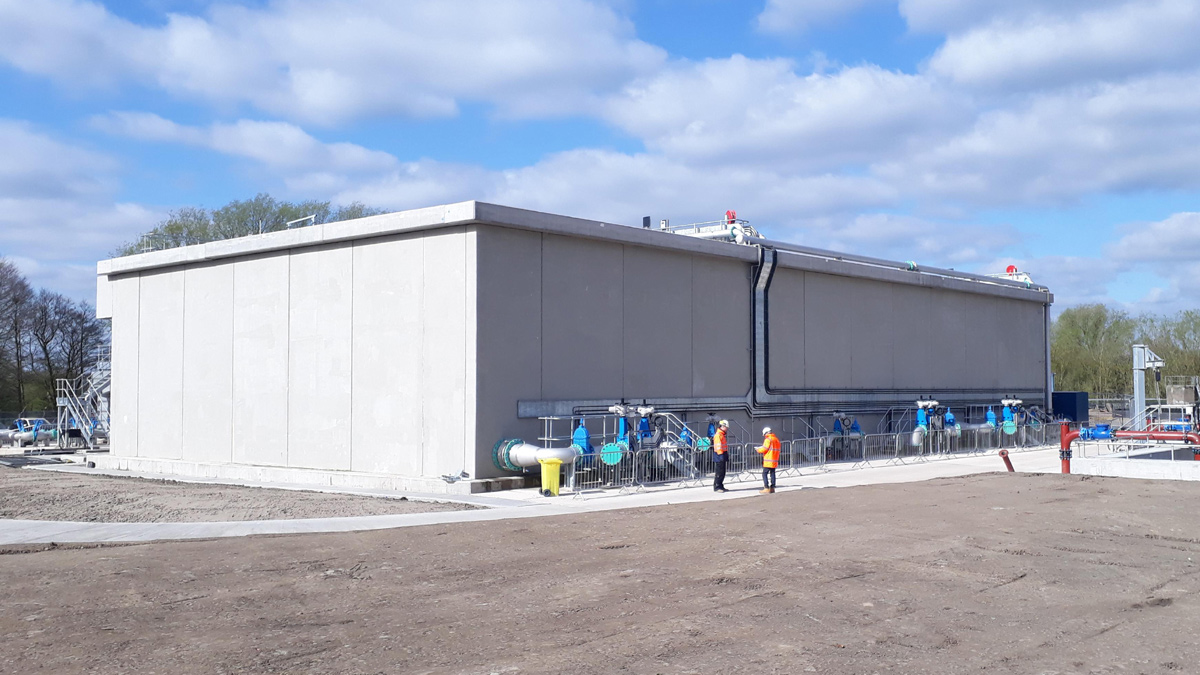
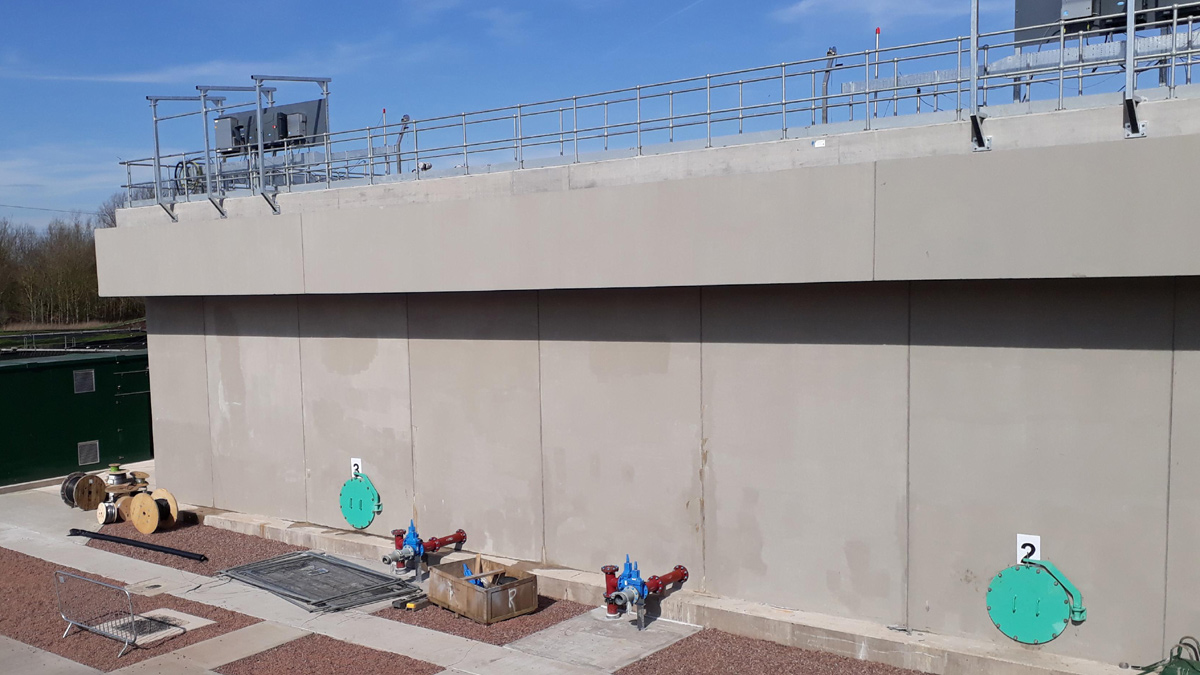
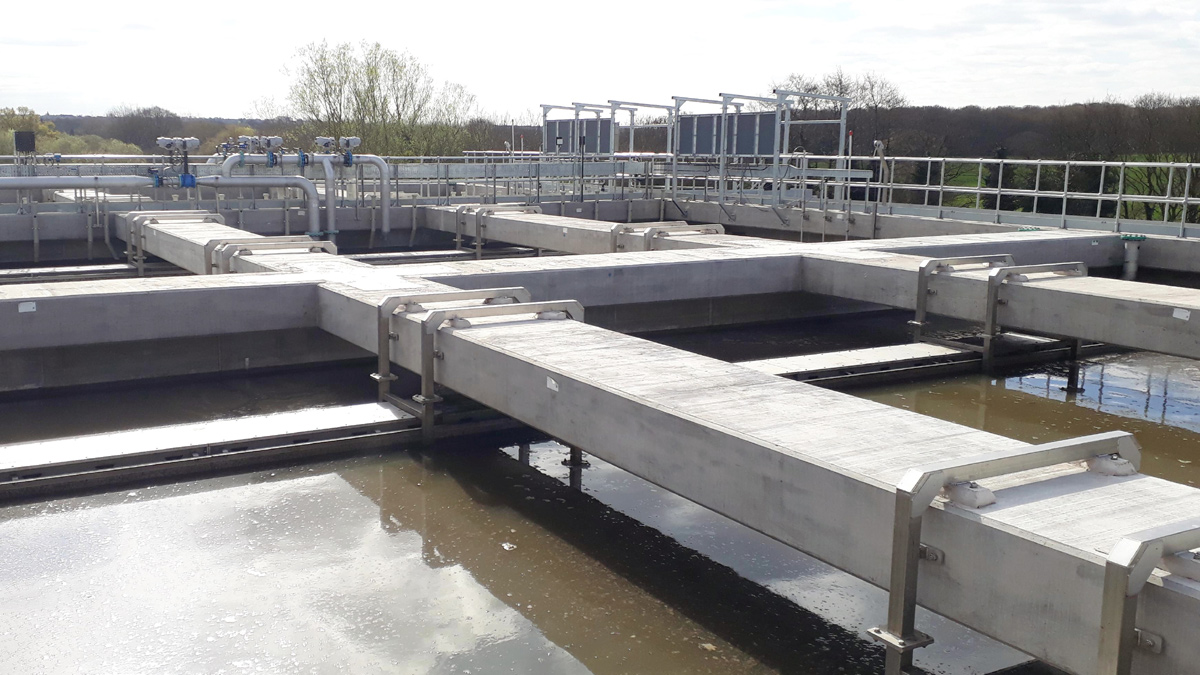
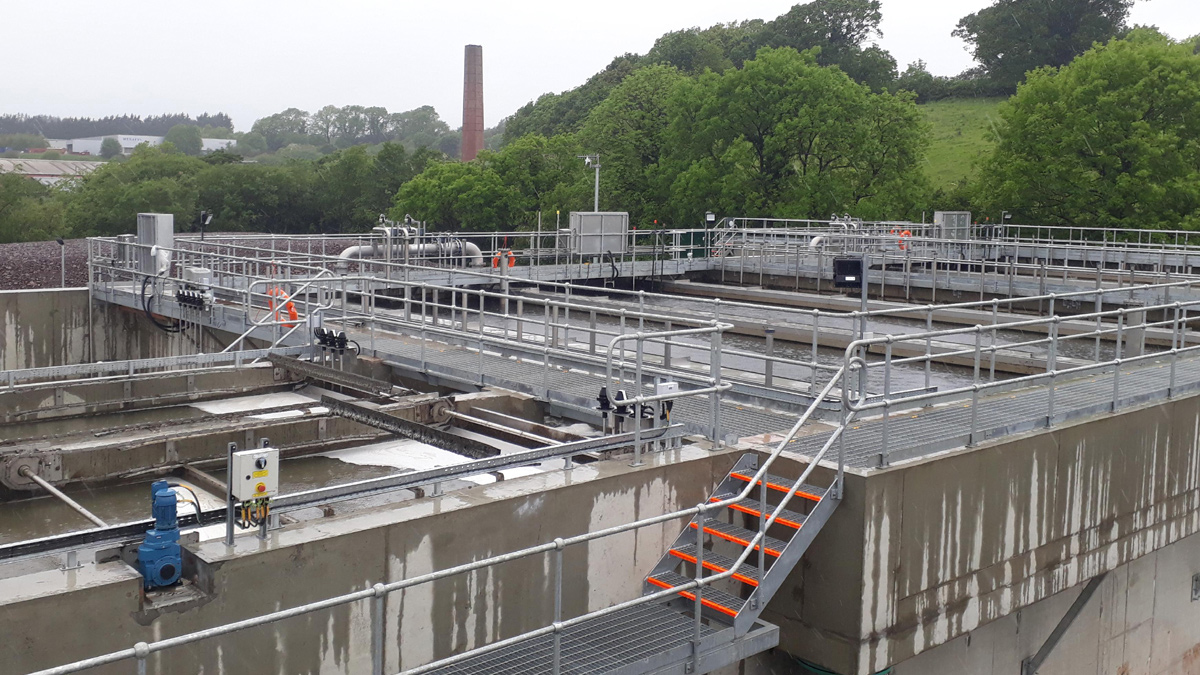
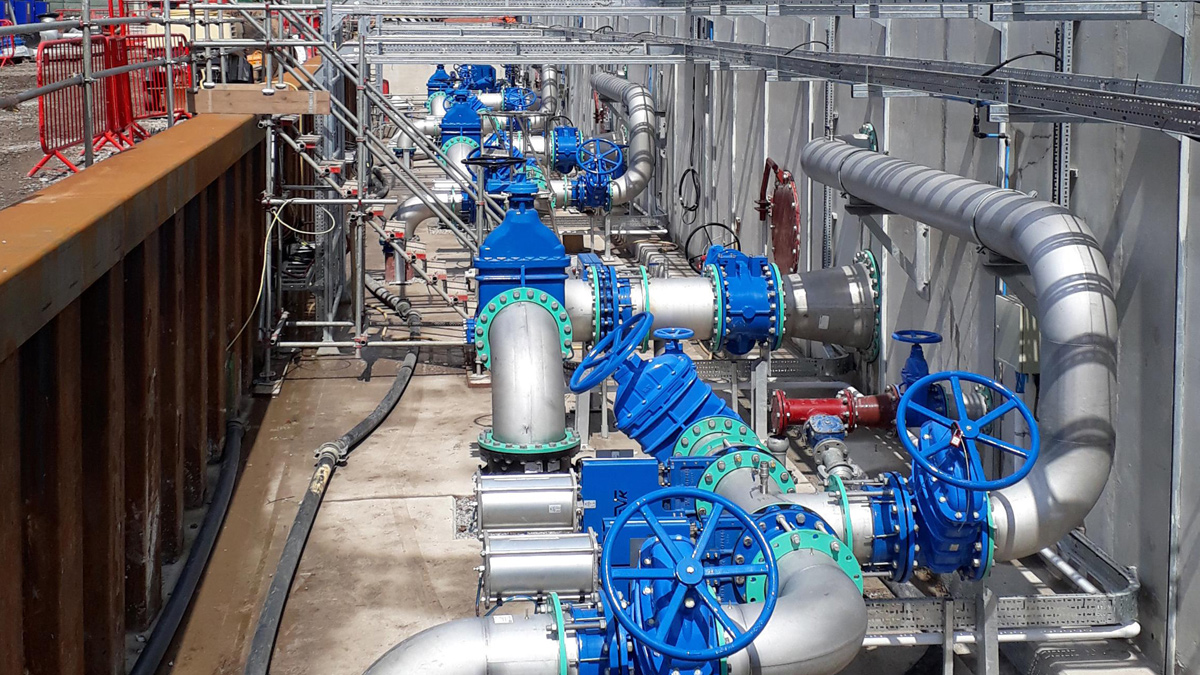
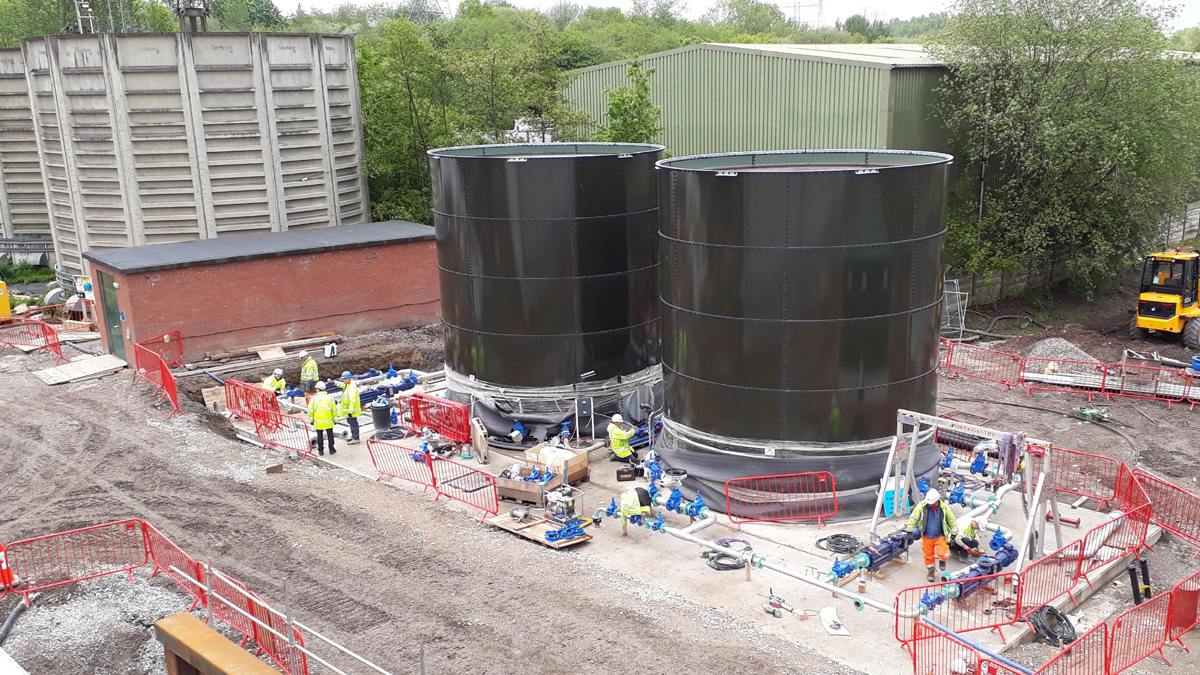
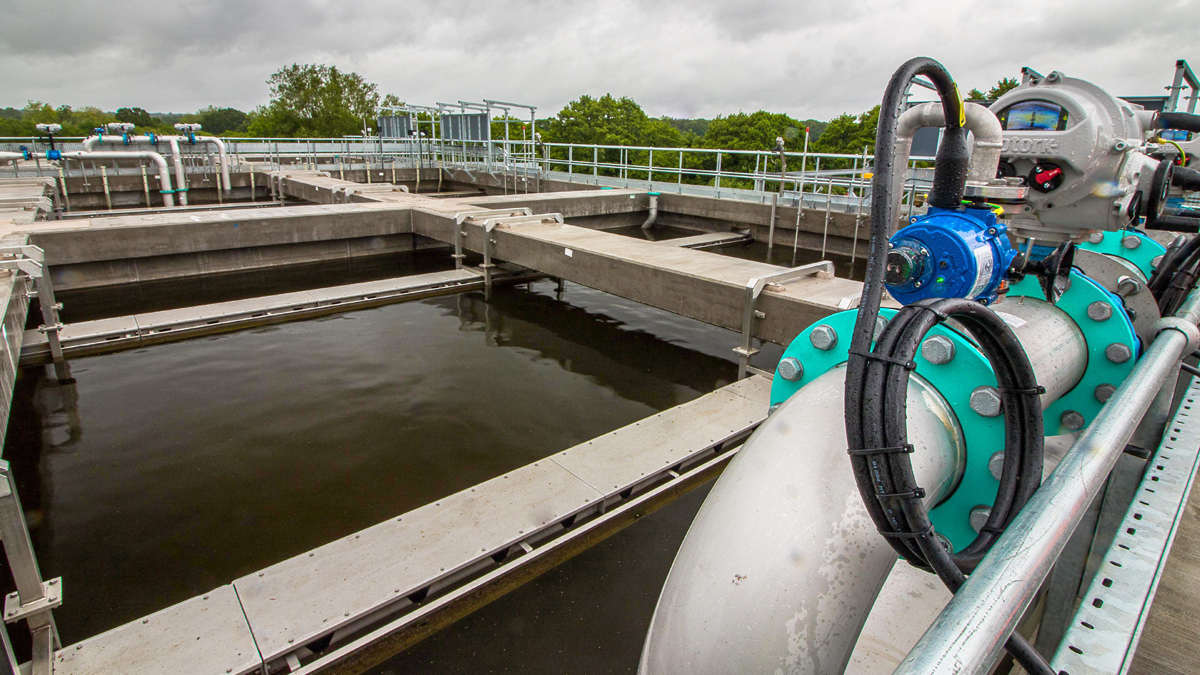
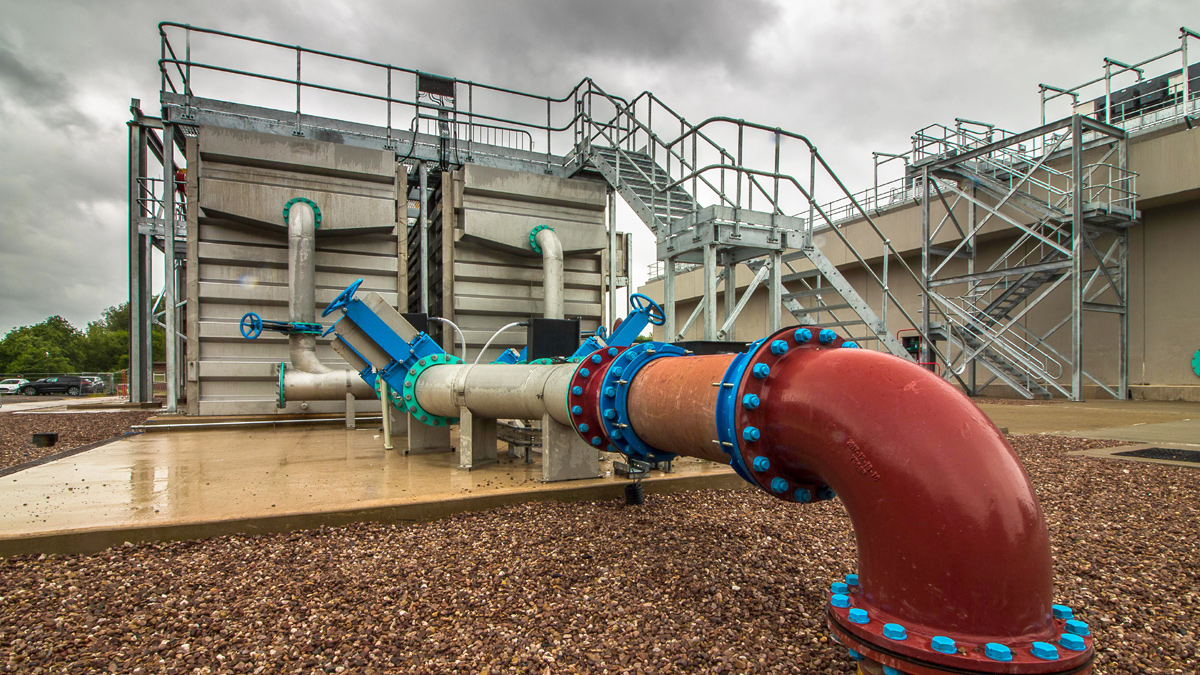
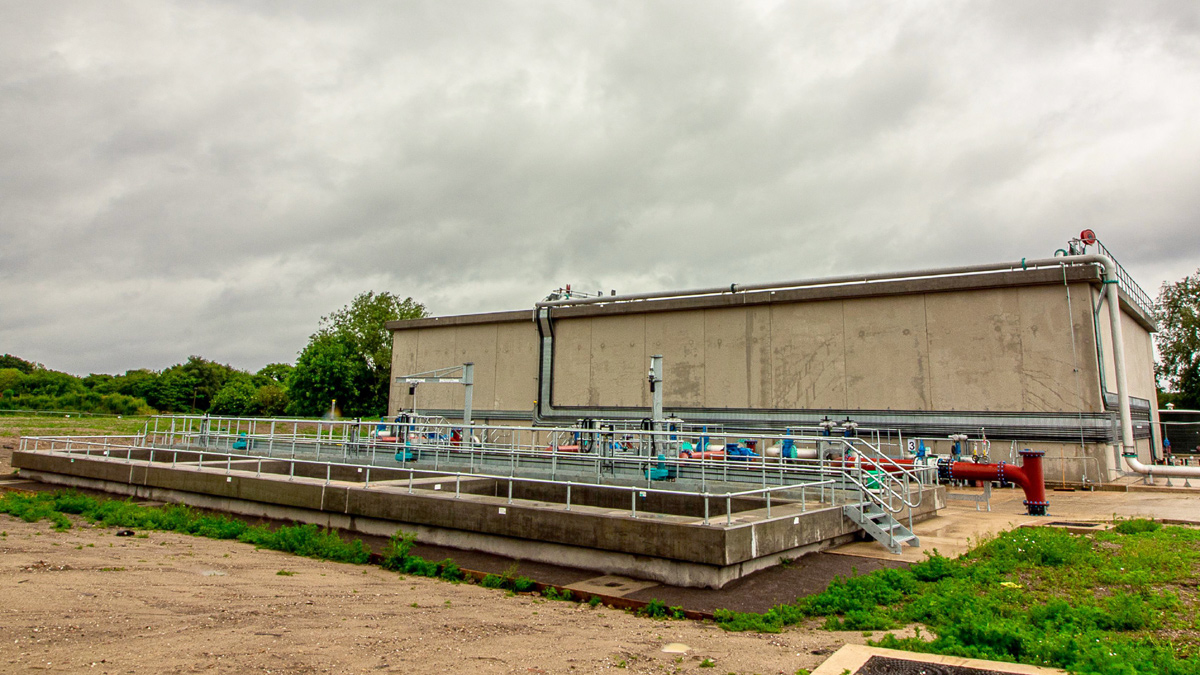
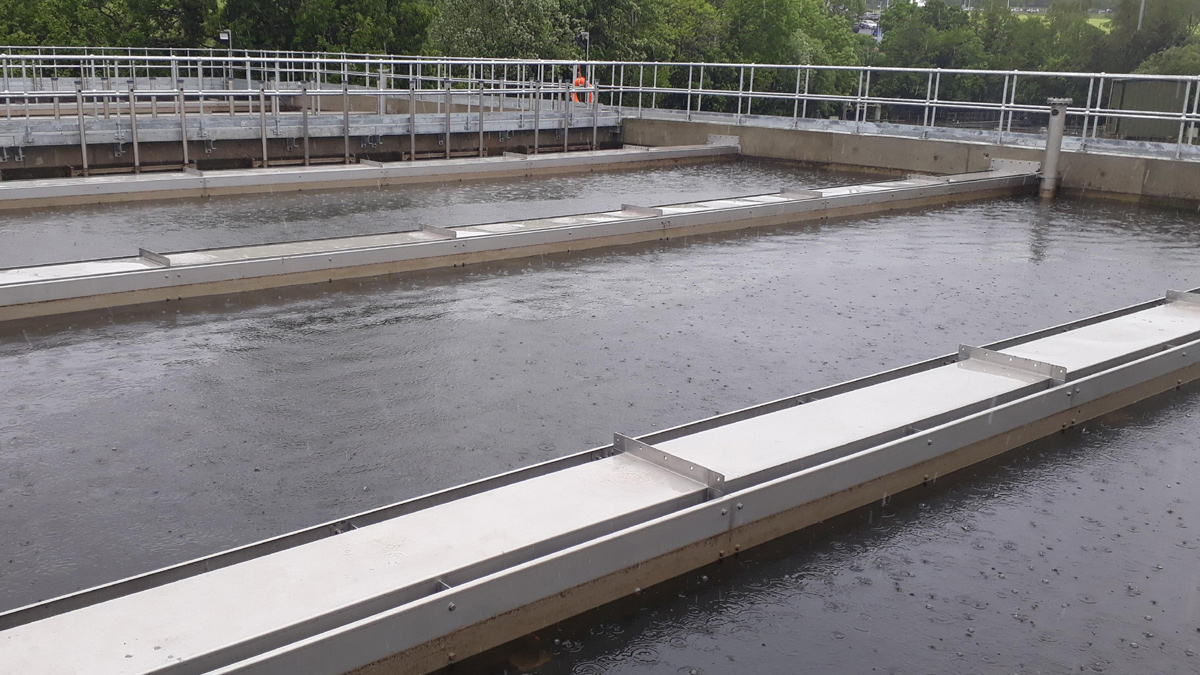
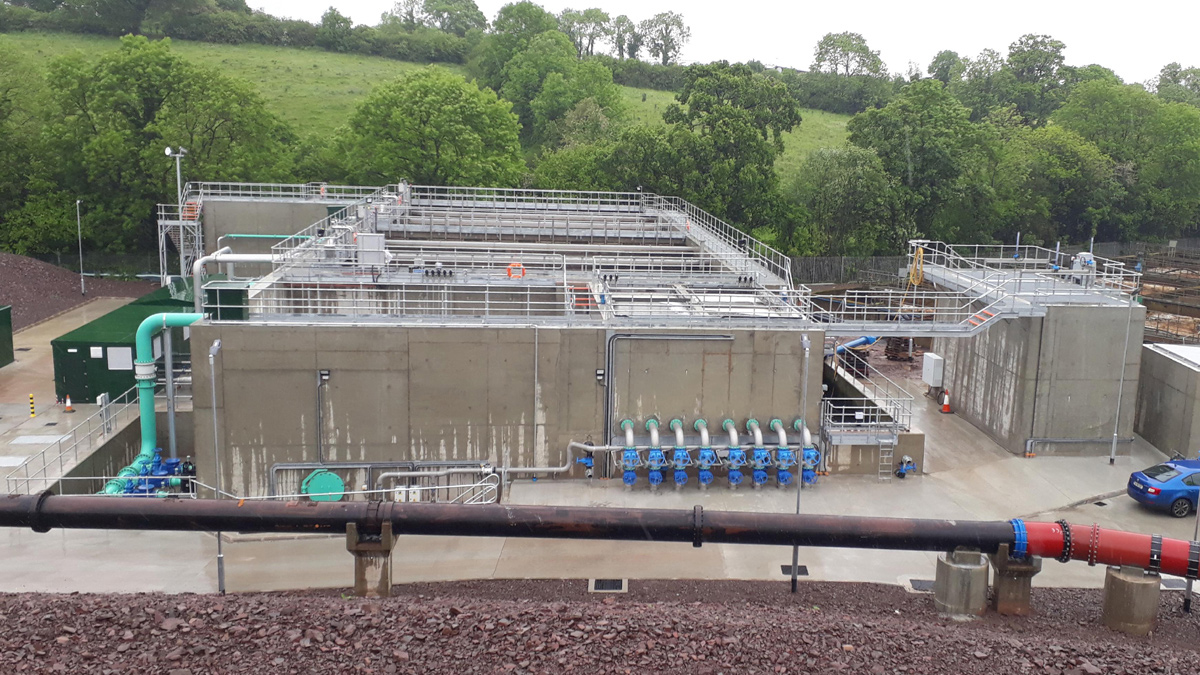
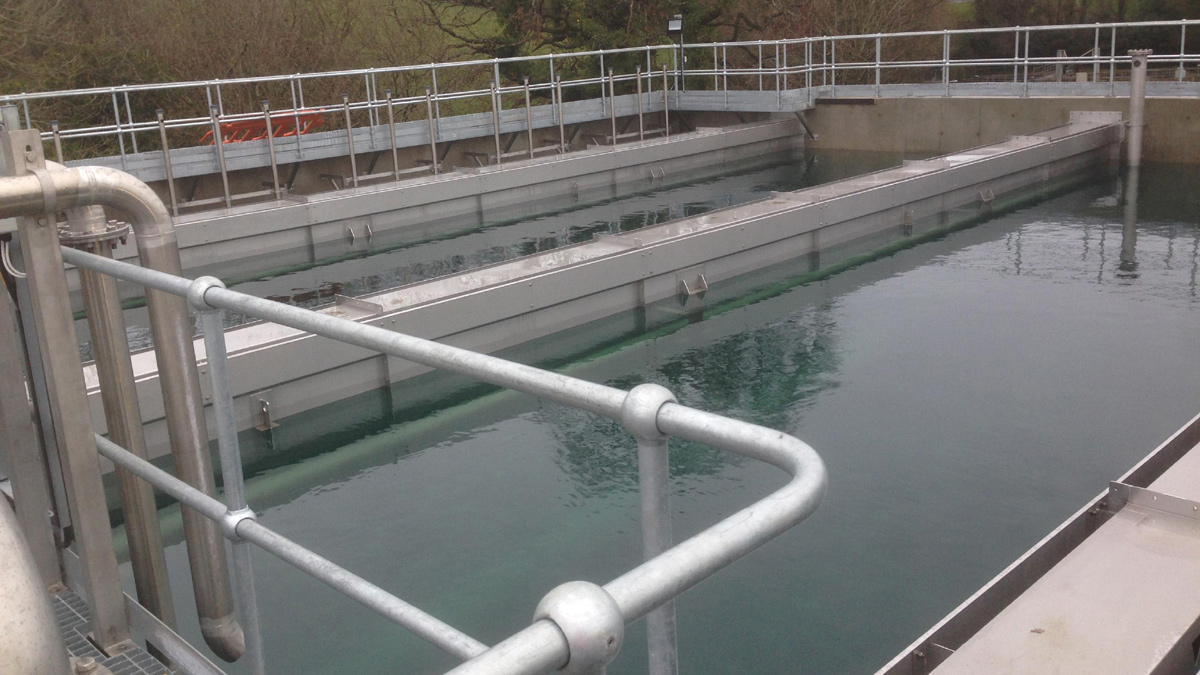
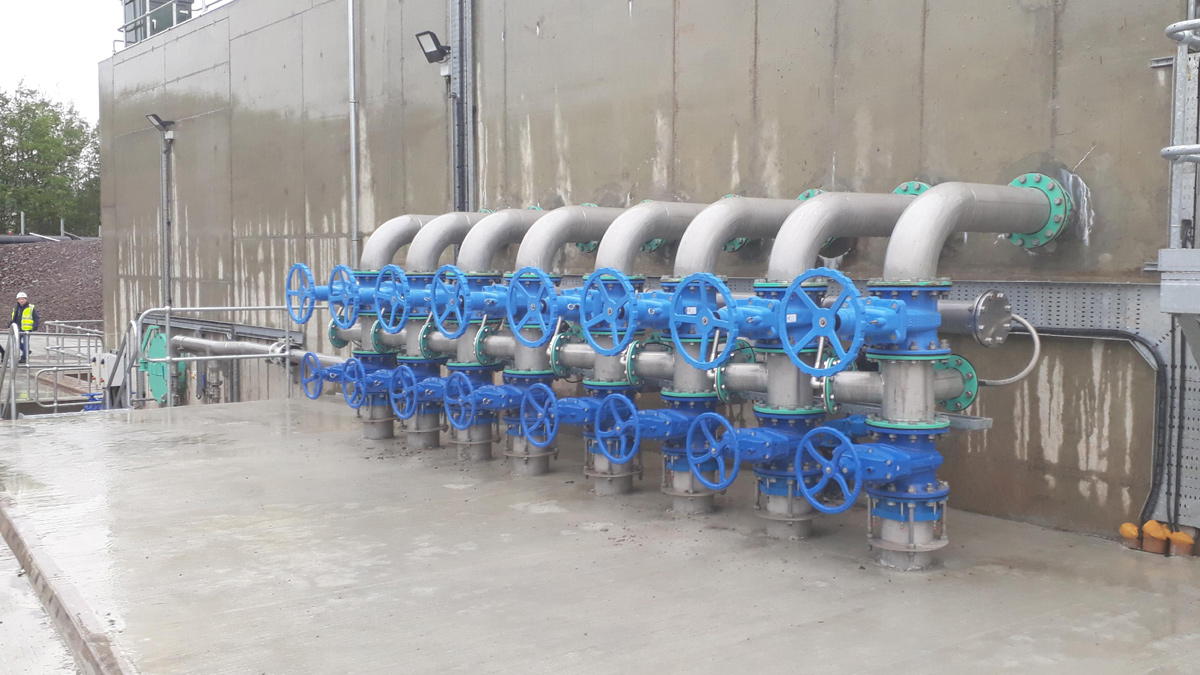