Safe Return of Recovered Process Water (2023)
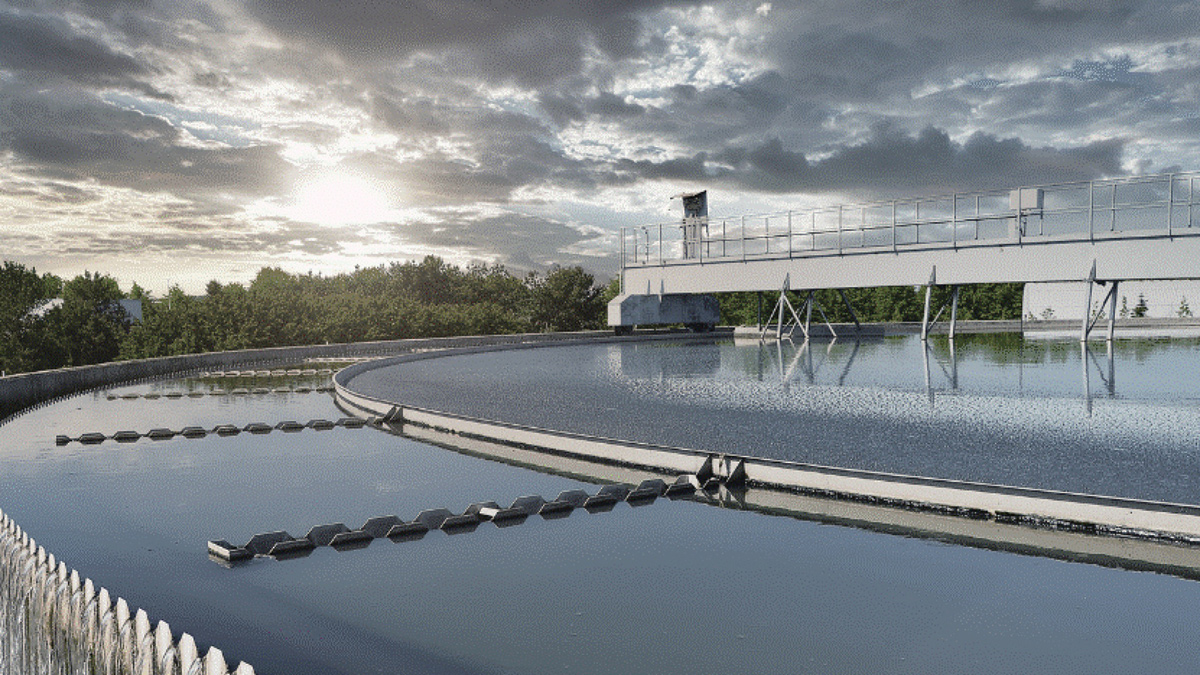
Process water treatment - Courtesy of WSP
This project was commissioned by UK Water Industry Research (UKWIR), as part of their efforts to address one of the 12 Big Questions the UK Water Industry is facing, “How do we achieve 100% compliance with drinking water standards (at point of use) by 2050?”.
Today, no more than 10% of the total incoming flows to water treatment works (WTWs) can be made up of treated recovered process water streams (e.g. centrate/filtrate from sludge processing units, filter backwash, membrane concentrate/reject, etc.). One of the main concerning issues prohibiting the higher ratios of recovered process water/raw water mixing as an input to WTWs, is the risks associated with contaminants such as Cryptosporidium, viruses and microplastics which may be present at elevated concentrations in the recovered process water streams.
The goal of this project is to facilitate maximising the safe recycling of recovered process water streams at WTWs, through identifying and recommending the adoption of optimum methods of treatment and monitoring, as well as proposing methods of risk mitigation for the above-specified contaminants.
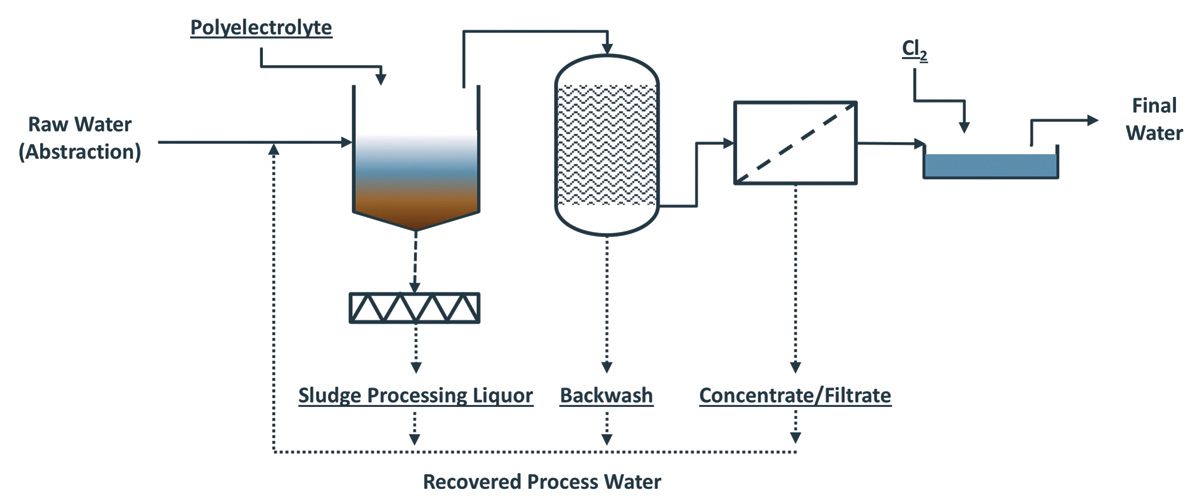
Recovered process water recycling at WTWs – Courtesy of WSP
Approach
From a long-list of 24 solid-liquid separation technologies (Figure 3.1), the ones deemed most suitable, both technically and commercially, for the removal of Cryptosporidium, viruses and microplastics from recovered process water streams were shortlisted under eight process groups:
- Coagulation/flocculation.
- Sedimentation.
- Depth filtration.
- Slow sand filtration.
- Surface filtration.
- Membrane separation (MF and UF).
- Adsorption (GAC and PAC).
- Microfluidic separation.
Detailed technical and commercial information for each process group was obtained from academic literature, case studies and vendor profiles. In addition to provision of performance data, an overview of waste by-products of each technology was given and CAPEX/OPEX calculations were undertaken.
This information was integrated with findings from an expert workshop with attendees from academia, industry, and regulators to feed into the development of a cost-quality model. This was to support the water industry in the selection of the most appropriate recovered process water treatment processes, based on the characteristics of the incoming recovered process water streams and the resilience of the existing treatment processes on-site.
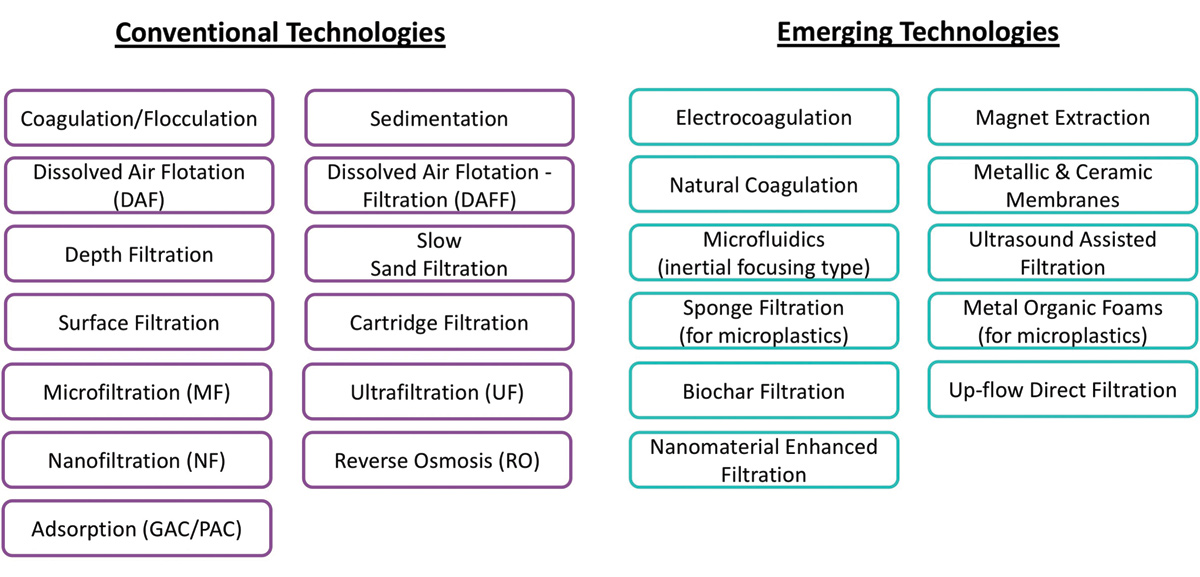
Technology appraisal: long list of solid-liquid separation technologies – Courtesy of WSP
Project outputs
Treatment technology selection: With regards to coagulation and flocculation, the use of conventional aluminium and ferric based coagulants is still dominant in the water industry. However, emerging technologies such as electro-coagulation and natural-substance coagulation can offer more sustainable and environmentally friendly options. Coagulation is not a solid removal treatment on its own and would require to be coupled with other technologies such as sedimentation, filtration and/or membrane separation to achieve high solid removal efficiencies.
The three main methods of sedimentation include horizontal flow, up-flow solid contact, and tilted plate (lamella) separators. While low in CAPEX and frequently used in the water industry, the horizontal flow systems require large footprint, and are prone to flow turbulence, short circuiting, and sludge re-suspension. These construction and operational issues can be significantly minimised when using compact tilted plate separators, although it comes at the cost of a higher CAPEX.
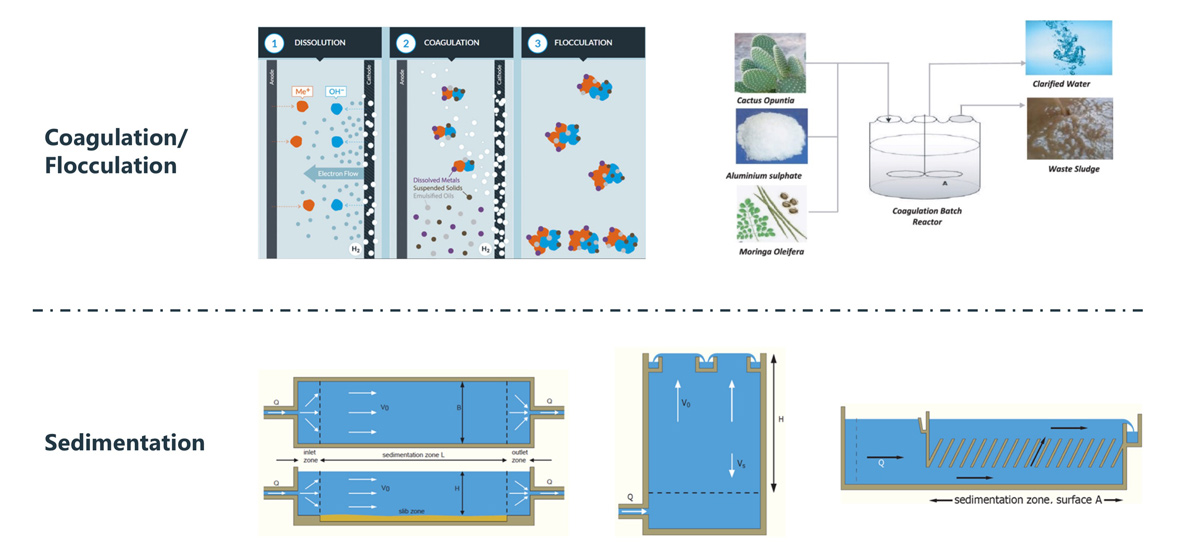
Coagulation/flocculation and sedimentation process groups – schematics from (Gandiwa, 2020) (watertectonics.com, 2022) (van Djik, 2007)
Among seven different types of depth filtration analysed in this study, the down-flow systems with continuous backwash showed the highest removal efficiency. Moreover, newly developed activated glass media was suggested to be more efficient at removing particles of 15 µm and smaller, compared to the conventional sand media. Therefore, upon more trials, these emerging media may be proven to be more suitable for the removal of viruses and Cryptosporidium from recovered process water streams.
Slow sand filtration has 20-50 times smaller flux than depth filtration, and thus it requires much larger footprint. Nevertheless, the free-gravitational operation of the system and no backwash requirements are among the key advantages of slow sand filters. These systems are not very efficient for total suspended solids (TSS)/turbidity removal (~90%), but highly effective for Cryptosporidium (up to 3 log) and viruses (1 – 4 log).
Surface filters offer higher efficiency than depth filtration with respect to TSS/turbidity. The backwash is also more efficient (2-5% of effluent) compared to depth filters (4-8% of effluent). However, sensitivity to influent quality (i.e. best at TSS< 20 mg/l) makes surface filters less suitable for recovered process water treatment compared to depth filters. Among different types of surface filtration methods analysed in this study, the bag filter offered the widest range of pore size (2-75 µm), and thus its design deemed to be easier to be tuned according to the specific contaminants in the recovered process water streams.
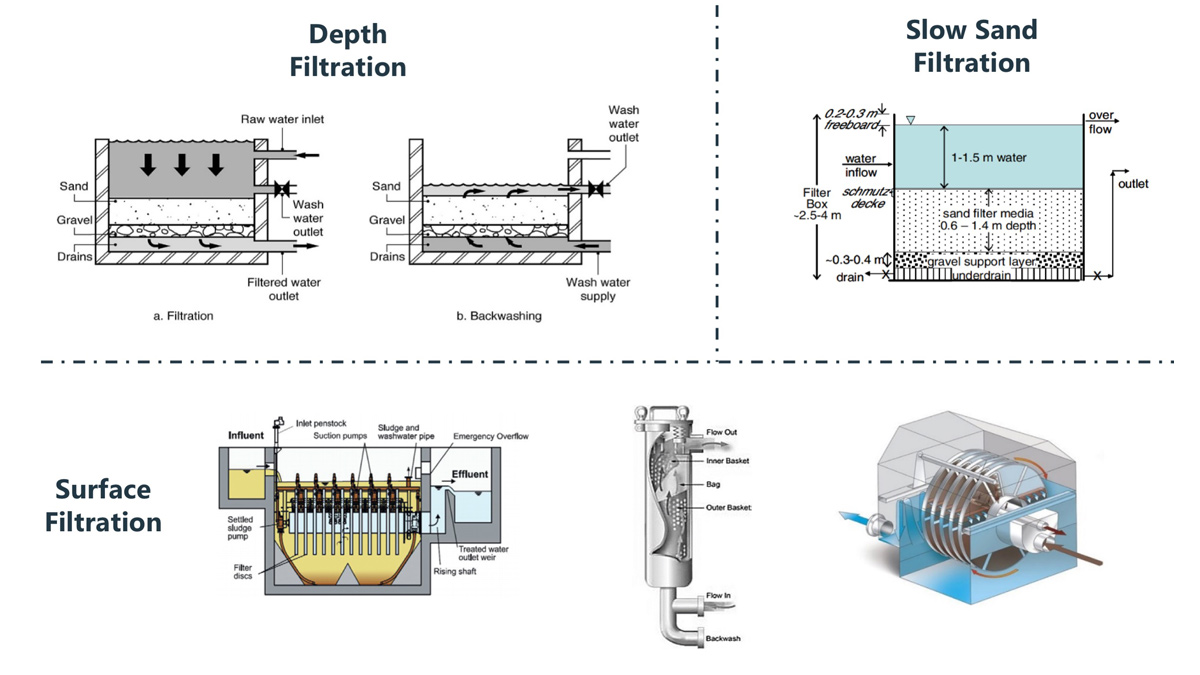
Depth filtration, slow sand filtration and surface filtration process groups – schematics from (Bielefeldt, 2011) (Metcalf & Eddy, 2014) (Eliquo Hydrok, 2020) (Rosedale Products, 2015) (mena-water.com, 2022)
Sedimentation, slow sand filtration, depth and surface filtration were in the same order of magnitude in terms of both CAPEX and OPEX. Conventional sedimentation (i.e. horizontal flow) and slow sand filtration offer the lowest overall cost and the simplest operation. Nevertheless, where space is a major constraint, the addition of lamella plates to the conventional sedimentation tanks, and/or the use of higher rate depth or surface filtration, instead of slow sand filtration can offer footprint efficiency at a slightly higher CAPEX.
The OPEX of solid-liquid separation technologies would increase when they are paired with coagulation/flocculation processes. The addition of coagulation/flocculation can significantly boost the performance of some technologies (i.e. sedimentation, slow sand filtration, depth filtration and surface filtration), but is less beneficial for other technologies (i.e. MF/UF and microfluidic systems).
Microfiltration (MF) and ultrafiltration (UF) offer modular and high efficiency solutions for fine solids removal, specifically with regards to viruses (up to 7 log removal) and Cryptosporidium (up to 6 log removal). Still, their sensitivity to fouling, scaling and large solid blockage (i.e. pre-treatment requirements) and high TOTEX are among the main considerations of applying these technologies. Among the different types of MF and UF configurations reviewed, hollow fibres offer better flux to volume (i.e. economy of scale) due to their high surface to volume ratio. Spiral wound types are also compact, but their resistance to positive hydraulic pressure make them more suitable for nano filtration (NF) and reverse osmosis (RO). In terms of material, emerging metallic membranes have been shown to be mechanically robust and efficient for the removal of fine particles, such as Cryptosporidium (5.1-5.4 log removal). Yet, further trials are needed before adapting these membrane types in a large scale in the water industry.
The small footprint, modularity, and scalability of membrane technologies make them a suitable choice for small WTWs, where having a compact design is a priority. Moreover, MF/UF offer effective removal efficiencies (i.e. up to 7 log removal for viruses, up to 6 log removal for Cryptosporidium) for where a high degree of purification is necessary. Still, for larger WTWs and/or where lower ratio of recovered process water recycling is required, MF/UF membranes do not offer an economically feasible option. The high cost of membranes makes MF/UF technologies 10 – 15 times more expensive in terms of CAPEX than other technologies, while the high cost of pumping energy (0.2-0.3 kWh/m3) make the OPEX of MF/UF systems 2-15 times higher than other solid-liquid separation techniques, except microfluidic devices.
Activated carbon adsorption (GAC/PAC) is not an efficient method of solid separation. However, it can offer effective polishing (as post-treatment) for other technologies to minimise the taste and odour issues in the recycled recovered process water. Among different configurations, the up-flow GAC columns offer higher efficiencies as they promote a greater surface contact between the granules and the effluent. The disadvantage of the up-flow systems is the higher OPEX associated with pumping and the risk of media loss into the final effluent. The costs of GAC are very similar to that of depth filtration, unless considering the assets and energy required for media regeneration, which would make the costs 2-5 times higher than that of depth filtration.
Inertial focusing (IF) microfluidics are among the emerging and rapidly growing methods of solid removal from water systems, working based on the selective separation of microparticles through variously sized microchannels. Separation efficiencies up to 96% for Cryptosporidium and 99% for microplastics have been achieved in the lab-scale. Microfluidic separation is a chemical-free and easily scalable process, with an in-built ability of waste streams segregation and collection. However, sensitivity to blockage (i.e. requiring significant pre-treatment) and the low level of technology readiness (lab tested with drinking water and Cryptosporidium, scaled up for other applications), are some of the main challenges for the full adoption of this technology in the water industry.
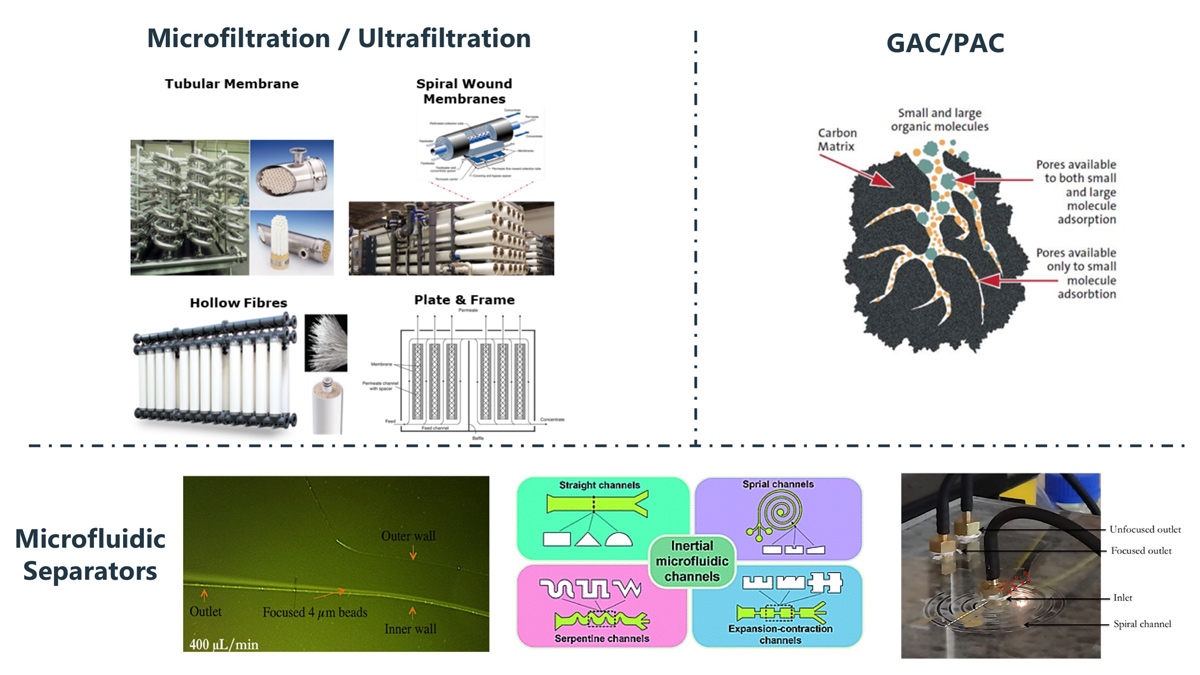
MF/RO membrane separation, GAC/PAC adsorption, and microfluidic separation processes – Schematics from: (PCI Membranes, 2021) (Applied Membranes Inc, 2021) (reverseomosis4operators.com, 2021) (Balster, 2013) (ElgaLab, 2021) (Jimenez & Bridle, 2016) (Tang, 2020) (Miller, 2016)
Cost estimations for inertial focusing microfluidics were provided by a UK-based vendor, extrapolating figures from previous smaller scale installations. The estimations suggest the lowest CAPEX among all processes (~3.4 £/m3), owing it to the significant advancements in the material and manufacturing methods (e.g. 3D printing, laser cutting, etc.) in the recent years. The OPEX however, is still the highest among all processes, about 2-10 times higher than MF/UF membranes, and 10-100 times higher than other separation processes. The high OPEX of microfluidics is due to the cost of pumping fluids through small micro channels. It is clear that significant reduction in pumping energy is necessary for microfluidic devices to be introduced as competitive solid-liquid separation technology in the water industry.
For the liquid waste (i.e. backwash from filtration and/or retentate/concentrate from the membrane systems) recycling to the head of the works, or mixing with the untreated process water, are key possibilities. However, further intermediary treatment (e.g. clarification) may be required depending on the quality of the liquid waste.
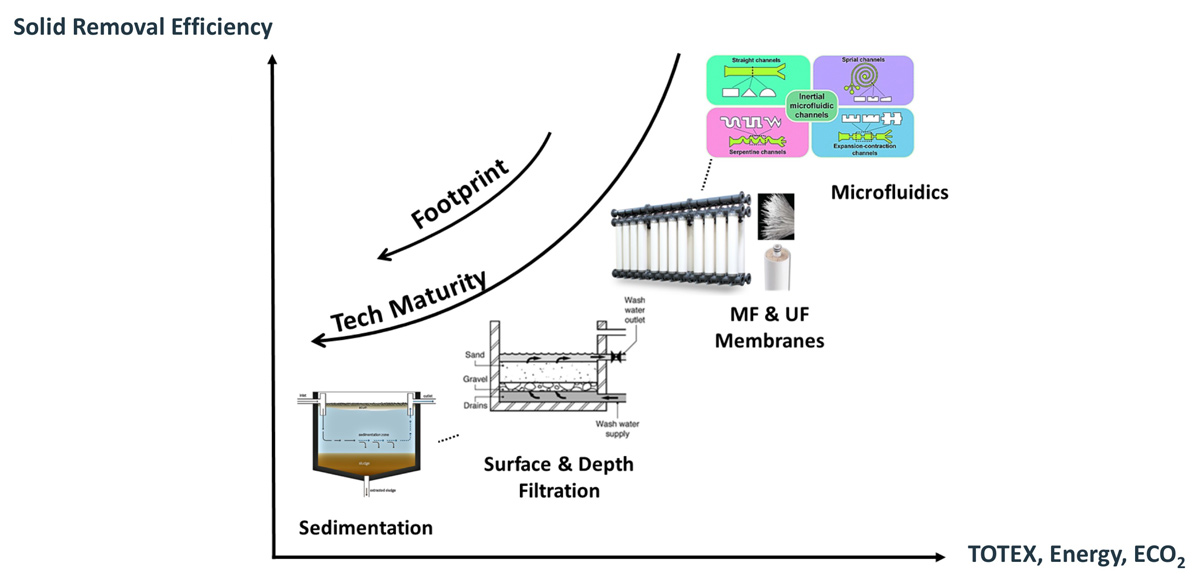
Treatment technology comparison overview – Courtesy of WSP
Cost-quality model: In order to assist water companies in the UK and the Republic of Ireland to compare and select the most appropriate recovered process water treatment processes, based on the characteristics of the incoming recovered process water streams, as well the resilience state of the existing treatment processes on each particular site, a quantitative cost-quality model was developed. The model generates as an output the following key analytics:
- Treatment process scenarios to choose from based on the provided recovered process water types and characteristics.
- CAPEX, OPEX and TOTEX estimations (-10% to +20% error margin).
- Operational daily energy cost (kWh range).
- Operational daily carbon footprint (kg CO2 range).
- Recovered process water volume for any given treatment scenario.
- Estimated efficiency of removal for Cryptosporidium, viruses and microplastics.
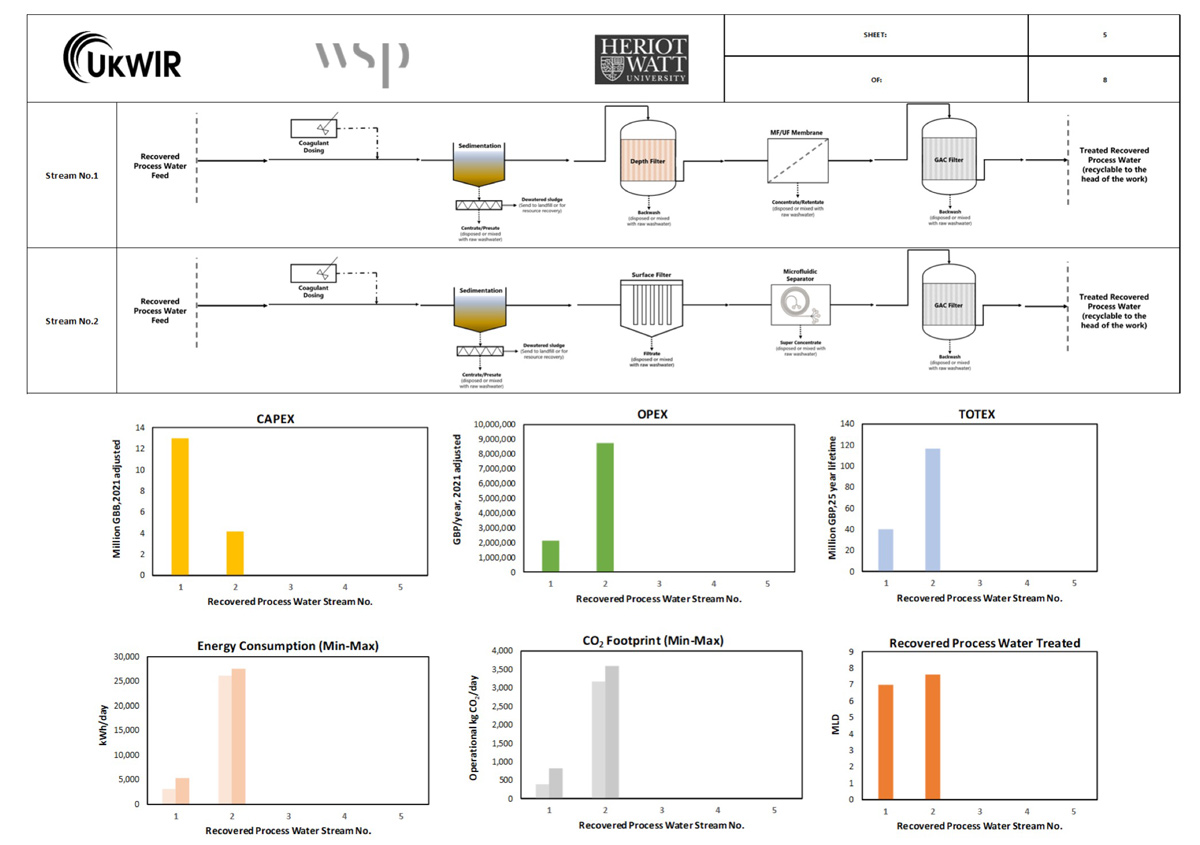
Model output example: scenario-based treatment technology & configuration comparison – Courtesy of WSP
Monitoring method selection: The main methods of detection and monitoring of microplastics, Cryptosporidium and viruses were grouped and reviewed under three main tiers, based on the methods ease of use/time to result, and the accuracy/quality of the results from each method.
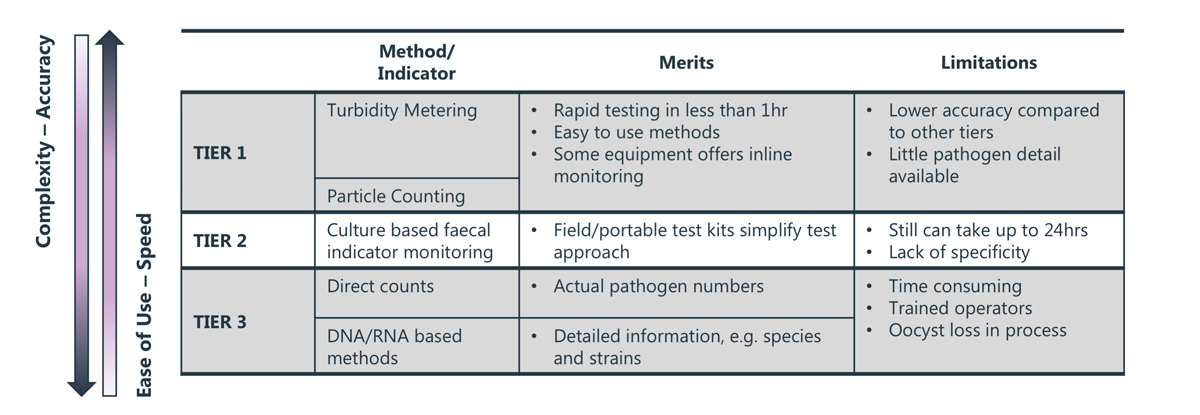
Key methods of detection & monitoring – Courtesy of WSP
Selection of monitoring methods should consider that recovered process water streams are likely to be relatively highly contaminated so any method should perform well under such conditions. Additionally, a review of particle counters noted that for particle counting there was good correlation between particle counts and oocyst numbers after coagulation/sedimentation treatments and slow sand filtration, but not after membrane filtration methods. Hence, it is important that the choice of monitoring method should consider the treatment methods used.
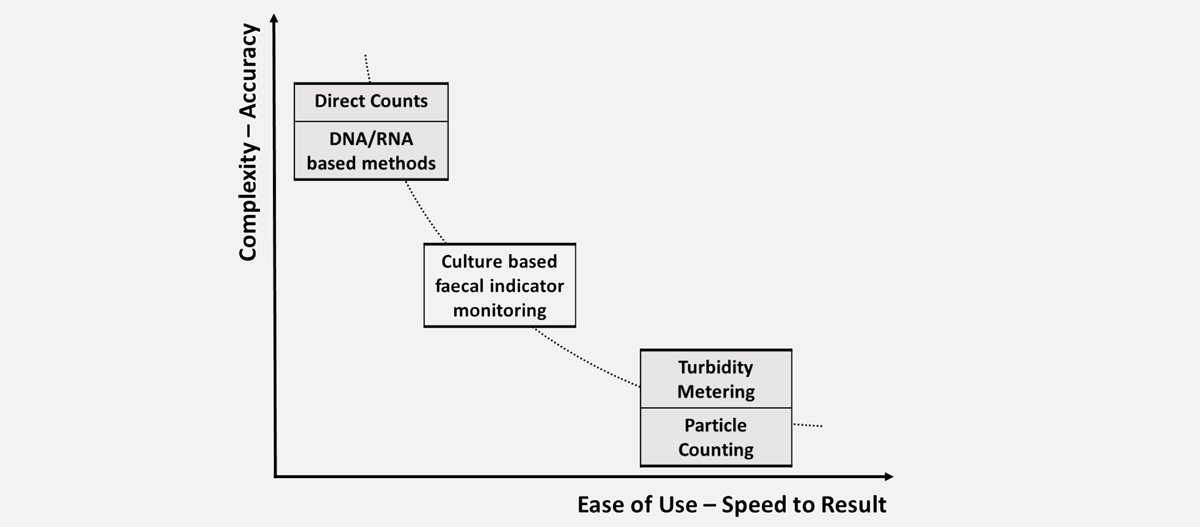
Detection and monitoring method selection – Courtesy of WSP
Operational risk control
A wide variety of potential risks related to the safe return of recovered process water, with a particular focus on the three target contaminants, were identified. However, weighting of the risks was considered challenging due to the variation between the different contaminations (e.g. acute versus chronic risks) and the broad nature of the contaminant classes, particularly viruses and microplastics. In general, the lack of knowledge/evidence was identified as being a high risk, especially in terms of microplastics behaviour/impacts, monitoring methods, the possibility of resistant strain selection through recovered process water return, and emerging contaminants. This latter factor and the difficulty of determining risk levels were the main regulatory risks.
Regular reviews of reports, such as the Badenoch and Bouchier reports, were deemed necessary to keep up with scientific advances and emerging contaminants. Commercial risks were to reputation and the associated cost, with operational factors like balancing flows, monitoring and contingency plans being of medium risk. Digital twinning can be used to model the impact of recovered process water return scenarios for individual WTWs, though water companies should consider the wider company perspective.
From the Expert Workshop the availability, approval and adoption of new treatment process was considered low risk though there were concerns about cost/space and the impact on existing processes when returning to head of the works. When evaluating the proposed technologies in this project, a variety of disadvantages, in categories of cost, space, performance, regulation and waste were identified for each technology, with no technology being clearly superior or worse to others.
The monitoring techniques were deemed essential by the Expert Workshop to the successful safe return of recovered process water, with more evidence required to assess different sensors and monitoring approaches, particularly in the more contaminated recovered process water streams, and to determine trigger levels for action. Turbidity was seen as a reasonable indicator of risk for Cryptosporidium, and more work is needed to determine methods and surrogate/indicator parameter correlations for viruses and microplastics. Monitoring should also be applied to source waters to identify potential for catchment management approaches as well as enable dynamic management of ratios of recovered process water return based on input water qualities.
Conclusions
The aim of this study was to facilitate maximising the safe recycling of recovered process water at WTWs, while minimising the risk of outbreaks and health issues concerning Cryptosporidium, viruses and microplastics. This goal was achieved through delivering:
- A detailed review of the best available techniques (BAT) to detect, monitor and remove the above-mentioned contaminants from recovered process water streams.
- A gap analysis of the expert reports by Badenoch and Bouchier to highlight monitoring, treatment and control advancements made since 1998.
- Expert recommendations for systematic minimisation of operational and control risks associated with the safe recycling of recovered process water at WTWs.
- A cost-quality model, to assist water companies with treatment technology comparison and selection for recovered process water treatment and recycling.
For the full project details and its outputs please visit UKWIR website at: https://ukwir.org/maximising-the-safe-return-of-recovered-process-water
Project stakeholders
- Client: UK Water Industry Research (UKWIR)
- Contractor: WSP
- Collaborator: Dr Helen Bridle, Heriot-Watt University
- Project Director: Elena Gil Aunon, WSP
- Technical Lead: Dr Payam Malek, WSP
- Project Manager: Barrie Holden, UKWIR
Project Steering Group
- Affinity Water
- Anglian Water
- Irish Water
- Northern Ireland Water
- Northumbrian Water
- Scottish Water
- South East Water
- United Utilities
- Welsh Water
- Yorkshire Water