FT Pipeline Systems
Haweswater Aqueduct
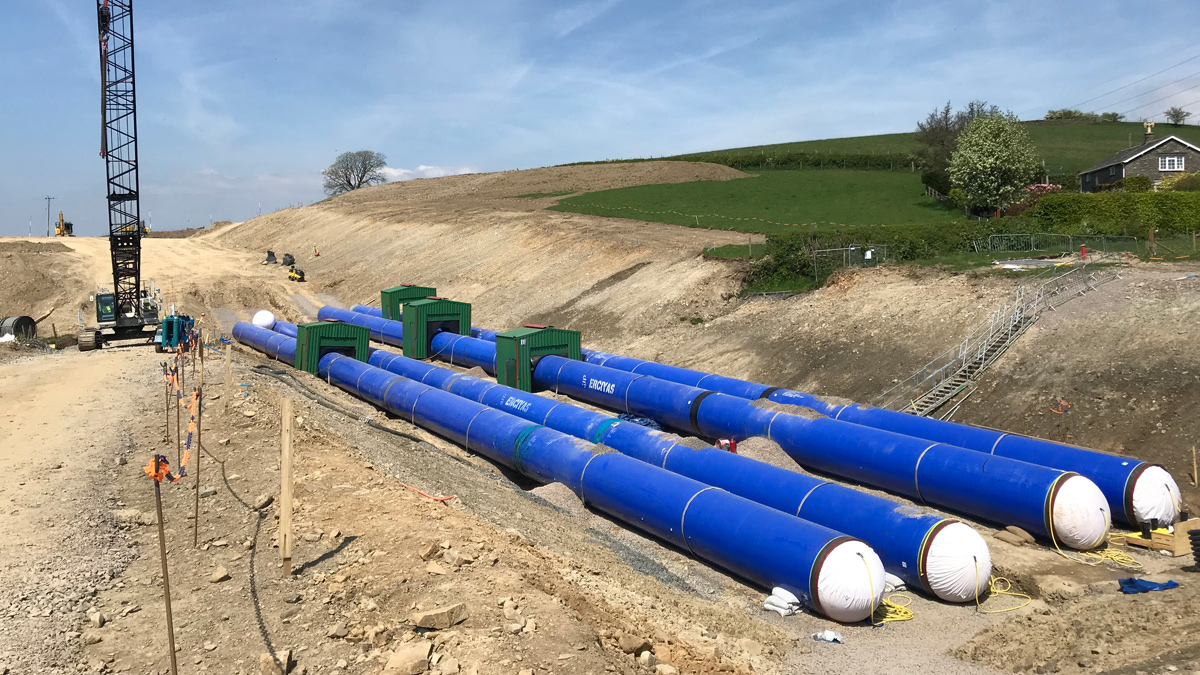
Pipe strings for the Haweswater Aqueduct Hallbank Project
MMB engaged with FT Pipeline Systems late in 2018 for the supply of 9640m of 1626 x 12.5mm coated and lined steel water pipe and bespoke fittings. The project – Hallbank – consisted of four runs of 1600mm steel pipe running alongside each other, to replace a section of the Haweswater Aqueduct.
The pipes originated from our pipe mill in Turkey and were shipped over on two dedicated vessels during 2019. FTPS had a team of staff at the docks to oversee the offloading operations. The pipes were 1600mm diameter and 14m long and were stacked in two layers inside the ship, with a total of 360 pipes on each. Once offloaded, each pipe was rolled twice to check for any nicks or damage. If there were any small areas needing repair, this was carried out prior to the pipes being restacked ready for delivery to the customer.
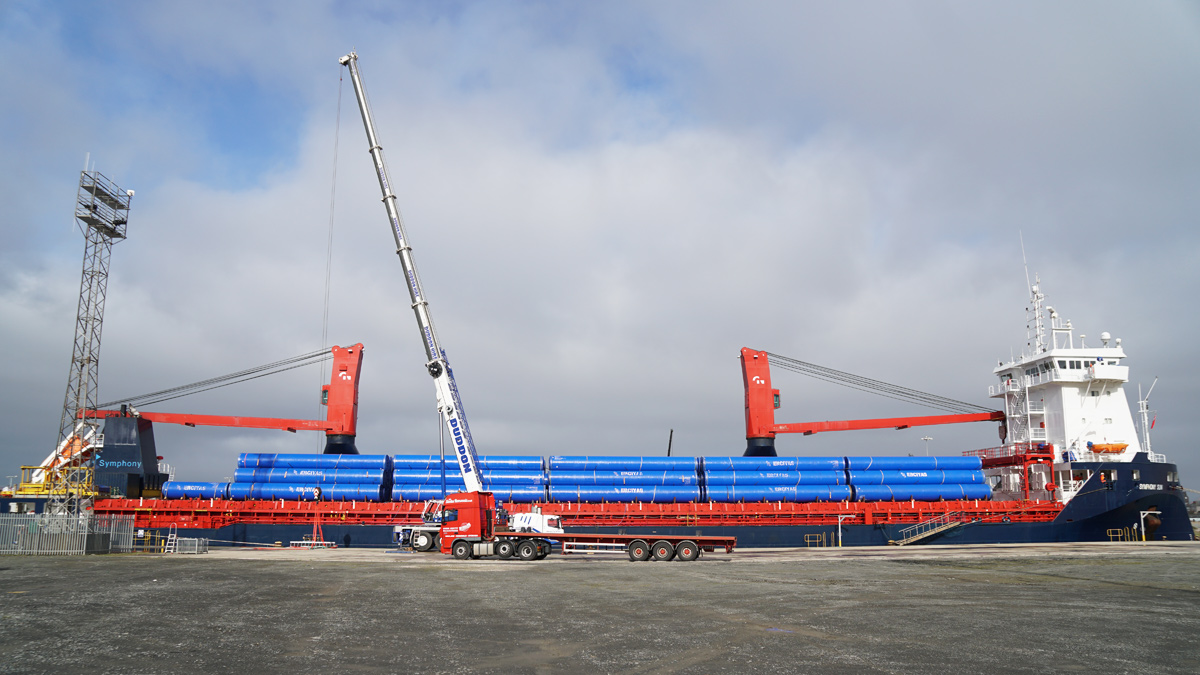
Steel water pipe being shipped from Turkey
Throughout the project we worked closely with our supply partner Lortub who manufactured the bends and fittings. The 10km of Ejoint/socket pipes utilised the maximum deflection in the joint allowable and rationalised the requirements for the bends. Assisted by Lortub we were able to remove close to 60 fittings from the scope thereby saving the contractor around £300k in terms of material cost, not including installation and fittings costs. In a demonstration of manufacturing control and quality, coupled with the logistical challenge, the pipework and fittings were delivered to site with a 1% ovality tolerance ensuring relatively easy fitting of these 14 long, 7-ton pipes.
Towards the end of 2020, after nearly two years constructing the new 2.5km section of pipe, United Utilities handed the entire site to framework contractor Mott Macdonald Bentley to complete the connections. They managed to do this in just under eight days. Connecting the brand new section near Hallbank meant shutting down the aqueduct.
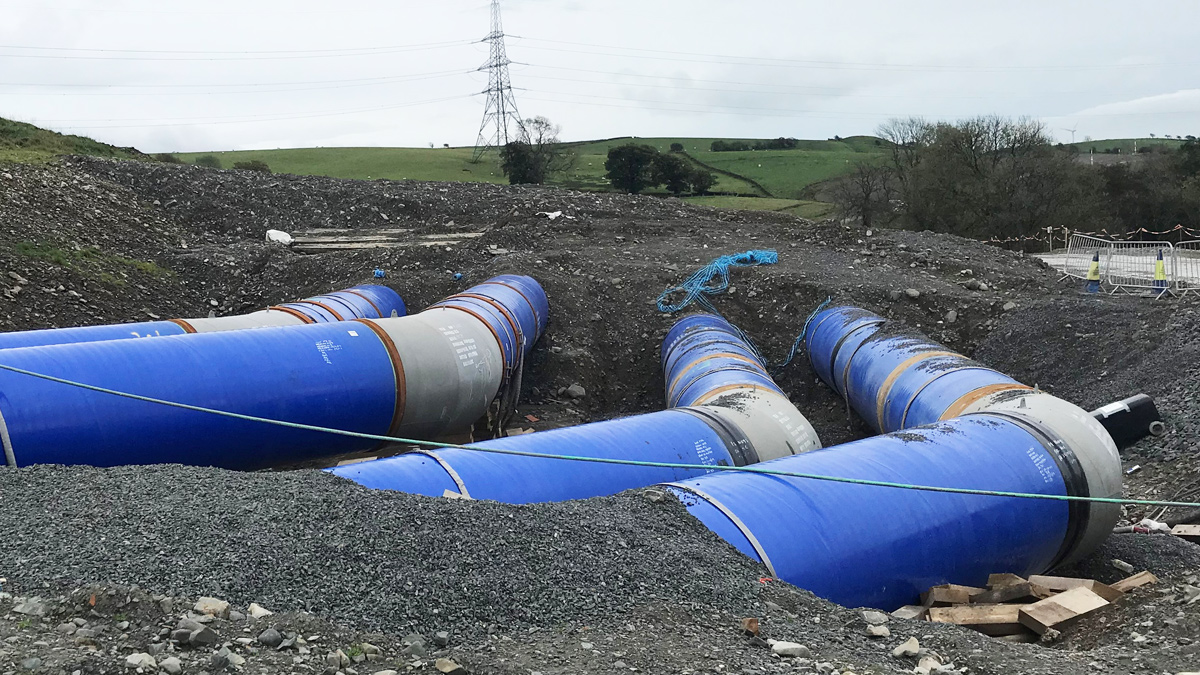
The coated and lined steel water pipe and bespoke fittings in place
The work at Hallbank in numbers
- The first major upgrade on the Haweswater Aqueduct for 65 years.
- At 2.5km, the new section of pipe, is slightly longer than the piece it is replacing.
- One pipe is being replaced by four separate pipes laid in parallel.
- Each one of the four new pipes is made up of 200 pieces of 14m long in 1.6 diameter pipeline sections.
- To maintain the flow of water by gravity, the new pipes have had to take a slightly different route to the original.
- Having four pipes instead of one makes things easier for when we need to do maintenance like this in the future. We can take one pipe out of operation temporarily while the others keep supplying water.
- The time taken to connect the new pipe was 7 days, 22 hours and 46 minutes.
- More than three quarters of a mile (1.35km) of welds for the connections alone.
For more information: FT Pipeline Systems: +44 (0)1543 416024 | www.ftpipelinesystems.co.uk
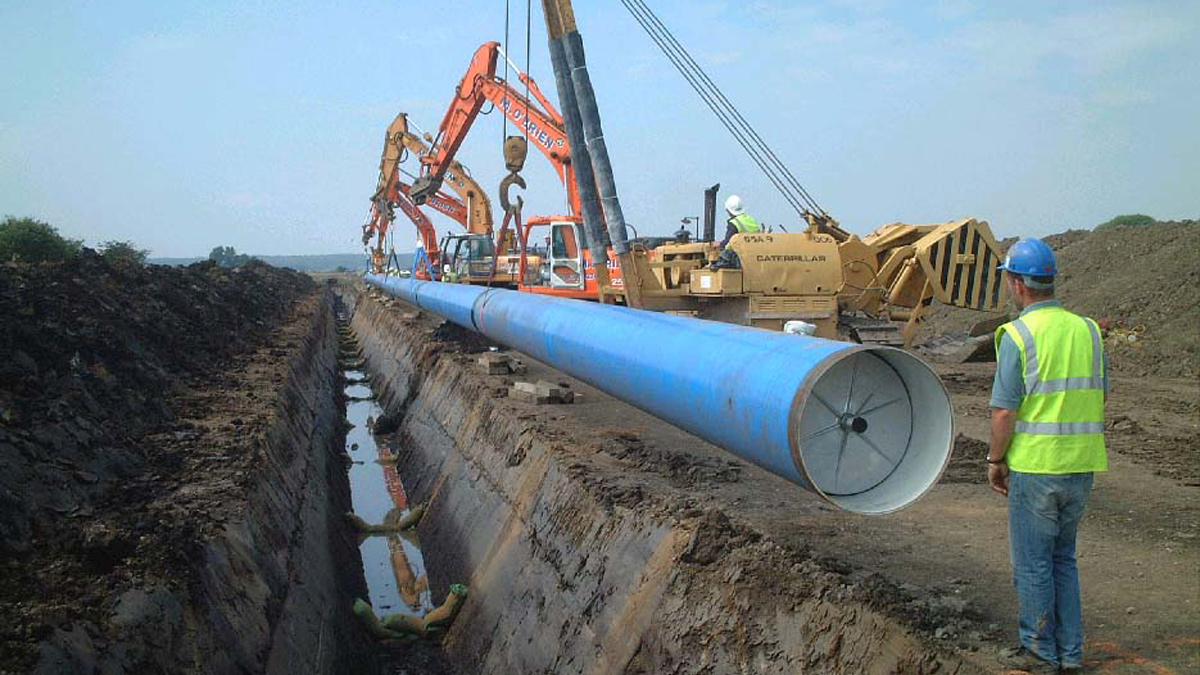
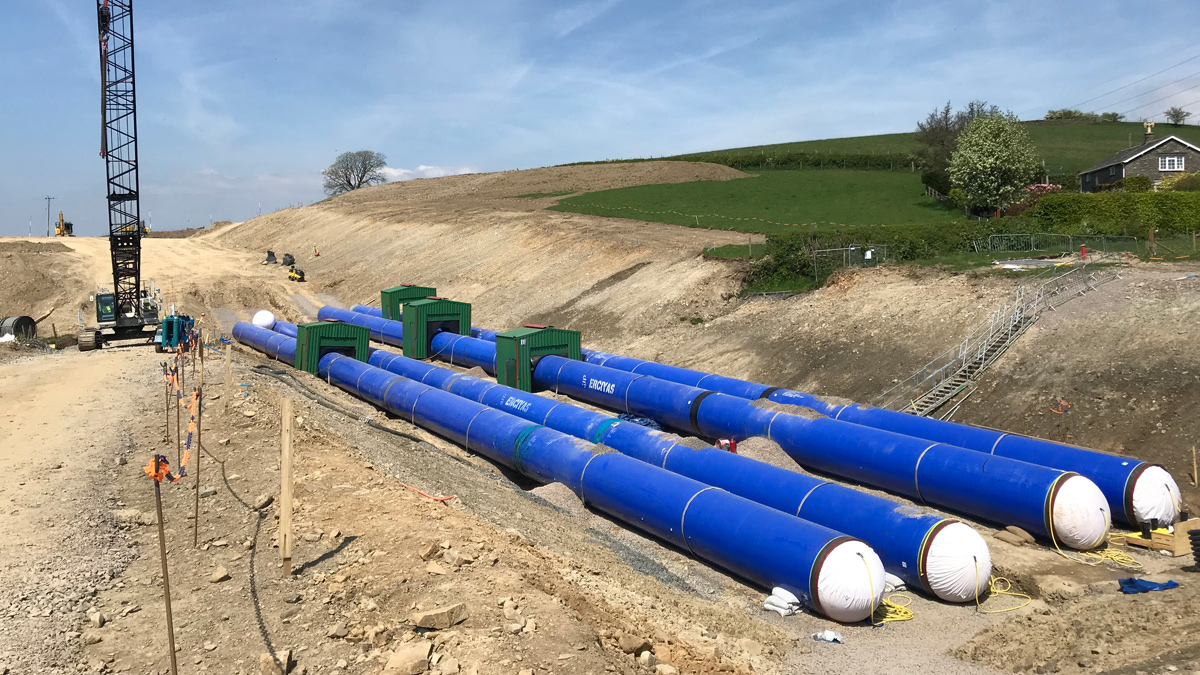
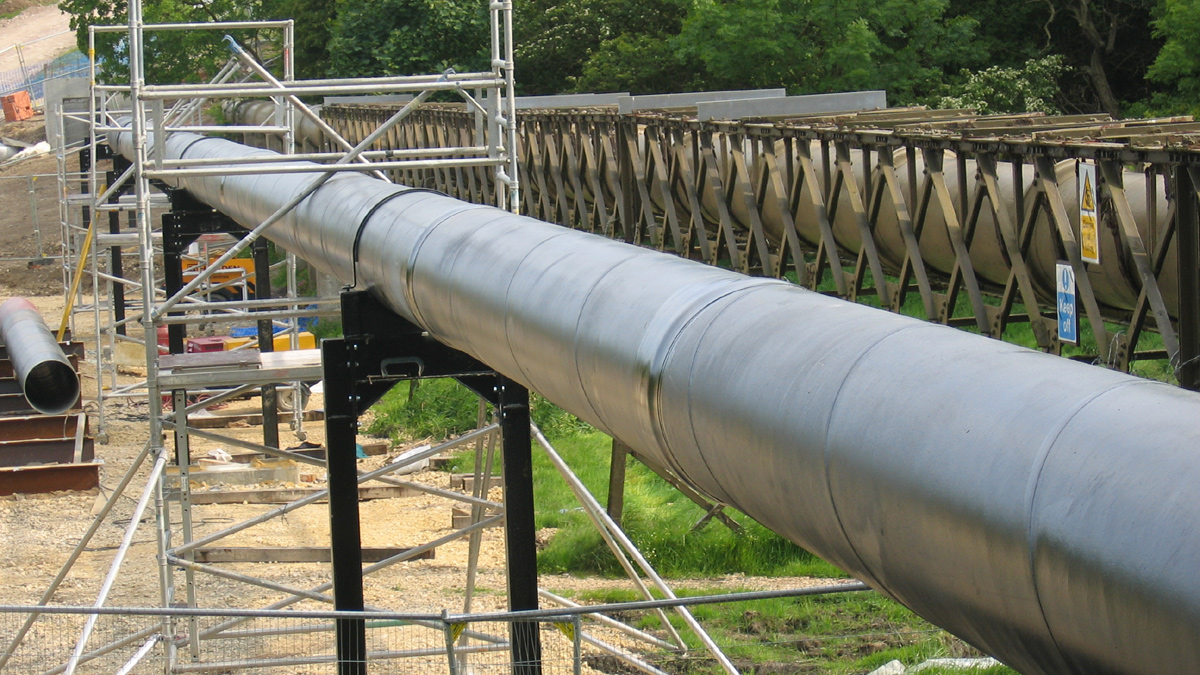
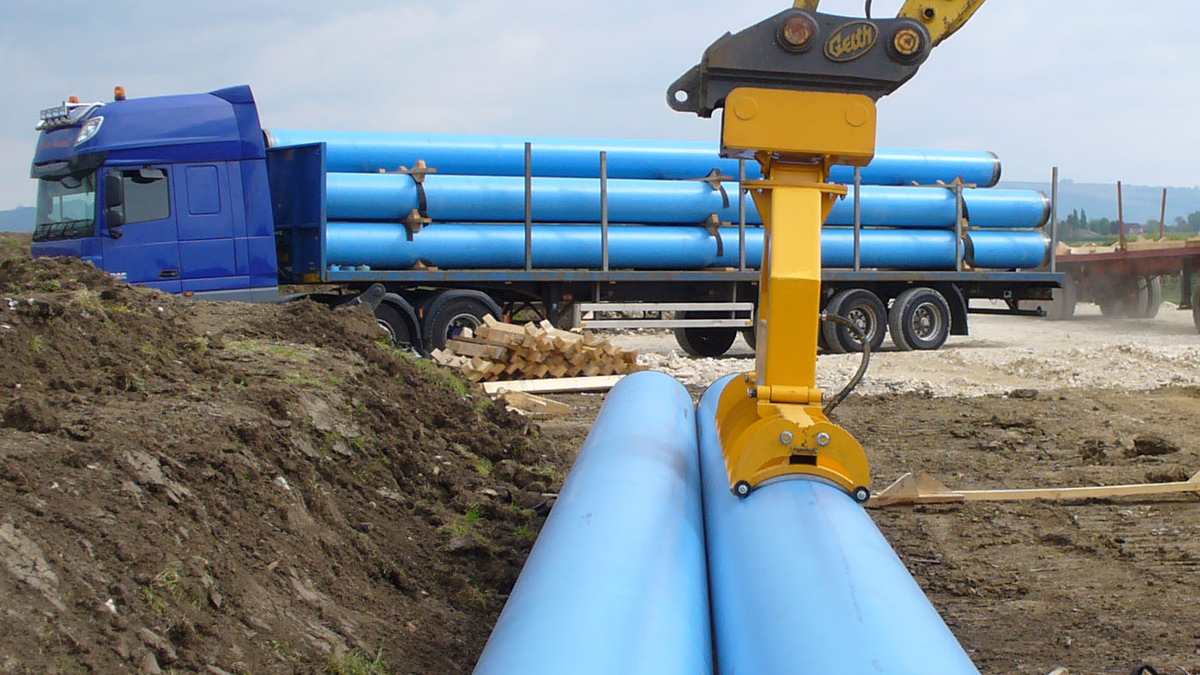
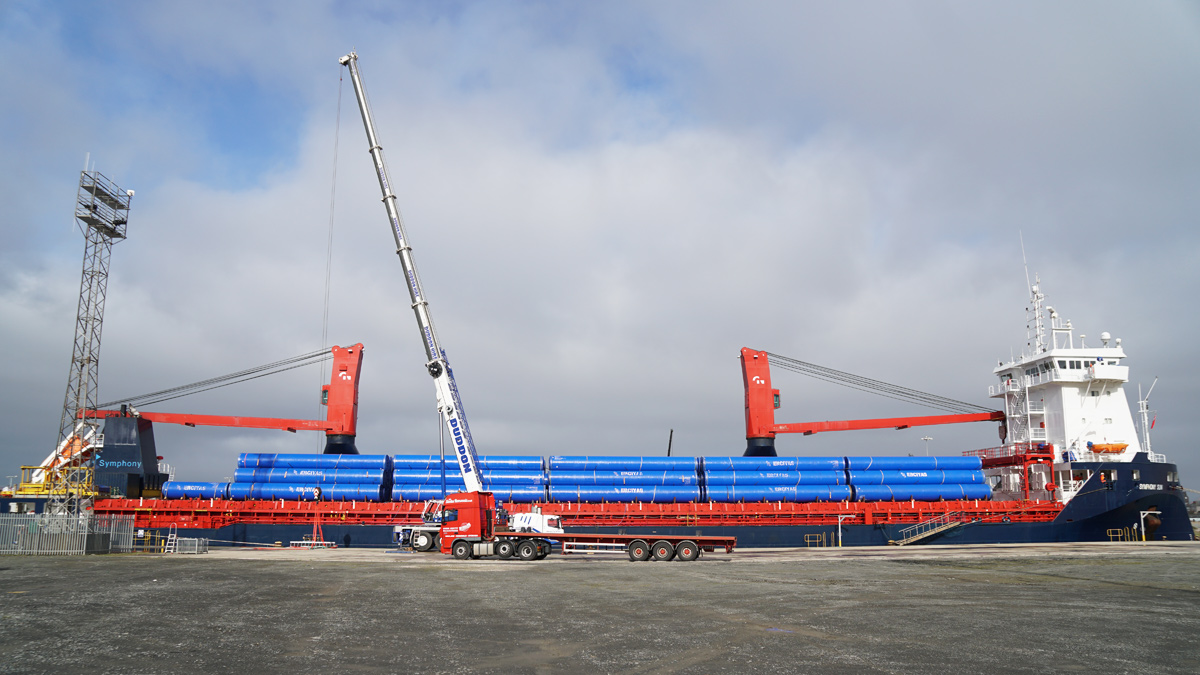
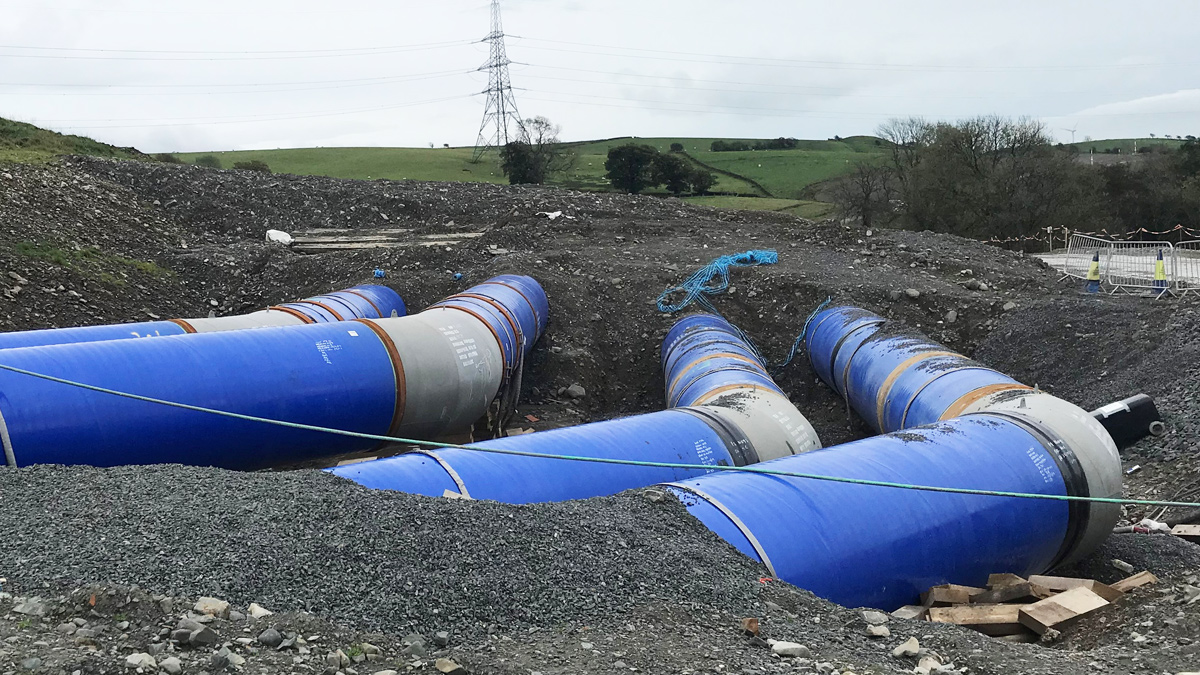
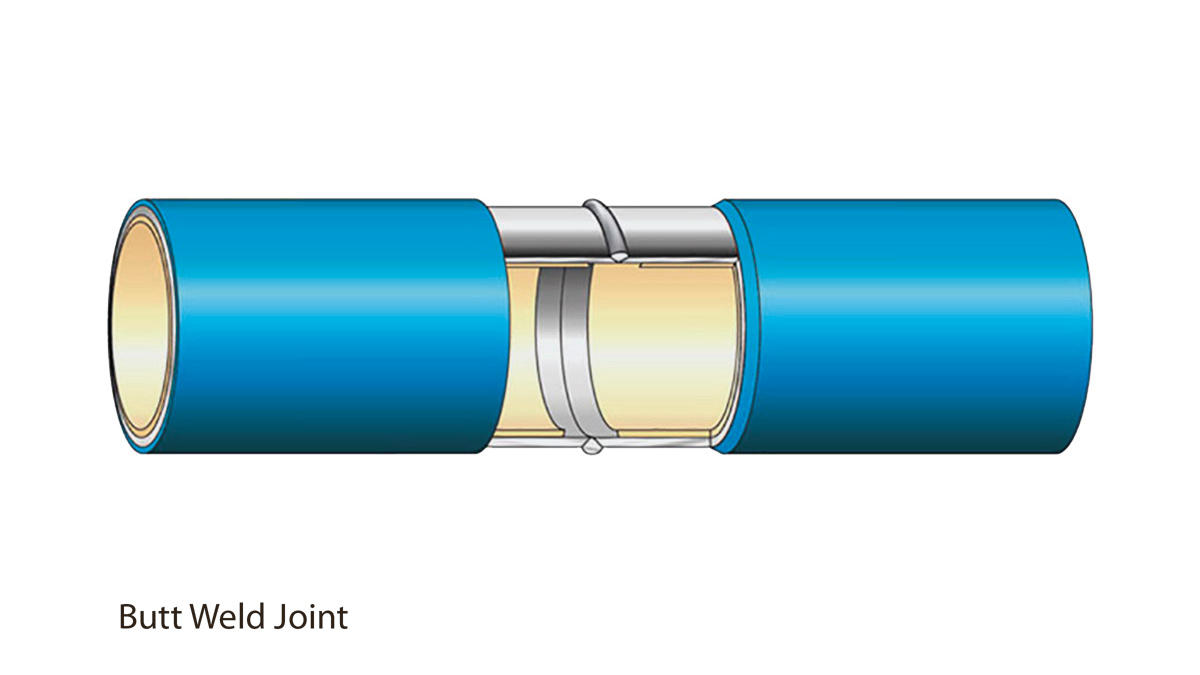
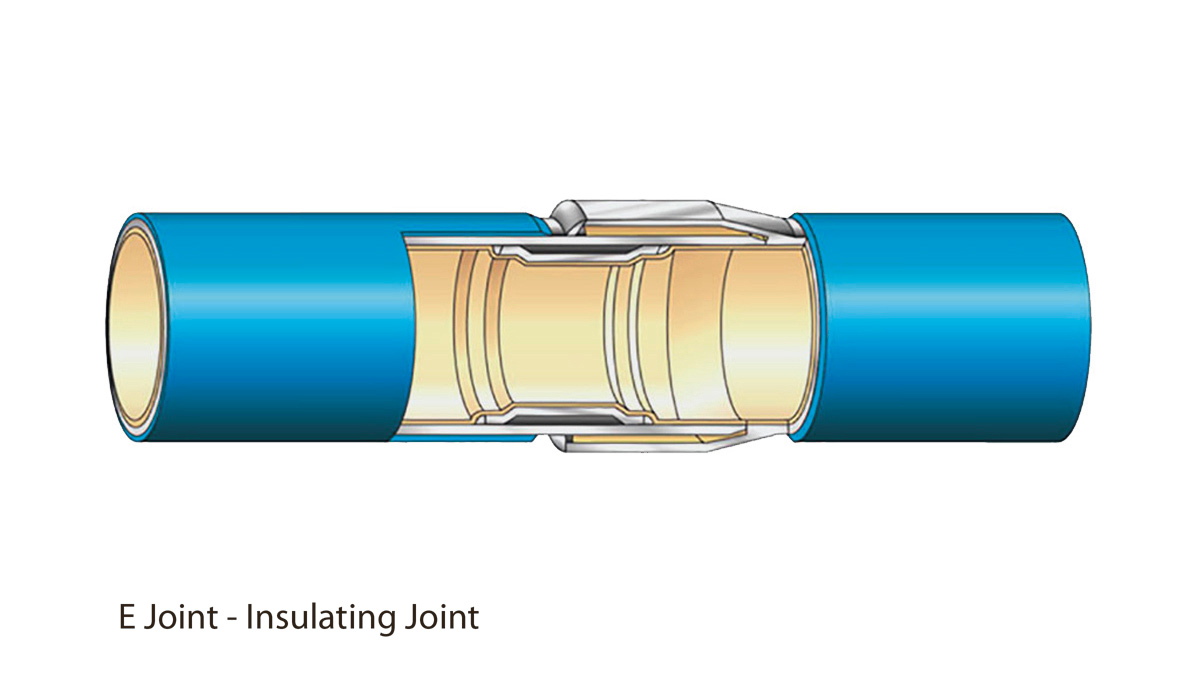
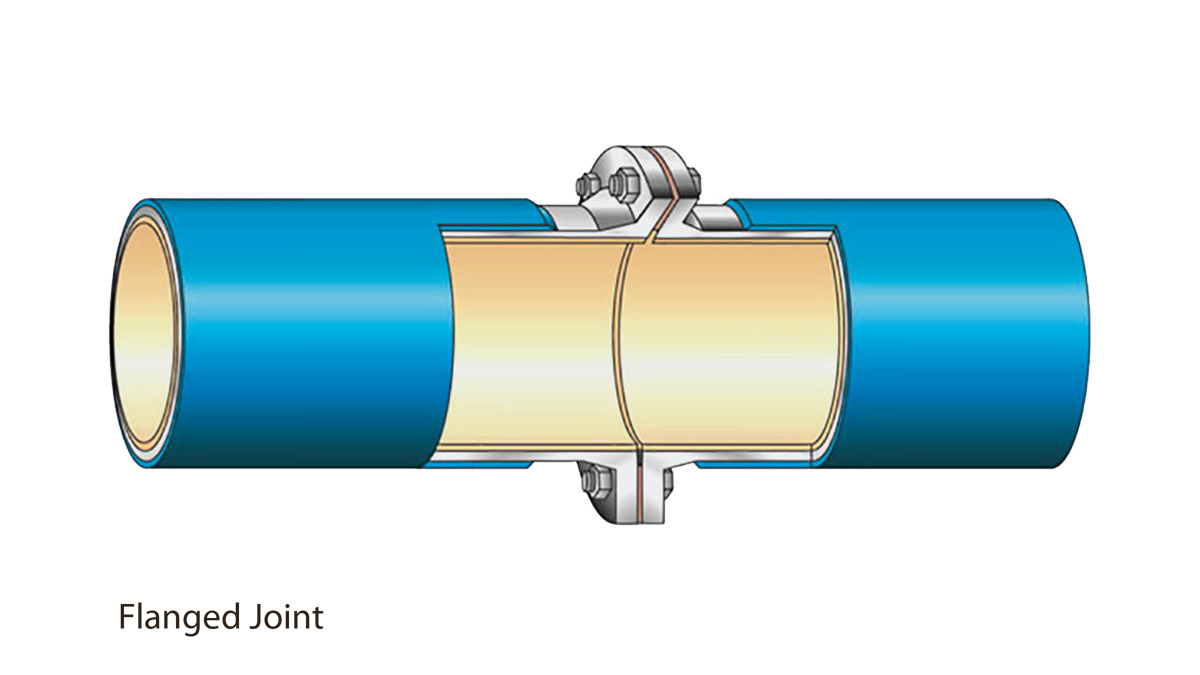
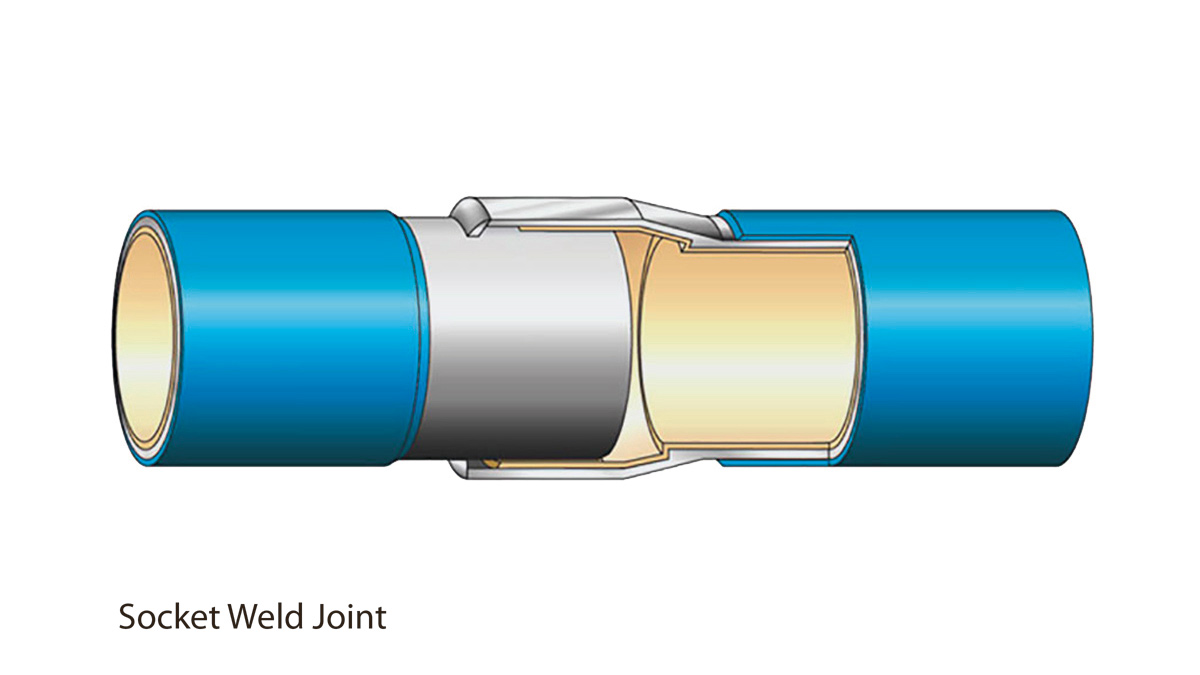
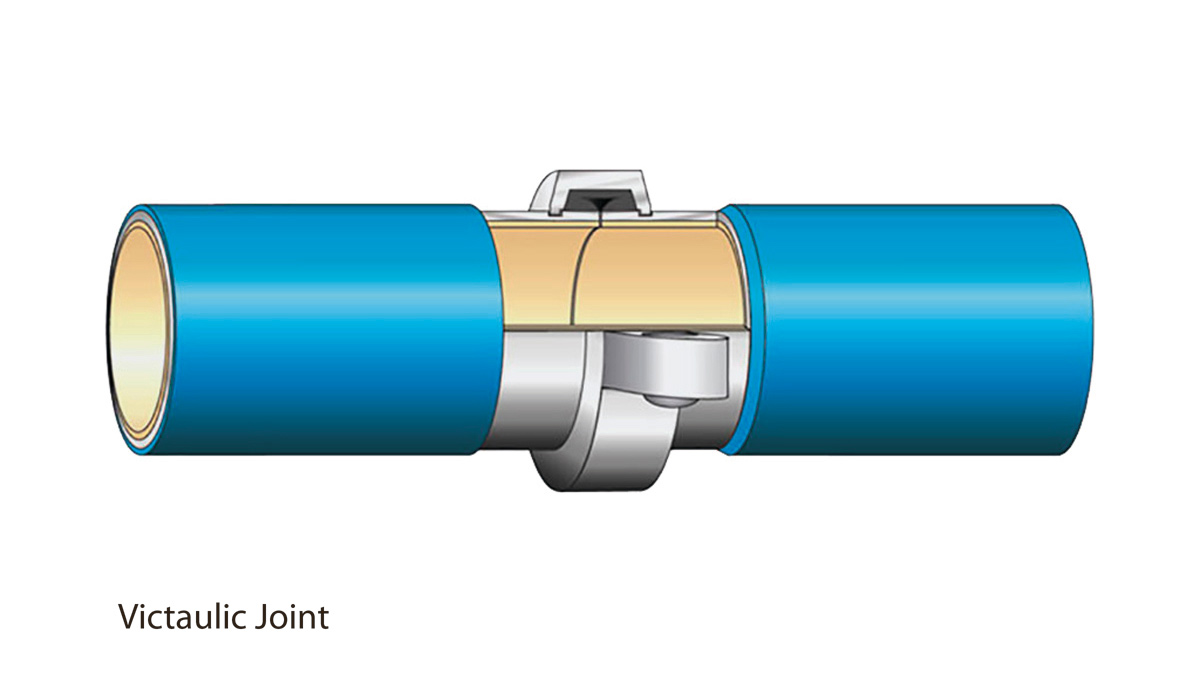
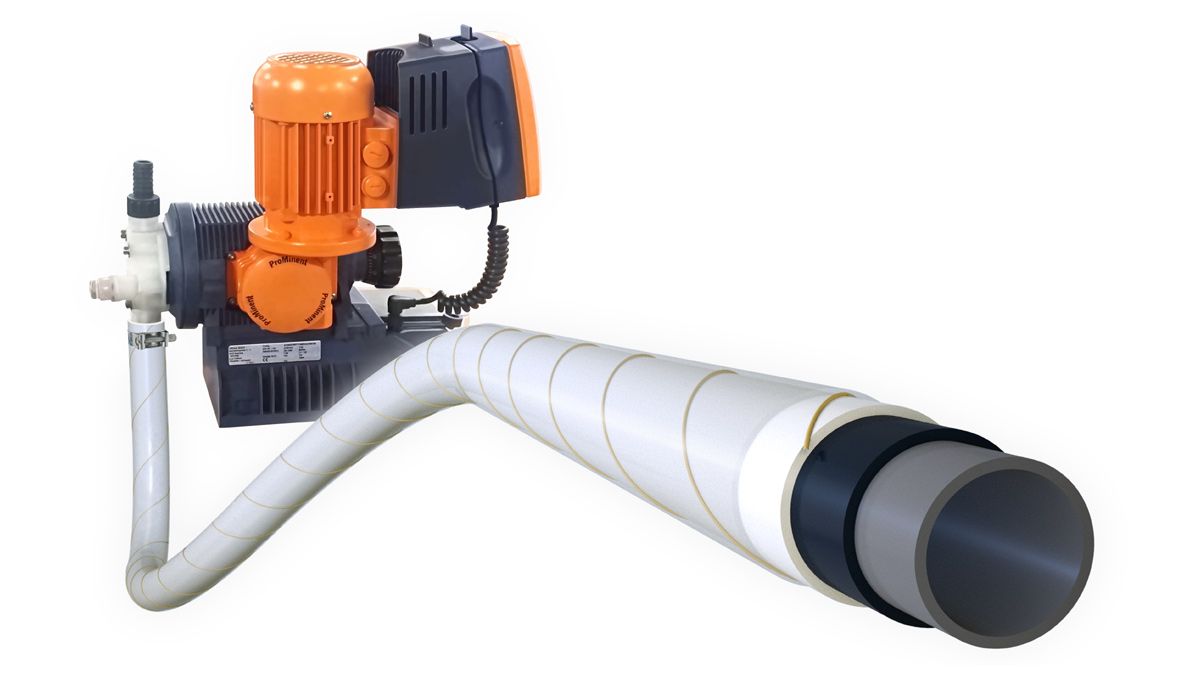
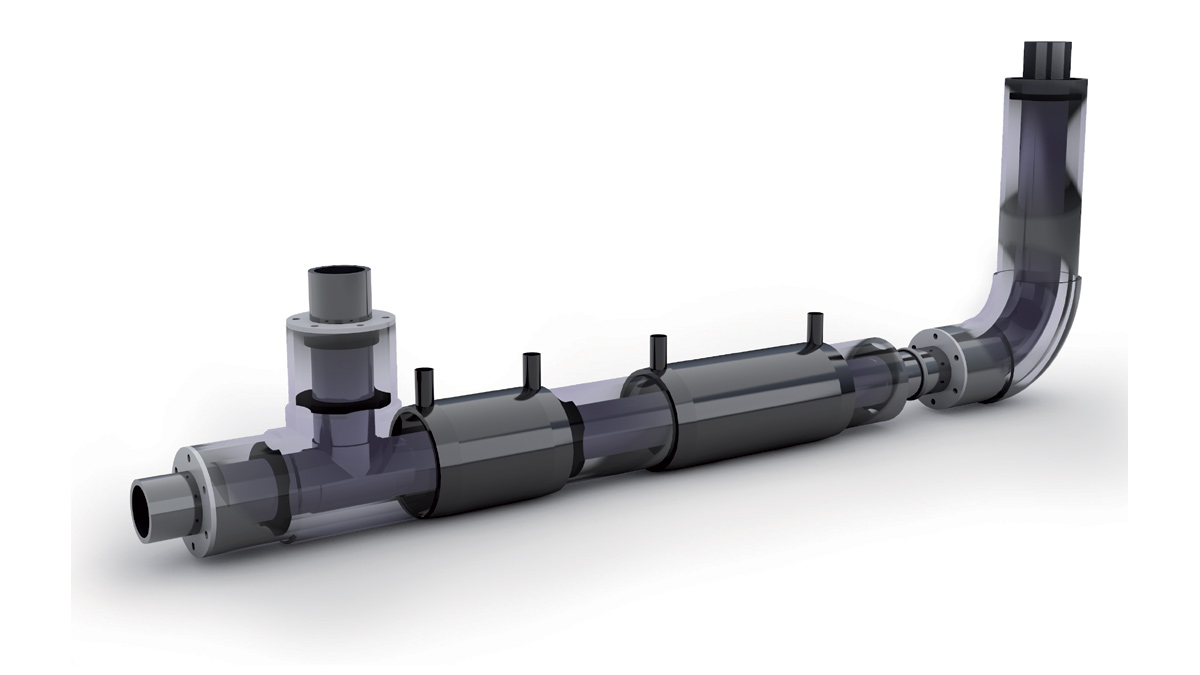
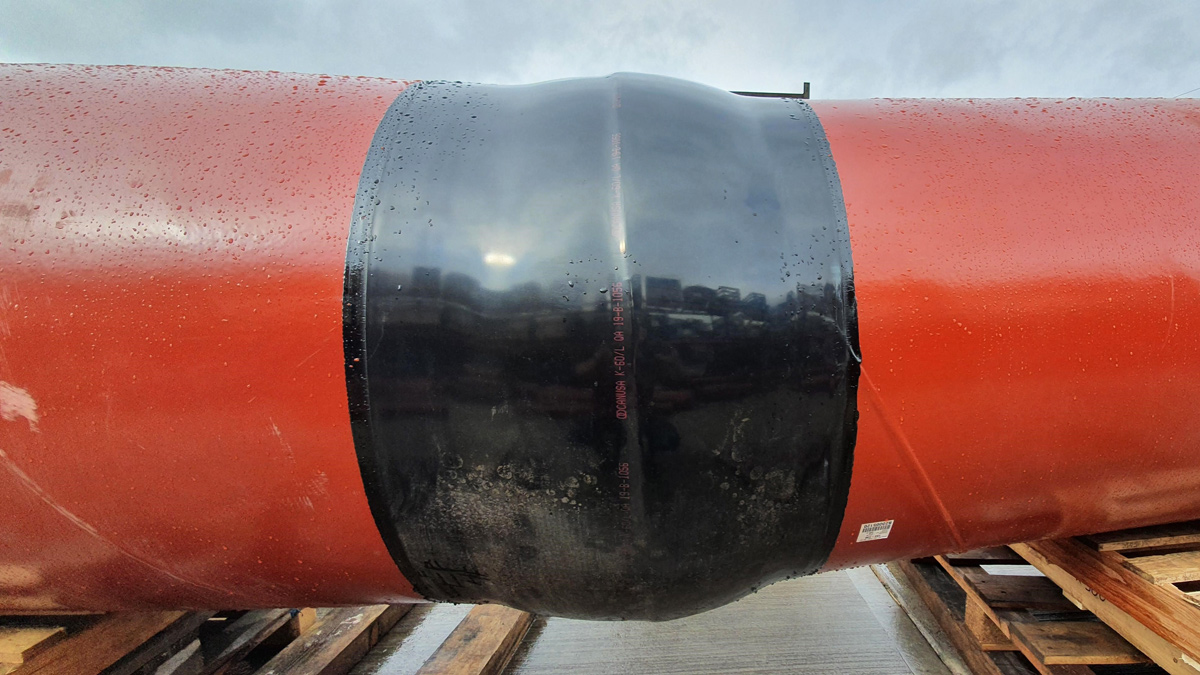
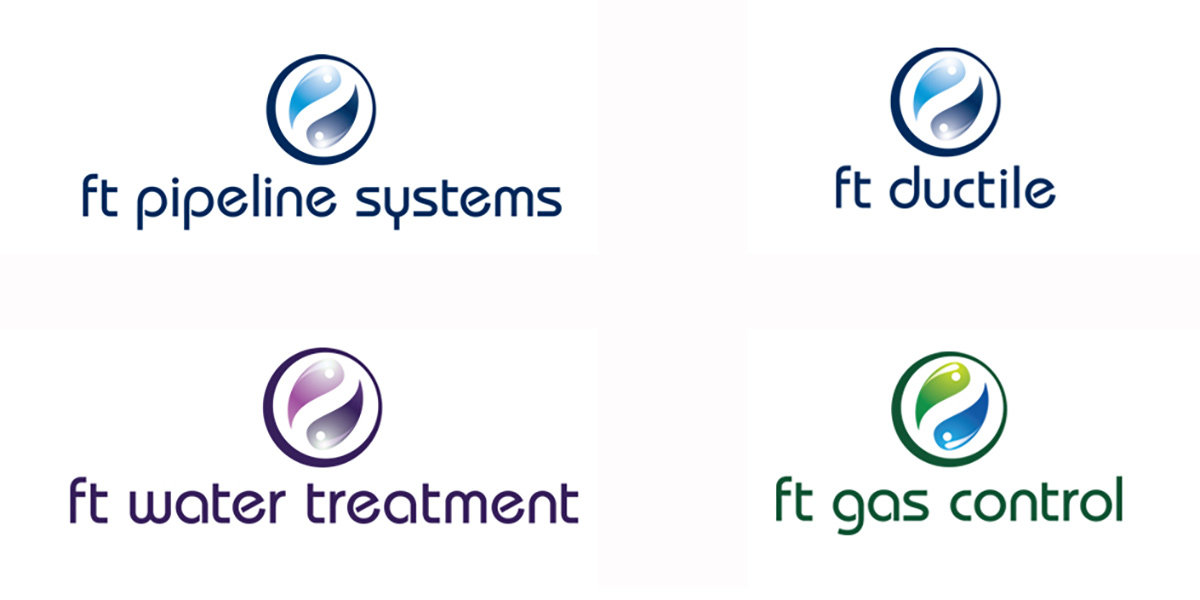