Seaham STW – Inlet Works Upgrade (2019)
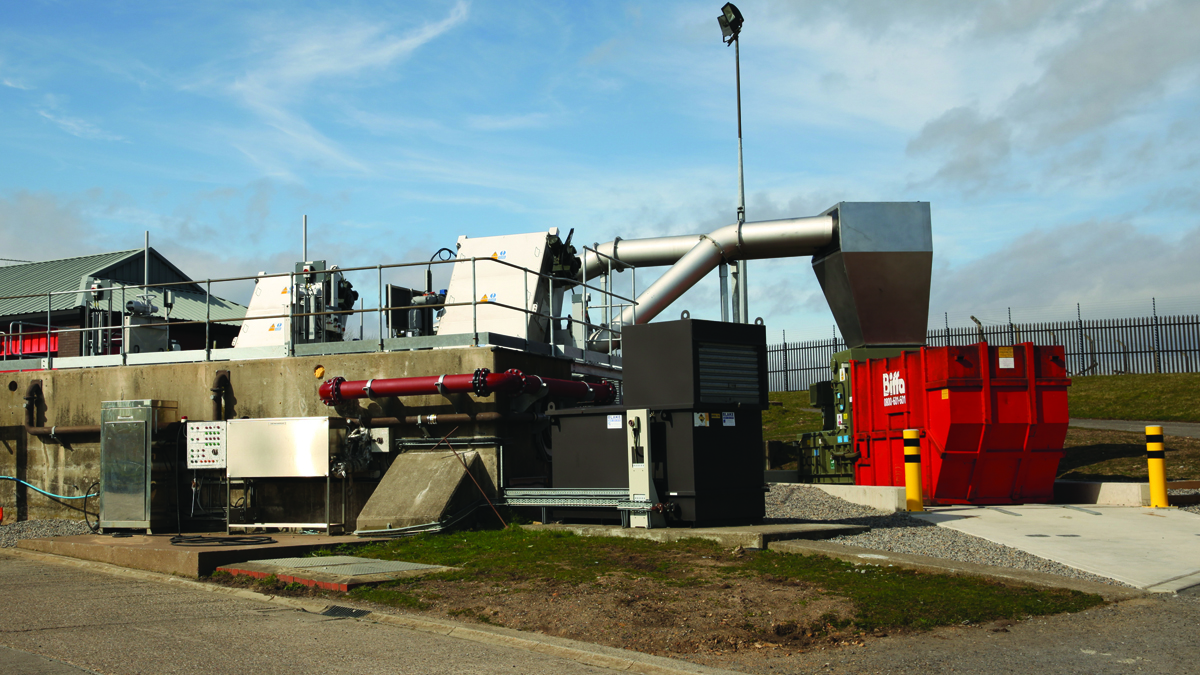
Upgraded inlet works - Courtesy of Mott MacDonald Bentley
Seaham Sewage Treatment Works (STW) receives and treats raw sewage from Seaham and the surrounding area. Constructed in phases between 1996 and 2001, the works serve a population of over 23,000 people. The works were originally built to ensure compliance with the Bathing Water Directive, as the site discharges directly into the North Sea via a long sea outfall, within close reach of two recognised bathing beaches. After over twenty years of service, the mechanical assets were being stretched far beyond the original design capacity, causing Northumbrian Water (NW) to incur increasing maintenance costs. In recent years, improvements to storm screens within the sewer network had reduced pollution incidents upstream of the works but had increased the solids loading on the inlet screens and screening system to beyond their original design capacity, accelerating the wear rate and leading to frequent blockages and breakdowns. These failures increase the risk of unconsented discharges into the North Sea and as such, have led to increased reactive maintenance costs.
Background
Northumbrian Water awarded Mott MacDonald Bentley (MMB) an Investigate and Define contract to review potential solutions, followed by a Design and Construction (D&C) contract. The solution included sequential demolition and reconstruction of the inlet works to enable migration from drum screens to more modern escalator screens. The original project cost estimate was £906k.
NW’s Project Sponsor set MMB a challenge to develop a design that would enable each operable drum screen to be decommissioned, removed and replaced with an operable escalator screen within just seven days to minimise the strain on the single remaining drum screen that would have to temporarily handle the full 330l/s flow rate during the works. The two screen types are very different in shape, size and configuration, significant remodelling of the inlet works structure would be required to facilitate the changeover, with no possibility of a works shutdown.
Seaham STW Inlet Works – Key participants
- Design & build: Mott MacDonald Bentley
- Band screens & screenings compactors: Longwood Engineering Co Ltd
- MCC modifications: Blackburn Starling Ltd
- Electrical Installation: Intelect (UK) Ltd
- Systems integration: Peak 42 Ltd
- Penstock installation: IQ Engineers Ltd
- Lagging & trace heating: Tees Insulation International
- Skip compactors: Thetford International
- Metalwork: Deritend
- Reinforcement installation: D&N Reinforcements Ltd
Technical engineering excellence and ingenuity
MMB reviewed lessons learnt at Cambois STW to identify potential constraints and opportunities for programme savings. A laser point cloud survey was used to create a detailed 3D Revit model of the existing inlet works.
The design team elected to represent the proposed sequence of works within the 3D model, identifying the extent and order of each phase of demolition and subsequent construction. This enabled the client, design and construction teams to visualise each of the key stages of demolition, construction and the temporary works required. Both the programme and model were developed concurrently, as the model was scrutinised for potential clashes and opportunities to simplify the sequence.
The model incorporated all mechanical equipment and was used to develop reinforcement schedules, pour volumes and sequences and was used in client meetings. This gave NW the confidence that MMB had developed an approach which would enable the site to continue to operate throughout the improvement works. To achieve design acceptance, a construction sequence video was produced to animate the process to the client maintenance and operations teams. This helped them visualise how the final structure would be accessed and operated both during and post construction.
Following commencement of construction, live updating of the model enabled the design team to anticipate any potential future effects from small changes and has ensured that highly accurate as-built information can be quickly developed upon completion.
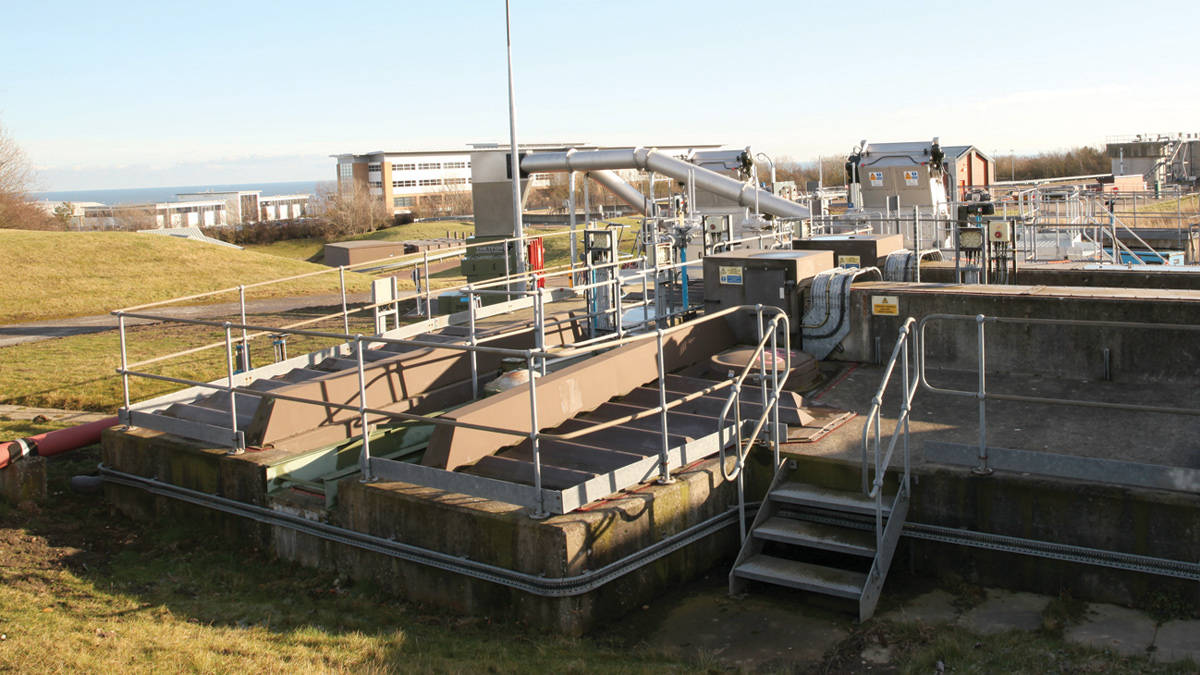
Upgraded inlet works – Courtesy of Mott MacDonald Bentley
Sustainability and environmental merits
Prior to the start of works, NW were incurring significant reactive maintenance costs relating to manual intervention of the screens and the associated macerator pumps. The total maintenance costs associated with keeping the screens running had exceeded £50k per year from 2013 and were projected to increase until catastrophic failure. Failure to intervene carried a major risk of unconsented, untreated discharges into the North Sea.
The use of the 3D model enabled accurate estimates of concrete volumes to be determined, which minimised on site wastage of concrete, reinforcement and formwork. The sequenced model was used to determine the penstock control procedure during construction works, used to aid installation and commissioning of the new screening equipment without any temporary overpumping, which has significant running costs and associated environmental risk. No bypassing of screens occurred at any point during the demolition, construction, installation or commissioning works and, critically, there were no occurrences of premature overflow to storm as a result of the works.
All mechanical equipment has been selected to be more efficient and capture a greater amount of solids, however, the installation of compactor units will minimise the space the screenings take up, which will reduce skip movements. Less solid matter passing into the downstream process will also have a beneficial effect on downstream process efficiency and the rationalisation of the procedures has had a net decrease on power demand.
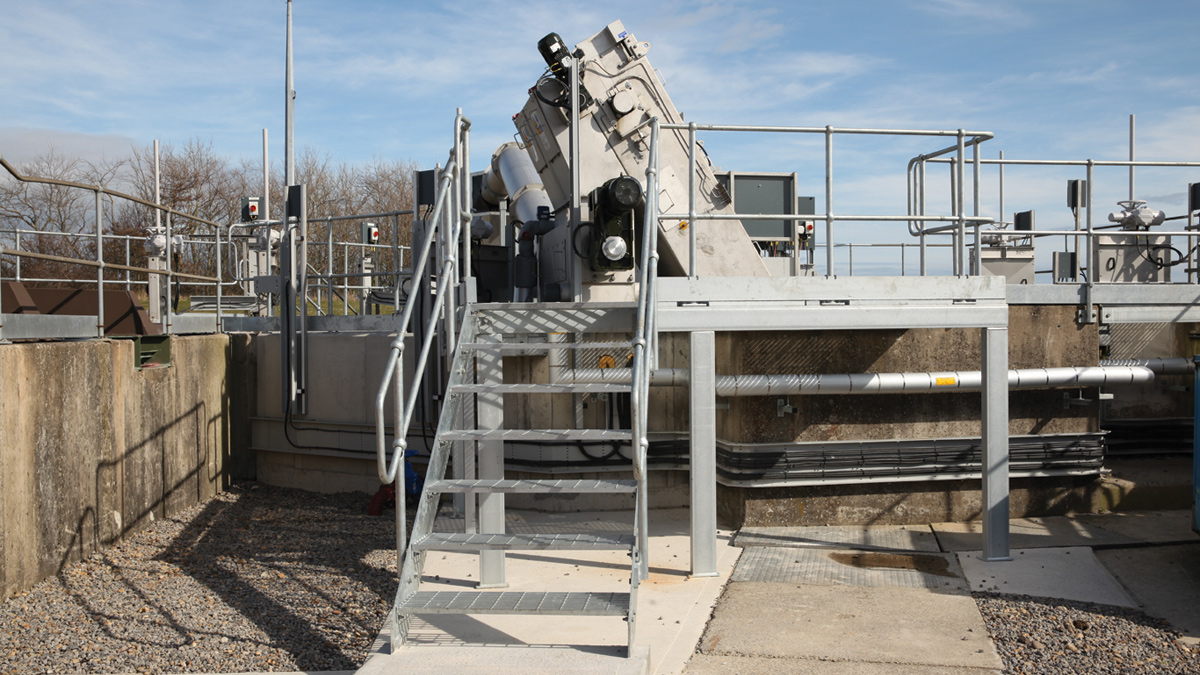
Access staircase to inlet works – Courtesy of Mott MacDonald Bentley
Approach to health and safety
Collaborative planning sessions were held with NW’s operations and maintenance team to demonstrate the proposals and to invite challenge, to ensure that meeting the challenge of installing the screens within a tight timeframe would not result in a configuration which could not be safely operated.
Aligned with the cost of the ongoing maintenance works were several health and safety risks involved. The reconfigured inlet works has reduced the number of mechanical processes involved in screening the sewage and utilises technology more frequently used across NW’s non-coastal sites, allowing for a more consistent approach to maintenance. All maintainable elements have been moved out of confined spaces, above the odour covers.
By involving the MMB Site Manager throughout the design process, buildability was considered at every stage of design. The model was developed to minimise temporary works where practical and identified key stages of the construction process where the construction risks, particularly falls from height, would be at their greatest. These risks were communicated to the site team through the drawings and enabled the site team to plan which stages would require temporary fall protection, such as when sections of handrail needed to be removed.
There were no lost time injuries or environmental incidents in over 16,000 hours worked, despite the complex nature of the construction works in a relatively small footprint.
A strong safety culture drove these results, evidenced by over 200 proactive H&S and environmental reports during construction by operatives, subcontractors, and visitors to site. To monitor, verify and maintain these high standards, regular Health, Safety and Environmental audits, inspections and behavioural discussions were undertaken.
Programme and budget
The D&C contract commenced in October 2017 with works on site commencing in July 2018. Construction works were completed in December 2018, beating the planned completion date of 19 February 2019.Lean planning techniques were employed throughout the design and construction phases. Identifying the project team at the start of the design phase, including the key construction personnel meant that potential ‘blockers’ were identified and confronted within design, reducing the potential for standing time on site.
Several buildability reviews were held between all parties to review the practicality of the developing methodology, ensuring that when the scheme finally reached site, all potential key interfaces had been determined, enabling a clear plan to be developed.
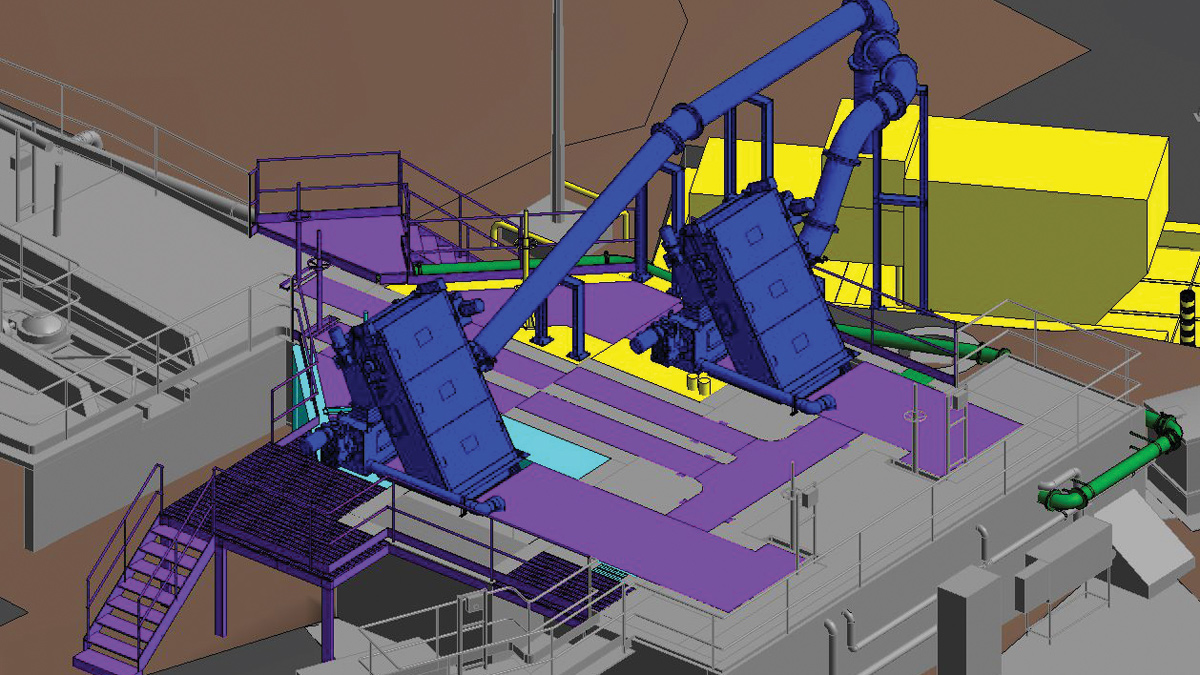
Phased 3D model – Courtesy of Mott MacDonald Bentley
CLIP planning meetings were held between designers, client, construction teams and key suppliers to minimise durations of key shutdowns and to promote the criticality of our constraints with our suppliers and subcontractors. This led to great relationships forming between suppliers; one positive example resulted in our electrical installer carrying out pre-wiring works within the screen manufacturer’s facility, reducing the number of contractors on site during a critical section of works and greatly reducing the installation time.
During these meetings, the sequenced model was utilised to incorporate subcontract installations, including cable routing and isolator locations. This ensured that any potential clashes were identified in design and mitigated prior to construction works commencing.
The works were completed 34 working days ahead of the construction programme in December 2018. All works have been completed without any shutdowns thanks to the carefully managed construction sequence.
The D&C contract has been delivered within the target cost, which can be attributed to strong collaboration between all parties, identifying key risks, constraints and opportunities.
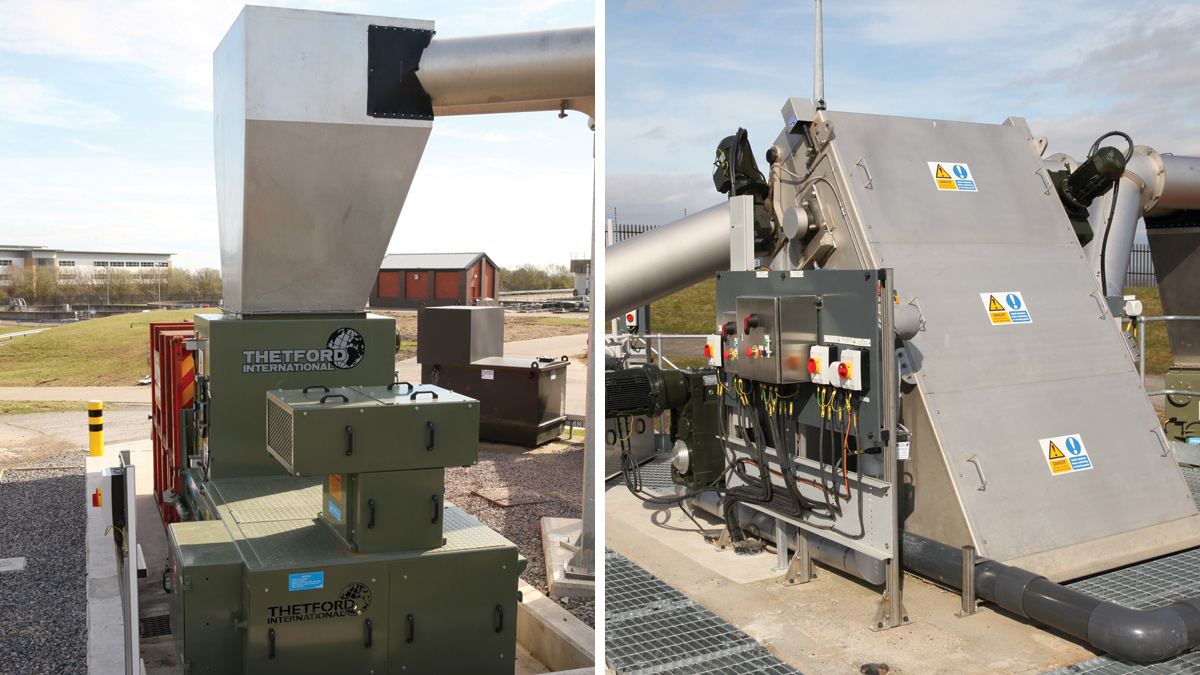
(left) New screenings compactor and (right) Completed inlet screen – Courtesy of Mott MacDonald Bentley
Community benefit
One of the key drivers was to minimise the risk of uncontrolled pollution events at Seaham Beach, which has maintained a consistent ‘excellent’ bathing water rating and is recommended by the Marine Conservation Society’s Good Beach Guide.
The improvement works to the screens enables the full flow capacity to pass through a single screen, which gives additional resilience to maintenance issues, particularly during higher flows. This enables the site to consistently draw down the main works pumping station and treat flows that could otherwise have discharged untreated via the works overflow into the North Sea.
The improvements to screen efficiency will reduce the solids load on the downstream process and ultimately increase the quality of the effluent discharging to sea.
Despite the increase screenings removal, the two-stage compaction will also reduce the number of skips required at the site, which will reduce vehicle movements to and from Seaham STW. The skip compactor is a sealed unit, which means that skip changeover will no longer result in odour release, which has led to complaints on other sites.
Conclusion
Through strong collaboration, several key risks were identified and mitigated, to ensure the project was delivered within the constraints. The use of a 3D model to plan and sequence the works enabled the wider core team to fully engage with each stage of the process and to identify opportunities to improve on the programme.