Oldham & Royton Integrated Strategy (ORIS) (2020)
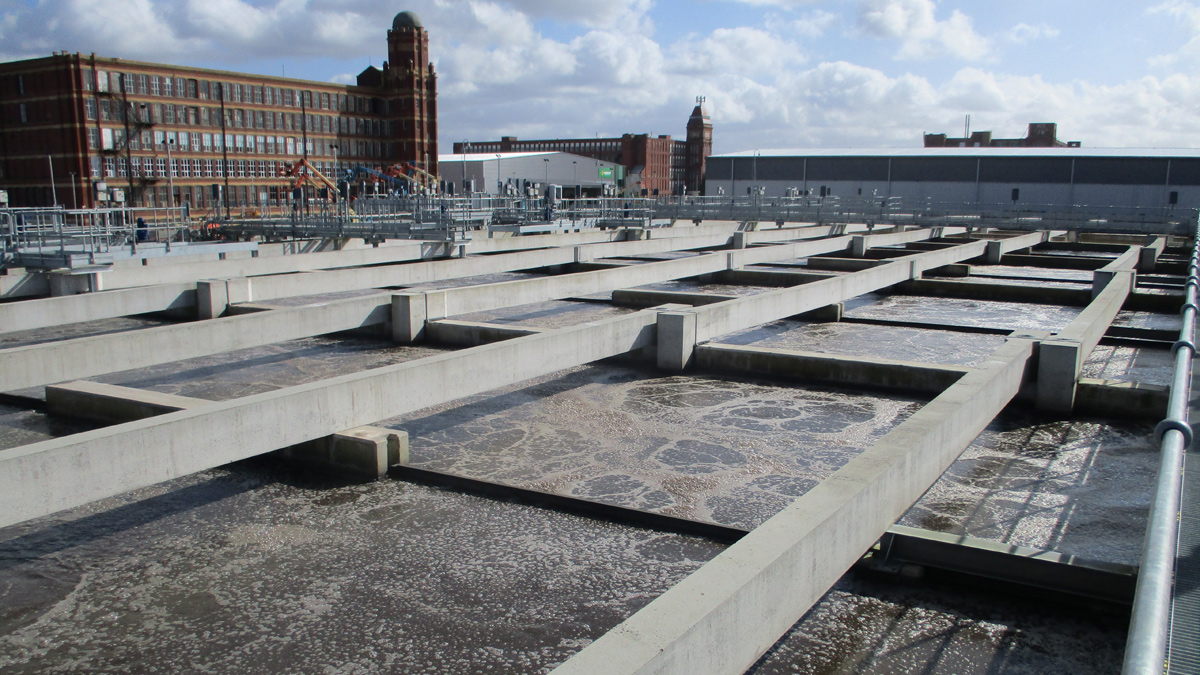
Oldham aeration lanes – Courtesy of Black & Veatch
United Utilities is the regional water company for the North West of England, delivering water and wastewater services to 7m people from Cheshire to the Scottish border. Oldham WwTW and Royton WwTW are two major wastewater treatment works located in Oldham, to the north east of Manchester. The Oldham and Royton Integrated Strategy (ORIS) project combines both wastewater network and wastewater treatment regulatory drivers at these two works into a single integrated solution. The backbone of the solution is to close Royton WwTW, transfer flow 4.2km to Oldham and upgrade Oldham WwTW to treat the combined flows to meet a higher river water quality standard. At both sites, additional storm storage is also required to reduce storm discharge. The main construction contract was awarded to Black & Veatch in spring 2015. At the time of writing (June 2020) the construction works are complete, and the commissioning and optimisation phases are in progress.
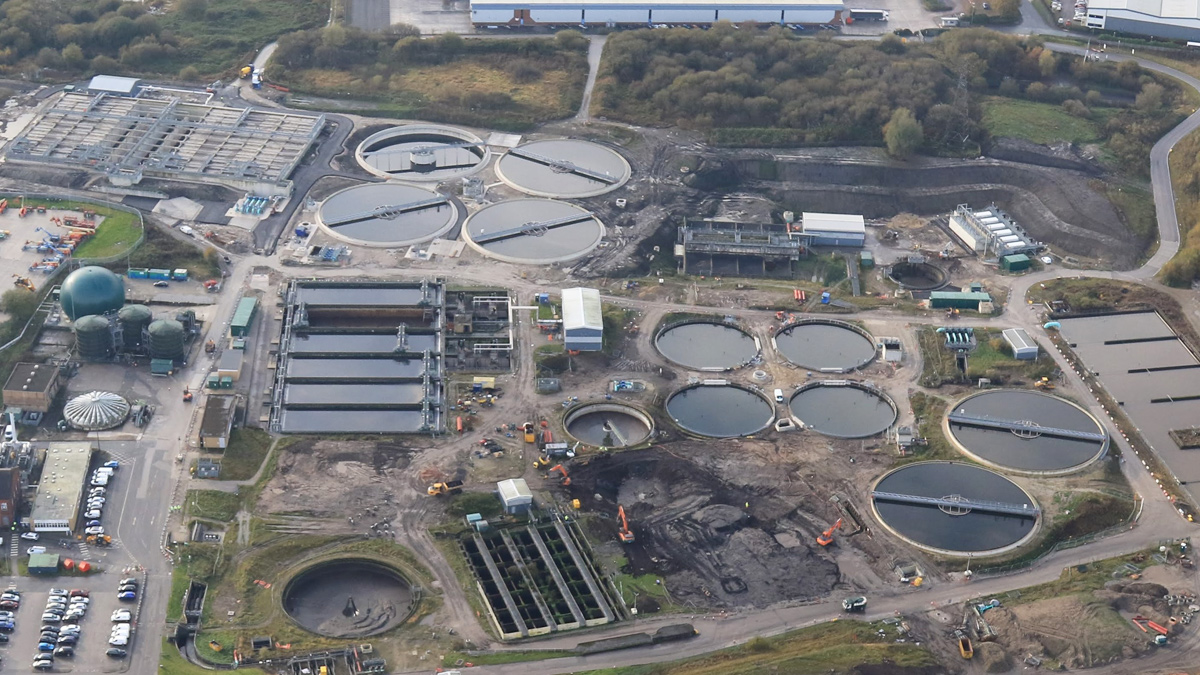
Overview of the Oldham WwTW site – Courtesy of United Utilities
Project key facts
- Client: United Utilities
- Project approved budget: £78m
- Main contractor: Black & Veatch
- Procurement strategy: OJEU competitive tender
- Form of contract: Design & Build, I Chem E Red Book
- Construction man-hours worked to date: approximately 1,280,000 (RIDDOR free)
Background and need
Both Oldham WwTW and Royton WwTW discharge final and storm effluent to watercourses that are tributaries of the River Irk, and both have regulatory requirements to improve the river water quality. Oldham WwTW has a population equivalent of 157,000 and Royton WwTW 28,000. The Oldham and Royton Integrated Strategy was born out of two regulatory drivers.
- Oldham WwTW Freshwater Fish Directive (FFD): Oldham needs to meet a new tighter final effluent consent of 6 mg/l BOD and 1 mg/l Ammonia (from 15 mg/l and 2 mg/l respectively) to meet the Freshwater Fish Directive.
- Oldham and Royton Storm Tank UIDs: Both Oldham WwTW and Royton WwTW storm discharges are classified as UIDs (unsatisfactory intermittent discharge) with a target to improve the River Irk.
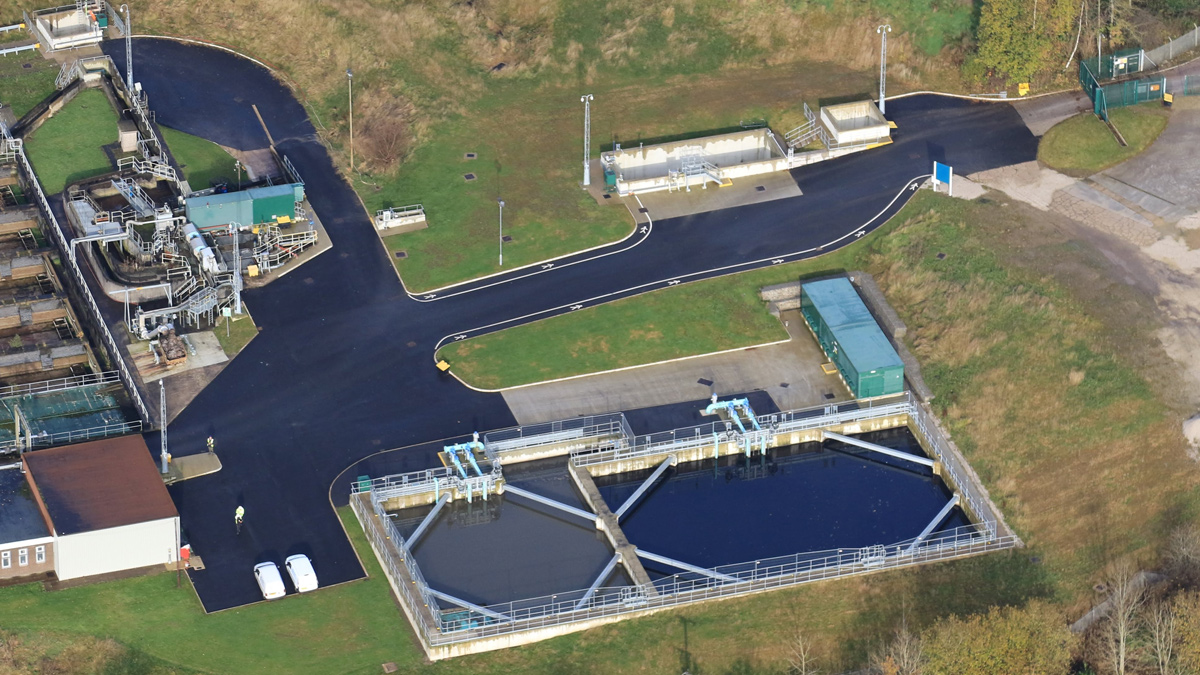
Overview of the Royton CSO and detention tank – Courtesy of United Utilities
In addition, many of the assets at both Oldham WwTW and Royton WwTW have passed their asset life and are in need of significant refurbishment and maintenance in the near future.
ORIS – Key participants: Designers and contractors
- Main contractor & designers: Black & Veatch
- Sub-consultant designer: GHD
- Royton site and transfer main package: Farrans Construction Ltd
- Structures sub-contractor: N.J. Doyne Ltd
- Large buried pipework sub-contractor: SGC Civil Engineering Ltd
- Small buried pipework sub-contractor: SB Utilities Ltd
- Main mechanical sub-contractor: Industrial Pipework Services
- Main electrical sub-contractor: Lloyd Morris Electrical Ltd
- HV electrical installation: Winder Electrical
- Access metalwork: Steelway Fensecure Ltd
- Primary settlement tank bridges: JK Fabrications
- Hydrotech Discfilters: Veolia Water Technologies
- External works: Byrne Civil Solutions Ltd
- Systems integrator: Tata Consultancy Services Ltd
- Royton storm tank temporary works design: OGI Groundwater Specialists
- Temporary over-pumping: Alba De-Watering Services Ltd
Design matters
Black & Veatch are delivering the ORIS project using a BS1192 configured Common Data Environment (CDE) – Bentley ProjectWise, hosted by United Utilities. The company has built a 3D model of Oldham WwTW with Navisworks software, which has been extremely useful, particularly when threading proposed large diameter gravity buried services through a complex arrangement of existing live buried services whilst minimising diversions. The 3D modelling has also proved invaluable at safety in operation and access, lifting and maintenance review meetings, and the as-built version will form a key component of the project BIM information. Hydraulic modelling for the interconnecting process pipework at Oldham has been carried out by Black & Veatch in-house with the aid of computational fluid dynamic modelling for ASP flow delivery and distribution. Black & Veatch have undertaken the sewer network modelling in-house with their specialist team based in Redhill, Surrey.
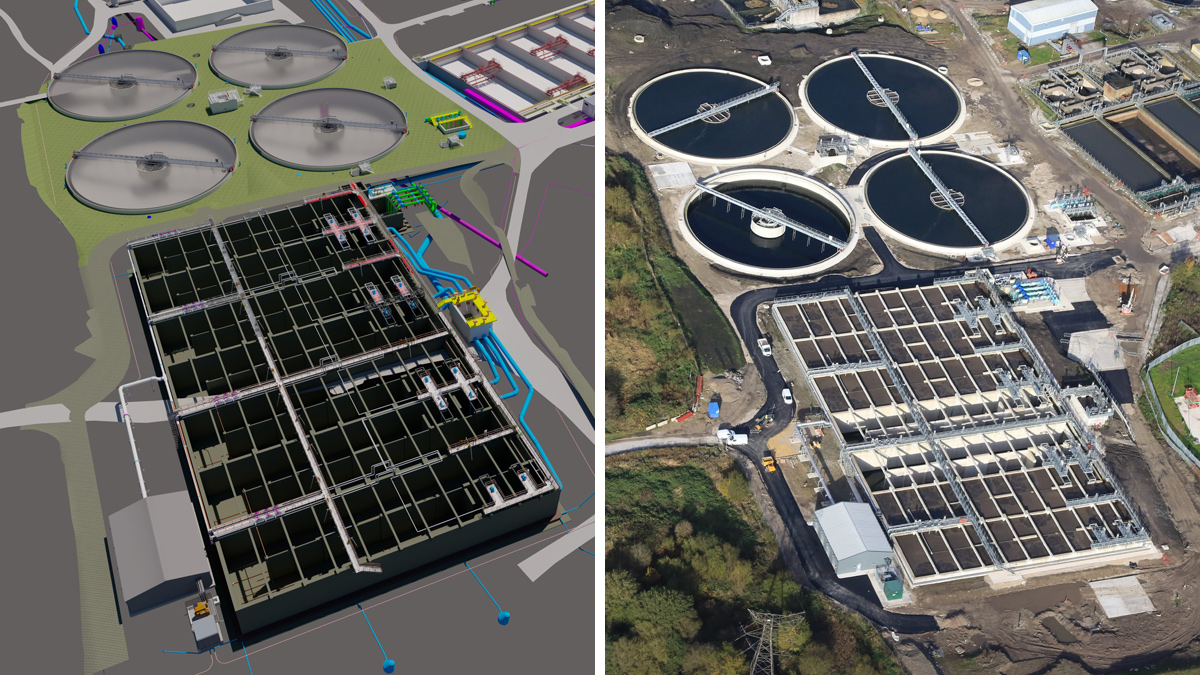
(left) Extract from the 3D model showing the Oldham ASP and FST 1-4 – Courtesy of Black & Veatch, and (right) aerial photograph of the constructed ASP and FSTs – Courtesy of United Utilities
Black & Veatch used Bentley Open Plant software to create the piping and instrumentation diagrams for the scheme to integrate the plant data within the schematics, and from which schedules of equipment and commissioning activities could be created.
The 4.2km pipeline design was undertaken by GHD Ltd, based in Cheadle. The pipeline has a number of level undulations along its length and is designed to operate in a batched sequence; it has a header tank at the higher elevation Royton WwTW end, and control valves at the lower Oldham WwTW discharge end.
Pipeline construction
To transfer flows of 325 l/s between Royton WwTW and Oldham WwTW, a new ductile iron gravity pipeline has been constructed and was successfully introduced to service in January 2020. This 600mm diameter, 4.2km long pipeline falls 24m from Royton to Oldham.
The pipe route was selected to minimise traffic disruption avoiding highways where possible, with as little as 600m laid in roads. To help achieve this three sections of pipe have been installed in tunnels driven from shafts using a tunnel boring machine of 1450mm diameter to give a 1200 internal diameter PCC tunnel through which the pipe was pushed in clamped sections. Directional drilling techniques have also been utilised for installation of fibre optic communication cables.
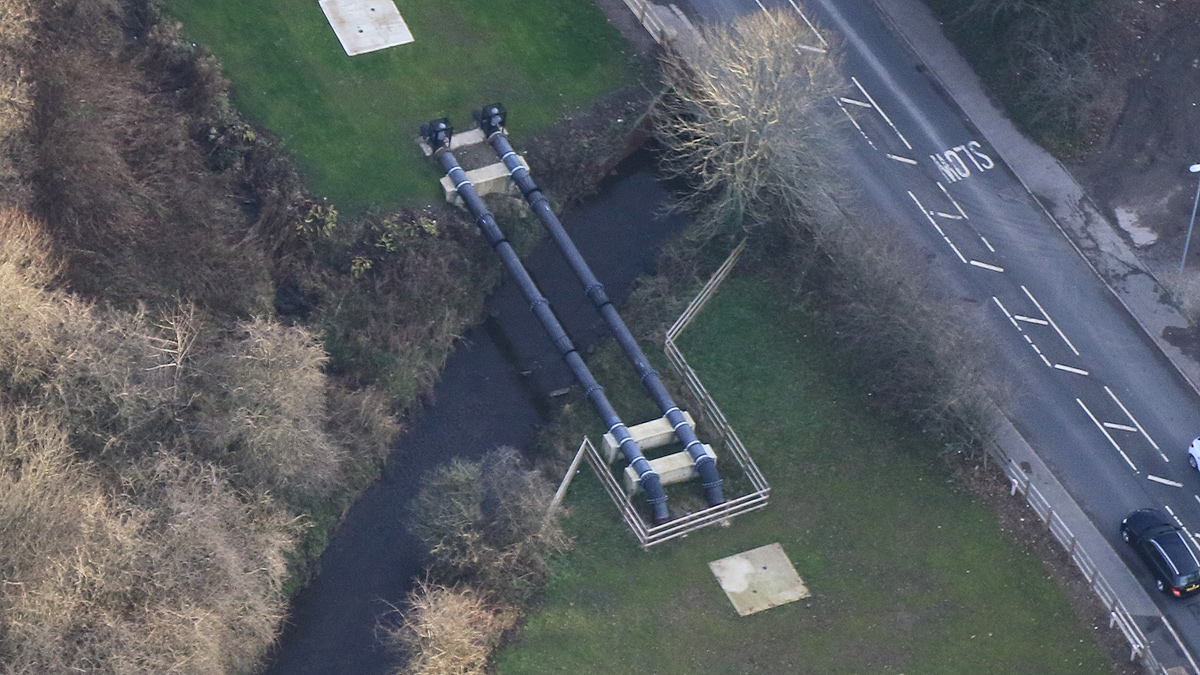
Transfer main twinned pipe bridge over the River Irk – Courtesy of United Utilities
The pipe crosses three water courses; the River Irk, twice, on pipe bridges and the Wince Brook where the pipe will be laid under the brook by open cut methods using aqua dams for flow control. The pipeline is twinned on the pipe bridges to provide resilience.
Royton WwTW construction
The scope of works at Royton WwTW included:
- New inlet combined sewer overflow (CSO).
- Retain existing inlet works.
- New FTFT (flow to full treatment) control set to 325 l/s.
- New storm outfall to River Irk.
- New 7,280m3 storm storage (detention tank).
- Associated HV and LV systems.
- Telemetry.
- Demolition of redundant assets.
At Royton WwTW construction is complete of the 7,280m3 capacity new detention tank, CSO and header tank to feed the gravity transfer main to Oldham WwTW. Works were constructed within the existing operational treatment plant with the majority of the construction being off-line to minimise impact on normal operation of the plant. The existing inlet screening and detritor are retained maintained and the redundant plant is being demolished and landscaped.
The reinforced concrete detention tank has been constructed in situ and measures 47.7m by 21.8m on plan and is 9.46m deep internally with external walls 900mm thick and standing 10.46m high overall. The base slab is 1m thick and the total volume of concrete poured for this structure is 2,750m3.
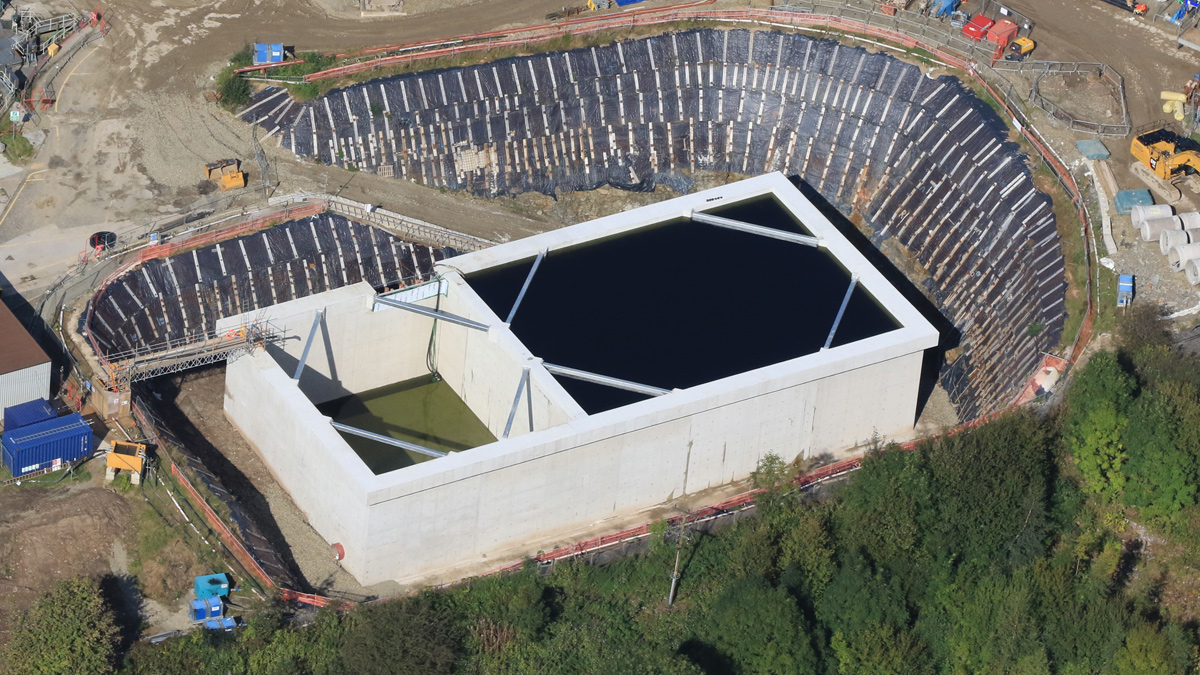
Royton detention tank prior to backfill showing the reinforced excavation temporary works installation – Courtesy of United Utilities
The tank has been constructed within an excavation with depths from 9m to 14m through made ground, soils and rock. In all 22,000m3 has been excavated and will be reused to fill abandoned structures and to landscape the site.
Space constraints, significant groundwater and the presence of rock resulted in a challenging temporary works design. The solution entailed the construction of a reinforced excavation face through installation of steel reinforcing mesh, timber wailers and ground anchors which allowed for a cut face at 55 degrees (or 1 in 0.7).
Oldham WwTW construction
The scope of works at Oldham WwTW included:
- Reception of new transfer pipeline.
- Retain existing inlet works.
- New FTFT control increased to 2,245 l/s (an increase of 25% compared to current FTFT).
- Refurbishment of existing primary settlement tanks (PSTs) including new scraper bridges.
- New fully nitrifying activated sludge plant (ASP): 7 lanes with anoxic zones.
- New 6 (No.) deep final settlement tanks (FSTs): 46.7m Diameter, 7.6m deep at deepest point.
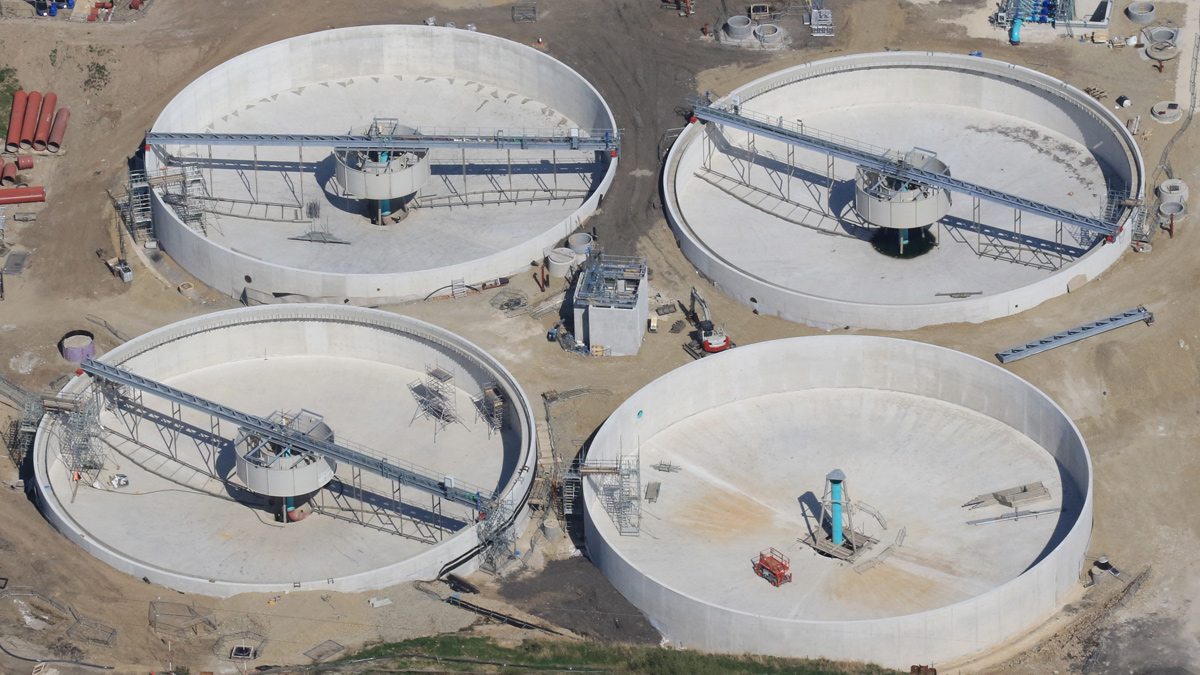
Oldham FST 1-4 (April 2019) – Courtesy of United Utilities
- Tertiary filtration by 6 (No.) Hydrotech Discfilters from Veolia Water Technologies.
- New SCADA for the full site, including sludge processing areas, Royton WwTW and the transfer pipeline.
- Upgrade to HV systems.
- Telemetry.
- Additional 11,800m3 of storm storage provided by converting existing (but redundant) final settlement tanks into storm tanks.
- Demolition of redundant assets.
Construction of the new works at Oldham WwTW are substantially complete. The process is now fully operational and is currently undergoing performance and optimisation trials. The new works includes refurbished 6-lane PSTs, a new interstage pumping station, 7-lane ASP with anoxic zones, 2 (No.) RAS pumping stations, 6 (No.) 46m diameter FSTs and a Discfilter tertiary treatment plant. All are sized for the combined full treatment flows from both Oldham and Royton. The new works were constructed whilst maintaining the operation of the existing process streams throughout.
ORIS – Supply chain: Process plant and equipment
- Aeration plant: Suprafilt Ltd
- Penstocks: Glenfield Invicta
- Valves: Industrial Valves Ltd
- Hydrostatic valves: Ham Baker Ltd
- GRP kiosks: Morgan Marine
- Storm tank jet mixers: KSB Ltd
- Pumps: Sulzer Pumps UK Ltd
- Wash water pumpset: Grundfos Pumps Ltd
- De-sludge pumps: Hidrostal Ltd
- Anoxic tank mixers: Aquasystems International NV
- Storm overflow screen: The Longwood Engineering Co Ltd
- Ductile iron pipework: Saint Gobain PAM UK
- Ductile iron pipework: Electrosteel Castings (UK) Ltd
- Lightning installation: BEST Services Ltd
- Hydrotech Discfilters: Veolia Water Technologies
- CopaTrawl screen: Jacopa Ltd
- CopaTrawl lifting gantry: ABUS Crane Systems
The existing rectangular primary settlement tanks have been fully refurbished. Works included the replacement of the scraper bridges and rails, de-sludge pumps, concrete repairs and the construction of a new concrete outlet channel for connection to the new ASP. Construction sequencing of the PSTs was optimised using collaborative planning workshops with UU, Black & Veatch and the key sub-contractors.
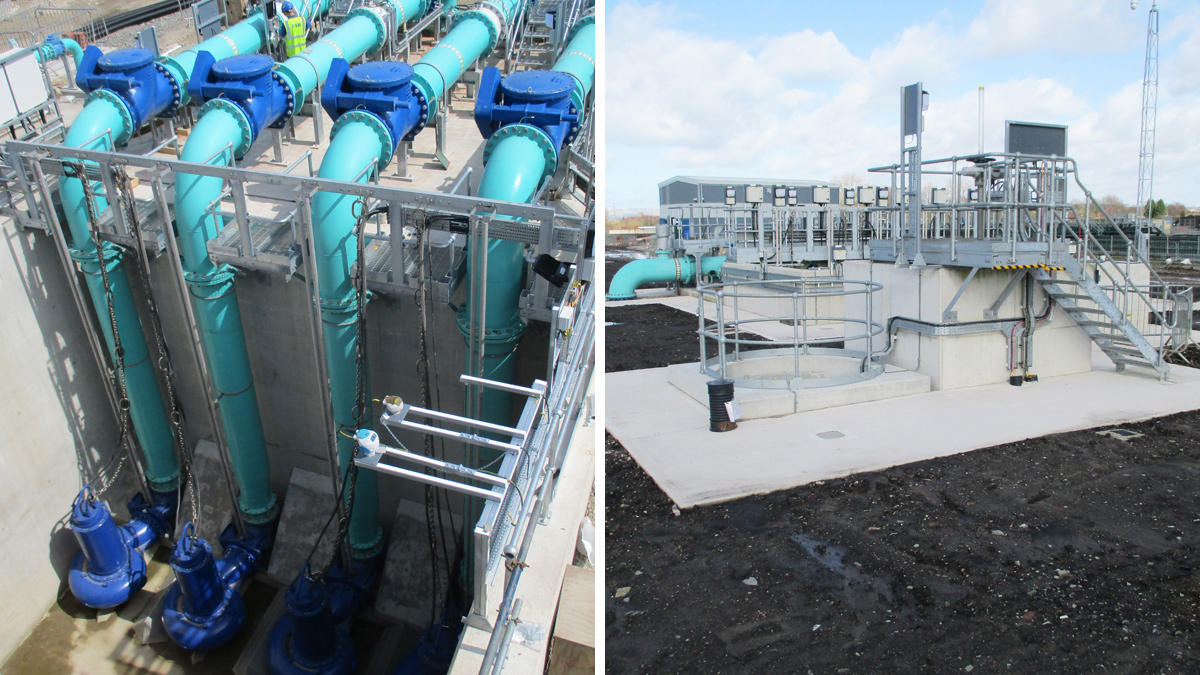
(left) Oldham Interstage Pumping Station and (right) Oldham FST de-sludge adjustable bellmouth chamber and RAS Pumping Station No.1 – Courtesy of Black & Veatch
The new process structures and pipelines were constructed within the limited remaining space on the Oldham site, including on the location of a disused sludge lagoon which contained high levels of heavy metal contaminants. The lagoon had a surface area of 9250m2 and was up to 6m deep, this was underlain by a further 5m of very soft made ground. Initially dredging and Geobag dewatering was used to thicken the sludge however the material did not behave as expected. Consequentially the methodology was changed to screening and centrifuge dewatering prior to removal from site for use in land reclamation. The soft soil layer was strengthened using mass soil stabilisation techniques, the soil being mixed in situ with a cementitious grout to produce a material suitable for reuse within the site landscaping. A total of 46,000 tonnes of sludge was removed from site, 80,000m3 of soil was excavated and 117,000 tonnes of aggregates were imported to remediate the lagoon area in preparation for the construction of the new ASP and FST structures.
ORIS – Supply chain: Civil engineering and building
- Sludge lagoon processing: Trade Effluent Services Ltd
- Demolition: PP O’Connor Group Ltd
- Storm return pumping shaft: EJ Kelly Construction Ltd
- Treatment of soft soils: Ground Developments Ltd
- Concrete repairs & concrete cutting: RAM Services Ltd
- Concrete repair surveys: Pebble Engineering Ltd
- Piling: SPI Piling Ltd
- Sheet piling/temporary works: SPI Appleton Ltd
- Blower building: JB Fabrications (Wrexham) Ltd
- ASP PCC tie beams: Ebor Concrete Ltd
- Precast concrete: Tracey Concrete
- PCC panels: FP McCann Ltd
- Time lapse cameras: Site Eye
The 7 lane ASP is an in situ reinforced concrete structure with precast concrete baffle walls. The structure is 101.7m long and 59.1m wide with a wall height of 7.9m. The in situ walls are tied using 16m long precast concrete tie beams to produce a more efficient design.
The 6 (No.) FSTs are 46m diameter with a 5 degree sloping base and a wall height of 5.9m, giving a total depth of 7.6m at the edge of the centre hopper and are fitted with a rotating full bridge scraper.
The tertiary treatment process incorporates a CopaTrawl screening structure from Jacopa and a 6 (No.) Veolia Hydrotech Discfilter installation.
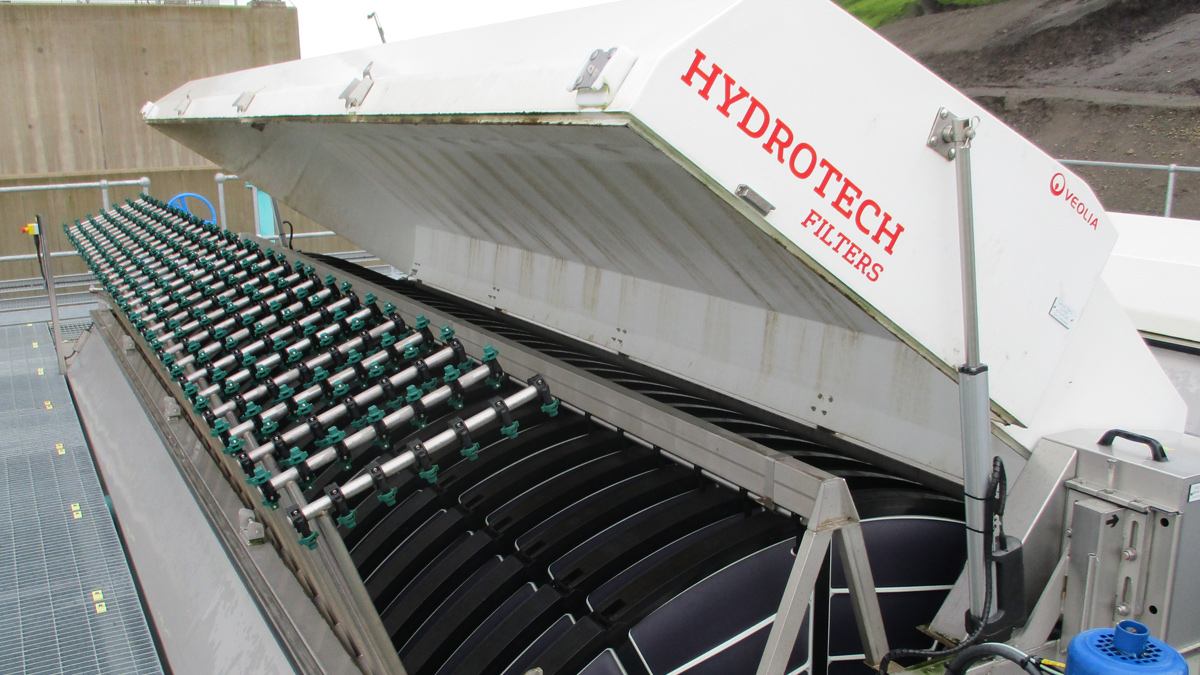
Oldham Hydrotech Discfilter – Courtesy of Black & Veatch
In addition to the new process structures a new HV ring main and wash water system has been installed to cover the whole site and a SCADA system for the combined works and interconnecting pipeline.
The stormwater storage capacity of the works has been increased by 11,800m3 by converting 4 of the existing final settlement tanks into storm tanks. Collaborative planning exercises identified that a 5-month programme saving could be achieved by the early conversion of the storm tanks. This was achieved by bringing 2 of the new FSTs into service early requiring the installation of a significant over-pumping system to transfer up to 1873 l/s of mixed liquors using 6 (No.) 12” electric submersible pumps with an automated control system.
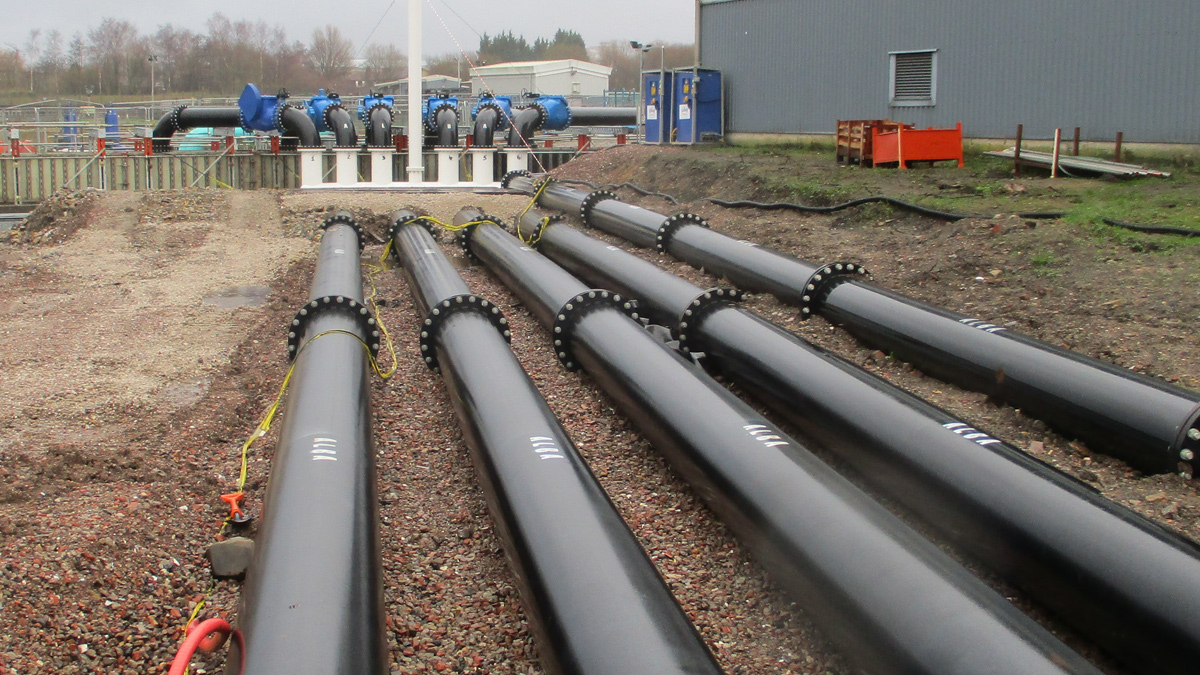
Oldham temporary 1873 l/s over-pumping installation for the storm tank conversion – Courtesy of Black & Veatch
ORIS – Supply chain: Instrumentation
- Instrumentation & ASP real time control: Hach
- Instrumentation: Process Instrumentation
- Instrumentation: Siemens
- Instrumentation: Endress & Hauser
- Inlet works flow measurement: RS Hydro
Commissioning
The works have been commissioned by the experienced in-house Black & Veatch commissioning team. The Process Establishment and Reliability Trials period has been completed and the project is currently (June 2020) in the Performance and Optimisation phase.
The 4.2km transfer pipeline process control system was optimised to ensure that self-cleansing velocities are achieved throughout the full flow range by controlled batching to maintain a primed main. The system is configured to ensure that full treatment flows are transferred from Royton to Oldham without any spurious early spills into the Royton detention tank and is set with a failsafe condition to transfer the maximum design flows.
As flows were increased to the FSTs during the commissioning stage oscillations in the feed pipelines to four of the FSTs were observed. These threatened to unbalance the equal flow distribution between the tanks and to compromise the settlement within the tanks. It was suspected that the cause was air accumulation in the pipelines. Black & Veatch hydraulic engineers built a detailed CFD model of the arrangement and analysed it to establish the causes, which comprised multiple contributing factors. Options to vent the air out of the pipelines were considered and modelled to assess predicted performance. The designers collaborated with the Black & Veatch site team and the supply chain to identify and refine the most cost-effective solution. Ultimately, a pipe sleeve with an incorporated vent arrangement was installed within each of the (4.5m high) drop pipes. These were installed within shutdowns of individual FSTs, allowing the process to remain live during the fix.
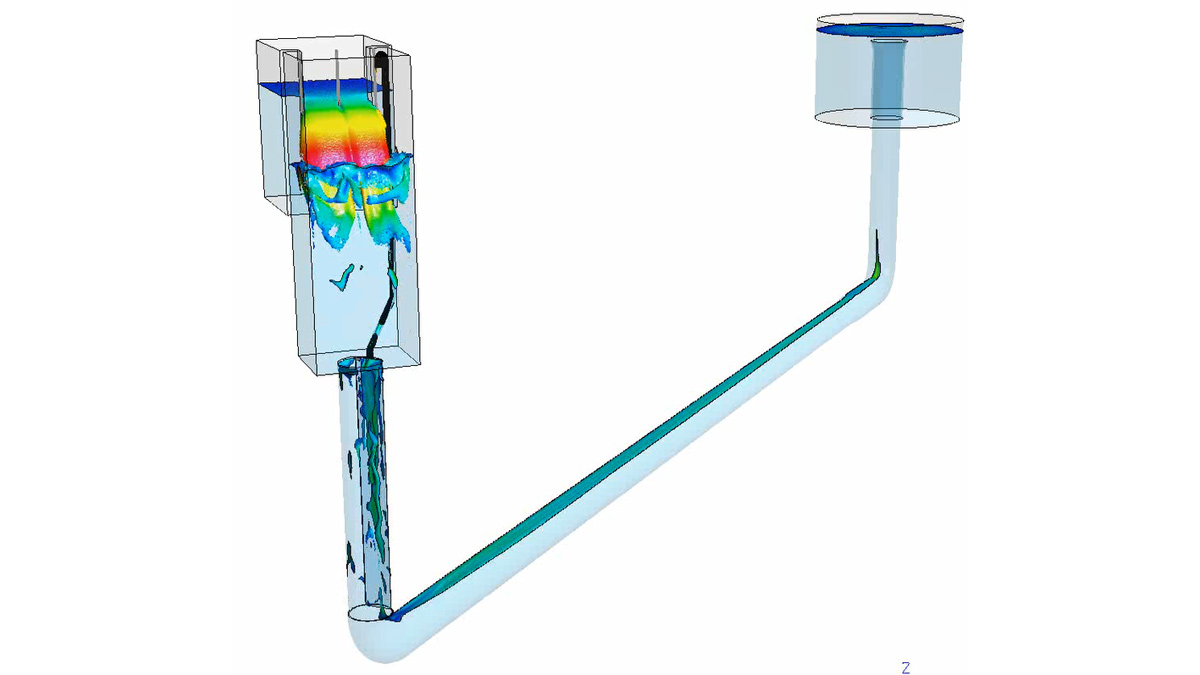
CFD modelling of the vented pipe sleeve solution to the air accumulation issue in the Oldham FST feed pipework – Courtesy of Black & Veatch
Conclusion
The plant has easily achieved the tightened consent for the works. The new plant incorporates real time control of the activated sludge plant and includes a highly efficient diffused aeration system that reduces power demand whilst meeting the tightened consent. The design is based on a year 2036 design horizon for catchment growth and anticipates the future updating of the current sludge processing system on site by incorporating features to facilitate the potential upgrades.