Uig WTW (2020)
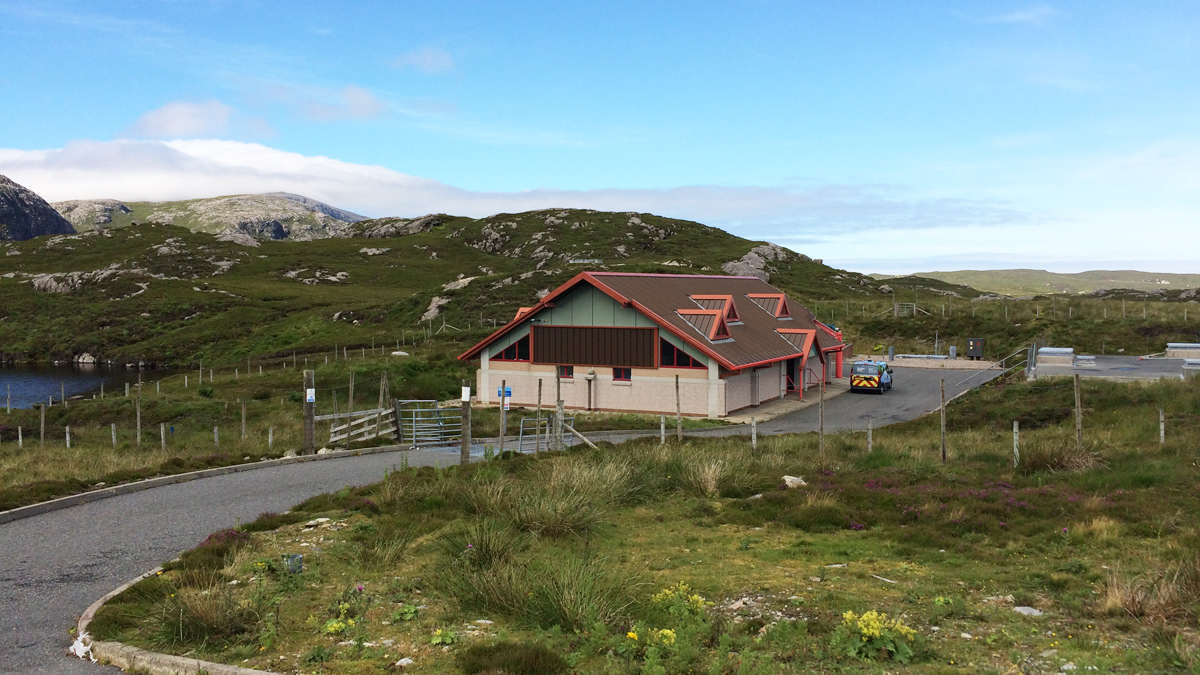
Uig WTW - Courtesy of ESD
Uig WTW is located on the west coast of Lewis and provides potable water to the community of around 500 residents, with a significant tourist increase in the summer months. The works are gravity-fed by a high-level loch around 2km from the site. Treated water is then pumped from the water treatment works to a storage reservoir on the surrounding hills from where the dispersed community is served by gravity.
SR15 Non-Infrastructure Programme
Significant capital upgrade works are being delivered for Scottish Water by Efficient Service Delivery (ESD); a Galliford Try, MWH Treatment and Binnies Joint Venture formed in order to manage, design and deliver Scottish Water’s SR15 Non-Infrastructure Programme. The Uig WTW project is one of a number of projects being undertaken in this programme where ESD has been able to demonstrate the benefits of the Alliance’s delivery on key tender offerings including Design for Manufacture and Assembly (DfMA) and collaboration with Scottish Water and its supply chain.
Existing works and drivers
The raw water is a typical highland soft water which suffers from seasonal colour, lack of alkalinity and low pH. The existing process consists of chemical conditioning by aluminium sulphate and soda ash dosing for coagulation. Filtration is then provided by two continually washed Dynasand sand filters. The water is then disinfected with sodium hypochlorite before passing to an on-site balancing tank. After the balance tank, the water is further dosed with ammonium sulphate and soda ash for chloramination and final pH correction, before being pumped to the off-site clear water tank.
The treatment works has drivers for capital maintenance and water quality. The capital maintenance is in relation to the existing chemical dosing plants, many of which are the original units fitted when the works were built in the 1980s. While these are still functional, they no longer comply with the Scottish Water’s latest specifications and standards and H&S standards. Aluminium sulphate is produced on site by saturation of alum slabs and sodium hypochlorite is produced from on-site electro-chlorination (OSEC). These two facilities are to remain, but all other elements of the chemical dosing are to be replaced with new specification compliant solutions.
The capital maintenance scope consists of powder handling units for soda ash, fully screened and bunded chemical storage areas, duty/standby screened dosing rigs, dual contained dose lines, and new static mixers with screened catch pots provided at the points of application for the chemicals.
The quality driver is in relation to the need for a dedicated chlorine contact time to ensure adequate disinfection. While the on-site buffer tank includes sufficient volume, this is not dedicated as the level can drop depending on supply and demand. There is also no facility to ensure an appropriate level of plug flow is provided.
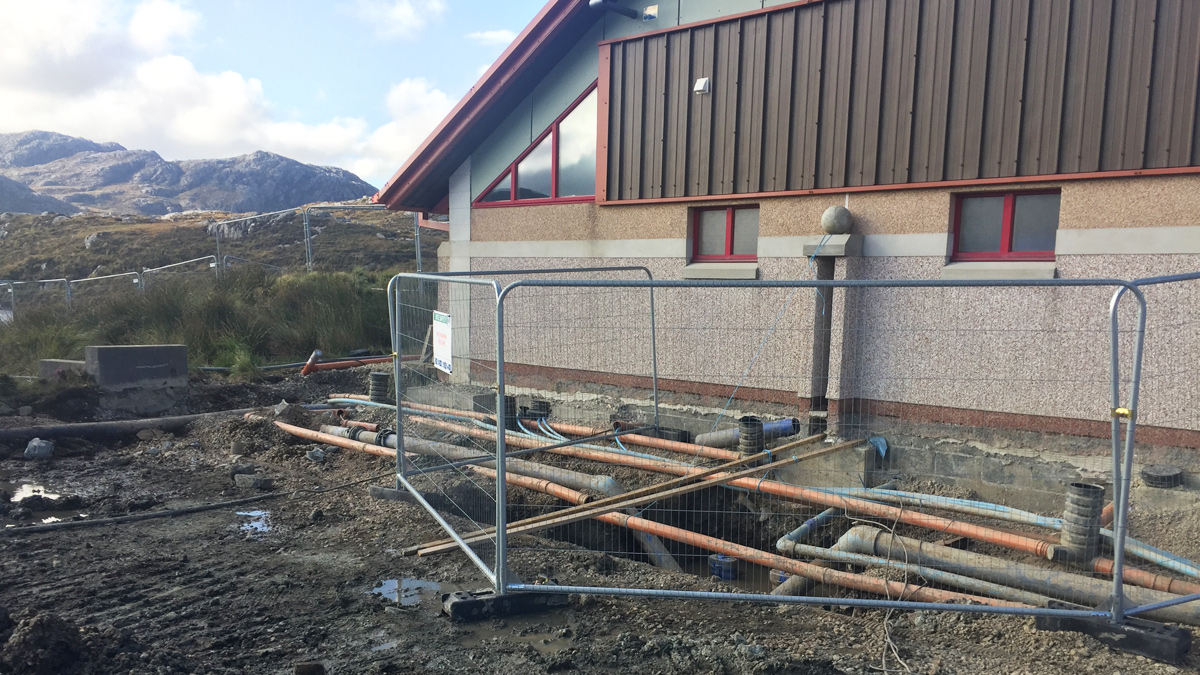
Early construction works – Courtesy of ESD
Uig WTW: Supply chain – key participants
- Client: Scottish Water
- Project delivery: ESD JV
- Civil & structural engineering: MacAulay Askernish
- Steelwork: Murray Steel Products
- Chemical dosing: Ross-shire Engineering
- Mechanical engineering: Specialist Welding Services
- Mechanical engineering: AJ Engineering & Construction Services Ltd
- MCC: Saftronics
- MCC: Boulting Group
- Instrumentation: Processplus
- Electrical: RS Merrimans
- Mixers: Statiflo
- Valves: Industrial Valves
Outline design
The outline design passed to ESD included a single bay extension to the building to accommodate the new chemical dosing equipment and a 500mm diameter by 41m long contact pipe constructed below the access road to provide the chlorine contact time. Chemical points of application were to be provided in below ground chambers upstream and downstream of the contact pipe. There were the following challenges with this option, which needed to be addressed:
- There was insufficient space in the building extension to accommodate the required facilities for the chemical dosing rigs.
- The only place where the contact pipe could be accommodated was beneath the site access road, which included several service crossings and was required for routine operational access.
- The end of the building where the extension was proposed included most of the works services including the raw water and filtered water main. It was not clear how these could be diverted as they needed to enter the building at this end.
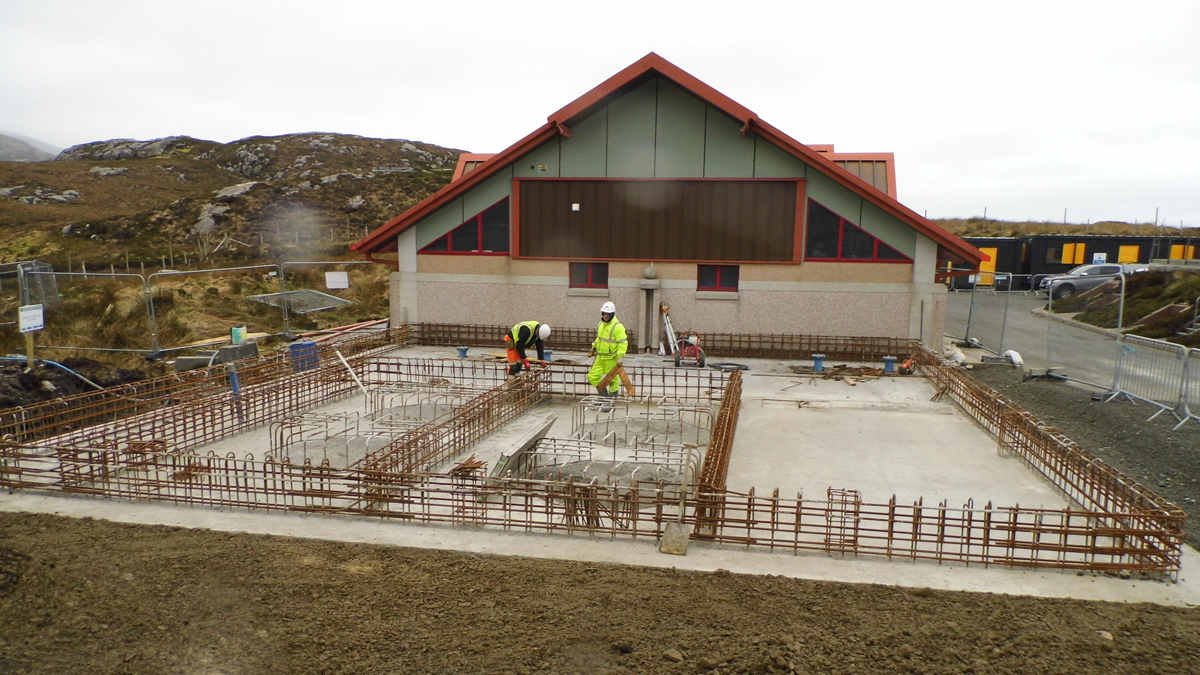
Reinforcement for the chemical bunds and tank plinths being fixed (pop ups for raw and filtered water tie-ins visible in the background) – Courtesy of ESD
Detailed design development
The above issues were addressed by the design team as follows:
- One of the framework chemical sub-contractors (Ross-shire Engineering – RSE) was engaged under a professional services contract to carry out an outline design for the chemical dosing arrangement, taking account of the particular constraints on the site. A collaborative design was developed with ESD, RSE and SW, including the use of 3D modelling for HAZOP and ALM. A compact arrangement was arrived at that used the space in the existing building to accommodate two of the dosing rigs; the space being made available following commissioning of the new rigs in the extension. Within the extension itself, the space was optimised through the use of a three-tiered approach with POAs below the false floor and top of tank access provided on a mezzanine floor. Working within the available hydraulic envelope, mounting the instruments at the lower floor level, and through careful selection of line sizes, all instruments were fed by gravity, thereby removing the need for ten sample pumps which would otherwise have increased the floor space required for the pumps and the MCC starters.
- Rather than a pipe, a design was developed for a bespoke stainless-steel tank which could be installed beneath the false floor of the building extension. As well as avoiding the issues with blocking the site access road and service clashes, this had the following additional advantages:
- It was fully fabricated off site and craned into place on site, thereby minimising site working.
- In collaboration with SW operational staff, an access hatch and scour arrangement were incorporated into the tank, allowing for quick and efficient cleaning of the tank. The inability to do this with a pipe was a particular issue for SW.
- Siting the tank and the associated feed pipework within the building enabled all the POAs to be readily accessible from within the building, thereby avoiding the need to work with chemicals in a confined space.
- An exercise of identifying each of the services beneath the slab was carried out. Many of them were associated with sample lines which would become redundant on completion of the new works, so it was agreed these could be left in place with a number of existing cables ducted beneath the slab. Options for the process lines were discussed with SW and the lengths that needed to pass beneath the new slab were replaced with ductile iron with valves and fittings minimised. A method was developed to allow the building to be built around the live pipes, with vertical legs left for the final tie-ins and a temporary link leg with commissioning valves left in a box out in the floor slab.
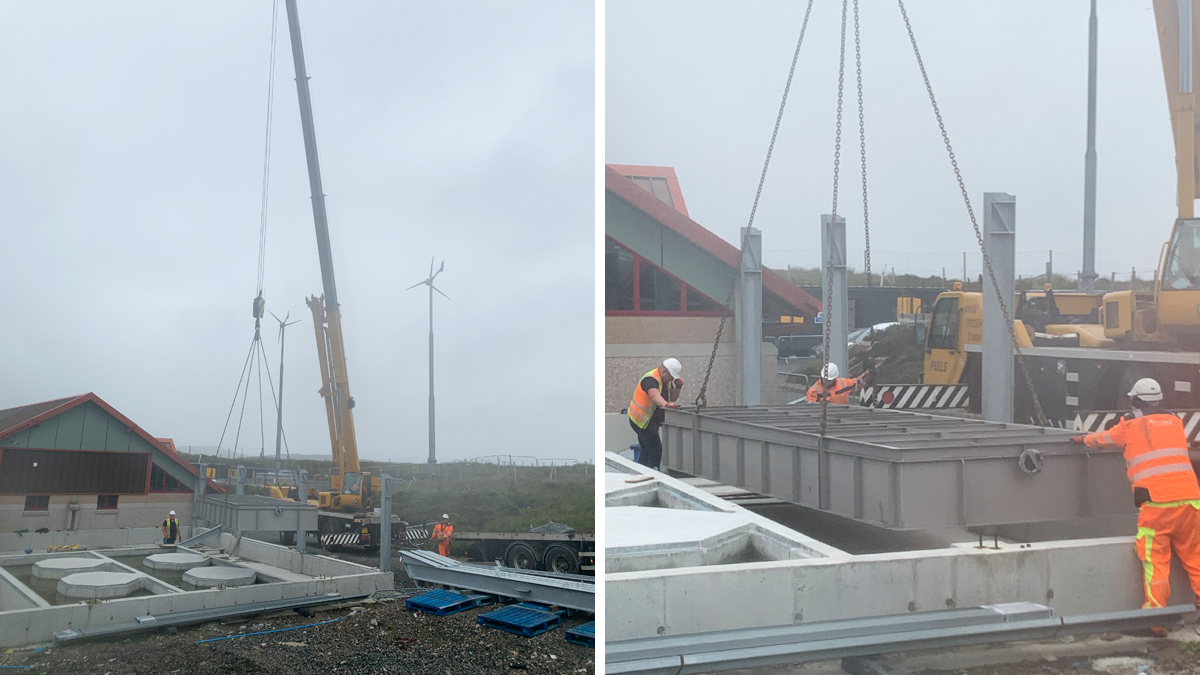
CCT tank being lowered into the building foundation prior to fixing of the roof steel – Courtesy of ESD
Early involvement of supply chain partners
Close collaboration with the key supply chain partners, namely RSE for the chemical dosing and AJ Engineering & Construction Services Ltd for the CCT tank, has enabled a realistic and accurate portrayal of the proposed infrastructure to be presented at HAZOP and other collaboration meetings. The early engagement of the supply chain has allowed their industry experience and knowledge to be input early to arrive at a better and more buildable final outcome.
Site progress
Work started on site in August 2019, with the exposure and modifications to the various services being one of the first activities. Once this was complete, the site access road had to be moved as this conflicted with the building extension footprint. Strategic site visits by the design team were used to confirm the services strategy.
Concrete works started in January 2020, with David Stuart subcontracted as labour only supply, working with McAuley Askernish as the main civil and plant contractor. The base slab incorporated chemical storage bunds, a rebate for floor and CCT drains and rebates to support the flooring, as well as upstand foundations for the blockwork and steel frame for the building. In line with all other construction sites which were deemed ‘non-critical’, the site was mothballed from March until July 2020, due to the Covid-19 lockdown.
At the time of writing (August 2020) the building superstructure is under construction with the remaining mechanical and electrical equipment being sized to fit through the new roller shutter door into the building. This is all being done in a working space which is entirely separate from the existing operational building, thereby avoiding any issues with cross contamination and accidental damage to live equipment.
The new dosing in the building extension is for alum and soda ash. Only once these are commissioned will the existing gable wall be partially removed to allow access into the original building. The existing alum and soda ash skids within this building can then be demolished, and this space will be used to house the new sodium hypochlorite and ammonia dosing rigs. Work is due to be completed in June 2021.
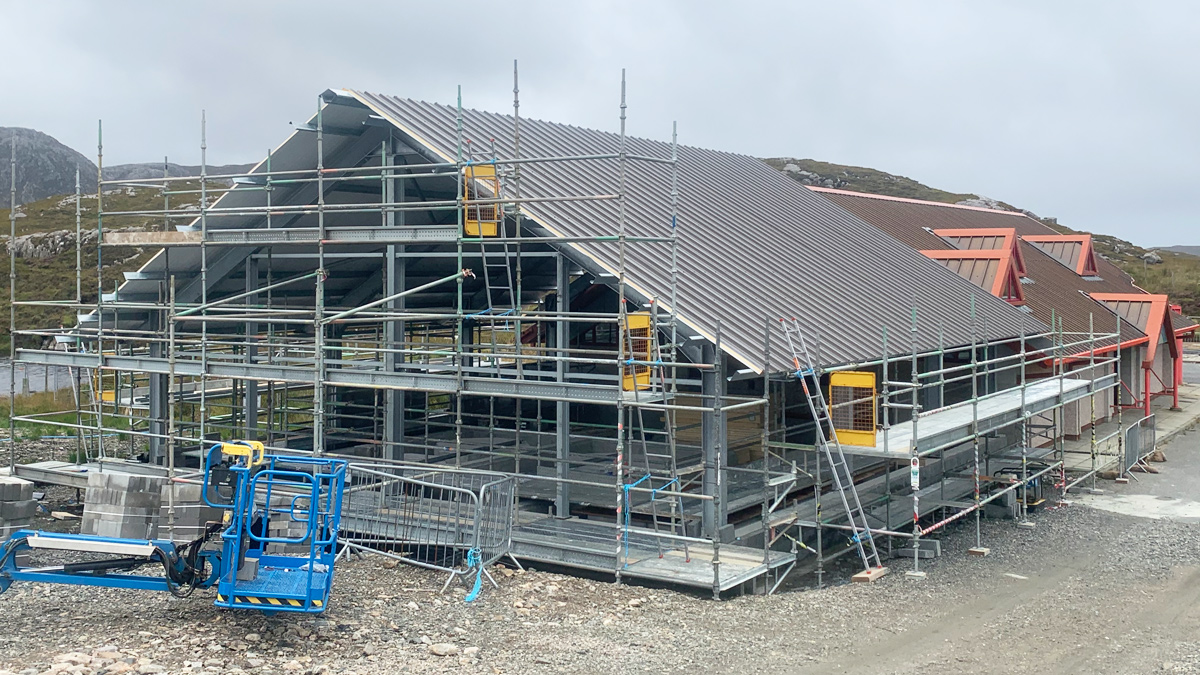
Building extension well under way with roof cladding in place – Courtesy of ESD
Conclusion
Close collaboration with the client in the early stages of the project has allowed ESD to understand the issues that are important in this project to the client. Not only from a final performance perspective, but also from the point of view of operability, ergonomics and maintenance. A period was then used to develop some options for exploration with the client before arriving at the novel CCT idea.
Once this had been agreed with the client, the supply chain was engaged, and the remainder of the building layout developed. Careful coordination has allowed the work to be carried out with minimal disruption to the operation of the live works.
Through the combined resources and knowledge of Scottish Water’s staff, ESD’s in-house staff and the supply chain, what seemed like a very difficult project initially has been progressed relatively quickly and efficiently through design and into the advanced stages of construction.