Ellesmere Port WwTW: Essar Upgrade (2020)

Ellesmere Port WwTW: Progress at September 2018 - Courtesy of United Utilities
The large, industrial town of Ellesmere Port in Cheshire is experiencing population growth, thanks to excellent transport links and an array of employment opportunities. The local population is set to rise by a further 10% by 2036, to over 76,000, so upgrades to the Ellesmere Port WwTW are necessary to cope with increased throughput. The major driver for the scheme is the industrial flow from Essar Oil UK’s local Stanlow Oil Refinery which, whilst small volume, represents a significant increase in load on the works. In 2018, United Utilities and C2V+, a joint venture between VolkerStevin and Jacobs, began a £24m upgrade to works to provide new secondary and tertiary treatment plant along with a sludge thickening system.
Overview
Today’s environment is placing greater pressure on wastewater treatment plant owners to control forms of nitrogen in their discharges. Secondary treatment processes have addressed the control of biochemical oxygen demand (BOD) and total suspended solids (TSS).
Essar Oil UK Ltd, which operates the Stanlow Oil Refinery in Ellesmere Port, will be significantly increasing the trade effluent flows and loads sent to Ellesmere Port WwTW for treatment by September 2021, and this is the primary driver for the project.
The plan
Ellesmere Port WwTW receives effluent into the inlet works from the surrounding catchment and from several traders. Currently, it receives a relatively small portion of its flow and load from Essar’s Stanlow Oil Refinery located on the opposite side of the main A5117 road from the WwTW.
The oil refinery plans to significantly increase the flows and loads it sends to Ellesmere WwTW. As a result, the quality of the effluent discharged to the watercourse will need to be improved and a change to the existing discharge permit will be necessary.
The solution, which will be built at the WwTW, is intended to provide wastewater treatment for the additional biological load expected from Stanlow Oil Refinery and to compensate for population growth. The new permit will come into force once the additional flows from Essar have been accepted and the works have been commissioned.
Commissioning must be completed by 30 September 2021.
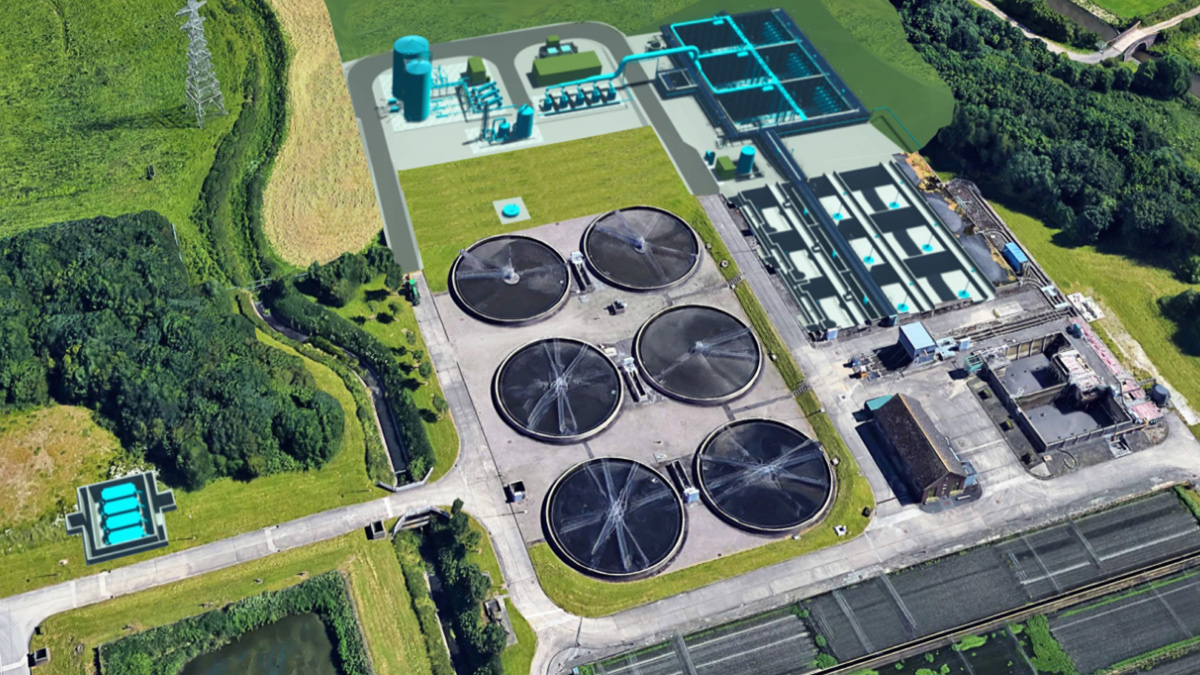
Ellesmere Port WwTW concept – Courtesy of United Utilities
Options considered at tender
- Install a new activated sludge system (70,000m3): Incorporate the 6 (No.) existing final settlement tanks (FSTs) and add a new FST for increased capacity. To do this, the team would have needed to add a new tertiary filter system to be compliant with new effluent biochemical oxygen demand and total suspended solids (TSS) consent. This option was discounted due to the limited available space on the existing plant and the fact that a new activated sludge system would not fit the site boundary.
- Install a step feed bioreactor (50,000m3): This option was identical to the first, except the bioreactor was designed as a step feed bioreactor, therefore reducing the overall volume needed for expansion. This option was discounted as step feed was not considered a viable option.
- Install a new integrated fixed-film activated sludge (IFAS) plant of 11,000m3: This option was taken forward because the integrated fixed-film activated sludge (IFAS) process uses suspended biofilm carriers to grow additional biomass. This greatly reduces the required bioreactor volume. C2V+ was able to draw upon experience from the US market due to parent company reachback. This is the first time that an IFAS plant has been integrated into an existing activated sludge process (ASP). Whilst a conventional activated sludge process (ASP) would provide adequate treatment, the IFAS process has a lower whole life cost due to its smaller footprint, which is hugely beneficial to the client and the wider industry.
Technical uncertainties
A major uncertainty is the impact on the IFAS process of the timing and volume of additional biological loads expected from Stanlow Oil Refinery. There is no precedent for similar plants encountering increased loads at these levels, therefore this project will improve metrics and knowledge for future projects.
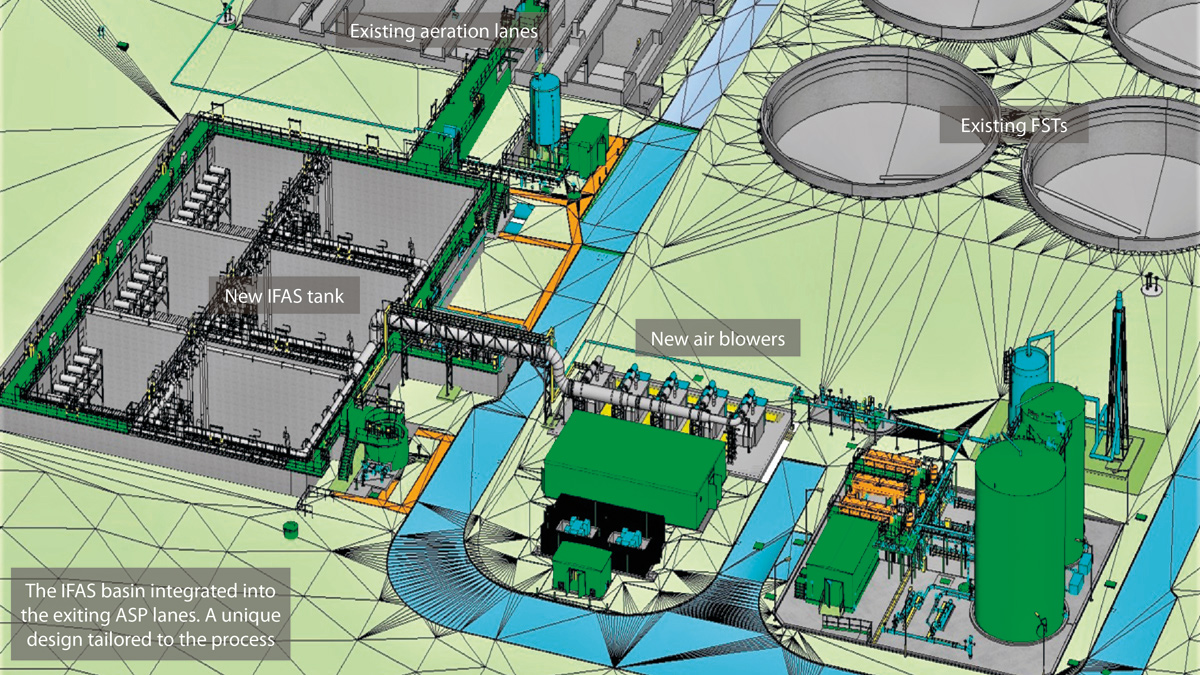
New build BIM model snapshot – Courtesy of United Utilities
Incoming streams
This project is unusual because there are three separate incoming streams. To date, the design team were not aware of any municipal plant that has had three incoming streams with such unrelated chemical properties, as noted below:
- Catchment loads are dependent on storm events and winter/summer variants.
- Incoming imported sludge tankers: Timing is dependent on United Utilities’ daily demand and tanker fleet movements.
- Oil refinery influent: This is entirely out of the control of the treatment works and could peak at any time dependant on the refinery process discharge.
The design
The design has been completed solely based on PRO2D process modelling, as there are very few papers on how to size IFAS plants. In the IFAS process, the kinetic rates are most critical for the nitrification process. In general, the reaction rate depends on the concentration of reactants. The dependence of reaction rate on concentrations of reactants can only be expressed mathematically in terms of the reaction rate constant and the powers of concentrations of reactants. This is due to the lack of historical data and unknowns associated with the increased influent from the refinery.
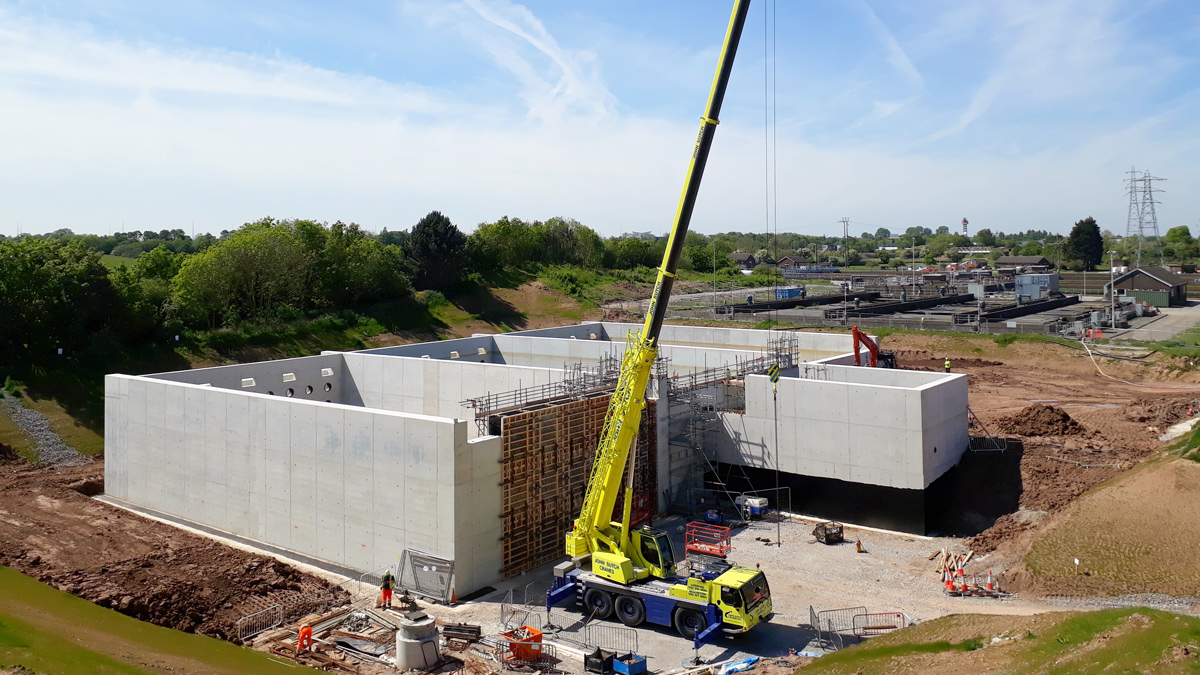
IFAS tank: Progress May 2019 – Courtesy of United Utilities
The influent temperature to the bioreactor is a critical component of the design, yet will be unknown until final flows to the tank are received in 2021. Historical temperatures have been collated and modelled and assumptions made around future temperature profiles.
Once the full flows are integrated into the system, a one-month summer and winter testing period will take place. Afterwards, all of the modelled parameters will be reviewed and modifications made, thus ensuring the effluent from the plant meets Environment Agency standards.
This project will not only assist in the team’s ability to design future plants but will also be shared with the industry to reinforce process design approaches.
Build summary
- FAS system, consisting of aeration system and 3 (No.) moving bed biofilm reactors (MBBRs) inside a new IFAS tank (55m x 35m in plan, 8m water depth).
- Inlet/outlet channels connecting the existing ASP to the new IFAS basin.
- Air will be provided via 4 (No.) high efficiency blowers each rated at 450kW.
Ellesmere Port WwTW – Essar Upgrade: Supply chain/key participants
- Client: United Utilities
- Main design & construction contractor: C2V+
- Ground investigation including boreholes and soil sampling: Geotechnics Ltd
- Tertiary treatment cofferdam: VolkerGround Engineering
- Formwork, reinforcement & concrete works: E Flood Construction Company
- IFAS system: ACWA Services
- IFAS lift pumps: Bedford Pumps
- System integration & SCADA: Tata Consultancy Services
- MCC: Lloyd Morris Electrical Ltd
- Tertiary treatment plant: Evergreen Water Solutions Ltd
- Polymer dosing: Northern Pump Suppliers
- Sludge thickening plant: Alfa Laval
- Sludge storage tanks: Balmoral Tanks
- IFAS metalwork & SW pump station: Franklyn Yates Engineering
- Electrical installation: Eric Wright Water
- RMU & MCC kiosk: Morgan Marine
- Penstocks & stoplogs: AVK UK Ltd (Glenfield Invicta)
- Flow controls: Auma Actuators Ltd
- Aeration blowers: Xylem Water Solutions UK
- Metalwork access flooring: JB Fabs Holdings
- Office & welfare cabins: VolkerBrooks
- Bitumin surfacing: Huyton Asphalt
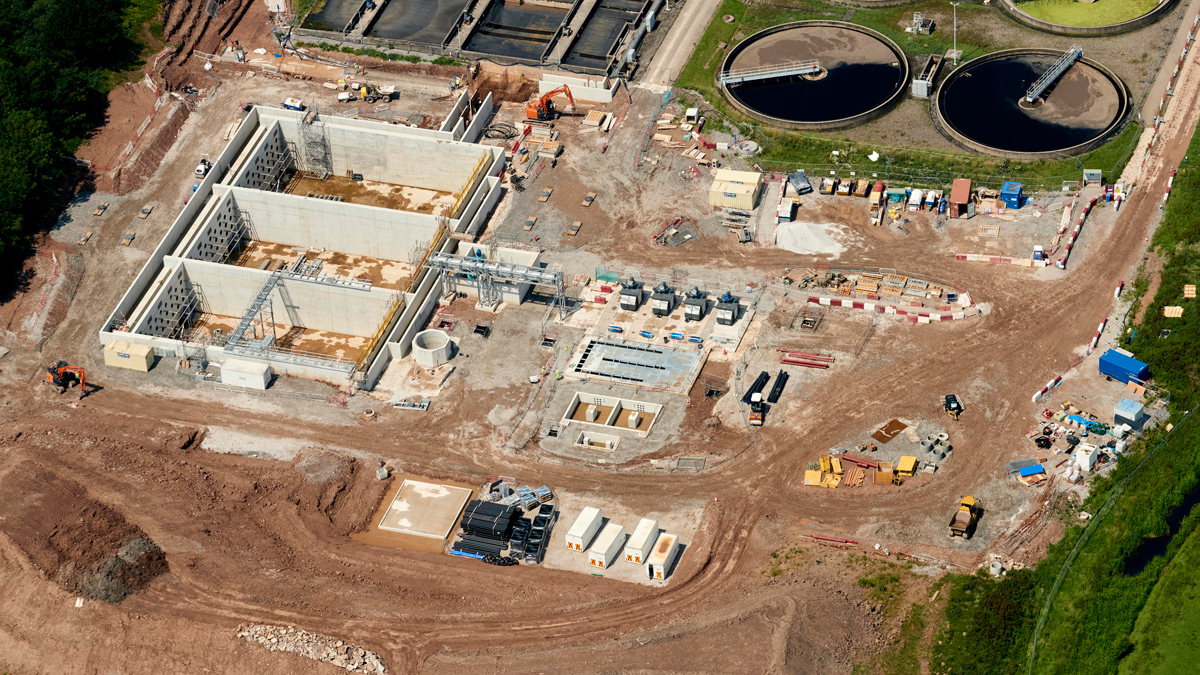
Ellesmere Port: Progress June 2020 – Courtesy of United Utilities
Adopting a ‘one team’ approach
As part of the strategy, a partner event was held at the beginning of the site works, which was attended by the C2V+ team, the client and the subcontractor teams. At this event the ‘one team’ project values and behaviours was agreed upon which created the Ellesmere Port Charter:
- Collaboration
- Work as one team to achieve the end goal.
- Co-location with the team in shared project offices.
- Close liaison with end user acceptance throughout the project lifecycle.
- Healthy challenge across the one team.
- Innovation
- Trust the design and build contractor to provide solutions to meet requirements.
- Challenge the asset standards.
- Close liaison with end user for acceptance.
- Risk and value
- Understand the key risks to make informed decisions.
- Push the boundaries of the expected norm.
- Collaborate with the supply chain on technical/financial constraints.
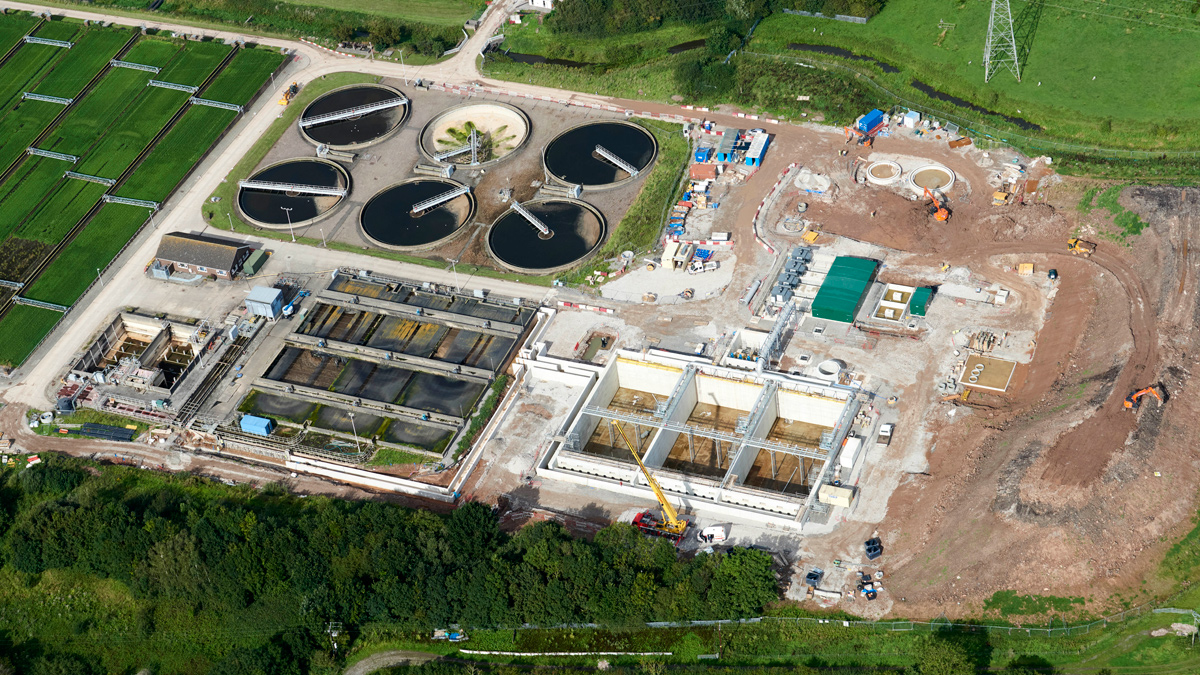
Ellesmere Port: Progress August 2020 – Courtesy of United Utilities
Project progress
Work on site began in May 2018. The new IFAS tank structure has been completed and various ancillary and associated infrastructure works have commenced. After commencing in Summer 2020, the procurement of mechanical and electrical packages are substantially complete.
The first phase of the project is currently on-programme to meet the increased flow and load from Essar’s Stanlow Oil Refinery, with summer testing due in August 2021.