Ardersier WwTW (2019)
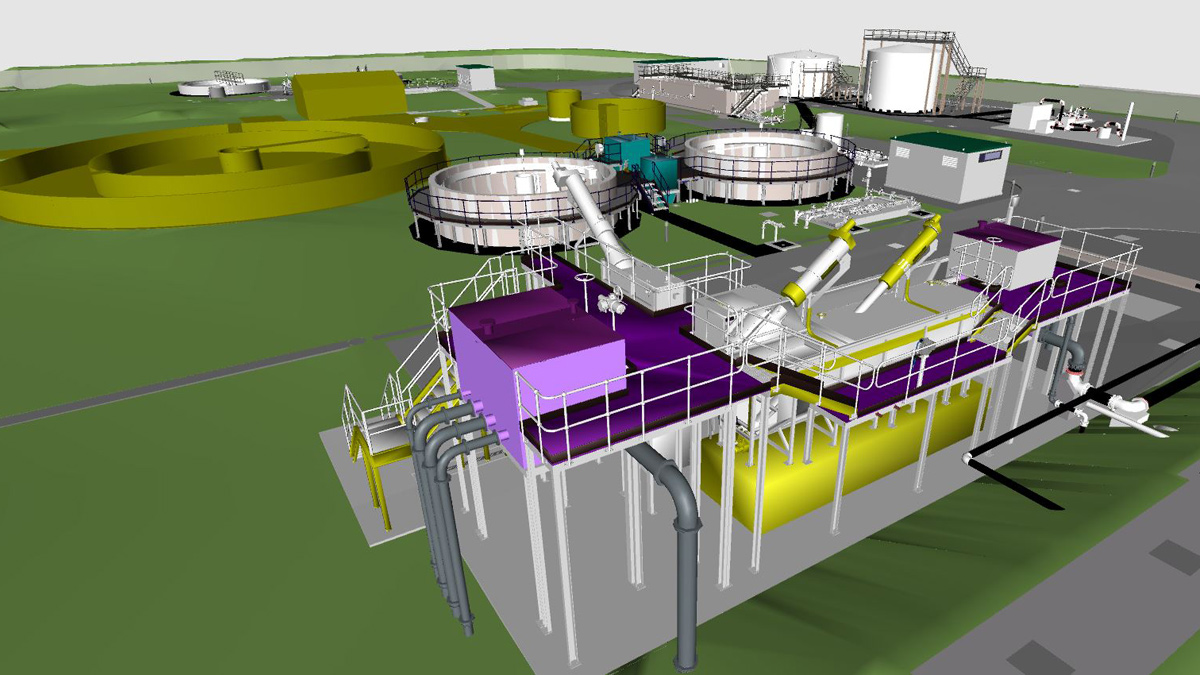
Ardersier WwTW - Courtesy of ESD
Ardersier is located on the Moray Firth some 11 miles east of Inverness. The wastewater treatment works serves the town of Ardersier and the surrounding area including Inverness Airport and Fort George Barracks. It currently serves a population of less than 2,000 but there are significant developments planned in the area with a long-term future population forecast of over 40,000. The new Ardersier WwTW has been designed to treat effluent arising from a total design population equivalent (PE) of 8,831 which will be realised from planned developments at Tornagrain, Whiteness and at the airport in the forthcoming years. The project is being delivered for Scottish Water by ESD; a Galliford Try, MWH Treatment and Binnies Joint Venture formed in order to manage, design and deliver Scottish Water’s SR15 Non-Infrastructure Programme.
Background
The Ardersier project is one of a number of projects being undertaken in the SR15 Non-Infrastructure Programme where ESD has been able to demonstrate the benefits of the Alliance’s digital toolkit and delivered on key tender offerings including DfMA (Design for Manufacture and Assembly) and collaboration with Scottish Water and its supply chain.
Existing works and drivers
The current works receives flow from the Ship Inn and Fort George Pumping Station as well as nominal flow from the Mid-Coul Pumping Station newly commissioned to serve the new development at Tornagrain. The existing works comprises inlet screening, a circular oxidation ditch with central final settlement tank, storm balancing tank and an outfall pumping station. Treated effluent is pumped to a coastal outfall (currently being extended) on the east side of Fort George where it discharges into the Moray Firth.
The main driver for the Ardersier WwTW Project is growth with significant developments anticipated to more than quadruple the current works PE to 8,831. The new works will also address the concerns expressed by Scottish Natural Heritage on the potential impact from the wastewater works’ discharge on the Moray Firth bottlenose dolphin population.
Process design
Due to the increase in flows arising from the projected growth in the catchment, Scottish Water was required to obtain a new SEPA CAR licence in the earlier stages of the project.
The new licence discharge consents applicable for the new treatment works are summarised below.
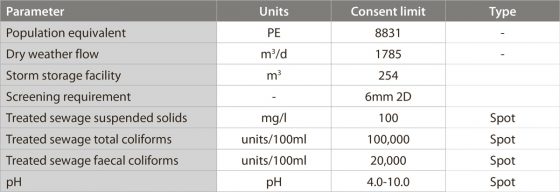
CAR Licence Details
Although there is no BOD discharge consent associated with the new STW, the CAR licence does identify a requirement to meet Bathing Water Directives with secondary treated effluent and UV treatment (total coliforms to 100,000 cfu/100ml and faecal coliforms to 20,000 cfu/100ml).
To achieve this it was identified that the UV treatment plant would require a TSS lower than stated in the CAR licence which will also mean a reduction in BOD arising from Scottish National Heritage (SNH) concerns related to the potential for sewage related pathogens to impact on the Moray Firth bottlenose dolphins.
To meet these exacting conditions the process solution developed by Scottish Water to meet the criteria for the new works comprises the following:
- 6mm 2D inlet screens and grit removal.
- Balance tank/storm storage with return pumps.
- 2 (No.) primary settlement tanks with scum removal.
- 2 (No.) activated sludge lanes with fine bubble diffusers and selector zone.
- 2 (No.) final settlement tanks with scum removal.
- UV disinfection (already installed and commissioned by ESD under a separate project).
- Picket fence thickener.
- Thickened sludge holding tank.
- Odour control for the sludge treatment, return liquors pumping station and storm/balance tanks.
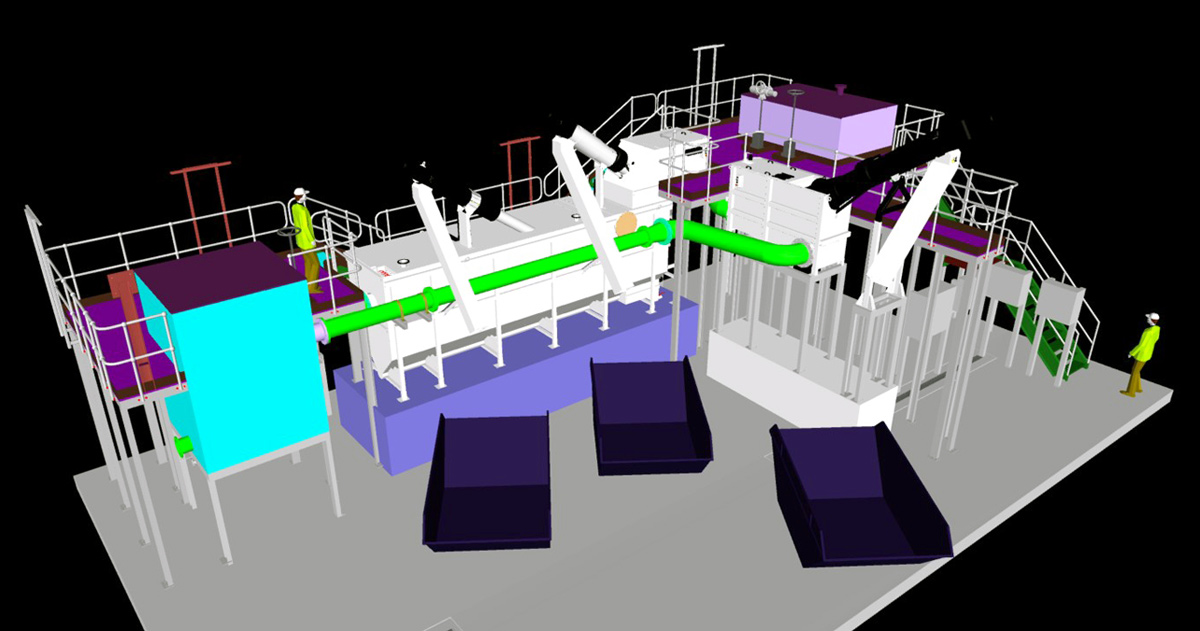
View of 3D model of inlet works from Navisworks viewer – Courtesy of ESD
Detailed design development
The detailed design makes extensive use of 3D modelling, with the entire new works designed and modelled using AutoCAD Revit, with BIM360 Glue being used as a viewer and mark-up interface between designer and modellers. Construction drawings are being delivered as 2D drawings extracted from the model.
In addition, Civil 3D has been used to extract the pipeline long sections throughout the site.
This approach has provided significant benefits during the design process including:
- Collaboration with suppliers: The model has been shared with others to allow suppliers to integrate their design and subsequently for their model to be incorporated into the overall composite model.
- Collaboration with the client stakeholders: The 3D model was used extensively for regular update meetings with Scottish Water to clearly illustrate the proposed layout, demonstrate the development of the design and build on stakeholder knowledge of the site and operations.
- HAZOPs: The 3D model along with screen shots of specific areas were of great benefit during HAZOP meetings and were invaluable when discussing and overcoming access and maintenance issues.
Examples of some of these benefits are developed further within the following sections.
Early involvement of supply chain partners
A major benefit of this approach during the design has been its use during HAZOPs with the client. For these it was necessary to import supplier models (various formats) into the Revit model. 3D models from the following suppliers have been successfully used during HAZOP Meetings or fully integrated into the main model:
- Inlet screens: Huber Technology
- Half bridge scrapers: Colloide
- Aeration system: Suprafilt
- FE washwater duty standby filter skid: Boll
- Sludge transfer progressive cavity pumps (Ardersier): SEEPEX UK Ltd
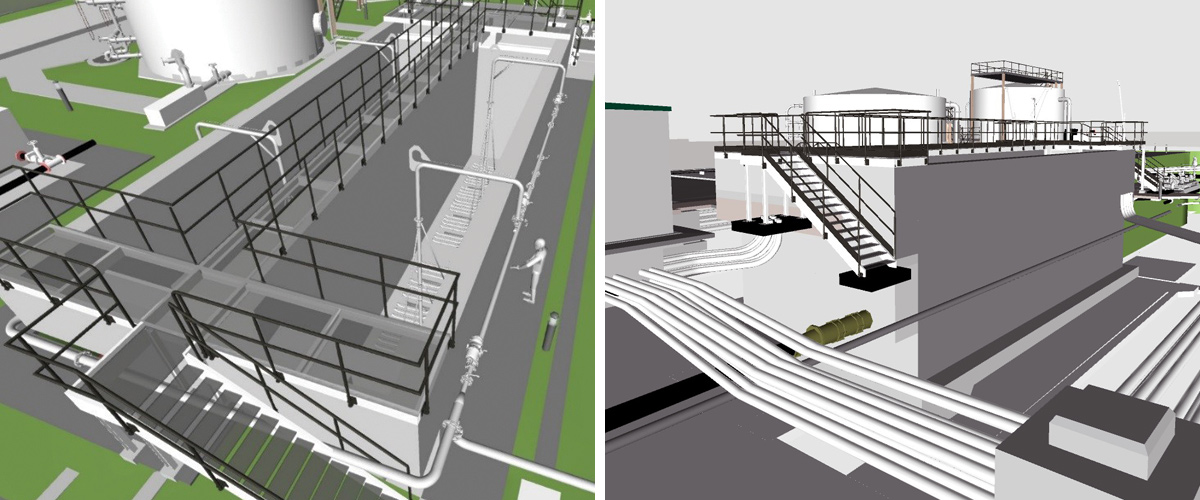
(left) Aeration lane 3D model with Suprafilt aeration system and (right) view of Aeration Lanes in BIM360 Glue – Courtesy of ESD
Inlet works and storm/balancing tanks
The inlet work screens have been designed for the maximum flow that can arrive at the works. There are five incoming mains that need to be diverted and connected to a new high-level inlet chamber with the potential to deliver a peak flow of 106 l/s.
In working with Scottish Water, ESD have developed an efficient layout making use of the larger RO5 HPPS screen from Huber Technology for 100% of the flow with the grit removal system included as an integrated package with this screen. The bypass screen will also be capable of screening the full flow but will have no provision for grit removal. Horizontal launders were removed from the layout during the design and HAZOP process providing a layout such that screenings can drop directly into the skips.
At the end of the inlet works, flows in excess of the flow to full treatment (FFT) overflow to the storm/balancing tanks. The FFT can be manually adjusted using simple underflow penstock with reference to an adjacent flow readout. An agreed volume of storage is to be provided at the works as part of the SEPA CAR discharge licence to reduce spill events from a CSO at the main pumping station serving Ardersier Village (Ship Inn PS). The tanks also balance the intermittent incoming flows from the upstream pumping stations.
The total volume of storage to be provided is 254m3 and an opportunity was identified to provide this volume using half buried (minimising excavation) cylindrical GRP tanks supplied and delivered by SPEL. There are two tanks in series being provided, with capacities of 150,000 litres and 125,000 litres.
SPEL are delivering the tanks to site complete with internal storm return pumps and a mixer to help keep sediment in suspension.
Primary settlement tanks
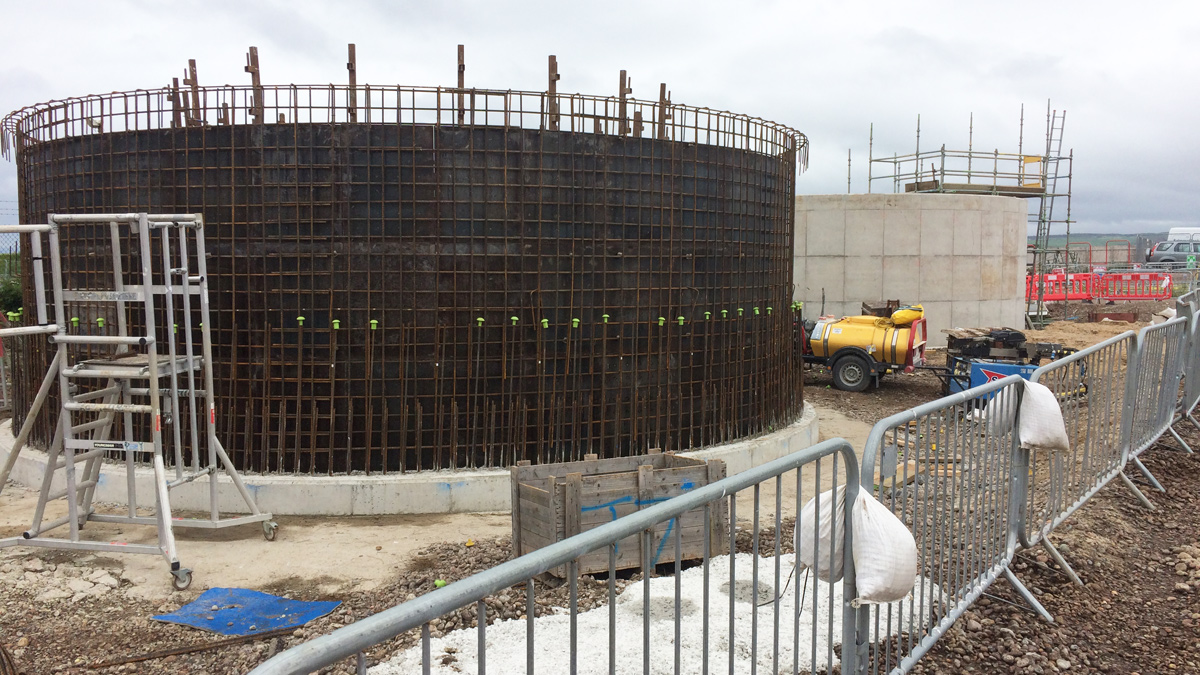
Construction of the 2 (No.) PSTs – Courtesy of ESD
From the inlet works, flow passes through a flow meter and is evenly split between 2 (No.) RC primary settlement tanks (9m diameter and 3m deep). These will be almost 2.5m above ground level and will have full circumferential access walkways, with a central platform for access to a scum collection sump and the splitter chamber.
The access steelwork and platforms will be constructed and installed by AJ Engineering & Construction Services Ltd. The 2 (No.) half bridge scrapers including GRP launders will be supplied and installed by Colloide Engineering Systems.
Duty/standby progressive cavity de-sludge pumps (by SEEPEX UK Ltd) extract sludge from the central bottom collection cone and deliver flow to the picket fence thickener. These pumps will be fitted off-site to a skid by AJ Engineering & Construction Services Ltd and delivered for quick on-site installation.
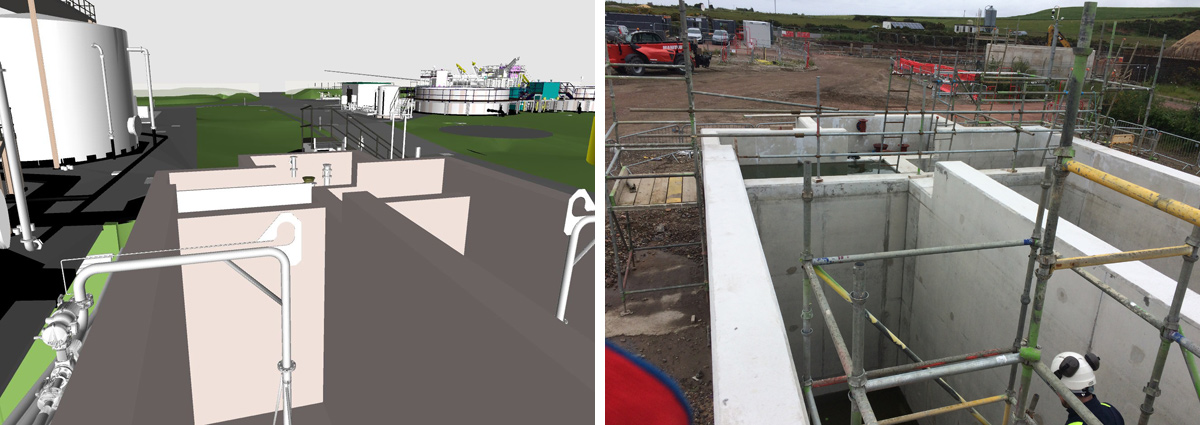
(left) View of aeration lanes in BIM360 Glue and (right) view of aeration lanes under construction – Courtesy of ESD
Aeration lanes
Effluent from the PSTs will pass to the activated sludge plant (ASP) comprising a distribution zone, selector zones and 2 (No.) aeration lanes, each lane being 15.3m long x 3.1m wide x 4.3m deep. The aeration system to be supplied by Suprafilt, comprises 3 (No.) blowers from Aerzen Machines, actuated valves for air control and 4 (No.) single liftable, tube diffuser aeration grids with EPDM membranes. Suprafilt were able to provide a 3D model of the system that ESD dropped into the Revit model. This was used during HAZOP to better understand and optimise:
- The height and location of the valves on the side of the tank.
- The aeration grids at the bottom of the tanks can be lifted out for maintenance avoiding the need for emptying and man entry. The rod for locating the lifting hook was adjusted to allow this to be done from ground level removing the need for MEWP/scaffolding.
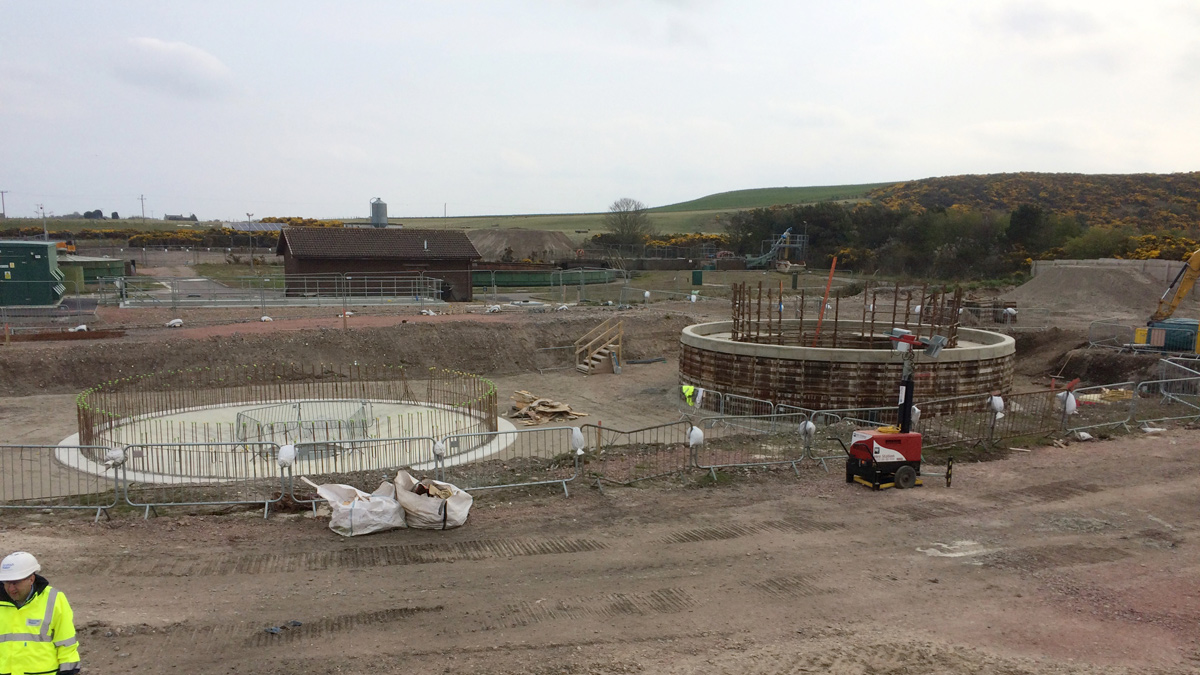
Construction of final settlement tanks – Courtesy of ESD
Final settlement tanks
From the aeration lanes flow is evenly divided between 2 (No.) final settlement tanks (10.6m internal diameter and 2m deep). These are similar to the PSTs with half bridge scrapers provided by Colloide Engineering Systems and return activated sludge (RAS)/surplus activated sludge (SAS) pumps taking activated sludge from the base of the tanks.
Each tank will have dedicated duty/standby dry well submersible centrifugal pumps that can pump RAS back to the aeration lanes, SAS to the picket fence thickener and SAS to the PSTs for co-settlement. A control valve skid (to be constructed off-site by AJ Engineering & Construction Services Ltd) will allow SAS to be bled off the main at a controlled rate at operator defined intervals as required.
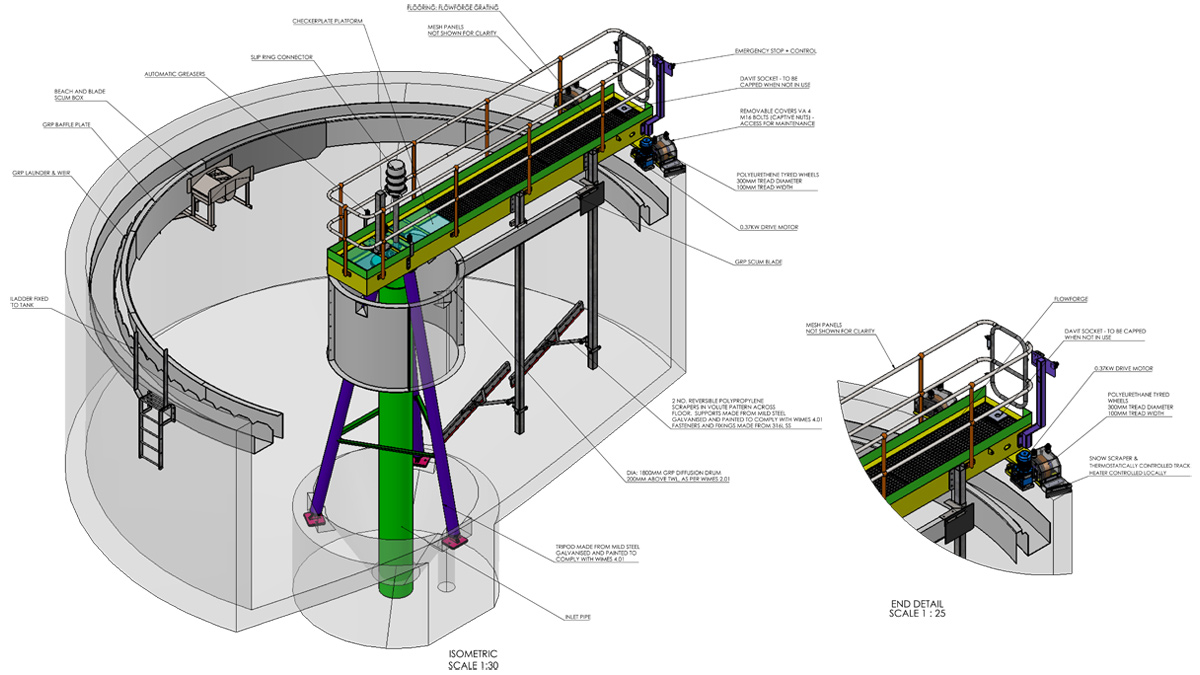
Colloide 3D model of half bridge scrapers – Courtesy of Colloide Engineering Systems
Sludge treatment
Sludge from the PSTs (and FSTs) will be treated and thickened in a picket fence thickener (167m3) before the sludge is pumped (by a SEEPEX UK Ltd progressive cavity pump) to a sludge holding tank (195m3). Both of these tanks will be of stainless steel construction by Homer Burgess, who are also providing the access stairways and steelwork. A drywell centrifugal pump will be installed external to the sludge holding tank for recirculation.
FE washwater system
Final effluent (FE) will be pumped from downstream of the FSTs to a new above ground storage tank. Duty/standby progressive cavity pumps will then pump the FE through duty/standby bollfilters from Bollfilter UK Ltd to the inlet screens and to the bio-trickling odour control unit.
Mechanical skid off-site construction
The pump and valve layouts throughout the site were identified as items that could be located above ground, constructed off-site and dropped into position, saving time and reducing construction safety risk on site. A total of 9 (No.) skids are being constructed and installed by AJ Engineering & Construction Services Ltd.
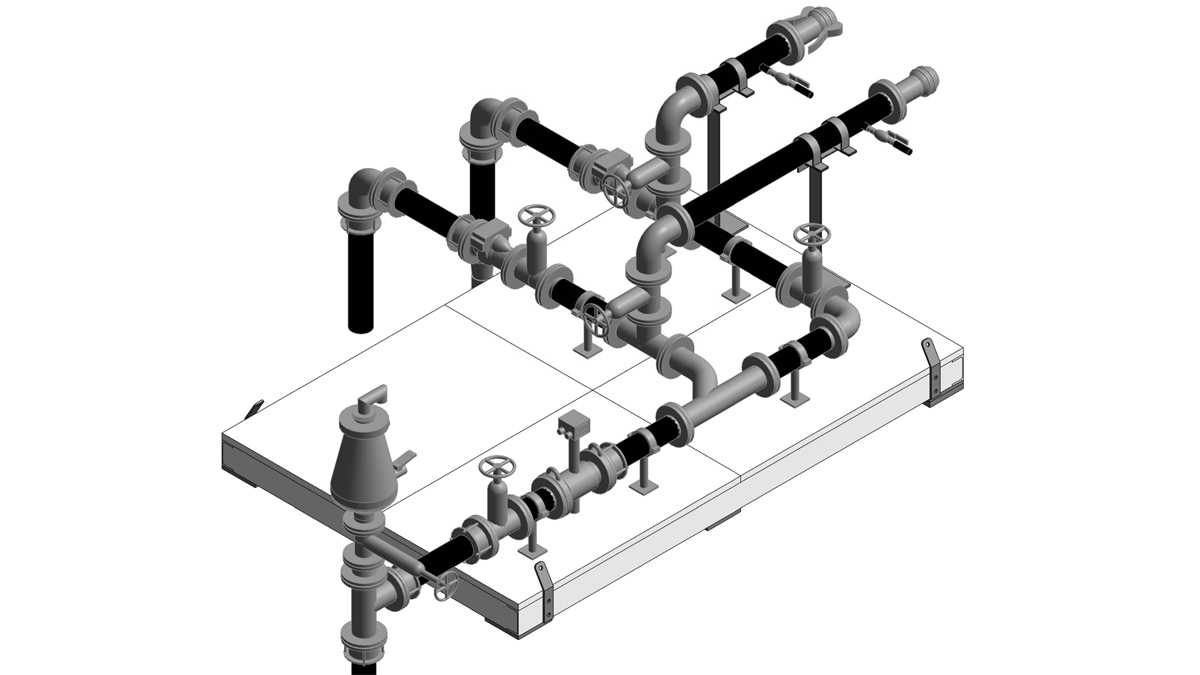
Pumping station valve skid (RLPS, storm pumps and FE washwater draw-off pumps) – Courtesy of ESD
Odour control
A bio-trickling filter (pumice stone) with a deep bed carbon filter on the outlet will be supplied by ERG (Air Pollution Control) to mitigate against odours. This will draw malodorous air from the return liquors pumping station, picket fence thickener and sludge holding tank by duty/standby fans. The storm/balancing tanks as well as the PST splitter chamber will have sealed covers and be connected passive carbon filters.
Electrical design
An upgraded power supply is required for the new site, which requires a new transformer which will be located within the site.
There will be two new MCCs on site that will be supplied and installed by MCS Control Systems and housed in kiosks supplied by Quinshield. An (as yet) unconfirmed electrical installation contractor will then install a site wide profibus system and all power and instrumentation required to operate the works.
The 3D model proved extremely useful in avoiding clashes between the extensive network of ducts with the other underground process and drainage pipework.
Site progress
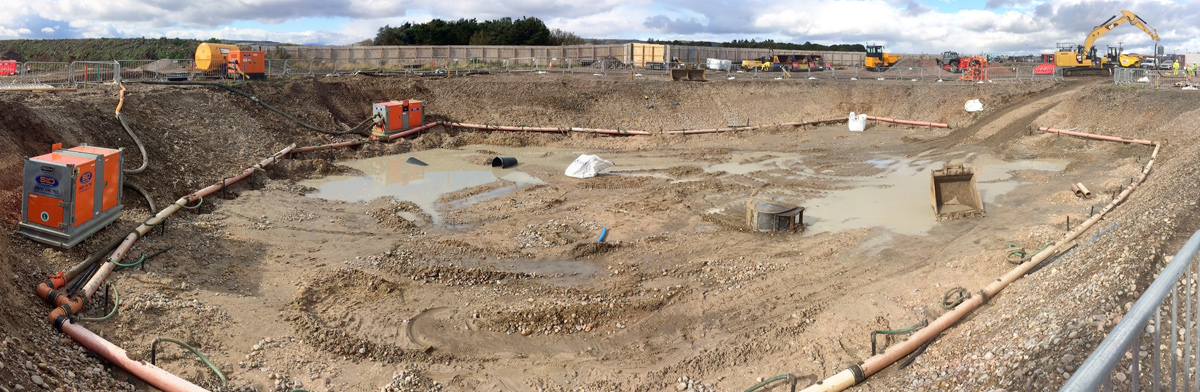
Well pointing installed for aeration lane construction (2m of excavation followed) – Courtesy of ESD
Site construction commenced in July 2018 with a view to constructing the major civils works before design completion of the remaining site. There have been a number of challenges during the construction works including the discovery of unexploded ordnance (requiring bomb disposal squad on site and extensive monitoring), nesting birds and contaminated land (traces of asbestos were found during excavations for the FSTs).
Conclusion
The design approach adopted by ESD to deliver this project provided a platform to demonstrate the capability of ESD to deploy the digital design toolkit and collaborate effectively with Scottish Water and the supply chain. The digital toolkit approach has brought innovation to delivery through identification of opportunities for DfMA and close working with Scottish Water’s supply chain to deliver quality, safety and programme benefits.
The new Ardersier Wastewater Treatment Works will provide a flexible but appropriate level of treatment which enables Scottish Water to satisfy growth commitments while safeguarding the marine environment. Completion of all the construction is planned for end January 2020 with acceptance by Scottish Water anticipated at the end of July 2020.