Beckton STW (2016)

Figure 1 - Air pipework installation inside a drained and cleaned aeration lane - Courtesy of MWH Treatment
In May 2015 Thames Water Operations identified emergency works on Activated Sludge Plant (ASP) 2 at Beckton STW in east London. The work was necessary to address the asset health and resilience of the treatment works, meet performance commitments and ensure satisfactory sludge disposal. The project was a fast track design and implementation with early contractor engagement following SMB’s model to safely deliver sustainable and innovative solutions for Thames Water’s 15 million customers that leave a lasting legacy, delivering outstanding value and meeting the specified outcomes.
Background
Beckton STW was built in 1864 as part of Joseph Bazalgette’s scheme to remove and treat sewage in London. The works are located in the Borough of Newham, East London and treats a population of approximately 3.5 million people. Beckton is Europe’s largest sewage treatment works and it is also the fourth largest in the world.
Thames Water (TWUL) asked SMB (an unincorporated joint venture consisting of Skanska, MWH Treatment and Balfour Beatty) to fast track the execution of Emergency Works to ASP2. SMB’s contract with Thames Water is for the provision of specialist expertise in the design, procurement and construction (including testing and commissioning) of works and programme management. The commercial arrangement is designed to maximise collaboration and innovation by sharing of risk and by eliminating waste, duplication and inefficiency.
ASP2
Activated Sludge Plant number 2 consists of buried concrete tanks forming 6 (No.) aeration lanes. There are 8 (No.) lanes per tank each measuring 118.87m long by 4.89m wide with a water depth of 3.66m.
The work inside the lanes was limited to diffuser and air pipework replacement, air main and air mixing repair, mechanical removal of existing aeration equipment, cleaning and foliage removal, valve and penstock repair or replacement and new structural jointing. In addition, the project included improving access to the ASP lanes and the provision of real time control (RTC).
Project mobilisation
From an initial scoping workshop held in May 2015, emergency funding was provided in June to fast track detailed investigation work with an anticipated start on site date of September 2015. SMB governance was streamlined to ensure that the correct level of management compliance was applied to the process while meeting the extremely tight schedule dates. Following settlement in July, full funding was approved at the end of August 2015 to execute the project; that’s a zero to bang achievement within 4-months of the first meeting and presentation of the needs.
The site team mobilised at the beginning of September 2015 and the first tank in ASP2 was isolated and drained down within 4-weeks of site start-up. Isolation of each lane was achieved by lowering a timber framed ‘dam board’ into pre-formed slots in the channel and over-pumping flows either side.
The project team investigated a number of possibilities for the design and fabrication of each ‘dam board’ and determined the most cost efficient method was to design and manufacture timber beams with a steel frame and integrated lifting eye. These were checked by a temporary works designer to ensure technical compliance. As part of the legacy of the project, the boards will be left on site for reuse on future projects.
In addition the project is modelling the design and installation so this can be used as a virtual run through to the isolation process. The ‘dam board’ installation is shown in figure 2.
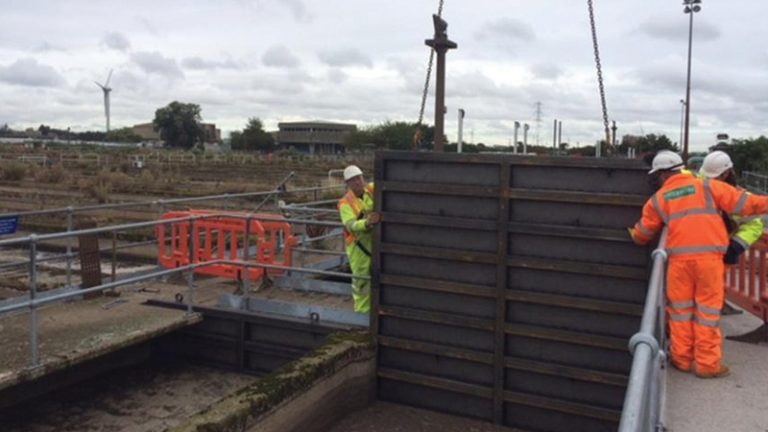
Figure 2 – Installation of timber ‘dam board’ into inlet channel to isolate incoming flows to aeration lane – Courtesy of MWH Treatment
Removal of the grit and material inside each lane was achieved through a combination of gravity drain-down and over-pumping the flows back to the head of the works. Once a lane was isolated the existing materials were removed and new diffuser pipework installed as shown in figure 3 (below).
Problems were encountered with the drain down due to faulty valves and the build-up of grit and silt at the bottom of the channels. High pressure gulley suckers were used to clear the material from the channels, returning the sludge to the head of the works thus reducing expensive off-site tankering and disposal costs.
The programme was split into 2 phases due to a limit on the number of tanks that could be taken out of service at any one time. Phase 1 was completed on schedule and handed back to TW Operations on 23 December 2015 and the phase 2 works, which also includes the provision of real time control will be completed by June 2016. This will reduce the energy consumption of the existing blowers and improve operational efficiency.
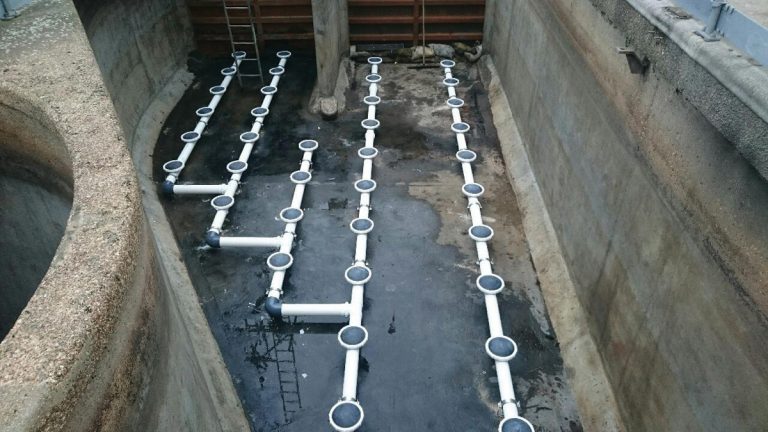
Figure 3 – Installation of new diffuser pipework inside drained down inlet channel – Courtesy of MWH Treatment
Challenges
One of the key challenges faced by the project team was understanding the extent of work required within each tank. This included establishing the accuracy of record drawings of recent completed works on site. Due to operational constraints it was not possible to isolate or drain down any part of the plant prior to commencing site works, so the manufacture of process critical plant began once the plant was drained and accurately surveyed.
Understanding the project needs
Due to the size and complexity of Beckton there is always work either going on or planned at the site, so the project team wanted to make a difference in understanding what had and had not worked on past projects, and what were the key drivers for doing the work.
A ‘Seek to Understand’ workshop was held at project kick-off with all the key stakeholders to understand the project needs, limitations, risks and opportunities. This was then developed into a scoping document which formed a key part of the project outputs.
A ‘Be Understood’ workshop with the same stakeholders was held 4-weeks later to provide assurance and evidence that the solutions proposed would deliver the required performance commitments, while being safe to construct, operate and maintain.
TW Operations were key to providing and assisting the project team in identifying isolation areas and sequencing for taking individual tanks out of service. Through engagement, regular discussions and physically walking the works the team was able to develop trust and understanding on project scope, programme, limitations, risks and opportunities.
A key differentiator to achieve project efficiency and value for money was what to do with the contents of the drained lanes. A number of options were investigated and both agreement and approval obtained in advance of submitting the final cost on what was to be done with the removed vegetation, sludge and grit. This has proved very effective in achieving part of the outcomes.
What was done differently?
The project needs came at the start of the AMP period which is always a challenge as a new team is brought together and procedures are still being developed.
The project required the development of a rapid solution from need identification to implementation. A small team of specific individuals (contracts manager, commissioning manager, process engineer and site operations) focussed on identifying the root cause, agreeing on the solution and determining how the works would be delivered from the start. In parallel the project team focussed on each specific need rather than outline design.
As part of the SMB collaborative approach, key supply chain partners were identified, engaged and embedded into the project team to develop the scope, programme, key risks and attendances. This is part of a left shift engagement SMB are implementing to put ‘procurement’ before ‘engineering’ (the ‘p’ before ‘e’).
At the time of writing (March 2016) the project is on schedule to deliver all its outcomes ahead of programme offering a 8% saving to the agreed target cost.