Highworth WwTW (2018)
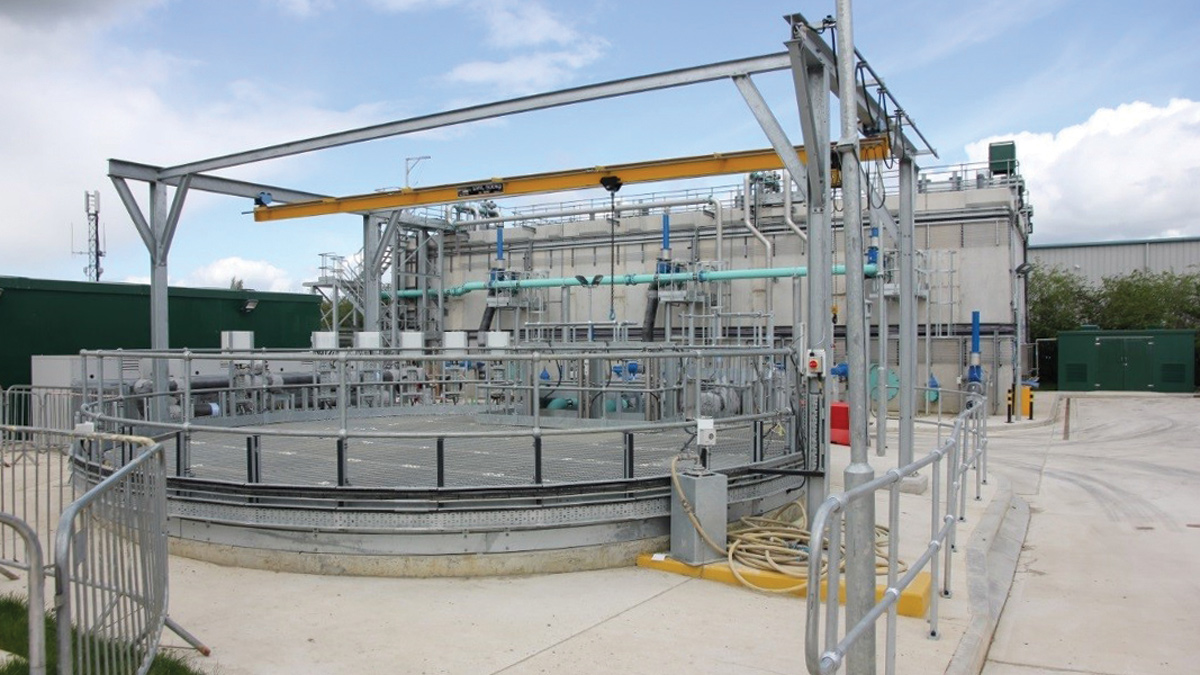
Highworth Nereda installation, buffer tank and reactors - Courtesy of Royal HaskoningDHV
Highworth Wastewater Treatment Works (WwTW) is located at Pentylands Lane, Highworth to the northeast of Swindon. The treatment works currently serves a population of approximately 10,000 customers, with an average daily flow of 1,720m3 per day and a peak flow of 55 l/s. The works is Royal HaskoningDHV’s first full-scale Nereda plant in the UK. The new granular activated sludge plant has been developed by the Costain Atkins JV, part of eight2O, the delivery partnership for Thames Water’s AMP6 investment programme. This new plant demonstrates the innovative Nereda technology for the Environment Agency, as part of Thames Water’s commitment to deliver the national Chemical Investigation Programme. It provides improved and sustainable wastewater treatment, with early results showing higher levels of nutrient removal, whilst using half the power of conventional systems. The plant will be monitored closely over the next year.
Previous works
The previous works consisted of screening, stormwater treatment and primary sedimentation. Percolating filters and HSAF treated 40% of the works flow and 60% was treated by a ‘SATEC’ activated sludge plant and disc filter, together with backup sidestream SAFs. Sludge treatment was limited to consolidation and holding tanks and the sludge tankered to the main Swindon works. The assets were life expired, in need of replacement and difficult to operate and maintain. Also, plant performance was limited and would not have been able to achieve the new quality driver being introduced in 2020 of 3mg/l ammonia.
CIP trials
The Environment Agency requested that Thames Water trialled Nereda as part of the Chemical Investigation Programme. Thames Water decided to select Highworth as the demonstration site, and install the UK’s first Nereda solution for improved wastewater treatment. Nereda offers the advantages of being very compact, capable of producing very high effluent quality and using significantly less power than equivalent processes.
With the added advantages of a learning optimising controller and biological phosphorus removal, the process is fast becoming the leading process for sustainable wastewater treatment.
New installation
The new Nereda installation at Highworth consists of an 180m3 influent buffer and 3 (No.) new-build reactors, each with a capacity of 500m3. Its small footprint allowed it to be constructed within the boundary of the existing site. The Nereda reactors incorporate a standardised design, modular precast concrete structures and new technology design, which can easily be upscaled for larger plants.
Also, Thames Water decided to install a Mecana cloth media filter as tertiary treatment unit downstream of the Nereda installation for further improved treatment performance.
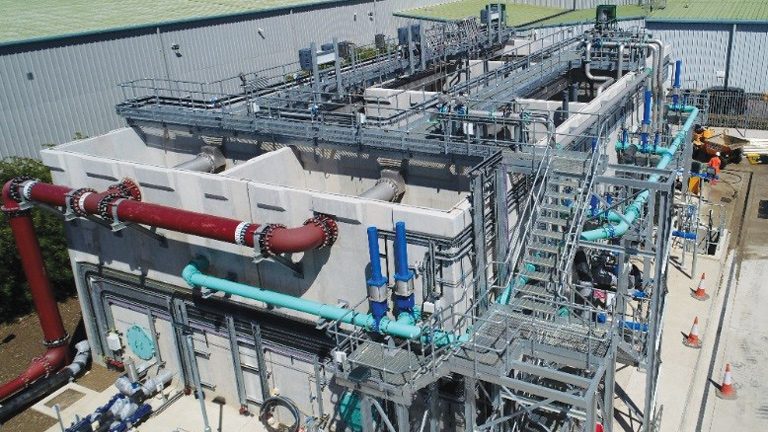
Aerial view of the 3 (No.) Nereda reactors and sludge buffer which consolidate the waste sludge, together with the treated water discharge pipe – Courtesy of Thames Water
Nereda technology
Nereda technology is the first aerobic granular sludge technology that has been applied at full-scale, and is fast becoming the best choice for sustainable wastewater treatment, with over 60 projects in delivery and more than 20 projects in operation worldwide. Developed in the Netherlands by water authorities and Royal HaskoningDHV, Nereda is a compact, sustainable, low power and cost-effective biological wastewater treatment process. Highworth is the first plant operational in the UK.
In this installation, the bacteria mass responsible for the natural treatment process of the wastewater is selectively managed in a way that not only treats the water, but also promotes the natural formation of sludge granules that settle quickly, allowing operation at higher biomass concentrations and thus achieving higher treated water quality at greater throughput than traditional treatment processes.
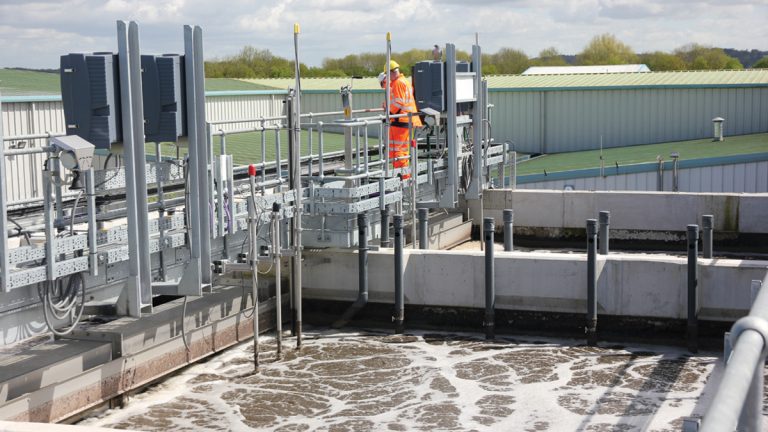
Highworth WwTW Nereda reactors in operation – Courtesy of Royal HaskoningDHV
All the biological treatment processes (nitrification, denitrification, and biological phosphorus removal) take place simultaneously within the Nereda granules, achieving high levels of nutrient removal without the use of chemicals.
The Highworth project was developed by the Costain Atkins JV, part of eight2O, in collaboration with the technology partner, Royal HaskoningDHV, contract partner, Trant Engineering and supply chain partners. Following commencement of basic design in January 2016, site construction started in September, with process start-up in August 2017. Following an extended process commissioning period to allow the phased decommissioning of the old works, the full works flow has been reliably treated by the Nereda installation since March 2018.
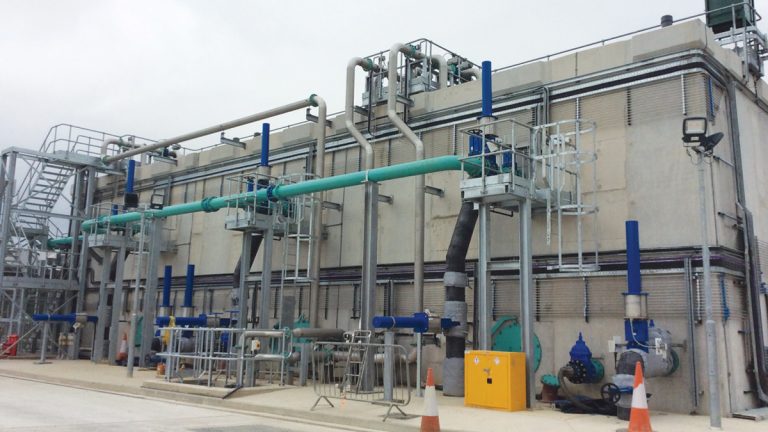
Highworth new process plant – Courtesy of Royal HaskoningDHV
Operating experience
Process start-up: The process start-up plan had to take account of maintaining wastewater treatment and effluent compliance at all times. This required interfacing with the existing treatment works during process commissioning with phased start-up and proving before phased decommissioning of the existing treatment assets. Particular care was given to returning batch flows from the Nereda discharge to the existing works, without hydraulically overloading the existing assets.
The process was initially seeded with granules from existing Nereda sites in the Netherlands to a concentration of 3.5g/l and discharge from the Nereda plant was returned to the existing works until Thames Water was convinced of process reliability. Next, the Nereda plant discharge was switched directly to works outfall and the existing percolating filters were decommissioned.
Finally, in March 2018, as confidence and robustness of the process was proved, the SATEC was switched off and all flows passed to the Nereda plant and granule growth was then observed at a rate of about 1g/l per month up to the overall design concentration of 6-8g/l. The plant is now fully operational and is reliably achieving all effluent quality parameters.
Phase 1: Establish good nitrification: Due to the commissioning restrictions, the initial challenge was to maximise nitrification with a low initial biomass concentration, to treat the full design ammonia load with around half the design biomass. Some additional control features were added to ensure compliance under all conditions.
Under this initial phase of treating the full works flow and load the aeration time was maximised and DO levels raised to maximise nitrification. In addition, the Nereda controller automatically adjusted the batch size depending on the buffer tank level and flow conditions in order to optimise performance.
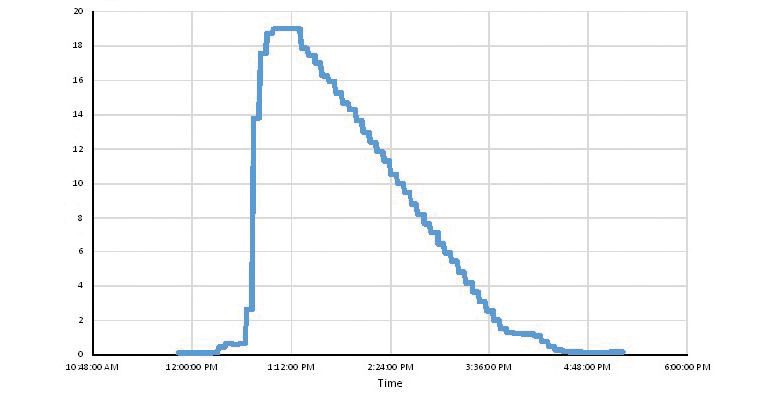
Figure 1: A typical batch profile of ammonia removal
Figure 1 (above) shows the rapid increase in ammonia concentration with the onset of aeration and then the high rate of nitrification achieved (up to 7mg/l/hr), despite the low biomass concentration. Figure 2 (below) shows the discharge ammonia concentration of every batch for the last two months. Over this period, Nereda has achieved ammonia effluent quality of 0.03mg/l (average) and 0.10mg/l (95%ile).
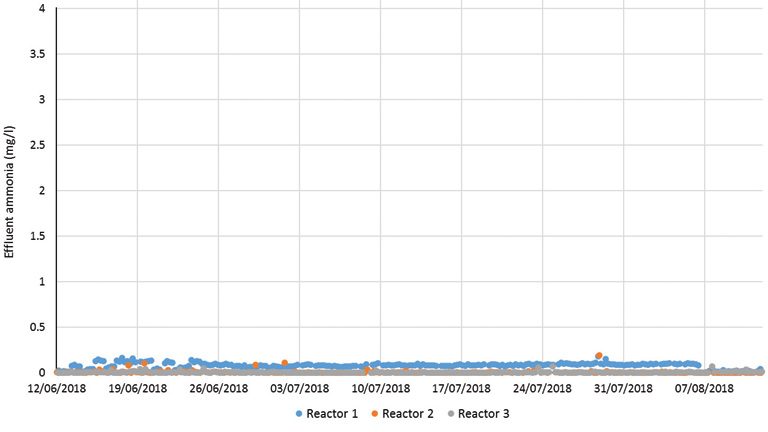
Figure 2: Ammonia concentrations of every batch for the last two months (average: 0.03mg/l; 95%ile: 0.10 mg/l)
Phase 2: Better than expected levels of denitrification and low effluent total nitrogen: During each reaction cycle, Nereda automatically stops aeration at the chosen ammonia setpoint corresponding to full nitrification of the liquors, which in turn allowed increased time for denitrification. This denitrification period leads to nitrate levels quickly reducing from typically 10-30mg/l to less than 6mg/l on average. Under these conditions increased air stripping was included in the treatment cycle to remove micro-bubbles of nitrogen and allow improved removal of fine solids.
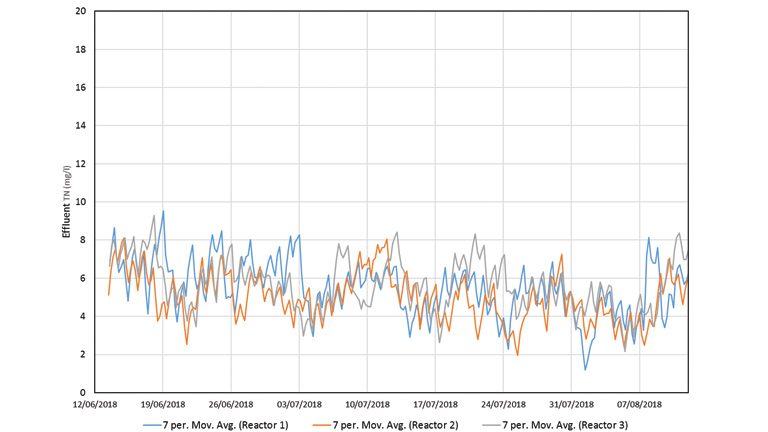
Figure 3: Effluent total nitrogen (average 5.3 mg/l)
Effluent TN levels as low as 0.3mg/l have been measured, although full acclimatisation has not yet been fully achieved. This shows that Nereda technology has the advantage of achieving future TN consent values, where required. Overall average total nitrogen is currently 5.3mg/l.
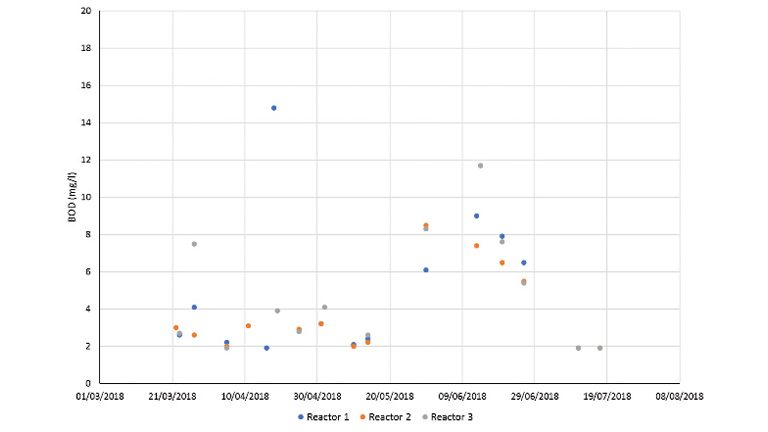
Figure 4: BOD (mg/l) in Nereda effluent
BOD removal
Treated effluent BOD levels have been consistently maintained at less than 15mg/l downstream of the Nereda plant, with a 95%ile of 9.0mg/l (see Figure 4 above). The installation was further enhanced through use of a Mecana cloth media tertiary solids removal unit. Overall, the combination of Nereda technology and Mecana achieved a 95%ile of 2.7 mg/l (see Figure 5 below). It should be noted that this figure is artificially high, as 35 out of 41 samples were below the BOD detection limit of 1.9mg/l.
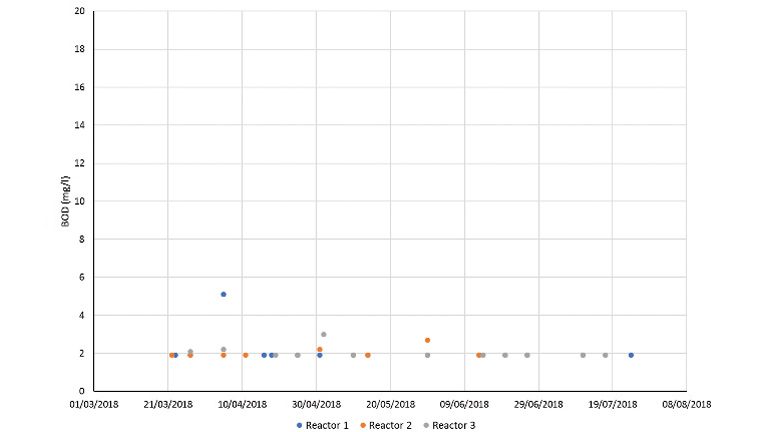
Figure 5: BOD (mg/l) after Nereda and Mecana (final effluent)
Power consumption
Figure 6 (below) shows the variation in ammonia load to the plant, and the power consumption used to treat that load. As can be seen, the power consumption of the Nereda installation has been low and consistent with the ammonia level requiring treatment.
Measured results show specific power consumption levels of 5.3kWh/kg ammonia, which is typically 30-50% lower than the power required for an equivalent activated sludge plant. This is equivalent to a specific power consumption of 13kWh/pe y which is 50% lower than an efficient equivalent ASP.
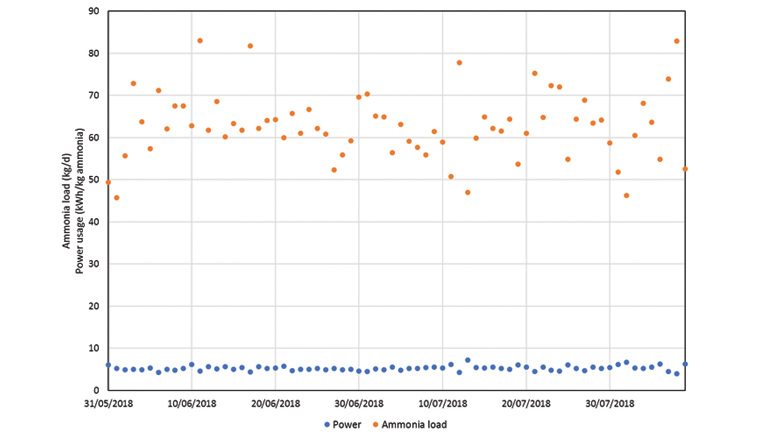
Figure 6: Ammonia load (kg/d) and specific power usage (kWh/kg ammonia)
Conclusions
The Nereda installation at Highworth is the first full scale application of the Nereda technology in the UK. The technology has been successfully implemented, treating the full range of flows and loads and producing treated water well within the works consent conditions.
Following design, construction and testing, process start-up commenced in August 2017. Extended process proving allowed phased decommissioning of the existing treatment assets and all flows finally transferred to the Nereda plant in March 2018. Initial process testing included optimisation of nitrification. Onset of denitrification required further optimisation, including extended periods of air stripping to release nitrogen gas.
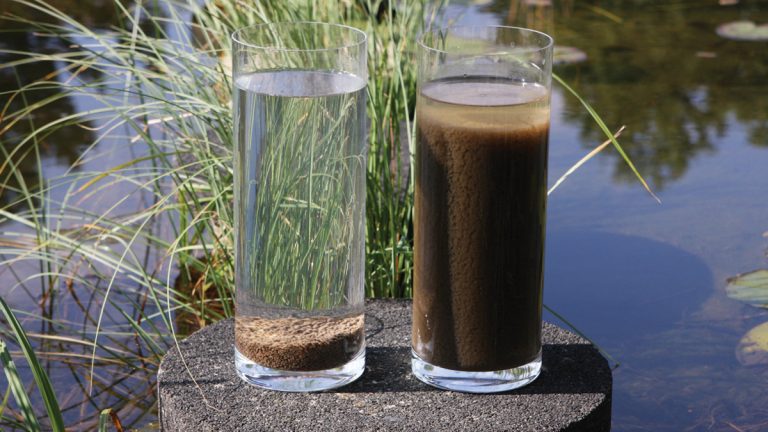
Settling properties of the aerobic granular biomass (left) compared to activated sludge (right) – Courtesy of Royal HaskoningDHV
Comprehensive instrumentation and data monitoring has provided large quantities of performance data and allowed the Nereda technology learning and optimising controller to achieve the target effluent quality across the full range of operating conditions and minimise power consumption. Measured power consumption is 13kWh/pe y, giving a 50% saving when compared to an efficient equivalent ASP.
Early performance results have demonstrated the Nereda plant’s capability of achieving exceptional levels of biological nutrient removal from a small footprint, automatic and low power installation. Performance will be closely monitored and further optimised over the next year.