Belle Greve Wastewater Centre Phase IV (2016)
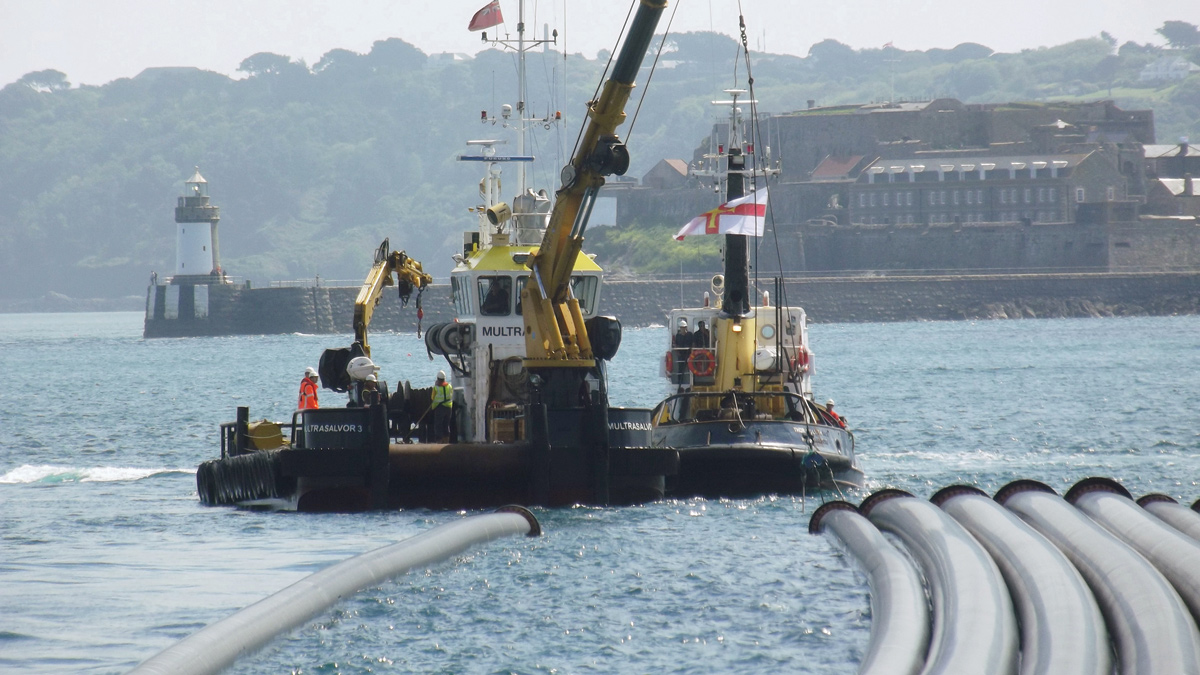
Delivery of pipes to Guernsey - Courtesy of Guernsey Water
Belle Greve Outfalls Replacement is the fifth and final phase of the Belle Greve Wastewater Centre (BGWwC) strategy to provide suitable wastewater treatment and disposal capability for the island of Guernsey. The strategy commenced in 2007 and was completed in 2015 with the replacement of the long sea outfall (LSO) and short sea outfall (SSO). The BGWwC receives over 99% of all the foul flows from the island prior to discharge into the Little Russel area off the east coast of Guernsey. The seas around Guernsey generate a 10m tidal range and 6 knot flow rates, with discharge perpendicular to these flows.
Background
The Bailiwick of Guernsey, whilst a Crown Dependency of the British Isles, is outside of the jurisdiction of the United Kingdom and is not covered by the laws and governance of the European Union. As such, the main European Directives relating to wastewater disposal (UWWTD, BWD, SWD and WFD) cannot be enforced and Guernsey has flexibility to relax or amend these standards where it is considered appropriate.
During development of the Belle Greve Wastewater Centre Strategy, detailed assessment of the coastal waters(1) concluded that with appropriate dispersion and diffusion of flows following screening to remove the non-biodegradable material, primary, secondary or tertiary treatment would not be required to meet equivalent standards of the UWWTD.
(1) Intertek Metoc Report 07 September 2011 ‘Discharge of Preliminary Treated Wastewater to the Little Russel’
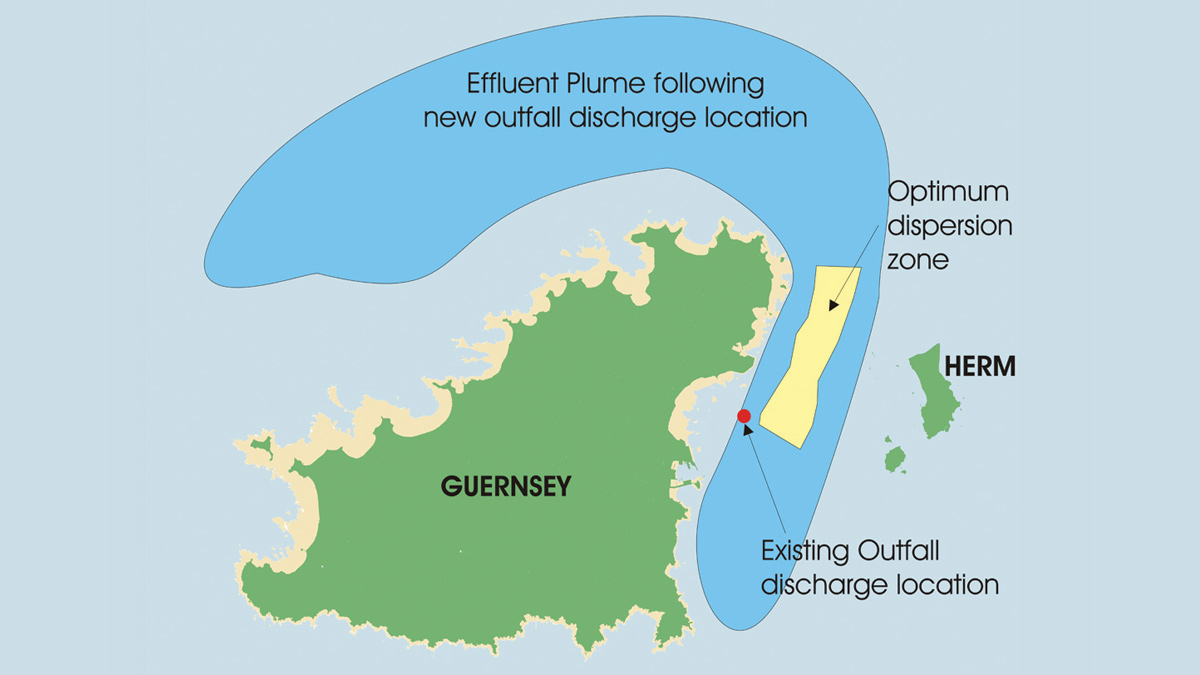
Dispersion Plume from LSO – Courtesy of Guernsey Water
Existing outfalls
The existing LSO was constructed in 1970, consisting of a 675 millimetre diameter ductile iron main, laid within a tunnel a maximum of 40 metres below the sea bed before rising to emerge through the sea floor, with a total length of 1,800 metres.
A condition and serviceability analysis on this main, undertaken in 2011, concluded that the remaining life expectancy was between zero and ten years. Catastrophic failure of the main beneath the sea bed was assessed as being extremely difficult to repair due to the pipe being laid in a permanently flooded gallery.
The Belle Greve Wastewater Centre Strategy
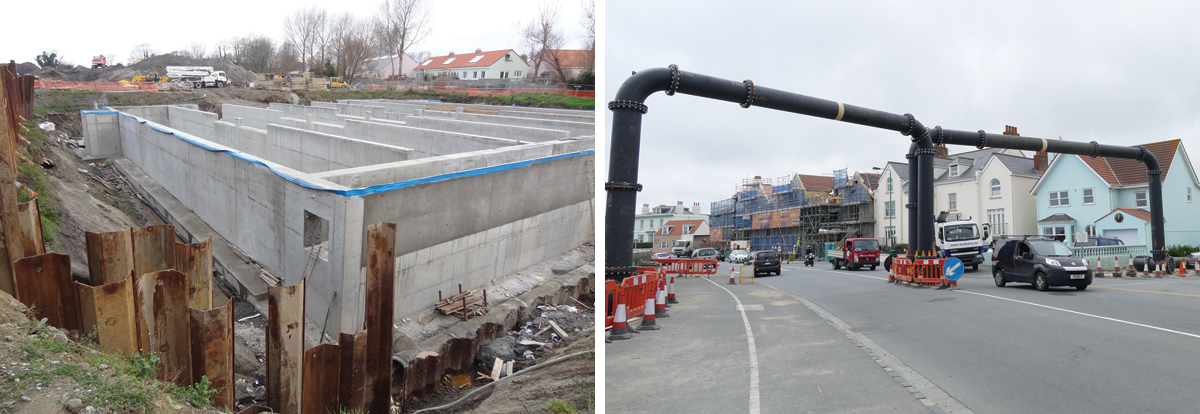
(left) Construction of storm tank and (right) stormwater overpumping pipe bridge – Courtesy of Guernsey Water
Previous phases of works included:
- Auxiliary pumping station: The first of 5 phases saw the construction of an auxiliary station to pump flows at a maximum flow rate of 1,000 l/s and connection of pipelines to existing 900mm diameter CI outfall constructed in 1905. This was designed to assist existing LSO with storm flow pumping and discharge.
- Tunnel and outfall pipes survey: The second phase saw the survey of existing tunnel and outfall pipes including non-destructive and destructive testing, which was carried out in 2008 by Black & Veatch. The reports concluded that the tunnelled outfall had a useful remaining asset life of between 10 and 20 years.
- LSO pumping station: Phase 3 was the complete renovation of the existing LSO station including new VSD Xylem pumps to replace the existing units and a new MCC panel. Additional works included breaking out much of the interior structure and providing flood protection to the station.
- Inlet works*: The Atkins Global designed inlet works provides the ability to screen to 6mm and remove grit from the waste flow. In addition, a 4,000m3 storm retention tank was constructed to provide a storage for flows in excess of the maximum LSO flow rate of 1,000 l/s upwards to maximum system rate of 2,500 l/s. These works were completed in 2013.
* Due to uncertainty surrounding the outfalls rehabilitation and the fact that the existing comminutor units and grit handling plant had finally ceased working, the decision was made to advance the phasing with the proposed inlet works (phase 5) being carried out as the fourth phase of works.
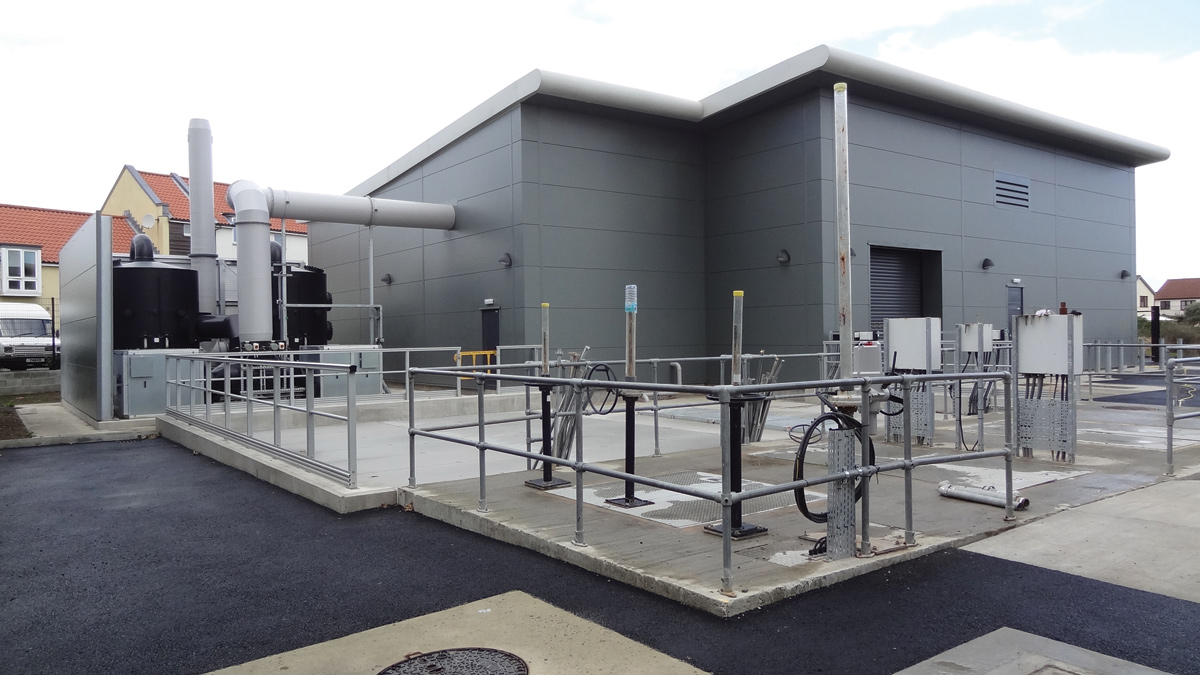
Belle Greve Inlet Works – Courtesy of Guernsey Water
Outfalls – Preliminary design and procurement
Preliminary design was initially developed by Guernsey Water and its consultants (CH2M and Ipitath Ltd) which resulted in the correct hydraulic parameters, specifications and preliminary design route being identified and assisted with compiling the contract documents.
The Guernsey east coast geology consists largely of hard Gabbro granite and therefore to assist with the preliminary route options a complete bathymetric and sub-sea seismic survey was undertaken of the Belle Greve Bay. The results from these surveys were able to identify a potential soft material channel that could be utilised to lay both pipes, without the need for removal of significant volumes of rock, although this resulted in a pipe configuration that curved both horizontally and vertically.
In January 2015 Guernsey Water appointed Van Oord UK Limited via an ‘NEC3’ design & build contract and was tasked with replacing both outfalls serving the BGWwC. The LSO was to discharge 1,000 l/s during all tide conditions and the SSO a further 1,500 l/s during intense storm conditions.
Van Oord appointed Royal Haskoning DHV to undertake the detailed design work and subcontracted all the onshore works to local civil engineering contractor, Geomarine Ltd.
The works entailed installing a new 900mm diameter solid walled high density polyethylene (HDPE) outfall pipe to discharge flows approximately 2.4km offshore in the fast flowing waters of the Little Russel at a depth of 30m below mean low water, together with a new 1,200mm diameter HDPE outfall for the storm flows approximately 1,800m off shore. The discharge locations were identified following coastal modelling by Intertek Metoc to determine the optimum dispersion and dilution zones. The existing LSO was maintained throughout the construction period until commissioning of the new outfall was achieved; the existing SSO had to be partly replaced with a temporary overland pipe arrangement during the onshore construction works as the new pipes were laid along the existing line.
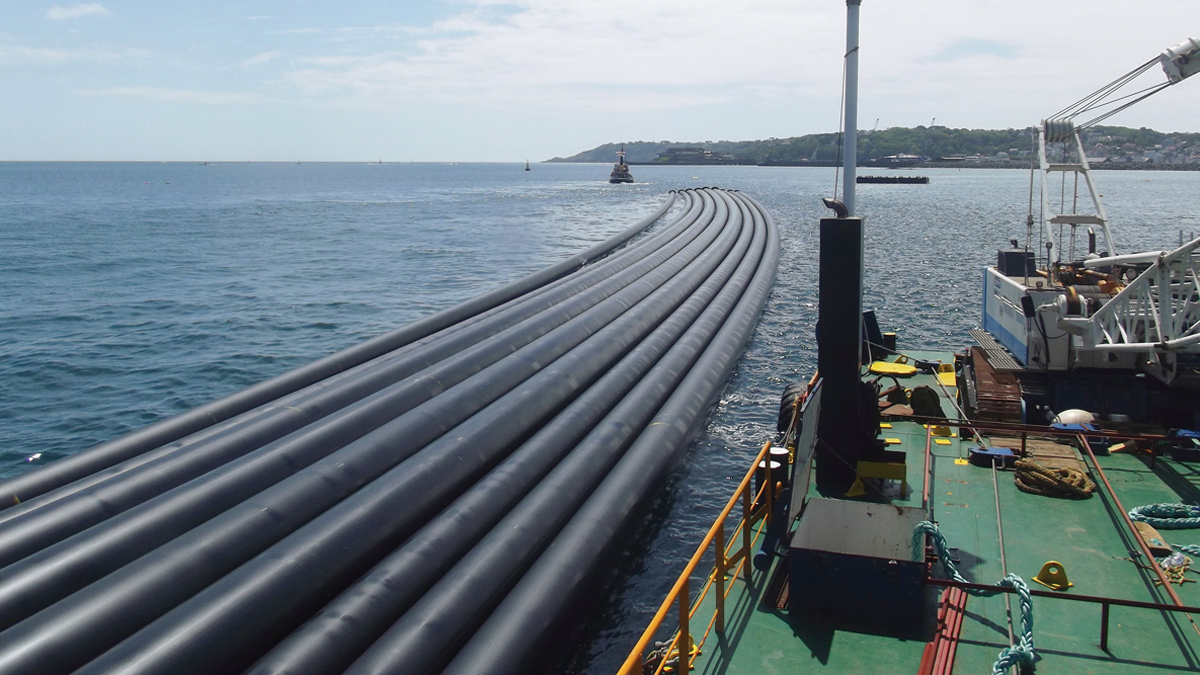
Mooring of pipes prior to collar installation – Courtesy of Guernsey Water
Offshore construction works
Early detailed design concentrated on the offshore pipes so that confirmation to the pipe manufacturer could be given for production to commence in Norway with Pipelife Norge AS, in time for delivery in late May to enable preparation and installation of the concrete collars.
Van Oord undertook a more detailed bathymetric survey of the sea bed along the line of the proposed route to confirm the exact route that both pipes could follow. The detailed design resulted in both pipes following a curved alignment from the existing Red Lion slipway area.
The parties worked in close cooperation to produce a final design which removed the need for large quantities of imported rock armour and provided a high standard of stability and protection to the pipelines. For the outfall pipes laid in a trench through the softer material channel the use of continuous concrete weight collars (1.2m long, 907kg each LSO, 1,498kg SSO) were used. For the section of the LSO laid on the seabed discrete concrete weight collars (0.85m, 2,100kg) were used. These concrete collars were sized to meet the minimum specific gravity requirement of 1.35 and the design wave and current conditions for stability.
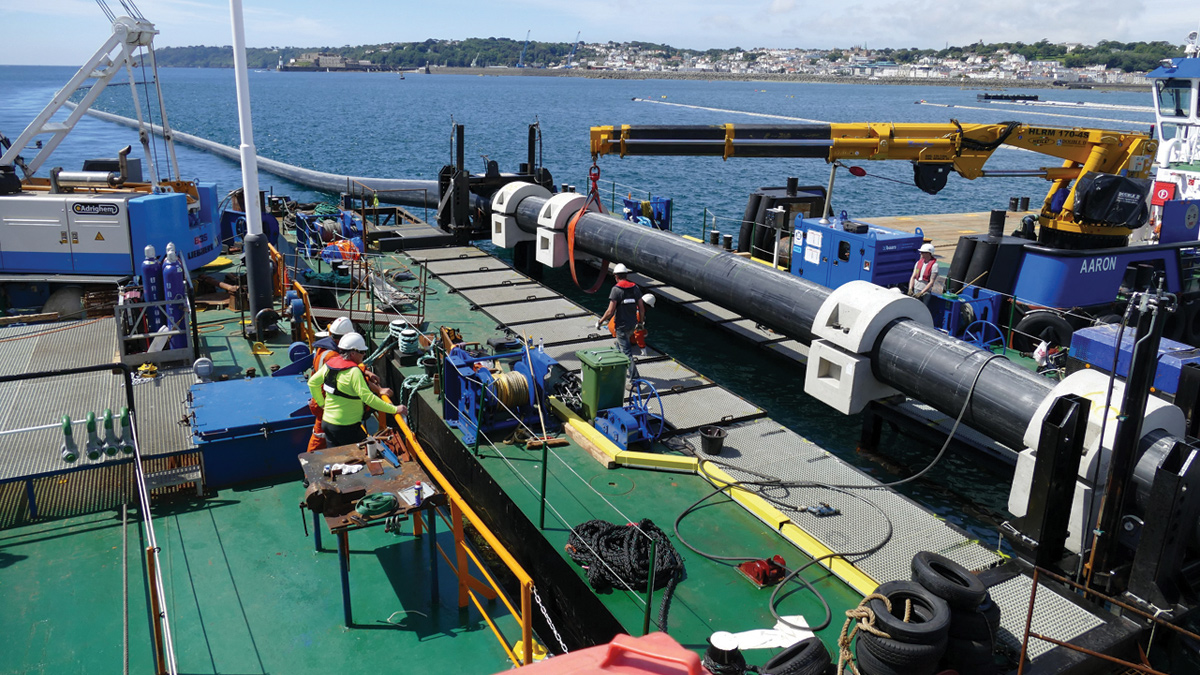
Traditional fixed collars fitted to LSO – Courtesy of Guernsey Water
Due to the limited land available, attention to the fitting of the concrete collars onto the pipe was a particular concern to the contractor. The usual arrangement is to secure a suitable quay or wharf where there is access to the floating pipe alongside a suitable hard-standing area to store and eventually fit the 3,000 (No.) collars to the pipes. However no location onshore could be identified where pipes in strings longer that 160m could be found; therefore a relatively innovative solution was developed where pipe and collar storage and subsequent fitting of the collars could be undertaken offshore. Van Oord designed and constructed a purpose built vessel, the ‘Rijger’, which was moored alongside the backhoe dredger ‘Piet Ponton’ configured for use with a mobile crane. Additionally the concrete collar storage vessel, the ‘Stemat 78’ was anchored adjacent ensuring a safe and stable platform for collar lifting and placing on pipes could be achieved.
The LSO outfall terminated with a diffuser section comprising of 8 (No.) separate discharge ports to ensure the required initial dilution figures were achieved. As the diffuser section was laid on top of the seabed it was not possible to install concrete diffuser domes to protect the ports. A revised design incorporated a steel frame fixed to adjacent concrete collars to protect the port and duck-billed valve from damage. The SSO discharged via a single pipe with a single duck-billed valve at the end of the trenched section with discrete collars and rock bags to provide additional stability.
Offshore dredging and trench formation
The pipe alignment resulted in both the LSO and SSO being laid below sea-bed level for approximately 1,700 metres from the foreshore. The dredging work was undertaken by the ‘Razende Bol’ working a 24/7 shift pattern to excavate approximately 70,000m3 from a trench with maximum excavated depth of 4m.
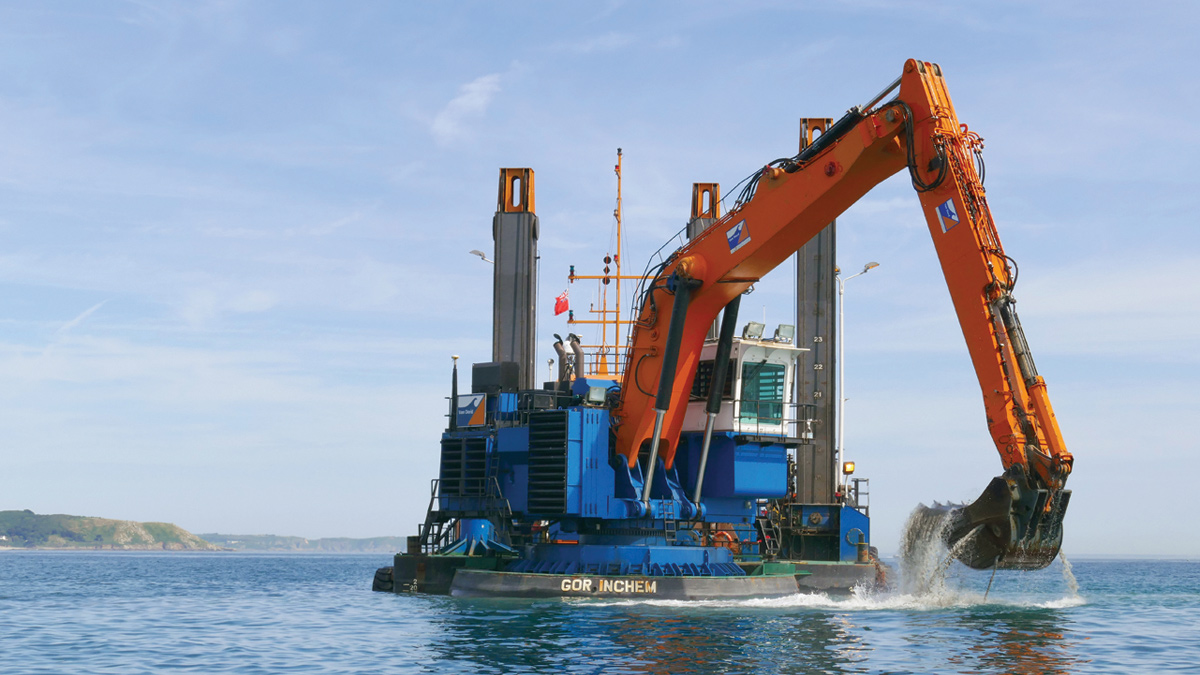
‘Razende Bol’ back-hoe excavator – Courtesy of Guernsey Water
Location and depth control was managed using real-time GPS information to ensure the correct alignment was achieved. Excavated material was deposited adjacent to the trench for use as backfill upon installation of the pipes; loss of material was estimated to be around 20%.
Further surveys were undertaken post-pipe sinking/pre-backfill to ensure they were correctly position within the trench.
Preparation work on the beach
Access to the beach for heavy plant and machinery was restricted to a single ramp, close to the main site compound and construction area for landward connection chamber.
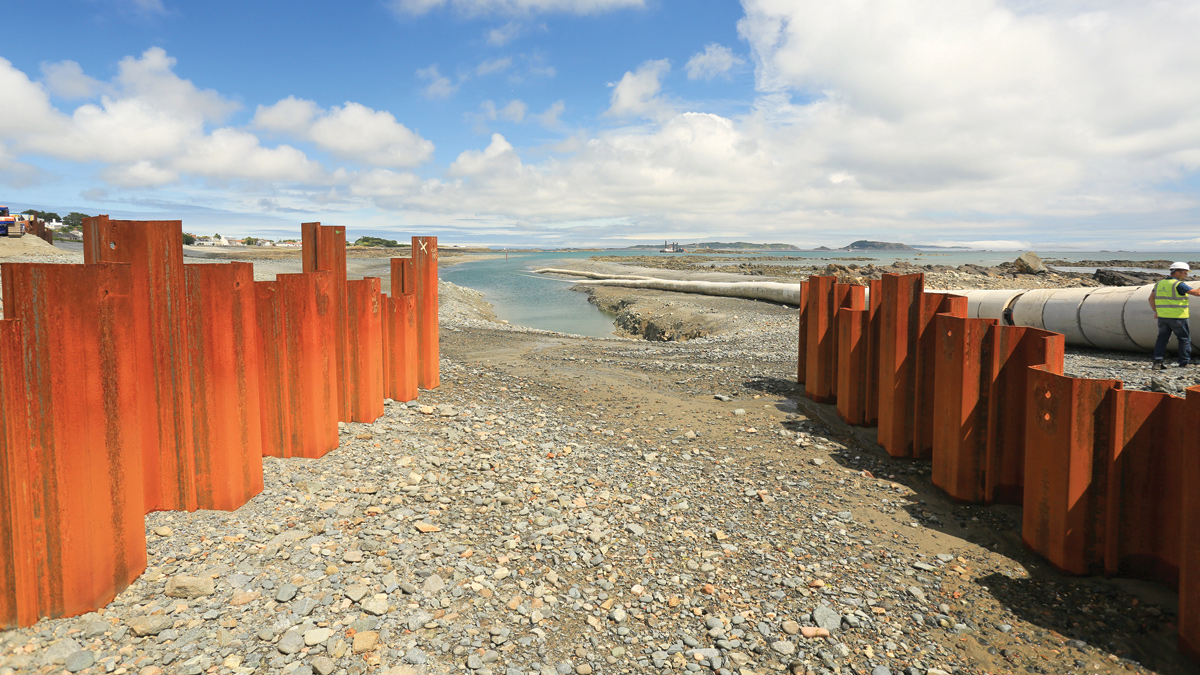
Cofferdam with pipes temporarily located off -line – Courtesy of Guernsey Water
At high tide, the beach floods up to the sea wall, therefore a substantial sheet-piled safe-refuge was constructed to the north side of the pipeline route close to the top of the beach, where piling plant, excavators and other equipment could be stored between shifts. Due to the close proximity of residential properties and tight noise nuisance restrictions imposed by the Environmental Health Department only daylight hours could be used to install the cofferdam.
A 40m long sheet-piled cantilever design cofferdam was installed from the seawall down the beach. The sheet piles were driven to depth but designed to extend 1.0m above the beach level to accommodate any small shift in beach level. Due to localised Gabbro outcrops not all piles could be driven to depth; in addition as the trench line was not ready at time of offshore pipe installation, the outfalls had to be laid adjacent to trench on the foreshore.
The cofferdam was excavated to the required trench profile using land-based plant. However due to the Gabbro outcrops, specialist Hydraulic rock rippers and pneumatic hammers had to be employed which had a significant impact on time and cost.
Pipe spool pieces were delivered to the site ready to connect the new outfall to the chamber.
Dredging and trench formation
The offshore trench was dredged by Van Oord using the back-hoe dredger ‘Razende Bol’; works were carried out switching between inshore and offshore depending upon tide and water depth and were carried out in two shifts to match tidal conditions.
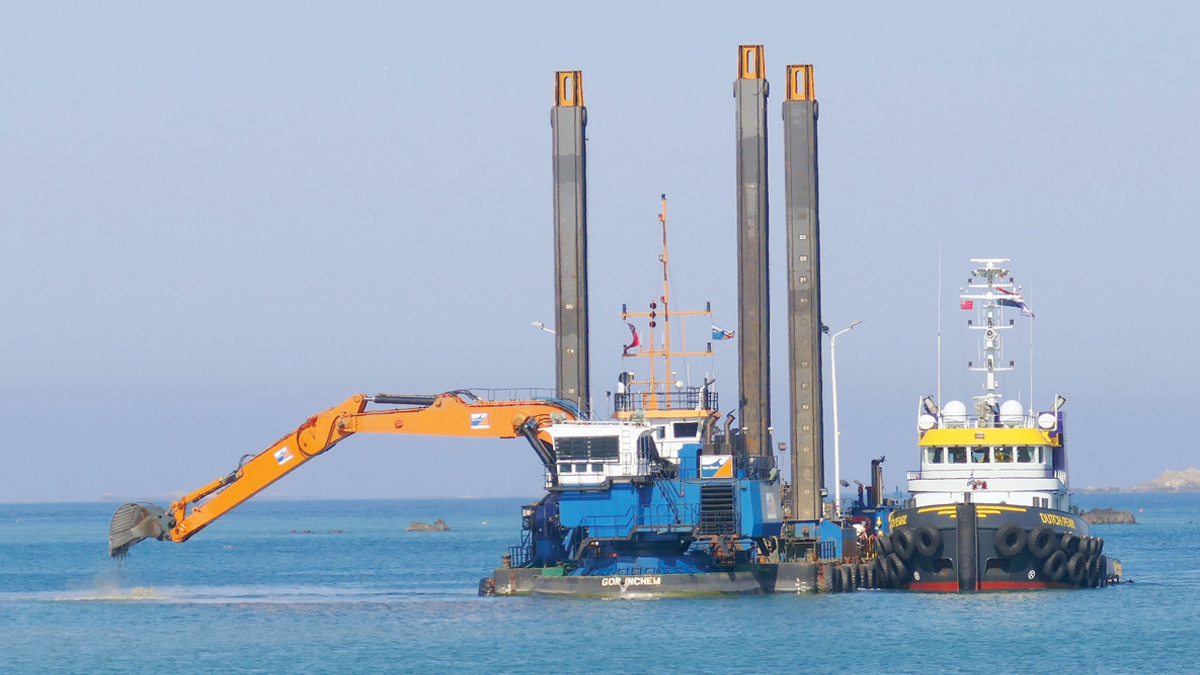
Razende Bol’ back-hoe excavator – Courtesy of Guernsey Water
All excavated material was side-cast for reuse as backfill once the buried sections of both the LSO and SSO had been installed; although there was a risk of material being lost this was estimated at being not greater than 20%. This proved to be the position upon final measure from the ‘out survey’.
Although rock was not encountered at any location beyond mean low water, a high point was found between chainage 40 and 130m from the sea wall, where 1,600m3 of hard Guernsey Granite had to be removed before both outfalls could be installed in their final position.
Installation of outfall and diffuser
The polyethylene pipe was delivered to Guernsey in nine lengths, each approximately 550m long; the tow taking just over one week from Norway. Due to the very high tidal range and lack of a suitable local sheltered area, the pipes were strung between two anchored barges within Belle Greve Bay.
Once the trench had been dredged and a suitable weather window identified, the pipes were assembled in lengths of approximately 1km and towed into position and held in place along the route using the spud barges ‘Stemat’ and ‘Abeko Server 1’, ‘Piet Ponton’, ‘Razende Bol’, along with work boats ‘Dutch Pearl’, ‘Multrasalvor III’, ‘Aaron’ and other smaller vessels.
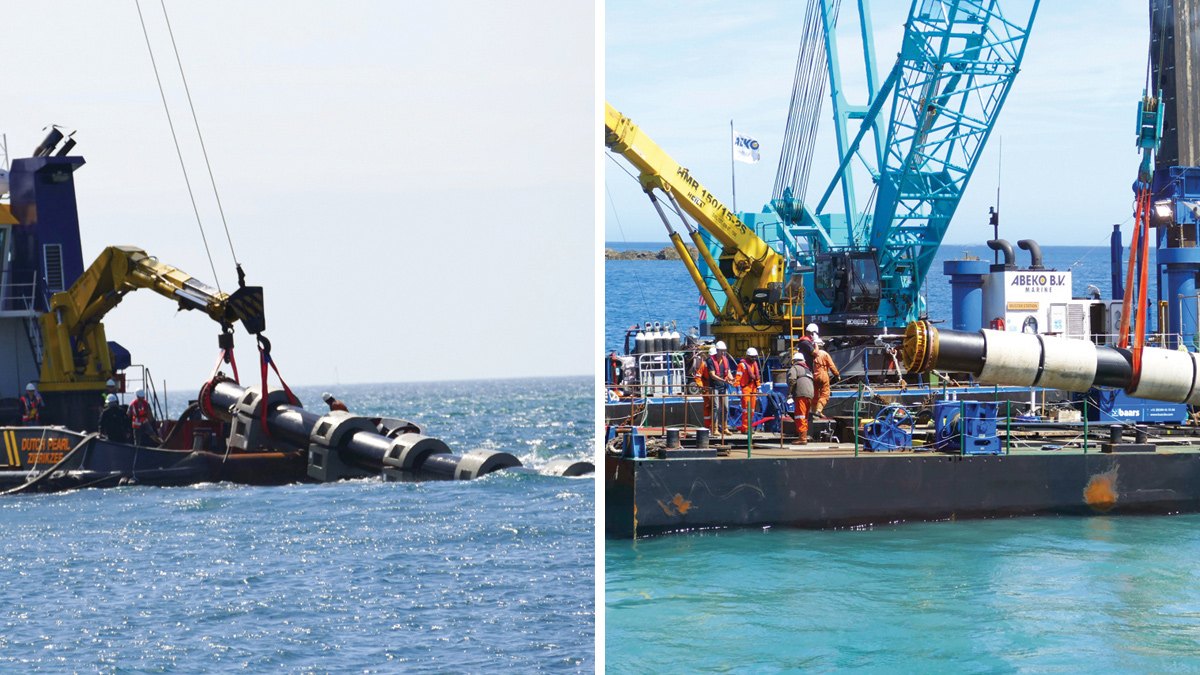
(left) Commencement of pipe sinking and (right) completion of first pipe string installation. Awaiting connection of second string – Courtesy of Guernsey Water
The pipeline was then flooded from diffuser end first using the float and flood technique, the long sea outfall was laid in three sections while the short sea outfall in two; jointing of each section was undertaken offshore.
Concrete circular collars were placed along the section to be buried below seabed level and traditional style collars fitted where the outfalls sit on the seabed; on completion, the open trench was backfilled.
3rd party and stakeholder management
The onshore works were situated between the two main population centres of St Peter Port and St Sampson and offshore in the heavily used and trafficked eastern seaboard. Therefore it was clear that impact on users (commercial and pleasure) of the Little Russel and the main carriageway on land would be significantly affected by the works.
Stakeholder engagement was commenced over twelve months prior to the expected 2015 summer start, with liaison to obtain necessary permissions (partial closure of the highway that needed to be crossed, restrictions on shipping and pleasure boat use in Belle Greve Bay and adjacent to works areas). The engagement also provided communications to local residents and the wider population on what would be a usual and interesting activity to the general public.
Tie in work, commissioning and removal of the old outfall
A series of polyethylene spools were made ready to make the connection from the inshore end of the outfall pipeline to the new outlet from the landward connection chamber. The old SSO pipe laid across the foreshore was removed; however the sub-sea LSO and tunnel section was left in place.
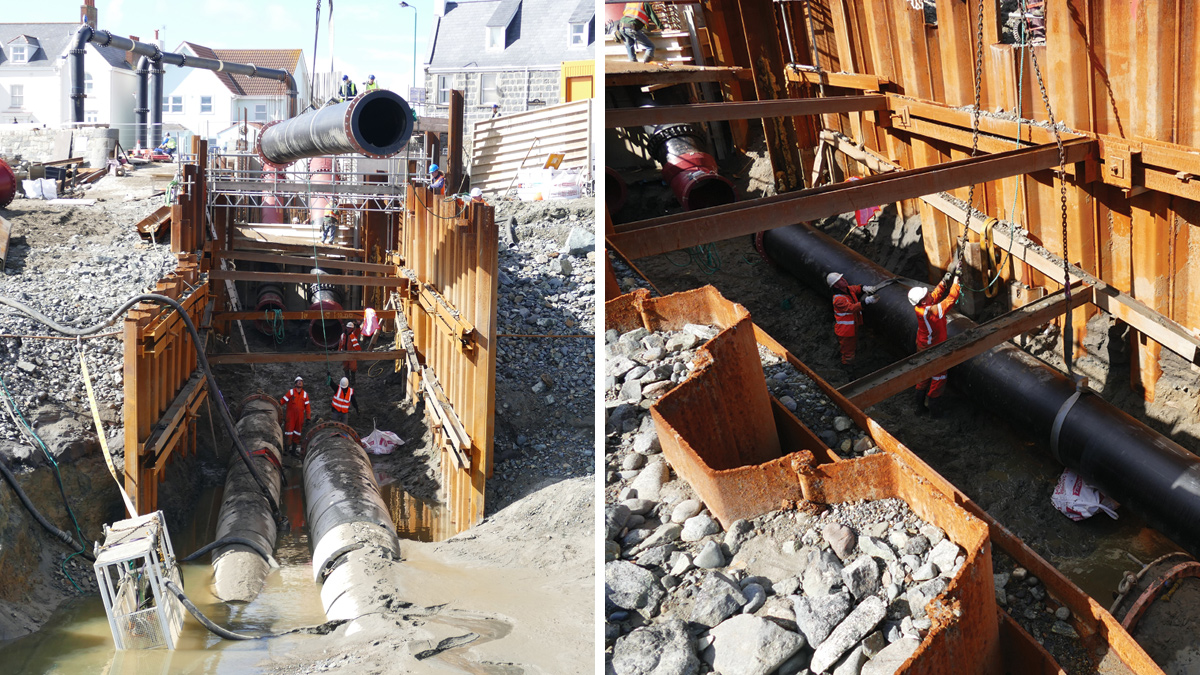
Installation of spool piece connecting offshore to onshore pipelines within cofferdam – Courtesy of Guernsey Water
Conclusion
The success of the Guernsey project is as a result of collaborative working and the excellent working relationships developed between Guernsey Water, CH2M, Ipitath, Van Oord, Geomarine, Pipelife Norge AS and many external stakeholders.