Harrowside Long Sea Outfall (2015)
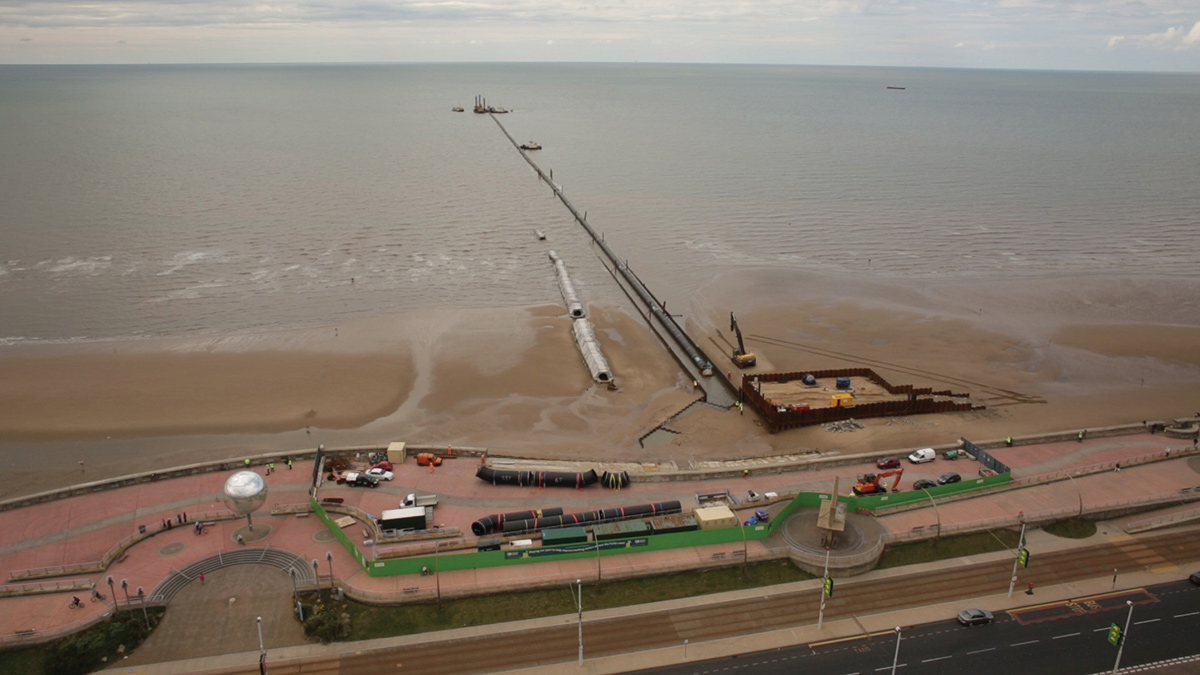
Harrowside pipe Installation - Courtesy of Land & Marine
Harrowside Outfall is the first element of the Blackpool South Strategy to further improve the bathing water quality along the Fylde Coast which involves increasing the capacity of the existing sewer network, surface water and maintenance works to the Lennox Gate Pumping Station. The existing Harrowside outfall, built in 1938, has reached the end of its useful life. The outfall is used as a storm overflow from two upstream pumping stations; Lennox Gate and Harrowside, which protect Blackpool from flooding during extreme rainfall. The AMP6 replacement Harrowside Outfall shall maintain the existing consent to discharge flow of 4m3/s at a tide level of 4.0m AOD, prior to any excess flow being discharged via the beach overflow. Flows in excess of 4m3/s are discharged from the outfall chamber via a beach outlet.
Undertakings
In March 2015, United Utilities appointed J. Murphy & Sons to design, build and commission works in connection with the replacement of Harrowside Outfall located just south of Blackpool Pleasure Beach. The project, which commenced on site in May 2015, will be delivered by Land & Marine Engineering, a wholly owned subsidiary of J. Murphy & Sons. The works are part of United Utilities’ £125m investment to improve the sewer network along the Fylde Coast over the next five years.
The engineering and construction work undertaken by Land & Marine involves the design and construction of a new 2.1m diameter solid wall polyethylene gravity outfall pipe to discharge the consented flows 1km offshore and the decommissioning and removal of the existing outfall. A distance of 1km was agreed with the Environment Agency to minimize quality and aesthetic impacts on bathing waters. Work also involves reconfiguration of the outfall chambers to maintain the existing flows until the new long sea outfall has been commissioned.
Permanent and temporary works design
Conceptual hydraulic design was initially developed by United Utilities resulting in specified hydraulic constraints and levels and design parameters. United Utilities pre-procured a pipe supply contract to ensure delivery could meet project timescales. The detailed design was carried out by Land & Marine’s in-house design team. Intensive analysis was undertaken within the first two weeks of the project to finally confirm the exact pipe dimensions and place the order for pipe production to get underway by Pipelife Norge AS in Norway.
Moving the alignment of the new pipeline 30m to the north minimised the risk of undermining the existing cast iron pipeline. This dictated that the diversion from the existing outfall chamber to the new alignment was required to cross the beach at an angle of approximately 45 degrees.
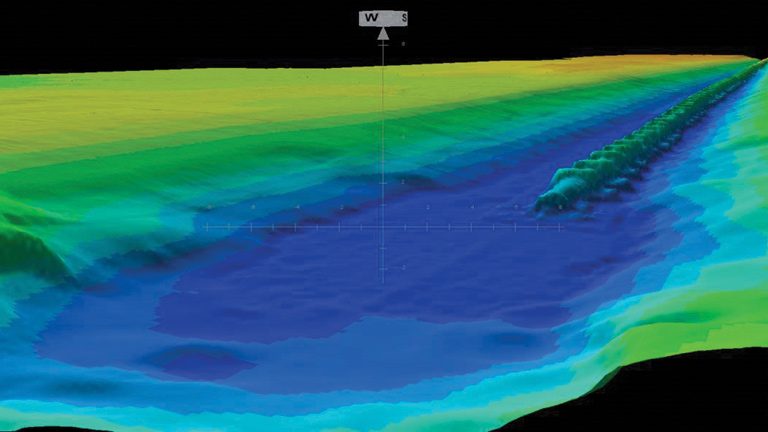
Harrowside pipe in trench – Courtesy of Land & Marine
The design brief required the diffuser to be fitted with non-return (or duck-bill) valves to withstand an external pressure of just over 10m head of seawater. At low or zero flow, the outfall pipeline will drain down at low tide but on the rising tide, the consequence of the duck-bill valves will prevent seawater ingress thereby creating the potential for the drained section of the outfall pipeline to become buoyant. To counter this effect additional measures were required and to ensure that the inter-tidal section would remain stable at all times, precast concrete ‘kennels’ were installed as additional weight along the entire length of the beach section.
The low lying nature of the Fylde coast, which is susceptible to flooding, means there is little potential head to drive the flow through the pipeline and diffuser. Land & Marine’s designers mitigated the head losses as far as practically possible and designed the diffuser arrangement to incorporate oversized duckbill valves.
Detailed calculations were conducted using the company’s in-house Float-Flood program, to confirm that the pipeline could be safely floated into the trench during installation and flooded. Stability calculations were performed to demonstrate that the pipeline would be stable in its installed and buried condition. The design team developed a concrete weight collar design which greatly simplified the installation and attachment operation thereby shortening the programme.
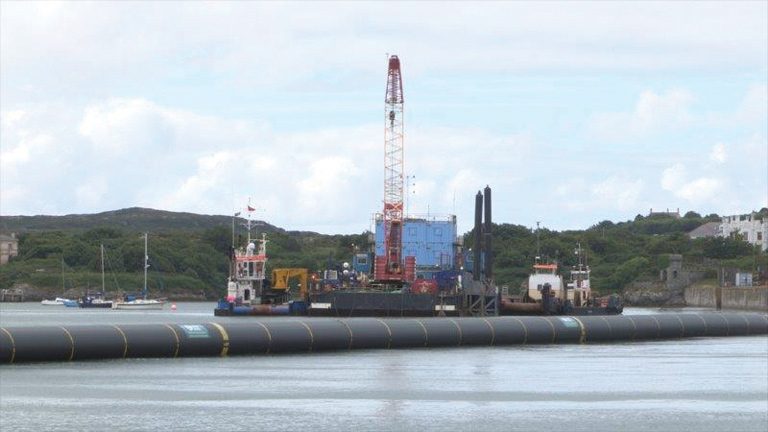
Vessels at Holyhead – Courtesy of Land & Marine
Preparation work on the beach
Access to the beach for heavy plant and machinery was restricted to a single ramp, close to the main site compound, some 800m south of the construction site from where all heavy plant and equipment was delivered. A second compound was constructed within a cordoned off area on the promenade close to the working area.
At high tide, the beach floods up to the sea wall, therefore a substantial sheet-piled safe-refuge was constructed to the north side of the pipeline route close to the top of the beach, where piling plant and other equipment could be stored between shifts. A shift pattern was adopted to maximise the time available to access the beach, to install the cofferdam and to work in the discharge chamber beneath the promenade.
A permit system was instigated with United Utilities operational staff to ensure that access to the chamber was only permitted when safe to do so and when there was no requirement for discharge from the upstream pumping stations.
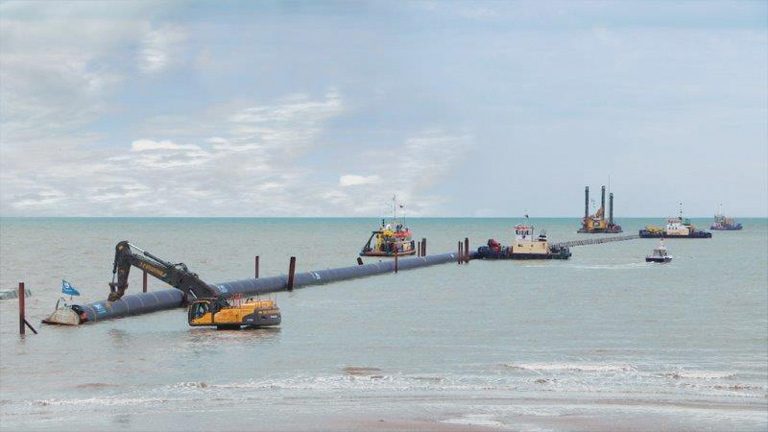
Harrowside pipe installation plant – Courtesy of Land & Marine
Considerable work was required within the outfall chamber, involving diamond wire cutting sections of the existing concrete weir walls to enable the main flow to be directed to the new outfall while at the same time maintaining the existing flow to the old outfall. Once the new outfall is connected, any storm water overflow will be discharged over a newly constructed weir wall at the point where the old outfall was previously connected to the chamber.
The constraints of confined space working was alleviated by the construction of an additional access point made by cutting a slot through the thick concrete roof. Land & Marine utilised the services of a specialist diamond wire cutting company operating remotely-controlled machinery which avoided the requirement for manned operation within the chamber for much of this work.
A 400m long sheet-piled cantilever design cofferdam was installed from the seawall down to mean low water. The sheet piles were driven to depth but designed to extend 1.0m above the beach level to accommodate any small shift in beach level. Specially designed guide piles were installed to ensure that the floating outfall pipe would remain within the cofferdam during the installation period at all states of the tide.
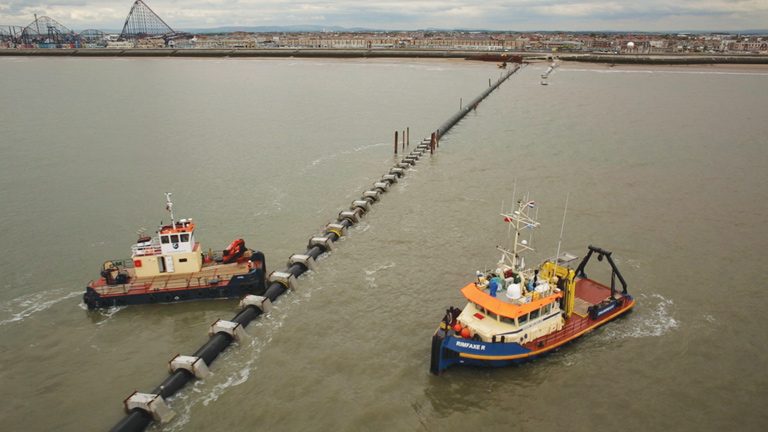
Harrowside pipe Installation – Courtesy of Land & Marine
The cofferdam was excavated to the required trench profile using land-based plant and a winch was set up on the adjacent safe refuge. A pull-in wire was installed via deflection rollers at the head of the cofferdam and laid out to the offshore end where it was buoyed off ready to hand over to the marine installation spread.
Pipe spool pieces were delivered to the site ready to connect the new outfall to the chamber.
Dredging and trench formation
The offshore trench was dredged by Rohde Nielsen using the back-hoe dredger Mjølner R with a split hopper dump barge in attendance. The spud pontoon dredger worked up to the cofferdam wing walls and as with the beach works utilised the tides to maximise operability close to the beach. The dredger was used during the outfall pipeline installation to support pipe positioning and flooding operations.
The as-laid survey results confirmed that the pipeline was installed within the trench corridor and down to the required depth. Work is planned to provide scour protection in the form of concrete mattresses from the promenade to mean low water springs and to back fill the trench with as-dug material.
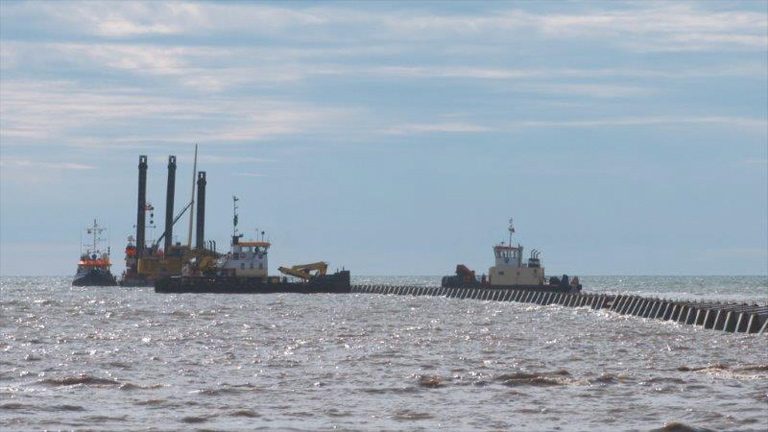
Harrowside pipe Installation – Courtesy of Land & Marine
Installation of outfall and diffuser
The polyethylene pipe was delivered to the UK in two lengths, each approximately 500m long; the tow taking just over one week from Norway. Due to the very high tidal range and lack of a suitable local sheltered area close to Blackpool, the pipes were towed to Holyhead Harbour in Anglesey, where on 19th June they were moored in preparation for attachment of the concrete collars.
Land & Marine’s barge, LM Constructor, recently equipped with twin spud legs, was mobilised to Holyhead to support this operation. By the third week in July, the two pipes were connected and a reinforcement system fitted at the joint. Tow and trail heads, pumping and venting valves were fitted and the Warranty Surveyor verified the pipeline as ready to tow.
Once the trench had been dredged and a suitable weather window identified, the fully assembled outfall pipe was towed to Blackpool for installation. On arrival at Harrowside on 31 July the pipeline was pulled ashore into the cofferdam using the beach winch.
The pipeline was then flooded within the cofferdam, using the float and flood technique. Concrete ‘kennels’ are to be placed over the pipeline within the beach trench to provide the additional stability required. On completion, the trench will be backfilled.
At the end of the outfall, a gravel bed is to be placed and prepared prior to placing the precast concrete diffuser structures. The diffuser structure was precast on site at Holyhead in three 30,000kg sections and will be transferred to Harrowside on the LM Constructor. The diffuser sections were each cast with locating configuration joints to enable the sections to be easily positioned using divers.
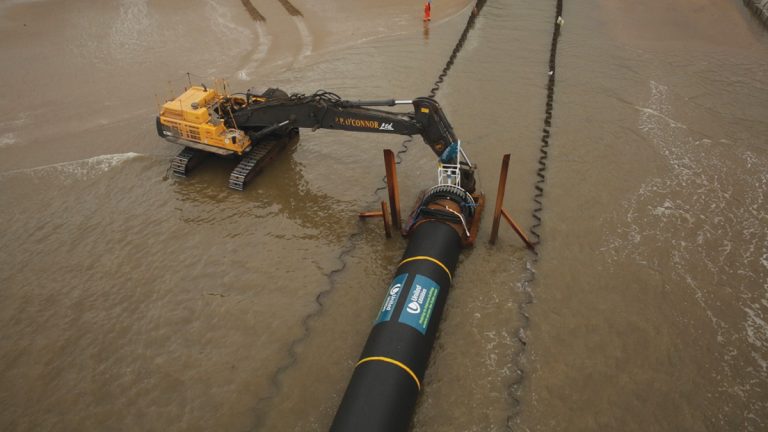
Harrowside pipe Installation – Courtesy of Land & Marine
The diffuser base is to be lowered into position using the LM Constructor and once in position the spool piece to connect the outfall pipe to the diffuser is to be site measured and prepared. Once the spool is installed, the diffuser top unit complete with duck bill valves, is to be placed in position and the spoolpiece grouted in place.
The trench is to be backfilled around the diffuser with scour protection material and a marker buoy installed.
Tie in work, commissioning and removal of the old outfall
A series of polyethylene spools were made ready to make the connection from the inshore end of the outfall pipeline to the new outlet from the outfall chamber. When this connection has been completed and construction works within the chamber have also been completed, work will commence on removal of the old outfall.
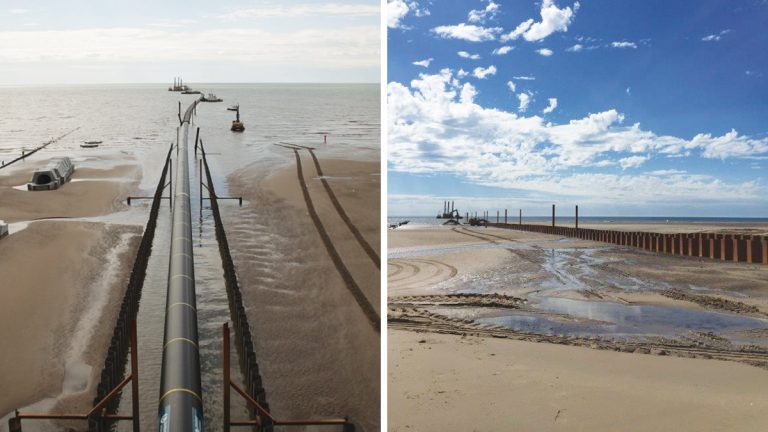
Harrowside pipe Installation – Courtesy of Land & Marine
Conclusion
The success of the Harrowside project is as a result of collaborative working and the excellent working relationships developed between United Utilities, Land & Marine and its supply chain and the many external stakeholders.
The schedule is restricted to works between April and September, due constraints set out in the Marine Management Organisation (MMO) license, such as wintering birds. The design and construction team have overcome a number of significant challenges to deliver a complex scheme within a tight time frame, and are set to achieving a project in use date within 6 months of the contract award.
At the time of writing (August 2015) the marine section of the pipeline including the diffuser installation is nearing completion.
The final tie-in and works to remove the existing outfall are on-going, with the overall project completion scheduled for October 2015. The successful completion of this project will improve bathing waters and also support Blackpool Council in maintaining a clean and safe beach for this popular tourist resort.