Bolton-upon-Dearne WwTW (2020)
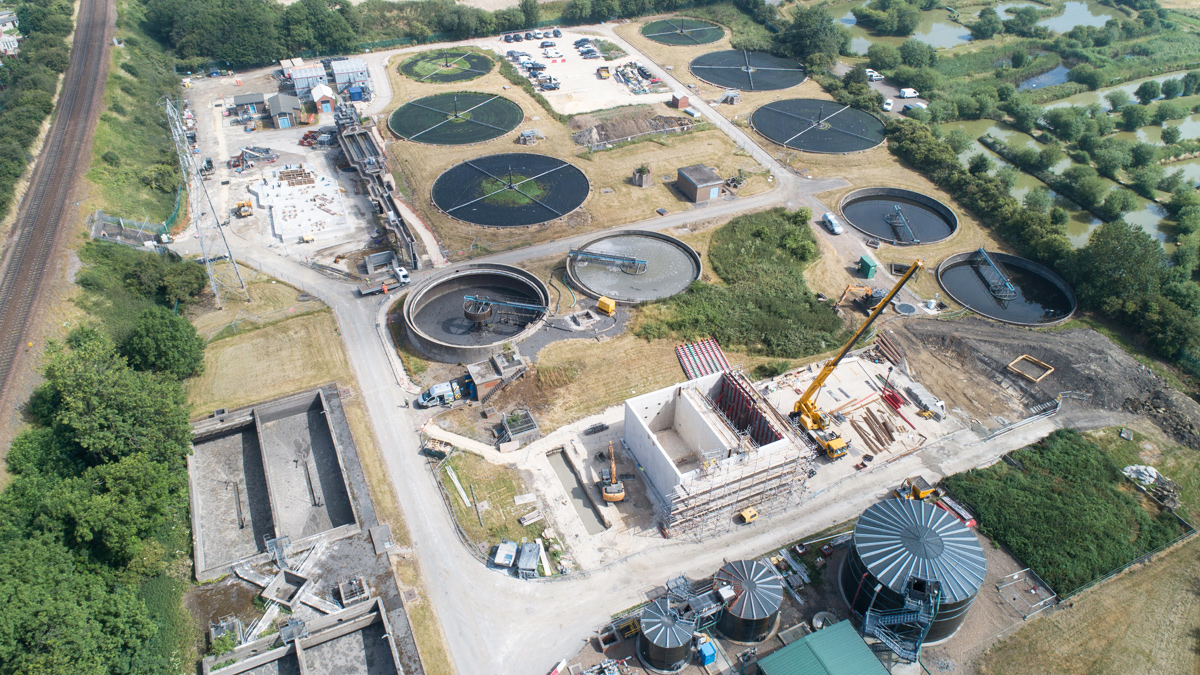
Bolton-upon-Dearne WwTW serves about 25,000 customers - Courtesy of Galliford Try
Bolton-upon-Dearne Wastewater Treatment Works serves approximately 25,000 customers in Rotherham. Faced with an Environment Agency consent to reduce ammonia at the works, Yorkshire Water has undertaken a £12.3m, 14-month project to construct a brand new inlet works and install a new treatment process that will greatly improve the quality of water being released back into the River Dearne, bringing about significant environmental benefits to the area including helping fish populations. Yorkshire Water contracted Galliford Try to install a moving bed biofilm reactor (MBBR) system that it expects to deliver quality results at a lower cost than activated sludge processes (ASPs).
Yorkshire Water MBBR installations
Bolton-upon-Dearne WwTW is Yorkshire Water’s biggest MBBR installation to date and follows on from a £4m upgrade also undertaken by Galliford Try at the nearby Tankersley WwTW, which serves around 2,000 customers.
Prior to the upgrade, the ammonia output from the Bolton-upon-Dearne WwTW was around 13 mg/l, risking toxic impacts on fish and macro-invertebrates. The new 2020 Environment Agency consent requires a fall to 3 mg/l at 95 percentile (requiring 95% of samples come in below that level) and 1.5 mg/l at 50 percentile, resulting in a significant improvement to the quality of the water released back into the River Dearne.
Following the installation of Veolia Water Technologies MBBR plant at Tankersley WwTW, ammonia output achieved a 0.65 mg/l target at 50 percentile, but it generally runs about 0.1 mg/l and so is almost completely ammonia-free.
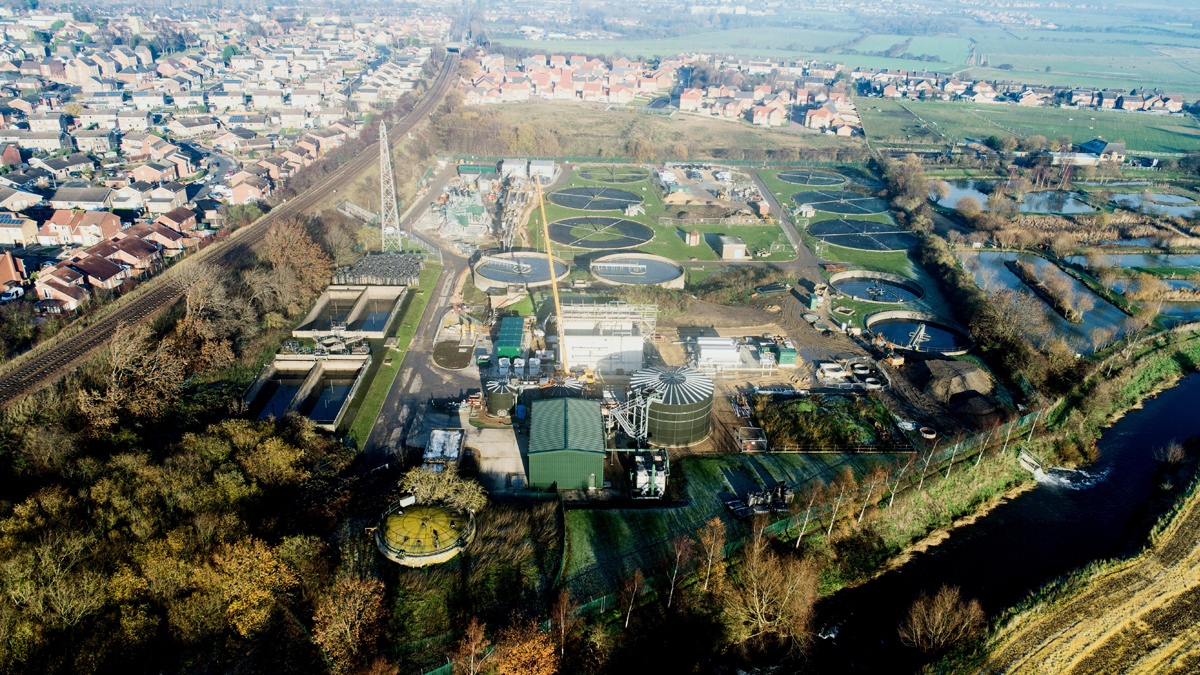
Bolton-upon-Dearne WwTW, South Yorkshire – Courtesy of Galliford Try
Moving bed biofilm reactor (MBBR)
The moving bed biofilm reactor is a low-maintenance, tertiary treatment system that involves growing a biofilm of bacteria and other micro-organisms on perforated plastic discs inside tanks. Aeration grids inside the tanks provide air bubbles that cause the discs to rotate and feed the bacteria. More aeration results in more ammonia-enriched feed being given to the bacteria, and the more active the system becomes. The concept was invented in the late 1980s by Prof. Hallvard Ødegaard, who was aiming to ‘adopt the best from both the activated sludge process and the biofilter processes without including the worst’. While it was developed with nitrogen removal in mind, further uses – including combating ammonia – have expanded the possibilities for its applications.
The Bolton-upon-Dearne WwTW operates using two pairs of 14m x 14m concrete tanks in a lead-lag system. After undergoing primary and secondary treatment, flow enters the first of one of the pairs of tanks to draw out some of the ammonia before entering a second to reduce levels further. Flow exits into a collection chamber featuring 10-micron drum filters, which will remove any micro-organisms that have died.
While MBBRs are lauded for their relative ease of use, the installation presented some challenges. The initial seeding process typically takes anywhere between eight and 16 weeks but can be unpredictable; factors such as the ambient temperature and the size of the MBBR, which is significant at Bolton-upon-Deane, can affect seeding time. Process engineers from Galliford Try and Veolia Water Technologies (who designed and manufactured the MBBR plant) provided the expertise to ensure that the initial seeding process was successful.
The 3 (No.) blowers used to aerate the MBBR required a power upgrade up to 450 kVA at a site that can only be accessed via a single lane. The transformer that serves the site also serves a nearby housing estate as well as new developments and a third-party power company had to dig up the site access road to put in the high-voltage cables, resulting in a near site shutdown for health and safety reasons.
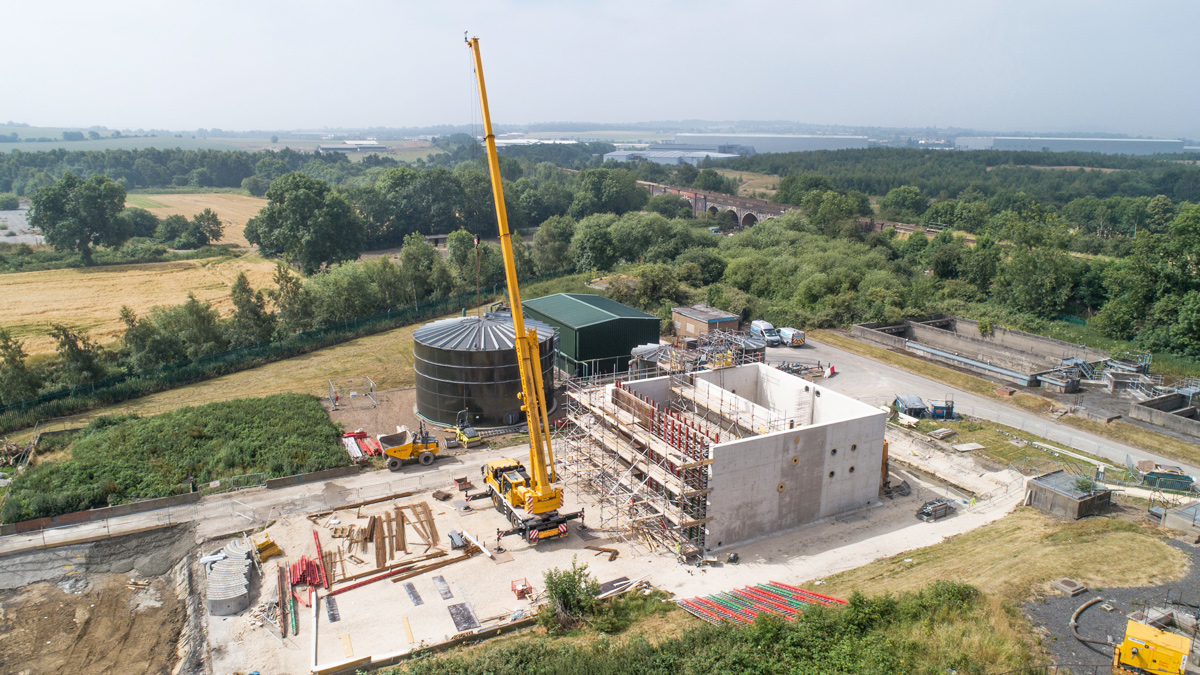
The MBBR during construction (June 2018) – Courtesy of Galliford Try
Bolton-upon-Dearne WwTW: Key project participants
- Principal contractor: Galliford Try
- Principal designer: Galliford Try Technical Services
- Civil and structural designer: GHD
- Subcontractors: CPC Civils
- MBBR plant: Veolia Water Technologies
- Inlet works modular package plant: SPIRAC
Bolton-upon-Dearne inlet works
The Bolton works has seen several upgrades over the last 100 years, most recently in the 1990s. Whilst many aspects of the site have remained in satisfactory shape, the 50-year-old inlet works could no longer cope with demand and needed to be replaced as part of this project.
The main issue with the old inlet works, and what posed the biggest problem for the site going forward, was that the receiving chamber was not big enough for the volume coming in and the screening process was not working. Rags were constantly bypassing the screens and following through into the secondary treatment area.
SPIRAC, subcontracted to Galliford Try, provided a prefabricated packaged treatment plant founded on a reinforced concrete slab. The plant was supported by a galvanised steel structure, elevated approximately 5m above ground level, to enable flows to gravitate through the downstream process units.
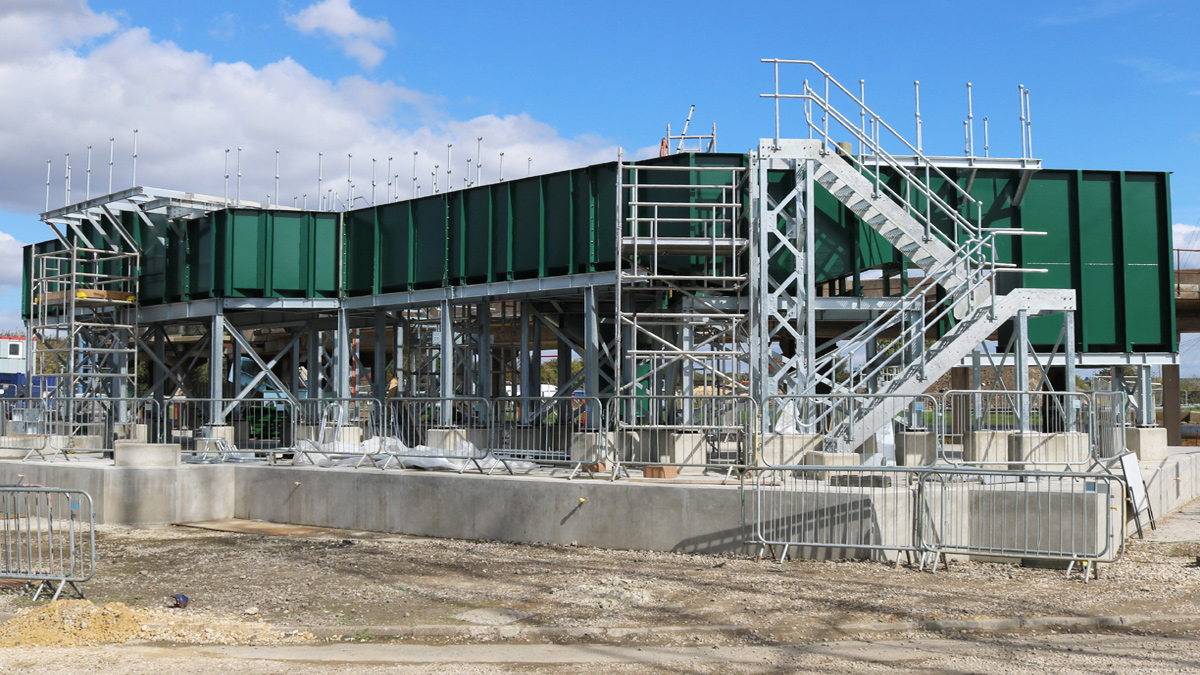
The new elevated inlet works make use of gravity to facilitate flows – Courtesy of Galliford Try
The stainless steel inlet was designed and built off site before being assembled on site in modules. SPIRAC installed 3 (No.) FINEGUARDTM screens, each capable of passing a maximum flow of 566 l/s of sewage at a design water depth of 1m downstream. The FINEGUARDTM screen consists of a band of perforated screen panels which are secured to drive chains on either side of the panels. On reaching the discharge section of the screen, the screen panels are cleaned of debris by means of a self-adjusting brush mechanism and water spray jets ensuring that clean panels are always presented to the oncoming flow. The screen panels are secured in such a way that replacement of individual panels can be achieved with a minimum of effort and downtime.
The screenings are transferred from the screens via a launder trough system. The SPIROWASH® units wash out the organic material, reduce the volume and weight of the screenings by compaction before delivering them to a skip via a press tube.
A grit vortex unit removes suspended grit from the sewage flow. This consists of a pre-fabricated grit vortex chamber capable of handling up to a maximum 628 l/sec of screened raw sewage flow. The grit is extracted by means of a grit pump and is fed to a SANDSEP® grit separator unit capable of handling up to 20 l/sec of grit slurry. The SANDSEP® unit dewaters and discharges grit into a skip.
Planning and design
Galliford Try Technical Services created a federated 3D model incorporating details from GHD’s civil and structural design, together with information from other subcontractors and suppliers. Design incorporated the use of ground granulated blast furnace slag as an admixture in the concrete design for the water retaining structure. This reduced the reinforcement required for the structure. The design team drew on previous experience of similar projects in North America to help understand the risks associated MBBR solutions.
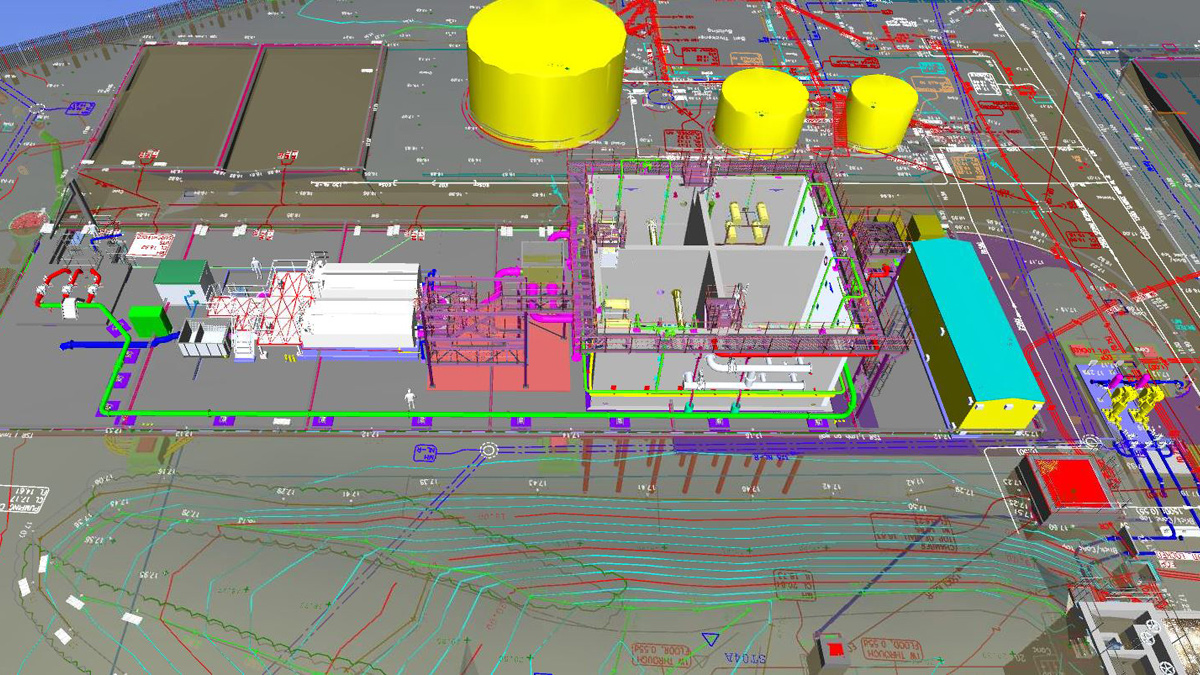
Galliford Try Technical Services assisted with 3D modelling – Courtesy of Galliford Try
The works had to remain operational throughout delivery, requiring careful consideration and planning. For example, design specified live connections using hot-tapping, enabling works to continue without impacting treatment operations. By utilising SPIRAC’s modular design and construction, the 3D models showed and prevented where potential clashes could be, resulting in days or even weeks saved on schedule.
Historical challenges
Galliford Try Technical Services came up against significant challenges in modelling Bolton-upon-Dearne. The inlet works and MBBR are relatively straightforward, but the hardest part was trying to get all the historical data from the 1960s and 1970s (which is all done in 2D) and details of upgrades that had been undertaken but not recorded, which created challenges on site. For example, the team was forced to raise the inlet works to allow reinforcements to be added underneath after historical drawings completely misrepresented the depth of the underlying pipework from the CSO to the storm tanks.
Civil engineering work
A civil engineering sub-contract package was awarded to CPC Civils incorporating:
- Site investigation and enabling works.
- Construction of various reinforced concrete structures including new 15.2m x 15.2m x 6.8m high MBBR tank, raised inlet works foundation slab, MCC kiosk and substation foundations, pump/pipework support plinths and new hardstanding/roads.
- 4.8m deep pumping station – a segmental shaft constructed within a sheet pile cofferdam.
- New ducting network across site.
- New process pipework and drainage.
- New feed and outfall chambers constructed off line and then connected to existing works when required.
- Refurbishment works inside existing low-level pumping station.
- Surfacing to existing access roads upon completion of works.
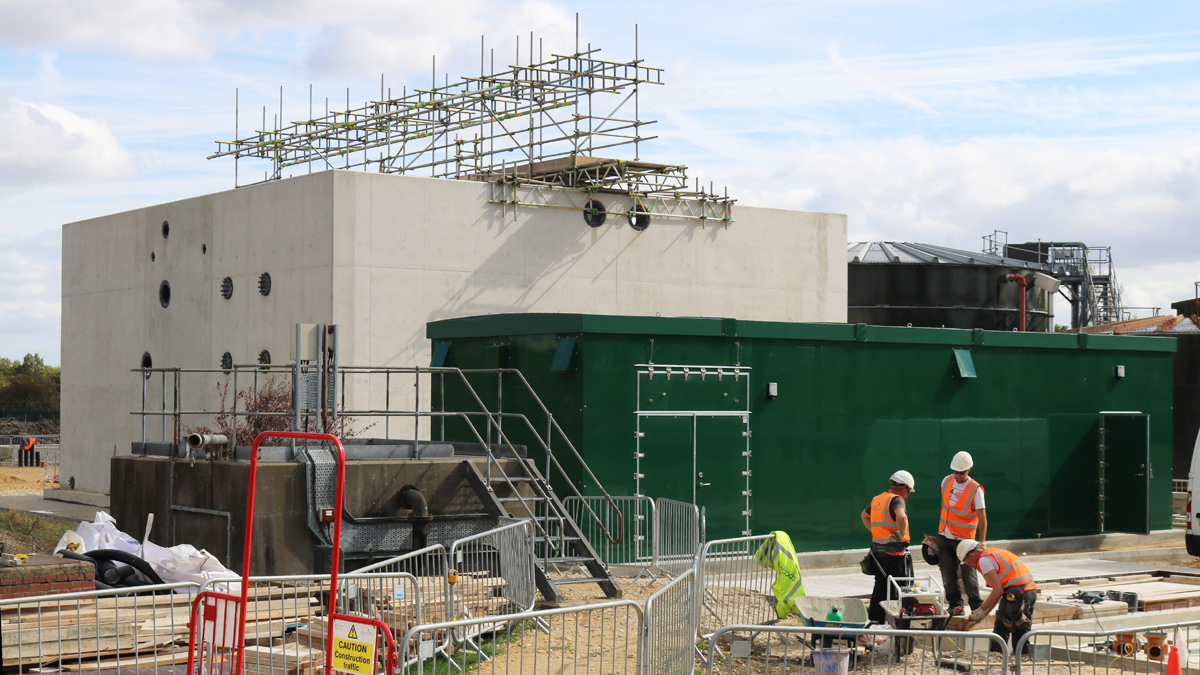
The new inlet was built offsite – Courtesy of Galliford Try
Conclusion
The project was completed on schedule and, once fully operational, the range of benefits will be significant. All the advance work undertaken on the primary and secondary treatment, the flow will pass through to the tertiary treatment stage a lot better, and the MBBR can then do exactly what it is required to do; feed on the ammonia, resulting in a significant improvement the quality of the water in the River Dearne.