Bonnycraig WTW (2024)
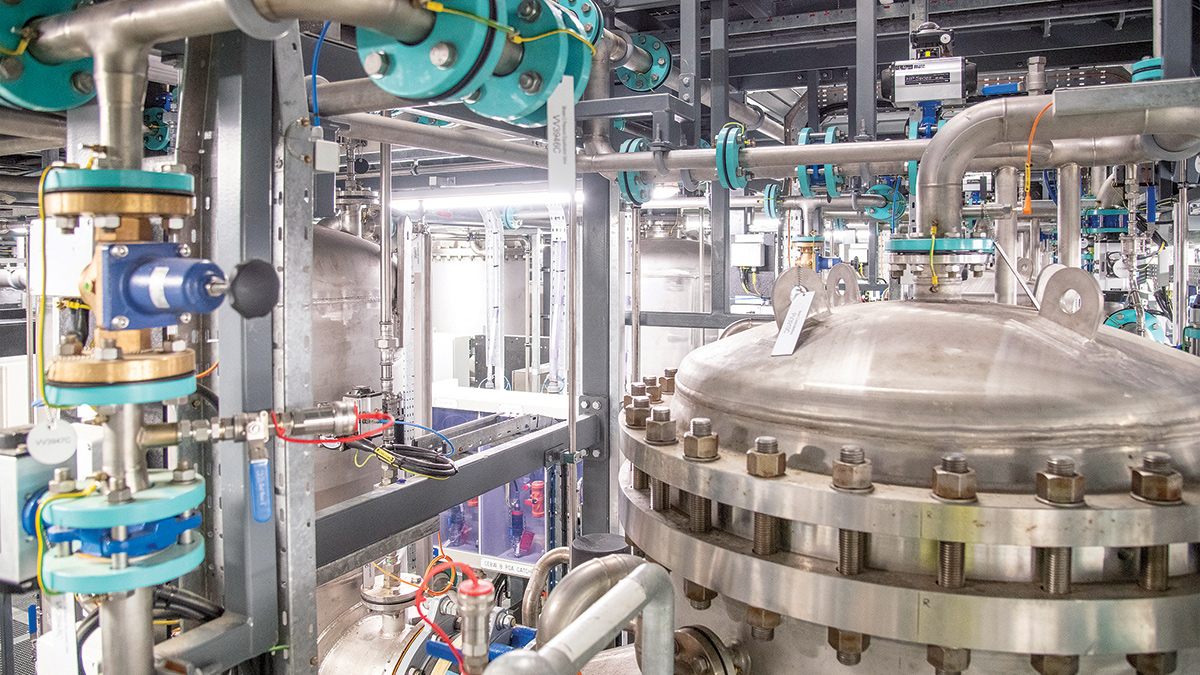
C19 ceramic membrane vessel - Courtesy of Scottish Water
Scottish Water’s Bonnycraig Water Treatment Works (WTW) supplies around 9,600 customers in and around Peebles in the Scottish Borders, treating water fed by gravity from Megget Reservoir. There were operational challenges at the existing works and to secure a long-term supply of clean, safe and fresh tasting water that takes account of summer peak demands and projected growth within the area, a new £31m water treatment works using ceramic membrane technology was utilised to improve the water quality for customers.
Background
The original Bonnycraig WTW was built in the 1960s and sized to 4.1 Ml/d, however this was later reduced to 2.8 Ml/d due to water quality issues. The old works utilised pressure sand filters however, due to Cryptosporidium failures, Scottish Water received a Drinking Water Quality Regulatory (DWQR) enforcement notice for both a short term and long-term solution to this problem. UV was installed within the old works in April 2017 as the short-term solution.
The long-term solution required Water into Supply (WIS) to be completed by December 2022, with the agreed solution being to build a new WTW using ceramic membrane technology. The enforcement notice provided a significant programme challenge to take the project from inception through design and construction to Water into Supply in only 3.5 years.
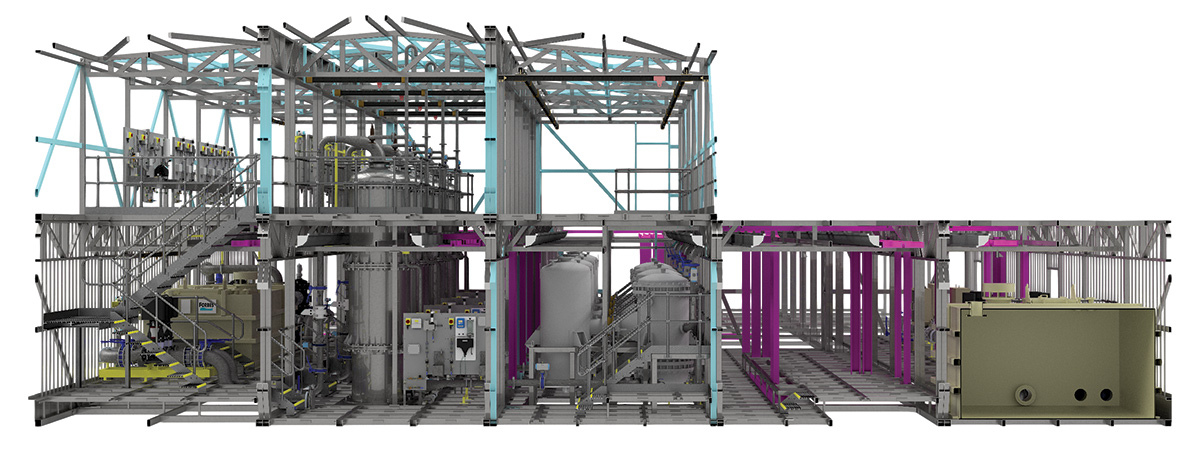
Model of the new WTW – Courtesy of RSE
Bonnycraig WTW (Peebles, Scotland): Supply chain – key participants
- Principal contractor: Amey
- Principal designer: RSE
- Project management: Turner & Townsend
- Process engineering support: M2
- Groundworks: APL Construction Ltd
- Ceramic membranes: PWNT
- MCC: Saftronics Ltd
- Telemetry integration: IDS
- Systems integration & chemical dosing: RSE
- Pumps: Grundfos Pumps
- Tanks: Forbes Technologies Ltd
- Underground tanks: SPEL Products
- PV solar panels: Ri Cruden
- Emergency generator: DTGen
- Kiosks: Quinshield Ltd
- Mixers: Statiflo International Ltd
- Safety showers: Aqua Safety Showers International Ltd
- Site security: Pointer
- Concrete & aggregates: Grange Quarries
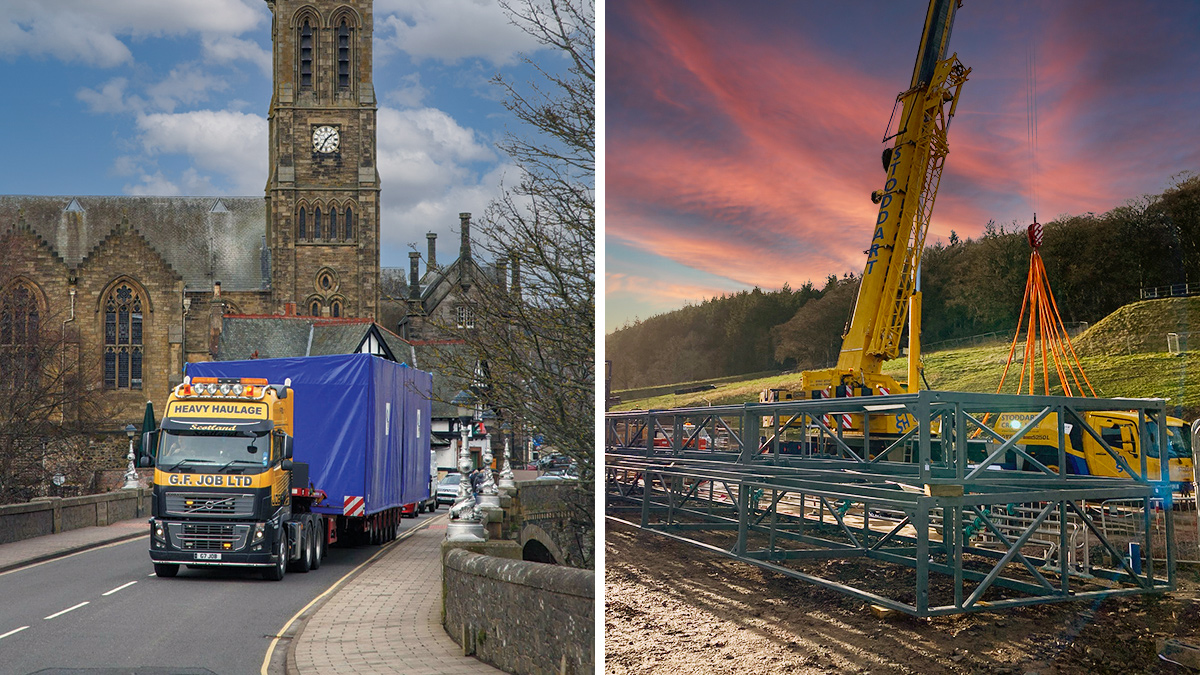
(left) TTU being delivered through Peebles – Courtesy of RSE, and (right) delivery of the TTUs to site – Courtesy of Scottish Water
Project scope
The main components comprised:
- A new ceramic membrane water treatment works on a greenfield site.
- Extensive groundworks/earthworks for new site.
- New external pipework facilities.
- New chambers, tanks and structures to facilitate the new WTW.
- New access and roads.
- Decommissioning of existing WTW.
The project was delivered by RSE for the MEICA and Amey for civil engineering, with PWNT supplying the membranes and filtration housing element for the ceramic membrane process. All working collaboratively with Scottish Water to manage, design and deliver the project in Peebles.
A summary of the construction works being undertaken including design and process considerations as well as some of the challenges encountered for these main components follows.
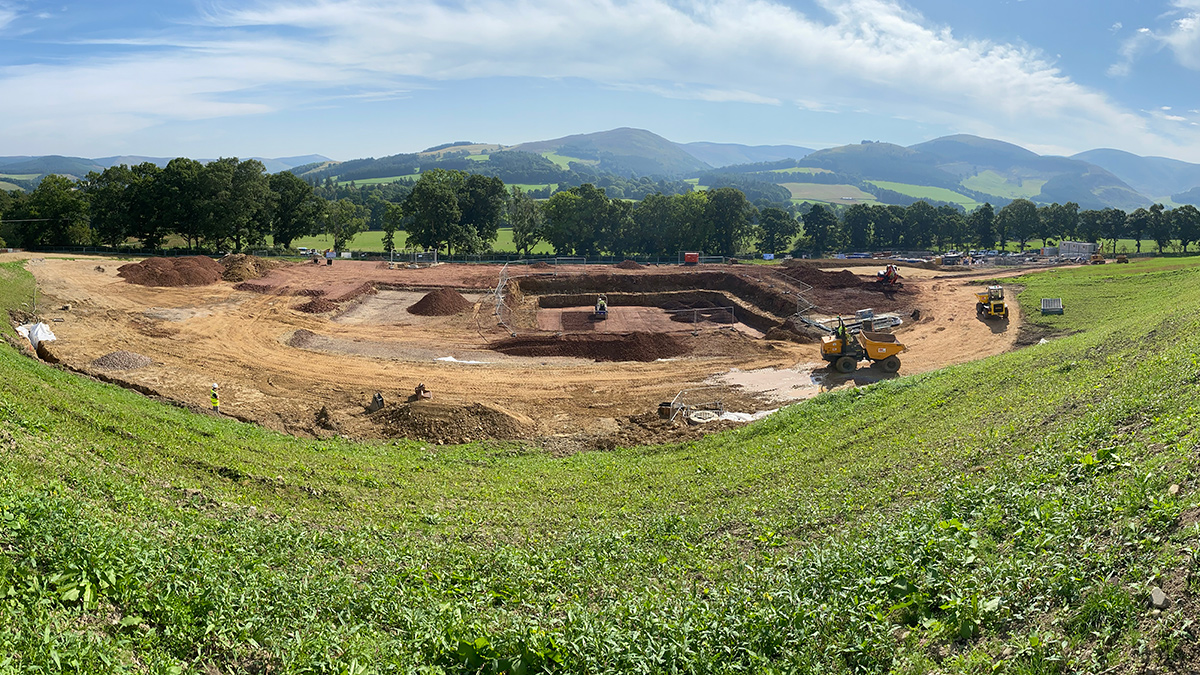
Early civils earthworks at the new site – Courtesy of Scottish Water
Water treatment works
The new works will have capacity to produce up to 4 million litres of drinking water per day and will be supplied by the raw water source of Megget Reservoir, which also provides majority of the raw water to Edinburgh. Within the treatment works site, as well as the new WTW building, inclusion will be made for associated infrastructure, utilising the existing clear water tanks.
Civil engineering works
The new site is located on a greenfield site adjacent to the existing works and therefore utilises some of the existing infrastructure. There were extensive civil works to prepare the site for the WTW, these included:
- Earthwork excavation/landscaping for new WTW.
- New external pipework facilities for the new WTW.
- New chambers, tanks and structures to facilitate the new WTW.
- New building slab.
- Chemical delivery area.
- Emergency outfall headwall at the Crookston Burn.
- Emergency generator, fuel tank plinth, ducting, fuel spill area and security fencing.
- Access roads.
- Site fencing.
- Wastewater holding lagoon.
- Chlorine contact pipe.
- Reinstatement.
All excavated materials were retained and reused on site therefore provided significant carbon and cost savings on the project. Reducing the traffic on the local roads also helped to limit the impact on the community.
The civil works began in February 2021 during the height of COVID-19 restriction across the UK, which brought with it a number of challenges to ensure the safety of all the workers while also trying to maintain the programme to comply with the Drinking Water Quality Regulatory enforcement date. It is testament to all the teams involved that the achieved this.
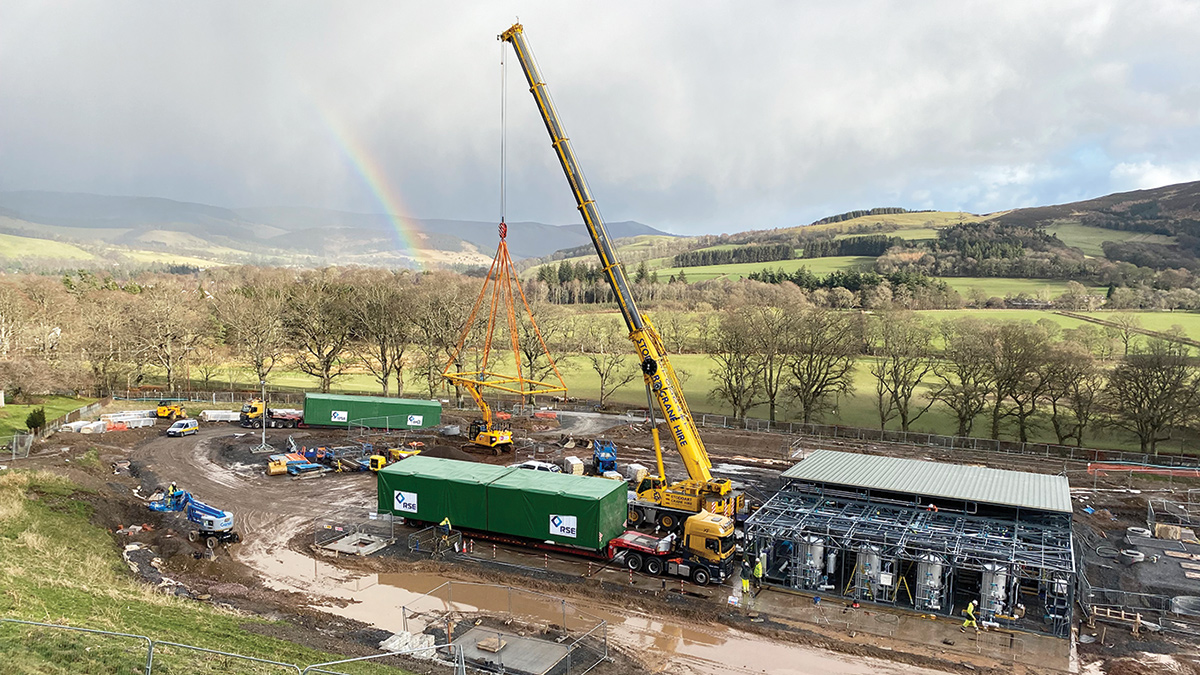
Delivery of the TTUs to site – Courtesy of Scottish Water
MEICA
The new WTW was assembled and commissioned at RSE’s specialised factory in Muir of Ord, before delivery to the site. The new WTW building was assembled as a modular construction with the design allowing the WTW to be dis-assembled, transported 200 miles to site by road and then quickly reassembled once delivered to site. The two-storey building consisted of 17 modular Transportable Treatment Units (TTU) and was RSE’s largest TTU build to date.
Utilising off-site construction allowed for significant programme efficiencies to be made of upwards of 18 months in both construction and commissioning as it allowed the existing civils works to start at the same time as the fabrication and assembly of the new building within RSE’s facility in Muir of Ord.
Furthermore, by undertaking the MEICA works in RSE’s facilities it ensured factory quality throughout. The segregated facilities with separate carbon, blasting, paint, stainless, fabrication and installation areas, coupled with all equipment and stores to hand, created a working environment that could not be matched by an on-site build.
The off-site modular approach also offered health and safety benefits by limiting the number of different trades working concurrently on site. In addition, carrying out the majority of the M&E work in the workshop made it safer for the trades as the work was carried out using standard task risk assessments in a safe predictable working environment.
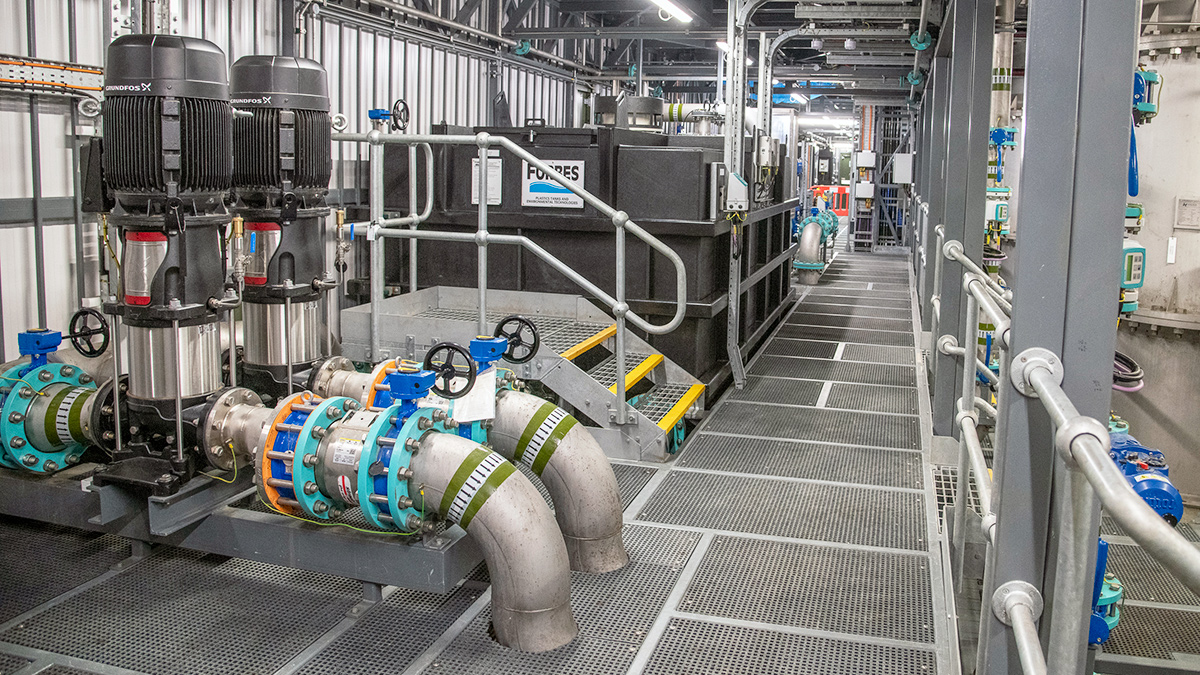
Raw water pumps and tank – Courtesy of Scottish Water
Ceramic membranes
The heart of the main treatment process, involves passing coagulated water through PWNT’s Inline Coagulation and Adsorption vessels (ILCA®) to form a microfloc which helps to bring together the contaminants present within the water to prior to filtration provided by a series of membranes which filter out the flocculated solids and bacteriological contaminants.
Water that has passed through the membranes is then subject to further treatment processes to ensure that it meets customers’ expectations at the tap. Bonnycraig is the first site in Scotland to use this technology and only the second in the UK.
Four ILCA vessels and four C19 Ceramic Membrane Vessels supplied by PWNT are installed at Bonnycraig, and this innovative solution offers a number of benefits over conventional treatment:
- Water quality: Absolute barrier – bacteriological cell reduction and Cryptosporidium removal.
- Lifespan of membranes: > 20 years.
- Water supply: Meet future demands.
- Resilience: Quick recovery from an outage event.
- Customer experience: Ability to build off-line and use of innovative technology.
- Small footprint: Each vessel contains 19 membranes.
The modular solution approach selected by Scottish Water along with its partner RSE has helped to achieve considerable carbon reductions by transferring the mechanical and electrical works from site to the workshop. Carbon conscious choices included opting for off-site manufacturing, saving approximately 18 months of works over traditional build methods, supported by an overall reduced project programme.
Furthermore, the roof of the water treatment works accommodates a solar array of 288 (No.) 325W solar panels that will contribute to the power supply, assisting in driving down power consumption from the grid.
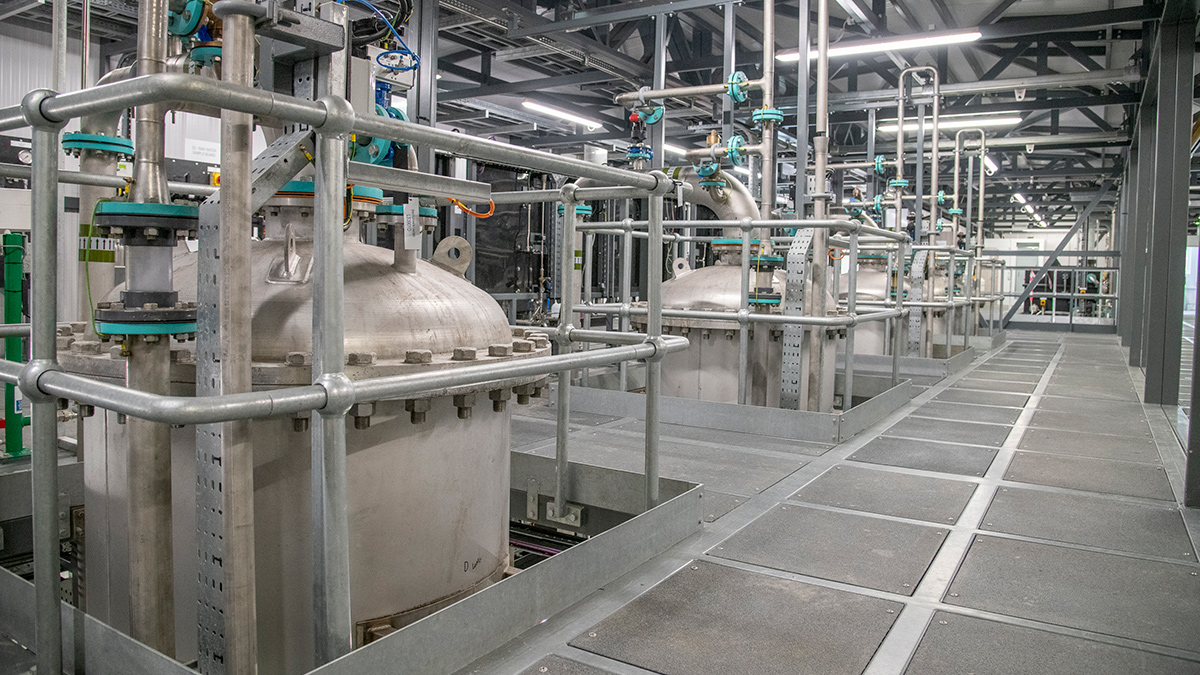
Top of ILCA® vessels – Courtesy of Scottish Water
Benefits of the modular solution
In summary, the use of the RSE modular solution provided a number of key benefits to the project:
- Reduced programme: TTU construction completed in RSE factory environment, reducing the amount of site hours while also enabling fabrication and assembly to be conducted concurrently with civil construction. This was critical to achieving the DWQR enforcement date.
- Improved quality: Stringent quality control in RSE fabrication facilities.
- Reduced HSE risk: Due to the factory construction of the TTUs, a significant portion of the construction is completed in a controlled factory environment, rather than on site.
The water treatment process
The process follows the following key process stages:
- 10mm coarse Simplex strainer
- 1.0mm duty/standby raw water screening with auto backwash.
- Raw water break tank.
- Raw water transfer pumps.
- Raw water pH correction using sodium hydroxide and sulphuric acid to achieve the required coagulation pH set point.
- Coagulant dosing using PACL.
- Coagulation/flocculation using four PWNT in-line coagulation and adsorber (ILCA®) vessels.
- Filtration using the PWNT CeraMac® process (four C19 membrane streams).
- Facilities for backwashing and cleaning (CEBW and CIP) of the CeraMac® membranes.
- Permeate/backwash water tank.
- Interstage permeate transfer pumps.
- Run to waste facilities for out of spec water (both individual and common membrane permeate streams).
- Disinfection using sodium hypochlorite.
- Orthophosphoric acid dosing for plumbosolvency control.
- Chlorine contact pipe (1200mm diameter x 75m long).
- Final pH correction using sodium hydroxide dosing to control final water pH.
- Storage in two clear water tanks prior to gravity distribution to supply (two existing tanks being retained).
- Chemical waste neutralisation tanks and systems (1 x acid and 1 x alkali) including caustic and sodium metabisulphite dosing skids.
- Discharge of backwash waste, neutralised CEBW and CIP wastes, and instrument wastes.
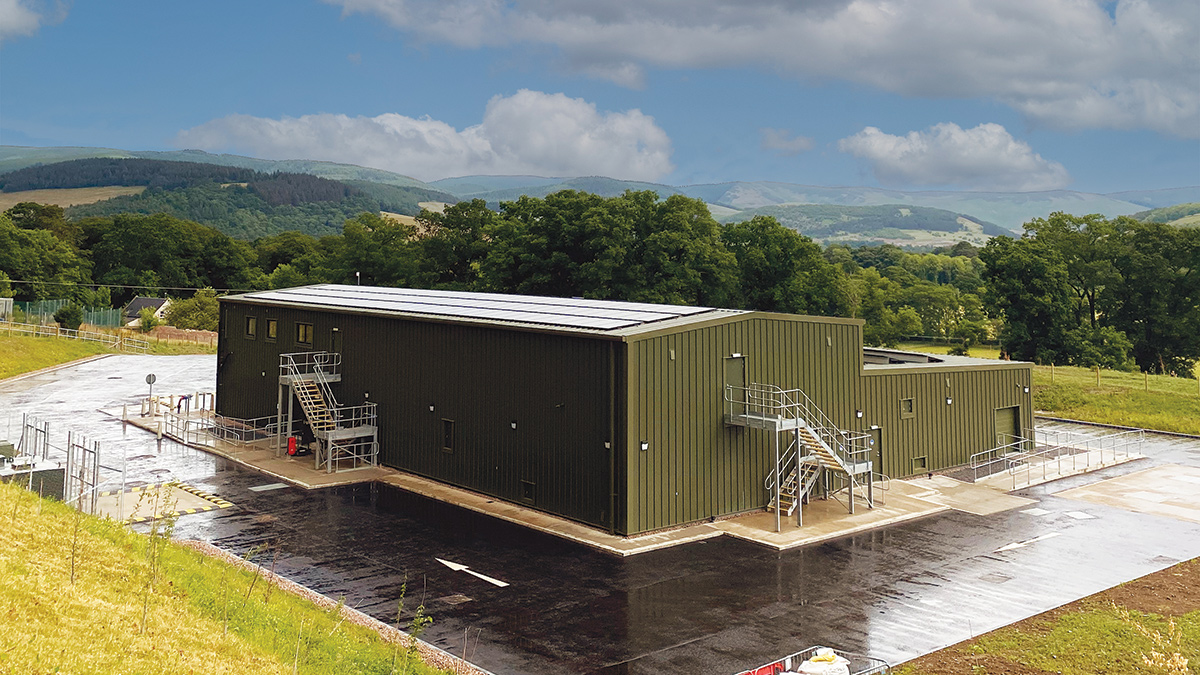
The completed Bonnycraig WTW – Courtesy of Scottish Water
Conclusions
This case study has highlighted the benefits of off-site manufacture particularly achieving a very tight programme and meeting the DWQR enforcement date.
The complexity of project interfaces was also greatly enhanced due to collaborative working between Scottish Water, RSE, Amey and PWNT. The consortium has successfully managed to navigate a path through all planning, land purchase, construction and commissioning activities to achieve a project that not only benefits the Scottish Water customer with safe clean drinking water but was delivered on time and within budget. Given this was all delivered during COVID restrictions further highlights the achievements of the project.
The new WTW has been live for 18 months and while there have been some snagging/defects that Scottish Water are continuing to work through, the works has always maintained the supply of safe clean drinking water with water quality being noted as being exceptional. While a number of key lessons learned have been documented, Bonnycraig is being used as a template for future WTWs within Scottish Water.
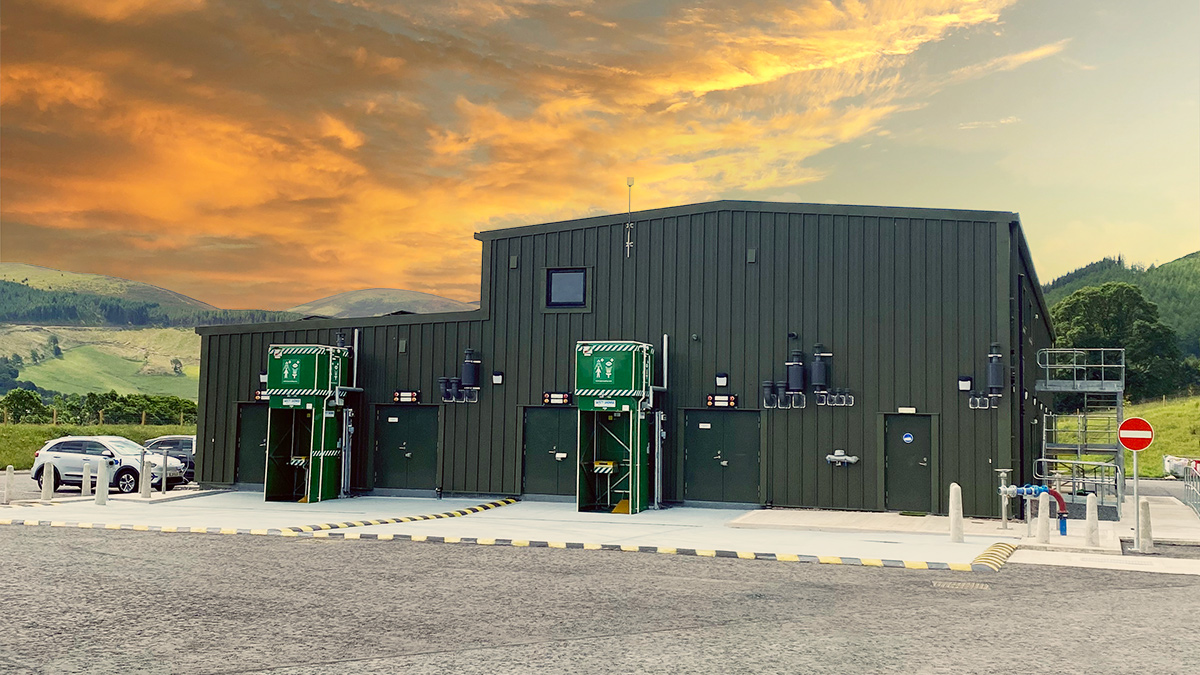
The completed Bonnycraig WTW showing the chemical delivery area - Courtesy of Scottish Water