Burnley WwTW Catchment Strategy (2023)
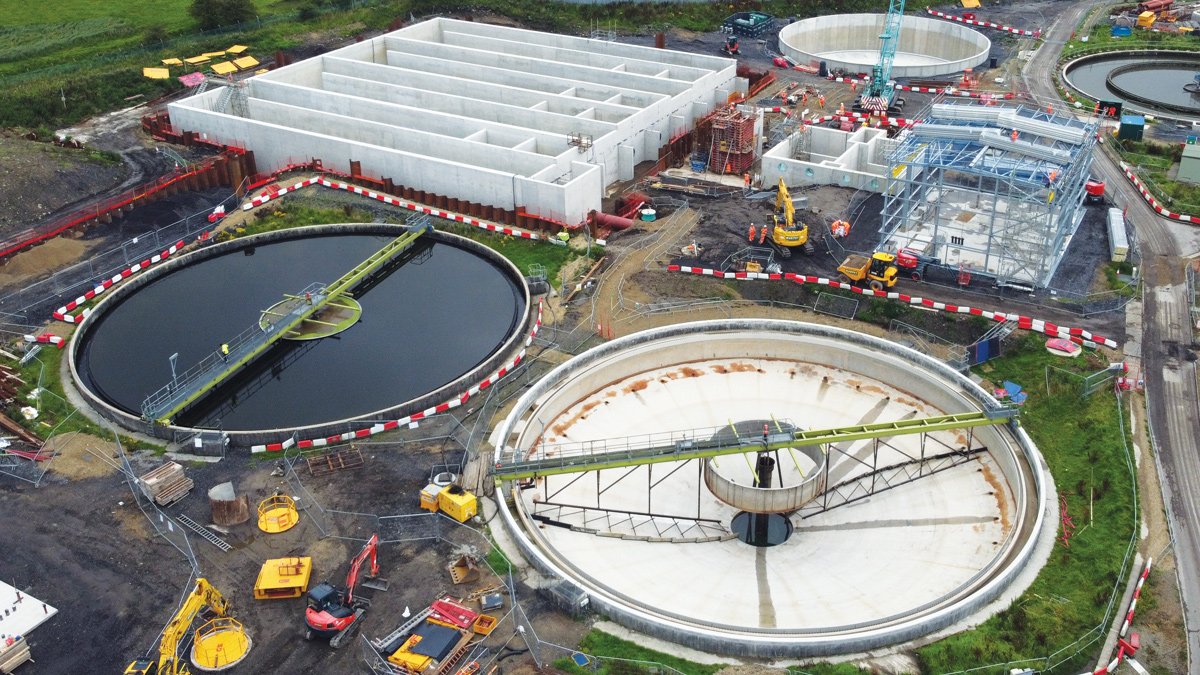
Burnley WwTW – Aerial view of new process areas under construction and refurbished FST - Courtesy of United Utilities
The Burnley integrated catchment scheme is one of United Utilities’ (UU) largest AMP7 projects with a value of £77m. The project is being delivered by UU’s construction delivery partner (CDP) framework by Advance-plus, a joint venture between MWH Treatment, J Murphy & Sons (JMS) and Stantec UK. The project commenced in 2020 and through two previous articles, UU and Advance-plus have shared the project background, the story of developing the solution and design, and commencing the build. In this year’s article, the project delivery team is pleased to provide an update on the construction progress and a look at the journey ahead as the project remains on course to achieve the December 2024 regulatory completion date.
A summary of the project requirements and the integrated catchment solution scope
The integrated solution scheme requirement is River Water Quality Improvement for the Water Framework Directive (WFD) driver identified in the Water Industry National Environmental Programme 3 (WINEP3) to achieve a ‘good status’ in the defined reaches of Pendle Water and the River Calder.
To meet this, the treatment capability at Burnley Wastewater Treatment Works (WwTW) is to be enhanced to achieve compliance with the new enhanced, treated effluent permit standards, and management of storm discharges in the defined reaches, to achieve a compliance with the WFD 99%ile wet weather intermittent standards. The project also includes the U_MON3 spill monitoring and U_MON4 flow monitoring drivers.
Through complex river water quality and network modelling, the lowest whole life cost integrated catchment solution was determined and developed. Four sites make up the integrated catchment solution which are all interdependent in delivering a total of ten regulatory outputs.
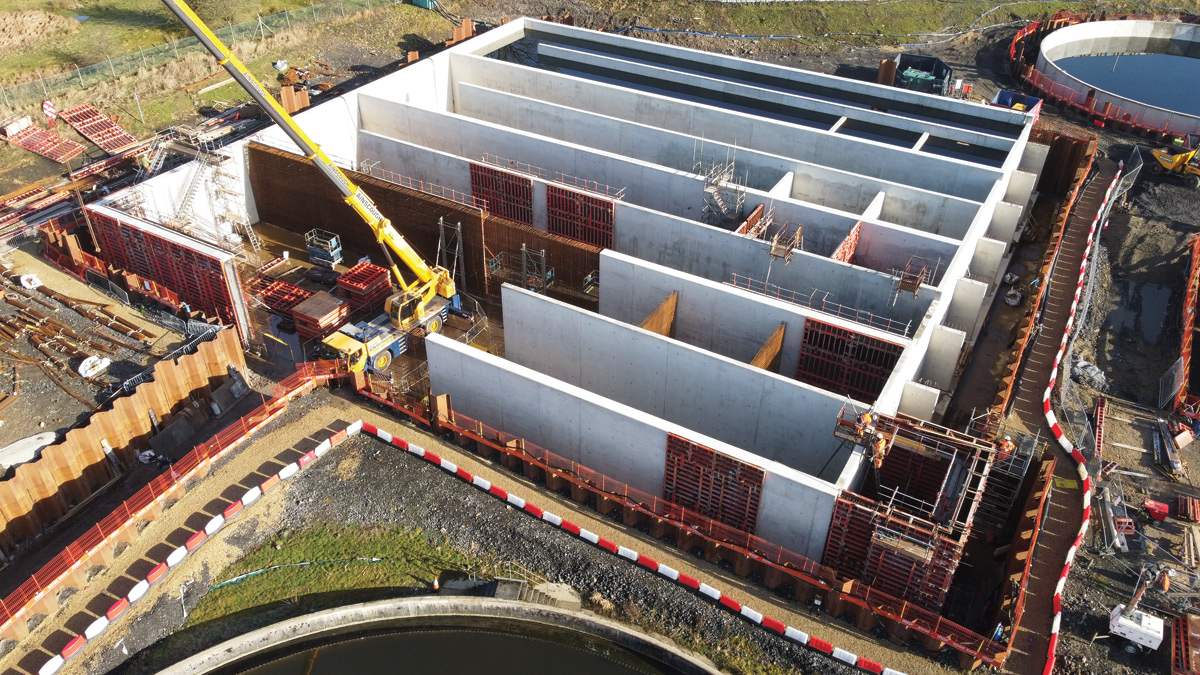
ASP under construction – Courtesy of United Utilities
Burnley WwTW
Burnley WwTW serves a domestic population equivalent (PE) of 107,115 plus trade load. The site is undergoing a significant upgrade with the scope comprising design, construction, and commissioning of:
- New 12,000m3 detention tank with associated pumping station.
- New additional primary settlement tank (PST).
- New 1300 l/s inter-stage pumping station.
- New activated sludge plant (ASP) with BioMag® process. The BioMag® System enhances conventional biological wastewater treatment by using magnetite (Fe3O4) to ballast floc allowing an increase in mixed liquor suspended solids (MLSS) in the ASP and enhanced performance in the final settlement tanks (FSTs).
- Refurbishment of existing final settlement tanks.
- New surplus activated sludge (SAS) thickening process.
- New ferric and caustic dosing plants.
- Associated motor control centres (MCCs), SCADA upgrade, and power upgrade.
Pipework
The last year has seen great strides being made across the site and various process areas, with major civils structures constructed and taking shape. The very constrained nature of the site, existing processes and services, and the need to lay many kilometres of small and large diameter underground pipework has proven to be a major constructability challenge. Most of the pipework installation has been self-delivered by J Murphy & Sons with Saint Gobain PAM UK being the main supplier of the pipework and fittings.
Detention tank
The new detention tank, has been constructed by A-Consult Ltd using 64 precast concrete panels, standing 10.4m high. The panels were precast in their factory before being transported to site for erection and subsequent post tensioning. Utilising this construction technique, with design for manufacture and assembly (DfMA) brings benefits in terms of quality, time and safety. The tank has successfully passed its water test and is currently being drained. The feed pumping station has been constructed and the mechanical installation of pumps, mixers and pipework is now in progress.
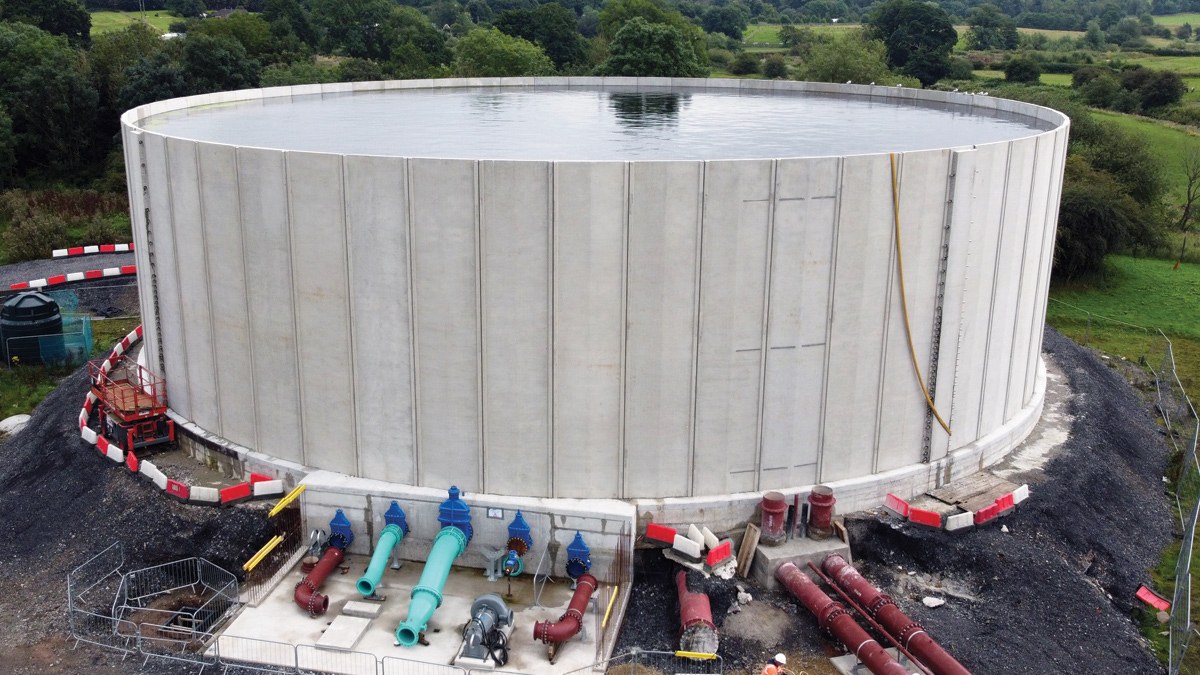
Detention tank on water test – Courtesy of United Utilities
Primary settlement tank
The new primary settlement tank (PST) civils construction is also complete, again undertaken by A-Consult Ltd using the precast concrete panel method of construction. It has also successfully passed its water test. Mechanical installation by EPS Water is now in progress on the ‘H’ frame steel structure which will support the scraper bridge. The design of the PST incorporates a fixed bridge arrangement with rotating scrapers beneath. This arrangement is necessary as the PST will eventually be covered with a GRP roof for odour mitigation. The odour control fans, ductwork and vent stack are scheduled to be installed in December.
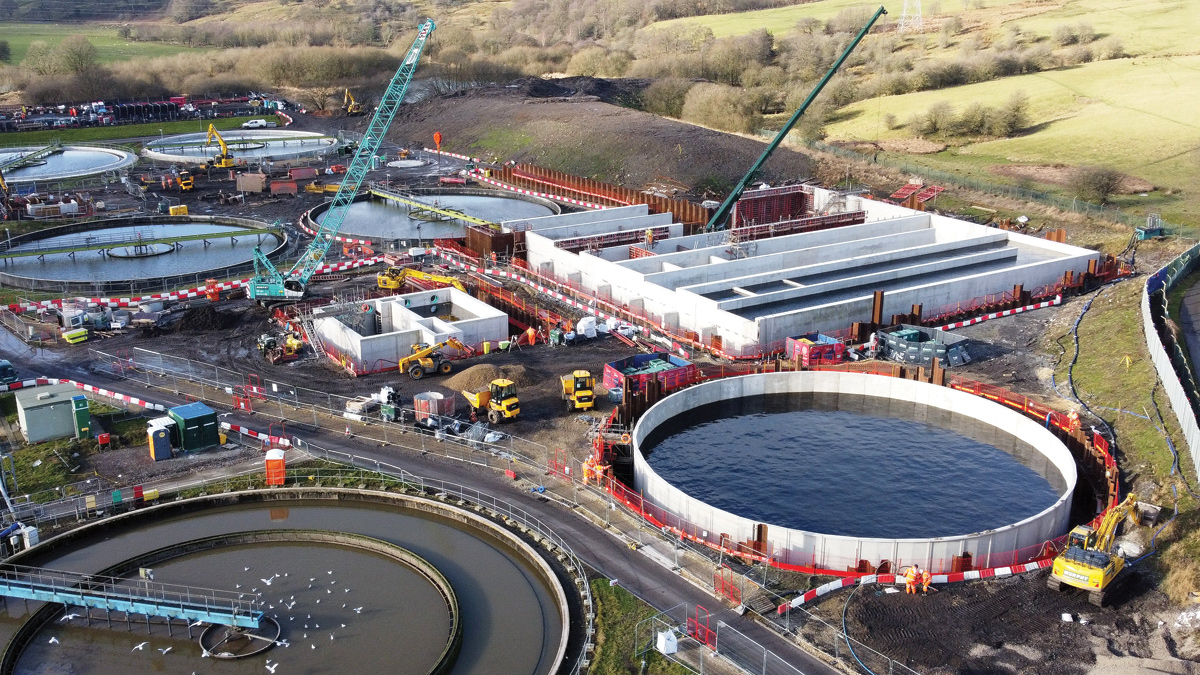
PST4 and ASP lane 1 on water test – Courtesy of United Utilities
Interstage pumping station
Due to the topography and hydraulic levels across the site, a new interstage pumping station (IPS) is required to pump the effluent leaving the four PSTs up to the new activated sludge plant (ASP) distribution chamber.
Civils FRC works are being undertaken by STAM Construction Ltd and contain 94 tonnes of rebar and 900m3 of in situ poured concrete. The pumping station structure is complete and has undergone successful water testing.
The internal benching is complete and the next activities planned for the coming period will be the mechanical installation of the pumps and pipework. As the pumping station is vital to keep all flows passing through the treatment process, a standby generator will also be installed. The IPS is a two compartment design to facilitate future maintenance activities preventing the need to take it completely out of service. The new pumps have been supplied by Xylem Water Solutions who have supported the designers in providing efficient selections for the large submersible pumps and optimising the layouts of the pump chambers.
Activated sludge plant
The ASP distribution chamber is currently being constructed with all four concrete walls having now been poured. These are curing and the structure will undergo a water test in September 2023.
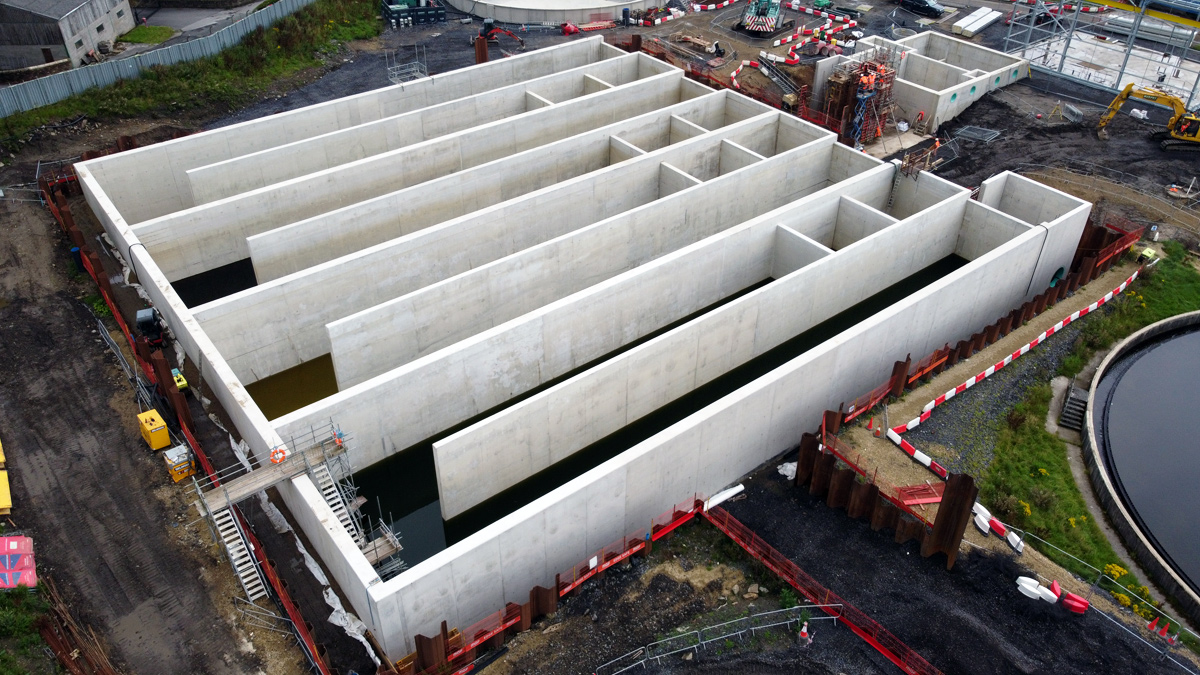
ASP constructed and water tested – Courtesy of United Utilities
In constructing the new ASP, STAM Construction Ltd have installed 650 tonnes of rebar and poured 4500m3 of concrete. The overall size of the ASP is 48m x 48m x 6.6m deep, has a capacity of 14,500m3 and comprises four lanes. Civils construction of the ASP is complete and fully water-tested with the mechanical installation of the internal pipework, aeration grids, diffusers and access platforms and walkways taking place over the next few months.
Suprafilt Ltd will be supplying and installing the internal pipework, aeration grids and diffusers. Mechanical installation of the pump stations and access steelwork etc will be undertaken by Fluid Sealing & Engineering (FSE).
BioMag®
The Evoqua Water Technologies detail design for the new BioMag® process has been finalised and the building layout confirmed. The main equipment including four Magdrums and two shear mills, process tanks, silo and pumps, which have been manufactured and are ready for delivery to site when required. The BioMag® building is currently under construction by Gallaway Construction.
The steel frame has been erected and the gantry crane and roof cladding have been installed. External wall cladding is in progress, after which attention will turn to the internal fit-out and installation of the BioMag® equipment.
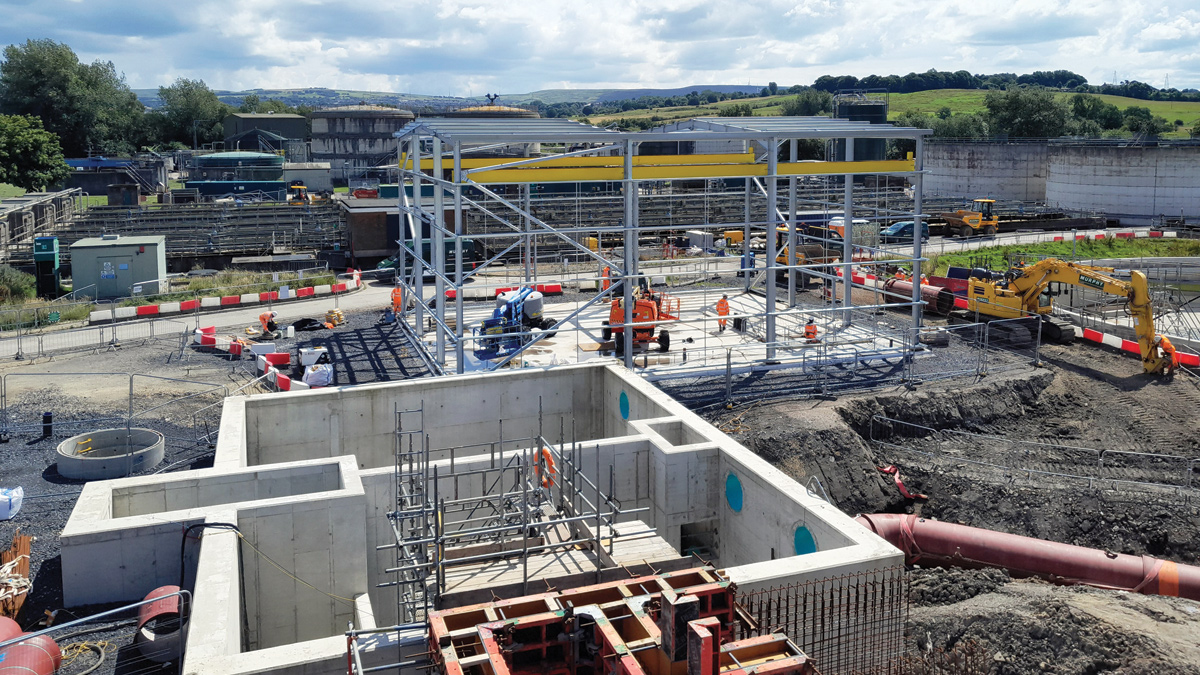
BioMag® building being erected – Courtesy of United Utilities
Final settlement tanks (FST)
There are four existing final settlement tanks which required refurbishing to ensure adequate performance and asset life are achieved. The scope includes civils refurbishment of the tank walls which involves cutting approximately 300mm from the top of the walls before installing new reinforcement and re-casting concrete to the required coping levels.
Cutting works is being undertaken by Holemasters and FRC works self-delivered by JMS. The mechanical and electrical work is being delivered by Jacopa and comprises refurbishment of the bridge, scraper assemblies, and other ancillary equipment. Three of the four FSTs have now been refurbished with the final one due to be undertaken towards the end of the year.
Surplus activated sludge (SAS) thickening
Civils works has been ongoing in the SAS thickening process area for the last couple of months with the storage tank, drum thickener, poly plant and kiosk bases all constructed. Underground services, ducts and pipework have also been installed and tested. The filtrate return pumping station construction is in progress with the mechanical installation due to follow on.
Chemical dosing
The new ferric and caustic dosing plants comprise storage tanks, dosing rigs and dosing pipelines, all of which have been designed and well progressed in manufacture. These are being supplied by NPS Engineering Group. A new chemical delivery facility will also be provided with civils construction in this area commencing towards the end of the year and installation of the new dosing plants taking place early 2024.
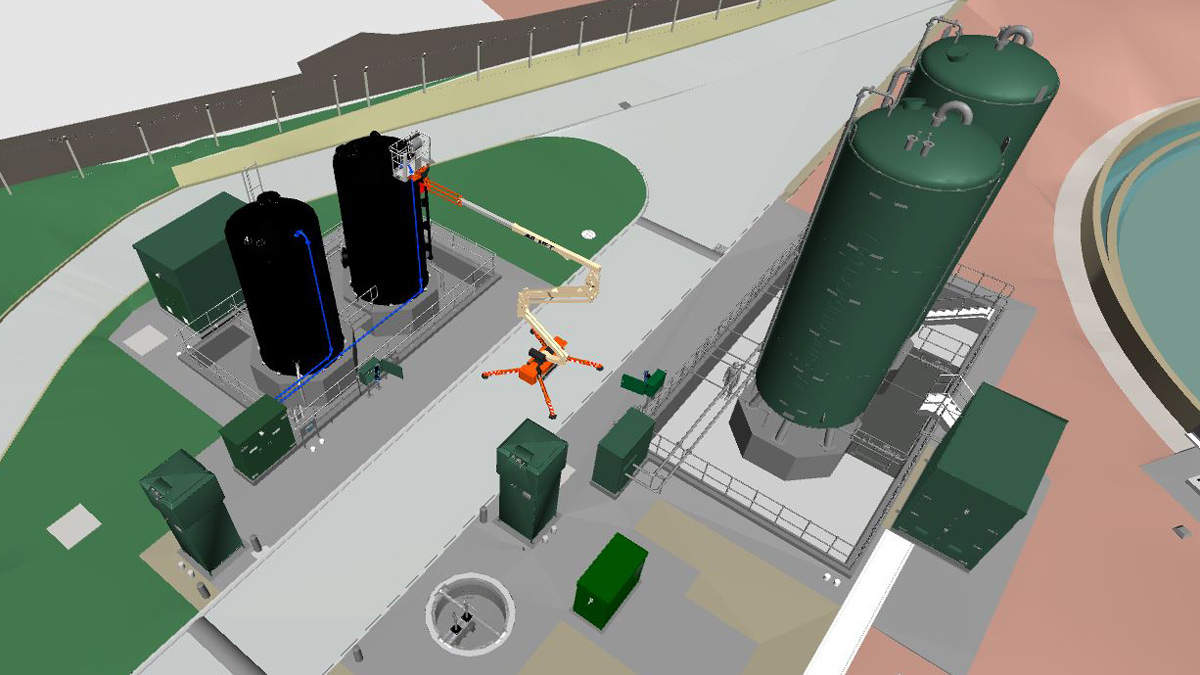
3D model of chemical dosing area – Courtesy of United Utilities
HV works
A new, uprated HV cable has been installed from the off-site substation to the wastewater treatment works, a length of approximately 900m, passing through a number of fields and third-party land.
Motor control centres (MCCs)
To control all the new assets a number of new MCCs housed within kiosks are required around the site, along with a new site-wide SCADA system. The MCCs are all in various stages of manufacture and factory testing. The electrical installation and system integration works, including dry testing, will be undertaken in phases over a period of months as the programme for each of the new process areas dictates.
The MCCs are being built by Technical Control Systems Ltd, electrical installation will be by PICOW Engineering Group and system integration by Tata Consultancy Services.
Looking forward to commissioning
Commissioning of the new treatment process, and transitioning from the old process in a controlled staged approach, will be complex.
The existing treatment stream and process compliance cannot be put at risk or compromised and months of hard work and planning for commissioning has already taken place. Wet commissioning is due to start in April 2024, gradually increasing flows into the new treatment process over several months while the new biological process builds up and matures to a point where the improved treatment standards are being met. The forecast project in use date is October 2024.

Aphex construction planning software map view – Courtesy of United Utilities
Burnley WwTW Catchment Strategy: Supply chain – key participants
- Construction Delivery Partner: Advance-plus JV
- MWH Treatment (Advance-plus jv)
- J Murphy & Sons (Advance-plus jv)
- Stantec UK (Advance-plus jv)
- CFD modelling: CER Technologies Ltd
- GPR & topo surveys: Atlantic Geomatics (UK) Ltd
- Flood risk assessment: Ambiental Environmental Assessment Ltd
- Physical modelling: Hydrotec Consultants Ltd
- Dewatering design: OGI Groundwater Specialists Ltd
- Concrete construction: STAM Construction Ltd
- Concrete supply: CEMEX UK
- Pump station shaft: EJ Kelly
- Sheet piling: Sheet Piling (UK) Ltd
- PCC driven piling: Van Elle
- Concrete cutting: Holemasters
- Temporary works/shoring: MGF Ltd
- Precast post tensioned tanks: A-Consult Ltd
- Earthworks: D Morgan plc
- Blower building: Saredon Steel Buildings Ltd
- Access metalwork: Tushingham Steel Fabricators
- BioMag process: Evoqua Water Technologies (Xylem Water Solutions)
- BioMag building: Gallaway Construction Ltd
- BioMag mechanical installation: Alpha Plus Ltd
- Ventilation: Air Technology Systems Ltd
- Pumping station mechanical installation: Fluid Sealing & Engineering (FSE)
- HV cable installation: Smith Brothers Ltd
- Transformers: Winder Power
- Electrical installation: PICOW Engineering Group
- MCCs: Technical Control Systems Ltd
- Systems integration: Tata Consultancy Services
- Standby generators: DTGen
- SAS glass coated steel tank: Stortec Engineering Ltd
- PST fixed scraper bridge: EPS Water
- Epoxy coated carbon steel pipework & wall starters: Freeflow Pipesystems Ltd
- Dosing systems: NPS Engineering Group
- SAS drum thickeners: Huber Technology
- Odour control system: Air-Water Treatments Ltd
- PST odour covers: Corporate Engineering
- Ductile iron pipework: Saint Gobain PAM UK
- Ductile iron pipework: Electrosteel Castings (UK) Ltd
- FST scraper bridge refurbishment: Jacopa Ltd
- Blowers: Sulzer Water & Wastewater
- Aeration system: Suprafilt Ltd
- SAS tank air mixing system: Utile Engineering
- Submersible pumps: Xylem Water Solutions
- Valves: AVK UK Ltd
- Kiosks: Industrial GRP
Lindred Road CSO (PEN0056)
Work at this existing combined sewer overflow (CSO) site comprises the construction of an online 1,950m3 detention tank which will hold stormwater during times of heavy rainfall, reducing discharges to the watercourse. New pumps within the tank will return the effluent to the sewer for onward treatment at Burnley WwTW.
The 15m diameter x 20m deep detention tank, is of segmental shaft construction and is located within the very busy and congested Lomeshaye Industrial Estate in Nelson, and was constructed by Joseph Gallagher Ltd. This was a highly challenging build within a car park of one of the local businesses and an enormous amount of planning and stakeholder management has been required.
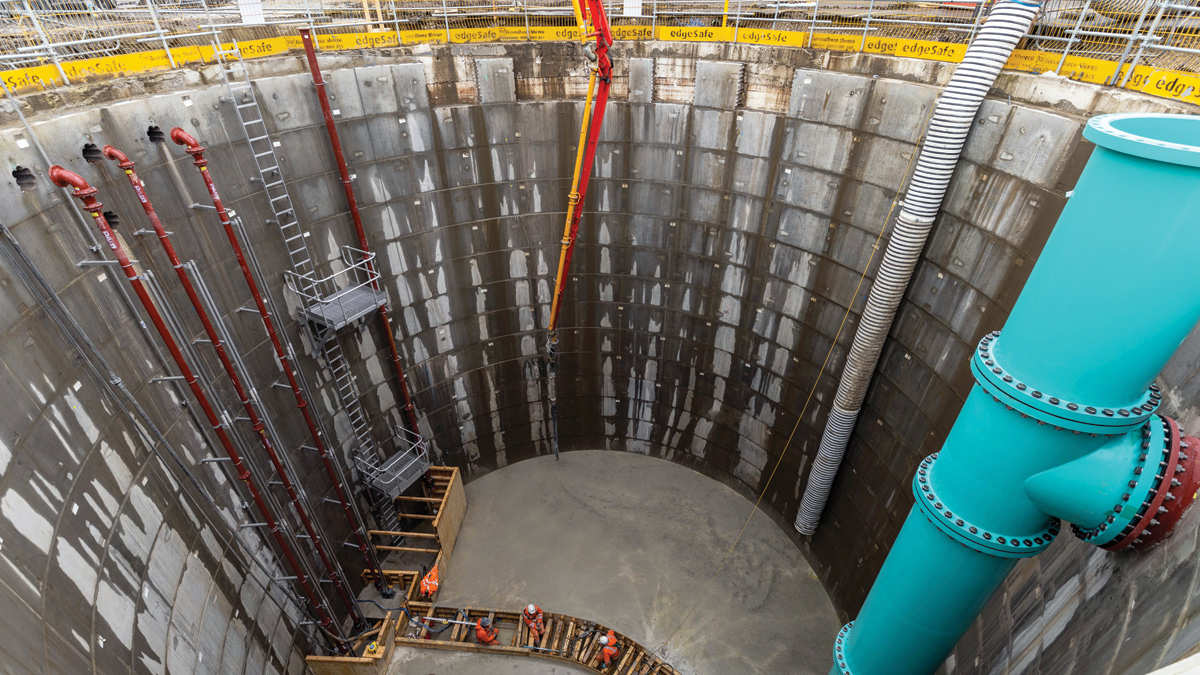
Lindred Road detention tank during construction – Courtesy of United Utilities
Work started on site in July 2022, with the first phase involving the diversion of numerous services, including gas, fibre, BT, water and power, to clear the area for the tank construction. Enabling works to provide safe access routes, segregation, and procurement of alternative car parking for the impacted business employees was also required before the main construction work could commence.
Ground was broken in August 2022 with the tank construction continuing through to December 2022 when full depth was reached. Construction of the pump sumps, inlet channel and complex benching arrangement followed.
The spring months of 2023 saw the mechanical works inside the tank take place with the installation of the pumps, pipework and access ladders and platforms. Once the internal works were complete, the roof beams were installed and the roof slabs placed on in May 2023.
The inlet and outlet pipework for the tank has now been installed, including associated manholes and chambers. To facilitate the connection of the 1200mm inlet pipe into the existing CSO chamber, a complex timber heading arrangement needed to be constructed in order to access beneath, and protect a myriad of services crossing the vicinity. All buried pipework, chambers and ducts etc have been completed and reinstatement of the area is in progress.
The civils and pipework has been undertaken by SGC Civil Engineering Ltd and the mechanical works by Fluid Sealing & Engineering (FSE).
A new motor control centre and power supply is being installed for this facility. The new control kiosk was delivered and installed in July 2023 and the electrical installation is currently ongoing with the new power supply due to be energised in October.
Testing and commissioning is scheduled to start in November, with the site achieving project in use in February 2024.
Lindred Road Detention Tank: Supply chain – key participants
- Civil design detention tank: COWI UK Ltd
- Detention tank shaft: Joseph Gallagher Ltd
- Civils & pipework: SGC Civil engineering Ltd
- Mechanical works: Fluid Sealing & Engineering (FSE)
- Precast roof sections: Macrete (Ireland) Ltd
- Precast shaft segments: FP McCann
- MCCs: Technical Control Systems Ltd
- Kiosks: Industrial GRP
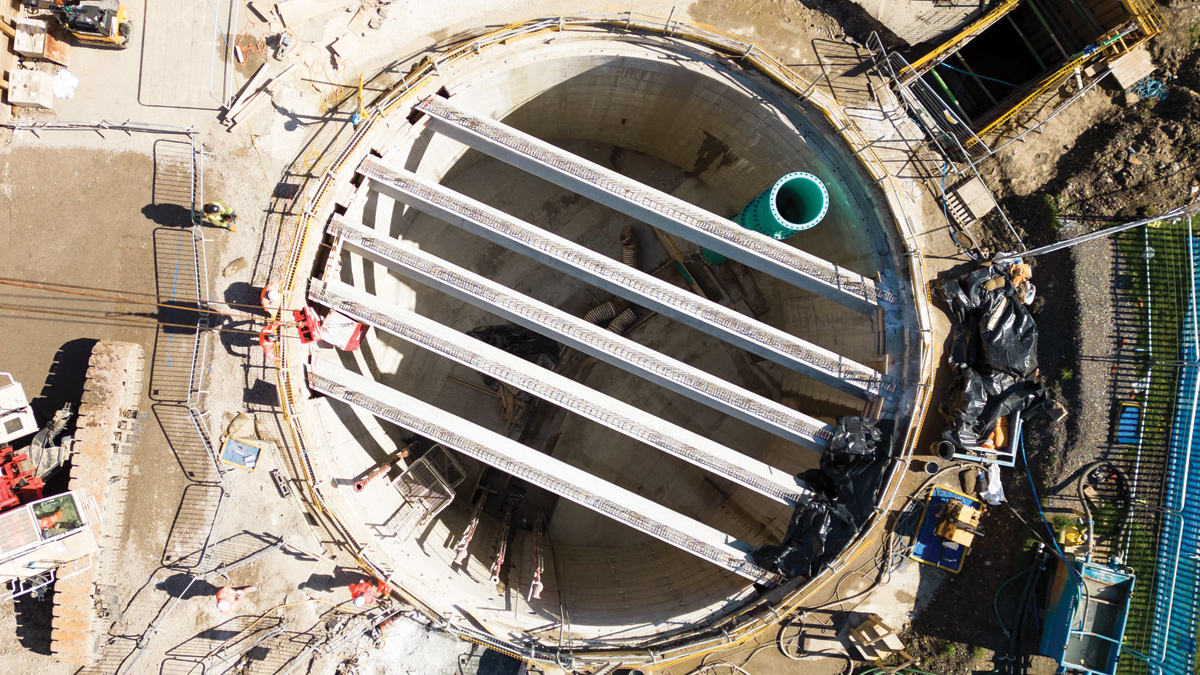
Lindred Road: Aerial view of detention tank – Courtesy of United Utilities
Altham Outfall Fennyfold CSO (BUR0026)
This existing CSO site is located in Padiham, near Burnley, and is part of the sewer network that transfers flows to Hyndburn WwTW for treatment. The solution here is to construct a new chamber over the downstream sewer, and install a new real time controlled actuated penstock valve that will regulate and optimise flows passed forward to Hyndburn, whilst reducing spills from the existing CSO. A new control kiosk and power supply are also required.
This new facility is situated within an environmental and stakeholder sensitive area, adjacent to a number of allotments and the River Calder. The parcel of land required for the new kiosk and chamber has been procured and a new access track for future operation and maintenance, as well as the build, will be required and constructed.
The detailed design is complete and some enabling works to set up site have been undertaken.
For the main construction activity, a complex temporary works arrangement will be required, with large scale over-pumping, to carry out the works on the live sewer. Plans are currently being made to install temporary isolation rails and plates during a suitable dry weather period in preparation. This site is scheduled to be complete in spring 2024.
Hyndburn WwTW
To cater for the change in flows being presented at Hyndburn WwTW through the inlet sewer from the BUR26 catchment, the solution modelling has identified that by reducing the time it takes for the storm tanks to be returned into the treatment stream would ensure that the river water quality objectives could be achieved.
The existing storm return pumping station is made up of fixed speed pumps operating at a duty of 100 l/s. A new variable speed storm return pumping station will be constructed which will be capable of returning flows across the range of 30 l/s to 330 l/s. This means that the contents of the storm tanks can be returned much quicker after a storm subsides.
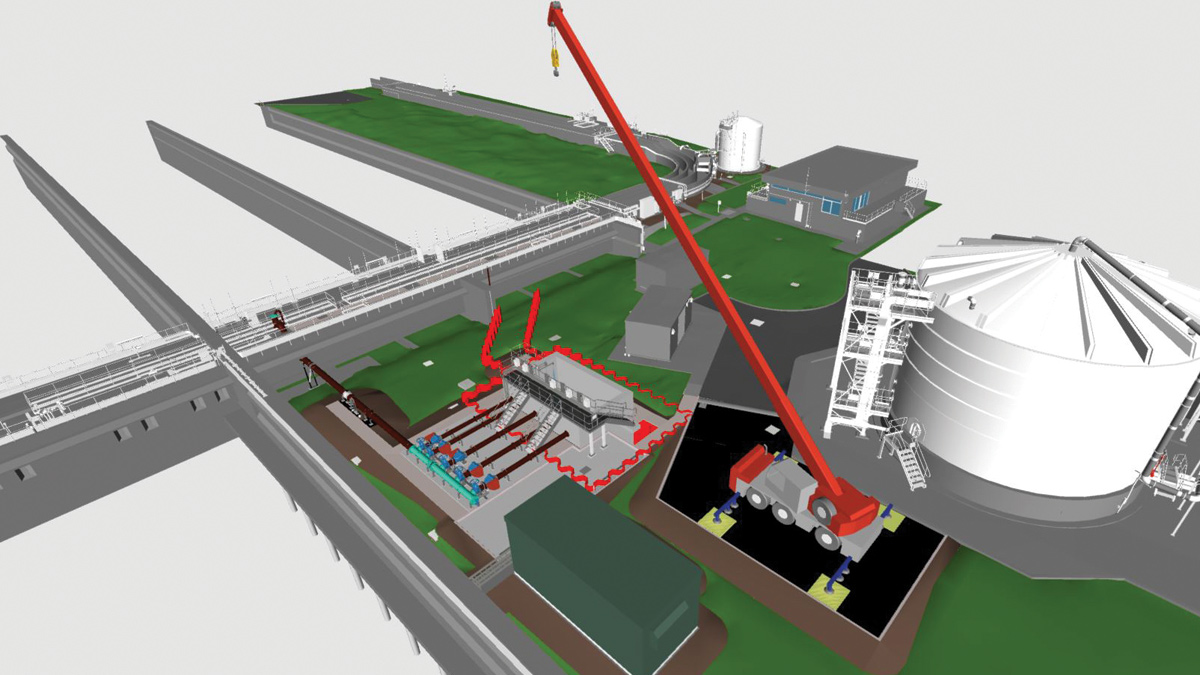
Hyndburn WwTW – 3D model of storm return pumping station – Courtesy of United Utilities
A new below-ground wet well type pumping station will be constructed with three high-flow pumps and two low-flow pumps which provides a more flexible and efficient system with greater turn down capability. A new single rising main will return the storm flows back to the head of the treatment works. A new kiosk and motor control centre will also be installed.
Planning permissions are in place and all pre-start surveys and investigations have been completed. Detailed design is nearing completion and the site has just been established. Construction is due to start in earnest in September on the new pumping station excavation. The winter months will see the civils works progress, with mechanical and electrical works due to start in spring. The project in use is forecast for July 2024.
The digital toolbox
4D digital rehearsals which link the 3D model to the programme have been used extensively by the site team to validate the constructability and sequencing of the works. Visualisation allows all parties to truly understand the construction sequence, interfaces and interdependencies which is relevant on such a congested work area with multiple subcontractors operating in close proximity. They have helped to identify high risk activities and plan mitigation measures. They also help provide programme and cost certainty and facilitate stakeholder engagement.
Over the last year Aphex, a powerful construction planning software tool which enables the delivery teams to better plan and work together has been introduced. This has been used for short term, look-ahead planning, which is linked to, and aligned with the master schedule in P6. It has also enabled the construction teams to control the build, assign ownership, communicate and track plans on a daily basis.
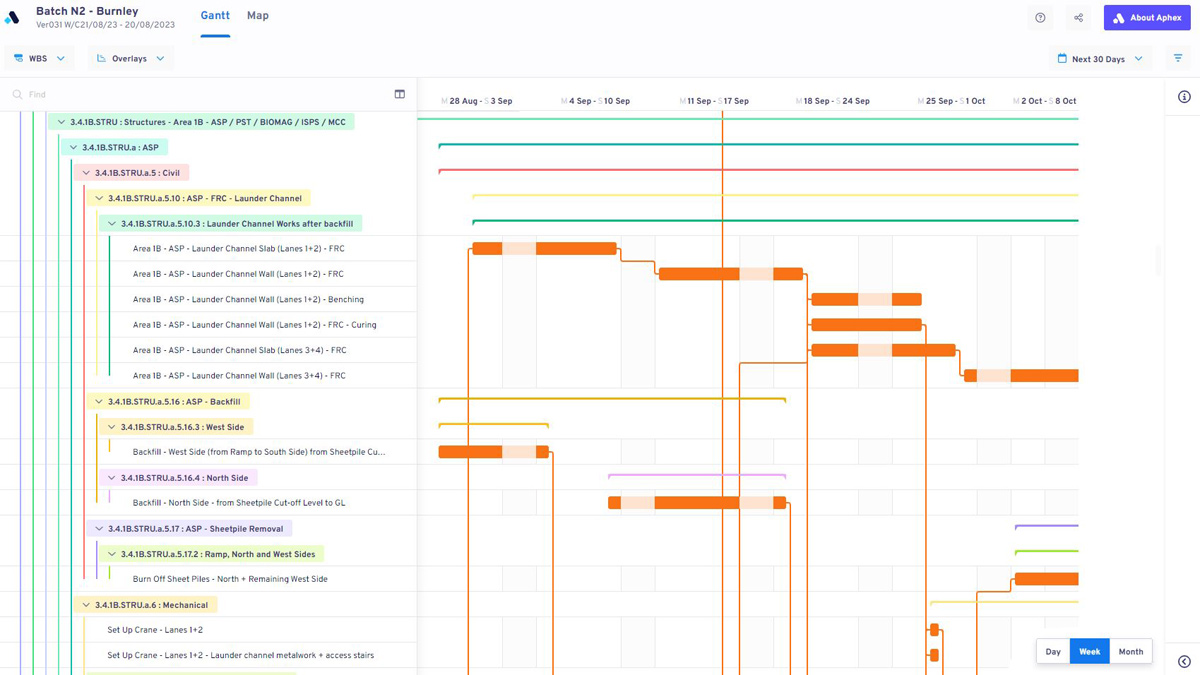
Aphex construction planning software Gantt chart – Courtesy of United Utilities
Challenges and collaboration
A large and complex project of this type, across several sites, brings enormous and numerous challenges. These include health and safety management of large scale, complex construction in constrained working areas, on live operational sites and in 3rd party and public areas, while also working in environmentally sensitive areas and requiring engagement and interfacing with customers.
Successful delivery would not happen without true collaboration. From the outset of the project we delivered a team development programme and established a co-located office which has proven to be invaluable in creating a great culture and an open and collaborative working environment over the last three years.
Challenges and emerging risks and issues are dealt with almost on a daily basis as a team. The project teams continually work together to ensure that delivery stays on track, the highest standards are maintained and everyone goes home safe and well.