Burnley WwTW Catchment Strategy (2024)
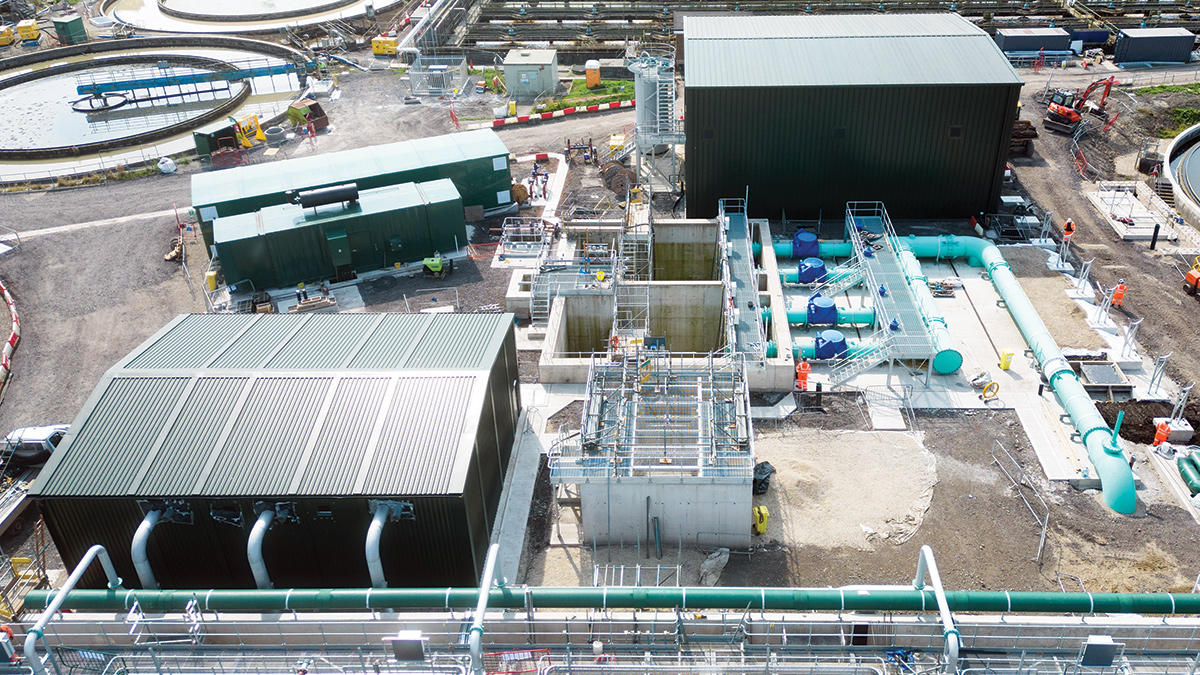
Blower building, Interstage Pumping Station & BioMag building - Courtesy of United Utilities & Advance-plus
The Burnley Integrated Catchment Scheme is one of United Utilities (UU) largest AMP7 projects. The project is being delivered through our Construction Delivery Partner (CDP) Framework by Advance-plus, a joint venture between MWH Treatment, J Murphy & Sons (JMS) and Stantec. The project commenced in 2020 and through previous years articles we have been able to share the project journey we have been on from concept, through solution and design development, and construction updates. In this year’s article we are pleased to provide an insight on the significant progress made over the last twelve months, and a look forward to the December 2024 regulatory outputs.
Project requirements & the integrated catchment solution scope
The integrated solution scheme requirement is River Water Quality Improvement for the Water Framework Directive (WFD) driver identified in the Water Industry National Environmental Programme (WINEP) to achieve a ‘good status’ in the defined reaches of Pendle Water and the River Calder. To meet this, the treatment capability at Burnley Wastewater Treatment Works (WwTW) is to be enhanced to achieve compliance with the new treated effluent permit standards, coupled with management of storm discharges in the defined reaches, to achieve a compliance with the WFD 99%ile wet weather intermittent standards. There are eight regulatory drivers attached to this WFD element of the scheme.
The project also includes a further two regulatory drivers for U_MON3 spill monitoring and U_MON4 flow monitoring.
Through complex river water quality and network modelling, the lowest whole life cost integrated catchment solution was determined and developed.
Four sites make up the integrated catchment solution which are all inter-dependent in delivering the regulatory outputs.
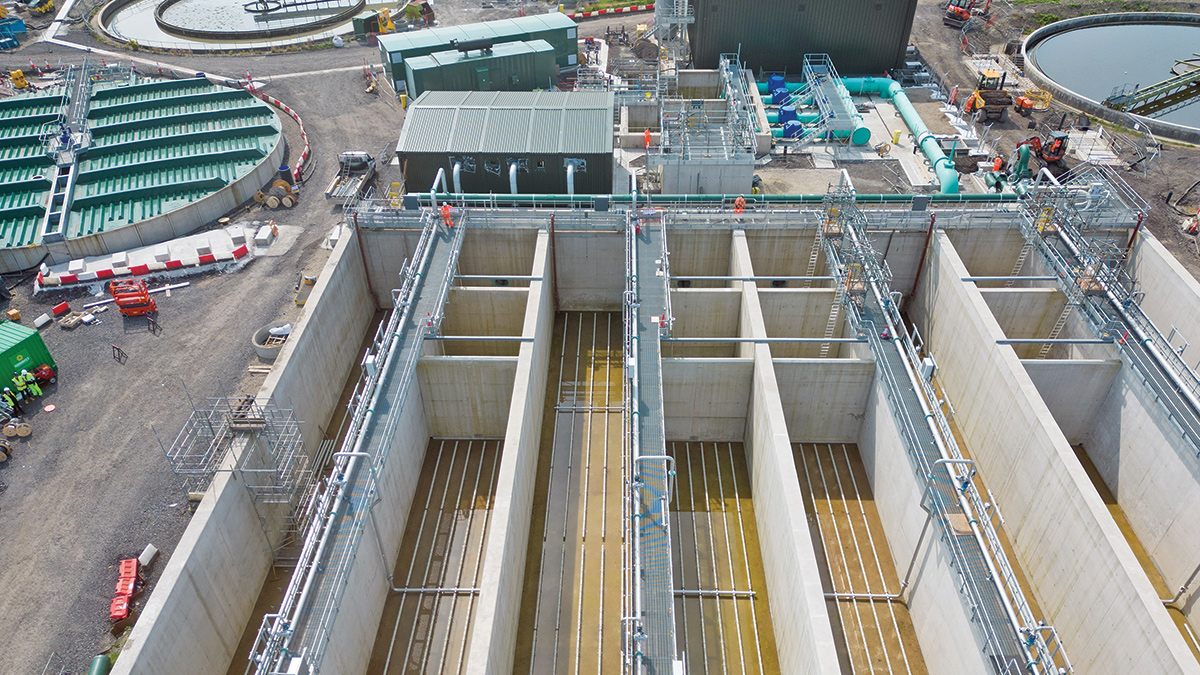
Activated sludge plant, interstage pumping station and blower building – Courtesy of United Utilities & Advance-plus
Burnley WwTW
Burnley WwTW serves a domestic population equivalent (PE) of 107,115 plus trade load. The site is undergoing a significant upgrade with the scope comprising design, construction, and commissioning of:
- New 12,000m3 detention tank with associated pumping station.
- New additional (4th) primary settlement tank (PST).
- New 1300 l/s interstage pumping station.
- New activated sludge plant (ASP) with BioMag process. The BioMag System enhances conventional biological wastewater treatment by using magnetite (Fe3O4) to ballast floc allowing an increase in mixed liquor suspended solids (MLSS) in the ASP and enhanced performance in the final settlement tanks (FSTs).
- Refurbishment of the four existing final settlement tanks (FSTs).
- New surplus activated sludge (SAS) thickening process.
- New ferric and caustic dosing plants.
- Associated motor control centres (MCCs), SCADA upgrade, and power upgrade.
- U_MON3 Event Duration Monitoring (EDM) on spills to storm tanks.
- U_MON4 flow monitoring.
2024 has seen the project progress at pace, transitioning through the typical construction sequence of civils, mechanical and electrical installation and now into commissioning.
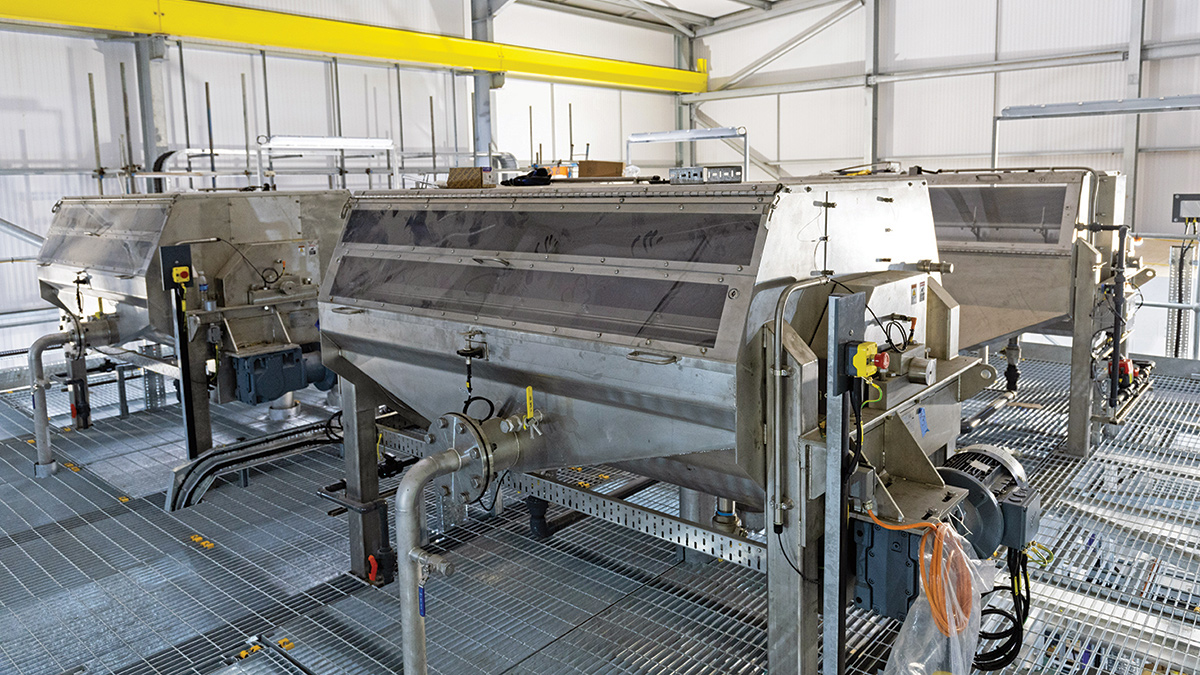
BioMAg Magdrums – Courtesy of United Utilities & Advance-plus
Storm tanks & interconnecting pipework
A critical element of the works has been modifications to the existing storm tanks and installation of interconnecting pipework to provide the flow path and link into the detention tank feed pumping station.
Safe access into the storm tanks to core the interconnecting walls and install the pipework is only possible during dry weather, low flow periods and requires robust planning and risk management with the operations staff. The wet and unpredictable weather during the first half of 2024 proved challenging and hindered progress in this area but is now complete and ready to go into service when required.
Primary settlement tank (PST)
The new PST was built by A-Consult Ltd using the precast concrete panel method of construction. The design comprises a fixed bridge, rotating scraper arrangement to accommodate installation of a cover to provide odour mitigation. The mechanical installation has been undertaken by EPS Water and Corporate Engineering supplied and installed the cover. The odour extraction fans, ductwork and vent stack have also been installed and put into operation. Commissioning of the PST is complete.
Interstage Pumping Station
To transfer flows to the new ASP, via a new distribution chamber, an interstage pumping station (ISPS) has been constructed, comprising a two-compartment design to facilitate future maintenance activities. The mechanical installation, by FSE, of the pumps and pipework is now also complete along with associated access steelwork. The new pumps have been supplied by Xylem Water Solutions who have supported the designers in providing the most efficient arrangement. The pumping station installation is complete and commissioned.
Activated sludge plant
In constructing the new ASP, STAM Construction Ltd have installed 650 tonnes of rebar and poured 4500m3 of concrete. The overall size of the ASP is 48m x 48m x 6.6m deep, has a capacity of 14,500m3 and comprises four lanes. For the last few months, mechanical installation of the air blowers, air pipework manifolds, internal pipework, aeration grids, diffusers (by Suprafilt Ltd) and access platforms and walkways (by Tushingham Steel Fabricators) has been taking place and now complete. The electrical installation followed swiftly behind, along with testing and commissioning.
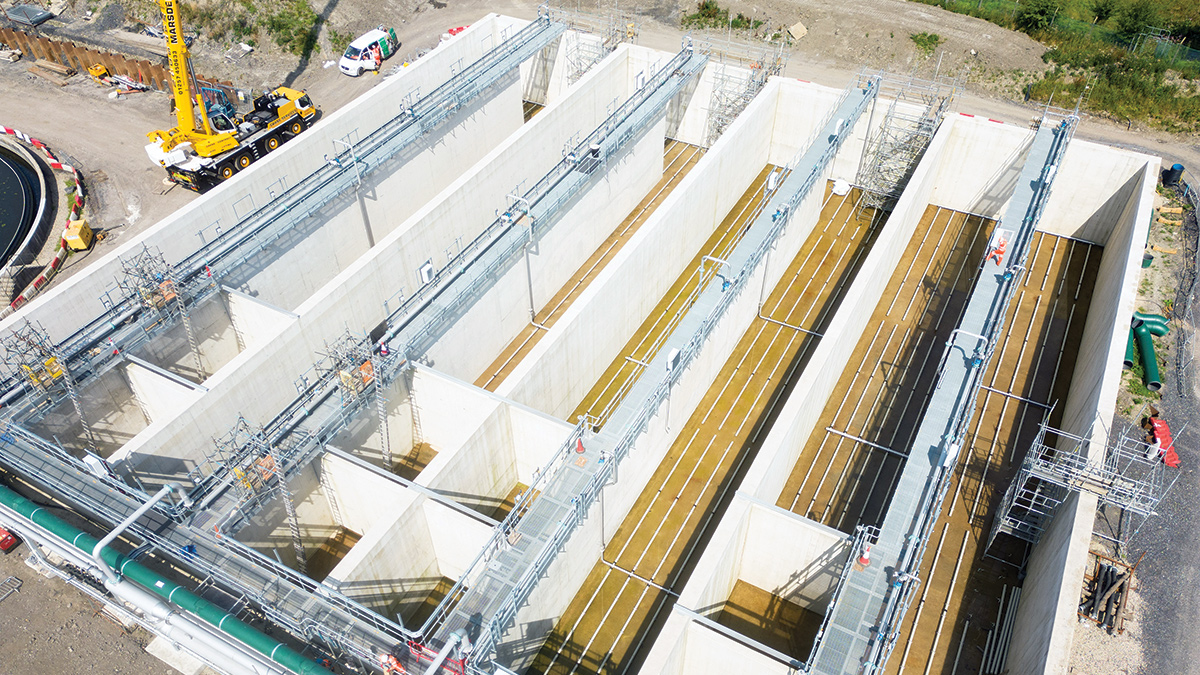
Burnley WwTW: ASP plant – Courtesy of United Utilities & Advance-plus
BioMag
Evoqua Water Technologies’ BioMag process involves dosing magnetite which acts as a ballast, which coupled with chemical dosing provides efficient solids removal from the process. Adopting the BioMag technology has meant the footprint of the ASP is smaller than a conventional ASP process and the four existing FSTs provided sufficient capacity and could be utilised with refurbishment without the need to build additional units. This has contributed significantly to the lowest whole life cost solution.
The BioMag comprises equipment including four Magdrums, two shear mills, process tanks, magnetite silo and pumps which have all been mechanically installed by Alpha Plus Ltd. The electrical installation, by PICOW Engineering Group, is complete and Evoqua Water Technologies have now commenced their commissioning.
To meet the desired performance with the introduction of the BioMag process and dosing of magnetite, and to provide asset life longevity, the four existing FSTs have undergone significant refurbishment work. The scope included civils refurbishment of the tank walls which involves cutting approximately 300mm from the top of the walls before installing new reinforcement and re-casting concrete to the required coping levels. Cutting works is being undertaken by Holemasters and FRC works self-delivered by JMS.
The mechanical and electrical work was undertaken by Jacopa and comprised refurbishment of the bridge, scraper assemblies, and other ancillary equipment.
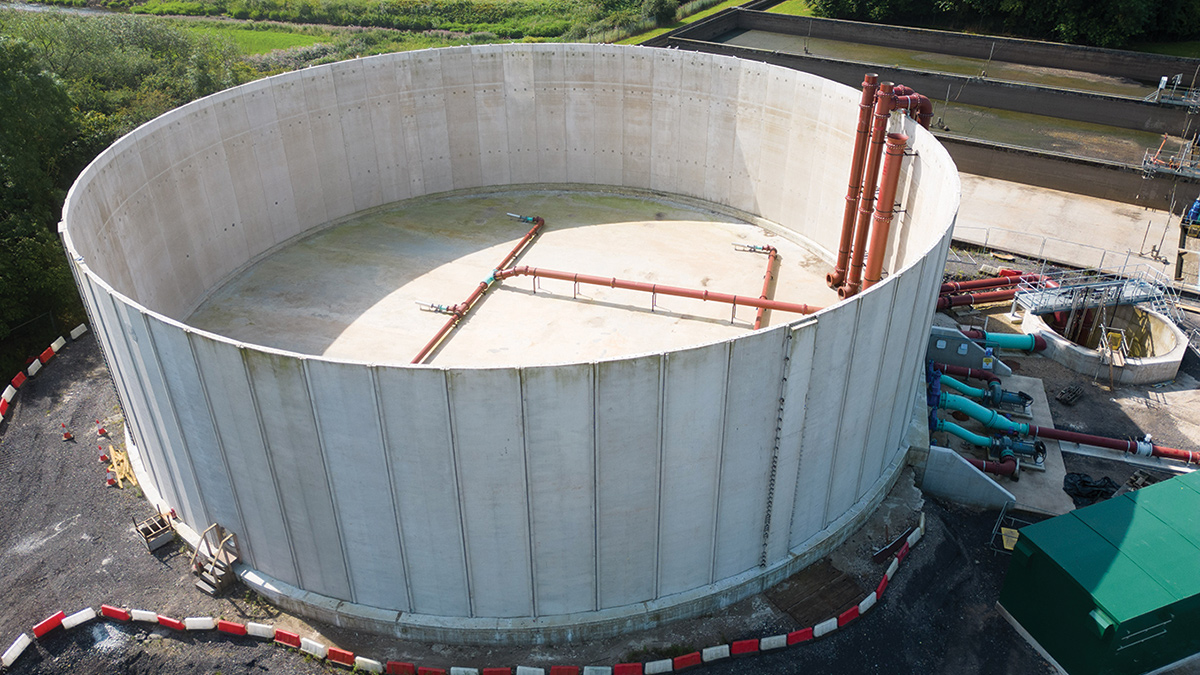
Detention tank and pumping station – Courtesy of United Utilities & Advance-plus
Detention tank
Construction of the new detention tank has been completed by A-Consult Ltd and comprised 64 precast concrete panels, standing 10.4m high. Works included the mechanical installation of the internal and external pipework and fluidic mixing system by Fluid Sealing & Engineering (FSE). The feed pumping station has also been constructed and the pumps and pipework installed. The electrical installation by PICOW Engineering Group is just completed with commissioning due to be undertaken in October 2024.
Sludge thickening
The new sludge thickening plant, via a new storage tank, accepts sludges from the treatment process, and through two Huber Technology drum thickeners with poly dosing, thickens the sludge to 5.5% dry solids before sending it to the existing sludge treatment centre via new transfer pumps.
The plant also includes a new pumping station to return filtrate from the thickening process back to the front end of the treatment process. The installation is fully complete and commissioned, awaiting sludge to be generated through process commissioning of the new process.
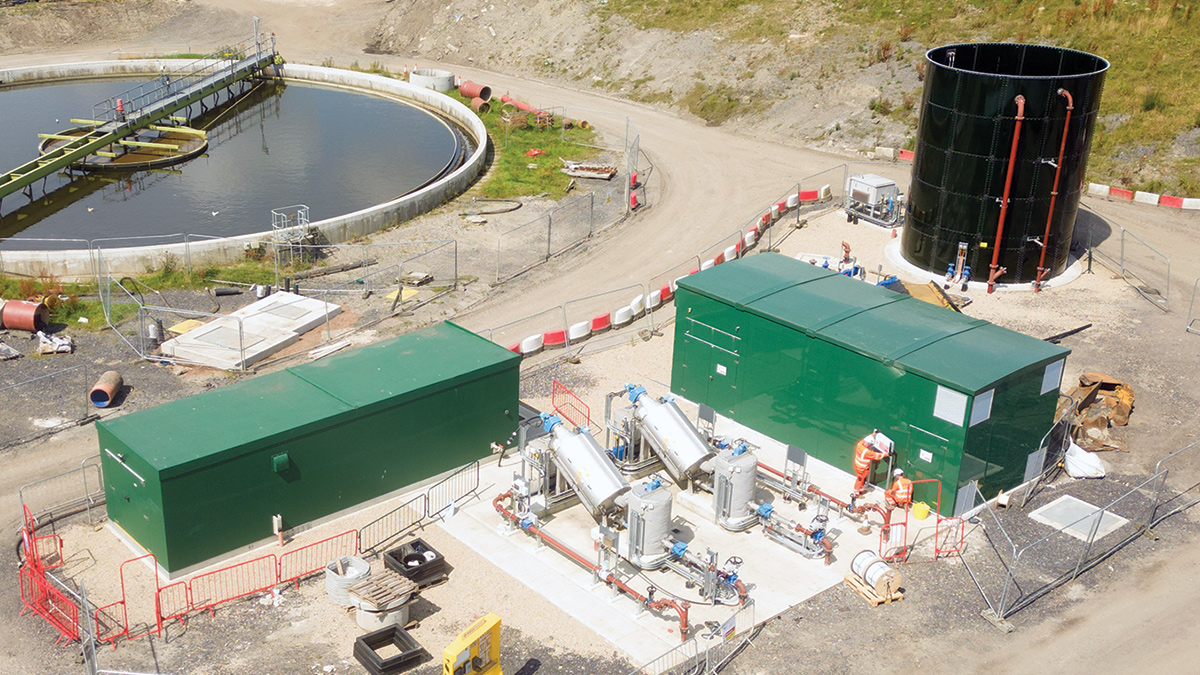
Sludge thickening area- Courtesy of United Utilities & Advance-plus
Chemical dosing
The new ferric and caustic dosing plants comprise storage tanks, dosing rigs and dosing pipelines, all of which have been delivered and installed on site by NPS Engineering Group. A new chemical delivery and offloading facility has also been constructed with final tie-ins to the existing site road network ongoing. The electrical installation is also now complete in this area with dry testing and commissioning in progress.
Electrical works
A new, uprated HV cable has been installed from the off-site substation to the wastewater treatment works, a length of approximately 900m, passing through a number of fields and third party land. To meet permit requirements, a new automated standby generator has also been installed to provide resilience to the interstage pumping station and ASP in the event of mains power failure. The generator has undergone successful G99 testing and now in operation.
To control all the new assets a number of new motor control centres (MCCs), housed within kiosks, are required around the site, along with a new site wide SCADA system. All MCCs have been provided and installed by Technical Control Systems Ltd. The electrical installation of the associated assets and field instruments etc is complete in all process areas. The new SCADA system and associated fibre network are now operational providing full control and visibility of all new and existing assets.
Meeting drivers
To satisfy the U_MON3 driver, an ultrasonic level device detects any spills into the storm tanks. This was verified and certified to allow the U_MON3 driver to be satisfied in May 2024.
To cater for the increase in flow to full treatment (FTFT) of 275 l/s (taking FTFT to 1295 l/s), a second channel has been constructed, complete with flume and flow monitoring. In conjunction with the existing flume, the system will be verified and certified to U_MON4 standards.
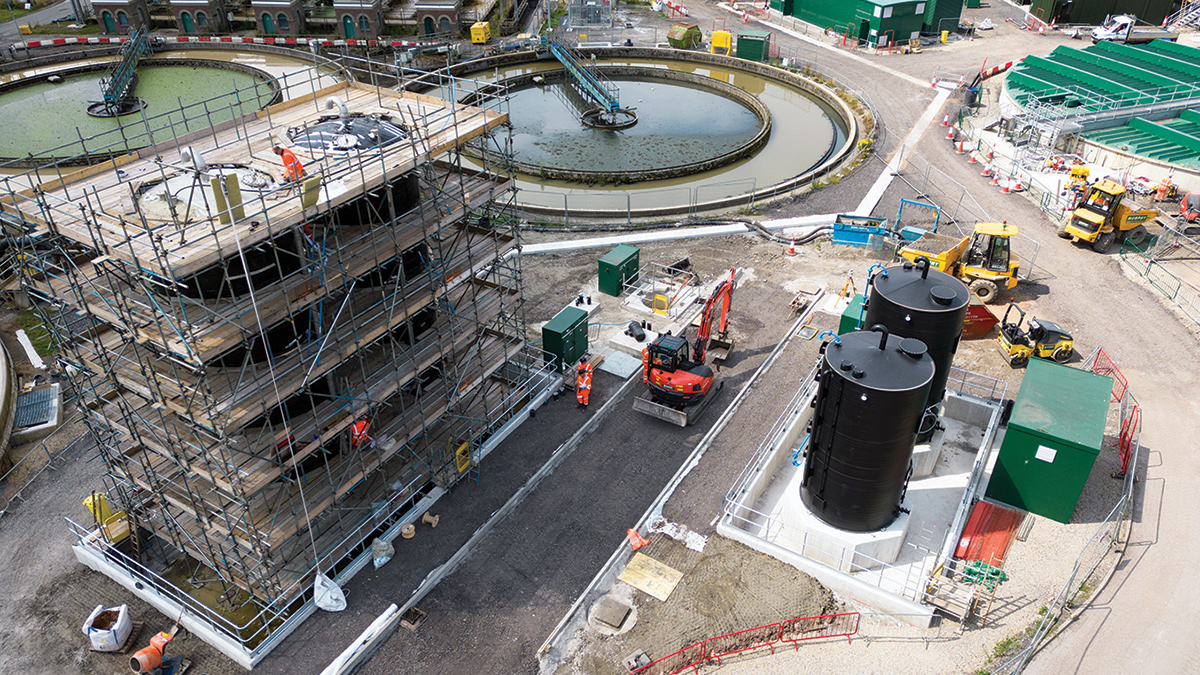
Burnley STW: Chemical dosing area – Courtesy of United Utilities & Advance-plus
Burnley process commissioning & start-up
Planning for commissioning commenced in the design phase anticipating the complexity of managing a smooth transfer from the existing process to the new, without compromising compliance. The design and build have included things such as pipework, sacrificial valves, connection points, and isolation points etc to facilitate effective commissioning. Monthly process commissioning workshops have been held throughout the last year, involving the project teams and operational staff, to jointly develop the start-up plan and methodology. Lots of hard work has gone into developing this robust plan taking into consideration all aspects of process risk and appropriate mitigation and contingency measures.
It is envisaged to take around 8-10 weeks to start-up, establish and stabilise the biological treatment, and migrate from the existing to the new process, passing through a structured Agreement to Operate (ATO) process, comprising nine interim stages. A period of optimisation will follow before entering into the 56 days completion test period.
- iATO 1A: Commence flow to PST4, ISPS and ASP lanes 1&2, with MLSS build up.
- iATO 1B: Pass forward flows from ASP Lanes 1 & 2 to FSTs.
- iATO 2: Turn all flows to new ASP.
- iATO 3: ASP Lanes 3 & 4.
- iATO 4: SAS thickening.
- iATO 5: Magnetite loading.
- iATO 6: Primary ferric and caustic dosing.
- iATO 7: Increase flows to new FTFT of 1295 l/s and detention tank.
- iATO 8: Secondary ferric & liquid poly dosing.
At the time of writing (September 2024), the project has hit the major milestone of interim ATO 1A which is the initial turning of a portion of incoming flows into PST4, interstage pumping station and lanes 1&2 of the ASP plant. The team is now in the process of establishing the biology in those two lanes, and using a mixture of crude effluent and surplus activated sludge (SAS) from the existing process, building up the mixed liquor suspended solids concentration towards the target of 2500 mg/l, which is the gateway to stage iATO 1B.
It is expected that the new process to be fully operational and optimised with completion testing commencing in December 2024.
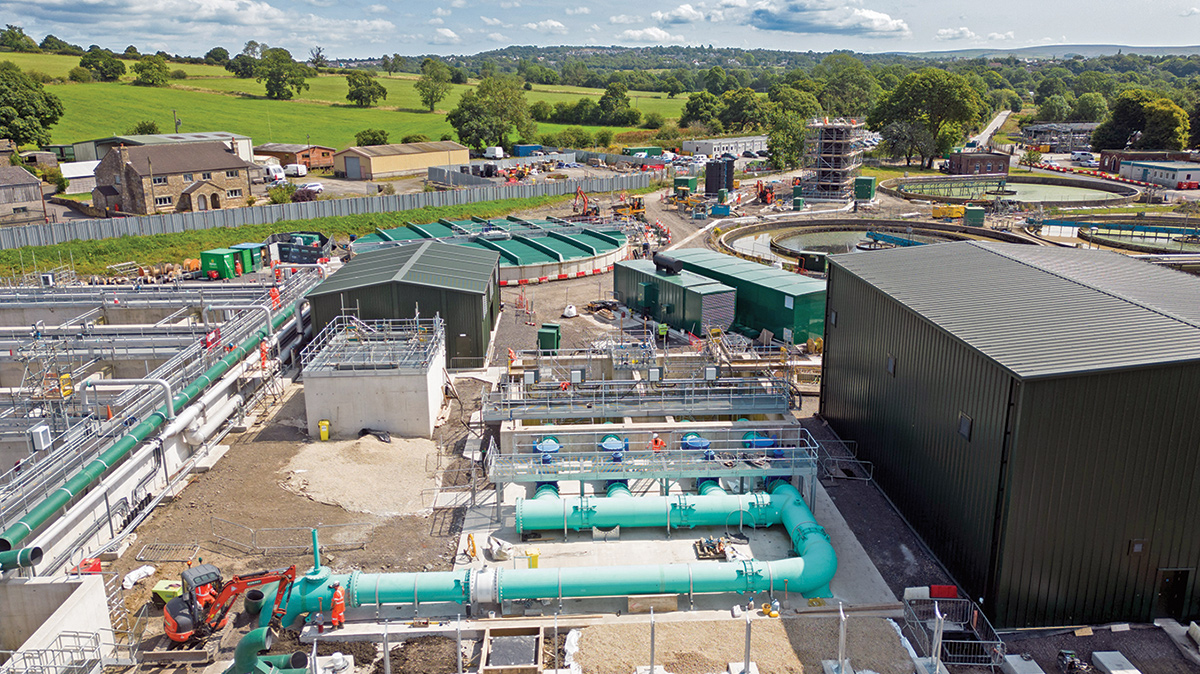
Interstage pumping station and BioMag & blower buildings – Courtesy of United Utilities & Advance-plus
Burnley WwTW Catchment Strategy: Supply chain – key participants
- Client: United Utilities
- Construction Delivery Partner: Advance-plus JV
- MWH Treatment (Advance-plus jv)
- J Murphy & Sons (Advance-plus jv)
- Stantec UK (Advance-plus jv)
- Civil design detention tank: COWI UK Ltd
- Physical modelling: Hydrotec Consultants Ltd
- Dewatering design: OGI Groundwater Specialists Ltd
- Dewatering: Alba Dewatering Services Ltd
- Concrete construction: STAM Construction Ltd
- Detention tank shaft: Joseph Gallagher Ltd
- Pump station shaft: EJ Kelly
- Sheet piling: Sheet Piling (UK) Ltd
- PCC driven piling: Van Elle
- Concrete cutting: Holemasters
- Temporary works/shoring: MGF Ltd
- Precast post tensioned tanks: A-Consult Ltd
- Precast roof sections: Macrete (Ireland) Ltd
- Precast shaft segments: FP McCann
- Blower building: Saredon Steel Buildings Ltd
- BioMag building: Gallaway Construction Ltd
- Access metalwork: Tushingham Steel Fabricators
- BioMag process: Evoqua Water Technologies
- BioMag mechanical installation: Alpha Plus Ltd
- Civils & pipework: SGC Civil engineering Ltd
- Pumping station mechanical installation: Fluid Sealing & Engineering (FSE)
- Transformers: Winder Power
- Electrical installation: PICOW Engineering Group
- MCCs: Technical Control Systems Ltd
- Systems integration: Tata Consultancy Services
- SAS glass coated steel tank: Stortec Engineering Ltd
- Dosing systems: NPS Engineering Group
- PST fixed scraper bridge: EPS Water
- Epoxy coated carbon steel pipework & wall starters: Freeflow Pipesystems Ltd
- SAS drum thickeners: Huber Technology
- Odour control system: Air-Water Treatments Ltd
- PST odour covers: Corporate Engineering
- Ductile iron pipework: Saint Gobain PAM UK
- Ductile iron pipework: Electrosteel Castings (UK) Ltd
- FST scraper bridge refurbishment: Jacopa Ltd
- Blowers: Sulzer Pumps Wastewater Ltd
- Aeration system: Suprafilt Ltd
- SAS tank air mixing system: Utile Engineering
- Submersible pumps: Xylem Water Solutions
- Valves: AVK UK Ltd
- Standby generators: DTGen
- Kiosks: Industrial GRP
- Ventilation: Air Technology Systems Ltd
Lindred Road CSO (PEN0056)
Work at this existing combined sewer overflow (CSO) site comprised the construction of an online 1,950m3 detention tank which will hold storm waters during times of heavy rainfall, reducing discharges to the watercourse. New pumps within the tank return the effluent to the sewer for onward treatment at Burnley WwTW. A new motor control centre and power supply were installed for this facility.
The detention tank which is of segmental shaft construction, 15m diameter x 20m deep, and located within the very busy and congested Lomeshaye Industrial Estate in Nelson, has been constructed by Joseph Gallagher Ltd. This was a highly challenging build within a car park of one of the local businesses and an enormous amount of planning and stakeholder management was required.
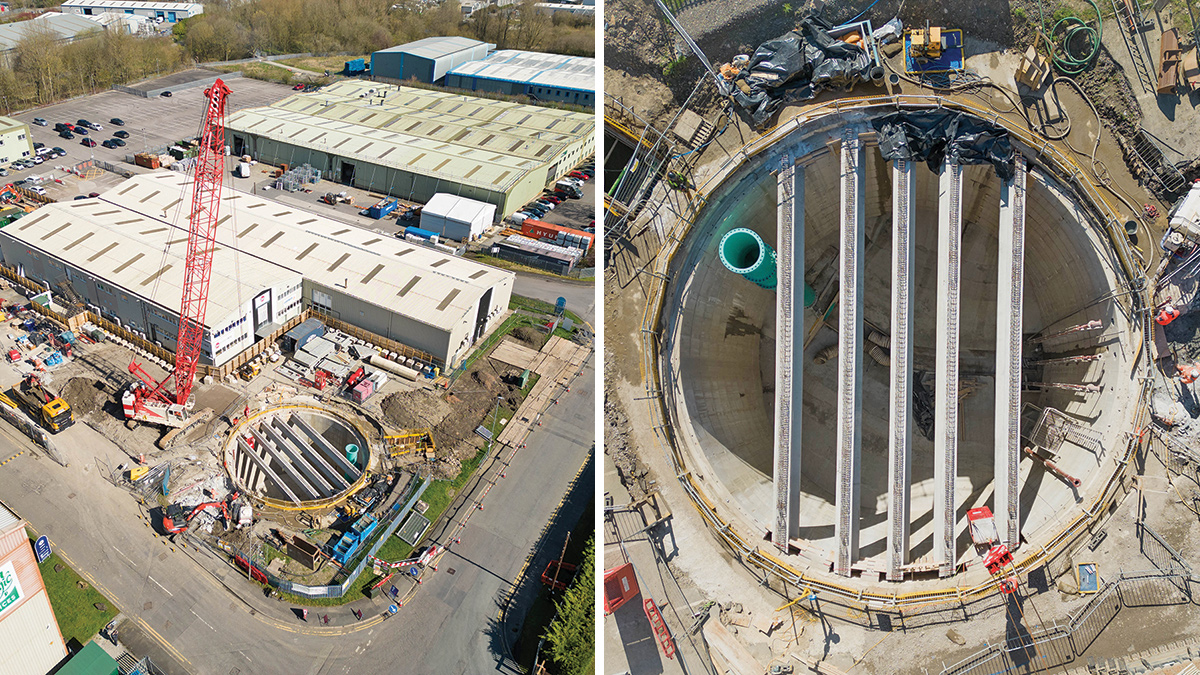
Lindred Road detention tank during construction – Courtesy of United Utilities & Advance-plus
Work started on site in July 2022, with the first phase involving the diversion of numerous services, including gas, fibre, BT, water and power, to clear the area for the tank construction. Enabling works to provide safe access routes, segregation, and procurement of alternative car parking for the impacted business employees was also required before the main construction work could commence in earnest.
Ground was broken in August 2022 with the tank construction continuing through to December 2022 when full depth was reached. Construction of the pump sumps, inlet channel and complex benching arrangement followed.
The spring months of 2023 saw the mechanical works inside the tank take place with the installation of the pumps, pipework and access ladders and platforms. Once the internal works were complete, the roof beams were installed and the roof slabs placed on in May the same year.
The subsequent months saw the installation of the inlet and outlet pipework for the tank, including associated manholes and chambers. To facilitate the connection of the 1200mm inlet pipe into the existing CSO chamber, a complex timber heading arrangement needed to be constructed in order to access beneath, and protect a myriad of services crossing the vicinity.
The civils and pipework were undertaken by SGC Civil Engineering Ltd and the mechanical works by FSE. The new site power supply was energised in October 2023 allowing testing and commissioning to follow.
The new detention tank went into operation in December 2023 with all works on site complete in March 2024, and is now providing great environmental benefit through significantly reduced discharges.
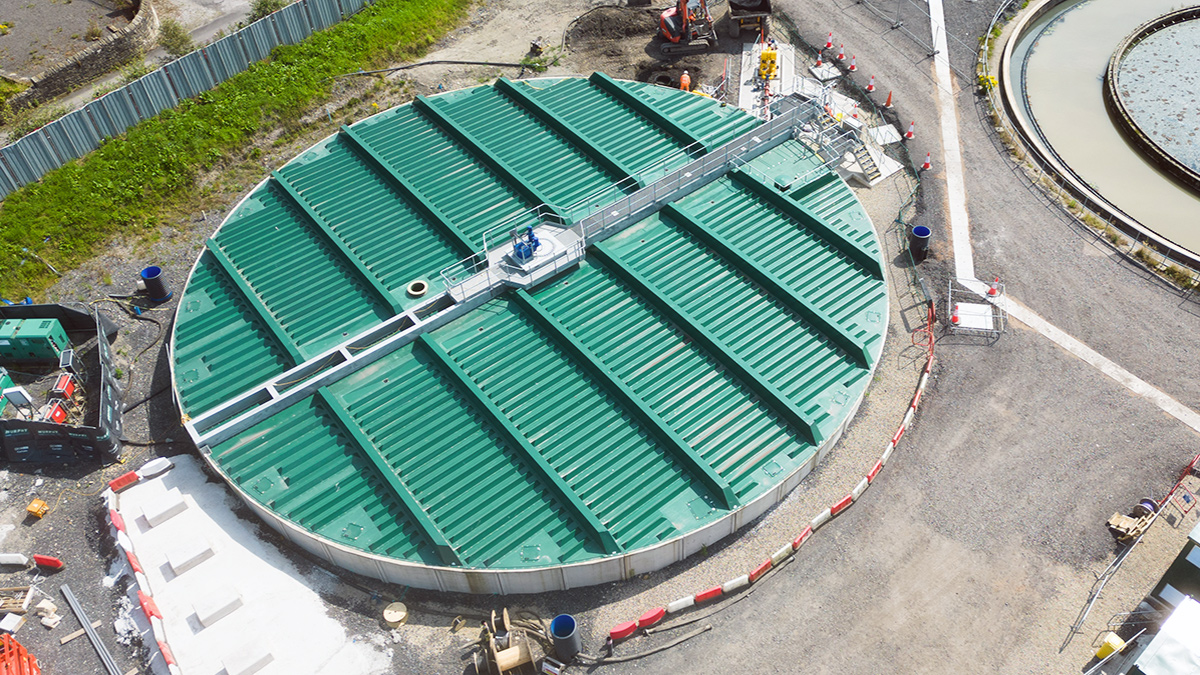
Burnley WwTW: Odour control cover for PST4 from Corporate Engineering – Courtesy of United Utilities & Advance-plus
Altham Outfall Fennyfold CSO (BUR0026)
This existing CSO site is located in Padiham, near Burnley, and is part of the sewer network that transfers flows to Hyndburn WwTW for treatment. The solution here was to construct a new chamber over the downstream sewer, and install a new real time controlled actuated penstock valve that regulates and optimises flows passed forward to Hyndburn, whilst reducing spills from the existing CSO. A new control kiosk was also provided.
This new facility is situated within an environmental and stakeholder sensitive area, adjacent to a number of allotments, and the River Calder. The parcel of land required for the new kiosk and chamber had to be procured and a new access track for both construction and future operation and maintenance was laid. To facilitate the main construction activity, a complex temporary works arrangement was required, with large scale over-pumping, to carry out the works on the live sewer. Works included installing temporary isolation rails and plates during overnight and low flow conditions.
The civils and mechanical works were undertaken during spring 2024, with the new mains power supply being energised in June. Testing and commissioning ensued, with the new real time controlled system going into full automatic operation in August.
Reinstatement and landscaping took place during summer and the works are now complete at this site.
There was lots of positive engagement with the local community of allotment holders throughout the works, including a tree planting day with the local school arranged.
Hyndburn WwTW
To cater for the change in flows being presented at Hyndburn WwTW through the inlet sewer from the BUR26 catchment, the solution modelling identified works would be required on the site storm tank return system to ensure that the river water quality objectives would be achieved.
The initial solution model indicated the existing storm tank return pumping station needed to be replaced with a new facility with an increased pumping capability which would have cost in the region of £2.4m.
Through value engineering workshops, pushing the boundaries with several iterations of water quality solution modelling, and positive discussion and engagement with the EA, we successfully designed out the need to build a new storm tank return pumping station. Instead, the works simply comprised optimisation of the existing facility to return the storm tank contents sooner once a storm event has subsided.
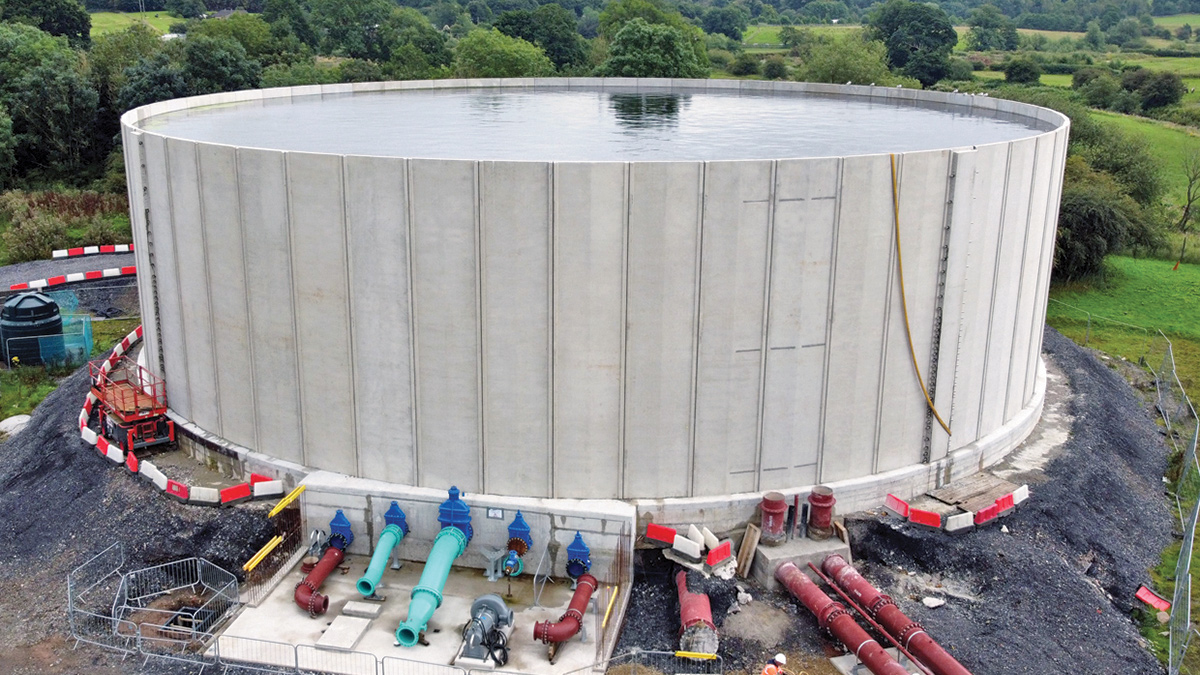
Detention tank on water test – Courtesy of United Utilities & Advance-plus
On course for success….
With the works at Lindred Road CSO, Altham Outfall Fennyfold CSO and Hyndburn WwTW now complete and in full operation, and Burnley WwTW in the thick of process commissioning, the United Utilites/Advance-plus team are on course to successfully deliver the catchment solution project and meet the eight Water Framework Directive regulatory outputs ahead of the 22 December 2024 regulatory date.
At Burnley, the U_MON3 output is complete with the U_MON4 verification and certification is due to take place in October.
Getting to this stage, and on course to successfully deliver, this major and highly complex scheme, has not just happened by chance. It has been years of hard work, dedication, and an intense focus on health, safety and wellbeing being at the forefront.
A proud landmark moment of reaching 500,000 hours worked across the project RIDDOR free was achieved in May this year.
It is testament to true collaboration between the United Utilities and Advance-plus project teams and wider stakeholders which has seen us overcome many challenges and get to where we are today as we head into the home straight.
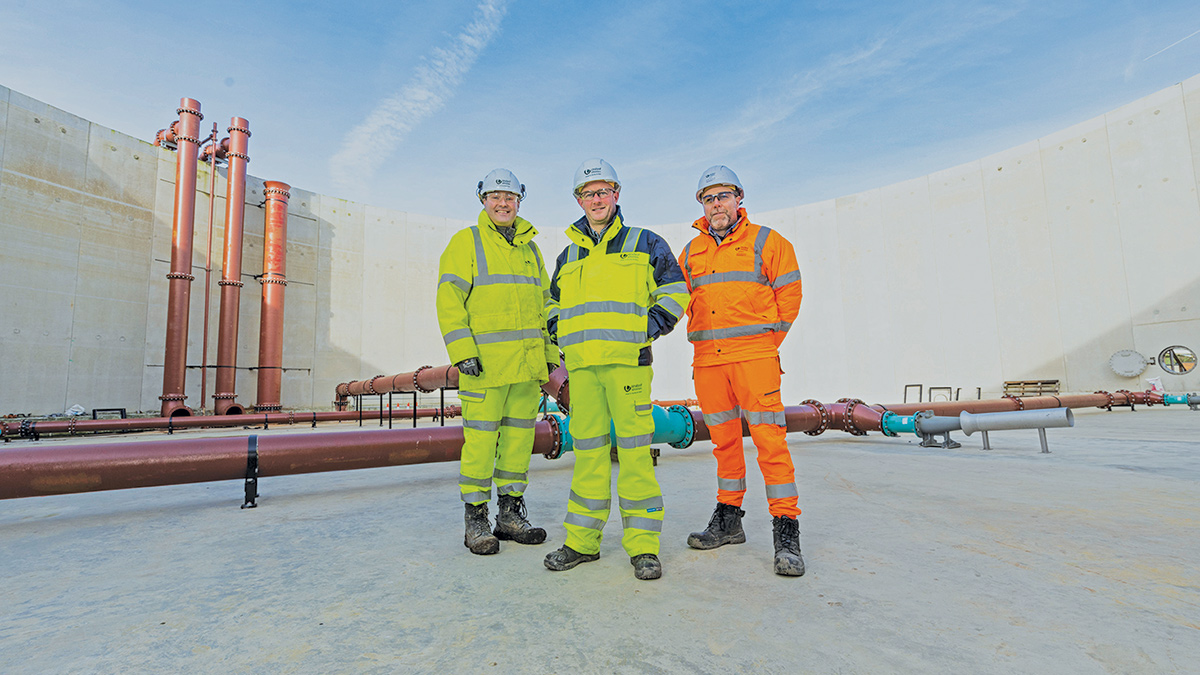
Inside the detection tank - Courtesy of United Utilities & Advance-plus