Galgorm Wastewater Pumping Station Upgrade (2018)
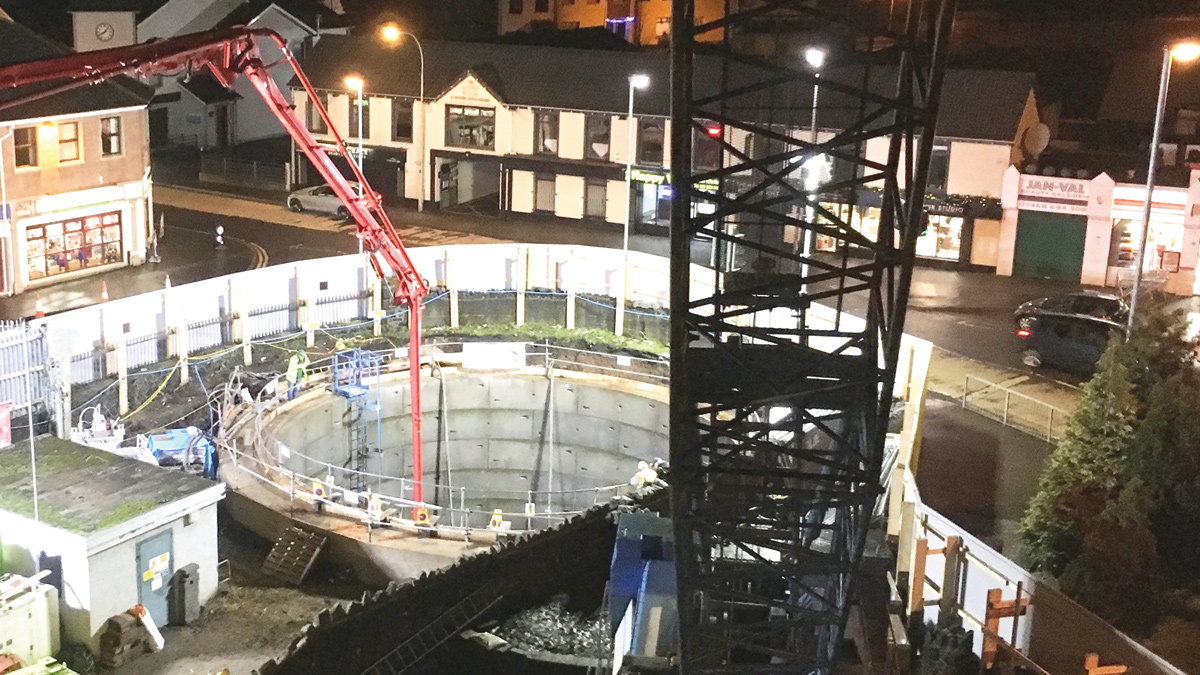
Night time concrete pours to minimise disruption - Courtesy of NI Water
Galgorm Wastewater Pumping Station (WwPS) is located within a busy public car park in the centre of Galgorm village, approximately 3.5km to the west of Ballymena, Co. Antrim. The WwPS is accessed via a steep laneway off the A42, Fenaghy Road, adjacent to Galgorm roundabout. Galgorm WwPS passes forward flows to Tulllygarley Wastewater Treatment Works (WwTW) in Ballymena. The population served is 18,088 PE (2013), including trade effluent, and there are eleven pumping stations within the catchment that all contribute to Galgorm WwPS. May 2018 saw the completion of Galgorm Wastewater Pumping Station upgrade as part of a £1.4m investment by NI Water to modernise the existing sewerage infrastructure, accommodate future expansion and address the reoccurring out-of-sewer flooding in the village and surrounding area.
Background
A number of out-of-sewer flooding incidents and public complaints had been received by NI Water which have been attributed to difficulties with Galgorm WwPS. Cullybackey WwPS and nearby Lowtown WwPS also experienced operational problems, again attributed to the difficulties at Galgorm WwPS and it was understood that the incoming sewers surcharged at high flow volumes.
RPS was initially appointed by NI Water in 2013 for the provision of professional services under the IF11-Professional Services Support Framework, to complete a Capital Investment Appraisal Report, including a population equivalent (PE) report. Following A1 approval, RPS was then retained to bring the project from A2-A4 stage (design, procurement, construction and handover).
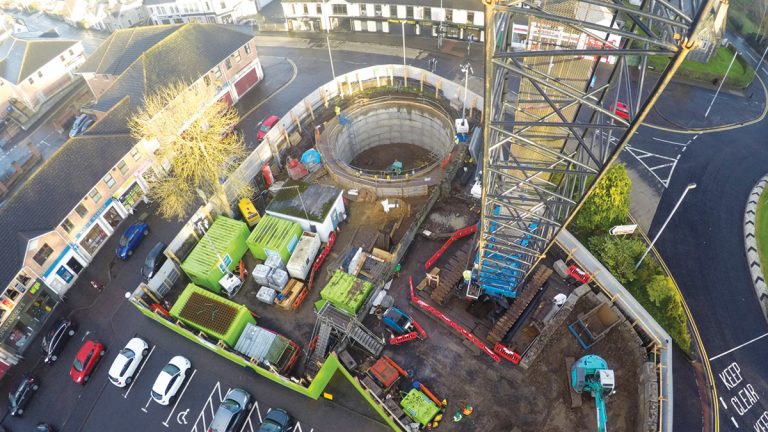
Galgorm WwPS site within public car park – Courtesy of NI Water
Need for improvements
The existing pumping station was vastly undersized offering no emergency storage and therefore did not meet the NI Environment Agency (NIEA) requirement of two hours’ storage at 3 x dry weather flow (DWF) – this is a time set to enable an operative to get out to site to fix a problem in an emergency. NIEA has set standards to comply with EC Legislation of which compliance is mandatory, and capital investment was required to provide an upgraded WwPS at Galgorm to manage wastewater pass forward and overflow to the required quality standards and to serve for the current and future population.
A desktop analysis and site survey was undertaken in 2013 to determine the current PE and the future projected PE contributing to the WwPS. A population and flow report was completed and forwarded to NI Water Asset Management Unit in May 2013 for review and agreement. A synopsis of the PE findings were:
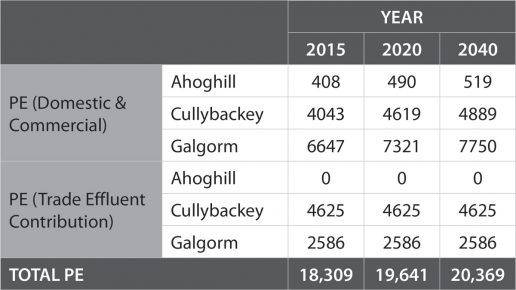
PE findings
The PE was projected to increase by approximately 2,000 between the year 2015 and 2040. The existing station was constructed in the early 1970s and the design PE for the existing WwPS was unknown, however, it was clear that there had been substantial increase in commercial operations in the local area since construction.
Without capital investment Galgorm WwPS would have continued to:
- Be non-compliant with NIEA requirements.
- Be non-compliant with H&S regulations.
- Demand a significant commitment and resources from NI Water Operations.
- The incoming sewers would continue to surcharge and the frequency and risk of out-of-sewer flooding could increase, with potential further customer complaints and possible media attention.
Project drivers
- Flood protection for Galgorm WwPS and surrounding area.
- Compliance with NIEA emergency storage requirements (all pumping stations should have a minimum of 2 hours’ storage at 3 x DWF, to minimise the risk of the Emergency Overflow discharge occurring and allowing the operator time to take preventative measures = 820m3 of storage).
- Improve quality of any emergency discharges by way of a screened overflow.
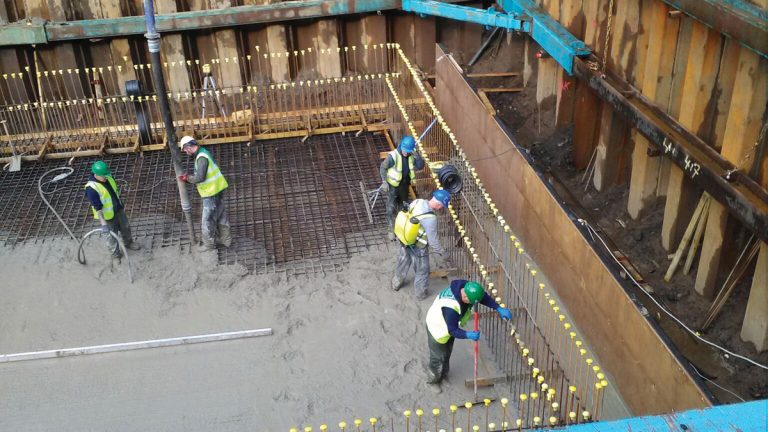
Concrete pour on storage tank at Cullybackey – Courtesy of NI Water
Brief description of the work
Northern Ireland Water developed a proposal for a £1.4m investment to significantly upgrade wastewater pumping stations serving the villages of Galgorm and Cullybackey. This major funding would provide a modern new pumping station at Galgorm and much-needed storm storage at Cullybackey to help reduce the risk of out-of-sewer flooding in the area. The new Galgorm WwPS would be constructed on the site of the existing station which would be demolished once the new station had been successfully commissioned.
The project included the construction of a combined flow wastewater pumping station incorporating: wet well, valve chamber, emergency storage tank and all associated pipework and pumping equipment. The works also included the provision of a new MCC control panel within a new kiosk, the provision of a new standby generator, facility for mobile generator and the provision of wash water air break and booster set at Galgorm WwPS. In addition to the works at Galgorm WwPS an emergency storage tank and all associated pipework was to be provided at Cullybackey WwPS upstream of Galgorm WwPS.
Tendering process
RPS developed a comprehensive scope of works for the delivery of the project including, site information, pre-construction information, works information and contract documents. The contract chosen for this project was an NEC ECC Option A Design and Build contract. Option A is a lump sum priced contract with activity schedule and was chosen for this contract as the scope of the project was well defined and therefore minimised the risk of cost increase to the employer.
In December 2016 the project was uploaded to e-Tenders for competitive tender with Graham Construction being successful. Following a post-tender interview Graham was appointed Principal Contractor and Principal Designer for the scheme in March 2017.
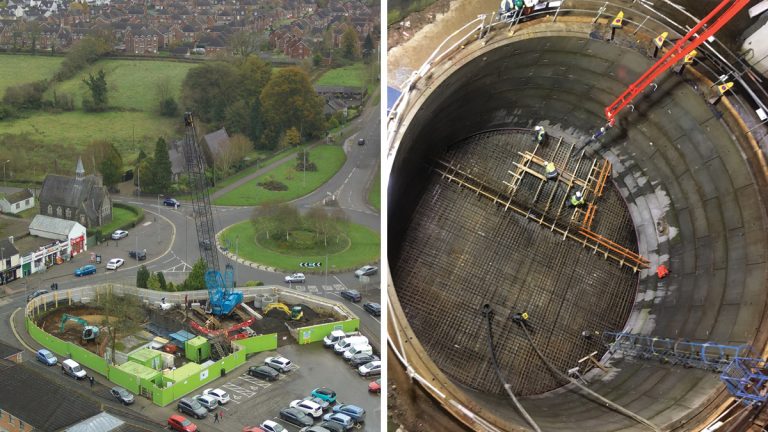
(left) Galgorm WwPS site set up and (right) concrete pours at night to minimise disruption – Courtesy of NI Water
Engineering solutions to minimise impact
Undoubtedly one of the biggest challenges facing the project team was the location of Galgorm Pumping Station – within a public car park, located beside an electricity substation and adjacent to village shops and a pedestrian crossing.
From the outset of project inception, the project team worked collaboratively with NIEA and other relevant stakeholders to reduce the extent of construction required at the Galgorm site and devised these engineering solutions to minimise impact:
- Relocating 321m3 of the 820m3 emergency storage required at Galgorm to Cullybackey WwPS. This removed the need for a larger storage tank at Galgorm, which would have significantly extended the programme and increased disruption.
- Upgrading Gracehill CSO to eliminate emergency overflow at Galgorm – something that NIEA require on all new stations. This would have required laying a pipe through main roads and local football pitches, again causing significant local disruption.
- Thorough investigation of pumping main and pump selection removed the need for an upgraded pumping main preventing further disruption.
Significant disruption would have been caused had extensive design optioneering and negotiations with regulatory bodies not have been explored.
Following several meetings with various stakeholders including NIEA, an agreement was reached to enhance the Cullybackey WwPS (located upstream) to reduce the storage and subsequent tank size required at Galgorm. It was also agreed to use and upgrade Gracehill CSO to prevent the requirement for an emergency overflow at Galgorm; something that NIEA require on all new stations.
Following further investigation of the pumping main and pump selection, the need for an upgraded pumping main was removed preventing significant disruption. With all these measures considered the contractor developed a much more efficient, less disruptive design.

Completion of Galgorm WwPS shaft – Courtesy of NI Water
Construction proposals to further minimise impact (at detailed design) and stakeholder liaison
Due to the space constraints at the site to house a 150T crane and the need to maintain the existing pumping station until the replacement was commissioned (NI Water Operations staff visit daily), as well as the busy nature of the surrounding area and the proximity of a toucan crossing at the site entrance (Transport NI had expressed concerns for the safety of pedestrians and other road users) and not to mention the need to construct a new 12.5m wide x 11m deep pumping station (requiring a dig of 181m2 – almost half the area of the site) while maintaining the existing station (60m2), required innovative thinking.
Following early liaison with Transport NI and Council the requirement to access the site via the public car park was identified to avoid large construction vehicles entering and exiting the site via the existing narrow access lane off the roundabout. At an early stage the Council had agreed for the contractor to use a small section of car park to facilitate the construction work, but it was quickly realised that in order to aid safe movement of site vehicles and allow any turning movements to take place within a secure compound, that a bigger area of car park would be required.
Taking a bigger section of car park would significantly help the construction process, provide a much safer working area and allow the project to be carried out more quickly but it would have a much bigger impact on the local community and businesses.
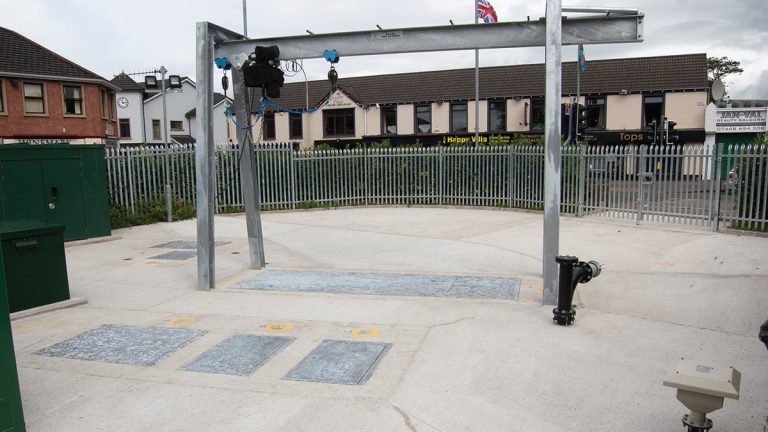
Finished WwPS site with levelled access – Courtesy of NI Water
During the design/engineering phase, NI Water, Graham and RPS looked at several options to minimise the impact to the public during construction works if a larger section of public car park could be taken. Ideas discussed with Council and Transport NI included:
- The use of the car park at Galgorm & Gracehill Community Centre for public parking.
- Construction of a temporary new car park on grass area adjacent to the A42.
- Construction of new car park further out of the village.
With the above options all ruled out due to health and safety reasons or time constraints, NI Water and its project team reassessed the programming of works based on taking the original smaller car park section previously approved by Council.
The main priority for the team during the civil construction phase was to have no large scale construction traffic through the car park during working hours. To achieve this, the project team developed a proposal to work within the small confined site during the day – excavating spoil and stockpiling – and to close the car park at night during which time the stockpiled spoil was loaded onto lorries and removed while no public vehicles were parked.
A survey of the carpark was undertaken to gauge how many cars used the car park in the evening and what time the car park normally emptied. Shops in the village were visited by the project team to explain the proposals and to gather information on deliveries to businesses etc.
Through early research it what realised that the car park was busier in the months of July and August and therefore a decision was made to delay construction start until September. Meantime, an extensive report was prepared for Council on the team’s proposals and survey findings and approval was granted for the night time closure.
Community engagement
Ahead of construction start a number of public relations activities were employed to advise the general public of plans and keep the local businesses abreast of developments. These included: a public information event and briefings to shop keepers; press articles in the local media and on social media and signage around the village to advise on temporary car parking arrangements.
Closer to construction start, flyers explaining parking arrangements were left on cars parked in Galgorm car park and information boards detailing the wider construction work and timescales were erected on the hoarding of the site.
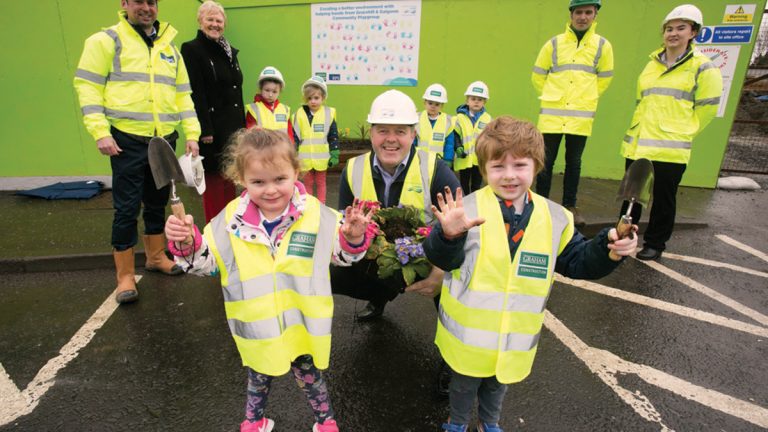
Children from Gracehill & Galgorm Community Playgroup helping to brighten up the site with plants – Courtesy of NI Water
To enable people to stop by and have a look at the work (once underway), peep holes were left at strategic positions in the hoarding and signs put up with mobile numbers for site staff should any member of the public need help to park. To promote good housekeeping, site workers were encouraged to clean their boots going out of site and to brush up the car park regularly. During the winter months, Graham site staff went so far as to salt the entire car park so that residents in the village could park and make their way to the shops more safely.
Throughout the construction period, a number of PR and education events were organised with the local village playgroup including a visit by ‘Ivor Goodsite’ and a planting event which brought some of the younger members of the community to site to learn about the environmental benefits the project would deliver.
Continuous stakeholder liaison with NI Water, NIEA, Transport NI, Council, fishing groups, elected representatives and the public ensured no stakeholder-driven delays.
Construction challenges and methodologies
In addition to the logistical challenges already mentioned, the contractor was faced with many other difficult tasks while building the new pumping station (PS) within a 20m x 20m area which housed an existing PS which also had to be maintained and operated.
The design/construction methodology was considered very carefully with the contractor using a 150T crane located outside the site in the adjacent car park to reduce the need for large plant within the actual PS site. The design methodology allowed for the new PS to be constructed offline with a planned operation to divert flows from the old to new. The need to carry out rock breaking in close proximity to buildings and structures was an initial hurdle.
In advance Graham engaged a specialist sub-contractor (Datum Ireland) to set-up monitoring points on local buildings to gauge any impact and help satisfy local property owners, and only small items of plant were used to break out rock.
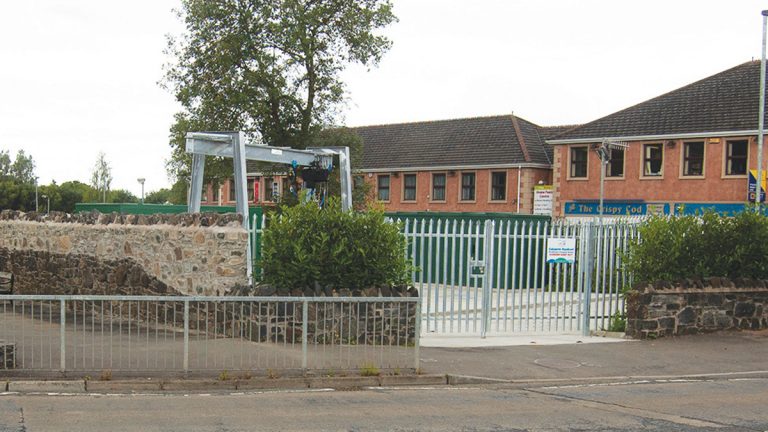
Levelled access at new Galgorm WwPS – Courtesy of NI Water
Construction of the new PS required excavation to a formation level of 11m below adjacent road (within 3m) and car park within (2m). Again an innovative design and construction methodology was employed which included the use of precast concrete segmental sections (1m) deep and a ‘top down’ excavation and construction method to retain/support the surrounding road and car park. This approach eliminated the need for substantial temporary works (piling) and associated heavy plant and machinery.
With regards to the storage and removal of excavated material, a two-shift system was used when excavating for the shaft i.e. the daytime gang installing the segmental sections stored the excavated spoil in a bespoke soil-containing bay and the night-time gang loaded it into lorries and took it off site. This cycle continued until the shaft was complete. The bespoke soil-containing bay was built using precast concrete blocks which were later incorporated into the permanent works (building retaining wall).
To reduce the volume of spoil removed at Galgorm the ground level of the site was raised. This reduced vehicle movements and improved the steep access for NIW staff which was particularly dangerous in winter.
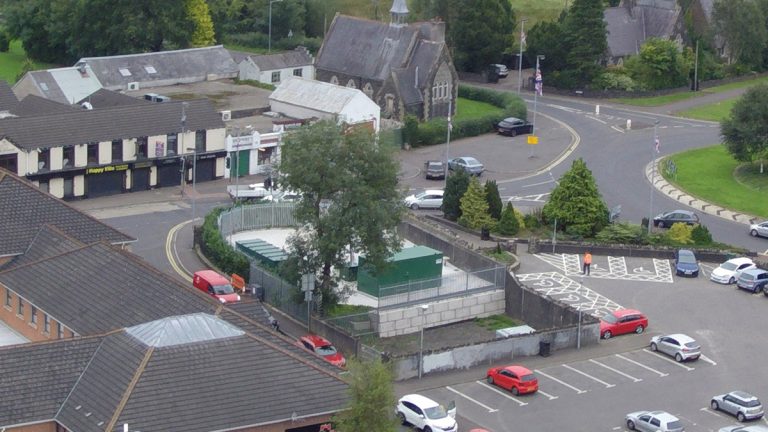
Aerial of completed Galgorm WwPS – Courtesy of NI Water
Maintaining the existing stone walls and wrought iron railings around the site was another challenge. Again utilising the crane outside the site to lift in and out all materials mitigated the need to demolish stone walls. The walls were further protected using concrete Kelly blocks which were reused in the permanent retaining wall. The design also incorporated retaining an existing tree on site and associated protection during construction.
Project success and completion
Both Cullybackey WwPS upgrade and storage facility and the new Galgorm WwPS were completed at the end of May 2018 and were due to be handed over to NI Water Operations at the end of July 2018. As part of the stakeholder working relationship, improvements were made to the entrance of Galgorm car park following completion of the project and the car park was fully reopened as promised well before summer.
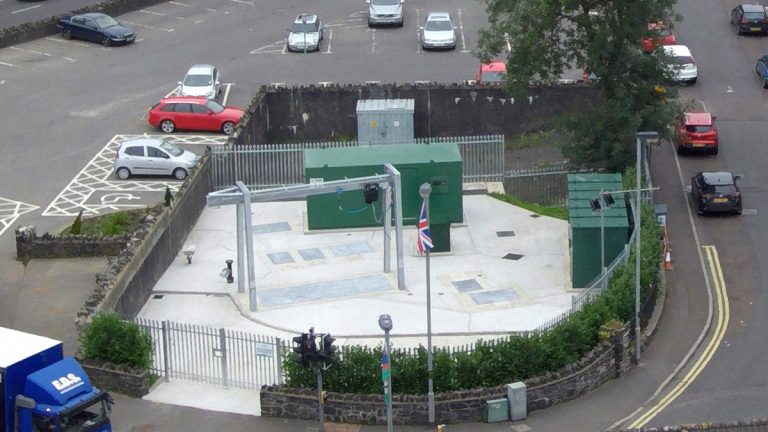
Aerial of completed Galgorm WwPS – Courtesy of NI Water
There is no doubt that the confined space made for a more labour-intensive project with unavoidable double handling but night-time working helped keep the project to programme and no accidents were reported over the 20,000 man-hours worked.
Throughout the project, which was completed to budget despite the changes made to the original proposals, approximately 1/3 of the total budget was spent through local suppliers and service providers and many positive comments were made about the scale of the project and how it was completed. At the time of writing the scheme was shortlisted as a finalist in a construction excellence award due to be announced in October 2018.