Goddards Green WwTW (2023)
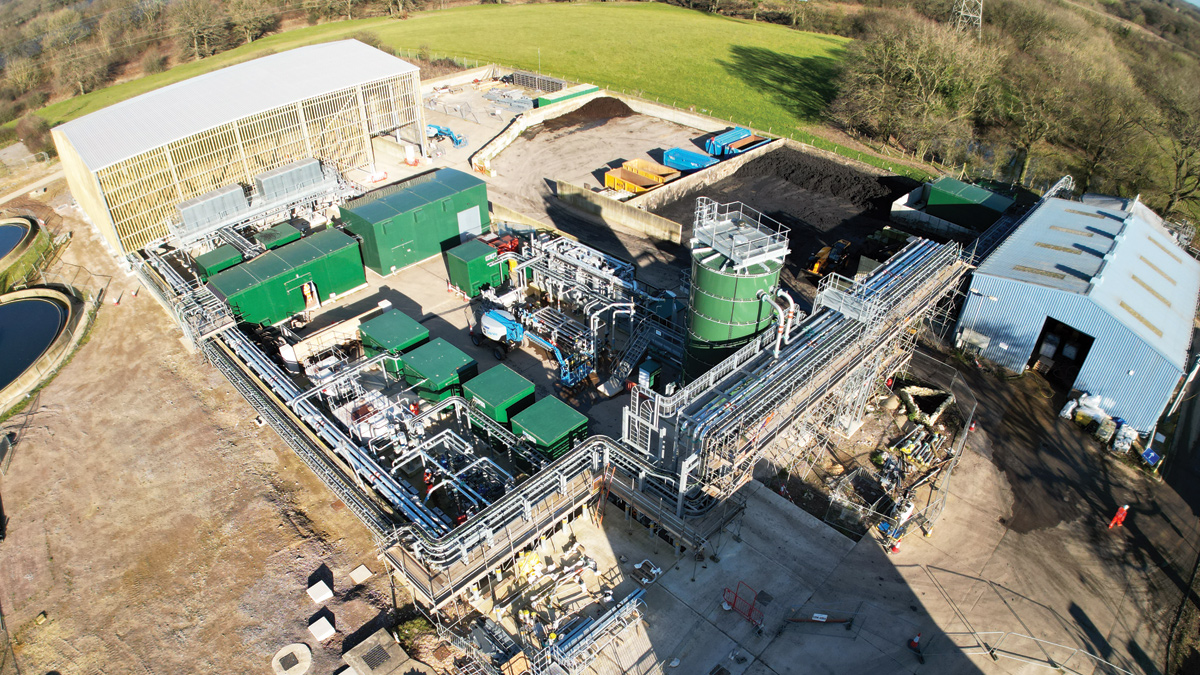
Goddards Green WwTW - Courtesy of Galliford Try
Goddards Green Wastewater Treatment Works (WwTW) is a Sludge Treatment Centre (STC) located near Burgess Hill in West Sussex. The catchment serves the towns of Burgess Hill, Hassocks, Hurstpierpoint and surrounding villages, providing for 54,789 people. The project implements an innovative approach to mitigate the likely odour from the processes at the WwTW to prevent any potential impact on the planned Northern Arc development in the surrounding area. To enable the new development to proceed in the surroundings of the WwTW, there was a planning requirement for the odour of the WwTW to be limited to 1.5 OUE/m3 odour contour.
Existing works
The main components of the WwTW consist of inlet works (screening and grit removal), storm tanks, a primary settlement tank, anoxic tanks, oxidation ditches, returned activated sludge pumping station, final settlement tanks and disc filters. Treated final effluent is discharged into the River Adur East.
Besides indigenous sludge, the STC also processes imported sludge (liquid and cake). The main components of the STC consist of sludge reception and storage facilities, screening and screened sludge storage, drum thickening, anaerobic digestion, digested sludge storage tanks, centrifuge dewatering and cake storage bays. Liquors from the sludge treatment process are treated in a cyclic activated sludge system (CASS) plant before being returned to the WwTW. Hot water for digester heating is produced by burning biogas either in hot water boilers or in the 800 kW CHP (combined heat and power) engine.
Northern Arc development
The Burgess Hill Northern Arc is a development in the southern part of the parish between Ansty and Burgess Hill. The project spans a period of over 15 years. Once complete it will provide 3500 houses with 30% affordable housing, four hectares of employment land, a community centre, two primary schools and a secondary school.
The project is being run by a government agency, Homes England, and is a strategic development which is part of the Mid-Sussex District Council Development Plan.
Southern Water’s project at Goddards Green WwTW aims to deliver a range of odour mitigation improvement measures; removing barriers to the housing development at the Northern Arc. Southern Water have committed to delivering a scheme that achieves a 1.5 OUE/m3 limit for a boundary as defined by the odour contour image (see below).
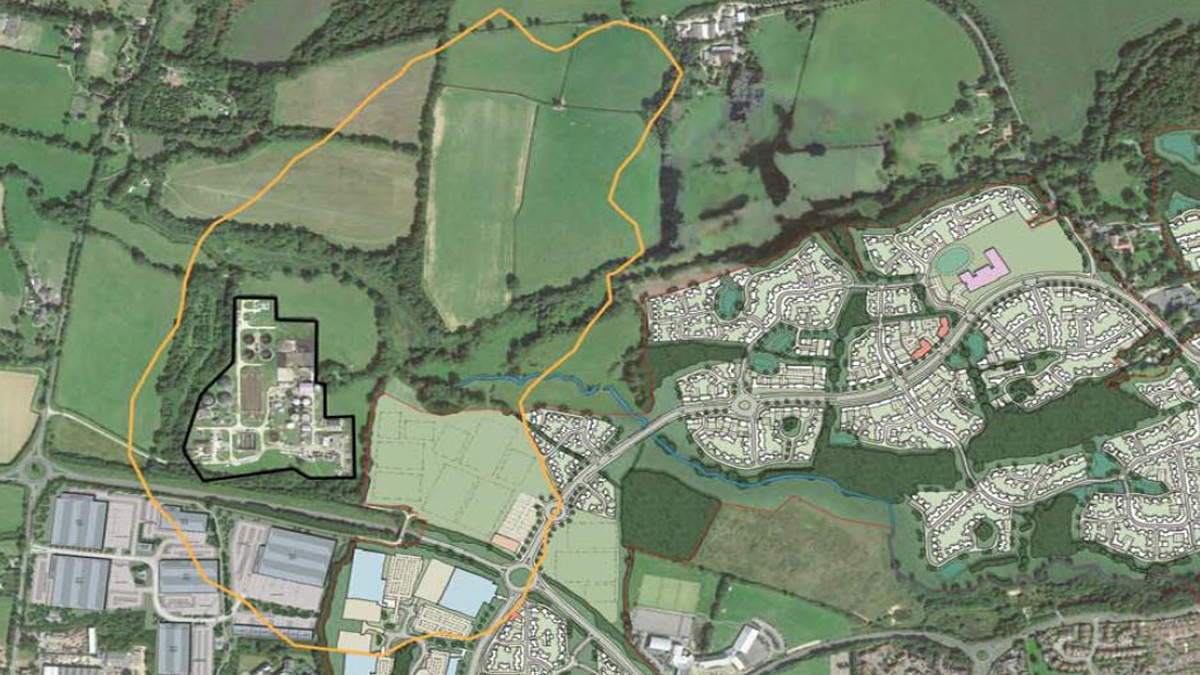
Odour model emission contours for selected solution – Google Maps
Project synopsis
This scheme is being delivered in two phases. Phase 1 was delivered in May 2020 with the installation of a new odour control unit and odour covers to reduce odour emissions at the site. Phase 2 comprises the installation of a thermal hydrolysis plant (THP) with associated equipment, provision of a cake reception building to control odour during deliveries and a cake barn to protect the product from the weather.
The THP will reduce odour emissions from the sludge treatment process, improve sludge quality and enhance gas yields from the digesters.
The outcome will mean that new housing developments in the area will be better protected from odour emissions. Output of the THP process will provide enhanced treated sludge for farmers to spread to land as well as greater green energy production from the existing CHP engine, reducing the site’s need to draw power from the National Grid.
Funding
Mid Sussex District Council, in collaboration with Southern Water and West Sussex County Council, successfully secured government funding of £10.54m under the Local Enterprise Partnership (LEP) Growth Deal (Programme) and the Homes England Housing Infrastructure Fund.
Southern Water has invested an additional £17m to deliver the odour and sludge treatment upgrade project.
Phase 1 scope
Phase 1 was delivered in May 2020 and comprised the installation of a new odour control unit and odour covers to reduce odour emissions. High odour emitting existing asset sources as identified from the odour model were covered. These assets included the primary settlement tanks, liquid sludge reception tank and oxidation ditch distribution chamber.
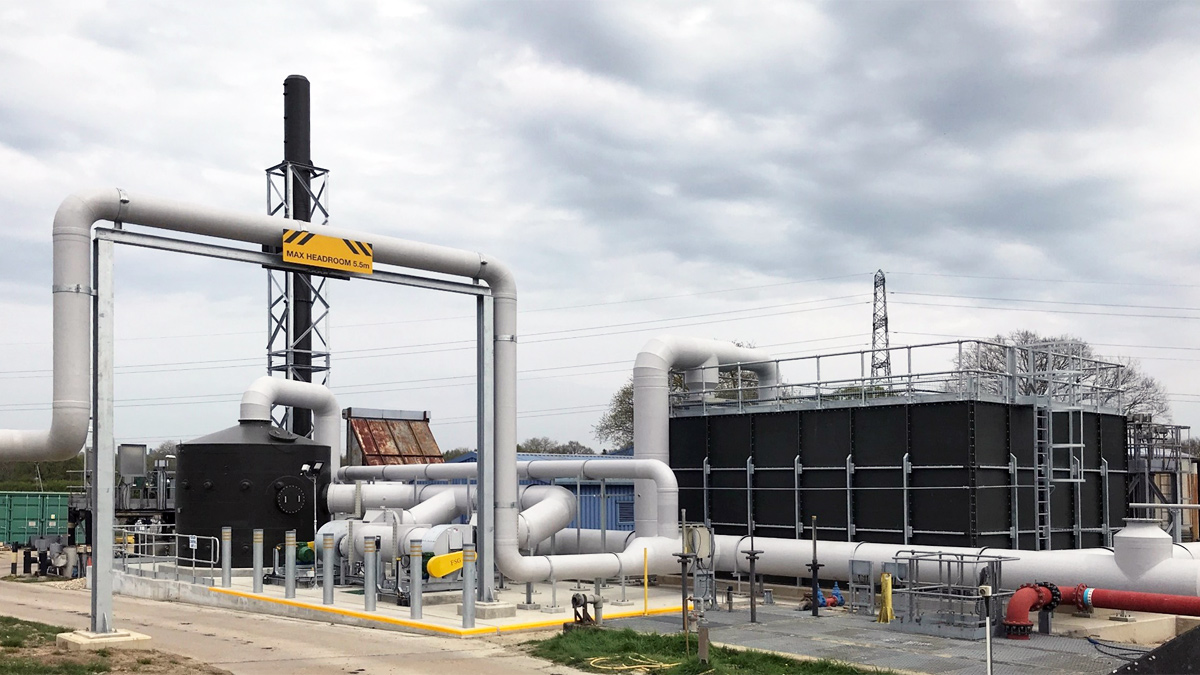
Phase 1 odour control unit from ERG (Air Pollution Control) Ltd – Courtesy of Galliford Try
Phase 2 scope
The current practice of blending imported cake with indigenous liquid sludge has been retained. The blended sludge is then screened using existing strain presses and thickened using existing drum thickeners. New centrifuge feed pumps have been installed to feed thickened sludge to the existing centrifuges – these were previously used for digested sludge dewatering but have been repurposed to produce raw cake for the new THP process.
Conveyors transfer the dewatered sludge to duty/standby cake hopper pumps which deliver raw cake to a 130m3 cake storage silo. Cake from the silo is discharged to duty/standby hopper pumps where dilution water is added to achieve a target dry solids content of 16.5% DS in the THP feed sludge.
A single Cambi B2-4 THP stream is provided, capable of processing up to 24 tDS/d. The first vessel in the THP is the pulper which homogenises and pre-heats the sludge. Pre-heated sludge from the pulper is fed to the reactors in a sequential process that ensures sealed batches of sludge in each reactor.
Steam is injected to raise the temperature of the sludge in the reactor to 165°C at a pressure of about 6 bar. At the end of the hydrolysis period, hydrolysed sludge is discharged from the reactor to the flash tank, which operates at about 0.2 bar. The sudden drop in pressure ruptures any remaining biological cells in the sludge. Flash steam generated by the pressure drop is returned to the pulper to preheat the incoming sludge.
Thermal hydrolysis of sludge generates a highly odorous off-gas (referred to as ‘process gas’) which is continuously extracted from the pulper and passed through a cooler, with condensate from the cooler gravitating back into the pulper. Non-condensable gases pass from the cooler to the process gas unit where they are pressurised and injected into the digester feed lines (downstream of the sludge coolers).
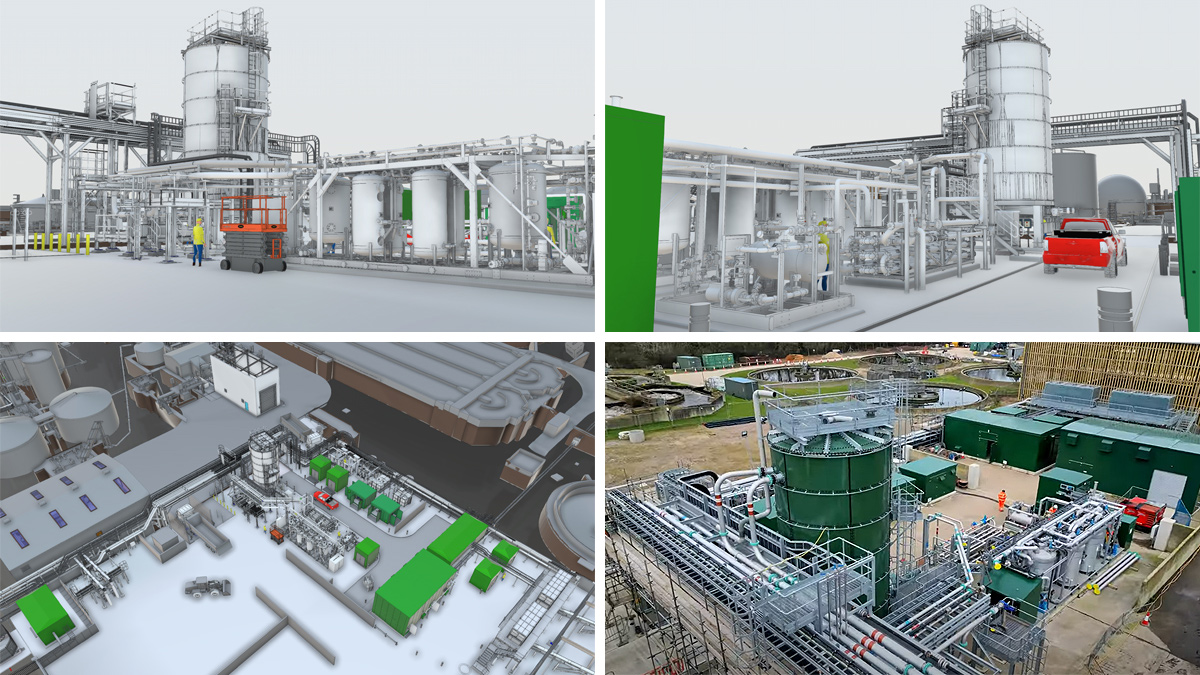
(top & bottom left) BIM models showing the THP plant area and (bottom right) Phase 2 THP area looking north-west – Courtesy of Galliford Try
Digester feed pumps are used to pump hydrolysed sludge from the flash tank to the digesters. Disinfected process water is added to the suction side of the digester feed pumps to dilute the hydrolysed sludge to achieve the target digester feed sludge dry solids content.
Diluted hydrolysed sludge is combined with recirculated digested sludge before being cooled while passing to the two existing digesters.
The new digested sludge dewatering stage comprises new duty/standby centrifuges and an associated polymer preparation/dosing system. Enhanced treated cake is conveyed to the new cake barn.
There is an existing 800 kW CHP engine. High grade waste heat from the CHP engine exhaust gas is recovered in a new composite steam boiler. Low grade heat is also recovered from the CHP engine jacket cooling water and used to pre-heat the boiler feed water. These heat recovery systems help to minimise the consumption of supplementary fuel (biogas or diesel) required to meet the THP steam demand.
A new final effluent (FE) pumping station supplies cooling water to the sludge coolers. All applications requiring dilution or carrier water are supplied with filtered FE that has been UV-disinfected, ensuring that an enhanced treated cake is produced.
The schematic diagram below shows the process stages with the additional odour reduction measures undertaken in Phase 1 (in green) and the main changes to the sludge treatment process for Phase 2 (in orange).
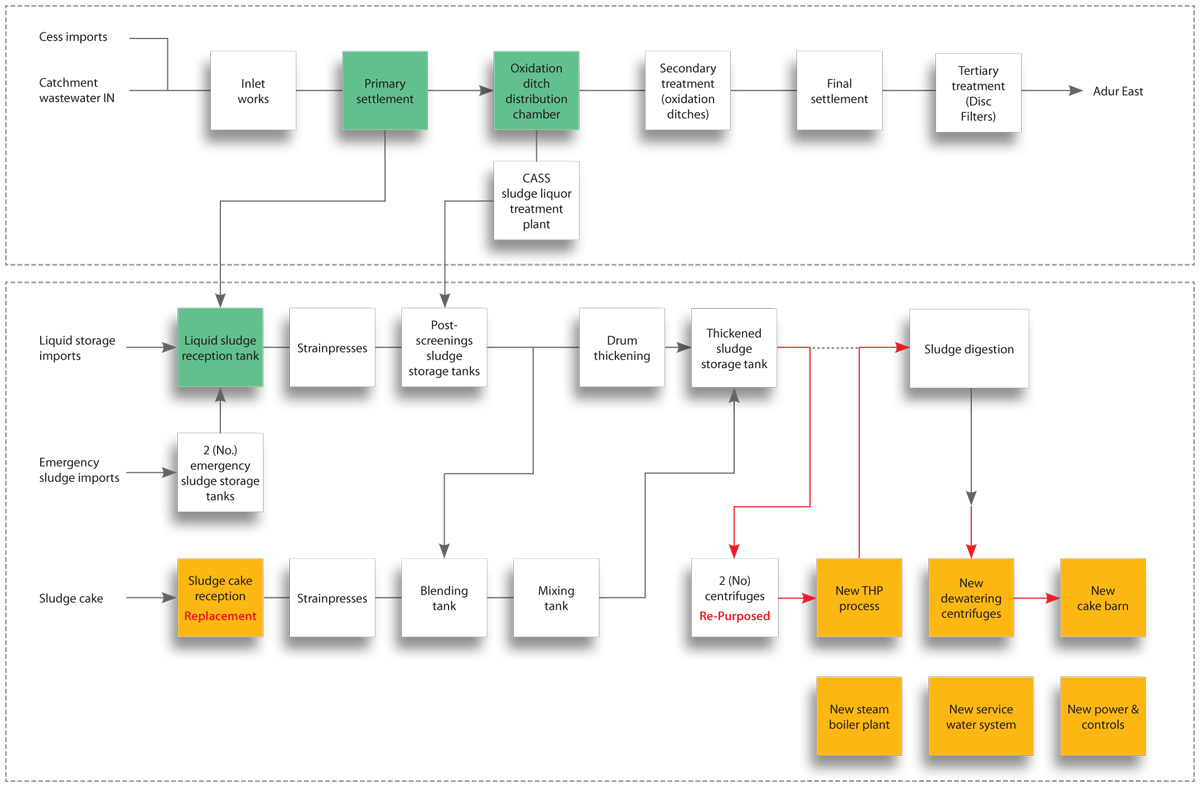
Schematic showing the process stages – Phase 1: Additional odour reduction measures (green) and, Phase 2: The main changes to the sludge treatment process (orange)
Design
Galliford Try’s (GT) inhouse engineering team based in Stafford, have undertaken and coordinated the detailed design process, supplemented by specialist suppliers. Atkins were also contracted to undertake the civil engineering design on behalf of Galliford Try. Southern Water carried out the process design. Regular design coordination meetings have been held between all parties to ensure a coordinated approach to the design.
3D and Building Information Modelling (BIM) modelling has been used throughout the scheme to coordinate and manage the design process. Viewpoint for Projects was used as the project’s cloud-based collaboration tool throughout. The use of 3D modelling was particularly useful in spotting clashes and to enable early process plant operator involvement and feedback. This has been beneficial in highlighting access and maintenance issues, prior to construction work beginning.
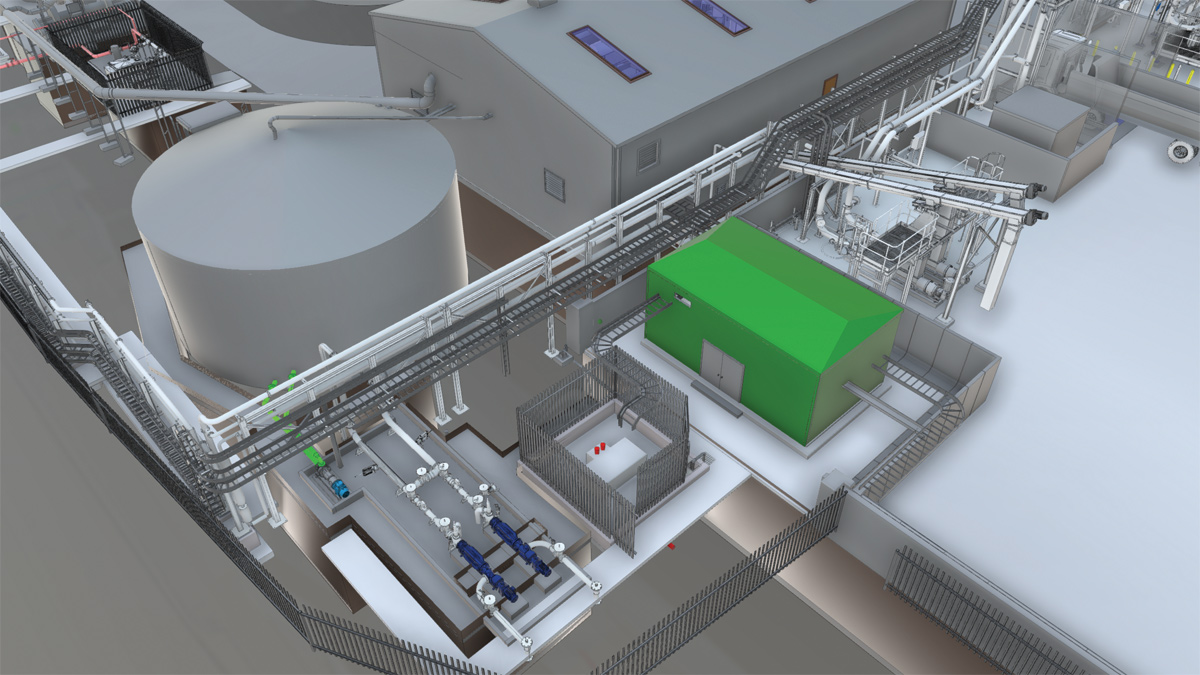
View looking at Serpecon conveyors and pre-THP silo feed pumps – Courtesy of Galliford Try
Goddards Green WwTW – Supply chain: key participants
- Client: Southern Water
- Main contractor: Galliford Try
- Outline design: Stantec UK
- Detailed design: Atkins
- THP plant: Cambi AS
- Cake reception building/cake barn: APT Engineering Ltd
- Imported cake reception silo: Saxlund International Ltd
- Steam boiler package: Dunphy Combustion Ltd
- Groundworks drainage: TC Jones Groundworks
- Concrete cutting/diamond drilling: Castle & Pryor Ltd
- Workforce supply: Hercules Site Services
- Workforce supply: Fortel Group
- Kiosks: Morgan Marine
- UV Treatment: Xylem Water Solutions – Wedeco
- FE booster set & portable water booster set: KGN Pillinger
- Pre-THP centrifuge screw conveyors: Serpecon Ltd
- Vehicle exhaust: Air Technology Systems
- CHP exhaust flue: Rung Heating
- CHP pipework modifications: Edina UK Ltd
- MCCs: Blackburn Starling Ltd
- LV Switchboard/MCC 10: MCS Control Systems Ltd
- Final dewatering units & access platform: Alfa Laval
- Biogas booster system: DSL Building Services
- Final dewatering polymer system (powder): Richard Alan Engineering
- Mechanical/electrical installation: Field Systems Design Ltd
- Submersible centrifugal pumps: Xylem Water Solutions – Flygt Pumps
- Concrete: Hanson Aggregates
- Muck-away: Hesus UK Ltd
- Sub-base materials: Day Group Ltd
- Drainage materials: Jewson Civils Frazer
- Heat exchangers: HRS Heat Exchangers Ltd
- Reinforcement: Hy-ten Ltd
- Pumps: P&M Pumps Ltd
- Draeger control units: Draeger Safety UK Ltd
- DS monitors: Flow Technology Services Ltd
- Valves & instruments: ABB Ltd
- Valves & instruments: Siemens
- Valves & instruments: Glenfield Invicta Ltd
- Valves & instruments: Xylem Water Solutions
- Instrumentation: IFM Electronic Ltd
- Performance monitoring & operational support: PBJ Engineering Services Ltd
- Supply of steam boiler water treatment chemicals: EB Critical Engineering Services Ltd
Construction
Construction of the Phase 2 works commenced in the spring of 2021 with the clearing of existing cake bays and the construction of new openings to the existing structure. Castle & Pryor Ltd undertook the work to create new openings, utilising track saws and robotic demolition techniques. The decision for this technique was taken to minimise the health and safety risks associated with more traditional demolition methods.
Once the new openings were formed, Galliford Try went on to construct new foundations to accommodate the new process units. Hercules Site Services and Fortel Group were engaged to supply the necessary skilled workforce to work directly under Galliford Try’s own control.
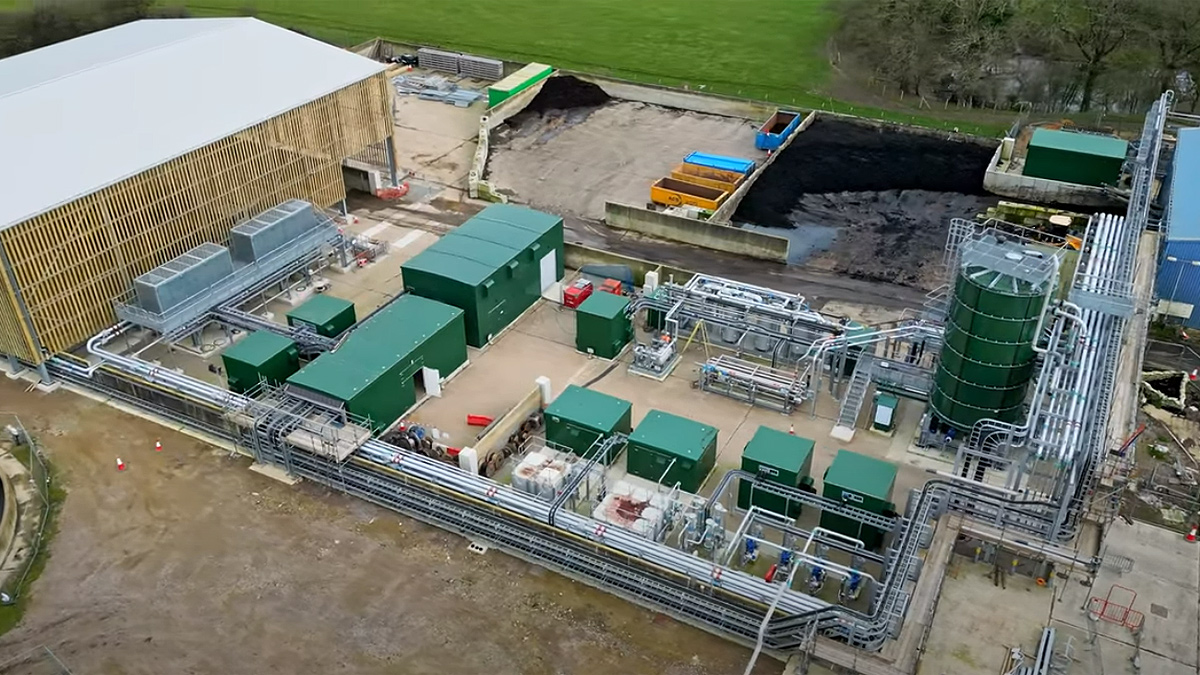
THP area looking north east – Courtesy of Galliford Try
This approach has proved successful throughout the first three years of the current programming AMP7 period (2020-2025) as it affords greater flexibility and control. Wherever possible the existing structure was retained and re-purposed to speed up the construction, and to reduce overall costs and the carbon footprint of the scheme. Before reusing the foundations, detailed in situ and pull-out testing was undertaken. The Cambi B2 unit and associated ancillary equipment are all located within the original cake drying beds.
In parallel to the cake bay works, construction was undertaken within the existing plant to facilitate the installation of the other process units. This required close collaborative working between the contractor and the onsite operations team, to minimise disruption to day-to-day activities and the running of the treatment plant. Throughout the scheme, this close cooperation has continued, ensuring all stakeholders are kept up to date with activities and progress.
Field Systems Design Ltd was engaged by Galliford Try to undertake the detailed design and installation of the complex interconnecting cabling and mechanical piping systems throughout the scheme. This included high voltage cabling and transformer upgrade works, low voltage power cables, signal cables and fibre optic networks. The scope of the mechanical supply included all piping and access arrangements, steam lines and pressure networks.
In total, 48 kilometres of cable, 2.5 kilometres of pipes and associated support systems have been installed. These systems are predominantly placed above ground for ease of future maintenance, and to mitigate the risks of burying equipment within an already congested plant. Collaborative planning and design management have been undertaken between the site team and Galliford Try, to ensure the smooth flow of the mechanical and electrical phase of the works.
Overall, the scheme is now (June 2023) approaching 200,000 hours worked without any lost time or other significant incidents.
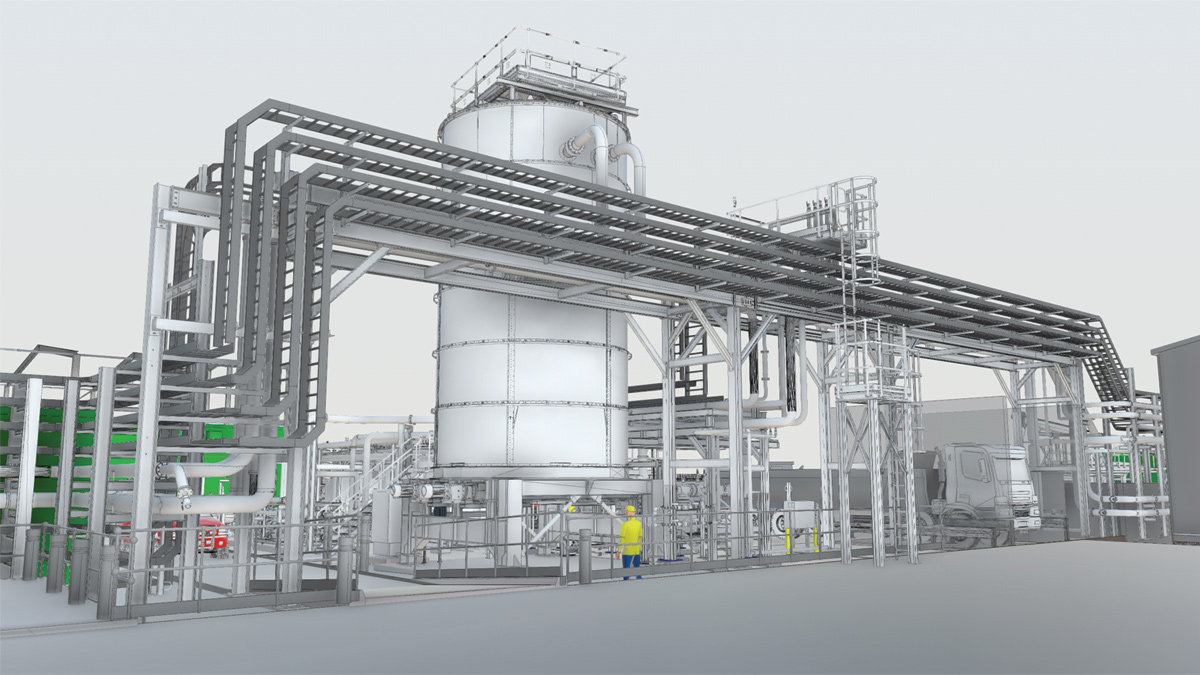
View looking north-east towards the Saxlund pre-THP cake silo – Courtesy of Galliford Try
Risk management
De-risking of the construction phase was considered key to the delivery of project. To achieve this, regular risk reviews and workshops have been undertaken throughout with significant benefits being realised.
For example, the project team identified early on that Southern Water were best placed to deliver the improvements to the existing on site gas storage facility and flaring arrangement in advance of the main Phase 2 works starting. It also identified the need to procure longer lead-in items in advance of the main contract award being in place. This meant that the Cambi B2 unit, Dunphy boiler building, and Saxlund pre-THP silo were all procured under an early works agreement.
This joined up approach to risk management meant that the scheme was able to rapidly adapt to the challenges posed by the worldwide semi-conductor shortage. The shortage affected the project, due to the multiple control panels and complex equipment being procured. The team agreed to utilise refurbished parts within the panels to enable off-site fabrication and factory testing to take place. These refurbished parts will then be replaced on site once the delayed components become available, which has saved many weeks of further delay.
Stakeholder management
As Southern Water had obtained funding from Homes England to undertake the odour reduction scheme at Goddards Green, they were identified by the project team as key stakeholders. It was therefore essential that they were kept informed of progress throughout the delivery phase. To achieve this, the project team held regular site tours and liaison meetings with the representatives of Homes England and the local council members, fielding questions and explaining the process and progress on site.
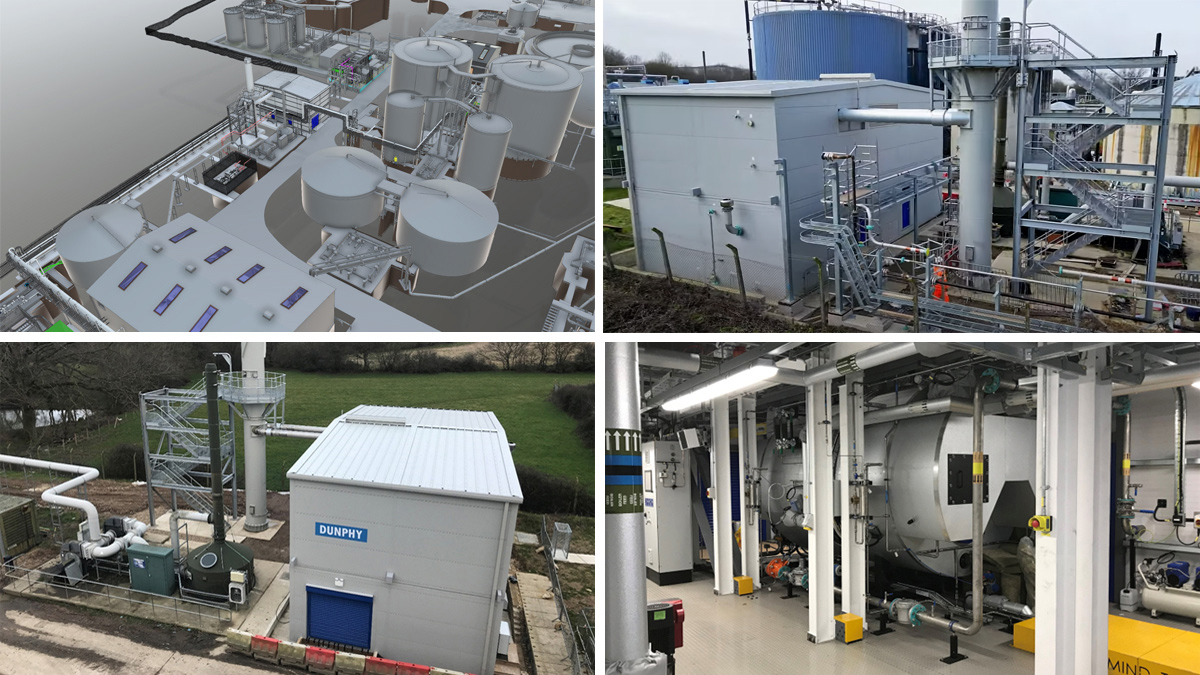
(top left) BIM model showing the steam boiler system, (top right) the rear of the steam boiler building and emissions stack, (bottom left) the front of the steam boiler building and emissions stack, and (bottom right) the Dunpy boiler package – Courtesy of Galliford Try
DfMA – Design for Manufacture and Assembly
Design collaboration from the earliest stages of the project has provided tangible benefits in terms of costs, speed, sustainability of the project, and health and safety benefits. These small but practical examples are a core part of Galliford Try’s sustainable growth strategy.
Galliford Try’s installation of the steam boiler at Goddards Green WwTW using an off-site solution, has reduced construction time on site as well as bringing health, safety, carbon, and community benefits. Manufactured and installed by Dunphy, the modularised plant room was fully fired and tested off site before delivery in two days using DfMA to allow modular construction of the building and plant, reducing the amount of time spent on site during the installation. The reduction of time spent working on site also has health and safety benefits, as more work is completed in a safer factory setting, and many of the hazards of a live site can be reduced or avoided.
Conclusion
At the time of writing (June 2023) the Goddards Green WwTW project’s construction phase is nearing completion and commissioning works have commenced on ancillary equipment. Beneficial use is currently forecast for the end of 2023. The use of THP is the first of its kind within Southern Water. Therefore, despite being utilised to manage odour, it will also alter the way the sludge is managed on site, contributing to several economic and environmental benefits.