Guildford STW (2024)
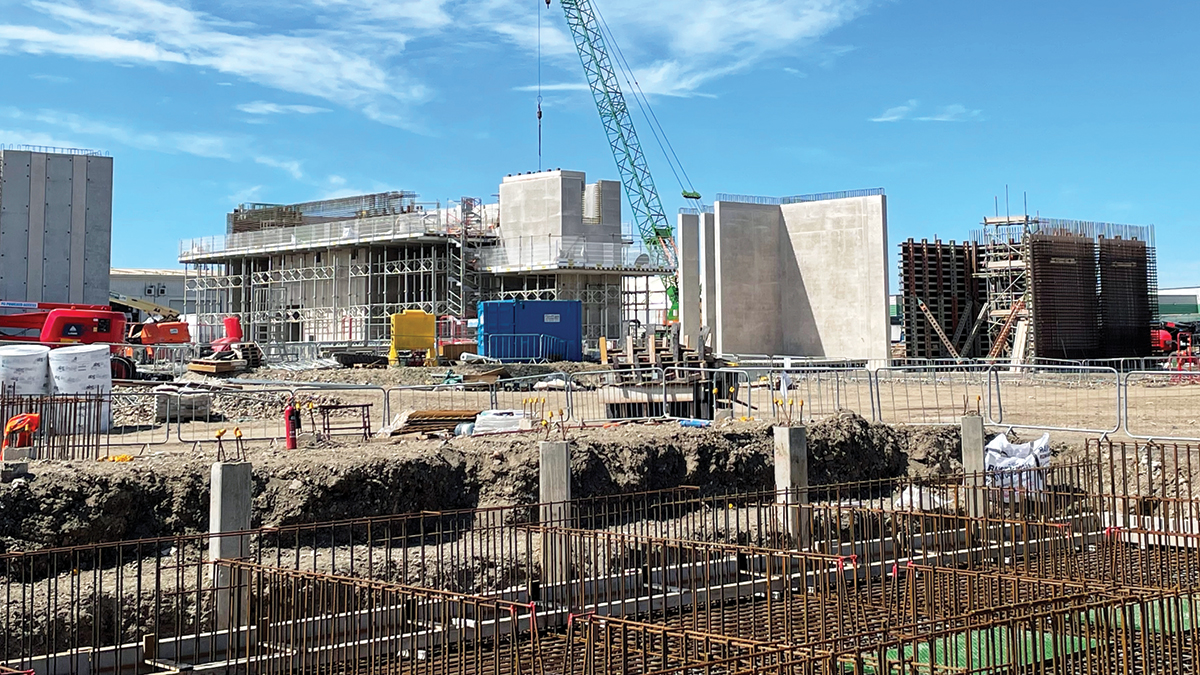
Construction of the high-level inlet works structure - Courtesy of Bam Nuttall Ltd
Guildford town and the surrounding residential areas are currently served by an existing sewage treatment works (STW) located adjacent to the River Wey, just north of the town centre. The land which this occupies has been identified as part of the Slyfield Area Regeneration Project (SARP), which includes the new Weyside Urban Village (WUV). This mixed-use regeneration project will include circa 1,500 new homes, new community facilities and 6,500m2 of commercial space to improve the local area. Thames Water Utilities Ltd (TWUL) is working in partnership with Guildford Borough Council (GBC) to move the STW to a new location, which is not suitable for housing.
The location chosen is on the north-east extent of the existing Slyfield Industrial Estate and is on an area previously used as a landfill site. In August 2023 Water Projects published a case study which provided insight into the extensive pre-construction design for civil and process engineering elements of the project. This article delves into the construction of the project and provides an update on the significant progress made to date on site.
Site historical use
The site for the new STW is approximately 70,000m2 and was previously used as a landfill site. It had originally been used as sand and gravel quarries and then subsequently used as landfill from the 1960s to the 1980s.
The landfill material is generally domestic and light industrial. It consists of black bag waste, timber, plastics, fabrics but contains fragments of asbestos and other materials.
The site was capped off with a granular layer in the early 1980s and has laid dormant ever since. The landfill depth varies across the site from between 2m and 6m thick. This then overlies an alluvium layer, sands and gravels and London Clay. The depth of the London Clay is approximately 10m below existing ground level.
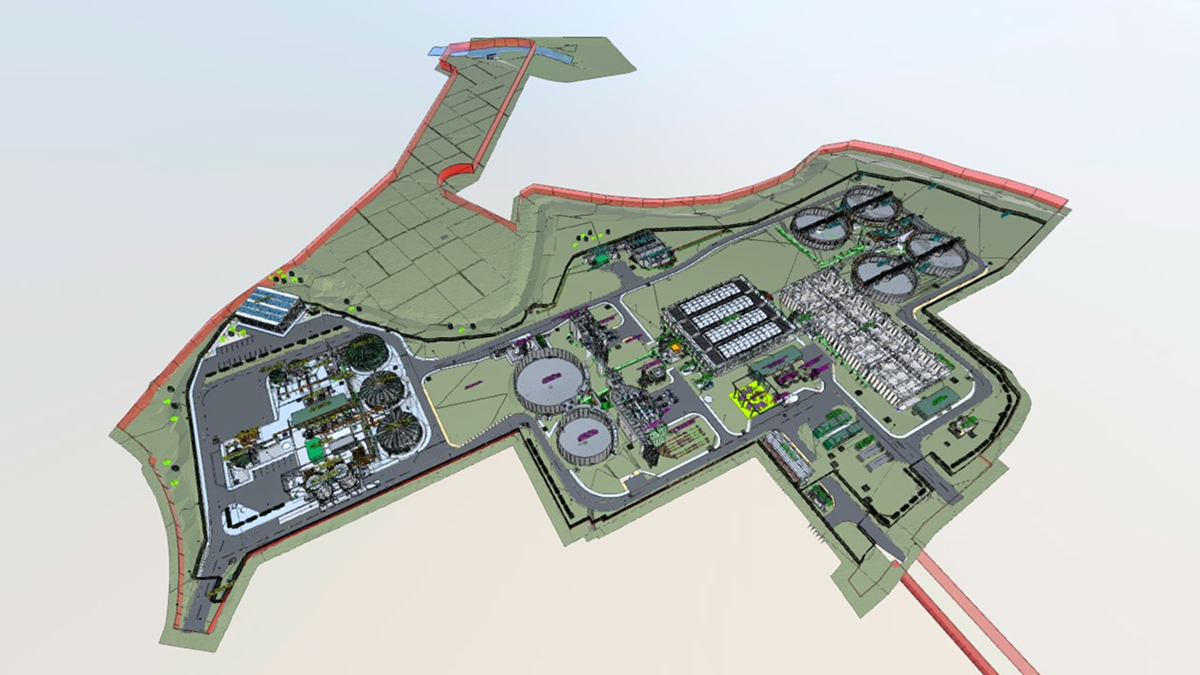
A screenshot of the 3D model used for design and construction – Courtesy of Bam Nuttall Ltd
Civil engineering: Basis of the design
Typically, major structures within a sewage treatment works are built below or partially below ground level to maximise gravitational energy. The new Guildford STW differs in that the strategy is to deliberately design and build above ground as far as practicable.
This is to minimise the disturbance to, and removal of the existing landfill thereby reducing the impact on the environment and the cost of disposal.
Undertakings
After a period of Early Contractor Involvement, Thames Water awarded a contract to BAM-Enpure Joint Venture (BEJV) in 2021 to design, build and commission this significant new works and once operational, to de-commission the existing works.
BEJV is a non-integrated joint venture, formed specifically to combine the excellence of experienced civil engineering contractor Bam Nuttall Ltd and the process engineering/MEICA specialism of Enpure Ltd to deliver a turnkey solution for Thames Water. The workscope split is as follows:
Bam Nuttall Ltd: Civil engineering workscope
- Principal contractor
- Civil engineering design
- Ground stabilisation & piling
- Structures
- Underground pipework
- Tunnels, shafts and connections
- Buildings
- Outfall pipeline & structure
- Roads, fencing & general civil engineering works
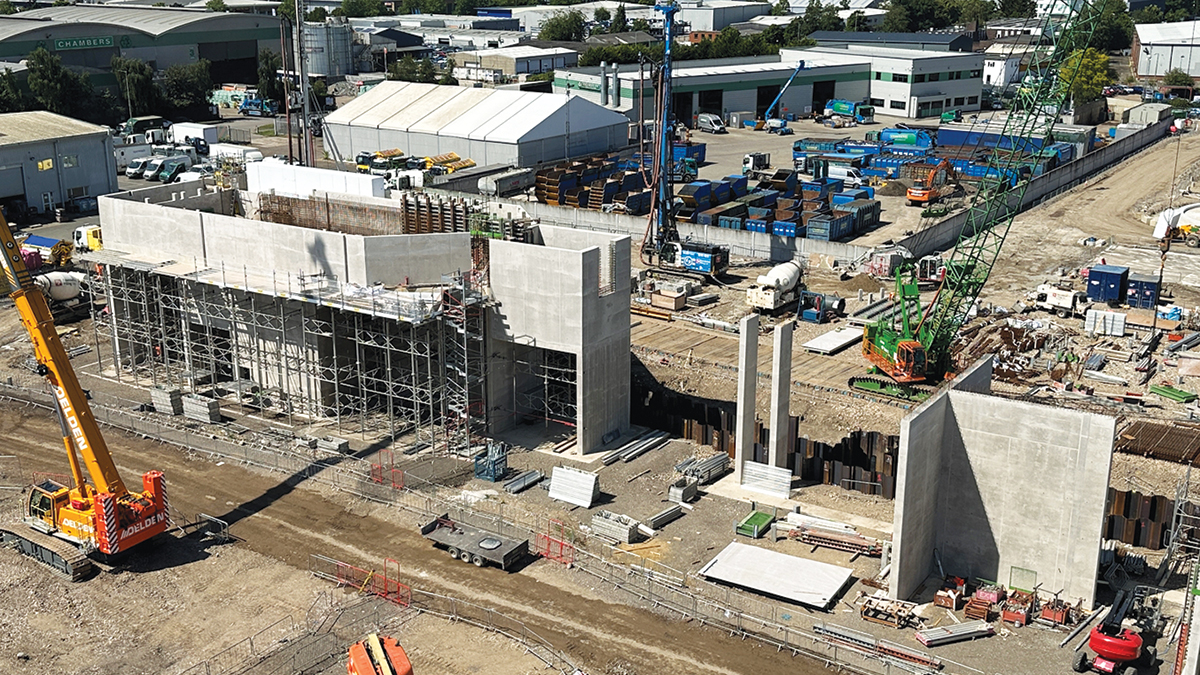
Construction of the high level inlet works structure – Courtesy of Bam Nuttall Ltd
Enpure Ltd: Process engineering/MEICA workscope
- Principal designer
- MEICA design
- Process design
- Mechanical works
- Electrical works
- Control systems
- Commissioning
Decommissioning of the existing STW will also be undertaken by BEJV, in addition to working collaboratively with TWUL operational and networks teams to integrate existing TWUL operational assets into the new sewage treatment works.
Site trials
BEJV undertook a series of site trials in 2021/2022. The purpose of this was to investigate the proposed ground improvement techniques further in order to validate proposals and inform detailed design. There are a combination of techniques which interface with each other in a complex manner.
The trials also gave important information about potential effects to both leachate levels and ground gas within the existing landfill to ensure there would be no impact on environment, ecology and human health.
Four trial areas were chosen, to provide a variety of conditions and in each of these areas a set of boreholes was established at increasing offsets away from the trial areas. These boreholes contained monitors for both leachate levels and ground gas volumes and were monitored 24/7. In addition, noise and vibration monitoring was also undertaken.
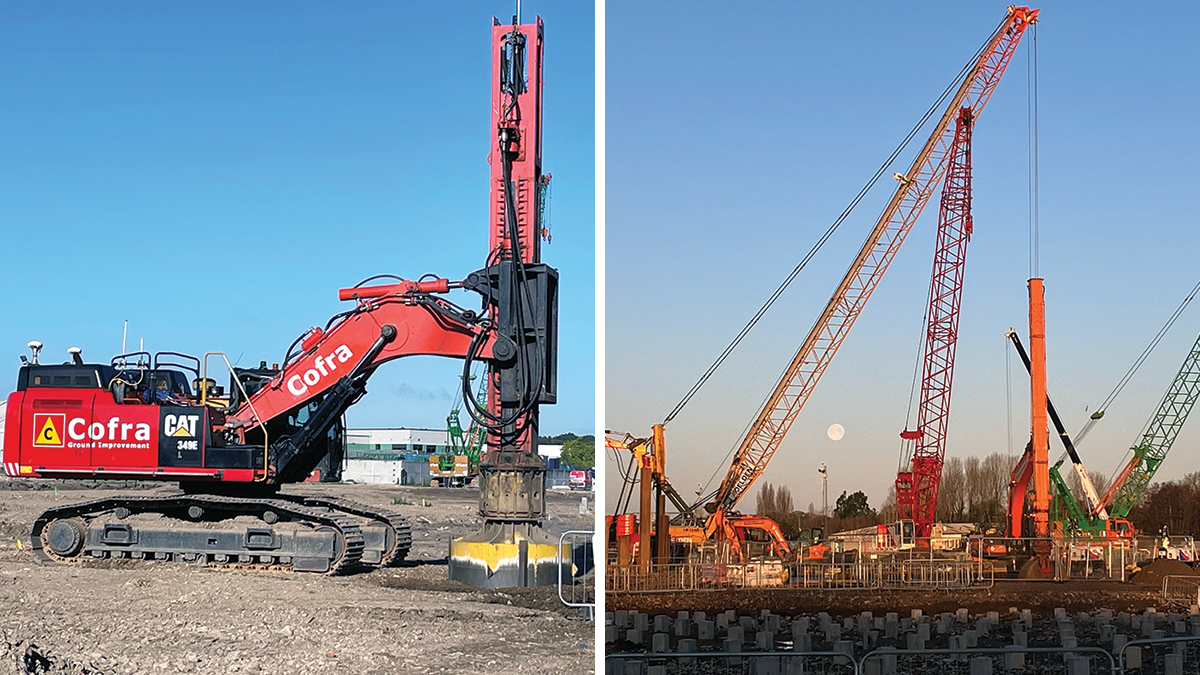
(left) Rapid impact compaction underway and (right) a selection of site plant in use – Courtesy of Bam Nuttall Ltd
The three techniques tested, and subsequently used within the works were as follows.
1. Rapid impact compaction (RIC): RIC was undertaken to remove the risk of long-term settlement to the landfill. Whilst the main structures would be supported on piles, this was to remove the risk of long term ground settlement underneath and around the structures. RIC is a method of imparting energy to the ground using a repeated but relatively short drop-weight, where a base plate is in constant contact with the ground. It is undertaken on a pre-determined grid pattern. At Guildford a 9T hammer was chosen, fitted to a 35T base machine and working on a 2.5m x 2.5m grid. Each ‘pass’ of the technique used 40 blows at each point.
Within the trial areas the technique was tested with 1, 2 or 3 passes (ie, 40, 80 or 120 blows per location). Cone penetrometer tests were used to measure the extent of deep level ground compaction before and after the trials. The continuous monitoring from the boreholes demonstrated that at each ‘thump’ of the ground there was no discernible change in leachate levels or ground gas volumes, and that there was no dispersal of leachate happening throughout the landfill.
From the trials it was determined that all areas of the site that are being built on should receive either 1 or 2 passes of RIC for the permanent works.
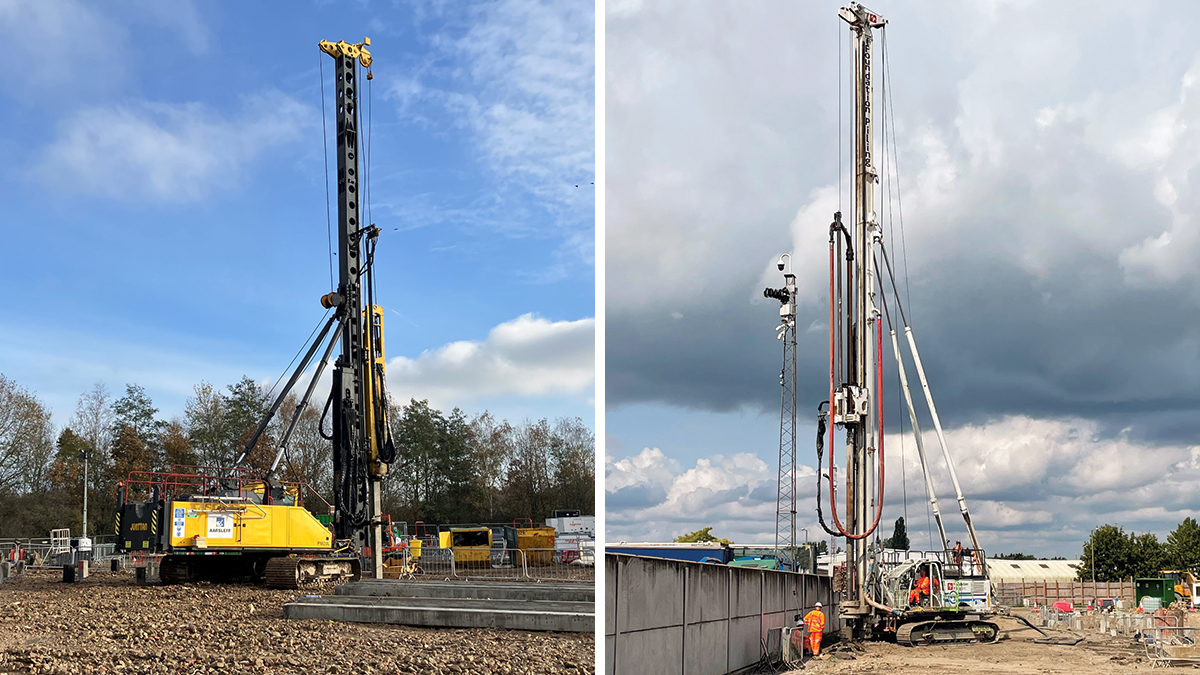
(left) Driving precast concrete piles and (right) vertical rigid inclusion installation – Courtesy of Bam Nuttall Ltd
2. Precast driven piling: The main structures and pipelines are founded on precast driven piles. These are end-bearing into the London Clay, approximately 10m below ground level. Precast driven piles were chosen as the solution as the operation does not bring any landfill to the surface. Various size piles were driven to various depths and tested with both dynamic and static tests. Borehole monitoring showed that there was no discernible change to leachate and ground gas levels and that there was no dispersal of leachate happening throughout the landfill.
3. Vertical rigid inclusions (VRI): VRIs are mass concrete piles which are used for lightly-loaded structures and areas such as roads and hardstandings. They are a displacement pile, with the surrounding soil pushed sideways by an auger. As the auger is withdrawn the resulting void is filled with concrete up to ground level. They therefore work by increasing the density of the ground. A granular layer is then installed above to remove any ‘hard spots’. Again, this technique does not bring landfill material to the surface. It was trialled in two areas and found to be suitable for use, without causing any effects to leachate levels or ground gases. It is therefore being used as part of the permanent works over the whole site wherever there are not piled structures.
The trials of all three techniques, together with the subsequent site testing proved that the design principles were correct, and gave information on how to refine the solutions further. It also demonstrated that the techniques would not cause any adverse environmental effects.
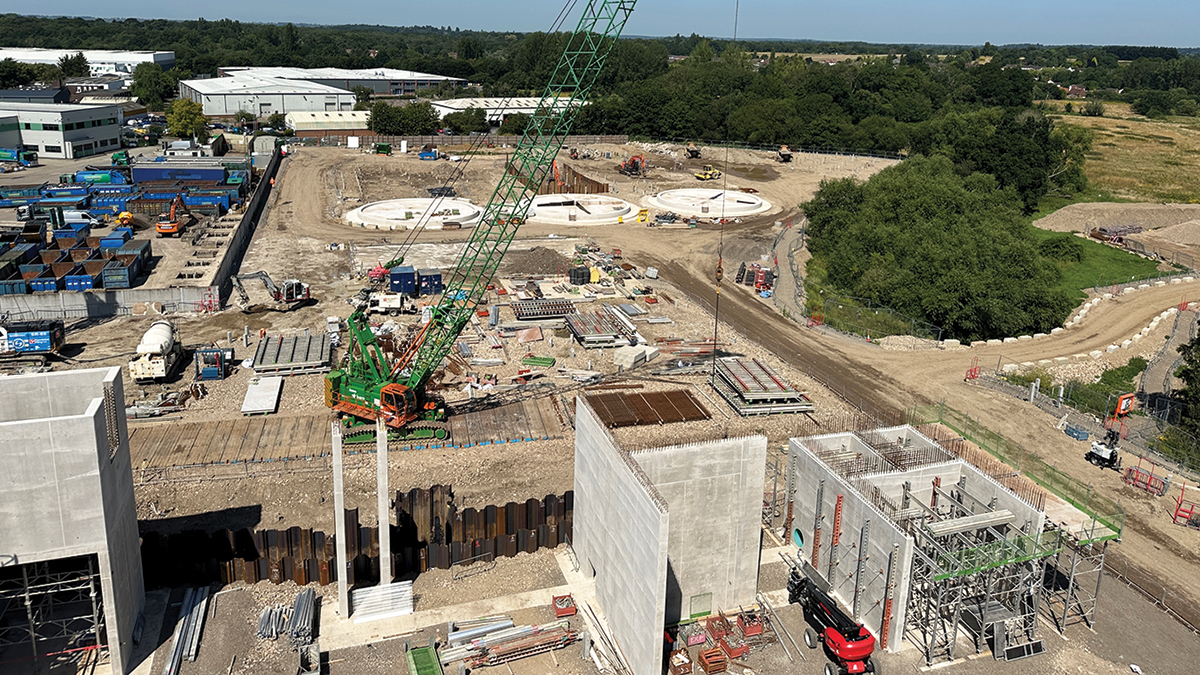
(foreground) Ferric mixing and flocculation chambers and (background) concrete bases for sludge tanks – Courtesy of Bam Nuttall Ltd
Guildford STW: Civils works supply chain – key participants
- Main contractor: Bam Nuttall Ltd
- Planning consultant: Adams Hendry Consulting Ltd
- Civil engineering design: Arcadis Group Ltd
- Boreholes & testing: Geo-Environmental Services Ltd
- Asbestos monitoring: Socotec Ltd
- Rapid impact compaction: Cofra Ltd (Boskalis Group)
- Vertical rigid inclusions: Foundation Piling Ltd
- Concrete piling: Aarsleff Ground Engineering Ltd
- Temporary works specialist: Mabey Hire Ltd
- Temporary works specialist: MGF Ltd
- Tunnels & shafts: Joseph Gallagher Ltd
- In situ concrete works: Kelly Formwork Ltd
- Precast concrete works: DJ Civils Ltd
- Precast concrete manufacturer: FLI Precast Solutions
- Precast concrete manufacturer: A-Consult Ltd
- Soil processing: Remediation Waste Management Services
- Concrete supplier: Heidelberg Materials
- Gas protection: PAGeo Contracting Ltd
- Crane supply: Delden Cranes
Enabling works
Enabling works took place during Spring 2023 and consisted of site clearance, setting up the site offices and welfare and establishing fencing. The whole site was then covered with a 100mm thick layer of imported granular material to provide further protection against the risk of asbestos within the existing capping layer.
A series of 20 further boreholes were installed around the perimeter of the site to enable daily monitoring of both leachate and ground gas within the landfill and to ensure that none was being mobilised by our works. Mobile monitoring stations for noise, dust, vibration and asbestos were all set up, which are monitored continuously throughout the works. Over half a million data points have already been captured.
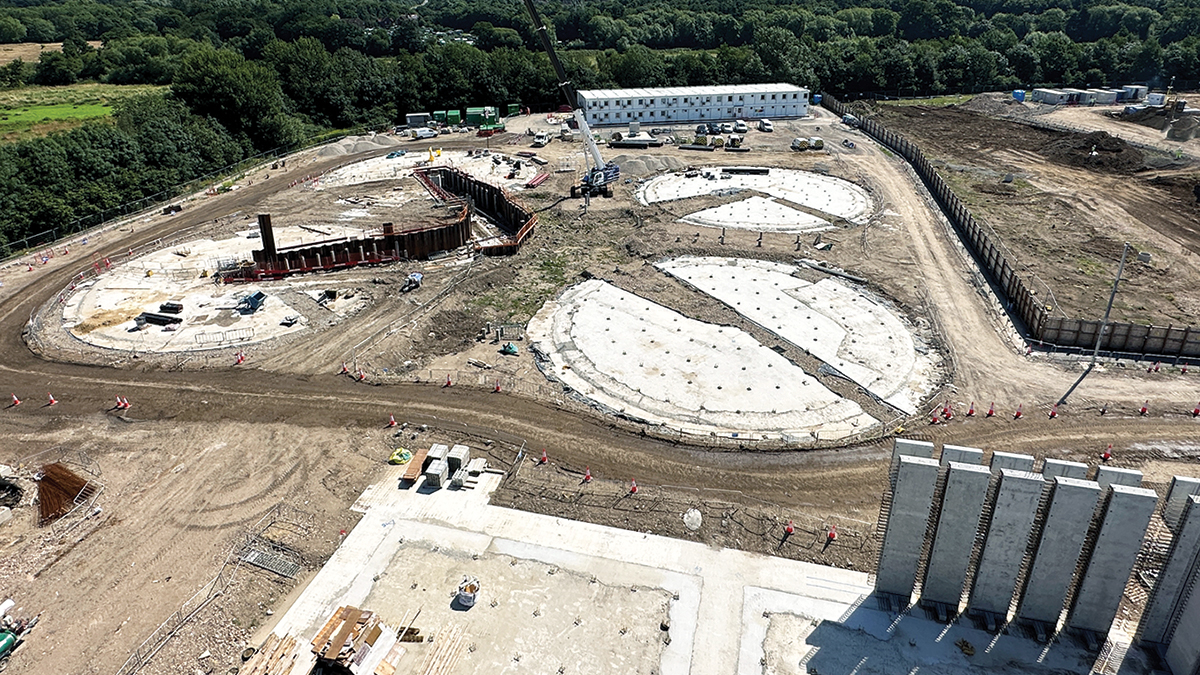
Piles and blinding concrete for the four final settlement tanks and (left) temporary ground support for pipelaying into the centre of the tanks – Courtesy of Bam Nuttall Ltd
Guildford STW: MEICA works supply chain – key participants
- Main designer/contractor: Enpure Ltd
- CFD analysis: The Fluid Group
- Cake silo: Saxlund International
- PST scrapers & ferric dosing plant: Colloide
- Inlet works & PST odour covers: Power Plastics Ltd
- Grit remover plant: Jacopa
- Escalator screens: Longwood Engineering
- Imported sludge Strainpress: Huber Technology
- Sludge thickening & dewatering: Kent Stainless Ltd
- Odour control plant: Odour Services International Ltd
- FBDA grids & blowers: Xylem Water Solutions
- Cloth pile filters: Eliquo Hydrok Ltd
- Storm tank cleaning system: Sulzer Pumps Wastewater Ltd
- Tank logging system (WASP): JR Pridham Services Ltd
- Glass lined steel tanks: Balmoral Tanks Ltd
- Sludge tank mixing: Landia UK Ltd
Groundworks and foundations
The permanent works started in earnest in Summer 2023 and in August, rapid impact compaction was conducted over the site, with a combination of one or two passes, as informed by the results of the previous site trials. In total the ground was hit 360,000 times! Precast piles were then driven for the major structures and pipelines. These were all 250mm square piles and varied in length from 16m to 20m. A total number of 3,422 piles have been driven using three piling rigs.
Vertical rigid inclusion installation is currently underway, with a total of 1,700 out of 9,000 already completed. The works are sequenced to avoid clashes with other work areas, on what is a congested site. Following installation, each work area is left for the piles to cure for the following seven days, thus effectively sterilising large areas of the site at a time. This therefore requires detailed collaborative planning on all work fronts to ensure that the site can remain operational.
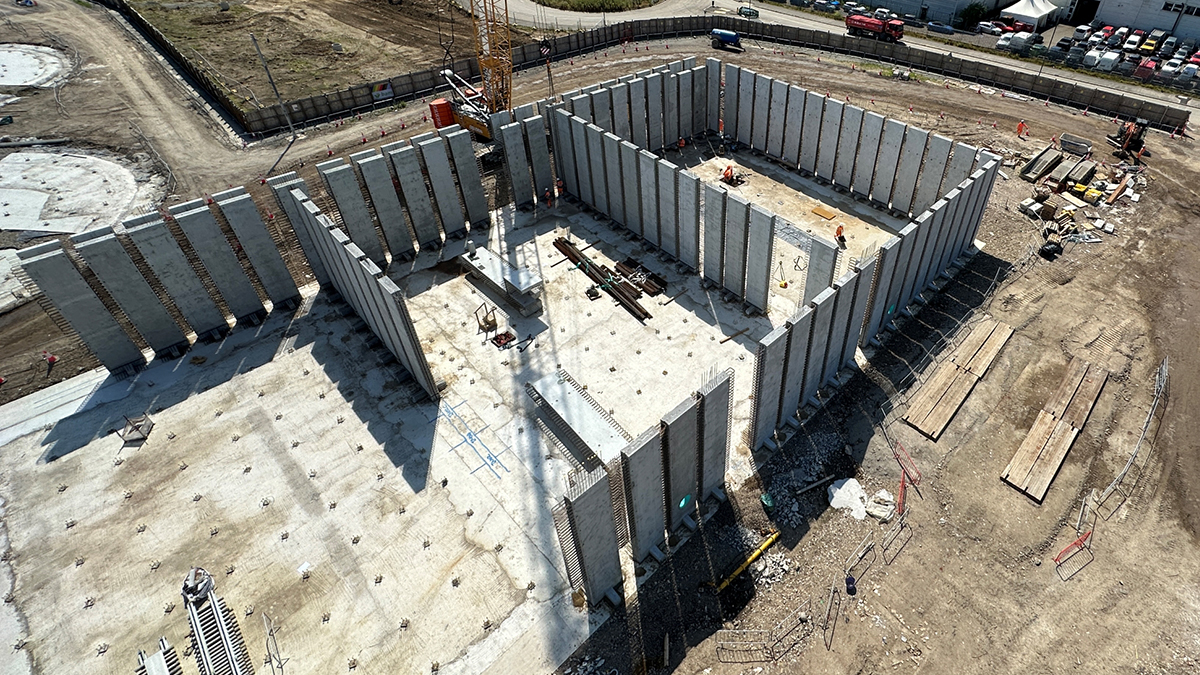
Activated sludge plant precast walls erected, prior to pouring base slab and concrete stitches – Courtesy of Bam Nuttall Ltd
Concrete structures
Of the 59 concrete structures, some are simple reinforced bases, however ‘the big 5’ are significant structures:
- Inlet works.
- Primary settlement tanks (PSTs).
- Activated sludge plant (ASPs).
- Final settlement tanks (FSTs).
- Tertiary treatment plant (TTP).
Due to the repetitive nature of their construction, BEJV chose to construct the PST and the ASP using precast concrete techniques, which are then stitched together on site. The four FSTs and two storm tanks are also being constructed using precast panels which are then post-tensioned.
The inlet works and TTP are complex, bespoke structures with very little repetition and so are more suited to traditional in situ concrete construction. The inlet works is a particularly complex structure, and is the tallest structure on site at 13m above ground level and being formed of five separate elements.
As of August 2024, the inlet works concrete structure is half complete and the TTP structure underway. The PST precast walls are mostly in place and stitched together, with roof beams now being installed. Works have also started on the ASP walls.
Pipework to the FSTs is underway, which will then allow the construction of the bases to follow on. To date (August 2024), 4,000m3 out 14,000m3 of concrete has been poured, and 205 out of 454 precast wall elements installed.
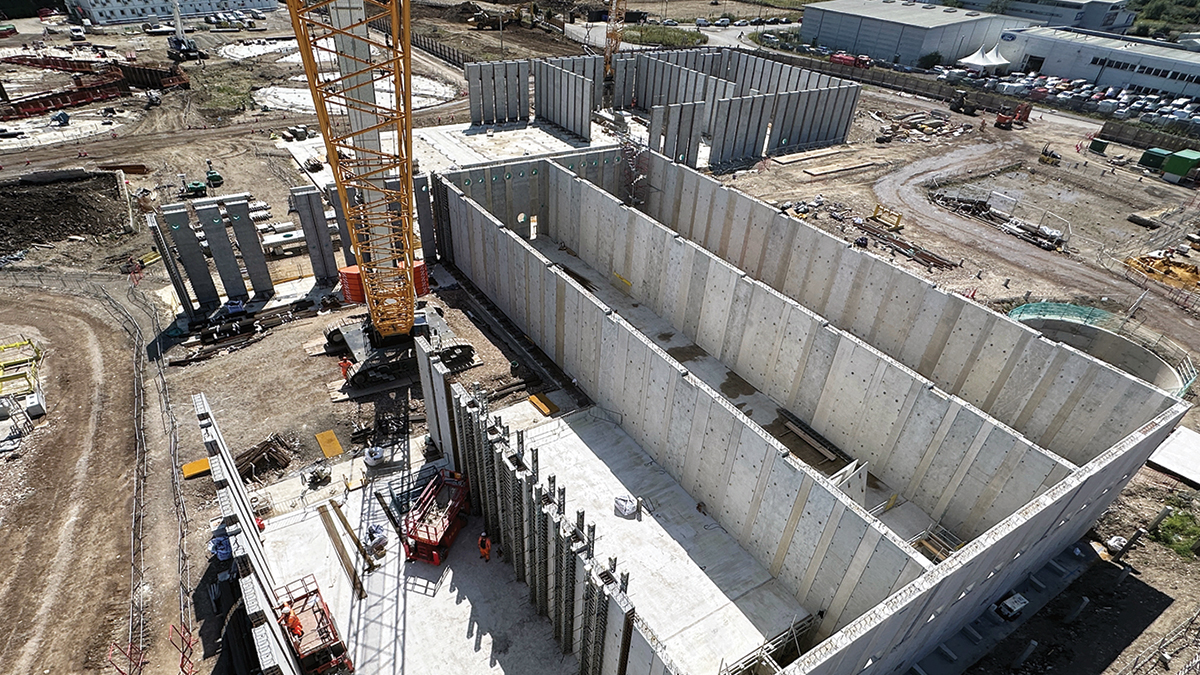
(foreground) PST precast walls with concrete stitches and bases and (background) ASP precast walls – Courtesy of Bam Nuttall Ltd
Transfer tunnel
The flows to the existing STW enter at the southern end of the works. A new transfer tunnel has therefore been constructed to intercept this and transport the flows to the new STW. This tunnel is 1.4km long, 1.5m internal diameter and flows by gravity. It is formed at an invert depth of 10.6m to 15.7m below existing ground level, entirely within the London Clay.
To construct the tunnel a series of six shafts were sunk. The largest of these is 12.5m diameter and forms the inlet shaft in the new STW. The raw sewage will then be pumped from this to the inlet works, from where it will then flow by gravity through the new STW. The remaining five shafts were used to launch or receive the tunnel boring machine (TBM) and pipe-jack, as well as being used for auxiliary connections to sewers in the existing network which don’t get picked up by the main connection.
The tunnel was constructed using the pipe-jacked method using a tunnel boring machine. This was named ‘Daphne’ in a competition by Bisley Church of England School. Daphne Jackson was the first female physics professor in the UK and taught and researched in Guildford. The tunnel consists of four straight sections, one curved section and one short hand-dug section to connect to the existing network.
Current progress is that all of the shafts have been sunk, the main tunnel is complete and fit out the shafts has commenced.
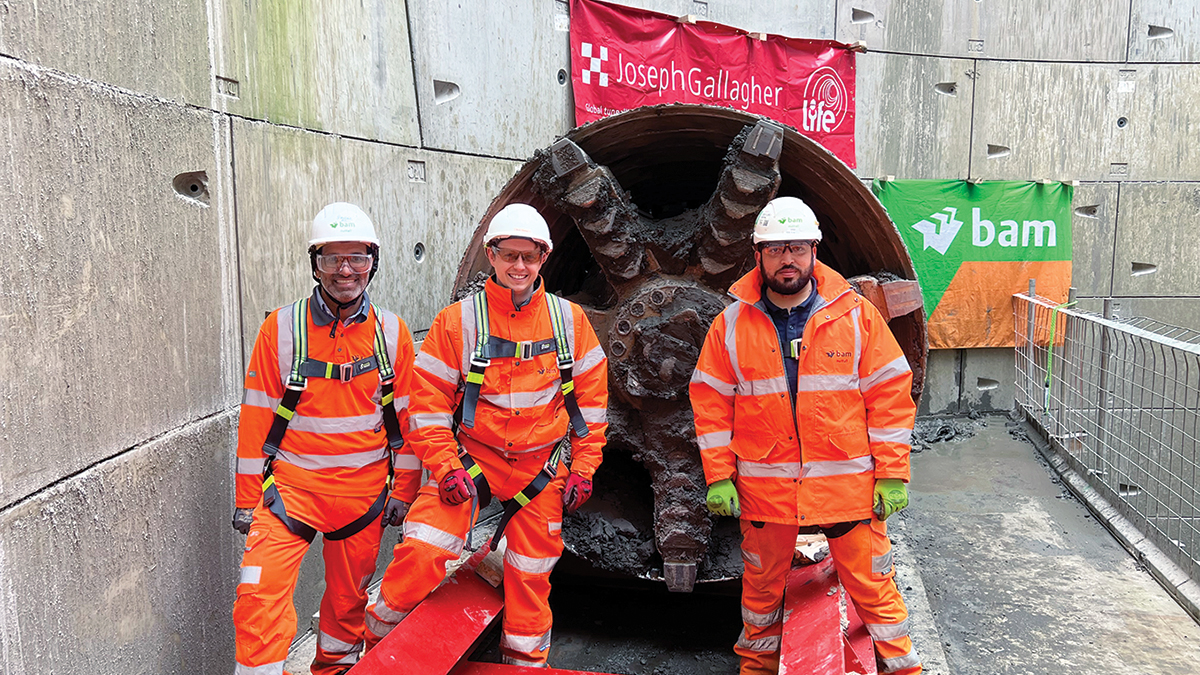
Safdar Ali, Andrew Dawes and Izhar Ahmad from the BAM team at the completion of the tunnel – Courtesy of Bam Nuttall Ltd
Outlet
The outlet for the new STW consists of a 750mm diameter pipe from the TTP and a 1050mm diameter pipe which acts as a storm overflow during extreme weather events. These pipes are laid across a floodplain to the River Wey, a distance of approximately 330m before discharging via a bespoke headwall into the River Wey. This has been designed in conjunction with Environment Agency to minimise erosion in what is classified as a salmon river.
Due to Environment Agency and Local Authority permitting requirements as well as practical requirements of working on a floodplain with underlying running sand, these works are practically restricted to a short duration in the summer. This is being undertaken during Summer 2024 and the works are on target for completion within this period.
Below-ground pipework
The majority of underground assets in the new works are being constructed within the existing landfill. This brings plenty of challenges in both design and construction. Assets must be designed to withstand both differential settlement and potential degradation from existing contaminants in the land fill material.
A variety of ductile iron, carbon steel, and concrete pipes are being used with various protection methods. The work is being self- delivered by the BAM workforce and the installation of below-ground pipework is underway with a focus on where it interfaces with the new structures. This requires extensive temporary works solutions to provide a safe working environment for the workforce within the band of landfill material.
Steel sheet piles are being used to provide temporary ground support and excavated landfill material is being sorted in a material handling area on site. This is being done to reduce the amount of hazardous material being sent off site, halving the amount of excavation and disposal required using traditional open cut methods.
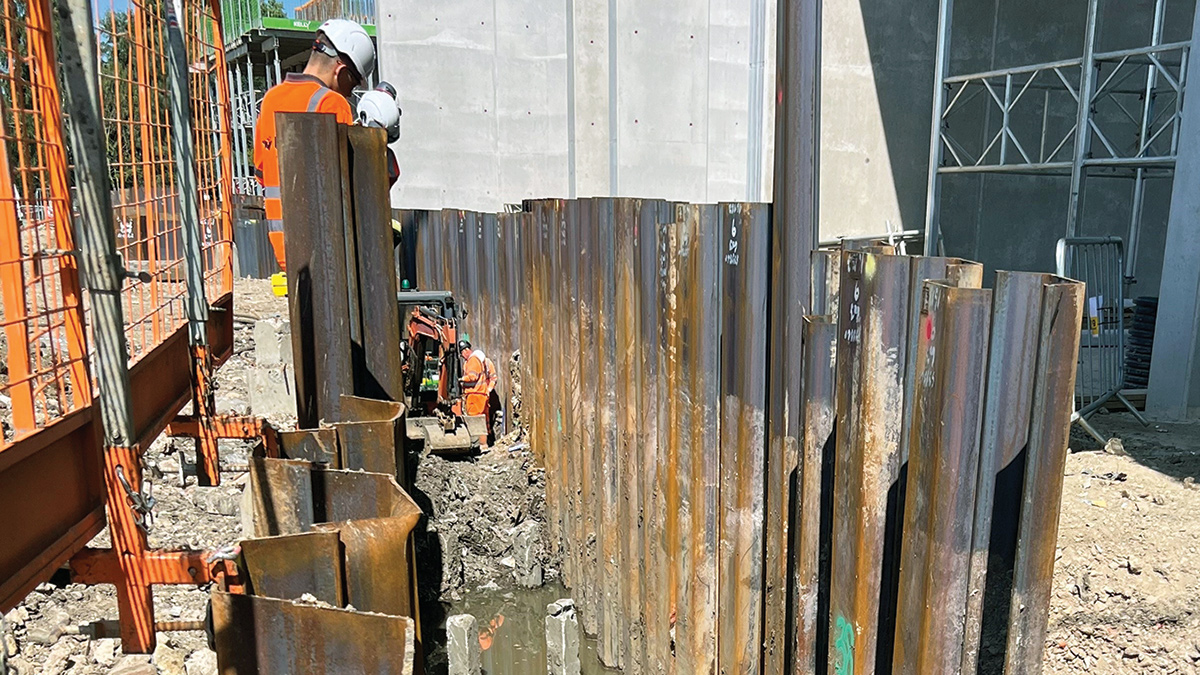
Threading buried process pipework between new structures requires extensive temporary works – Courtesy of Bam Nuttall Ltd
Integration of existing assets
As well as the main connection taking flows form the existing works to the new, there are three other existing assets which are to be integrated into the new system, at various points along the length of the new tunnel. This involves extensive research and planning in an open and collaborative approach with TWUL networks teams.
Bowers Farm Main was successfully diverted in November 2023, and has been constructed such that the final connection and commissioning to the new system will be a more straightforward operation. Planning works are currently underway on both Stokes Road syphons and Abbotswood syphons in order to construct similar scenarios for future connection and commissioning.
The main connection to the existing Guildford Main at the head of the new scheme entails connecting into an existing 10m deep concrete and brick built chamber, which carries live flows 24/7. The site team have undertaken several successful drawdowns in conjunction with TWUL to ascertain the dimensions and condition of the chamber in order to plan the final breakthrough works in great detail. This design work is currently underway and the new tunnel hand drive has been stopped a few metres short of the final breakthrough and shored up, prior to the final connection to the existing network.
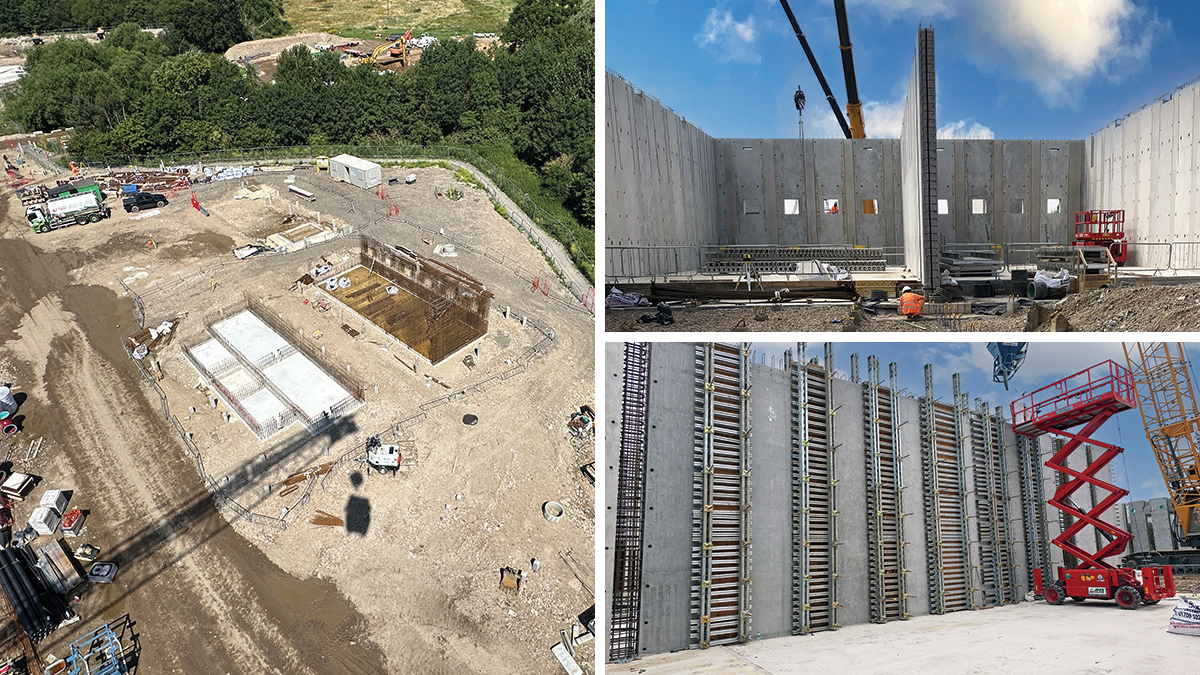
(left) Concrete bases for the tertiary treatment plant, (top right) cross-sectional view through the primary settlement tank, showing the piles and gas dispersal layer beneath the base, and (bottom right) precast wall panels are joined with an in situ concrete stitch – Courtesy of Bam Nuttall Ltd
Future works
Construction works of the ‘Big Build’ are continuing at pace and the BEJV Team are now focusing on ensuring a safe, effective and efficient integration of civils and MEICA elements. This will start in late 2024 and continue throughout 2025.
Following successful completion of commissioning of the new sewage treatment works in 2026, the existing works will be de-commissioned making way for the next stage of the Weyside Urban Village, providing homes and leaving a true legacy for local people and businesses.
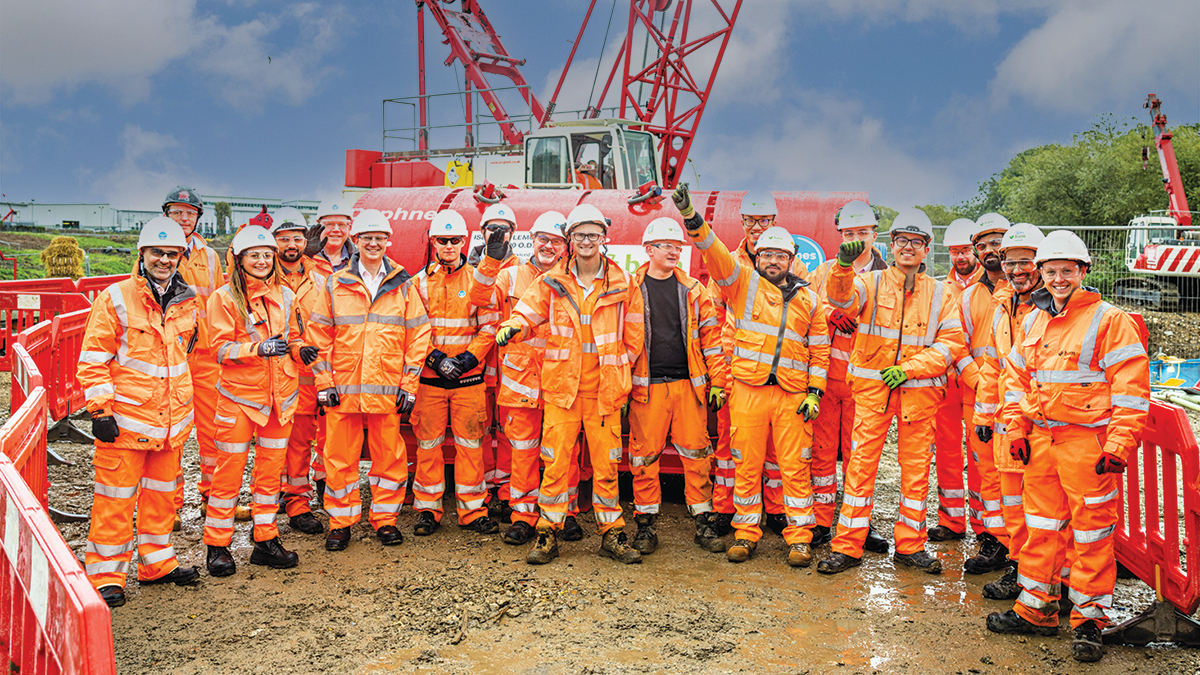
Members of the Thames Water and BAM team prior to launching the Tunnel Boring Machine “Daphne” - Courtesy of Bam Nuttall Ltd