Herricks WTW (2024)
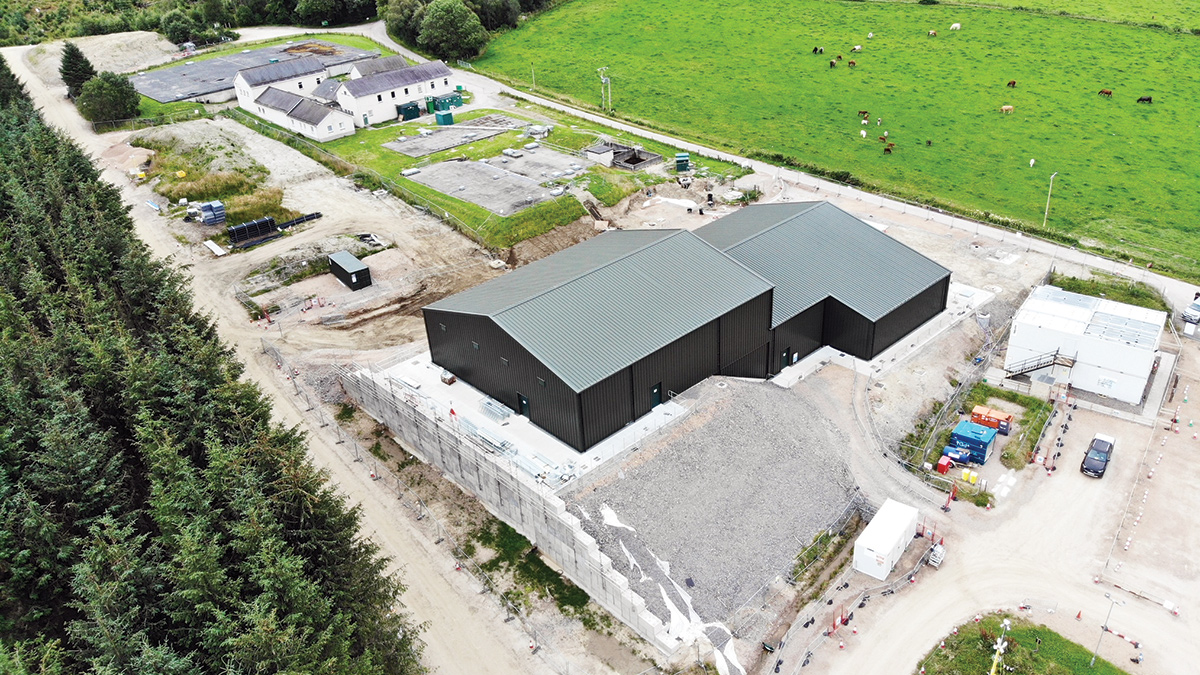
Construction phase progress (July 2024) - Courtesy of ESD
Herricks Water Treatment Works supplies treated water to the town of Keith and the surrounding area in Morayshire in the north-east of Scotland. The asset condition was considered poor (with some assets dating back to 1960), and the water treatment process was not of an acceptable standard. To address this issue, a new water treatment works is being constructed adjacent to the existing site, which will be decommissioned once the new works is in service. Scottish Water has also identified the following needs at the Herricks WTW: (i) risk of Cryptosporidium failure, (ii) components of the existing works are reported by CSD (Customer Service Delivery) to be life expired, and (iii) spare parts are very difficult to procure.
Existing works
Raw water is abstracted from various sources which ultimately combine at a header tank located within the treatment works building, before entering the raw water reservoir. Water is then pumped from the raw water reservoir to the works.
Raw water is dosed with soda ash for pH control. PACL (poly aluminium chloride) is dosed to provide coagulation control and polymer is dosed as a coagulation aid. Dosed raw water is fed to two flocculation/DAF (dissolved air flotation) streams.
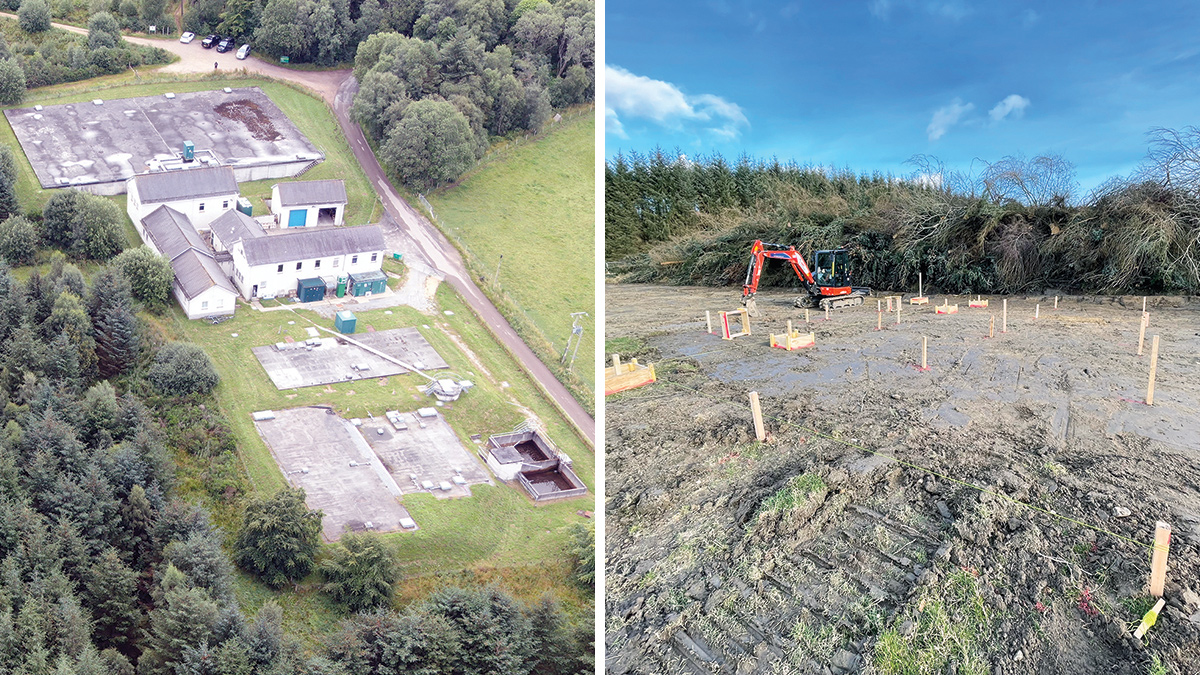
(left) The existing Herricks WTW and (right) construction phase progress (February 2023) – Courtesy of ESD
Clarified water is recycled via fixed speed pumps to a single saturator. The DAF system is hydraulically desludged to sewer.
Clarified water from the DAF passes directly to three rapid gravity filters (RGFs). The RGFs are backwashed with chlorinated water from a dedicated backwash tank. Filtered water from the RGFs is dosed with sodium hypochlorite for disinfection before entering the chlorine contact tank (CCT). Disinfected water is then dosed with lime in a lime reaction chamber prior to flowing to the works clear water tank.
Process selection and scope
A new water treatment works designed to treat water to current potable water standard is to be built on a site opposite to the existing WTW. The works will be designed to supply up to 2.1 MLD (million litres per day) and feed the existing clear water tank on the site at Herricks WTW.
The strategic objective for this project is to identify and carry out an intervention that reduces the risk of Cryptosporidium breakthrough and provides a treatment water works in which components or process units can be readily replaced or repaired thus maintaining regulatory required levels of water quality compliance.
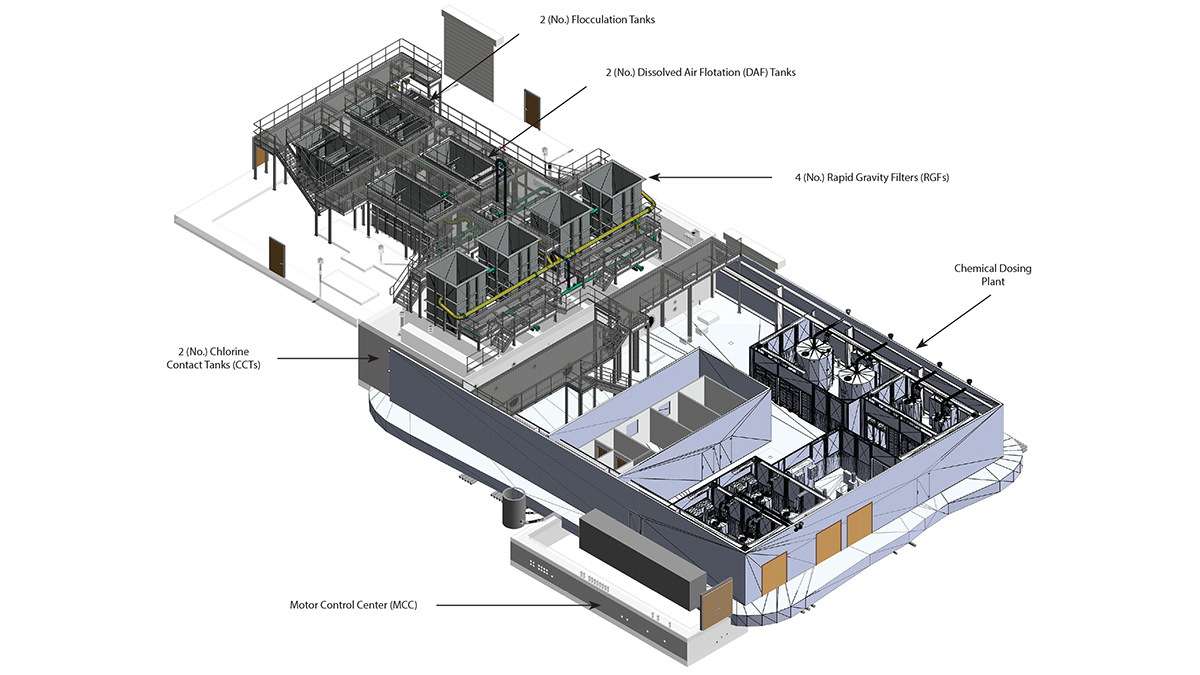
Solution layout for Herricks WTW – Courtesy of ESD JV
The design comprises the following:
- Raw water pumping station.
- Raw water chemical dosing with polymer, sulphuric acid and sodium hydroxide.
- First stage clarification (two streams including flocculation and DAF).
- Rapid gravity filtration utilising four RGFs.
- RGF backwash system including pumps, blowers and clean backwash tank.
- Rinse return tank and pumping station.
- Dirty backwash balance tank and pumping station.
- Treated water disinfection (sodium hypochlorite dosing).
- Chlorine contact tanks.
- Final water pH correction with sodium hydroxide.
- Service water system.
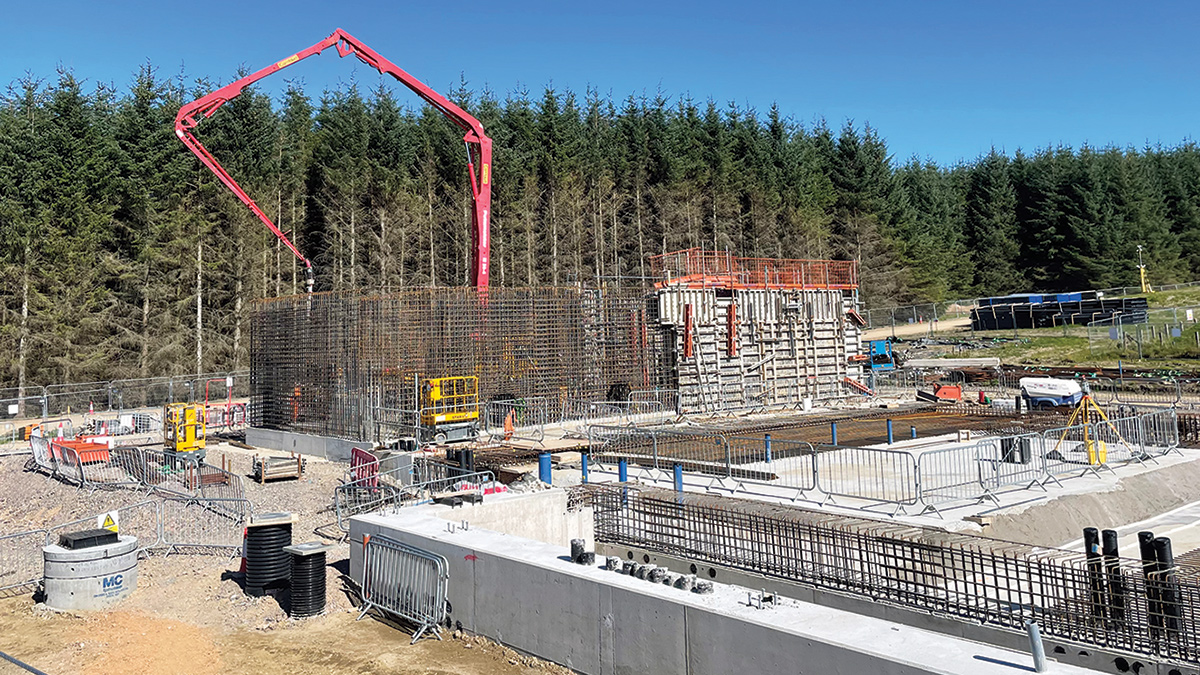
Construction phase progress (September 2023) – Courtesy of ESD
Main challenges
The principal challenges were:
Buildability & design complexity
The project involved constructing a large foundation with a retaining wall, initially appearing as a simple structure but requiring careful planning and modular design to allow for efficient and fast construction. Precast elements and a self-delivery approach facilitated this process, reducing the need for specialized labour and enabling parallel activities.
Weather & time management
Delays due to weather were a significant concern, and optimizing time on site was crucial. To address potential delays, off-site construction was employed for certain components, which required quick decision-making and collaboration between the design and site teams to adjust plans and maintain project timelines. The project faced significant logistical challenges due to restrictions on large vehicles using the existing Edindiach Road specially in the last two winters (2022 and 2023), requiring the use and maintenance of an alternative forestry road.
During peak periods, up to 20 articulated trucks made deliveries, and bad winter weather required full-time road maintenance to ensure progress. The team had to pre-plan all materials and logistics before the harsh winter months to continue the build, as material transport in late January and February was impractical. The persistent need for road maintenance underscored the difficulty of operating in this remote and elevated location.
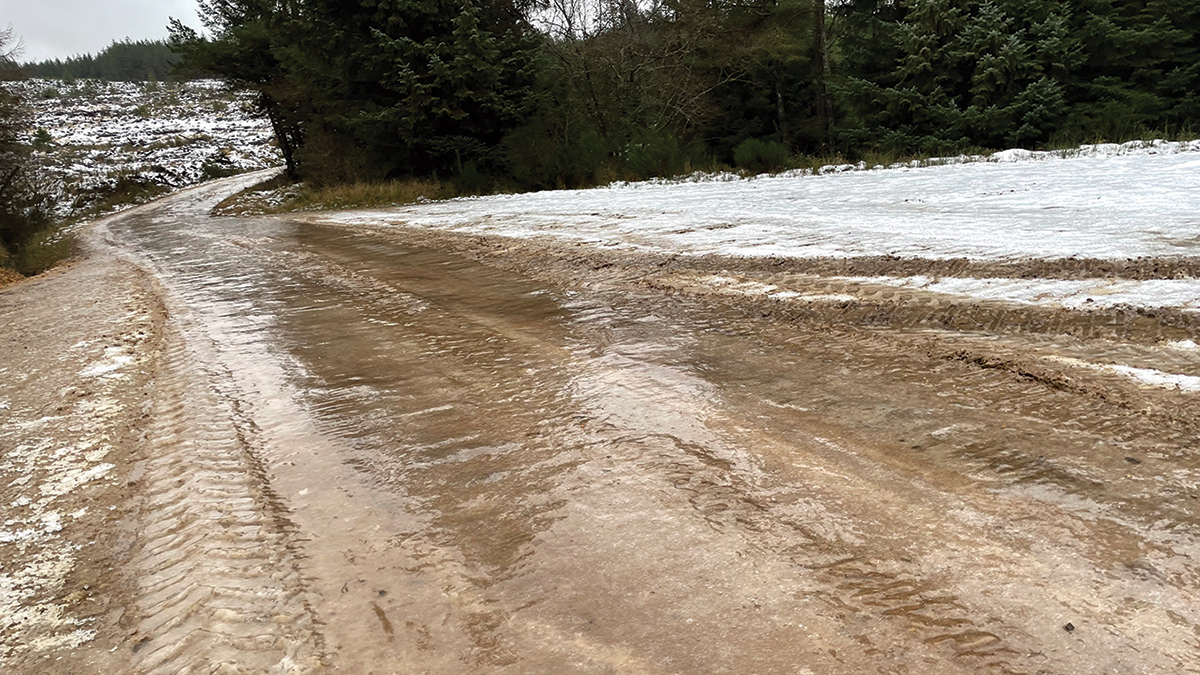
Edindiach Road condition (December 2023) – Courtesy of ESD
Space constraints & safety
The project site was extremely limited in space, necessitating meticulous coordination among multiple contractors working simultaneously. Daily briefings and segregation of work areas were implemented to ensure safety and maintain smooth operations, emphasizing the importance of collaboration and communication to prevent accidents and keep the project on track.
Raw water deficit
The primary challenge in the commissioning phase will be a significant lack of raw water. The current plant operations demand 95% of the available raw water, leaving only 5% for commissioning the new plant. This deficit is critical since the new plant would typically require the same 95%. The problem will become pressing towards the end of the year when testing of the new plant begins. To address this, the team proposes a recirculation system, isolating the raw water tanks to manage water use between the new and existing plants.
This requires careful handling as the existing plant needs 100% raw water. The blending of partially treated recirculated water with raw water necessitates adjustments in the old plant. A de-chlorination chamber will also be set up to ensure seamless operation of both plants, based on lessons from a previous project.
Herricks WTW: Supply chain – key participants
- Design & project delivery: ESD
- FRC contractor: Global Infrastructure
- Raw water diversion: Nicol of Skene
- Groundworks, drainage & tie-ins: Seivwrights
- Metal structure & mechanical installation: AJ Engineering & Construction Services Ltd
- Chemical dosing: RSE
- Main control system: MCS Control Systems
- Electrical package: FSD Ltd
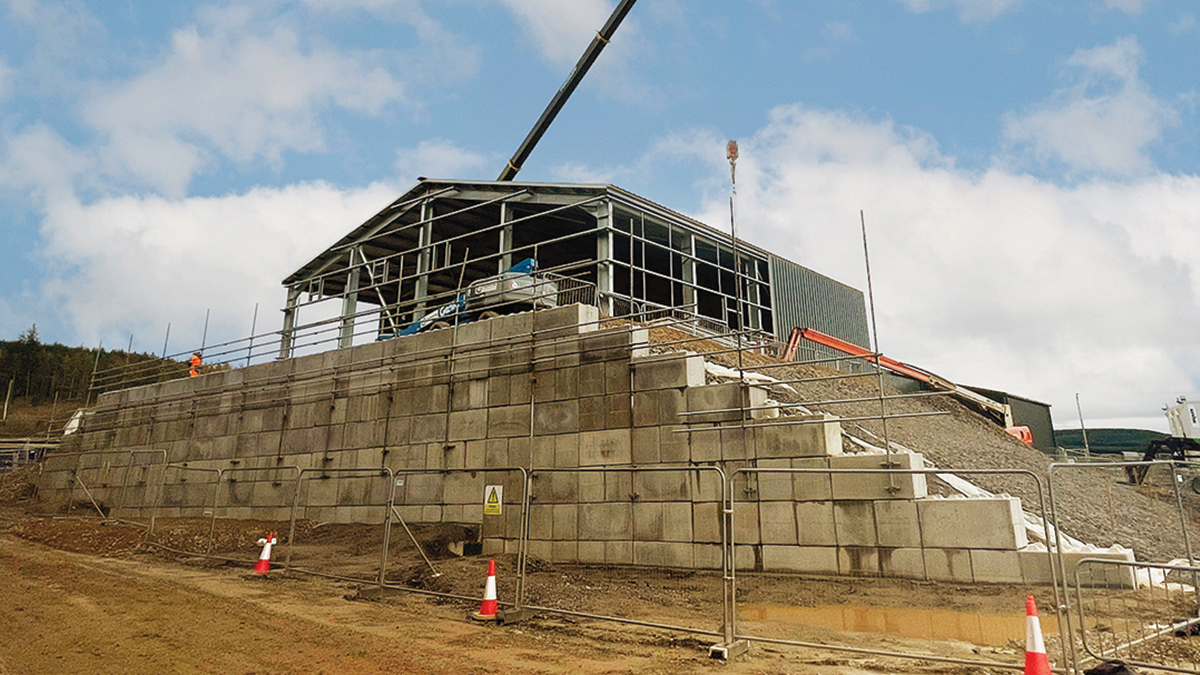
Retaining wall – Courtesy of ESD
Current status: July 2024
The project commenced in 2021 with an outline design to establish the basic framework and key scope items to be addressed. This was followed by a detailed design stage delivered by ESD, where the specifics and technical aspects were meticulously developed. Cost estimates were then prepared to understand the financial implications of the project.
By August 2024, the project team aims to complete the mechanical assembly, chemical dosing systems, civil structures, and reinforced concrete (RC) elements. Electrical installations, including the motor control center (MCC), are expected to start at that point.
Some elements of commissioning are planned to begin in August 2024, with the physical construction mostly complete and only wiring and final connections remaining.
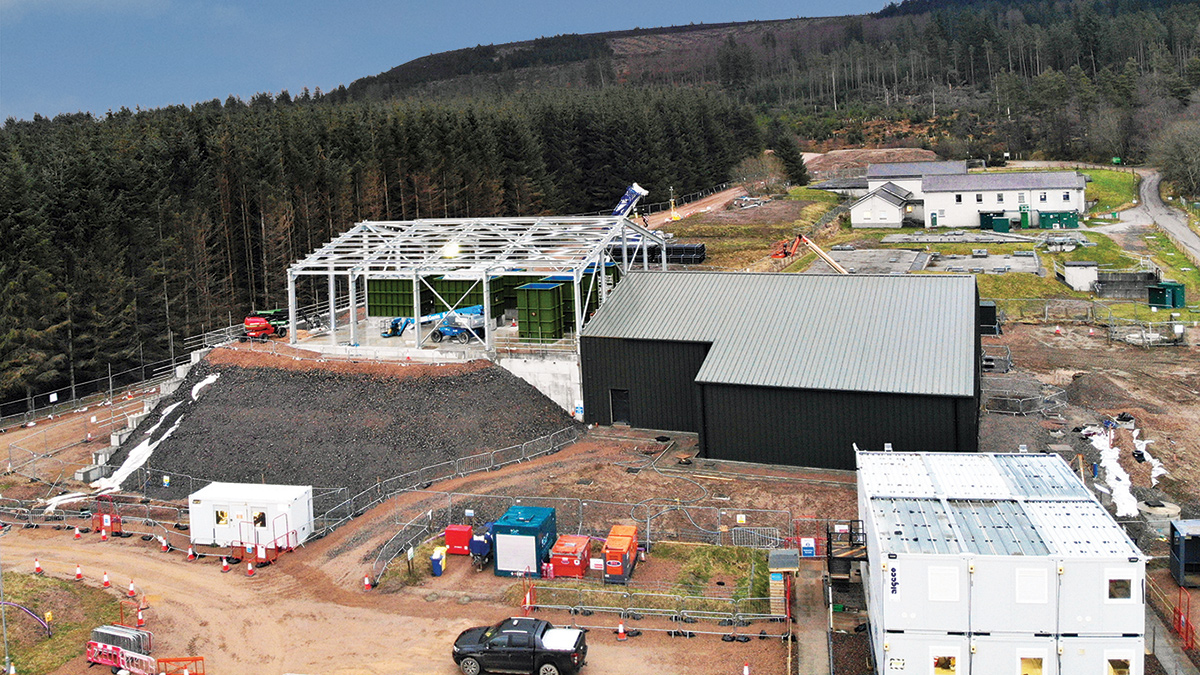
Construction phase progress (March 2024) - Courtesy of ESD