Hookstone Road CSO (2020)
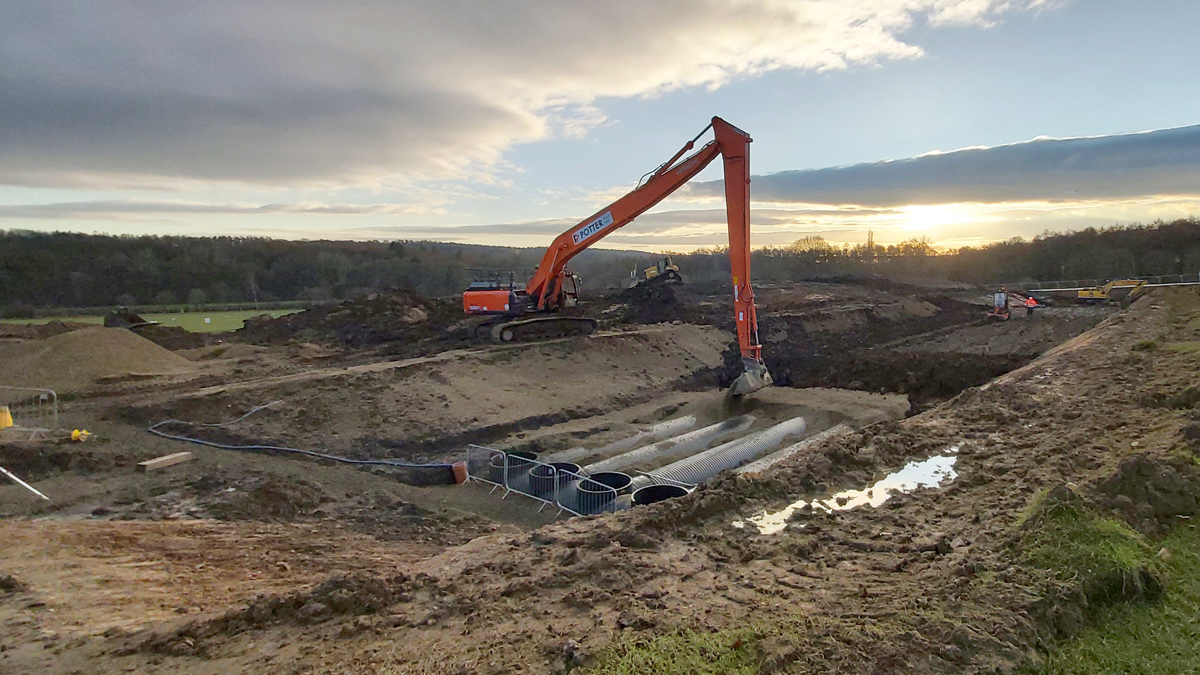
Installation of network storage - Courtesy of MMB
Hookstone Road CSO in Harrogate, North Yorkshire, is a CSO chamber with upstream and downstream online storage provided by large diameter pipes. During storm events, pass forward flow is restricted by the 200mm outlet pipe and 90 degree bend downstream and partially fills the storage pipes before excess flows pass through a screen at the CSO chamber and discharge to the adjacent watercourse, Hookstone Beck. Mott MacDonald Bentley (MMB) were appointed by Yorkshire Water to carry out investigation works following blockages of the outlet sewer. In order to comply with the existing Environment Agency (EA) Discharge Consent for the asset, the pass forward flow and storage volume provided at the point of spill of the CSO were key in developing an acceptable solution.
Solution development
A hydraulic model was used in the process of design optioneering, as any modifications to the system had the potential to cause issues elsewhere in the network. The catchment was particularly challenging due to the large number of other CSOs, which could not experience detriment as a result of the solution.
The Early Contractor Involvement (ECI) report produced by MMB proposed extensive pipework remediation in the downstream catchment to reduce infiltration and provide additional capacity for the increased pass forward flow, however following site investigation it was found that these flows were from uncharted connections and could not be removed. The additional storage volume was proposed as an offline, pumped return storage shaft downstream of the CSO screen, however the steep terrain adjacent to the watercourse made construction extremely challenging.
Under the AMP6 Framework Agreement, MMB was appointed as design and build contractor for the delivery of the £3m scheme.
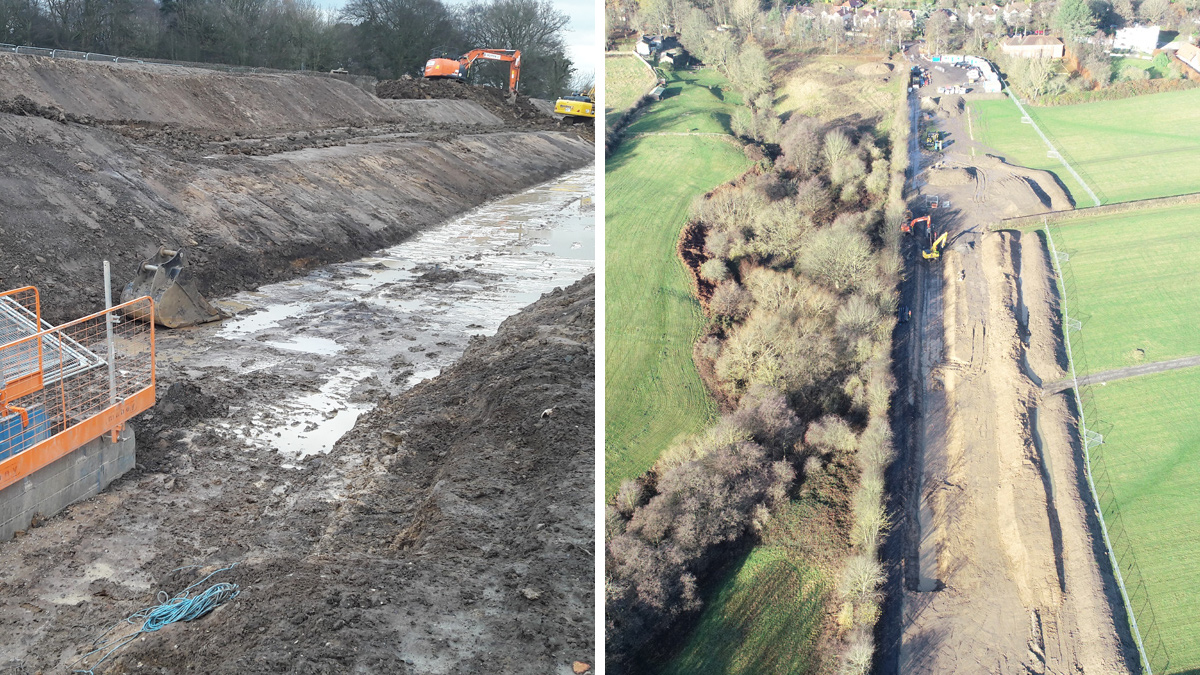
(left) Installation of 6m deep sewer and (right) aerial view of outlet sewer installation – Courtesy of MMB
The delivery team worked closely to develop a revised solution within the Client’s original target cost. The construction team carried out investigation works including topographical surveys, CCTV and surveys of the existing sewer system, trial holes for unconfirmed service locations and ground investigation works. Using this information, the hydraulic model was updated with a revised solution which maximised the use of gravity return storage and avoided the use of small orifices which had resulted in problems in the system in the past.
The final design included four phases:
- 184m3 of additional storage within large diameter pipes upstream of Hookstone Road CSO.
- 360m sewer upsizing to 450mm diameter, replacing the existing throttle and 90 degree bend downstream of the CSO.
- 730m3 online storage within 1400mm diameter pipes in the downstream catchment to minimise detriment.
- Rehabilitation and patch repairs to sections of combined sewer in the downstream catchment to reduce water ingress.
Using the hydraulic model to carry out Time Series Rainfall analysis, it was shown that the proposals would significantly reduce the annual spill volume within the catchment, resulting in water quality benefits to the receiving watercourse.
In order to get the input of the end-user, access, lifting and maintenance (ALM) reviews were carried out. This enabled the network operators to raise any concerns and make requests regarding the design of the proposed assets. Following on from this, the design team made some modifications to include improved access, flushing points, a sump and additional telemetry monitoring. An ALM review of the final design was then held to ensure end-user buy-in.
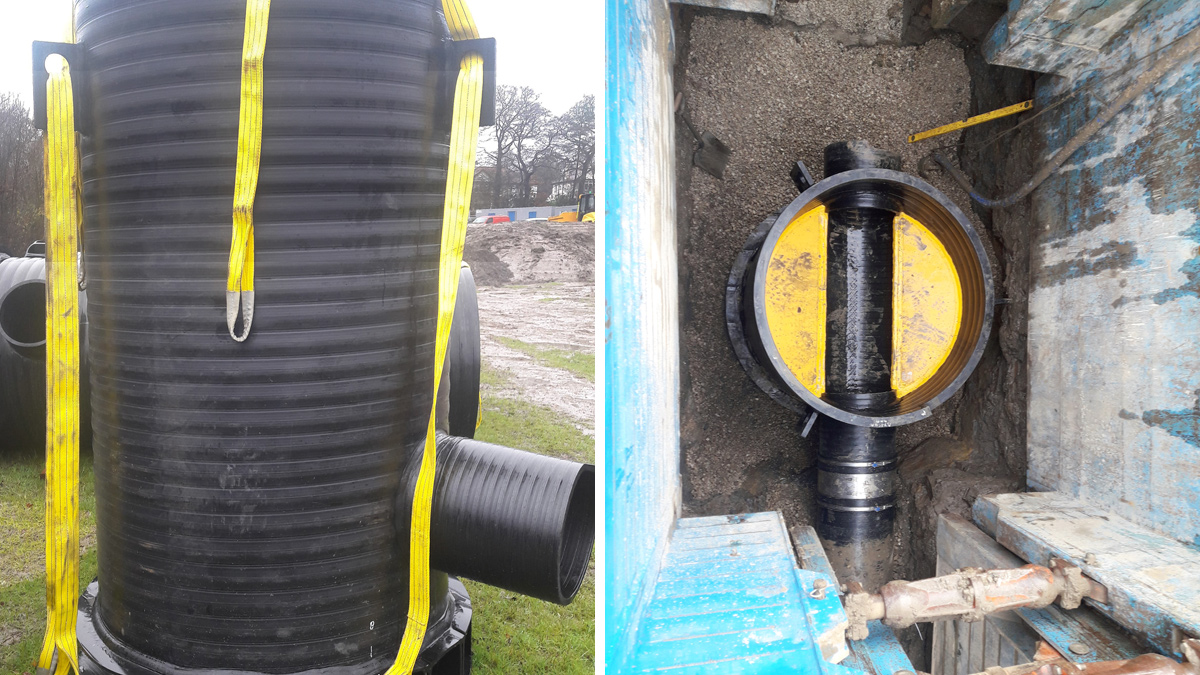
(left)manhole delivered pre-slung ready for installation and (right) pre-benched manhole base installation – Courtesy of MMB
Efficient construction
During the detailed design phase, the design, construction and procurement teams worked closely to engage with the supply chain and explore the potential of a variety of products. It was agreed that making use of off-site fabricated products wherever possible would be important in minimising the construction programme and maximising the quality of installation, reducing the risk of re-work.
New, off-line manhole chambers were identified as an opportunity to utilise off-site fabrication and a variety of products were considered. High density polyethylene (HDPE) chambers supplied by Weholite® was chosen for the scheme as they had a number of benefits including:
- Lightweight for handling and installation.
- Integral baseplate to help counteract flotation.
- No concrete surround required.
- Inlet and outlet stubs at required angle and gradient.
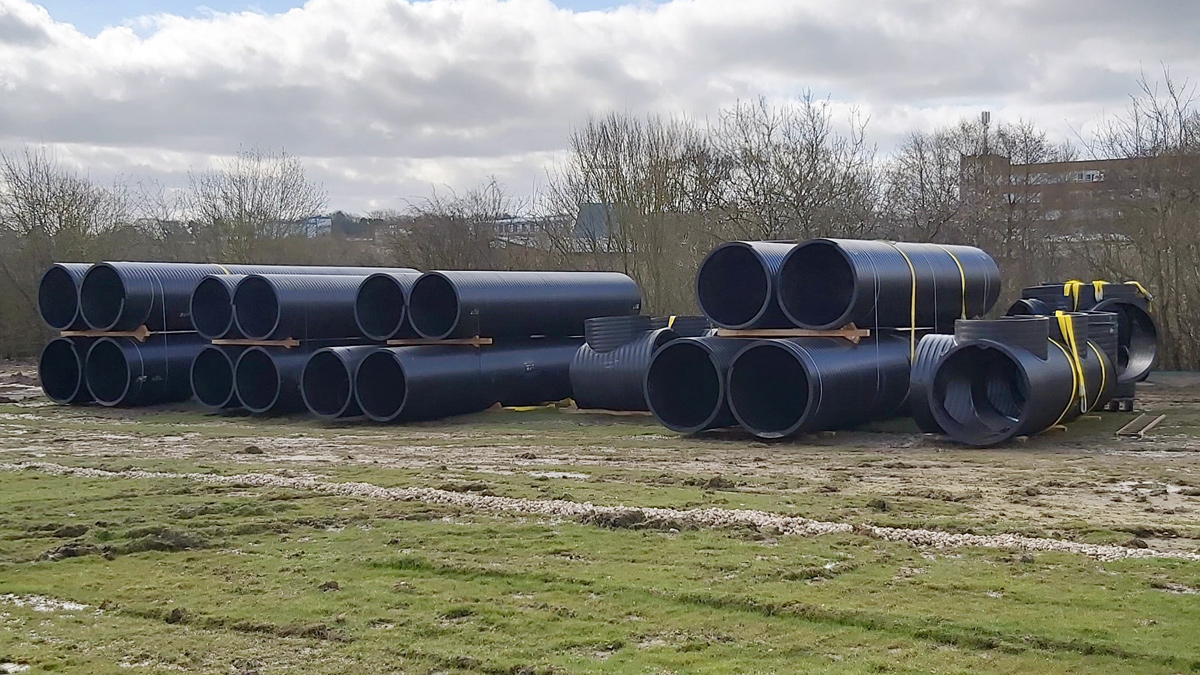
Weholite® pipes delivered pre-slung ready for installation – Courtesy of MMB
Installation of each prefabricated manhole reduced the construction duration by 4 days compared to traditional in situ construction for a 6m deep chamber. The pre-slung units:
- Were safe and easy to transport.
- Minimised work in deep excavations.
- Reduced the amount of waste.
- Reduced the need to transport materials around the site during challenging winter working conditions.
Construction of the 450mm diameter outlet sewer was particularly difficult. The level of the existing upstream sewers and CSO meant that the pipes were 6m deep in challenging ground conditions. Heavy clay soils with groundwater fissures meant that the excavation required constant dewatering during the very wet winter months. Silt management was required and constantly maintained throughout the works to prevent any detriment to the adjacent watercourse.
Weholite® was selected to supply the large diameter storage pipes. These were fabricated off-site and included manifold sections. They were delivered to site in units up to 10m long and welded together in situ by the supplier on site.
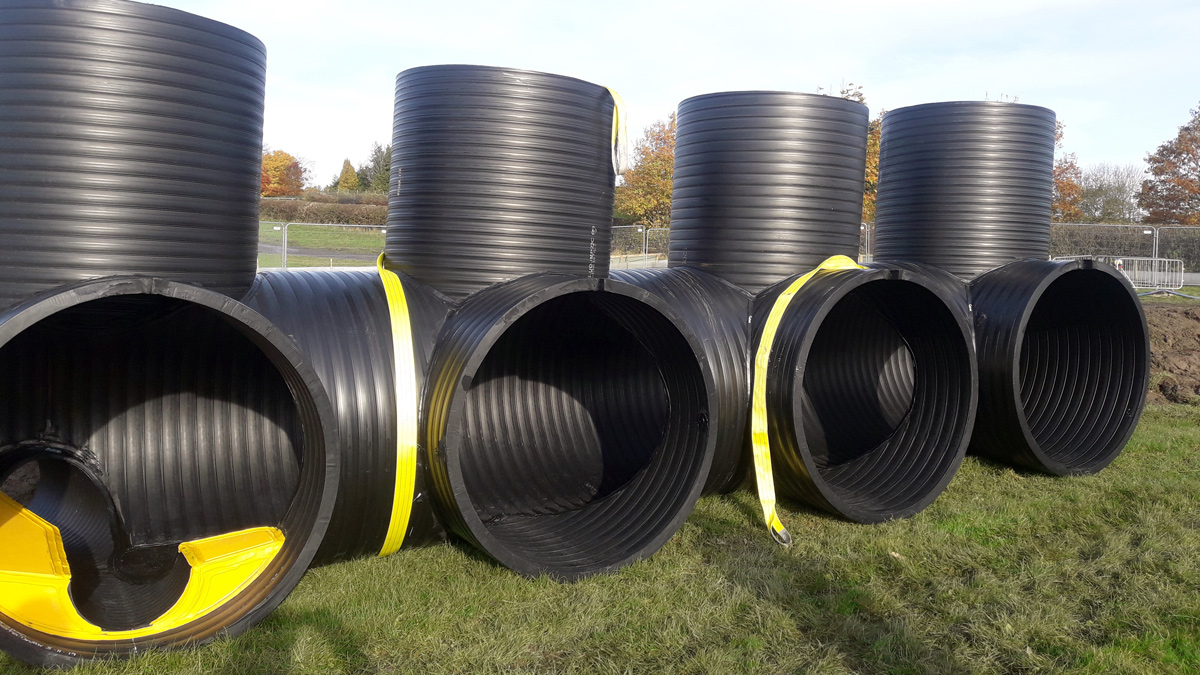
Off-site fabricated manifold – Courtesy of MMB
Installation of the storage pipes up to 4m deep was carried out by MMB. Early engagement with plant supplier Potter Plant Hire meant that use of a long-reach excavator was suggested. This improved the construction methodology as the 22m reach of the excavator meant that all construction activities could be carried out from one side of the excavation. This reduced the working area and the amount of plant required.
The 730m3 online storage was provided by 4 legs of 1400mm diameter, 120m long storage pipes. The site team developed an installation methodology with a bulldozer working in front of the pipe-layers to carry out the bulk of the excavation. An excavator working within the excavation set the final levels using a rotating laser, whilst the long-reach excavator laid pipe bedding, carried out the pipe installation and backfilled from the side of the excavation. Excluding earthworks, the pipe installation took approximately 4 weeks, allowing the excavation to be backfilled by Christmas.
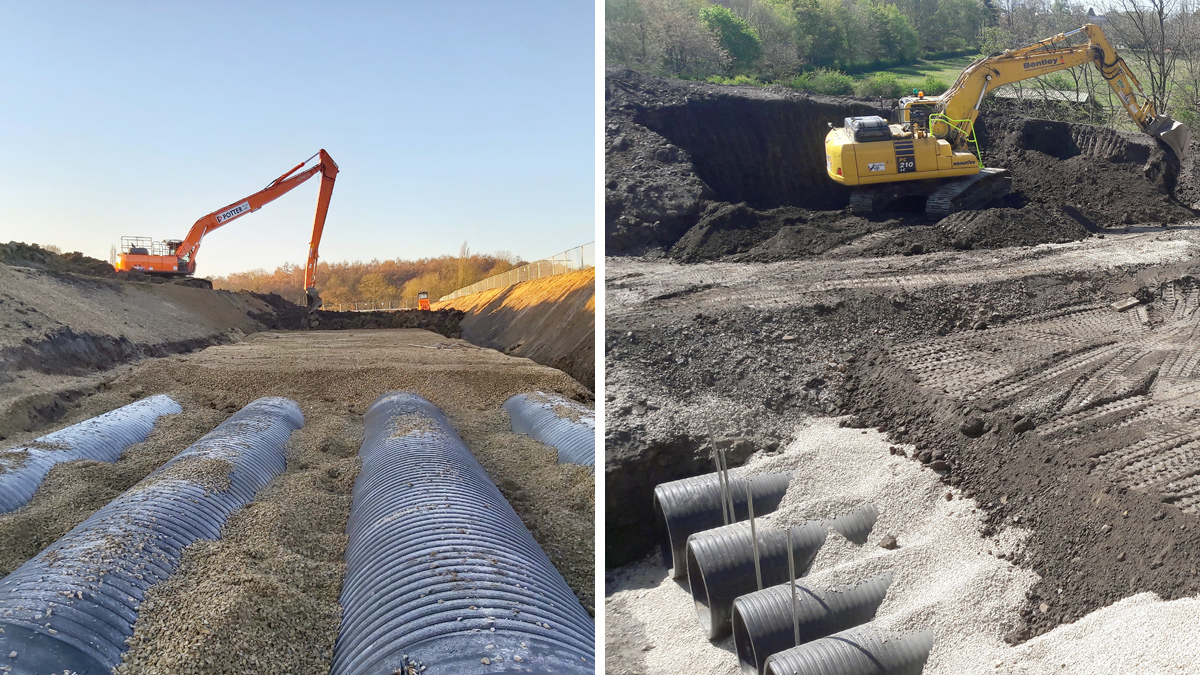
(left) Backfilling excavation and (right) construction of storage upstream of CSO – Courtesy of MMB
The storage pipes were then internally welded by Weholite®’s specialist subcontractors, prior to cleaning and a CCTV survey was carried out for quality assurance.
MMB constructed the access points, utilising Pecafil permanent formwork to form an internal shutter so that the cover slabs do not transfer load onto the plastic turrets. Flows were diverted and the 730m3 storage was the first part of the scheme to become operational, allowing additional flows to be passed forward into the downstream system.
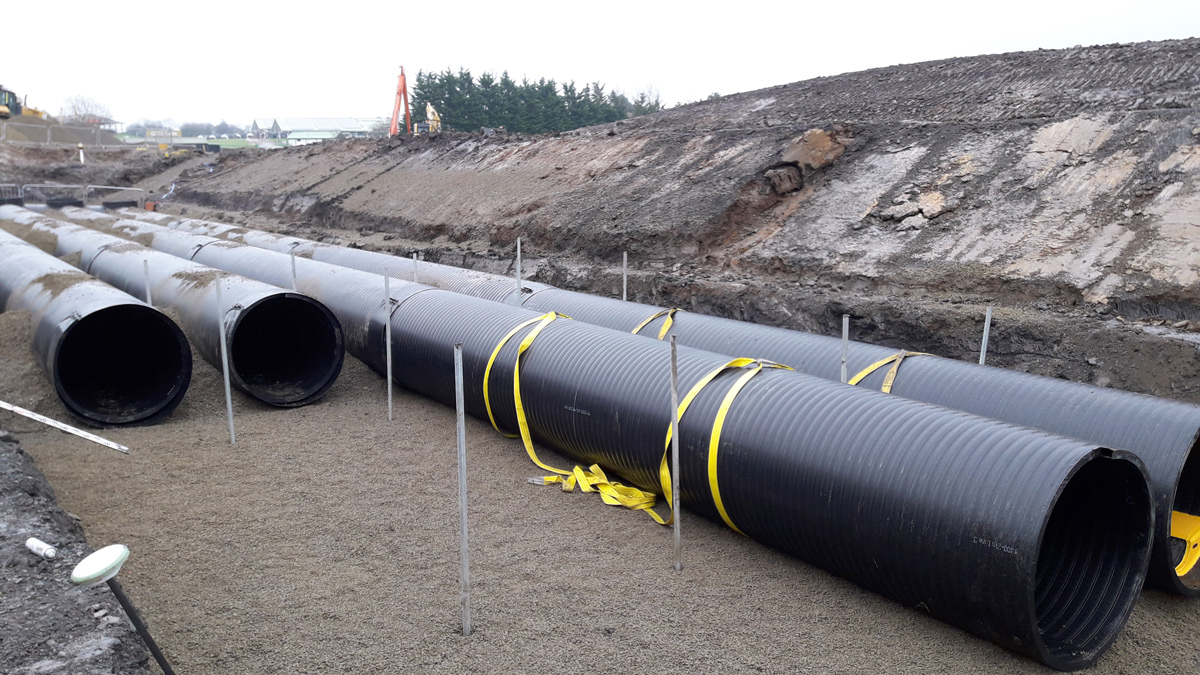
Storage pipe installation – Courtesy of MMB
External factors
The location of the scheme within the grounds of the Great Yorkshire Showground, a national event venue, presented additional challenges to the successful delivery of the scheme. Construction could not get underway until after the UCI Road World Championships cycling event at the end of September 2019. The site is also critical for the Great Yorkshire Show, which is held annually in July.
As soon as the outline design was finalised, the team liaised with the landowners to plan the delivery of the project so that it was acceptable to all parties. The 730m3 storage pipes were sited in a critical parking area for the Great Yorkshire Show, and vehicle access through all other areas was also essential for this event. The programme was adapted to install these elements as early as possible and a contingency plan developed to assure the landowner that the event would not be impacted by the works.
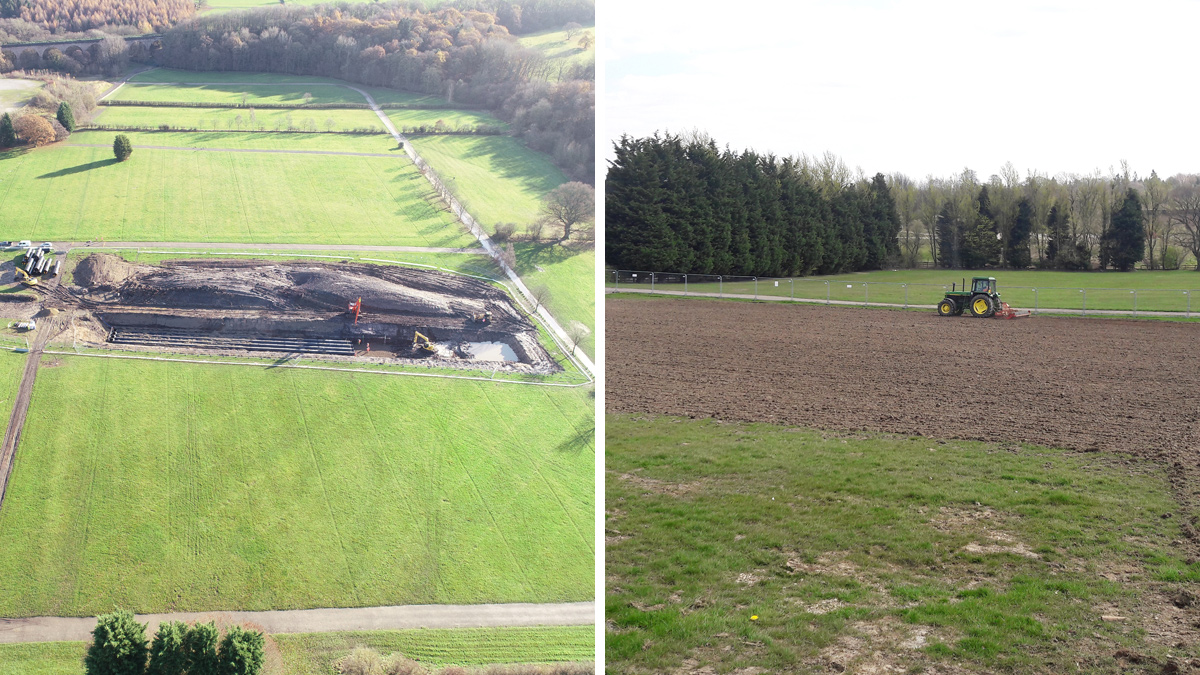
(left) Construction within Great Yorkshire Showground and (right) reinstatement of the show ground – Courtesy of MMB
Surveys and optioneering
Prior to the site works commencing, planning permission was required to upgrade the site access and prune the overhanging trees. Following liaison with both the Arboriculture Officer and highways department, planning permission was granted. Identifying potential blockers such as this very early in the delivery process meant that they could be addressed and avoided impact on the construction programme.
Ecological surveys were carried out during the design phase and the potential for great crested newts, a protected species, was identified. As the work locations were fixed by the hydraulics of the existing system, mitigation measures were required. Specialist fencing was installed to stop any great crested newts entering the site as construction was underway prior to the weather being cold enough for hibernation. The construction team carried out toolbox talks and maintained the fencing throughout construction.
As part of the optioneering process the design team used The Carbon Portal, Mott MacDonald’s in-house carbon assessment tool, to assess capital and operational carbon. The updated solution reduced the total carbon impact by 66%.
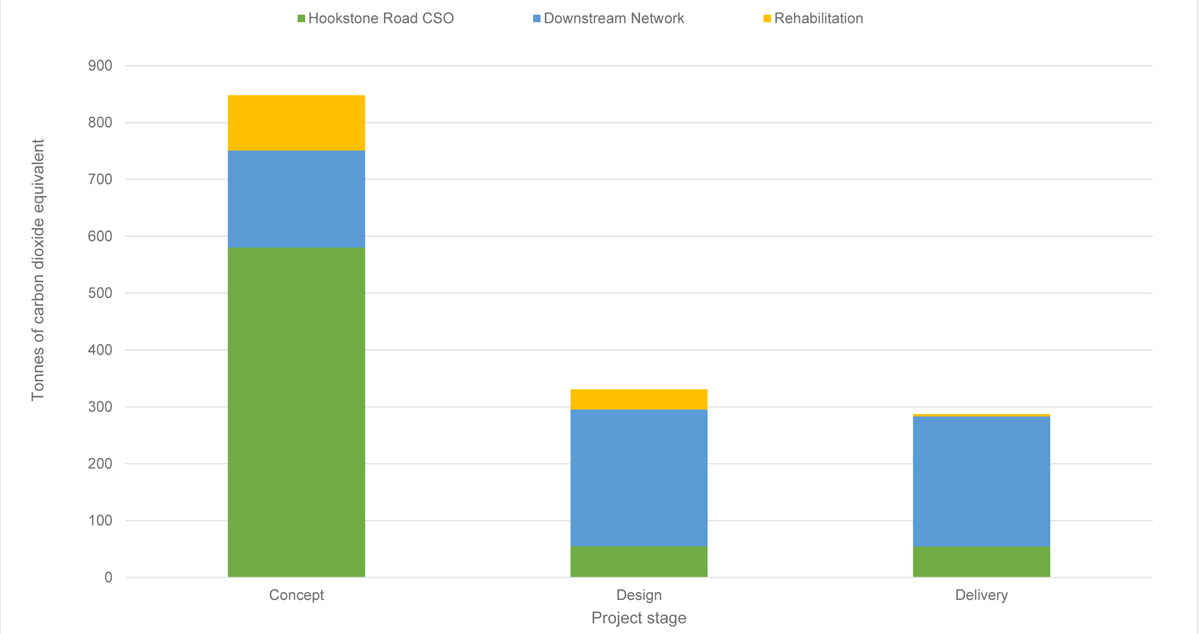
Carbon impact of proposed solution – Courtesy of MMB
Hookstone Road CSO supply chain: Key participants
- Design investigation: Mott MacDonald Bentley
- D&B contractor: Mott MacDonald Bentley
- Weholite® prefabricated sewer storage pipes and welding contractor: SDS Limited
- Weholite® prefabricated manholes: SDS Limited
- LV Electrical: Circle Control & Design Systems
- Key plant and equipment: Potter Plant Hire
Progress
At the time of writing (May 2020) construction of the scheme is well underway with all works downstream of the CSO completed. Construction of the additional storage upstream of the CSO is ongoing and due to be completed by late summer 2020.