Inlet Enhancement Projects (2024)
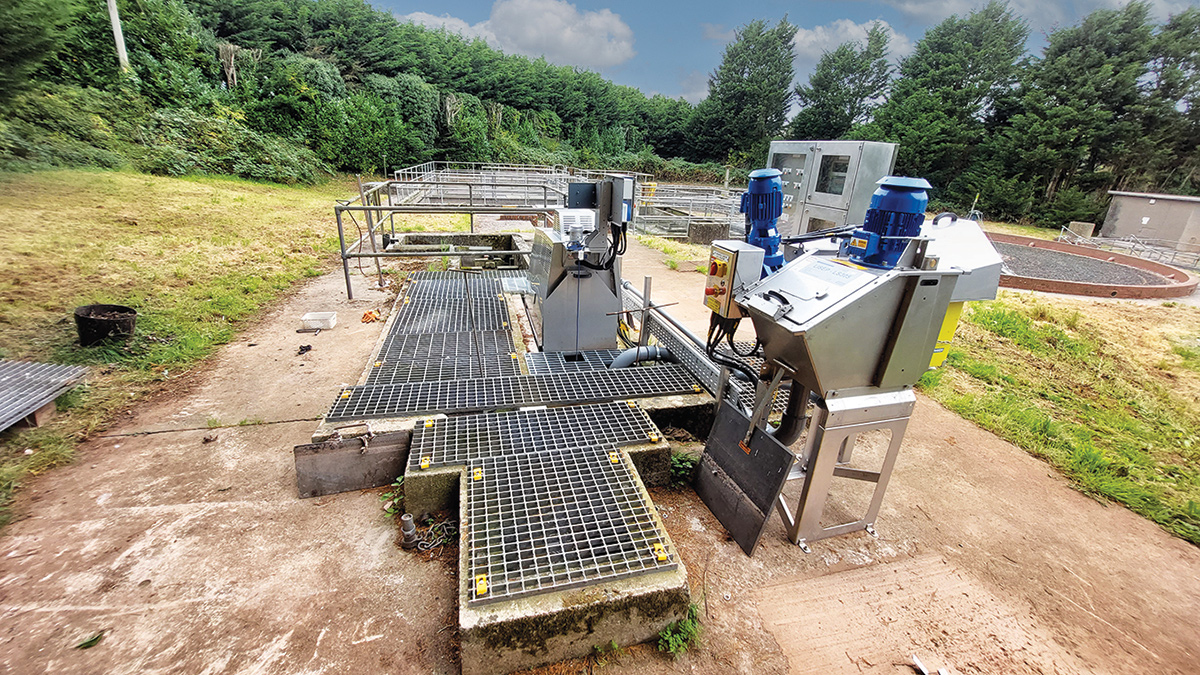
Compton STW with new screen and LISEP in place - Courtesy of Galliford Try
One of South West Water’s aims is for everyone to feel confident about the water at their favourite beach, river, or lake. The Inlet Enhancement Projects programme of work was put in place to ensure that all flows coming into sewage treatment works under normal conditions are screened down to 6mm 2D and that the storm spills were screened down to 10mm. As part of this programme, Galliford Try was engaged to deliver 10 projects across Devon for the enhancement of the inlet works and install new automated preliminary screens with manually screened bypass channels and associated LCPs for control.
Planning and design
Following a full review and selection process for a preferred screen provider to ensure that the correct product was selected for the application, South West Water and Galliford Try, supported by the civils design arm of Fishtek Consulting, selected Haigh Engineering Ltd as the main supply partner.
Galliford Try worked collaboratively with Haigh Engineering to discuss the specific requirements for each of the sites individually. This included a programme of site visits to gather information about the existing structures and hydraulic profiles that were to be adapted. After this, Galliford Try held numerous design review meetings with South West Water’s key stakeholders, including the operational area managers, to discuss the best specific application that were developed with the delivery partners for each of the sites along with design flow rates.
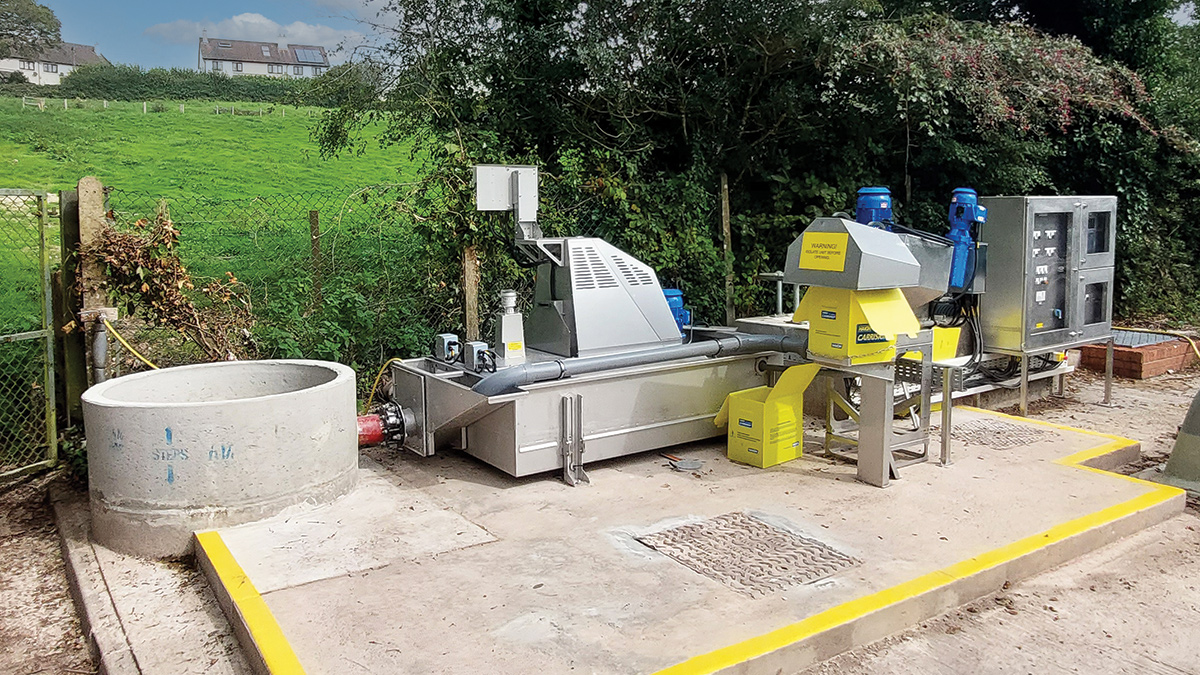
The new screen, LISEP and grit trap at Moreleigh STW – Courtesy of Galliford Try
Locations
The 10 wastewater treatment works are:
- East Ogwell STW
- Compton and Marldon STW
- Drewsteignton STW
- Diptford STW
- Moreleigh STW
- Whiddon Down STW
- Cornworthy STW
- Zeal Monachorum STW
- Parkham STW
- Bridford STW
The sites were batched – 3 sites at a time – with South West Water and Galliford Try prioritising those which would gain the most benefit from the scheme. Fishtek Consulting was engaged as designers to look at the civils detailed design and to model each of the sites with the new screens in place.
Each site had its own complications as Galliford Try had to manage flows through to the rest of the site. With each site being different in nature of hydraulics, there was a varied approach to be taken; whether that be pumped flows or gravity flows into the site.
Another challenge to each project was the selected screen, as some of the screens come as a package screen with bypass included and all that was required was a level foundation, whilst some screens sat in the channel, meaning that Galliford Try and CR Civil Engineering had to break out existing channels and benching to facilitate the installation of the new screen and associated equipment.
Construction
Where possible, construction was scheduled for the dryer months to minimise the impact on the performance of the site and risk of delays due to high flows. After initial site set-up, the first task was to set up over pumping or a bypass on each site which was agreed up front with the client and a process risk assessment put in place for the duration of the works. Once this was set-up, the deconstruction of some of the existing inlet structures could be undertaken to form a new base slab or a new benched inlet for the screen to sit.
Once the new screen was installed with all relevant ducting in place to take power and control cabling, commissioning engineers from Galliford Try and Haigh Engineering Ltd set the parameters for the new screen and ensure the process worked as it should.
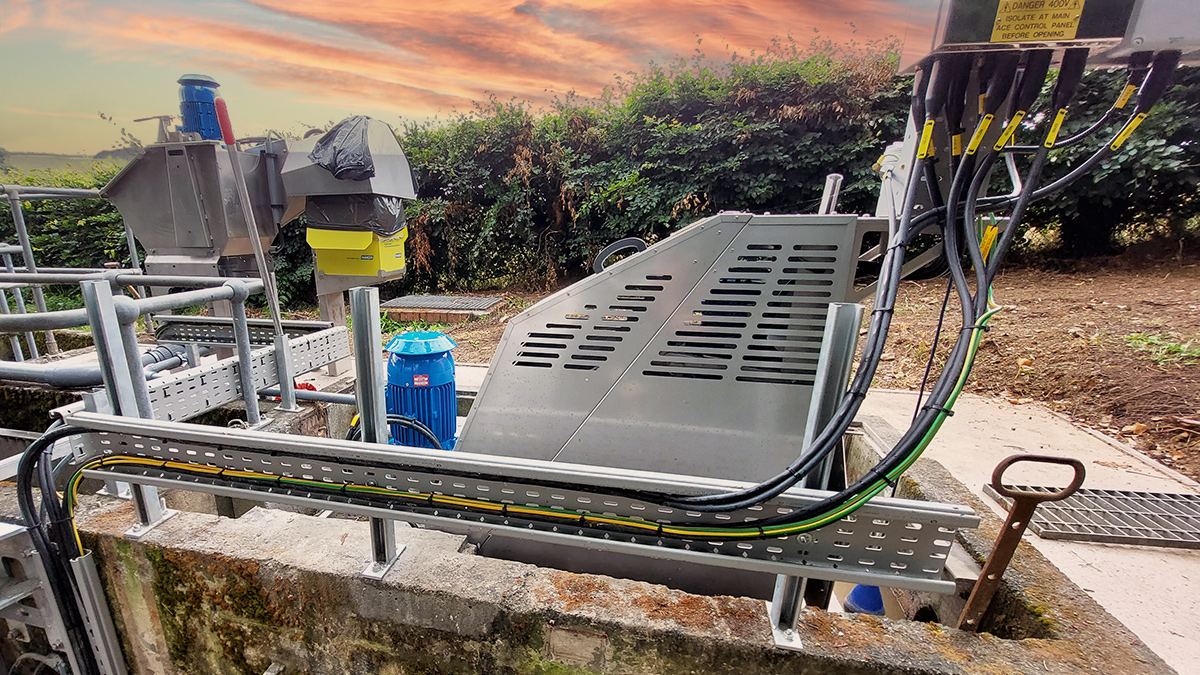
Drewsteignton STW screen in foreground and LISEP tucked behind – Courtesy of Galliford Try
Inlet Enhancement Projects: Supply chain – key participants
- Project delivery: Galliford Try
- Civils design: Fishtek Consulting
- Civil engineering: CR Civil Engineering
- Electrical installation: AGT Electrics
- Screen supplier: Haigh Engineering Ltd
- Pumping: Pump Supplies Ltd
Innovations
Galliford Try used a specialist expanding grout for the controlled breaking out some of the civils structures on some of the sites. The process required small holes to be drilled into the structure and then the grout was mixed and poured into the holes. This took 18 hours to work and expand. The slow expansion then broke each structure away with minimal dust, noise, and risk due to the lack of potential for flying debris. In addition, this methodology significantly reduced hand and arm vibration exposure.
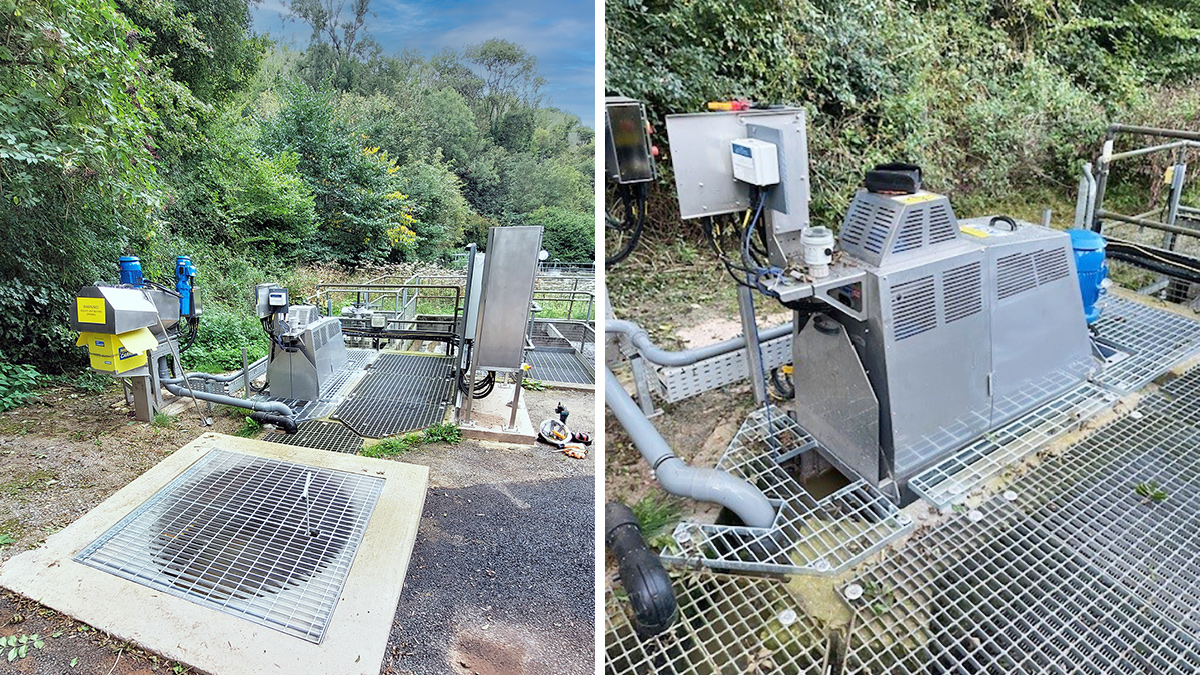
East Ogwell STW: (left) overall view of inlet and (right) new screen in place – Courtesy of Galliford Try
Risk management
Primarily, a lot of the design was undertaken up front with multiple visits to site to confirm what was required and at this stage high risk tasks were either worked around or agreed upon up front. Risks were further mitigated by good planning and communication with all parties on site. Any risks that did occur were communicated back to the client for further instruction.
Results
- Cost savings: Galliford Try added value by minimising costs on equipment and man hours on each project as the projects were repetitive and design did not change much. Through multiple sites and screens of the same nature, efficiencies were gained. The use of Galliford Try`s in-house capabilities to fabricate and produce the control panels benefited the overall programme of works. This enabled a succedent programme of works to be maintained throughout with zero incidents on site.
- Carbon savings: With the sites being in close proximity there were carbon savings on travel and by ordering multiple units at the same time, there were carbon savings in the delivery of plant to sites.
- Health & Safety: Minor works health and safety plans were produced along with all site information compiled on site. Zero accidents or incidents were reported over an average of 810 man hours per site
Engagement
Galliford Try was heavily engaged with operations through pre-construction to delivery and closeout, ensuring that all snag items were closed out efficiently and the end user was happy with the solution provided.