Little Eaton WTW (2016)
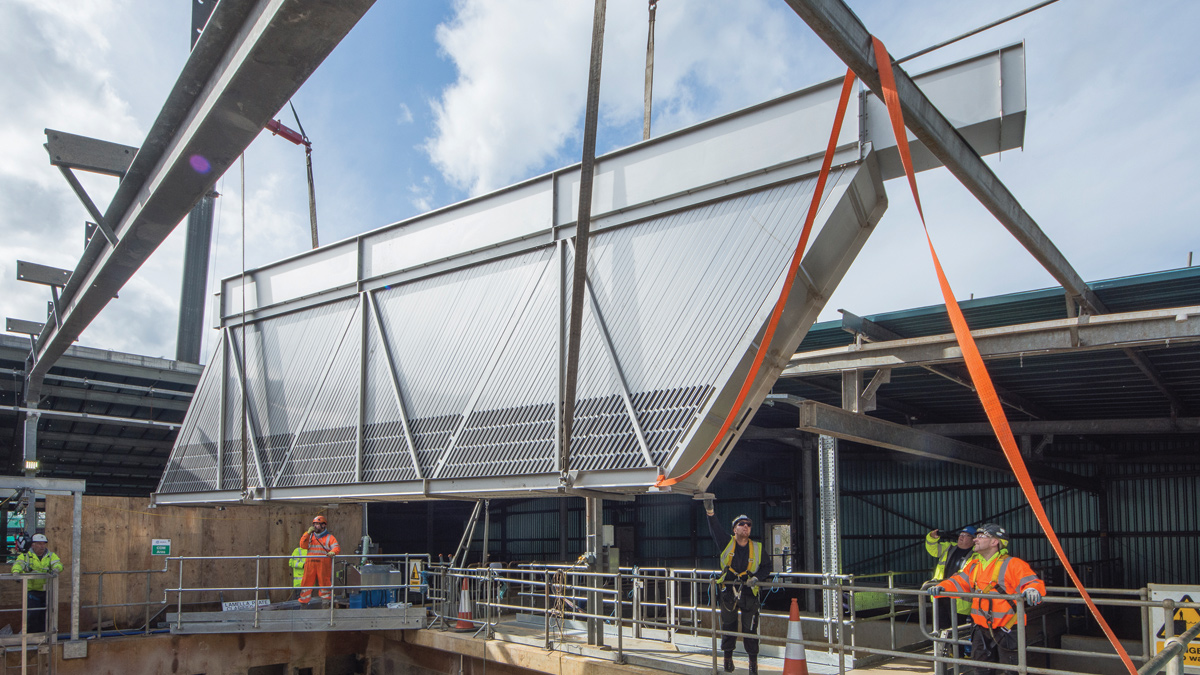
One of the new Lamella plates being lowered into position - Courtesy of Hydro International
Little Eaton Water Treatment Works is located approximately 4 miles north of Derby just off the A38. The works supplies safe, clean drinking water to the growing community of north-west Derby and was originally designed for a maximum water output of 85MLD. The operational efficiency had been severely compromised due to a number of factors and the equipment was in need of a major overhaul; in particular the fragile lamella plates, which were life expired and required extensive labour to maintain efficient water production output.
Background
The existing works process consists of the following operations:
- Raw water inlet pumping station.
- Lamella clarifiers.
- Rapid gravity filters.
- Granular activated carbon.
- Disinfection contact tank.
- High lift pump station into supply.
The need for change
The clarifier tanks in which the lamella plates were housed required draining every two weeks just to keep the plates clear of sludge build up. This was a maintenance-intensive task that was further complicated by a troublesome scraper system, which was prone to mechanical failure that resulted in scraper blades falling off. Diagnosing the problems required the isolation of equipment and removal of sludge build-up in order to make a thorough assessment.
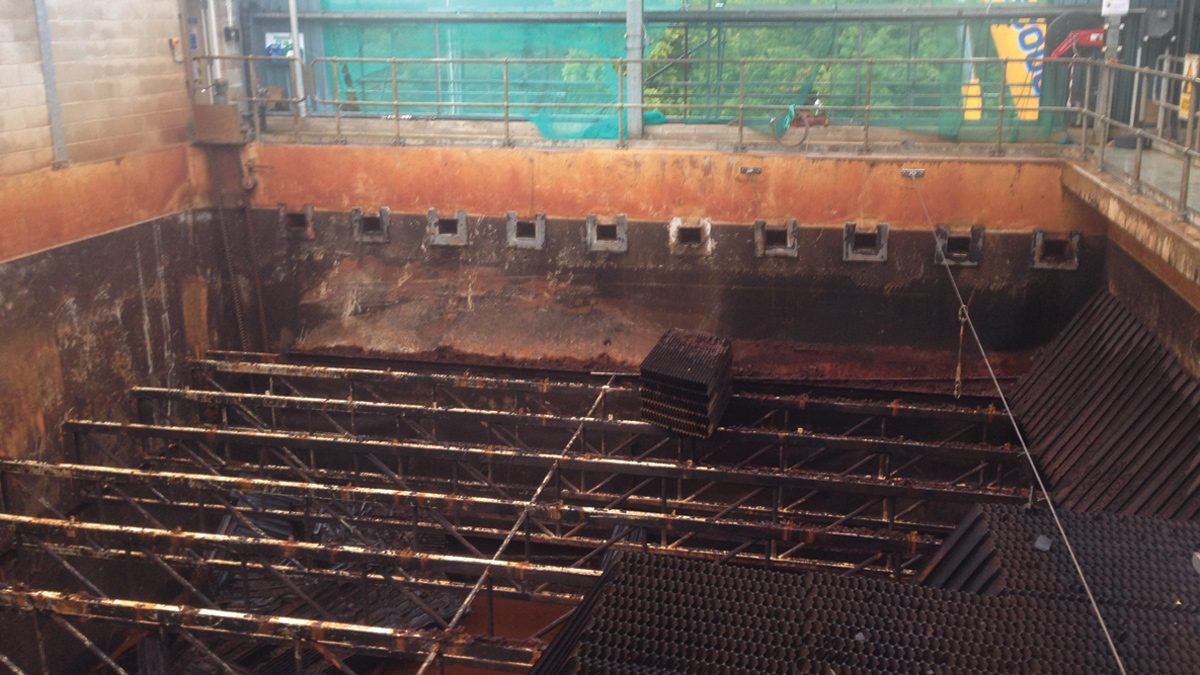
Old lamella pack removal with safety wires – Courtesy of MWH
Engineering a solution
The team comprising MWH Treatment, Hydro International and Severn Trent Water set to work refurbishing the 2 (No.) lamella tanks using innovative design in deeper than normal lamella packs to provide the required quality and flow output. They considered ways to improve access to the equipment in order to facilitate future maintenance operations.
The design also looked at the access for any future cleaning down and maintenance requirements and positioning of a new control panel in an already very tight environment.
It took a team of dedicated professionals to implement a solution, but it was anything but clear how the task would be accomplished or if they could deliver the solution by the completion date established by the Drinking Water Inspectorate
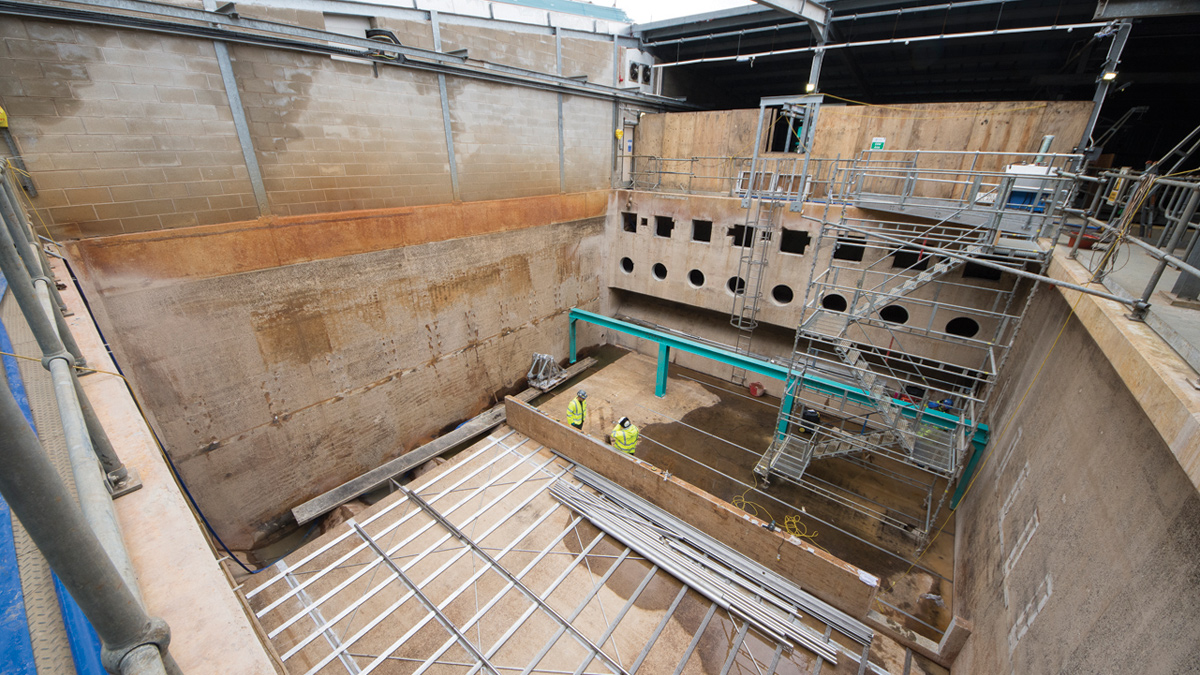
The existing settlement tank (with roof removed for access – Courtesy of Hydro International
Challenges
The challenges started on day one, as the team sorted out the plethora of operational and functional problems at the 20-year-old facility:
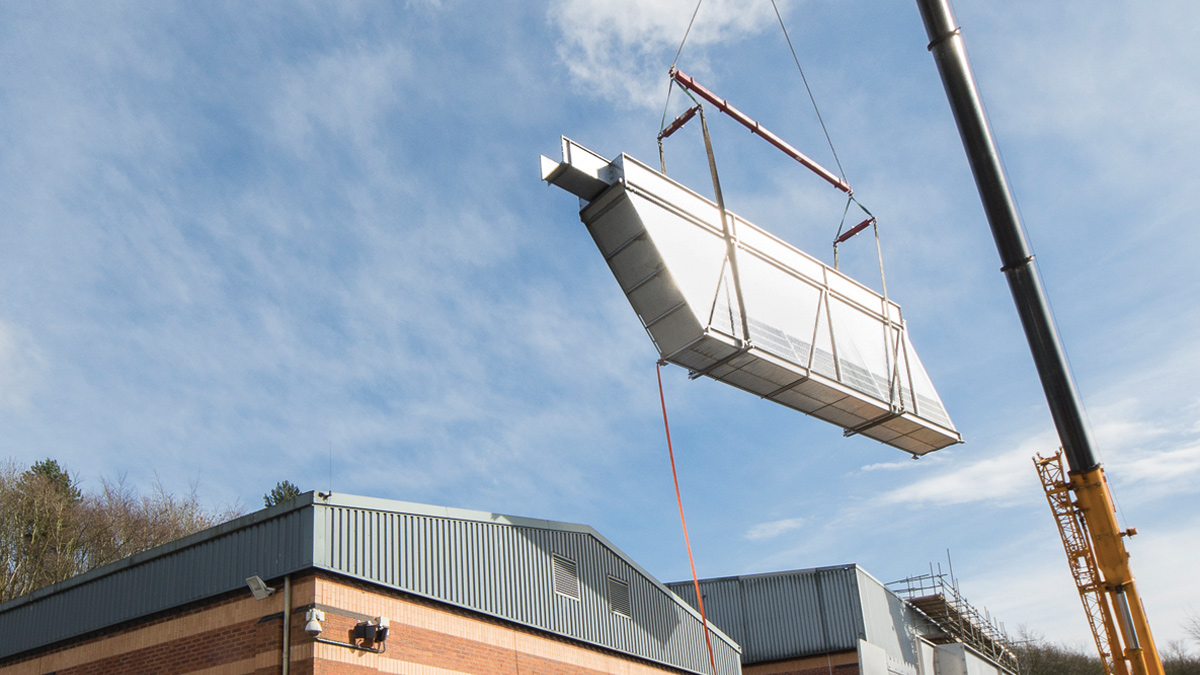
Crane lifting in the new Lamella plate – Courtesy of Hydro International
- The new lamella plates, the first of its kind in the UK, are larger than the traditional plates, and a lot of time and collaborative working between all parties was necessary to ensure proper fit and function in the existing settlement tanks.
- There was a need to understand the best way to secure removal of the old plant from the existing tanks. This was achieved by carrying out assessments in order to estimate the weight of the old units and how fragile the existing lamella packs might be. Additional planning was required to establish how to deal with the significant amounts of heavily compressed sludge on the old lamella packs and in the base of each tank.
- Working in conjunction with two other major capital schemes (sludge improvements and rapid gravity filter refurbishment) greatly increased the need for good communication and careful clear planning. Good coordination was essential for the lifting operations to crane in and install the new and significantly larger build packs. The build packs had been manufactured off site and delivered insitu within the existing settlement tanks.
- The Little Eaton WTW project teams needed to find a safe and secure way to access the existing plastic lamella packs for removal. It was essential to provide a stable lifting platform around critical services to position a 100 tonne crane to allow the 16 (No.) pre-constructed 10m long lamella packs weighing over 4 tonnes to be lifted. Consideration was also given to of removal of side wall panels to prevent imploding of lamella structure due to wind loads.
All these works were to be carried out whist causing minimum disruption to the existing water supply.
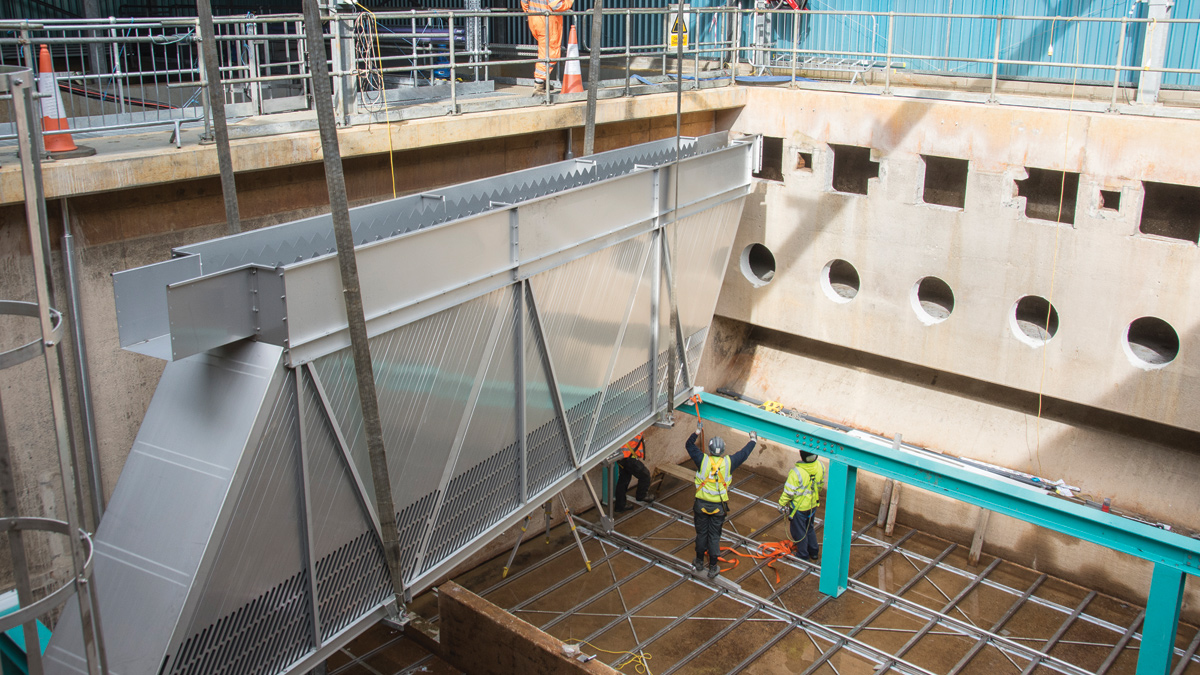
New lamella plate being positioned into the final settlement tank – Courtesy of Hydro International
Innovative working
Whilst it was recognised that the first tank would pose some challenges due to nature of construction, MWH looked at providing safety wires stretched along the length of the lamella packs by which the operators could move around the area with a hitching process similar to high tree trekking.
Initial attempts at removing the old lamella packs proved cumbersome and long winded due to the packs breaking up and splitting so the MWH operators came up with a fabricated combination of straps and a steel lifting device which was easy to manhandle and set up and once implemented, saved approximately 60% on the removal time.
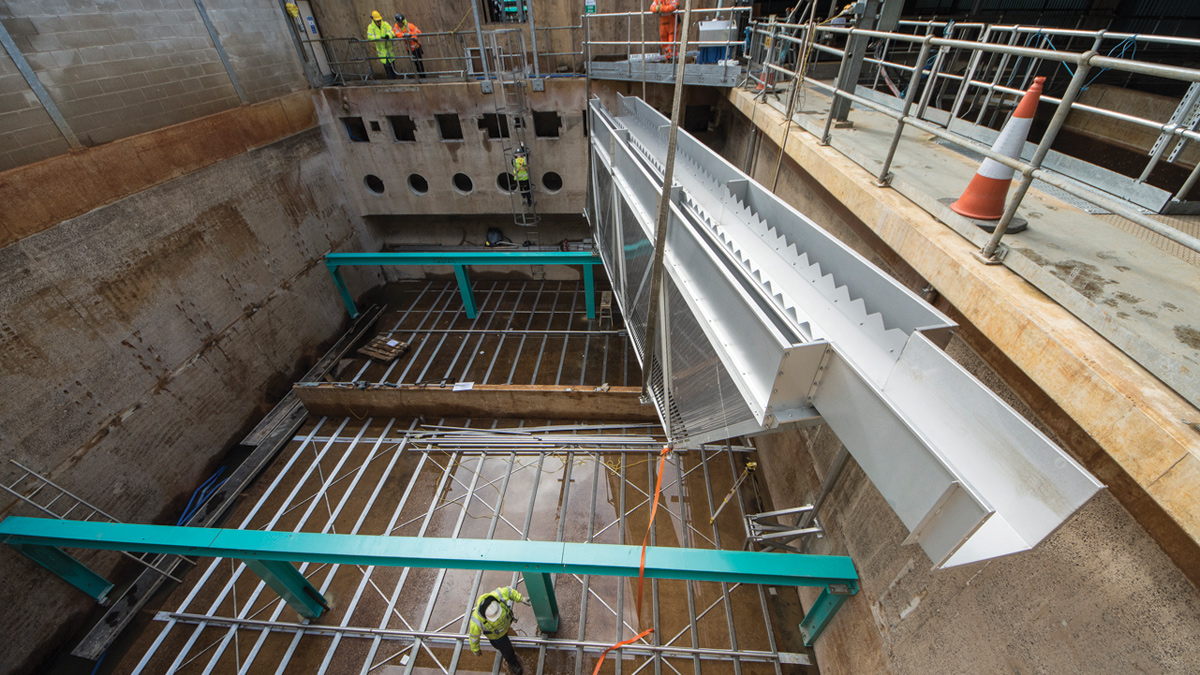
Lowering Lamella plate into position – Courtesy of Hydro International
By utilising the position of the crane during the removal the redundant equipment in the tank, it was possible to build the new Lamella packs offline in controlled assembly line conditions. This was in readiness to lift the plates into the tank, reducing overall project time and health and safety risk associated with spending time in the tank.
With the collaborative efforts and dedication from the MWH Treatment, Hydro International and Severn Trent Water teams, this date was achieved three months ahead of time with the first tank gaining ‘plant in use’ on 22 December 2015.
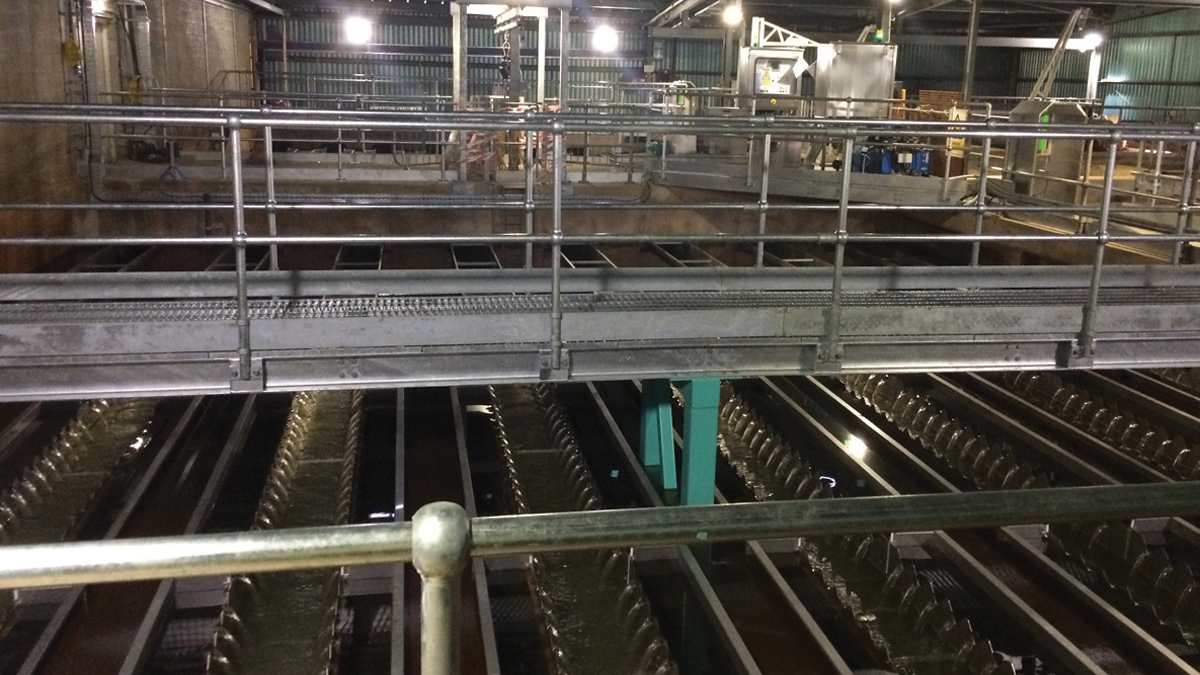
Final installation of lamella – Courtesy of MWH
Leaving a lasting legacy
The site team have optimised the new system to prove that a single tank can operate at 60MLD and at present a combination of the 2 (No.) tanks can achieve an increased output of 120MLD.
The second tank was completed, and ‘plant in use’ achieved, on 19 April 2016. The first tank has been drained and inspected after 6 months of operation and all found to be in good order.
By adopting a factory thinking approach and building off-site, the profiles of the plates were delivered to site prior to assembly in the tanks. The new plates were installed in 2 days, a task that would traditionally take around 6 weeks. By using this method the teams were able to reduce cost, time on site and eliminate risks.
By isolating the one tank at a time MWH was able to maintain the existing water supply causing zero disruption to the people of north-west Derby.
The new lamella plates are heavier and longer than the previous plates making it easier for larger quantities of flock to settle enabling the plant to process larger volumes of water effectively.
Conclusion
As a result of the works, the plant will serve the community of north-west Derby for many years to come and with the population anticipated to continue to grow the site is equipped to accommodate this growing population and the extra demand on the water supply by increasing the potential output from 90MLD to 120MLD per day.