Macclesfield WwTW (2024)
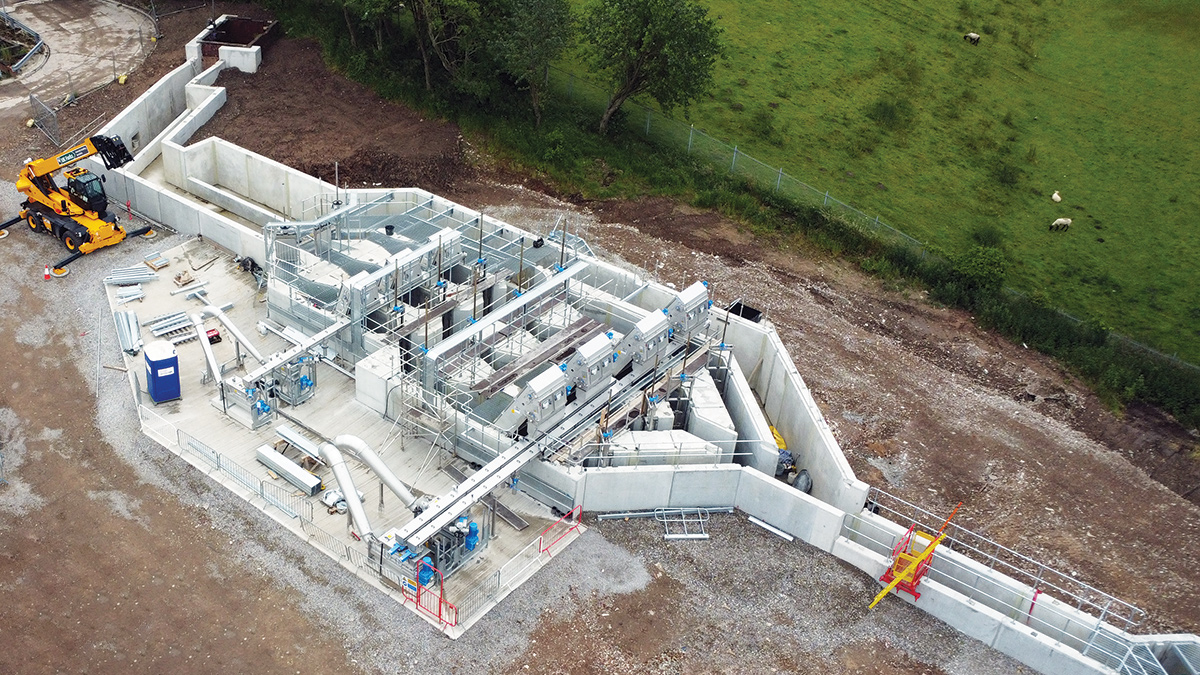
New inlet works at Macclesfield WwTW - Courtesy of C2V+
Macclesfield Wastewater Treatment Works is located north-west of the market town in Cheshire. The Macclesfield WwTW project is one of United Utilities’ largest projects with an investment value of £59m. The project is being delivered in collaboration with C2V+, a joint venture between VolkerStevin and Jacobs. This case study details the Macclesfield solution which involves a significant site upgrade, including the Mobile Organic Biofilm (MOB)TM plant technology. The MOBTM at Macclesfield will be the first to be commissioned in the UK to meet the December 2024 regulatory commitment date.
Tightening consents
Under the new consents Macclesfield WwTW is required to serve a 2035 population equivalent of 82,679 with a final effluent quality of 0.3 mg/l Total Phosphorus (TP), tighter ammonia consents of 2mg/l ammonia on a 95th %-ile basis, and 12 mg/l ammonia as an upper tier limit. The works must also provide UMON_3 spill and UMON_4 flow to full treatment monitoring.
The works has a discharge permit with a flow to full treatment limit of 61,430 m3/day and a dry weather flow limit of 28,500 m3/day.
Preliminary treatment
The area for the inlet works had limited working area space. To minimise the interface with existing live plant at the inlet, the team chose to use an off-site manufactured precast construction approach for a majority of the new inlet works. The precast design incorporated 218 precast panels and two precast raker beams. Utilising this construction technique, with design for manufacture and assembly (DfMA), had several advantages including:
- An 80% reduction in site personnel.
- A 95% reduction in working at height activities.
- An 80% reduction in on-site wet concrete and reduction in people-plant interface.
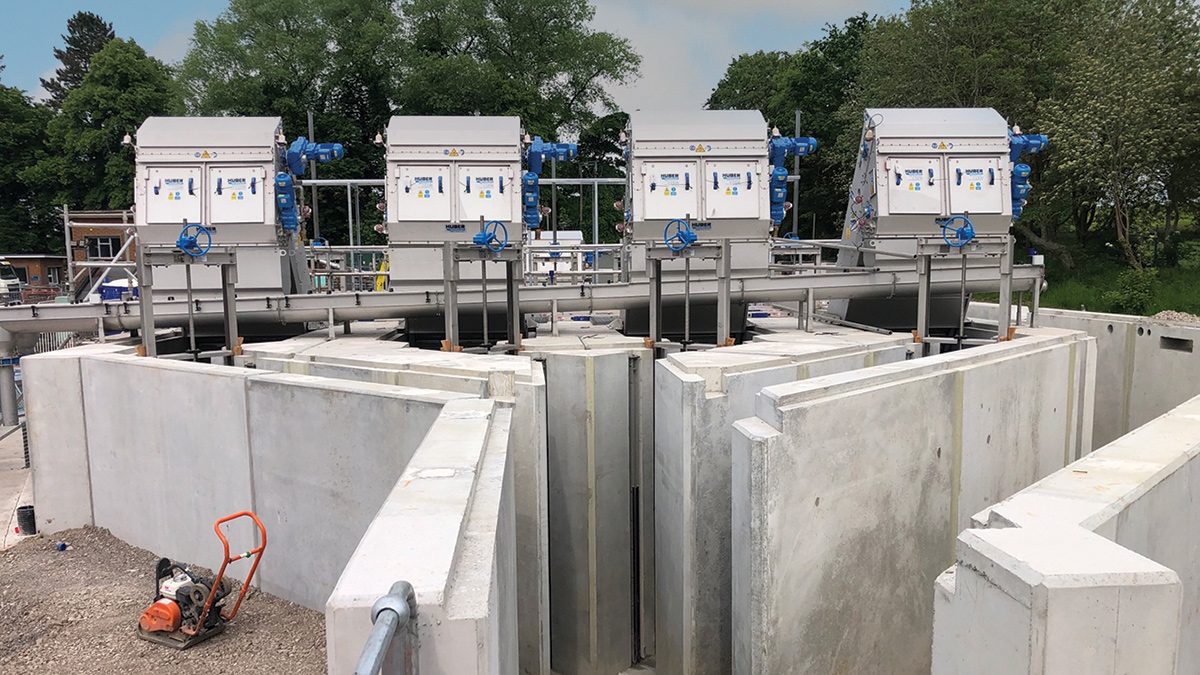
Inlet works screens – Courtesy of United Utilities
The delivery strategy involved 79 shipments direct from Shay Murtagh Precast in Ireland, as opposed to a minimum of at least 250 concrete wagons. This resulted in substantial carbon savings in transportation of rebar and concrete; approximately 50% reduction in embodied carbon, along with minimised local nuisance and disturbance and reduced material wastage.
At the time of writing (July 2024) the precast inlet has passed its water test and mechanical and electrical installation is in progress.
In addition, a new interception chamber has been constructed to collect flows from Macclesfield and Bollington Sewers alongside three new coarse screens and screen management within the precast inlet. Four new fine screens, a new grit removal stage situated within the precast inlet, storm flow to full treatment (FtFT) separation, and MON_3 and MON_4 monitoring are also included.
A new wet well submersible primary treatment feed pumping station has been constructed which comprises four pumps to transfer FtFT plus returns to a new distribution chamber, which splits flows to the north and south primary settlement tank groups.
Three new launder pumps have been installed to transfer water to enable cleaning of the launder trough. There is a new below-ground culvert to connect storm water overflow to the existing storm tank feed channel. Drainage from Pump Station 2 and the admin building has been diverted into the new inlet works. Furthermore, there is a new MCC kiosk at the new inlet works. The site solution will reuse the existing storm tanks.
The inlet works precast concrete approach resulted in substantial carbon savings in transportation of rebar and concrete. There was a reduction of approximately 50% in embodied carbon, along with minimised local nuisance and disturbance. There was a 42% reduction in time to construct against the original in situ plan and reduced material wastage.
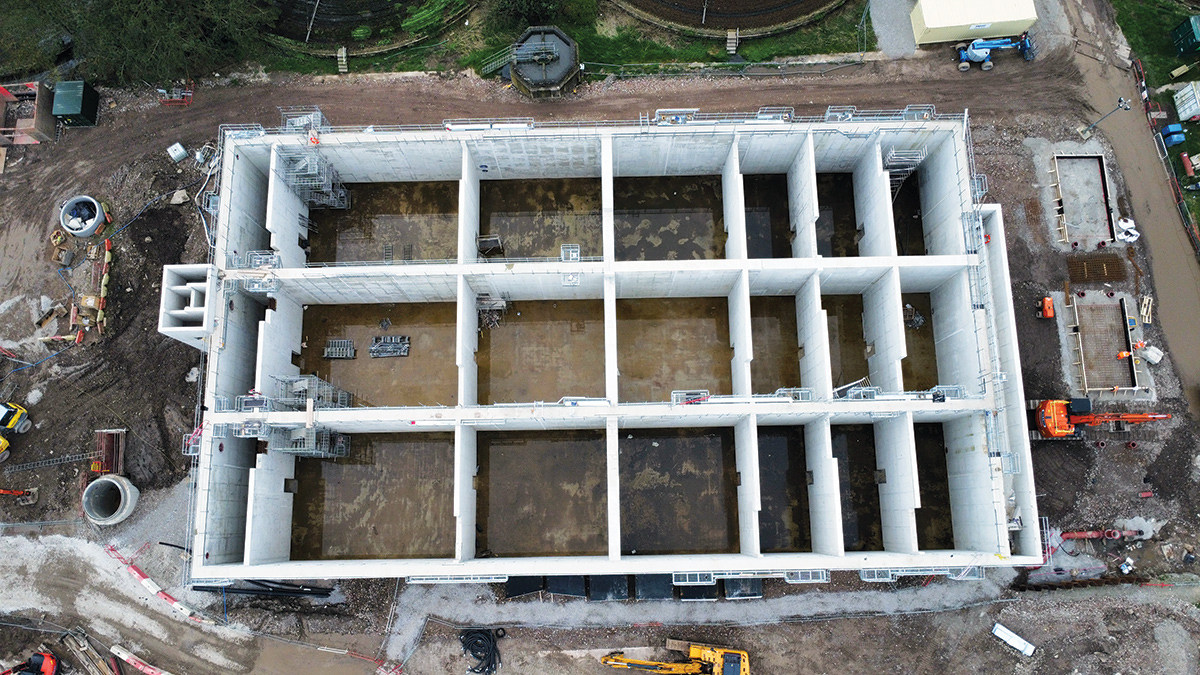
Drone image over the MOBTM plant cells – Courtesy of C2V+
Secondary treatment
The secondary treatment area solution includes a new final settlement tank distribution chamber, replacing the half bridge scrapers and reusing the existing final settlement tanks (FST). Each FST features new dedicated return activated sludge (RAS) and surplus activated sludge (SAS) pumps and new scum pipework.
Mobile Organic Biofilm (MOB)TM technology has been constructed in the secondary treatment area as an innovative and efficient solution. The media is a first for the wastewater industry’s (being a green, renewable plant-based media with a high surface area) and this is now on site, with the test plant running with parameters in place to measure settleability.
The MOBTM plant has been configured to allow future adaptation to an integrated fixed film activated sludge (IFAS) system including overall sizing, zoning and aspect ratio of the cells as future-proofing.
The MOBTM technology will be able to achieve nitrification and enhanced biological phosphorus removal (EBPR). The solution intends to improve settleability, help treatment capacity, provide nutrient removal, and enhance process stability.
There will be new pipework connecting the existing primary settlement tanks (PSTs) to the new MOBTM plant and a new wet well submersible MOBTM feed pumping station. There will be five blowers from Aerzen Machines to provide air demand from the MOBTM plant, two drum screens on the SAS line to recover MOBTM media, and six mixed liquor recycle pumping stations.
Whilst the civils work is complete, the mechanical and electrical installation is ongoing. The blowers have arrived on site and the secondary treatment area MCC kiosk has been delivered.
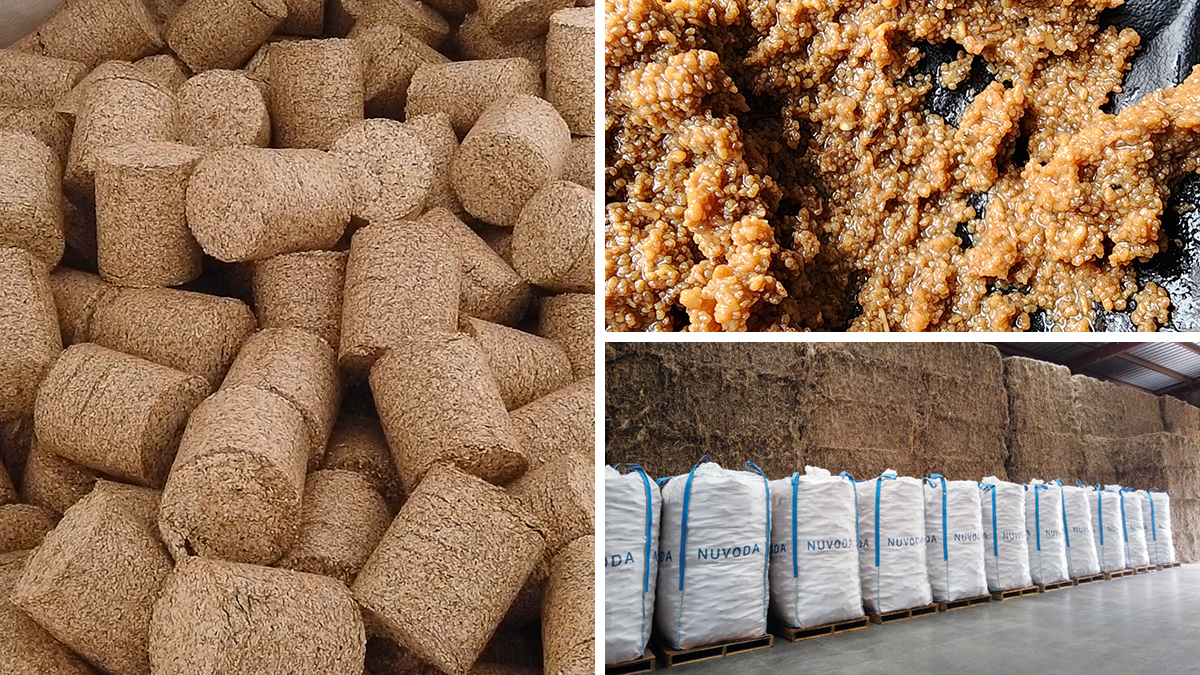
(left) MOBTM briquettes, (top right) fully developed biofilm on MOBTM media and (bottom right) MOBTM media – Courtesy of Nuvoda
Tertiary treatment & sludge handling
The tertiary treatment solution utilises Mecana tertiary pile cloth filters (TPCFs) for solids removal and these have arrived on site. The sludge handling system features:
- A new SAS draw off point to drum filters.
- A surplus activated sludge transfer pumping station to transfer SAS to the SAS thickener storage tank.
- A thickener for SAS feed storage tank and rotary drum thickener feed pumping station.
- New SAS air mixing system on the thickened feed storage tank.
- SAS thickening utilising rotary drum thickeners.
There are new thickened sludge transfer pumps, a new roof on an existing sludge tank and reuse for thickened sludge storage, and a new odour control system for the surplus activated sludge.
In addition, there is a pump mixer on the thickened sludge tank, and a new wet well submersible liquor returns pumping station comprising fixed speed pumps to return filtrate from the rotary drum thickeners and the Mecana tertiary pile cloth filters.
Finally, there is a new final effluent wash water pumping station comprising a packaged booster set inside a new kiosk and a new externally located buffer storage tank and automatic backwashing filter will be installed at the pumping station.
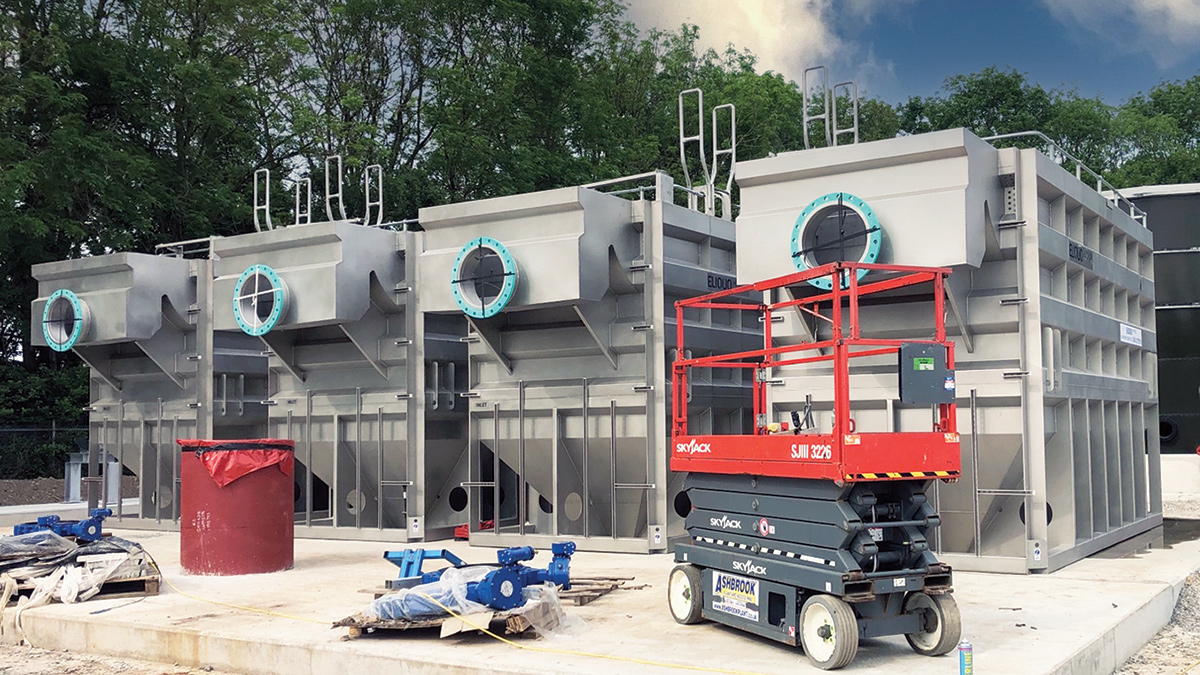
Mecana tertiary pile cloth filters – Courtesy of United Utilities
Macclesfield WwTW: Supply chain – key participants
- Delivery contractor: C2V+ JV
- Jacobs
- VolkerStevin
- MOBTM process: Nuvoda LLC via ACWA Services Ltd
- Mechanical installation: JBF Group
- Mechanical installation: Mectec Ltd
- Electrical installation: Eric Wright Water Ltd
- HV installation: Austin-Lenika Ltd
- Civils & pipework: LCS Pipework Ltd
- Sheet piling: VolkerGround Engineering
- Precast structures: Shay Murtagh Precast
- GCS storage tank: Tank Consult Ltd
- FRC: Offafix Formwork Ltd
- Reinforcement: Capital Reinforcing (Ireland) Ltd
- Concrete: Tarmac Ltd
- Systems integration: Tata Consultancy Services
- Motor control centres: Lloyd Morris Electrical Ltd
- Inlet screens: Huber Technology
- Scraper bridges: Graham Steelworks & Engineering Ltd
- Odour: Air-Water Treatment Ltd
- Detritors: ACWA Services Ltd
- Aeration package: Suprafilt Ltd
- Blowers: Aerzen Machines
- Wastewater pumps: Xylem Water Solutions
- Wastewater pumps: Hidrostal Ltd
- Wastewater pumps: Sulzer Pumps Wastewater Ltd
- Booster sets: Grundfos Pumps Ltd
- Mecana tertiary pile cloth filters: Eliquo Hydrok Ltd
- Penstocks: Glenfield Invicta Ltd
- Polymer dosing: Hydroklear Ltd
- Ductile pipework: Saint Gobain PAM UK
- Access metalwork: Steelway Fensecure Ltd
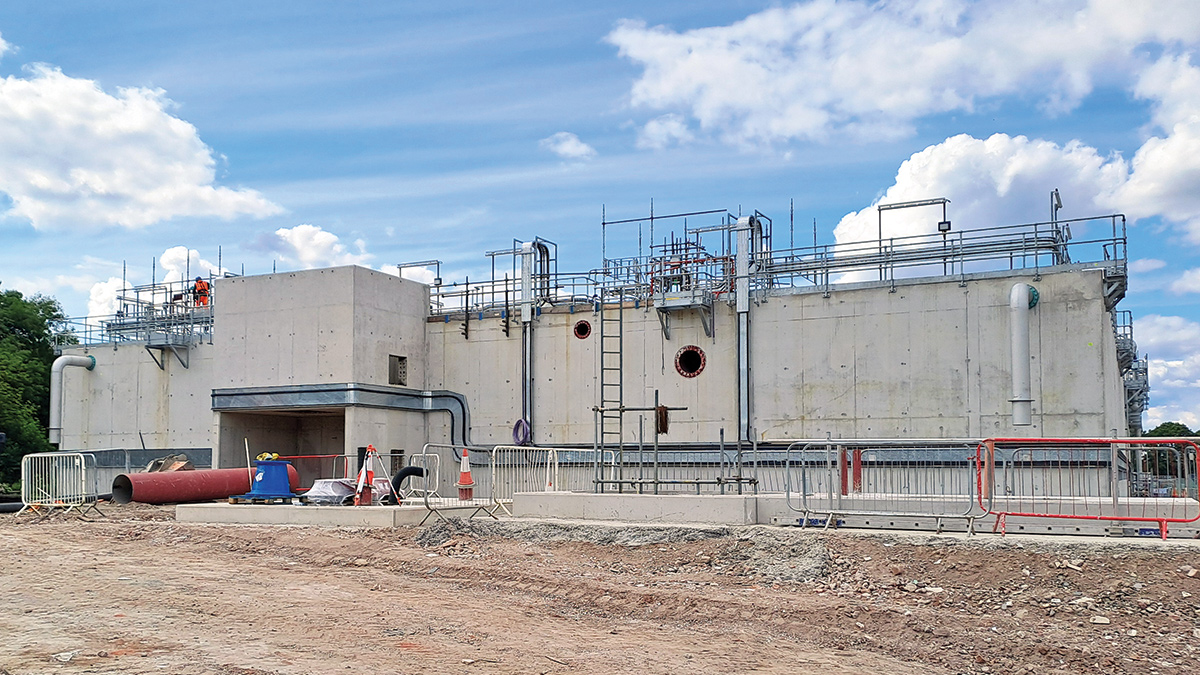
MOBTM plant – Courtesy of United Utilities
Value engineering
Whilst defining the solution for Macclesfield WwTW, it was identified through value engineering that the final settlement tanks, the existing sludge tank, and the storm tanks could be reused, and the requirement for additional primary thickened sludge storage could be removed.
The MOBTM technology eliminates the need for internal sieves and additional main flow screening. There is no micro-plastic generation and therefore less environmental risk, and improved settlement of sludge.
Further value engineering opportunities included:
- The RAS wet well was removed and replaced with dry bund for close coupled pumps.
- The tertiary pile cloth filter plant was moved to the north, avoiding the need for a large deep cofferdam.
- The MOBTM plant was sunken to mitigate piling requirements.
- Secondary actuated penstocks at the inlet works was replaced with manual penstock.
- Sacrificial valves were included in the permanent design for flow paths to avoid extensive temporary pumping requirements during commissioning.
- Launder filtrate returns into common pumping station.
- Walkways to MOBTM side-mounted handrailing.
- FST underslab pipework could be reused.
- Reduction and change in material for final effluent pipework.
- MMP to undertake materials processing for reuse at inlet works.
- Chemical delivery area relocated.
- Ferric dosing removed.
- Roads and paths installation reduced.
- Gas membrane requirements reduced.
- Elimination of new Admin, PS1, and PS2 pumping mains.
- Utilisation of a trough system in lieu of ducting and drawpits where possible.
- Inclusion of sacrificial below-ground systems for commissioning.
- Isolation/sluice plates for flow management during process commissioning.
- Reduced access metalworks site-wide, including removing the MOBTM north-side staircase
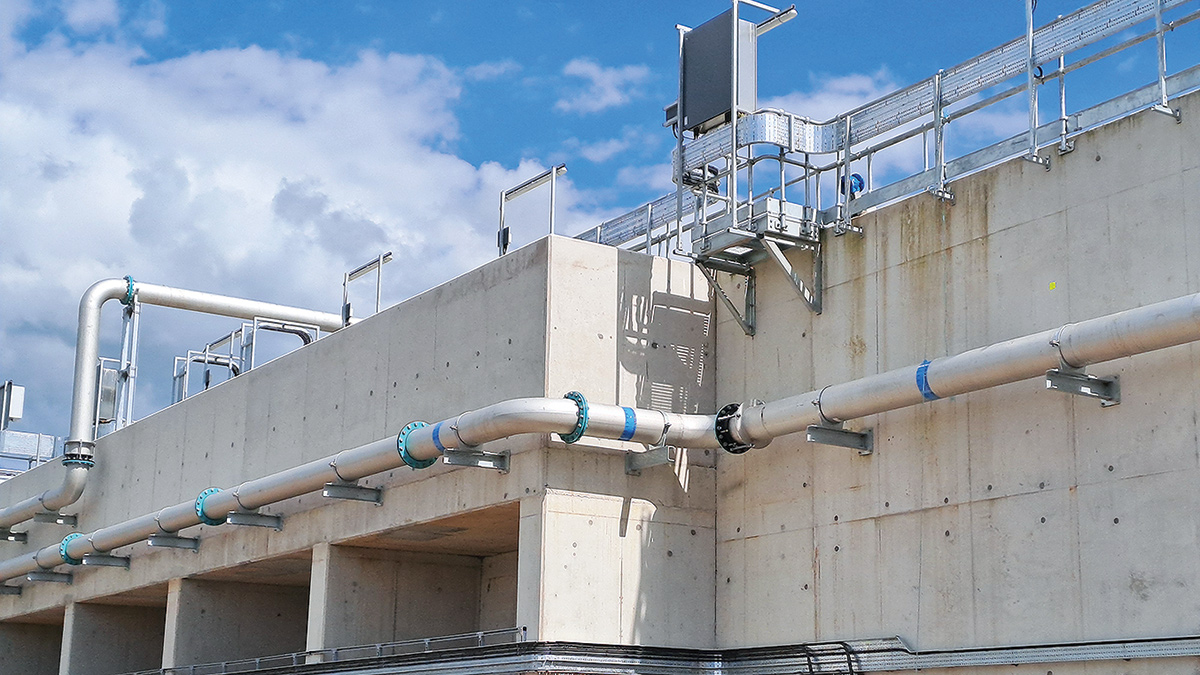
MOBTM plant – Courtesy of United Utilities
Health & Safety
For such a large scale, complex project with three working areas on site, there have been health and safety challenges and without collaboration from the outset, the project would have not been a success. Despite there being multiple sub-contractors on site at the same time, limited working areas, working on a live operational site, operations interface, and stakeholder interface, the project team have worked seamlessly together to meet the project’s requirements.
Next steps
The next stages of the project include connecting the power upgrade to all three sections of site, seeding flows through the MOBTM plant, and diverting the flows through the new inlet and integrated treatment works.
Site-wide software installation, commissioning end to end testing, and optimisation of the solution follow, in order to meet the December 2024 regulatory commitment date.
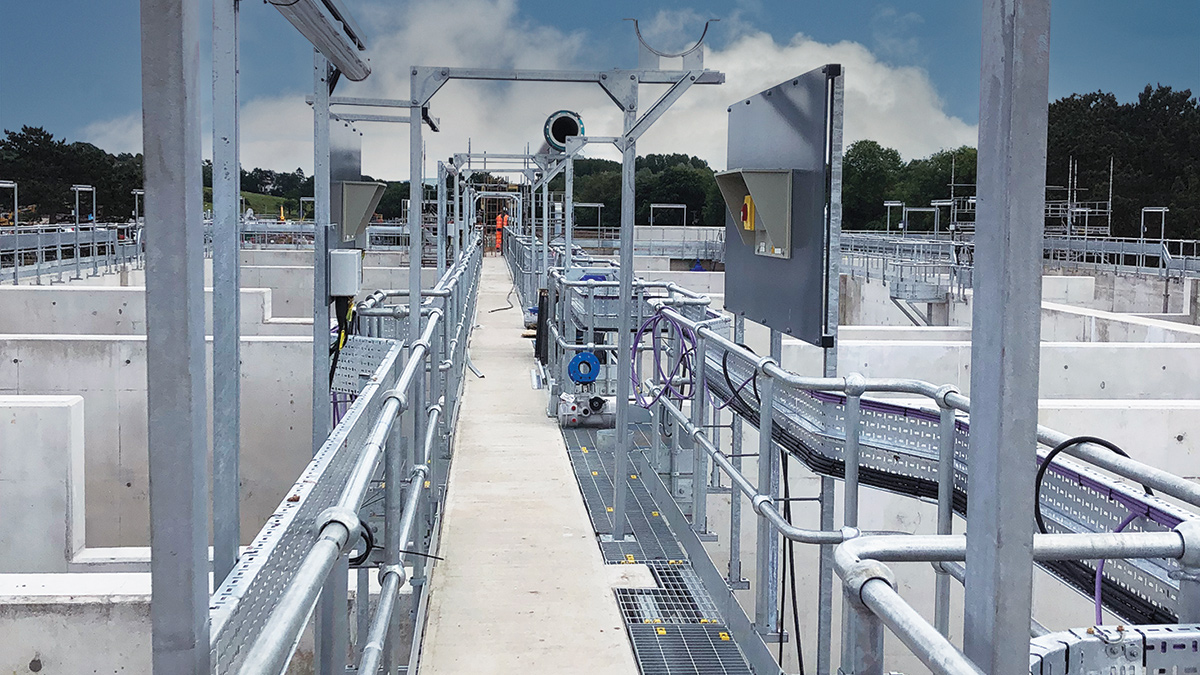
Top of the MOBTM plant - Courtesy of United Utilities