Minworth STW – Thermal Hydrolysis Plant (2017)
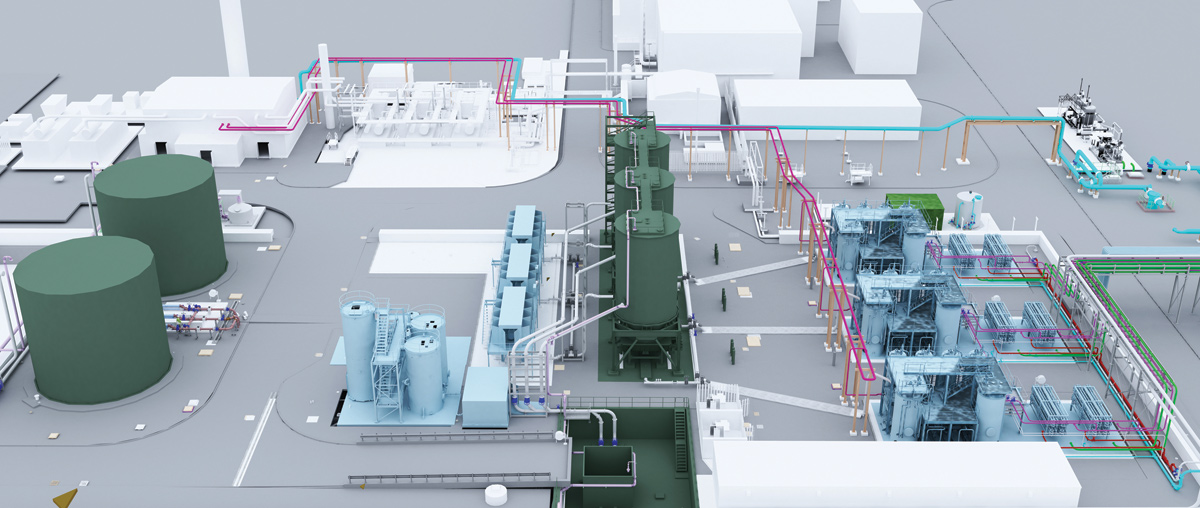
Minworth Thermal Hydrolysis Plant general arrangement - Courtesy of MWHT
Minworth STW is Severn Trent Water’s largest sewage treatment works and serves a population equivalent of 1.75 million from Birmingham with full flow to treatment of 1,070Ml/d. The works treats sludge arising from a population equivalent of 2.3 million which is made up of indigenous sludge plus imported sludge from the nearby Coleshill STW and various works in south Staffordshire and north Warwickshire. Minworth is Severn Trent Water’s largest renewable energy facility with 8MW CHP capacity and biogas to grid which produces 30% of their green energy. The Thermal Hydrolysis Plant (THP) project will further enhance renewable energy production by increasing the biogas yield.
Background
As part of their PR14 submission to OFWAT, Severn Trent made a commitment to cut their total carbon footprint by 10% through AMP6 and convert 25% of all of their biosolids to an enhanced status product. The THP will have capacity to process 250 tonnes of dry solids per day at peak with 3 (No.) streams and 198 tonnes of dry solids per day at average throughput. Severn Trent expects to realise significant benefits as a result of the investment required for a THP of this scale which will be one of the largest in the UK. These include:
- TOTEX benefit from revenue increase and OPEX savings.
- Enhanced status sludge cake (pathogen free).
- Reduced carbon footprint (this project delivers a third of STW’s 10% reduction target for AMP6).
- Improved dewaterability of the sludge to increase cake dry solids and reduce volume.
- Increased capacity for sludge treatment from existing assets avoiding CAPEX.
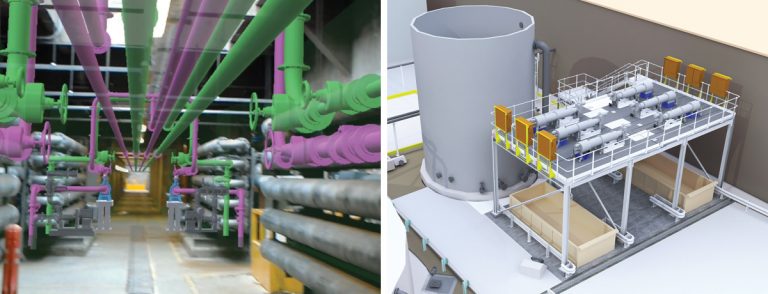
(left) Digester gallery recirculation pipework augmented reality and (right) primary sludge screens – Courtesy of MWH Treatment
Plant description
The new THP will be installed upstream of the existing digesters. Liquid imports, indigenous thickened surplus activated sludge (SAS) and screened primary sludges are blended in existing tanks then transferred utilising existing ram pumps to new buffer tanks for dewatering by centrifuges. Cake transfer pumps with boundary layer injection will transfer the dewatered cake (target 22% dry solids) to three reception silos then after further dilution to 16.5% into the three parallel Cambi THP streams.
Each stream consists of a pulper, 4 (No.) reactors and a flash tank. Steam is supplied by 3 (No.) dual fuel boilers with waste heat recovery from 5 (No.) CHP gas engine exhausts. The hydrolysed sludge is diluted 3:1 with recirculated sludge, then cooled in heat exchangers and pumped to the existing 12 (No.) digesters.
Each THP stream has 2 (No.) heat exchangers each connected to a pair of digesters. Biogas will be stored in 2 (No.) new gas holders then boosted to 33mbar to supply the CHPs and boiler siloxane plant.
Digested sludge will be dewatered using the 10 (No.) existing Klampress units and the enhanced product will be stored on the cake pad. Final effluent will be filtered in two stages with 300 micron and 50 micron auto backwashing strainers then sterilised with UV to prevent contamination of the enhanced product.
Early contractor involvement
The feasibility phase was improved by a collaborative approach with MWH Treatment appointed to verify the concept design and develop a fully priced solution with sufficient detail to sign up to the contract for the design and construction. The integration of the THP process into the existing assets was extremely complex and required extensive site investigations and discussions with the operations team to evaluate impacts.
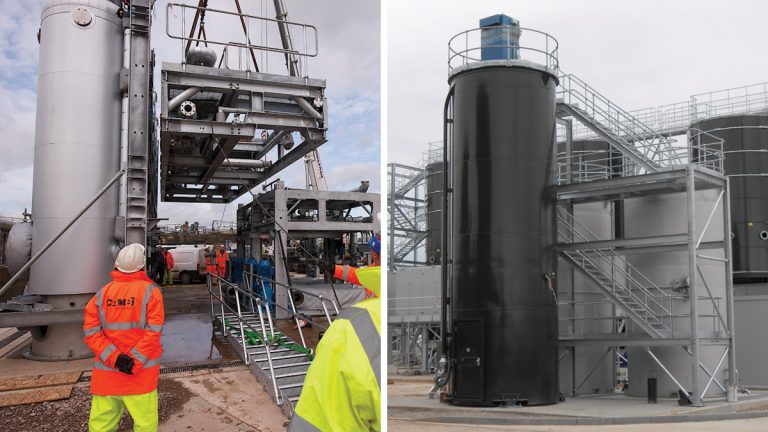
(left) Assembling the Cambi modules and (right) polymer dosing system – Courtesy of MWH Treatment
Capturing lessons learnt
MWH has been involved in numerous thermal hydrolysis plant projects both from a client engineer consulting role and as principal contractor, which enabled a comprehensive review of the major THP installations to be carried out to ensure real-time operational feedback was incorporated into the design.
The design and operations team visited a number of sites and saw first-hand the issues to be addressed.
Process engineering was based on best practices from the reference sites and specialist knowledge from the supply chain. Technical and commercial performance of the key process equipment subcontractors was used to formulate the procurement strategy which has been strictly adhered to at contract stage.
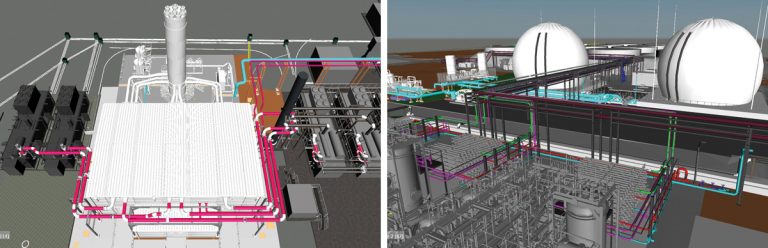
(left) Boilerhouse waste heat ducting and siloxane plant and (right) double membrane gas holders – Courtesy of MWH Treatment
Digital delivery approach improves project delivery
The implementation of Digital Delivery approaches have been used to enhance the quality and efficiency of the design and construction processes from concept to commissioning.
The most innovative part of this project can be coined as ‘Virtual Project Preparation’ (VPP) which includes:
- Laser-scanning of the existing assets enabled us to design and visualise concepts in context with the wellbeing of all employees in mind.
- 3D model conversion of the laser scan enabled us to develop the concepts into detailed designs with method statements for assembly and commissioning plans.
- Federated 3D models and fly-throughs utilised to fully integrate the process plant.
- 4D scheduling combining the 3D and the construction programme in a visual form.
Real incentives have been recognised in delivering this project ahead of the programme to realise increased benefits. There is a commitment from all to explore and promote new ideas in the live project environment even though many are working outside their comfort zones.
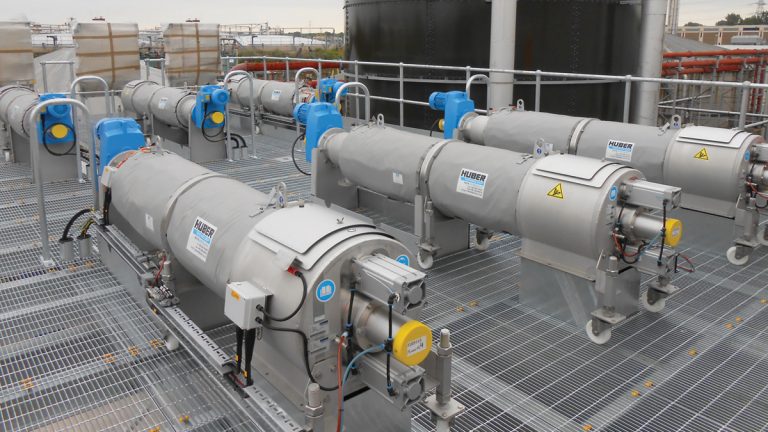
Primary sludge strainpress installation – Courtesy of MWH Treatment
Increased health and safety benefits with digital delivery
Reducing H&S risks on site is always at the forefront of our minds and Digital Delivery is helping to further reduce risks such as:
- Reducing confined space access: Laser scanning of the digester galleries has benefited the design of the complex recirculation pipework and pumping systems by reducing the number of designers who need to access the gas test confined space.
- Virtual reviews of safety, ergonomics and general accessibility: The Augmented Reality (AR) approach has enabled the site operations team to get a first-hand perspective of our design intent in advance of it being built. This is really valuable as it gives the opportunity to review the proposed installation in context and feedback raised can then be incorporated at minimal additional cost.This is a positive step forward for improved engagement with the operations team as well as achieving early agreement of the design. This AR ALM (access lifting maintenance) exercise was undertaken in the physical space of the existing retained assets with the new recirculation pipework, pumps, valves and instruments shown virtually where they will be installed, giving a really valuable contextualisation of the layout.
- Right first time: Most accidents on construction sites occur where there is a change to the original plan and rework is undertaken. Office based digital rehearsals of installation sequences, in 3D and 4D environments, reduces the number of unplanned changes at site therefore minimising the risk of accident. It is also a powerful tool for formulating the methodology and communicating it to the site team in the task briefing.
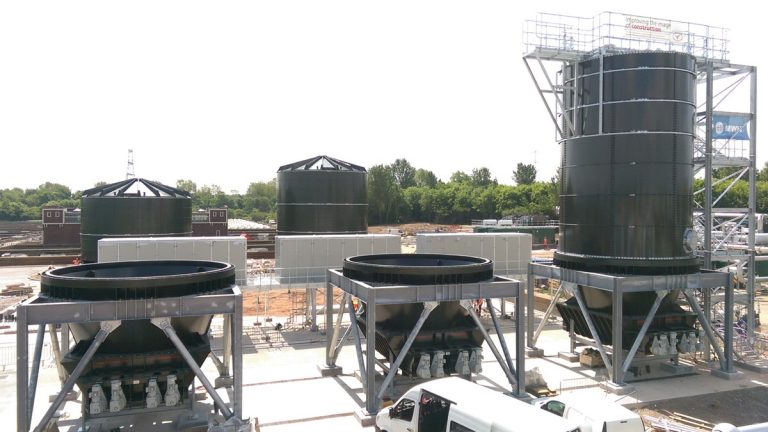
Silo and sludge buffer tank erection – Courtesy of MWH Treatment
Interface management
The complexity and number of key interfaces on a THP scheme must not be underestimated and therefore dedicated resource was allocated. The interface manager has excellent experience of the existing site and processes which has allowed an interface schedule to be developed listing all the assets to be re-utilised, detailing any maintenance work to be carried out in advance, connection methodologies and timescales all of which can be built into the contract programme to ensure access dates achieved. The commissioning plan has been developed to ensure that the health of the digesters is maintained during the conversion process to minimise disruption to the existing gas production.
Design for Manufacture and Assembly (DfMA)
The strategy for the project was for 70% of the equipment to be manufactured and assembled off-site to improve project efficiency, quality, shorten the programme and reduce site associated health and safety risks. This target has been exceeded and a summary of the key components are described below:
- Huber Technology: The 6 (No.) primary sludge screens (SP4 Strainpress) were pre-assembled onto a platform including electro-pneumatic LCPs
- Franklyn Yates: Supplied twin 300mm DI pipelines with GMS brackets for the sludge transfer mains
- Balmoral Tanks: Supplied 2 (No.) 1400m3 sludge buffer tanks. The epoxy coated panels and GRP roof sections were site assembled
- Utile Engineering: Supplied the air mixing and air lift systems. The compressors skid mounted with valves and pipework
- ERG (Air Pollution Control) Ltd: A biofilter with carbon filter odour control system was manufactured to minimise site assembly
- Alfa Laval: 3 (No.) pre-THP dewatering centrifuges (G3-125 low power type units) were factory mounted onto structural steelwork with pipework manifolds and acoustic enclosures. The walkways were site assembled
- Richard Alan Engineering: Supplied the poly dosing system, a 25T silo with walk-in skirted cone, AeroWet powder feed system, 20/20 IMS mixing/storage tanks, access steelwork and dosing skids pre-assembled and factory tested. LCP by TAP
- CTM Systems Ltd: Supplied 3 (No.) 300m3 sludge cake silos. The silo cone, slide valves, live screws and steelwork were pre-assembled. The glass coated panels and stainless steel roofs were assembled on site
- CTM Systems Ltd: Supplied 1 (No.) 30m3 imported sludge cake reception bunker. The silo hopper with steelwork and live screws was pre-assembled with a hydraulic door system. The complete unit was factory tested
- NOV Mono Pumps: Supplied 6 (No.) cake PC pumps and were EZstrip fitted with jacking caster wheels for maintenance. The pumps were factory tested
- Alpha Plus Ltd: Provided the Schedule 10 stainless steel PN25 cake transfer pipework
- Cambi: Supplied the 3 (No.) THP streams (B6(4)). The standard product was manufactured and assembled in modules each comprising a pulper, 4 (No.) reactors, flash tank, digester feed pumps, process gas unit, process air package, pipework and instrumentation. The software and ICA sections were integrated with an MCC
- Cambi: Provided 6 (No.) heat exchangers. The coolers were designed for hydrolysed sludge characteristics
- MEPS and ABC Stainless: Supplied 6 (No.) sets of recirculation pipework. The pipework was pre-assembled onto frames in 12m long sections. These were pressure tested in the factory and designed for ease of assembly
- Landia: The 12 (No.) chopper type recirculation pumps were designed for sludge applications and for ease of maintenance
- Dunphy Combustion: Supplied 3 (No.) 6 ton/hour natural gas/biogas steam boilers. The modular boiler house with all associated ancillary equipment and MCCs were pre-assembled and commissioned at FAT
- Hartwell Manufacturing: The 19m high chimney with 8 (No.) flues was delivered pre-assembled
- Clarke Energy: The waste heat ducting was fabricated and pre-lagged to minimise site assembly time
- SW Turner Mechanical Pipework Specialists: The steam pipework is to be factory welded, lagged and fixed to sub-assemblies including road crossing gantries
- Stortec Engineering Ltd: The twin membranes for the 2 (No.) 4000m3 gas bags were welded at the factory. Blowers were skid mounted and pre-wired. The condensate pots were fabricated from stainless steel
- Uniflare: Provided 2 (No.) waste gas burners each rated at 3669Nm3/hr. The combustion chamber, shroud, booster and pipework were skid mounted, factory assembled and tested with LCP
- Uniflare: The siloxane filter for boilers has a skid mounted dehumidifier, boosters and carbon filters with LCP
- SPP Pumps Ltd: The 3 (No.) FE pumps were factory assembled and tested
- KDN Pillinger: The process water booster set was skid mounted with TAP LCP
- Forbes Tanks: The process water tank was manufactured and tested prior to installation
- Bollfilter UK Ltd: Provided 6 (No.) auto-backwash strainers (6.18 PN16) with FouleX elements to resist biofilm. The units were factory assembled and tested
- Xylem Water Solutions (Wedeco): The 2 (No.) UV treatment units were factory assembled and tested with TAP LCP.
- Total Automation & Power (TAP): The framework supplier for the THP MCC, recirculation MCC and MCC 72 upgrade. TAP engineers worked collaboratively to ensure system integration. The MCCs and software were factory tested.
- Industrial GRP and Morgan Marine: The smaller GRP kiosks were delivered complete and the larger MCC kiosks in sections.
- Project 77 Environmental Ltd: Supplied the MCC air conditioning units which were delivered with minimal site assembly and no ducting required
- Galliford Try Fabrications and Tushingham Steel: The access steelwork was prefabricated where possible to minimise site assembly.
Modular steam boiler house (22m wide x 17m deep x 9m high)
The THP requires a steam generation system to deliver 12t/hour of saturated steam at 175°C at 12barg. This will be provided by 3 (No.) combination boiler units capable of burning biogas or natural gas and recovering CHP exhaust waste heat (421°C) through economisers to maximise efficiency.
Dunphy Combustion was selected as they were able to successfully demonstrate modular boiler house THP reference installations to the operators both in the factory and in operation. The standard design was updated to give improved access to the boilers and a separate control room on the request of the STW operation and maintenance team.
The advantage of the Dunphy Combustion DfMA approach is that the system is fully commissioned producing steam at the factory then shipped to site where the assembly time is only three weeks which is impressive for a plant room of such scale and complexity. Delays to the civil works have been mitigated by off-site construction.
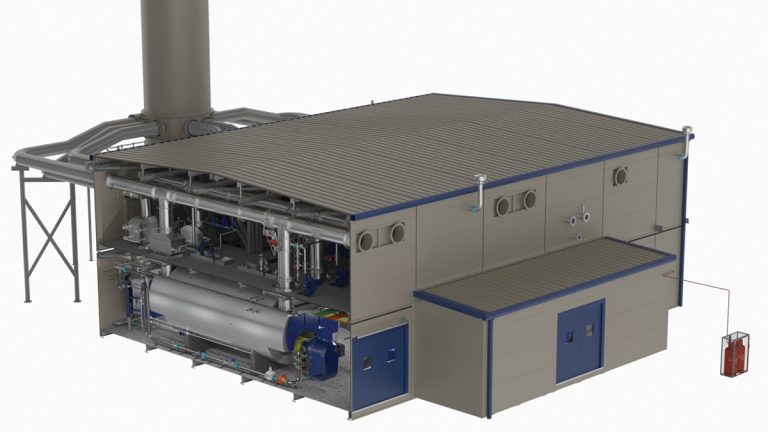
Steam generation – modular boiler house – Courtesy of Dunphy Combustion
Cambi streams installed
The Minworth THP project achieved a key milestone on 27 February 2017 with the commencement of the delivery and installation of the Cambi B6(4) modules.
This operation was planned with military precision including detailed load schedules and 4D synchro digital rehearsals. It is impressive to note that Cambi have manufactured and assembled the three streams in just 12 months. This is a great example of the DfMA approach with 3 weeks to position the modules followed by 6 weeks to complete site mechanical and electrical installation.
The benefit of the standard design is that the installation team have experience in installing the same equipment from numerous sites.
The design and construction of the civil works to the THP base slab involved demolition of a redundant sludge tank, backfilling with 25,000 tons of structural fill, underground drainage/process pipework and a myriad of electrical ducts!
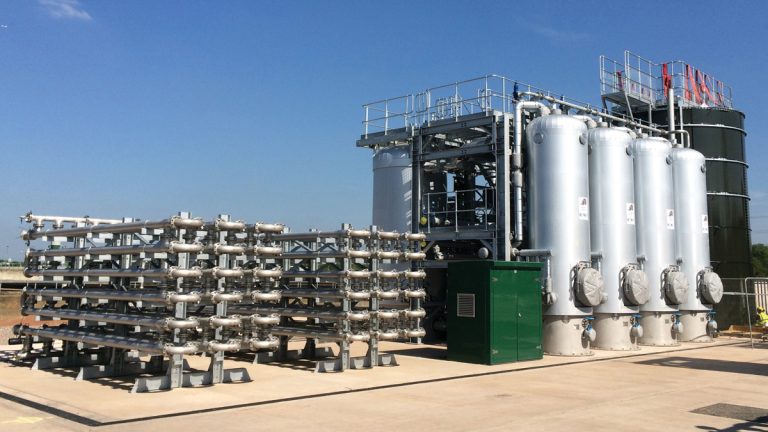
Cambi B6 Streams complete – Courtesy of MWH Treatment
Summary
The Minworth THP project is progressing ahead of schedule with civil construction complete and MEICA installation well advanced for site testing to start in September 2017. The collocated team are based on site to facilitate good communication and collaborative planning ensuring that all staff are task focussed and dedicated to achieving the stretch targets.
Digital delivery has benefitted the project delivery by:
- Reduction of rework.
- Improved quality.
- Better coordination.
- Clash detection.
- Interface management.
- Earlier resolution of issues.
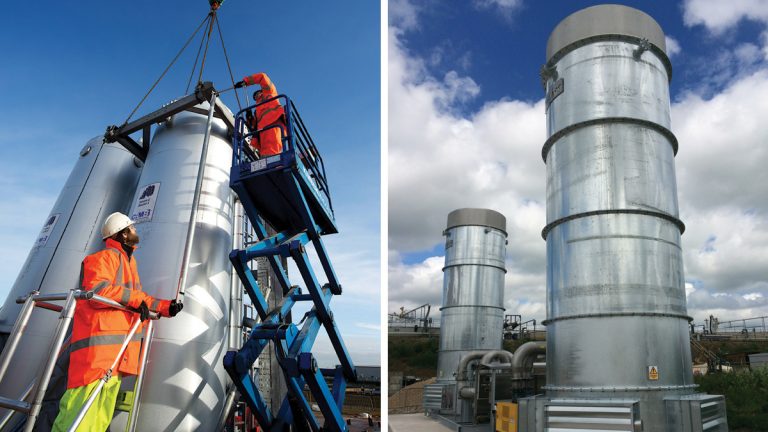
(left) Removing transport steel and (right) waste gas burners – Courtesy of MWH Treatment
Early procurement and DfMA has ensured that key equipment is ready for delivery as soon as the construction of the base slabs is complete capturing any programme gains.
The process commissioning phase for the Minworth Thermal Hydrolysis Plant is planned to take approximately 9 months to allow conversion of the sludge bacteria from conventional to the hydrolysed culture for the twelve digesters. Finally there will be a period of 54 days of reliability testing with completion and handover forecast for January 2019.